Page 2035 of 3419
FFD-4
PREPARATION
Revision: October 20052005 QX56
ST33081000
(—)
AdapterRemoving and installing side bearing inner
race.
a: 33.5 mm (1.32 in) dia.
b: 43 mm (1.69 in) dia.
KV38108300
(6958)
Spanner wrenchRemoving and installing drive pinion nut.
ST3127S000
(J-25765-A)
Preload gauge
1: GG91030000
(J-25765)
Torque wrench
2: HT62940000
(—)
Socket adapter (1/2″)
3: HT62900000
(—)
Socket adapter (3/8″)Inspecting drive pinion bearing preload and to-
tal preload
—
(C-4040)
InstallerInstalling drive pinion rear bearing inner race.
KV40105230
(—)
DriftInstalling drive pinion rear bearing outer race.
a: 92 mm(3.62 in) dia.
b: 86 mm (3.39 in) dia.
—
(C-4171)
Handle
Removing drive pinion front bearing outer
race
Removing drive pinion rear bearing outer
race Tool number
(Kent-Moore No.)
Tool nameDescription
ZZA0881D
LBIA0457E
NT124
SDIA2607E
ZZA1141D
LDIA0134E
Page 2039 of 3419
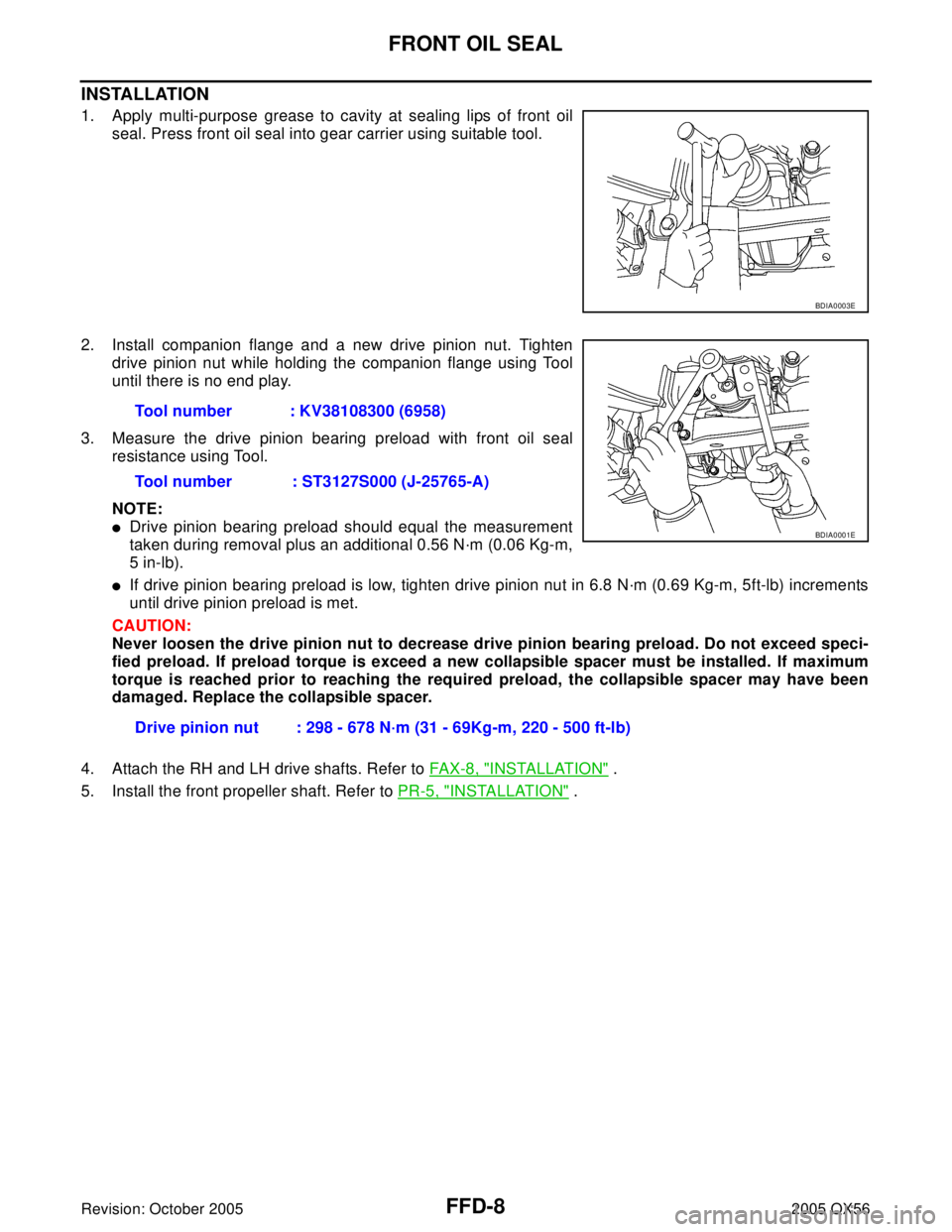
FFD-8
FRONT OIL SEAL
Revision: October 20052005 QX56
INSTALLATION
1. Apply multi-purpose grease to cavity at sealing lips of front oil
seal. Press front oil seal into gear carrier using suitable tool.
2. Install companion flange and a new drive pinion nut. Tighten
drive pinion nut while holding the companion flange using Tool
until there is no end play.
3. Measure the drive pinion bearing preload with front oil seal
resistance using Tool.
NOTE:
Drive pinion bearing preload should equal the measurement
taken during removal plus an additional 0.56 N·m (0.06 Kg-m,
5 in-lb).
If drive pinion bearing preload is low, tighten drive pinion nut in 6.8 N·m (0.69 Kg-m, 5ft-lb) increments
until drive pinion preload is met.
CAUTION:
Never loosen the drive pinion nut to decrease drive pinion bearing preload. Do not exceed speci-
fied preload. If preload torque is exceed a new collapsible spacer must be installed. If maximum
torque is reached prior to reaching the required preload, the collapsible spacer may have been
damaged. Replace the collapsible spacer.
4. Attach the RH and LH drive shafts. Refer to FAX-8, "
INSTALLATION" .
5. Install the front propeller shaft. Refer to PR-5, "
INSTALLATION" .
BDIA0003E
Tool number : KV38108300 (6958)
Tool number : ST3127S000 (J-25765-A)
Drive pinion nut : 298 - 678 N·m (31 - 69Kg-m, 220 - 500 ft-lb)
BDIA0001E
Page 2045 of 3419
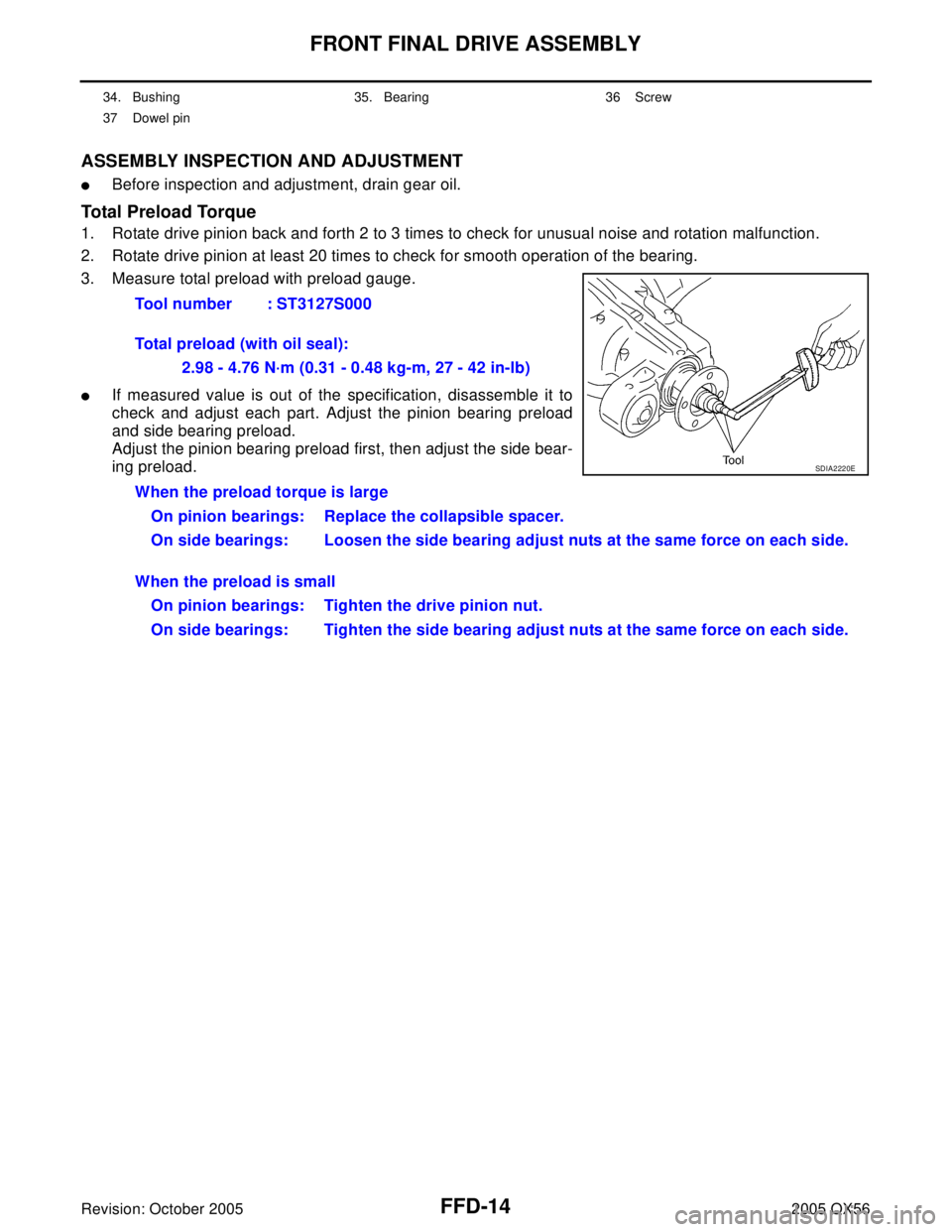
FFD-14
FRONT FINAL DRIVE ASSEMBLY
Revision: October 20052005 QX56
ASSEMBLY INSPECTION AND ADJUSTMENT
Before inspection and adjustment, drain gear oil.
Total Preload Torque
1. Rotate drive pinion back and forth 2 to 3 times to check for unusual noise and rotation malfunction.
2. Rotate drive pinion at least 20 times to check for smooth operation of the bearing.
3. Measure total preload with preload gauge.
If measured value is out of the specification, disassemble it to
check and adjust each part. Adjust the pinion bearing preload
and side bearing preload.
Adjust the pinion bearing preload first, then adjust the side bear-
ing preload.
34. Bushing 35. Bearing 36 Screw
37 Dowel pin
Tool number : ST3127S000
Total preload (with oil seal):
2.98 - 4.76 N·m (0.31 - 0.48 kg-m, 27 - 42 in-lb)
SDIA2220E
When the preload torque is large
On pinion bearings: Replace the collapsible spacer.
On side bearings: Loosen the side bearing adjust nuts at the same force on each side.
When the preload is small
On pinion bearings: Tighten the drive pinion nut.
On side bearings: Tighten the side bearing adjust nuts at the same force on each side.
Page 2057 of 3419
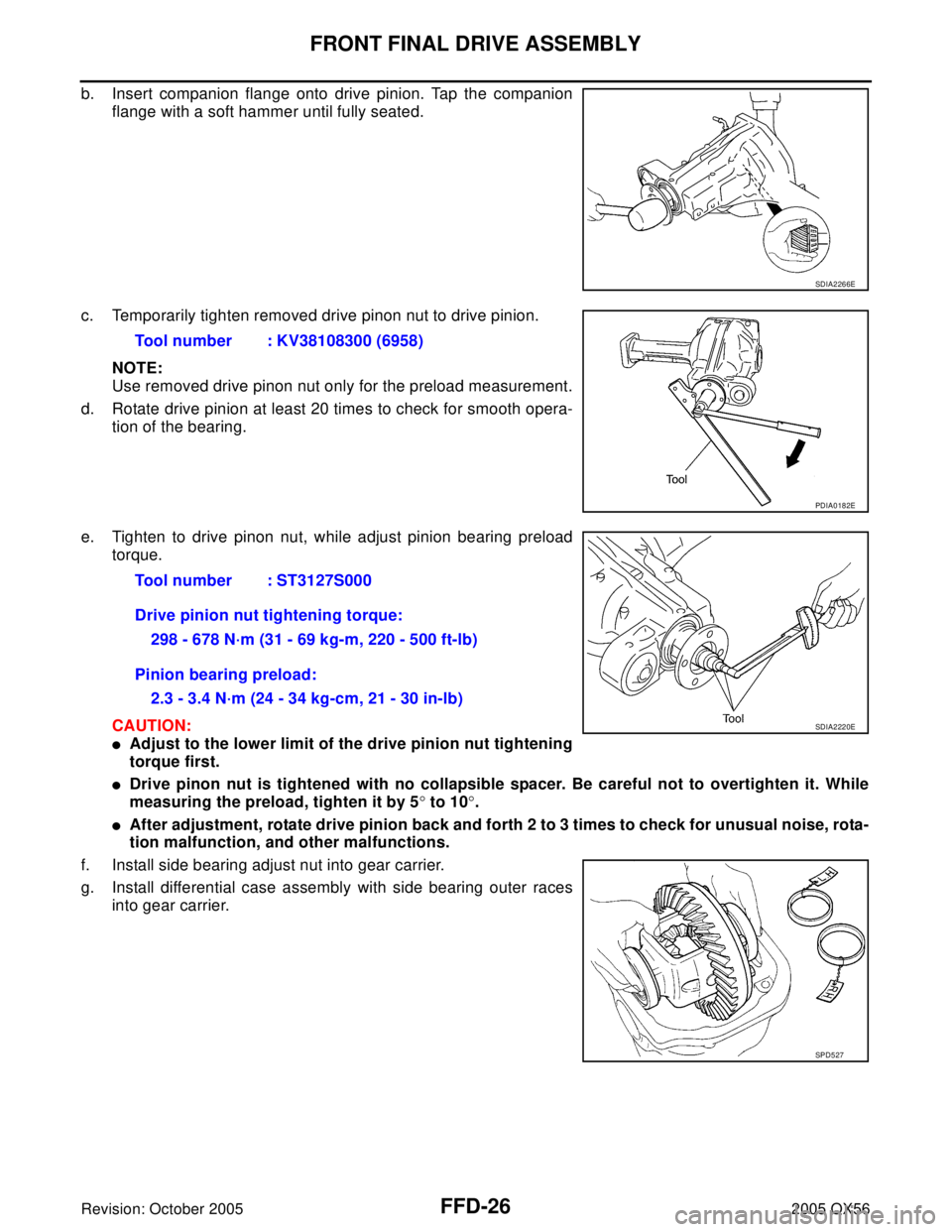
FFD-26
FRONT FINAL DRIVE ASSEMBLY
Revision: October 20052005 QX56
b. Insert companion flange onto drive pinion. Tap the companion
flange with a soft hammer until fully seated.
c. Temporarily tighten removed drive pinon nut to drive pinion.
NOTE:
Use removed drive pinon nut only for the preload measurement.
d. Rotate drive pinion at least 20 times to check for smooth opera-
tion of the bearing.
e. Tighten to drive pinon nut, while adjust pinion bearing preload
torque.
CAUTION:
Adjust to the lower limit of the drive pinion nut tightening
torque first.
Drive pinon nut is tightened with no collapsible spacer. Be careful not to overtighten it. While
measuring the preload, tighten it by 5° to 10°.
After adjustment, rotate drive pinion back and forth 2 to 3 times to check for unusual noise, rota-
tion malfunction, and other malfunctions.
f. Install side bearing adjust nut into gear carrier.
g. Install differential case assembly with side bearing outer races
into gear carrier.
SDIA2266E
Tool number : KV38108300 (6958)
PDIA0182E
Tool number : ST3127S000
Drive pinion nut tightening torque:
298 - 678 N·m (31 - 69 kg-m, 220 - 500 ft-lb)
Pinion bearing preload:
2.3 - 3.4 N·m (24 - 34 kg-cm, 21 - 30 in-lb)
SDIA2220E
SPD5 27
Page 2059 of 3419
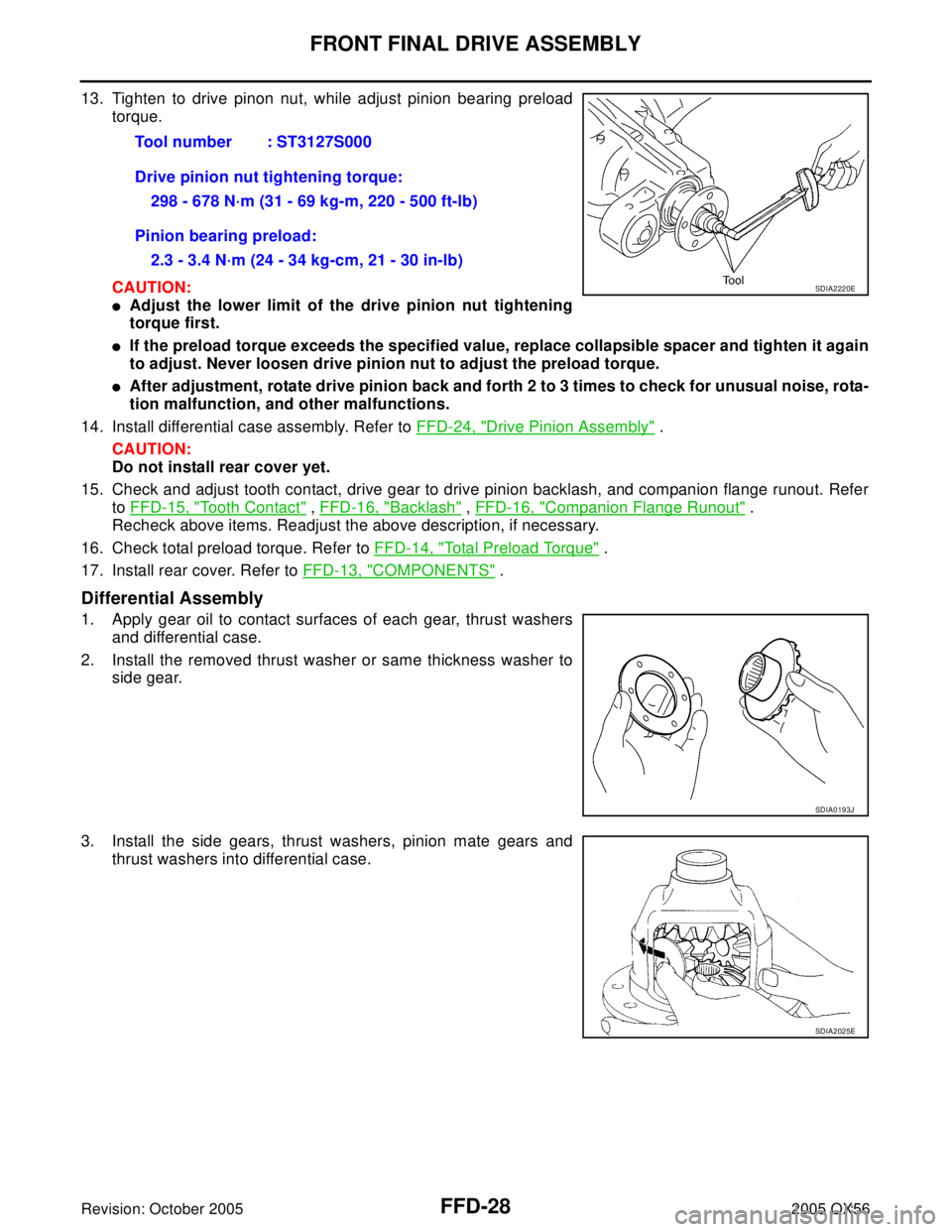
FFD-28
FRONT FINAL DRIVE ASSEMBLY
Revision: October 20052005 QX56
13. Tighten to drive pinon nut, while adjust pinion bearing preload
torque.
CAUTION:
Adjust the lower limit of the drive pinion nut tightening
torque first.
If the preload torque exceeds the specified value, replace collapsible spacer and tighten it again
to adjust. Never loosen drive pinion nut to adjust the preload torque.
After adjustment, rotate drive pinion back and forth 2 to 3 times to check for unusual noise, rota-
tion malfunction, and other malfunctions.
14. Install differential case assembly. Refer to FFD-24, "
Drive Pinion Assembly" .
CAUTION:
Do not install rear cover yet.
15. Check and adjust tooth contact, drive gear to drive pinion backlash, and companion flange runout. Refer
to FFD-15, "
Tooth Contact" , FFD-16, "Backlash" , FFD-16, "Companion Flange Runout" .
Recheck above items. Readjust the above description, if necessary.
16. Check total preload torque. Refer to FFD-14, "
Total Preload Torque" .
17. Install rear cover. Refer to FFD-13, "
COMPONENTS" .
Differential Assembly
1. Apply gear oil to contact surfaces of each gear, thrust washers
and differential case.
2. Install the removed thrust washer or same thickness washer to
side gear.
3. Install the side gears, thrust washers, pinion mate gears and
thrust washers into differential case.Tool number : ST3127S000
Drive pinion nut tightening torque:
298 - 678 N·m (31 - 69 kg-m, 220 - 500 ft-lb)
Pinion bearing preload:
2.3 - 3.4 N·m (24 - 34 kg-cm, 21 - 30 in-lb)
SDIA2220E
SDIA0193J
SDIA2025E
Page 2061 of 3419
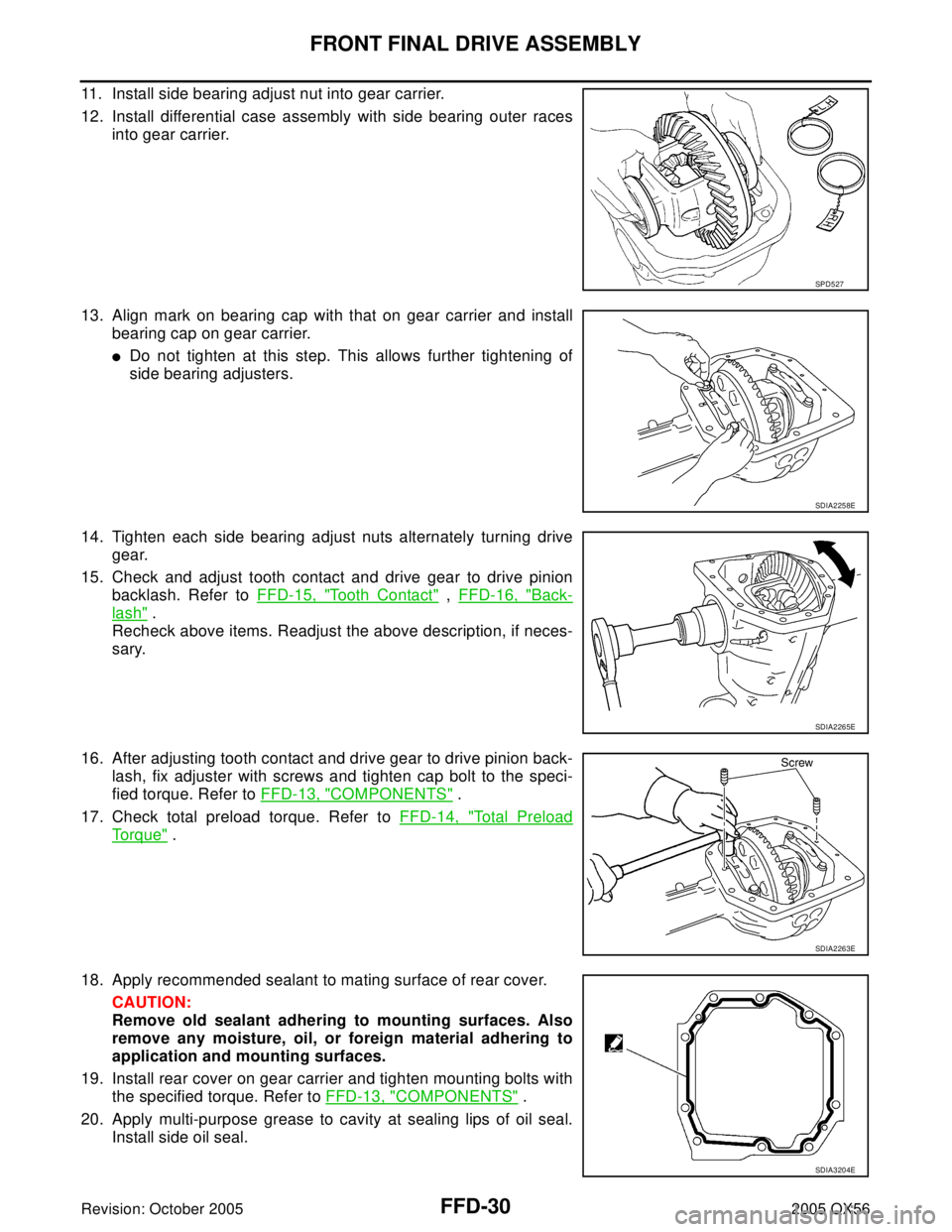
FFD-30
FRONT FINAL DRIVE ASSEMBLY
Revision: October 20052005 QX56
11. Install side bearing adjust nut into gear carrier.
12. Install differential case assembly with side bearing outer races
into gear carrier.
13. Align mark on bearing cap with that on gear carrier and install
bearing cap on gear carrier.
Do not tighten at this step. This allows further tightening of
side bearing adjusters.
14. Tighten each side bearing adjust nuts alternately turning drive
gear.
15. Check and adjust tooth contact and drive gear to drive pinion
backlash. Refer to FFD-15, "
Tooth Contact" , FFD-16, "Back-
lash" .
Recheck above items. Readjust the above description, if neces-
sary.
16. After adjusting tooth contact and drive gear to drive pinion back-
lash, fix adjuster with screws and tighten cap bolt to the speci-
fied torque. Refer to FFD-13, "
COMPONENTS" .
17. Check total preload torque. Refer to FFD-14, "
Total Preload
To r q u e" .
18. Apply recommended sealant to mating surface of rear cover.
CAUTION:
Remove old sealant adhering to mounting surfaces. Also
remove any moisture, oil, or foreign material adhering to
application and mounting surfaces.
19. Install rear cover on gear carrier and tighten mounting bolts with
the specified torque. Refer to FFD-13, "
COMPONENTS" .
20. Apply multi-purpose grease to cavity at sealing lips of oil seal.
Install side oil seal.
SPD5 27
SDIA2258E
SDIA2265E
SDIA2263E
SDIA3204E
Page 2068 of 3419
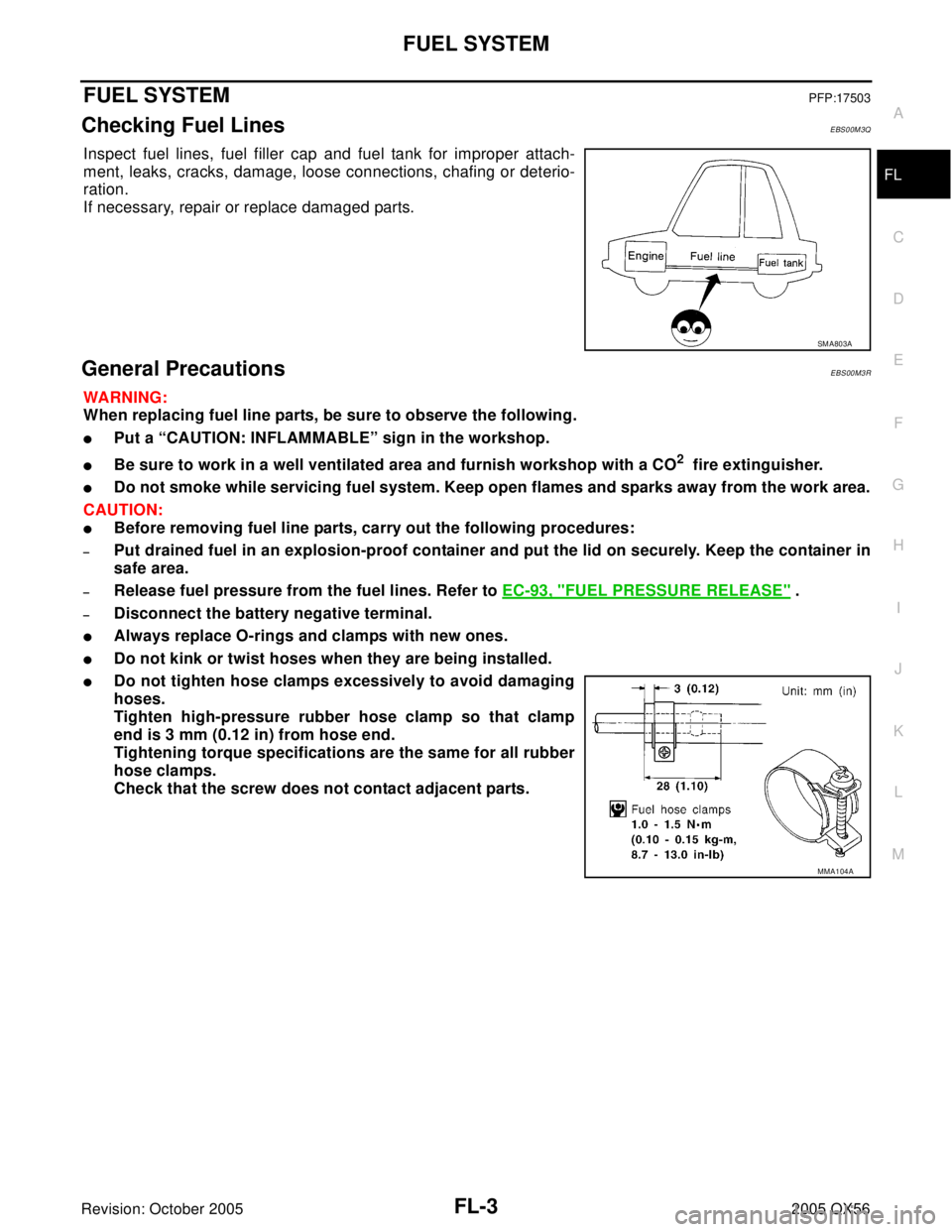
FUEL SYSTEM
FL-3
C
D
E
F
G
H
I
J
K
L
MA
FL
Revision: October 20052005 QX56
FUEL SYSTEMPFP:17503
Checking Fuel LinesEBS00M3Q
Inspect fuel lines, fuel filler cap and fuel tank for improper attach-
ment, leaks, cracks, damage, loose connections, chafing or deterio-
ration.
If necessary, repair or replace damaged parts.
General PrecautionsEBS00M3R
WA RN ING:
When replacing fuel line parts, be sure to observe the following.
Put a “CAUTION: INFLAMMABLE” sign in the workshop.
Be sure to work in a well ventilated area and furnish workshop with a CO2 fire extinguisher.
Do not smoke while servicing fuel system. Keep open flames and sparks away from the work area.
CAUTION:
Before removing fuel line parts, carry out the following procedures:
–Put drained fuel in an explosion-proof container and put the lid on securely. Keep the container in
safe area.
–Release fuel pressure from the fuel lines. Refer to EC-93, "FUEL PRESSURE RELEASE" .
–Disconnect the battery negative terminal.
Always replace O-rings and clamps with new ones.
Do not kink or twist hoses when they are being installed.
Do not tighten hose clamps excessively to avoid damaging
hoses.
Tighten high-pressure rubber hose clamp so that clamp
end is 3 mm (0.12 in) from hose end.
Tightening torque specifications are the same for all rubber
hose clamps.
Check that the screw does not contact adjacent parts.
SM A80 3A
MMA104A
Page 2085 of 3419
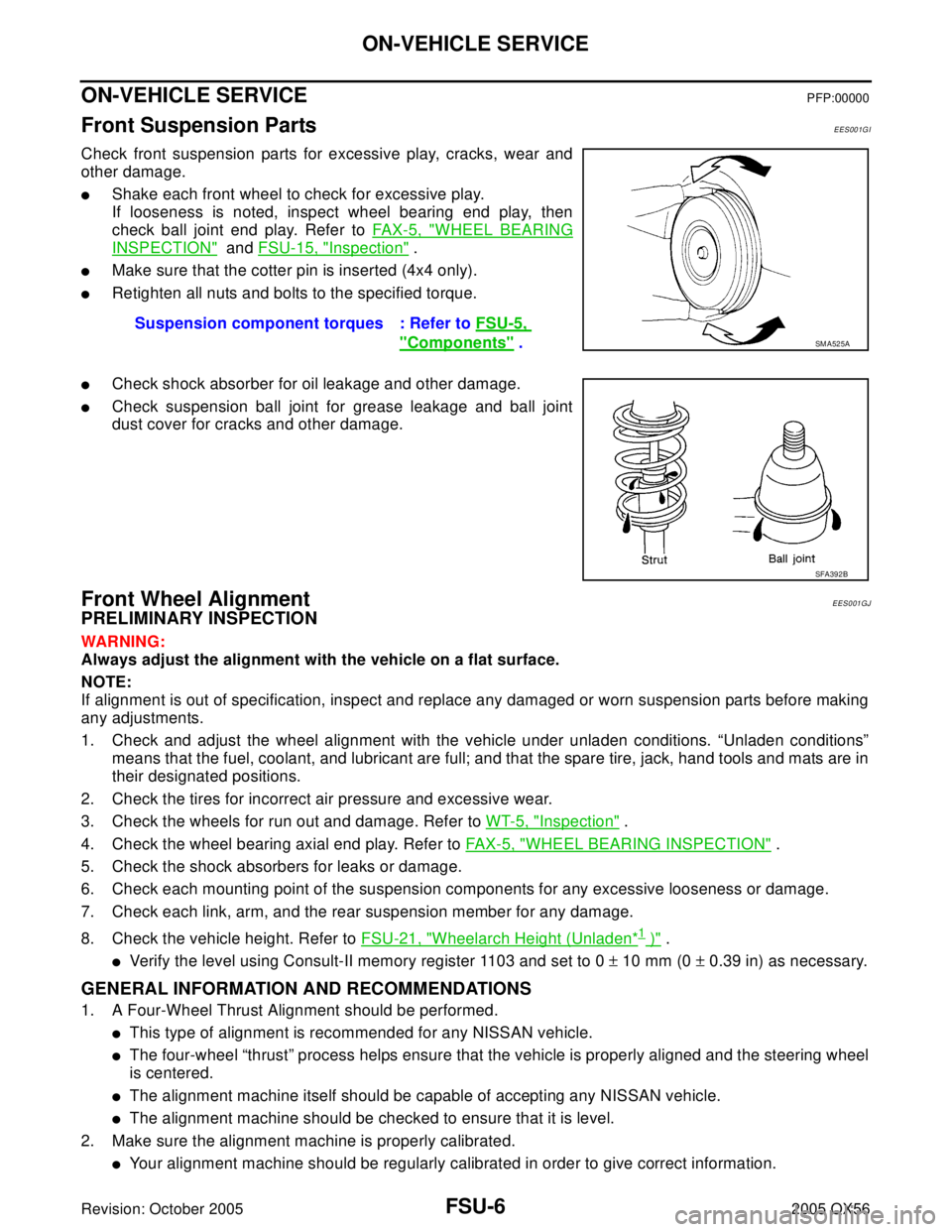
FSU-6
ON-VEHICLE SERVICE
Revision: October 20052005 QX56
ON-VEHICLE SERVICEPFP:00000
Front Suspension PartsEES001GI
Check front suspension parts for excessive play, cracks, wear and
other damage.
Shake each front wheel to check for excessive play.
If looseness is noted, inspect wheel bearing end play, then
check ball joint end play. Refer to FAX-5, "
WHEEL BEARING
INSPECTION" and FSU-15, "Inspection" .
Make sure that the cotter pin is inserted (4x4 only).
Retighten all nuts and bolts to the specified torque.
Check shock absorber for oil leakage and other damage.
Check suspension ball joint for grease leakage and ball joint
dust cover for cracks and other damage.
Front Wheel AlignmentEES001GJ
PRELIMINARY INSPECTION
WAR NIN G:
Always adjust the alignment with the vehicle on a flat surface.
NOTE:
If alignment is out of specification, inspect and replace any damaged or worn suspension parts before making
any adjustments.
1. Check and adjust the wheel alignment with the vehicle under unladen conditions. “Unladen conditions”
means that the fuel, coolant, and lubricant are full; and that the spare tire, jack, hand tools and mats are in
their designated positions.
2. Check the tires for incorrect air pressure and excessive wear.
3. Check the wheels for run out and damage. Refer to WT-5, "
Inspection" .
4. Check the wheel bearing axial end play. Refer to FAX-5, "
WHEEL BEARING INSPECTION" .
5. Check the shock absorbers for leaks or damage.
6. Check each mounting point of the suspension components for any excessive looseness or damage.
7. Check each link, arm, and the rear suspension member for any damage.
8. Check the vehicle height. Refer to FSU-21, "
Wheelarch Height (Unladen*1 )" .
Verify the level using Consult-II memory register 1103 and set to 0 ± 10 mm (0 ± 0.39 in) as necessary.
GENERAL INFORMATION AND RECOMMENDATIONS
1. A Four-Wheel Thrust Alignment should be performed.
This type of alignment is recommended for any NISSAN vehicle.
The four-wheel “thrust” process helps ensure that the vehicle is properly aligned and the steering wheel
is centered.
The alignment machine itself should be capable of accepting any NISSAN vehicle.
The alignment machine should be checked to ensure that it is level.
2. Make sure the alignment machine is properly calibrated.
Your alignment machine should be regularly calibrated in order to give correct information.Suspension component torques : Refer to FSU-5,
"Components" .SM A52 5A
SFA392B