Page 2041 of 3371
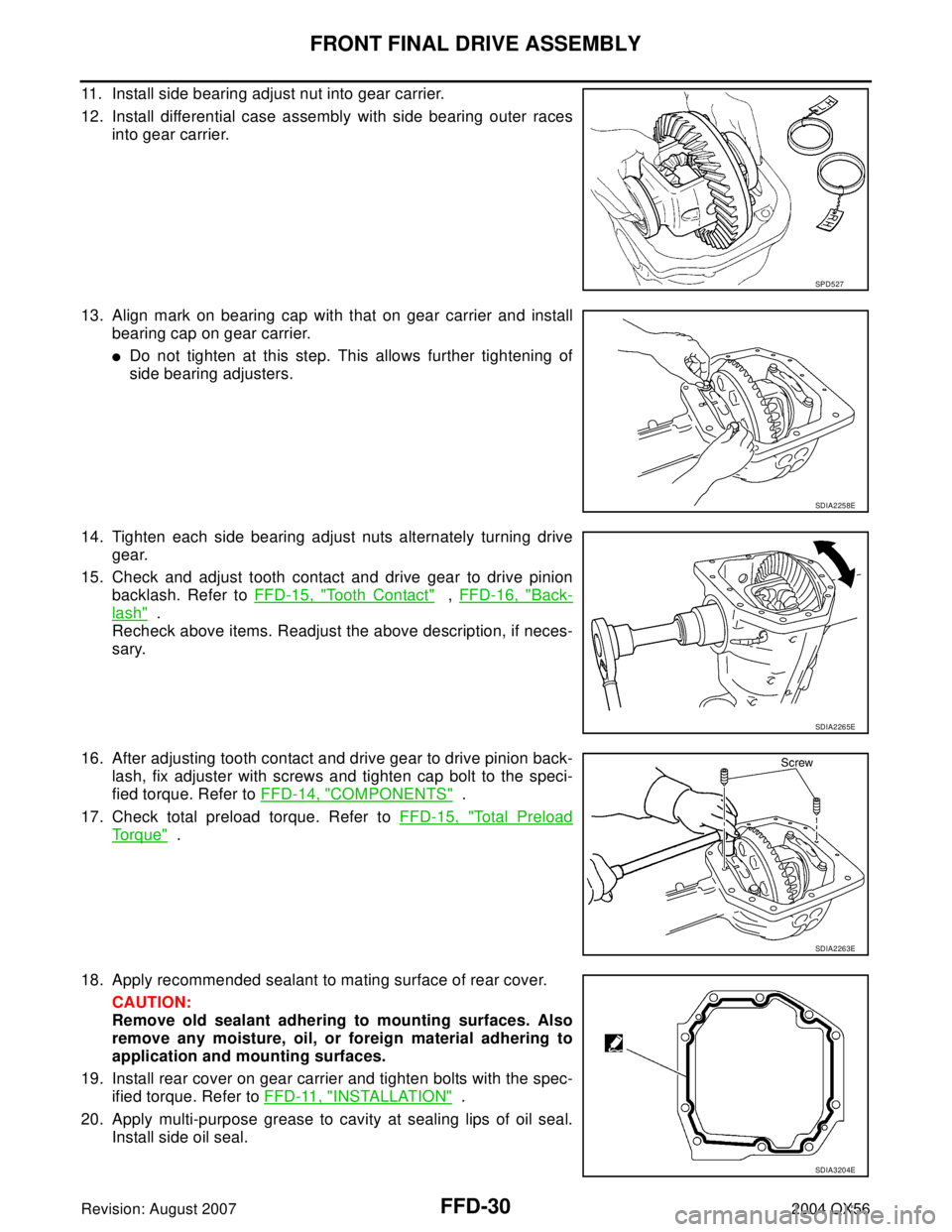
FFD-30
FRONT FINAL DRIVE ASSEMBLY
Revision: August 20072004 QX56
11. Install side bearing adjust nut into gear carrier.
12. Install differential case assembly with side bearing outer races
into gear carrier.
13. Align mark on bearing cap with that on gear carrier and install
bearing cap on gear carrier.
Do not tighten at this step. This allows further tightening of
side bearing adjusters.
14. Tighten each side bearing adjust nuts alternately turning drive
gear.
15. Check and adjust tooth contact and drive gear to drive pinion
backlash. Refer to FFD-15, "
Tooth Contact" , FFD-16, "Back-
lash" .
Recheck above items. Readjust the above description, if neces-
sary.
16. After adjusting tooth contact and drive gear to drive pinion back-
lash, fix adjuster with screws and tighten cap bolt to the speci-
fied torque. Refer to FFD-14, "
COMPONENTS" .
17. Check total preload torque. Refer to FFD-15, "
Total Preload
To r q u e" .
18. Apply recommended sealant to mating surface of rear cover.
CAUTION:
Remove old sealant adhering to mounting surfaces. Also
remove any moisture, oil, or foreign material adhering to
application and mounting surfaces.
19. Install rear cover on gear carrier and tighten bolts with the spec-
ified torque. Refer to FFD-11, "
INSTALLATION" .
20. Apply multi-purpose grease to cavity at sealing lips of oil seal.
Install side oil seal.
SPD5 27
SDIA2258E
SDIA2265E
SDIA2263E
SDIA3204E
Page 2043 of 3371
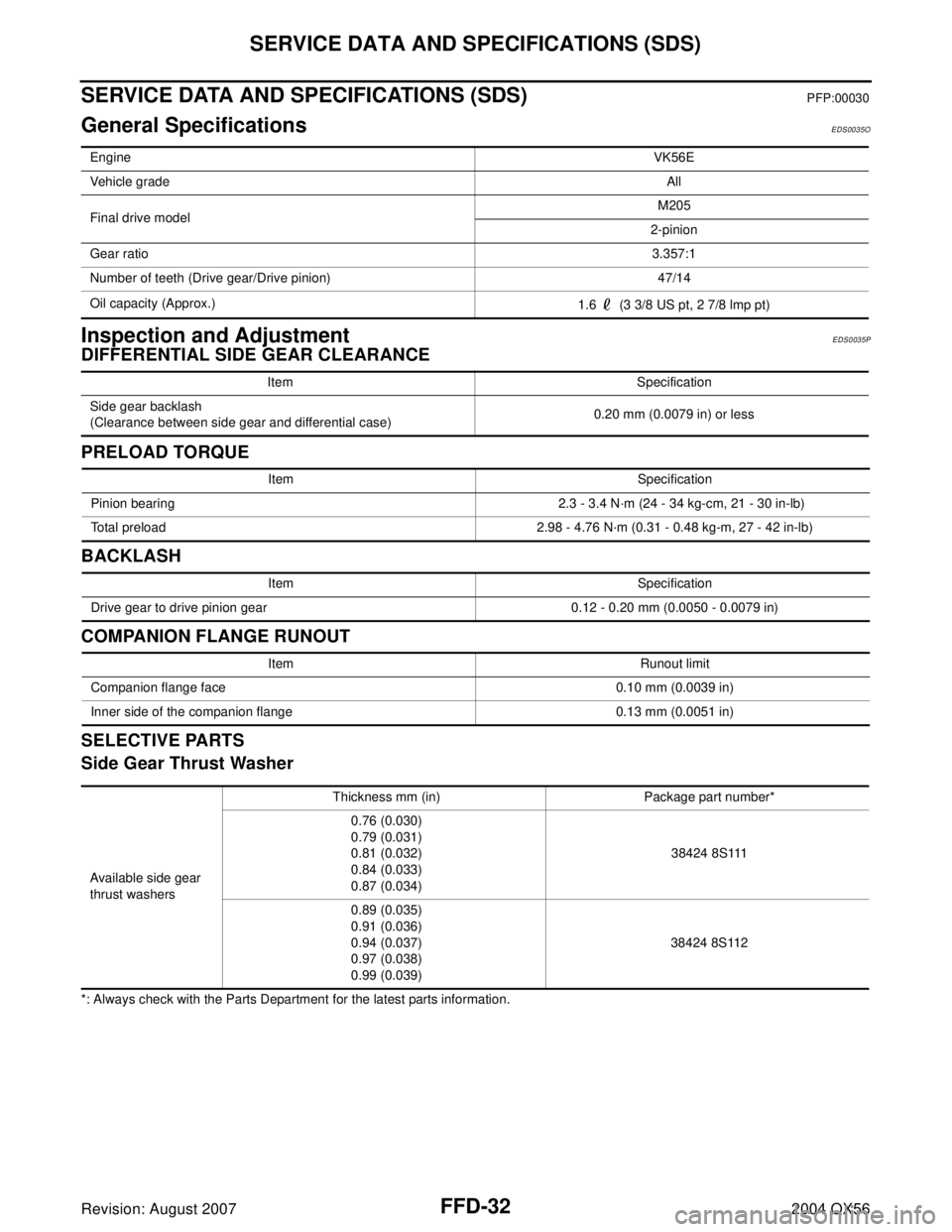
FFD-32
SERVICE DATA AND SPECIFICATIONS (SDS)
Revision: August 20072004 QX56
SERVICE DATA AND SPECIFICATIONS (SDS)PFP:00030
General SpecificationsEDS0035O
Inspection and AdjustmentEDS0035P
DIFFERENTIAL SIDE GEAR CLEARANCE
PRELOAD TORQUE
BACKLASH
COMPANION FLANGE RUNOUT
SELECTIVE PARTS
Side Gear Thrust Washer
*: Always check with the Parts Department for the latest parts information.EngineVK56E
Vehicle gradeAll
Final drive modelM205
2-pinion
Gear ratio3.357:1
Number of teeth (Drive gear/Drive pinion) 47/14
Oil capacity (Approx.)
1.6 (3 3/8 US pt, 2 7/8 lmp pt)
Item Specification
Side gear backlash
(Clearance between side gear and differential case)0.20 mm (0.0079 in) or less
Item Specification
Pinion bearing 2.3 - 3.4 N·m (24 - 34 kg-cm, 21 - 30 in-lb)
Total preload 2.98 - 4.76 N·m (0.31 - 0.48 kg-m, 27 - 42 in-lb)
Item Specification
Drive gear to drive pinion gear 0.12 - 0.20 mm (0.0050 - 0.0079 in)
Item Runout limit
Companion flange face 0.10 mm (0.0039 in)
Inner side of the companion flange 0.13 mm (0.0051 in)
Available side gear
thrust washersThickness mm (in) Package part number*
0.76 (0.030)
0.79 (0.031)
0.81 (0.032)
0.84 (0.033)
0.87 (0.034)38424 8S111
0.89 (0.035)
0.91 (0.036)
0.94 (0.037)
0.97 (0.038)
0.99 (0.039)38424 8S112
Page 2067 of 3371
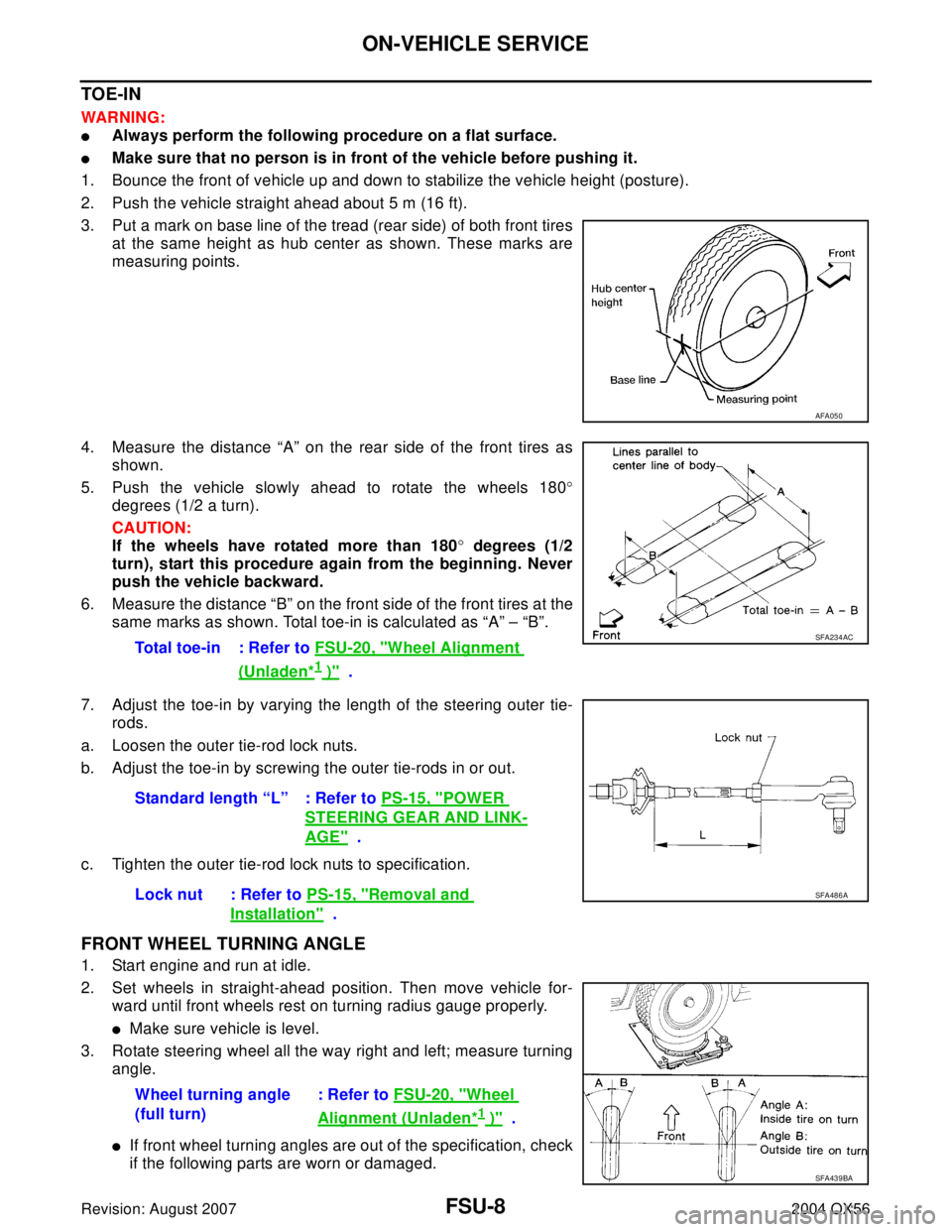
FSU-8
ON-VEHICLE SERVICE
Revision: August 20072004 QX56
TOE-IN
WAR NIN G:
Always perform the following procedure on a flat surface.
Make sure that no person is in front of the vehicle before pushing it.
1. Bounce the front of vehicle up and down to stabilize the vehicle height (posture).
2. Push the vehicle straight ahead about 5 m (16 ft).
3. Put a mark on base line of the tread (rear side) of both front tires
at the same height as hub center as shown. These marks are
measuring points.
4. Measure the distance “A” on the rear side of the front tires as
shown.
5. Push the vehicle slowly ahead to rotate the wheels 180°
degrees (1/2 a turn).
CAUTION:
If the wheels have rotated more than 180° degrees (1/2
turn), start this procedure again from the beginning. Never
push the vehicle backward.
6. Measure the distance “B” on the front side of the front tires at the
same marks as shown. Total toe-in is calculated as “A” – “B”.
7. Adjust the toe-in by varying the length of the steering outer tie-
rods.
a. Loosen the outer tie-rod lock nuts.
b. Adjust the toe-in by screwing the outer tie-rods in or out.
c. Tighten the outer tie-rod lock nuts to specification.
FRONT WHEEL TURNING ANGLE
1. Start engine and run at idle.
2. Set wheels in straight-ahead position. Then move vehicle for-
ward until front wheels rest on turning radius gauge properly.
Make sure vehicle is level.
3. Rotate steering wheel all the way right and left; measure turning
angle.
If front wheel turning angles are out of the specification, check
if the following parts are worn or damaged.
AFA05 0
Total toe-in : Refer to FSU-20, "Wheel Alignment
(Unladen*1 )" .
SFA234AC
Standard length “L” : Refer to PS-15, "POWER
STEERING GEAR AND LINK-
AGE" .
Lock nut : Refer to PS-15, "
Removal and
Installation" .
SFA486A
Wheel turning angle
(full turn): Refer to FSU-20, "Wheel
Alignment (Unladen*1 )" .
SFA439BA
Page 2076 of 3371
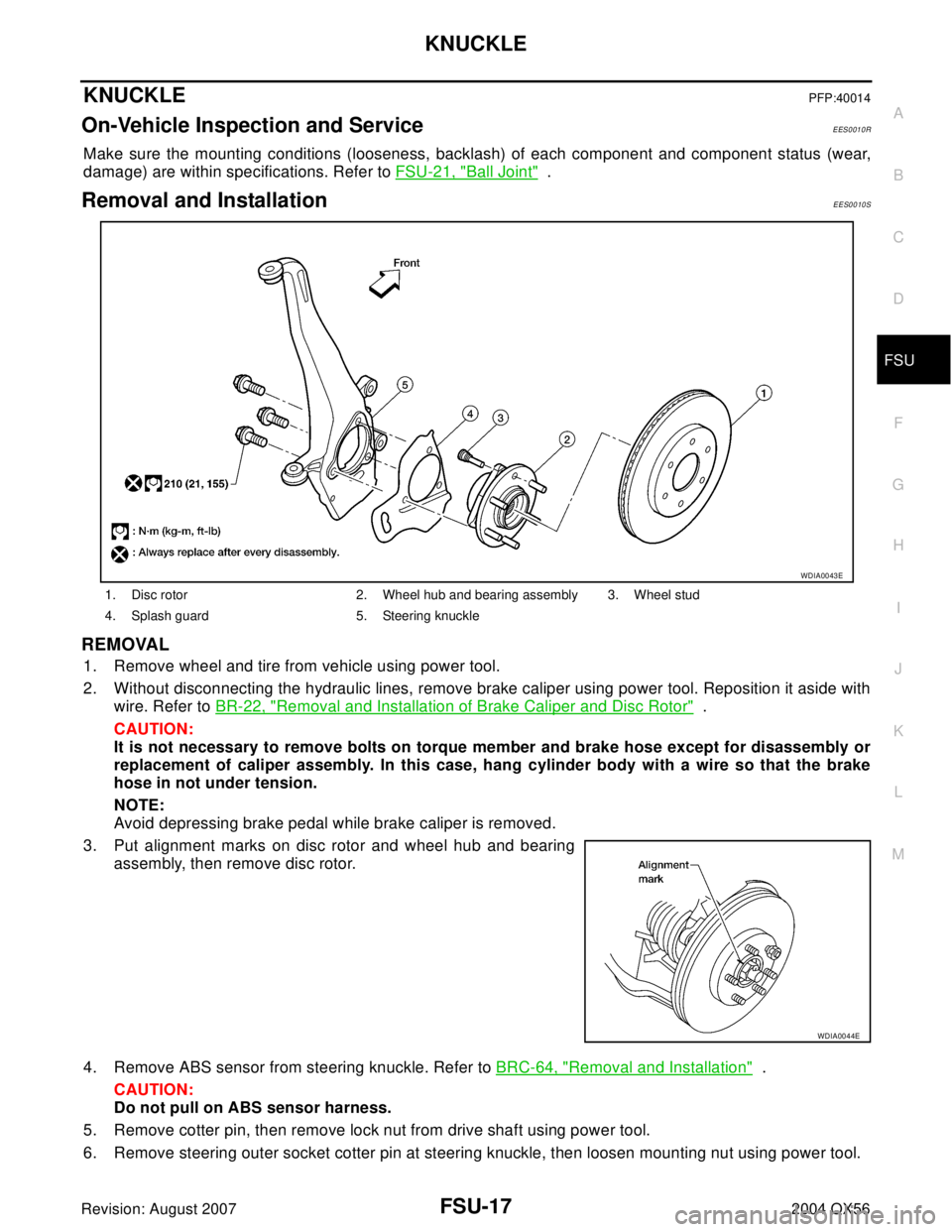
KNUCKLE
FSU-17
C
D
F
G
H
I
J
K
L
MA
B
FSU
Revision: August 20072004 QX56
KNUCKLEPFP:40014
On-Vehicle Inspection and ServiceEES0010R
Make sure the mounting conditions (looseness, backlash) of each component and component status (wear,
damage) are within specifications. Refer to FSU-21, "
Ball Joint" .
Removal and InstallationEES0010S
REMOVAL
1. Remove wheel and tire from vehicle using power tool.
2. Without disconnecting the hydraulic lines, remove brake caliper using power tool. Reposition it aside with
wire. Refer to BR-22, "
Removal and Installation of Brake Caliper and Disc Rotor" .
CAUTION:
It is not necessary to remove bolts on torque member and brake hose except for disassembly or
replacement of caliper assembly. In this case, hang cylinder body with a wire so that the brake
hose in not under tension.
NOTE:
Avoid depressing brake pedal while brake caliper is removed.
3. Put alignment marks on disc rotor and wheel hub and bearing
assembly, then remove disc rotor.
4. Remove ABS sensor from steering knuckle. Refer to BRC-64, "
Removal and Installation" .
CAUTION:
Do not pull on ABS sensor harness.
5. Remove cotter pin, then remove lock nut from drive shaft using power tool.
6. Remove steering outer socket cotter pin at steering knuckle, then loosen mounting nut using power tool.
1. Disc rotor 2. Wheel hub and bearing assembly 3. Wheel stud
4. Splash guard 5. Steering knuckle
WDIA0043E
WDIA0044E
Page 2100 of 3371
HOW TO USE THIS MANUAL
GI-19
C
D
E
F
G
H
I
J
K
L
MB
GI
Revision: August 20072004 QX56
Harness Indication
Letter designations next to test meter probe indicate harness
(connector) wire color.
Connector numbers in a single circle M33 indicate harness con-
nectors.
Component Indication
Connector numbers in a double circle F211 indicate component connectors.
Switch Positions
Switches are shown in wiring diagrams as if the vehicle is in the “normal” condition.
A vehicle is in the “normal” condition when:
ignition switch is “OFF”,
doors, hood and trunk lid/back door are closed,
pedals are not depressed, and
parking brake is released.
Detectable Lines and Non-Detectable Lines
In some wiring diagrams, two kinds of lines, representing wires, with different weight are used.
AGI070
SGI860
Page 2121 of 3371
GI-40
LIFTING POINT
Revision: August 20072004 QX56
LIFTING POINTPFP:00000
Pantograph JackEAS0014W
WAR NIN G:
Never get under the vehicle while it is supported only by the jack. Always use safety stands to
support the frame when you have to get under the vehicle.
Place wheel chocks at both front and back of the wheels on the ground.
Garage Jack and Safety StandEAS0014X
CAUTION:
Place a wooden or rubber block between safety stand and vehicle body when the supporting body is
flat.
LAIA0042E
WAIA0028E
Page 2123 of 3371
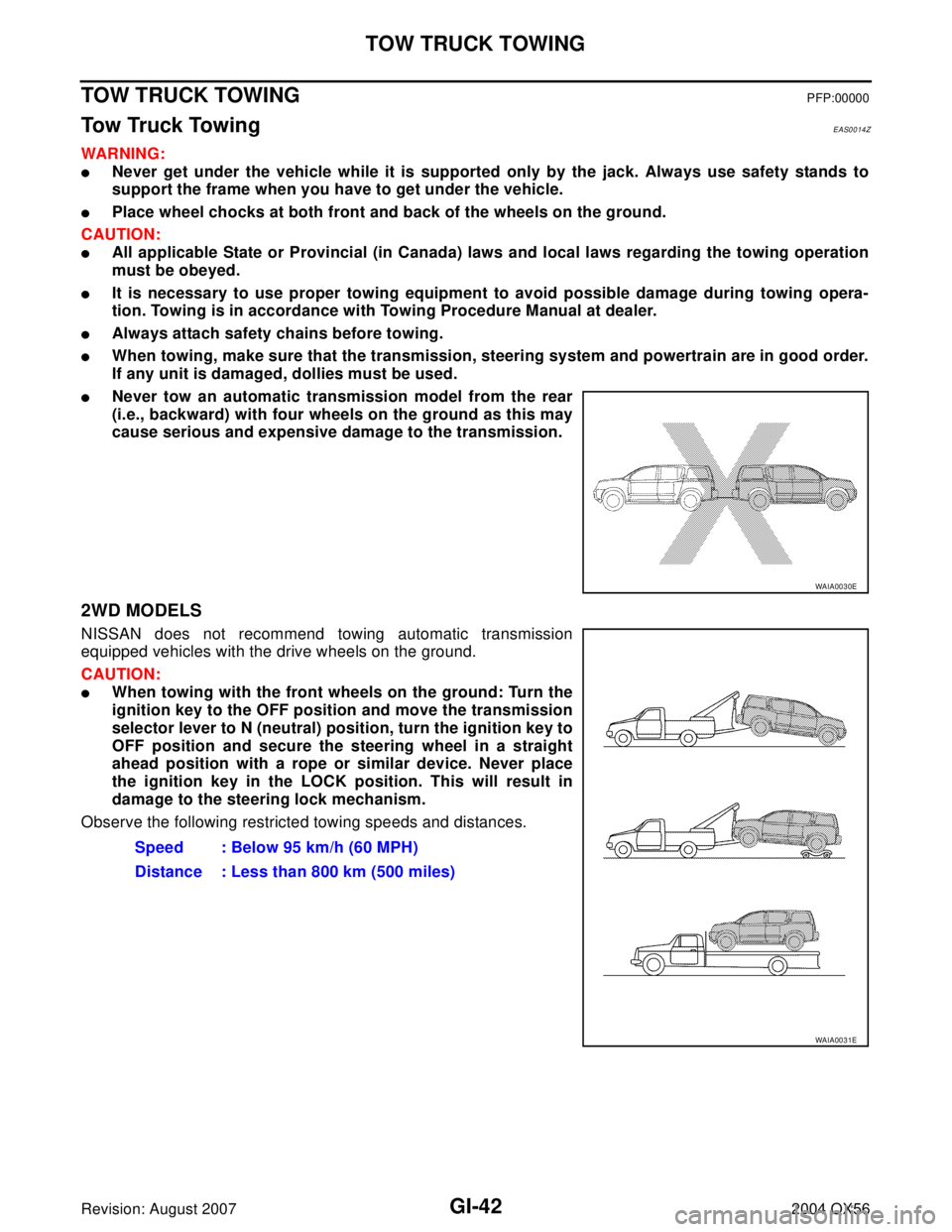
GI-42
TOW TRUCK TOWING
Revision: August 20072004 QX56
TOW TRUCK TOWINGPFP:00000
To w Tr u c k To w i n gEAS0014Z
WAR NIN G:
Never get under the vehicle while it is supported only by the jack. Always use safety stands to
support the frame when you have to get under the vehicle.
Place wheel chocks at both front and back of the wheels on the ground.
CAUTION:
All applicable State or Provincial (in Canada) laws and local laws regarding the towing operation
must be obeyed.
It is necessary to use proper towing equipment to avoid possible damage during towing opera-
tion. Towing is in accordance with Towing Procedure Manual at dealer.
Always attach safety chains before towing.
When towing, make sure that the transmission, steering system and powertrain are in good order.
If any unit is damaged, dollies must be used.
Never tow an automatic transmission model from the rear
(i.e., backward) with four wheels on the ground as this may
cause serious and expensive damage to the transmission.
2WD MODELS
NISSAN does not recommend towing automatic transmission
equipped vehicles with the drive wheels on the ground.
CAUTION:
When towing with the front wheels on the ground: Turn the
ignition key to the OFF position and move the transmission
selector lever to N (neutral) position, turn the ignition key to
OFF position and secure the steering wheel in a straight
ahead position with a rope or similar device. Never place
the ignition key in the LOCK position. This will result in
damage to the steering lock mechanism.
Observe the following restricted towing speeds and distances.
WAIA0030E
Speed : Below 95 km/h (60 MPH)
Distance : Less than 800 km (500 miles)
WAIA0031E
Page 2143 of 3371
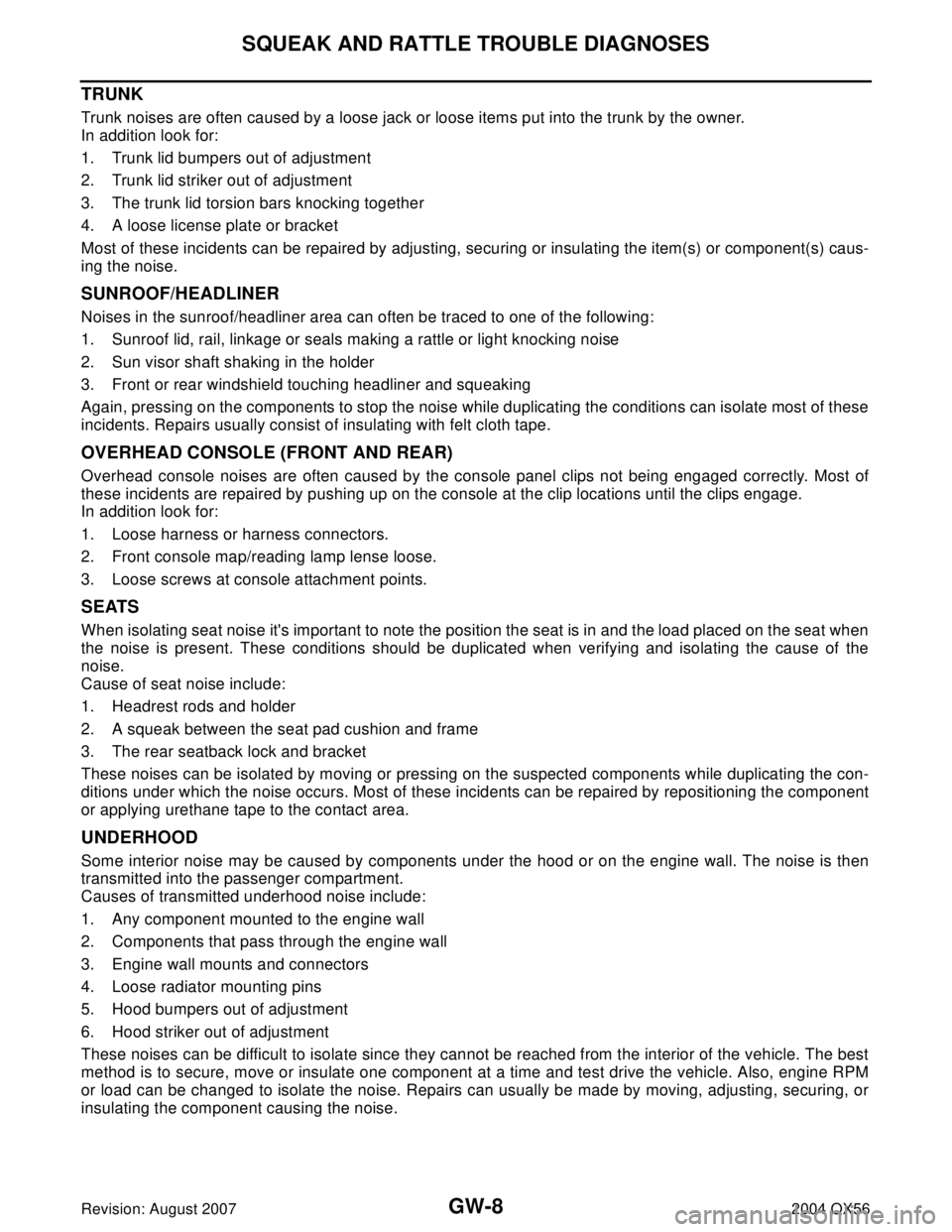
GW-8
SQUEAK AND RATTLE TROUBLE DIAGNOSES
Revision: August 20072004 QX56
TRUNK
Trunk noises are often caused by a loose jack or loose items put into the trunk by the owner.
In addition look for:
1. Trunk lid bumpers out of adjustment
2. Trunk lid striker out of adjustment
3. The trunk lid torsion bars knocking together
4. A loose license plate or bracket
Most of these incidents can be repaired by adjusting, securing or insulating the item(s) or component(s) caus-
ing the noise.
SUNROOF/HEADLINER
Noises in the sunroof/headliner area can often be traced to one of the following:
1. Sunroof lid, rail, linkage or seals making a rattle or light knocking noise
2. Sun visor shaft shaking in the holder
3. Front or rear windshield touching headliner and squeaking
Again, pressing on the components to stop the noise while duplicating the conditions can isolate most of these
incidents. Repairs usually consist of insulating with felt cloth tape.
OVERHEAD CONSOLE (FRONT AND REAR)
Overhead console noises are often caused by the console panel clips not being engaged correctly. Most of
these incidents are repaired by pushing up on the console at the clip locations until the clips engage.
In addition look for:
1. Loose harness or harness connectors.
2. Front console map/reading lamp lense loose.
3. Loose screws at console attachment points.
SEATS
When isolating seat noise it's important to note the position the seat is in and the load placed on the seat when
the noise is present. These conditions should be duplicated when verifying and isolating the cause of the
noise.
Cause of seat noise include:
1. Headrest rods and holder
2. A squeak between the seat pad cushion and frame
3. The rear seatback lock and bracket
These noises can be isolated by moving or pressing on the suspected components while duplicating the con-
ditions under which the noise occurs. Most of these incidents can be repaired by repositioning the component
or applying urethane tape to the contact area.
UNDERHOOD
Some interior noise may be caused by components under the hood or on the engine wall. The noise is then
transmitted into the passenger compartment.
Causes of transmitted underhood noise include:
1. Any component mounted to the engine wall
2. Components that pass through the engine wall
3. Engine wall mounts and connectors
4. Loose radiator mounting pins
5. Hood bumpers out of adjustment
6. Hood striker out of adjustment
These noises can be difficult to isolate since they cannot be reached from the interior of the vehicle. The best
method is to secure, move or insulate one component at a time and test drive the vehicle. Also, engine RPM
or load can be changed to isolate the noise. Repairs can usually be made by moving, adjusting, securing, or
insulating the component causing the noise.