Page 702 of 1574
SUSPENSION DIAGNOSIS 2A-5
INPUT & OUTPUT DEVICES AND DAMPING FORCECONTROL LOGIC
INPUT & OUTPUT DEVICES Damping force of shock absorber will rotate shock absorber control rod in 3 modes by driving actuator on the upper shock absorber when signaled from ECS. Rotary valve in the shock absorber will control hydraulic flow according to rotation of control rod to adjust damping force of shock absorber in SOFT MEDIUM HARD.
SYSTEM LAYOUT
1 ECS (ECU)
2 Body Vertical Acceleration Sensor (Vertical Sensor)
3 Body Lateral Acceleration Sensor (Lateral
Sensor)
Speed Sensor
Axle Vertical Acceleration Sensor (Wheel G Sensor)
Stop Lamp Switch
Body Vertical Acceleration Sensor (Vertical Sensor)
ECS Switch
Indicator Lamp
Actuator
Shock Absorber
Self-Diagnosis Connector
Damping Force Adjustment
ECS
(ECU)
Body Lateral Acceleration Sensor (Lateral Sensor)
4 ECS Mode Switch
5 Stop Lamp Switch
6 Axle Vertical Acceleration Sensor (Wheel G
Sensor)
7 Mode Actuator
Page 704 of 1574
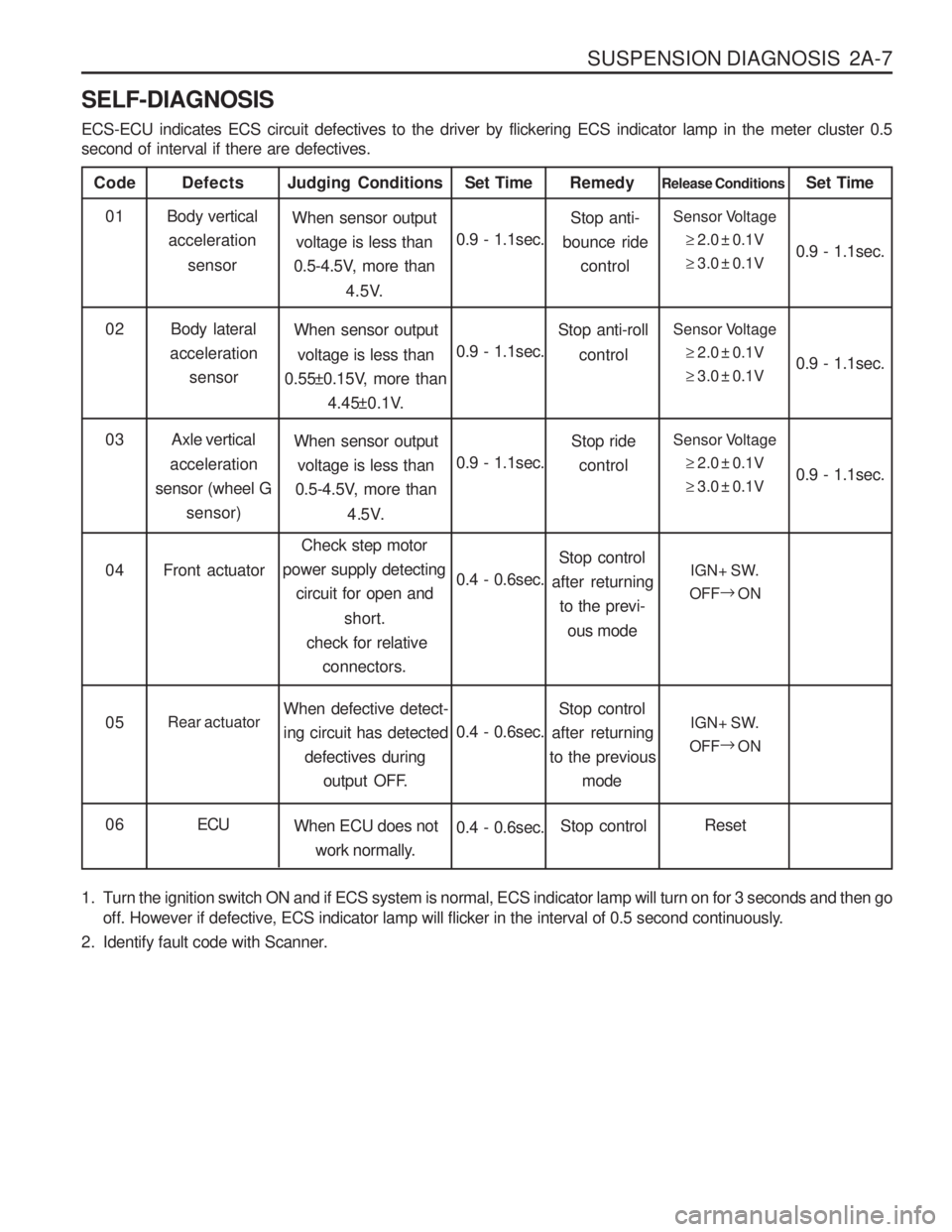
SUSPENSION DIAGNOSIS 2A-7
SELF-DIAGNOSIS ECS-ECU indicates ECS circuit defectives to the driver by flickering ECS indicator lamp in the meter cluster 0.5 second of interval if there are defectives.
Code
Body verticalacceleration
sensor
Defects
When sensor outputvoltage is less than
0.5-4.5V, more than
4.5V.
Judging Conditions01
0.9 - 1.1sec.Set TimeSensor Voltage
2.0 ± 0.1V
3.0 ± 0.1V
Release Conditions
0.9 - 1.1sec.
Set Time
Body lateral
acceleration sensor When sensor output
voltage is less than
0.55±0.15V, more than
4.45±0.1V.
02
0.9 - 1.1sec.Sensor Voltage
2.0 ± 0.1V
3.0 ± 0.1V 0.9 - 1.1sec.
Stop anti-
bounce ride
control
Remedy
Stop anti-roll control
Axle vertical
acceleration
sensor (wheel G sensor) When sensor output
voltage is less than
0.5-4.5V, more than
4.5V.
03
0.9 - 1.1sec.Sensor Voltage
2.0 ± 0.1V
3.0 ± 0.1V 0.9 - 1.1sec.
Stop ride
control
Front actuator Check step motor
power supply detecting
circuit for open and
short.
check for relative connectors.
04
0.4 - 0.6sec.IGN+ SW.
OFF
ON
Stop control
after returning to the previ-
ous mode
Rear actuator When defective detect- ing circuit has detected
defectives during
output OFF.
05
0.4 - 0.6sec.IGN+ SW.
OFF
ON
Stop control
after returning
to the previous
mode
ECU When ECU does not
work normally.
06
0.4 - 0.6sec.Reset
Stop control
1. Turn the ignition switch ON and if ECS system is normal, ECS indicator lamp will turn on for 3 seconds and then go off. However if defective, ECS indicator lamp will flicker in the interval of 0.5 second continuously.
2. Identify fault code with Scanner.
Page 708 of 1574
SUSPENSION DIAGNOSIS 2A-11
Connector Pin Number and Circuits
2
15
3
16
4
17
5
18
6
19
7
20
8
21
9
22
10
23
11
24
12
25
13
26
Ignition
Actuator R-MEDIUM Actuator R-SOFT
Actuator F-HEAD Select Switch
Speed Sensor
Wheel G Sensor
Wheel G Sensor Ground
-
Vertical G Sensor
Sensor +5V
Chassis Ground Indicator Lamp
NO. CircuitNO. Circuit
1 14
21 5
316
417
518
619
720
821
922
10 23
11 2 4
12 25
13 26 Chassis Ground
Actuator R-HEAD
Actuator F-MEDIUM
Actuator F-SOFT Brake Switch
-
Lateral G Sensor
Lateral G Sensor Ground
Vertical G Sensor Ground Diagnosis K Line
Diagnosis L Line - -
Page 710 of 1574
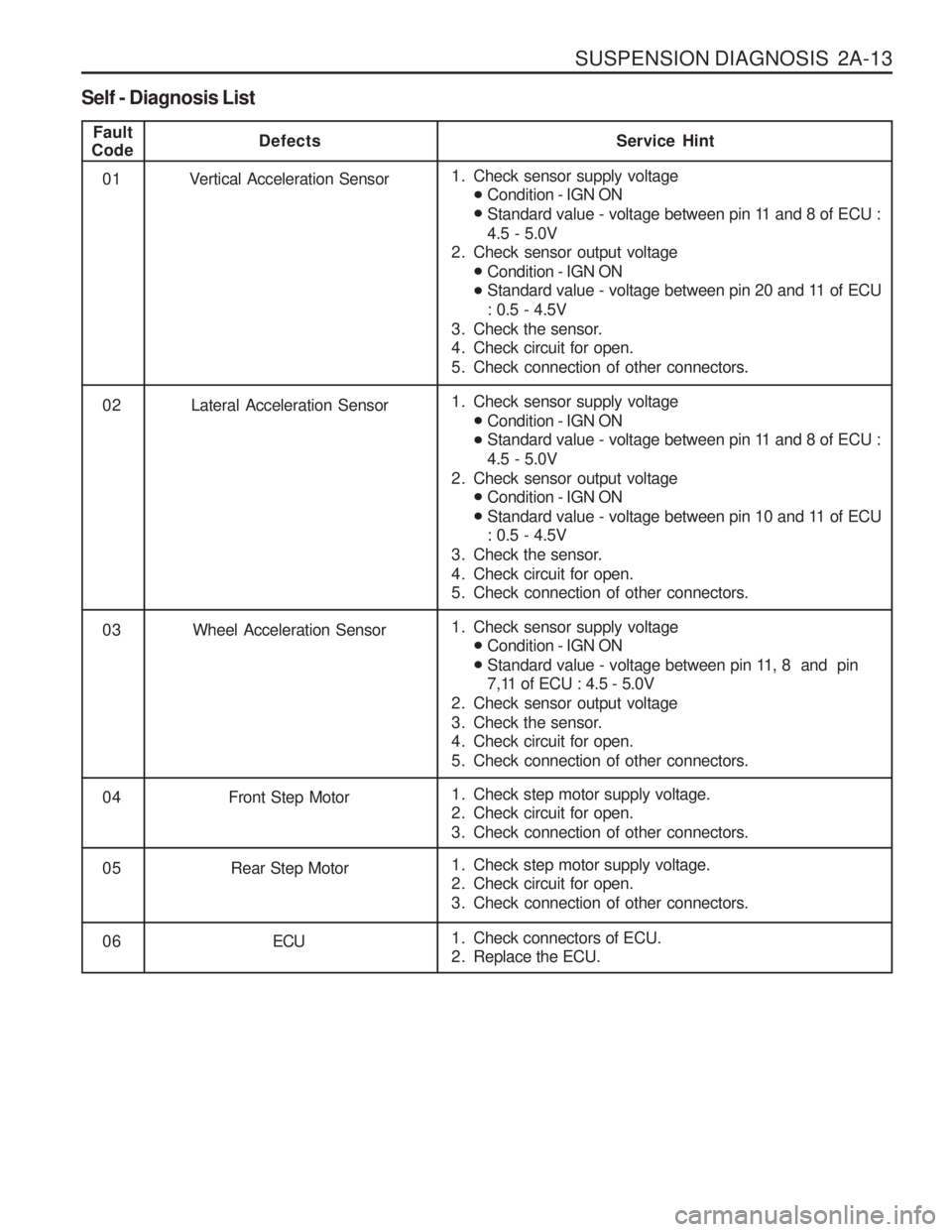
SUSPENSION DIAGNOSIS 2A-13
Self - Diagnosis List
Fault
CodeDefects Service Hint
01 Vertical Acceleration Sensor
02 Lateral Acceleration Sensor
03 Wheel Acceleration Sensor
04
05 Rear Step Motor
0 6 ECU Front Step Motor 1. Check sensor supply voltage
Condition - IGN ON
Standard value - voltage between pin 11 and 8 of ECU : 4.5 - 5.0V
2. Check sensor output voltage Condition - IGN ON
Standard value - voltage between pin 20 and 11 of ECU: 0.5 - 4.5V
3. Check the sensor.
4. Check circuit for open.
5. Check connection of other connectors.
1. Check sensor supply voltage Condition - IGN ON
Standard value - voltage between pin 11 and 8 of ECU : 4.5 - 5.0V
2. Check sensor output voltage Condition - IGN ON
Standard value - voltage between pin 10 and 11 of ECU : 0.5 - 4.5V
3. Check the sensor.
4. Check circuit for open.
5. Check connection of other connectors.
1. Check step motor supply voltage.
2. Check circuit for open.
3. Check connection of other connectors.
1. Check step motor supply voltage.
2. Check circuit for open.
3. Check connection of other connectors.
1. Check connectors of ECU.
2. Replace the ECU.
1. Check sensor supply voltage
Condition - IGN ON
Standard value - voltage between pin 11, 8 and pin
7,11 of ECU : 4.5 - 5.0V
2. Check sensor output voltage
3. Check the sensor.
4. Check circuit for open.
5. Check connection of other connectors.
Page 711 of 1574
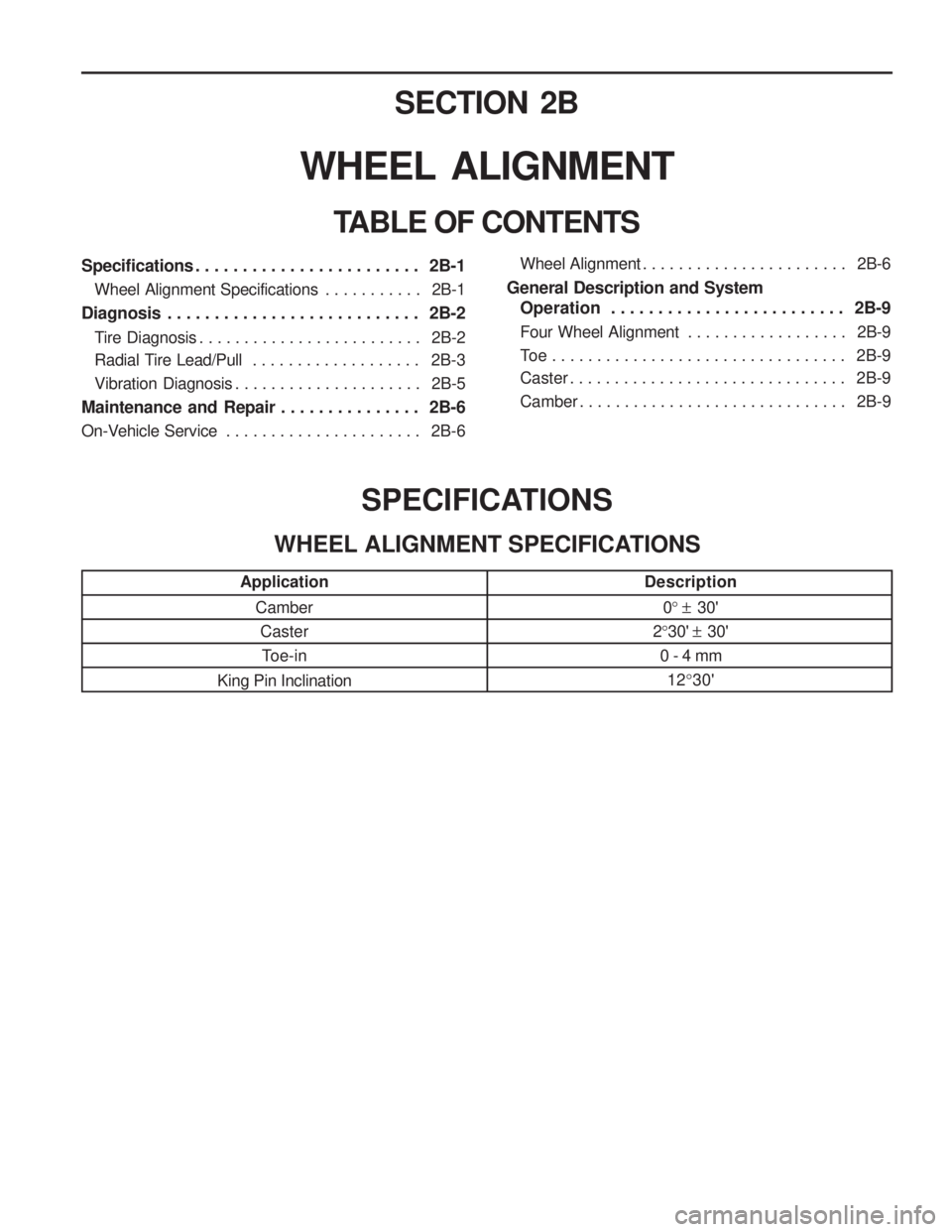
SECTION 2B
WHEEL ALIGNMENT
TABLE OF CONTENTSSPECIFICATIONS
WHEEL ALIGNMENT SPECIFICATIONS
Application CamberCaster
Toe-in
King Pin Inclination Description
0° ± 30'
2 °30' ± 30'
0 - 4 mm 12 °30'
Specifications . . . . . . . . . . . . . . . . . . . . . . . . 2B-1
Wheel Alignment Specifications . . . . . . . . . . . 2B-1
Diagnosis . . . . . . . . . . . . . . . . . . . . . . . . . . . 2B-2 Tire Diagnosis . . . . . . . . . . . . . . . . . . . . . . . . . 2B-2
Radial Tire Lead/Pull . . . . . . . . . . . . . . . . . . . 2B-3
Vibration Diagnosis . . . . . . . . . . . . . . . . . . . . . 2B-5
Maintenance and Repair . . . . . . . . . . . . . . . 2B-6
On-Vehicle Service . . . . . . . . . . . . . . . . . . . . . . 2B-6Wheel Alignment . . . . . . . . . . . . . . . . . . . . . . . 2B-6
General Description and System Operation . . . . . . . . . . . . . . . . . . . . . . . . . 2B-9
Four Wheel Alignment . . . . . . . . . . . . . . . . . . 2B-9
Toe . . . . . . . . . . . . . . . . . . . . . . . . . . . . . . . . . 2B-9
Caster . . . . . . . . . . . . . . . . . . . . . . . . . . . . . . . 2B-9
Camber . . . . . . . . . . . . . . . . . . . . . . . . . . . . . . 2B-9
Page 712 of 1574
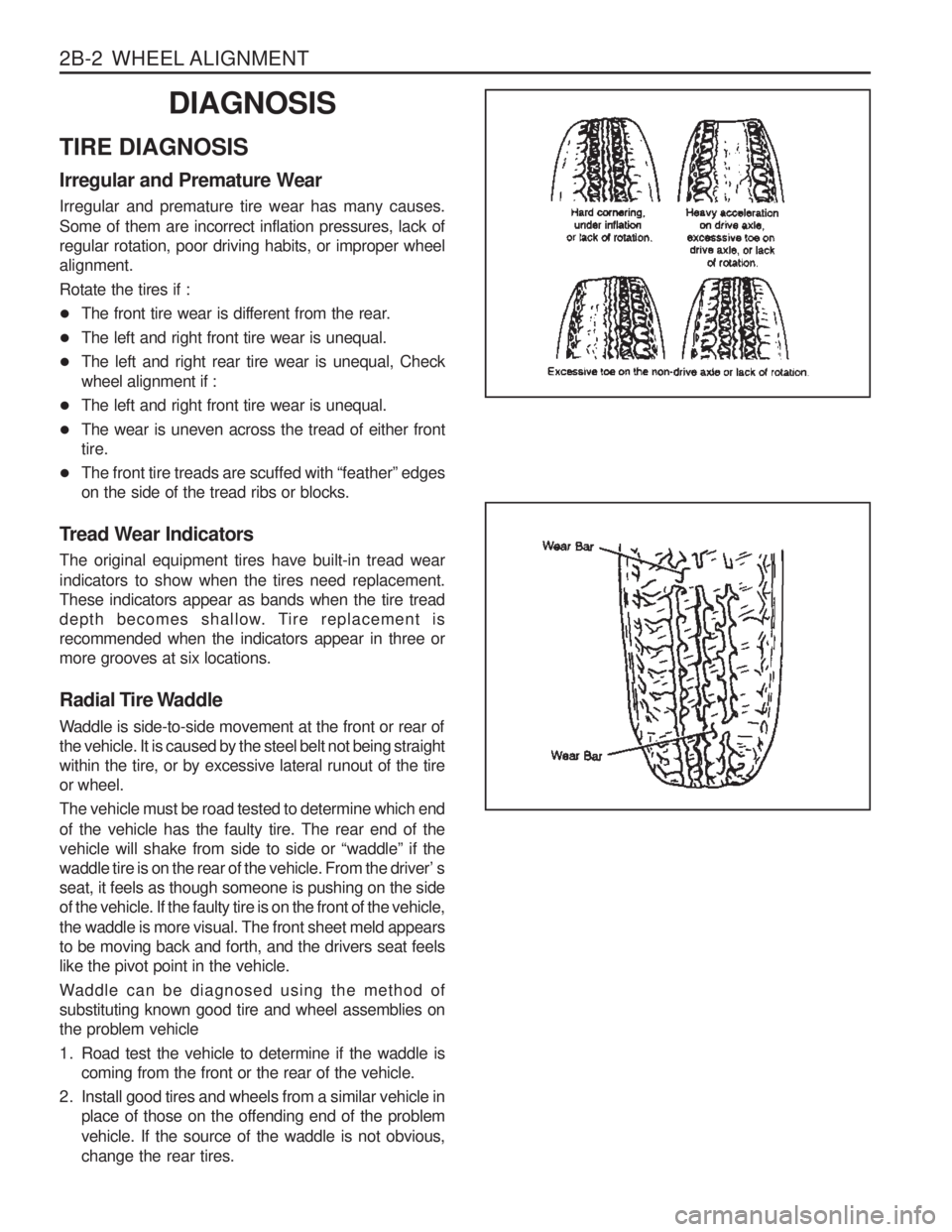
2B-2 WHEEL ALIGNMENT
DIAGNOSIS
TIRE DIAGNOSIS Irregular and Premature Wear Irregular and premature tire wear has many causes. Some of them are incorrect inflation pressures, lack of regular rotation, poor driving habits, or improper wheelalignment. Rotate the tires if :
The front tire wear is different from the rear.
The left and right front tire wear is unequal.
The left and right rear tire wear is unequal, Check wheel alignment if :
The left and right front tire wear is unequal.
The wear is uneven across the tread of either fronttire.
The front tire treads are scuffed with “feather” edgeson the side of the tread ribs or blocks.
Tread Wear Indicators The original equipment tires have built-in tread wear indicators to show when the tires need replacement. These indicators appear as bands when the tire tread
depth becomes shallow. Tire replacement isrecommended when the indicators appear in three ormore grooves at six locations.
Radial Tire Waddle
Waddle is side-to-side movement at the front or rear of the vehicle. It is caused by the steel belt not being straightwithin the tire, or by excessive lateral runout of the tireor wheel. The vehicle must be road tested to determine which end of the vehicle has the faulty tire. The rear end of the vehicle will shake from side to side or “waddle” if the
waddle tire is on the rear of the vehicle. From the driver’ sseat, it feels as though someone is pushing on the sideof the vehicle. If the faulty tire is on the front of the vehicle, the waddle is more visual. The front sheet meld appears to be moving back and forth, and the drivers seat feelslike the pivot point in the vehicle.
Waddle can be diagnosed using the method of substituting known good tire and wheel assemblies onthe problem vehicle
1. Road test the vehicle to determine if the waddle is coming from the front or the rear of the vehicle.
2. Install good tires and wheels from a similar vehicle in place of those on the offending end of the problem vehicle. If the source of the waddle is not obvious, change the rear tires.
Page 713 of 1574
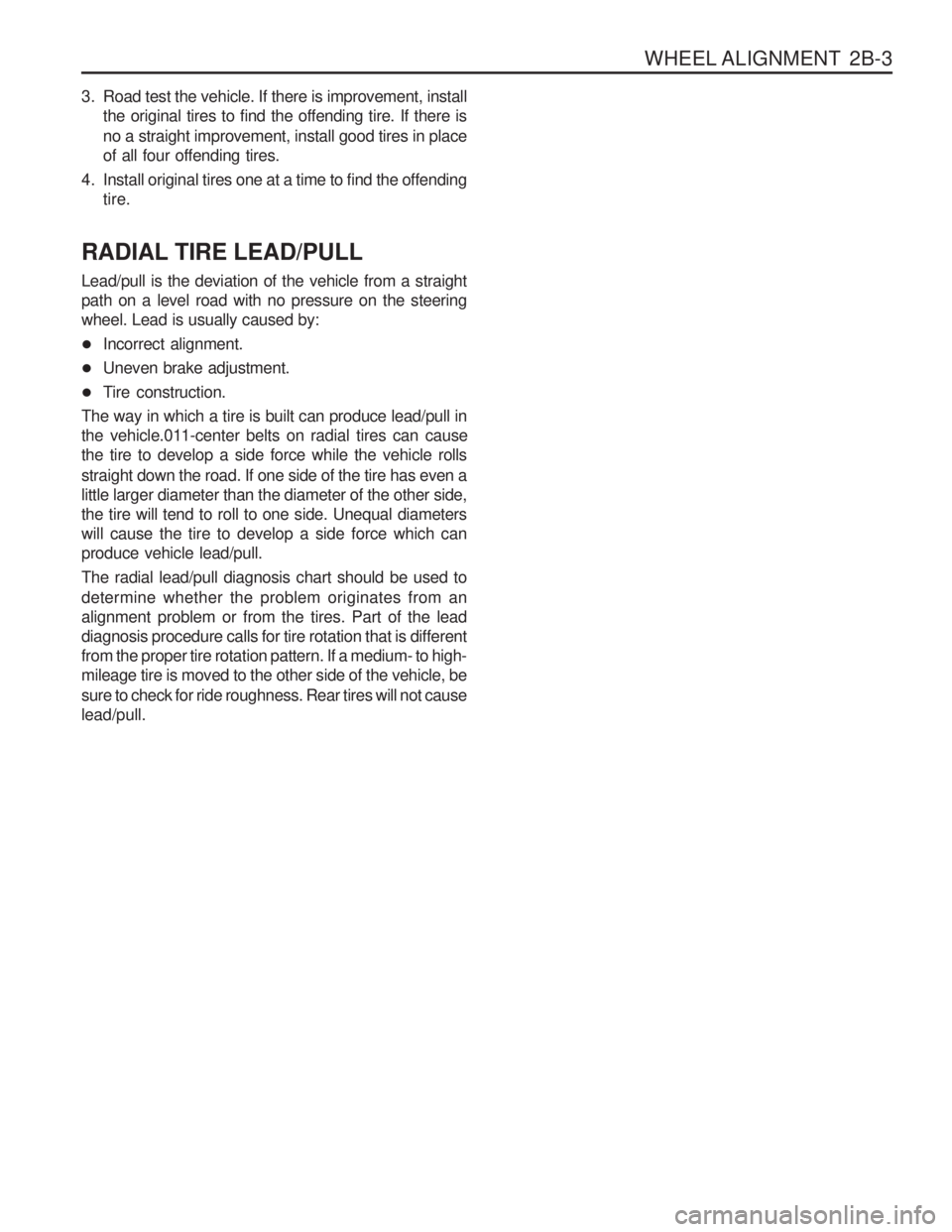
WHEEL ALIGNMENT 2B-3
3. Road test the vehicle. If there is improvement, installthe original tires to find the offending tire. If there is no a straight improvement, install good tires in place of all four offending tires.
4. Install original tires one at a time to find the offending tire.
RADIAL TIRE LEAD/PULL Lead/pull is the deviation of the vehicle from a straight path on a level road with no pressure on the steeringwheel. Lead is usually caused by:
Incorrect alignment.
Uneven brake adjustment.
Tire construction.
The way in which a tire is built can produce lead/pull in
the vehicle.011-center belts on radial tires can causethe tire to develop a side force while the vehicle rolls straight down the road. If one side of the tire has even a little larger diameter than the diameter of the other side,the tire will tend to roll to one side. Unequal diameterswill cause the tire to develop a side force which canproduce vehicle lead/pull. The radial lead/pull diagnosis chart should be used to determine whether the problem originates from an alignment problem or from the tires. Part of the leaddiagnosis procedure calls for tire rotation that is differentfrom the proper tire rotation pattern. If a medium- to high-mileage tire is moved to the other side of the vehicle, be sure to check for ride roughness. Rear tires will not cause lead/pull.
Page 714 of 1574
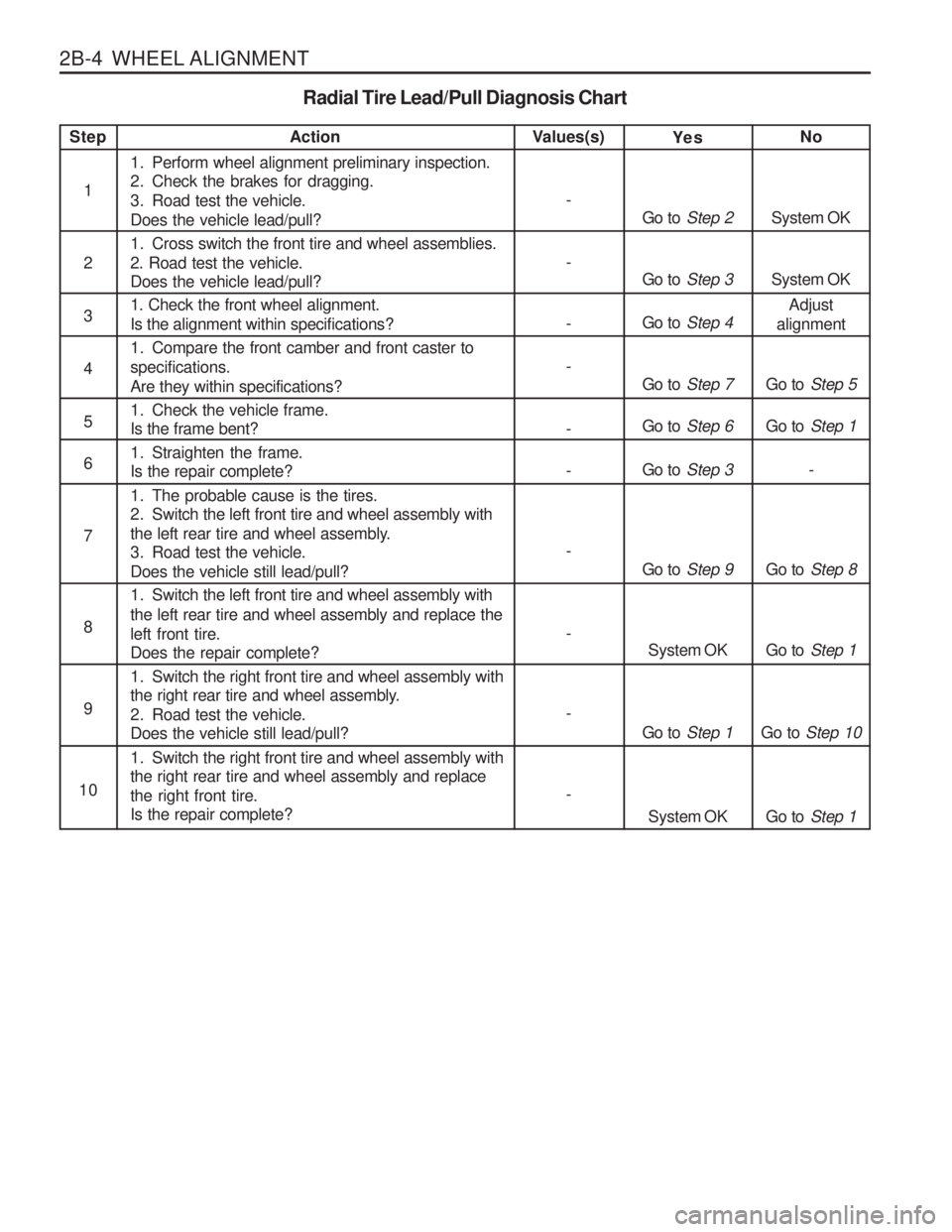
2B-4 WHEEL ALIGNMENT1. Perform wheel alignment preliminary inspection.
2. Check the brakes for dragging.
3. Road test the vehicle.Does the vehicle lead/pull?
1. Cross switch the front tire and wheel assemblies. 2. Road test the vehicle. Does the vehicle lead/pull? 1. Check the front wheel alignment. Is the alignment within specifications?
1. Compare the front camber and front caster to specifications.Are they within specifications?
1. Check the vehicle frame. Is the frame bent?
1. Straighten the frame. Is the repair complete?
1. The probable cause is the tires.
2. Switch the left front tire and wheel assembly with
the left rear tire and wheel assembly.
3. Road test the vehicle. Does the vehicle still lead/pull?
1. Switch the left front tire and wheel assembly with the left rear tire and wheel assembly and replace theleft front tire. Does the repair complete?
1. Switch the right front tire and wheel assembly with
the right rear tire and wheel assembly.
2. Road test the vehicle. Does the vehicle still lead/pull?
1. Switch the right front tire and wheel assembly with the right rear tire and wheel assembly and replace the right front tire. Is the repair complete? Action
Radial Tire Lead/Pull Diagnosis Chart
Step
1Values(s)
- Ye s
Go to Step 2
Go to Step 3
Go to Step 4
Go to Step 7
Go to Step 6
Go to Step 3
Go to Step 9
System OK
Go to Step 1
System OK No
System OK System OK Adjust
alignment
Go to Step 5
Go to Step 1
-
Go to Step 8
Go to Step 1
Go to Step 10
Go to Step 1
2 345 6 7 8 9
10 - - - - - - - - -