Page 401 of 557
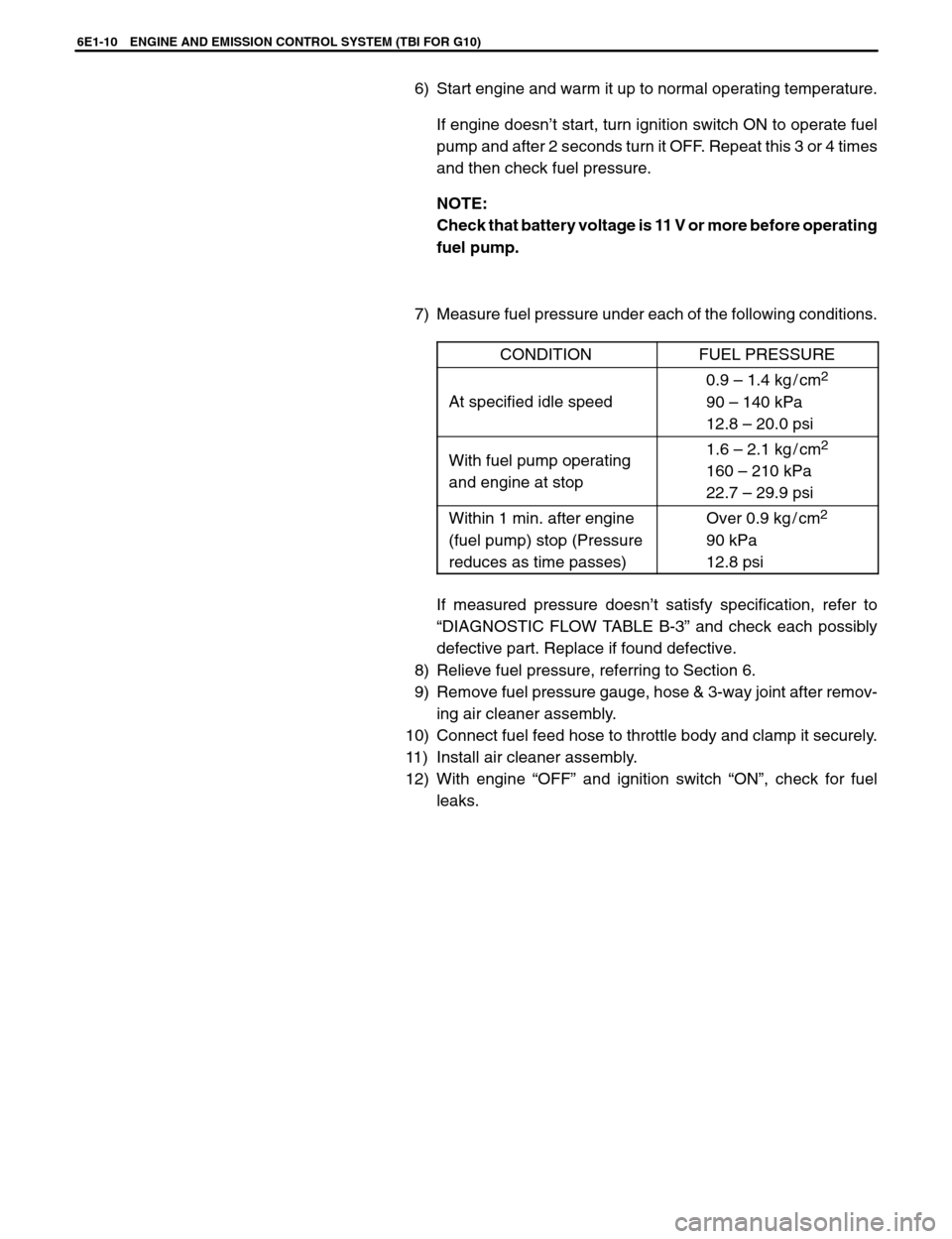
6E1-10 ENGINE AND EMISSION CONTROL SYSTEM (TBI FOR G10)
6) Start engine and warm it up to normal operating temperature.
If engine doesn’t start, turn ignition switch ON to operate fuel
pump and after 2 seconds turn it OFF. Repeat this 3 or 4 times
and then check fuel pressure.
NOTE:
Check that battery voltage is 11 V or more before operating
fuel pump.
7) Measure fuel pressure under each of the following conditions.
CONDITION
FUEL PRESSURE
At specified idle speed
0.9 – 1.4 kg / cm2
90 – 140 kPa
12.8 – 20.0 psi
With fuel pump operating
and engine at stop1.6 – 2.1 kg / cm2
160 – 210 kPa
22.7 – 29.9 psi
Within 1 min. after engine
(fuel pump) stop (Pressure
reduces as time passes)Over 0.9 kg / cm2
90 kPa
12.8 psi
If measured pressure doesn’t satisfy specification, refer to
“DIAGNOSTIC FLOW TABLE B-3” and check each possibly
defective part. Replace if found defective.
8) Relieve fuel pressure, referring to Section 6.
9) Remove fuel pressure gauge, hose & 3-way joint after remov-
ing air cleaner assembly.
10) Connect fuel feed hose to throttle body and clamp it securely.
11) Install air cleaner assembly.
12) With engine “OFF” and ignition switch “ON”, check for fuel
leaks.
Page 406 of 557
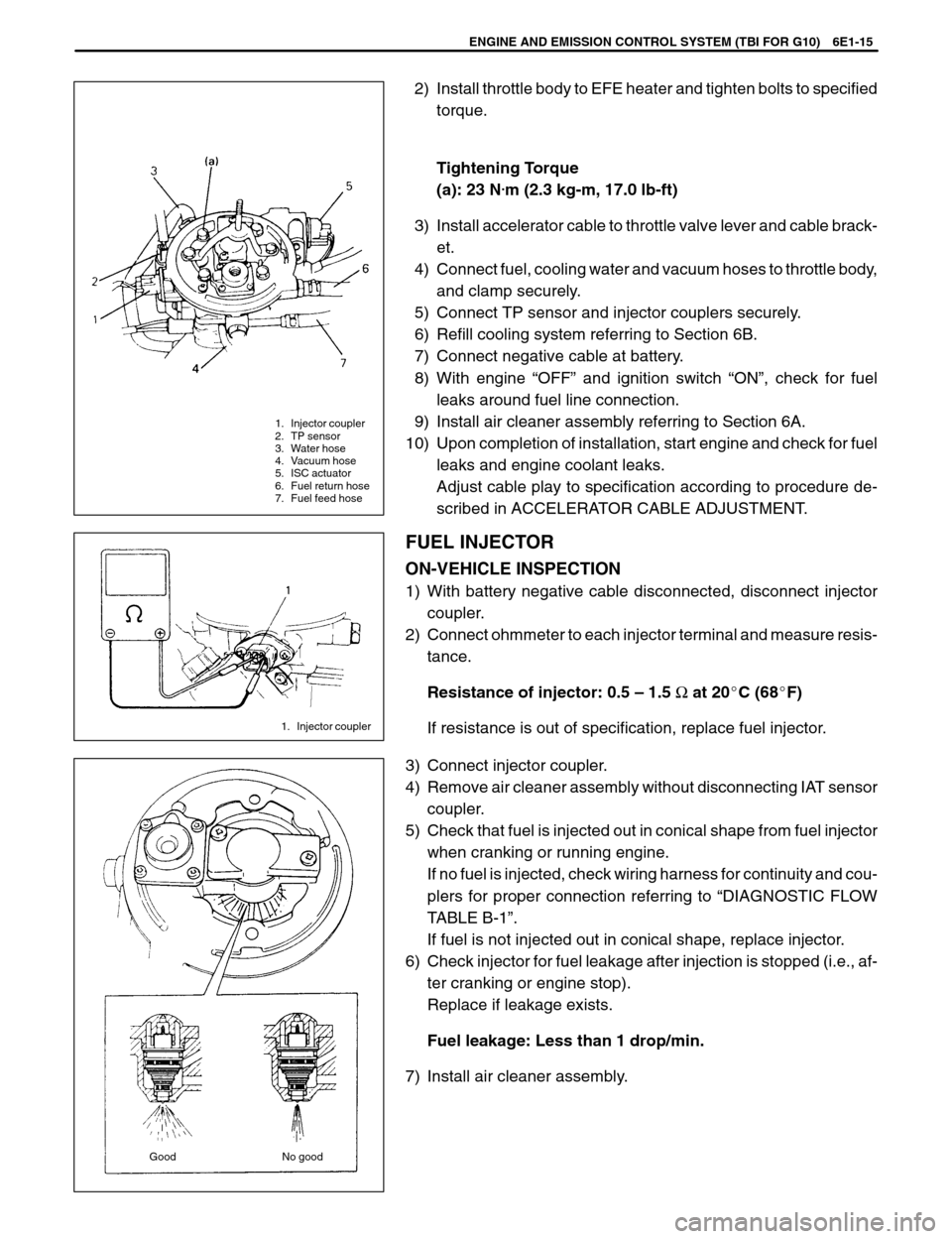
ENGINE AND EMISSION CONTROL SYSTEM (TBI FOR G10) 6E1-15
1. Injector coupler
2. TP sensor
3. Water hose
4. Vacuum hose
5. ISC actuator
6. Fuel return hose
7. Fuel feed hose
1. Injector coupler
Good No good
2) Install throttle body to EFE heater and tighten bolts to specified
torque.
Tightening Torque
(a): 23 N
.m (2.3 kg-m, 17.0 lb-ft)
3) Install accelerator cable to throttle valve lever and cable brack-
et.
4) Connect fuel, cooling water and vacuum hoses to throttle body,
and clamp securely.
5) Connect TP sensor and injector couplers securely.
6) Refill cooling system referring to Section 6B.
7) Connect negative cable at battery.
8) With engine “OFF” and ignition switch “ON”, check for fuel
leaks around fuel line connection.
9) Install air cleaner assembly referring to Section 6A.
10) Upon completion of installation, start engine and check for fuel
leaks and engine coolant leaks.
Adjust cable play to specification according to procedure de-
scribed in ACCELERATOR CABLE ADJUSTMENT.
FUEL INJECTOR
ON-VEHICLE INSPECTION
1) With battery negative cable disconnected, disconnect injector
coupler.
2) Connect ohmmeter to each injector terminal and measure resis-
tance.
Resistance of injector: 0.5 – 1.5 Ω at 20C (68F)
If resistance is out of specification, replace fuel injector.
3) Connect injector coupler.
4) Remove air cleaner assembly without disconnecting IAT sensor
coupler.
5) Check that fuel is injected out in conical shape from fuel injector
when cranking or running engine.
If no fuel is injected, check wiring harness for continuity and cou-
plers for proper connection referring to “DIAGNOSTIC FLOW
TABLE B-1”.
If fuel is not injected out in conical shape, replace injector.
6) Check injector for fuel leakage after injection is stopped (i.e., af-
ter cranking or engine stop).
Replace if leakage exists.
Fuel leakage: Less than 1 drop/min.
7) Install air cleaner assembly.
Page 408 of 557
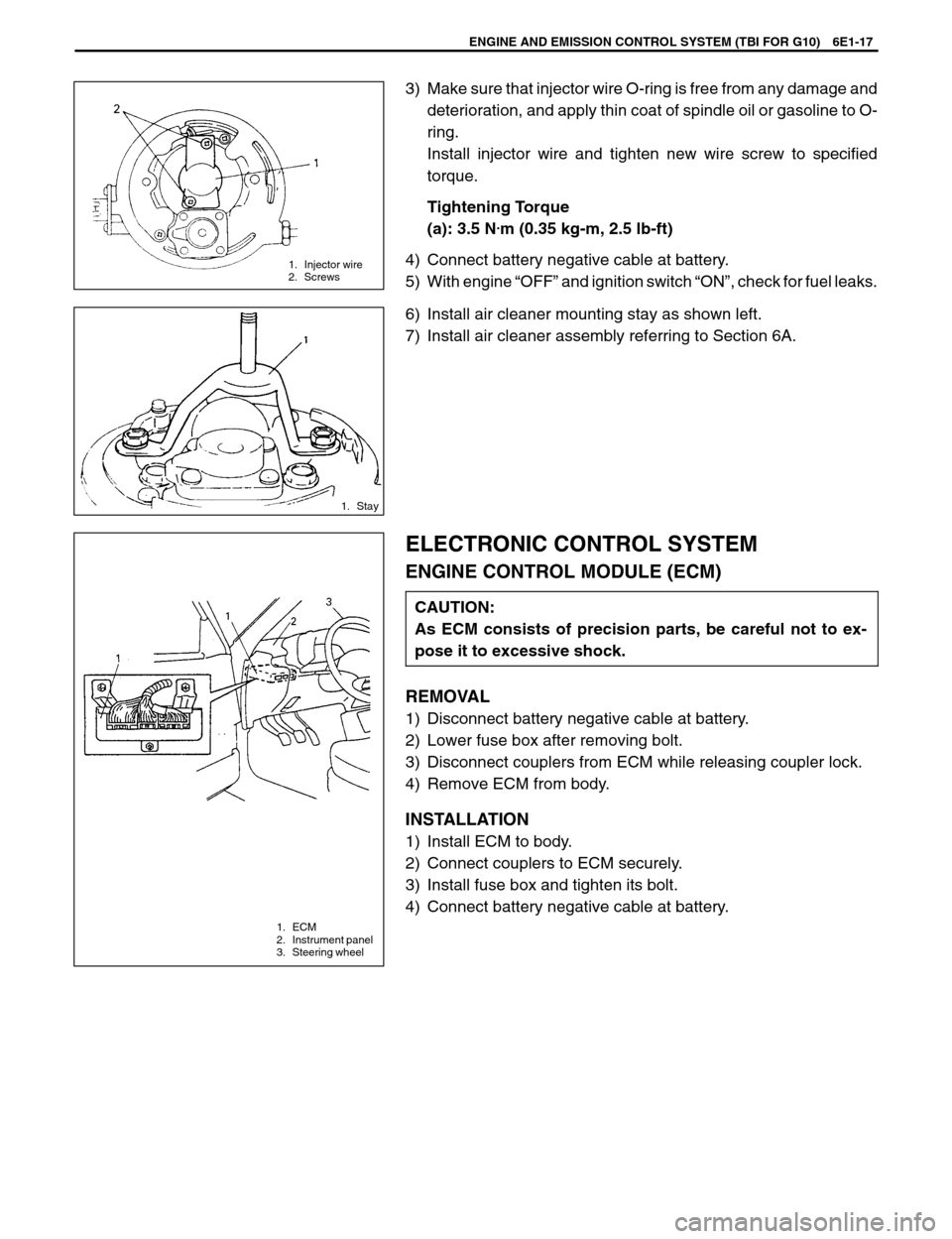
ENGINE AND EMISSION CONTROL SYSTEM (TBI FOR G10) 6E1-17
1. ECM
2. Instrument panel
3. Steering wheel
1. Injector wire
2. Screws
1. Stay
3) Make sure that injector wire O-ring is free from any damage and
deterioration, and apply thin coat of spindle oil or gasoline to O-
ring.
Install injector wire and tighten new wire screw to specified
torque.
Tightening Torque
(a): 3.5 N
.m (0.35 kg-m, 2.5 lb-ft)
4) Connect battery negative cable at battery.
5) With engine “OFF” and ignition switch “ON”, check for fuel leaks.
6) Install air cleaner mounting stay as shown left.
7) Install air cleaner assembly referring to Section 6A.
ELECTRONIC CONTROL SYSTEM
ENGINE CONTROL MODULE (ECM)
CAUTION:
As ECM consists of precision parts, be careful not to ex-
pose it to excessive shock.
REMOVAL
1) Disconnect battery negative cable at battery.
2) Lower fuse box after removing bolt.
3) Disconnect couplers from ECM while releasing coupler lock.
4) Remove ECM from body.
INSTALLATION
1) Install ECM to body.
2) Connect couplers to ECM securely.
3) Install fuse box and tighten its bolt.
4) Connect battery negative cable at battery.
Page 409 of 557
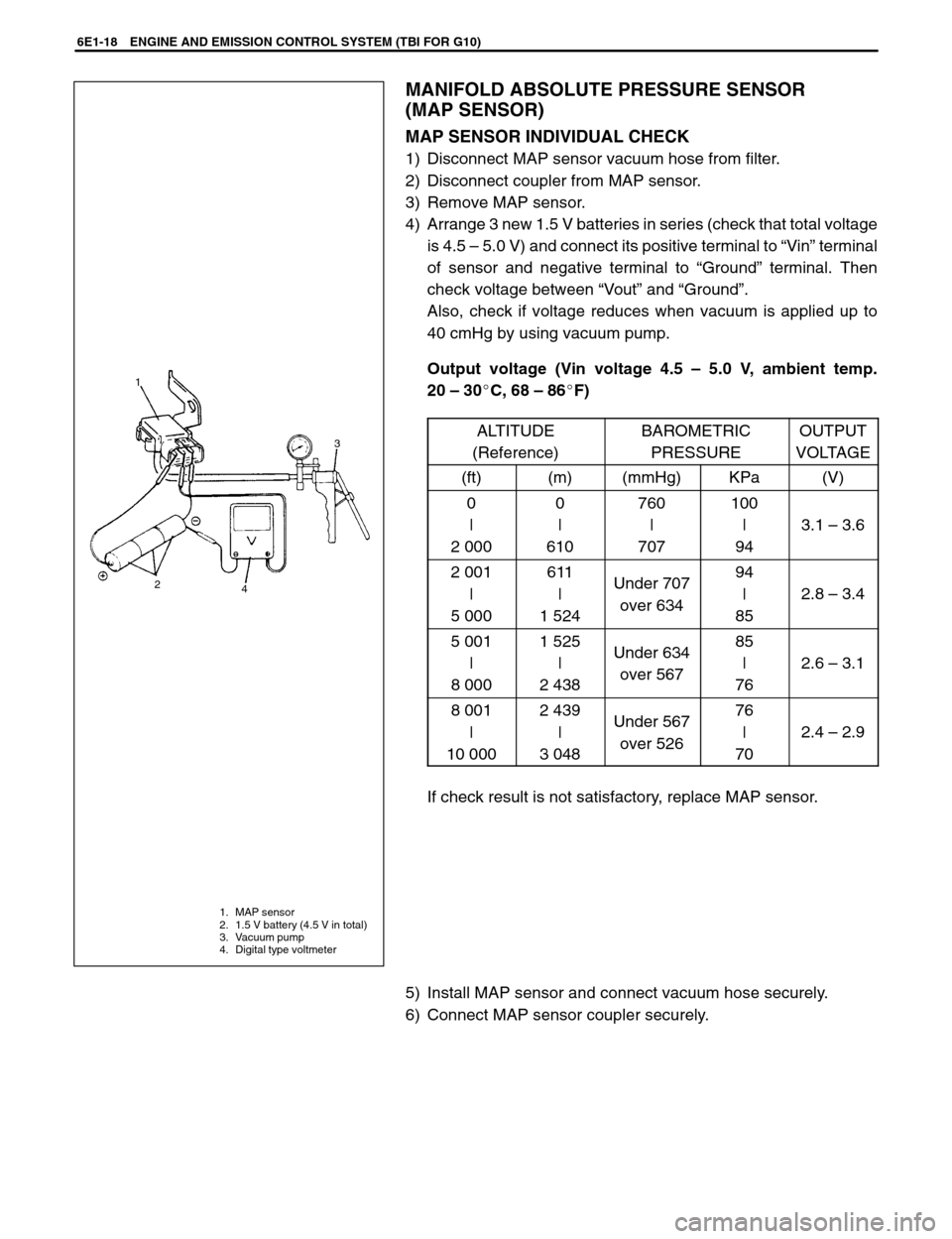
6E1-18 ENGINE AND EMISSION CONTROL SYSTEM (TBI FOR G10)
1
2
43
1. MAP sensor
2. 1.5 V battery (4.5 V in total)
3. Vacuum pump
4. Digital type voltmeter
MANIFOLD ABSOLUTE PRESSURE SENSOR
(MAP SENSOR)
MAP SENSOR INDIVIDUAL CHECK
1) Disconnect MAP sensor vacuum hose from filter.
2) Disconnect coupler from MAP sensor.
3) Remove MAP sensor.
4) Arrange 3 new 1.5 V batteries in series (check that total voltage
is 4.5 – 5.0 V) and connect its positive terminal to “Vin” terminal
of sensor and negative terminal to “Ground” terminal. Then
check voltage between “Vout” and “Ground”.
Also, check if voltage reduces when vacuum is applied up to
40 cmHg by using vacuum pump.
Output voltage (Vin voltage 4.5 – 5.0 V, ambient temp.
20 – 30C, 68 – 86F)
ALTITUDE
(Reference)
BAROMETRIC
PRESSUREOUTPUT
VOLTAGE
(ft)(m)(mmHg)KPa(V)
0
|
2 0000
|
610760
|
707100
|
94
3.1 – 3.6
2 001
|
5 000611
|
1 524Under 707
over 63494
|
85
2.8 – 3.4
5 001
|
8 0001 525
|
2 438Under 634
over 56785
|
76
2.6 – 3.1
8 001
|
10 0002 439
|
3 048Under 567
over 52676
|
70
2.4 – 2.9
If check result is not satisfactory, replace MAP sensor.
5) Install MAP sensor and connect vacuum hose securely.
6) Connect MAP sensor coupler securely.
Page 410 of 557
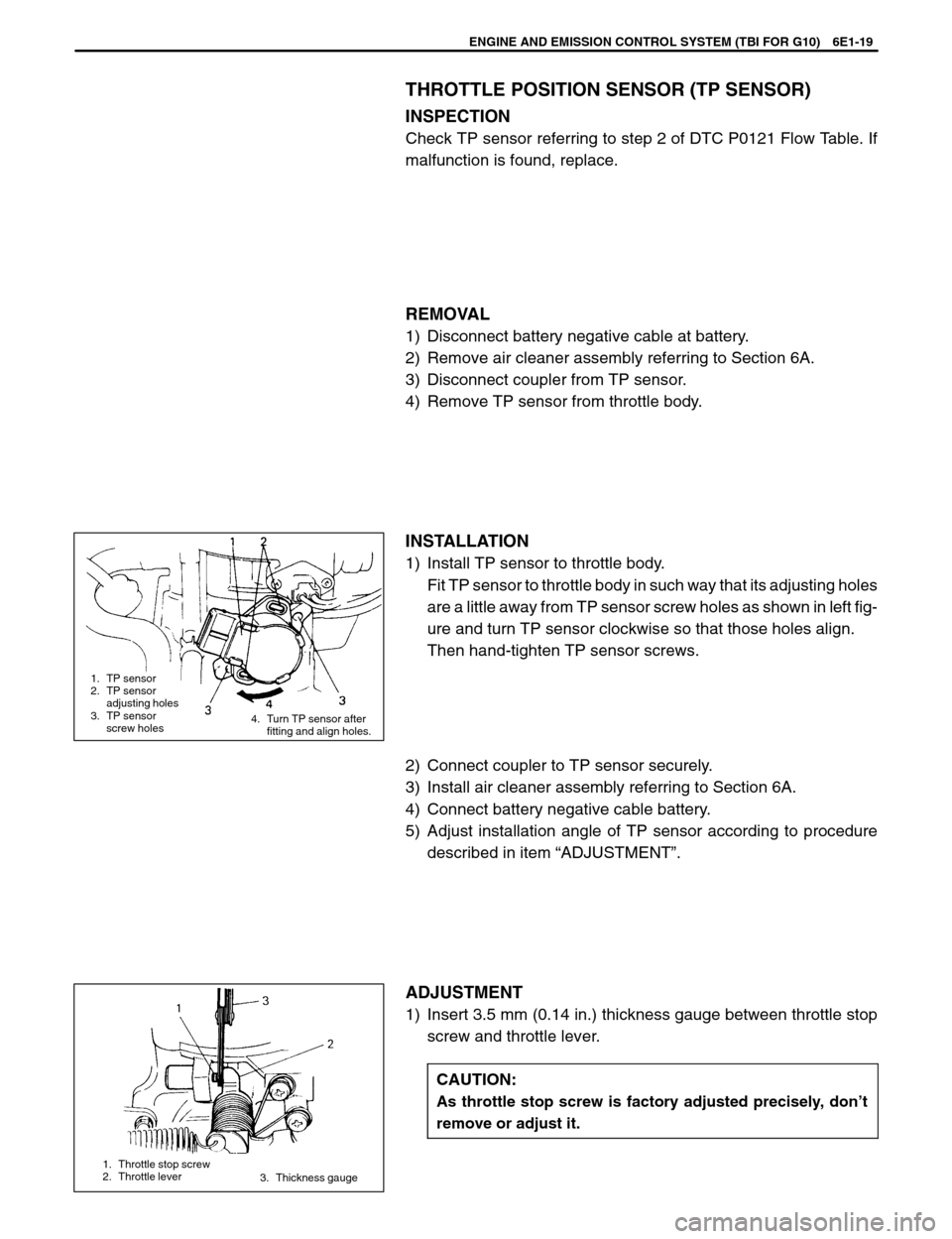
ENGINE AND EMISSION CONTROL SYSTEM (TBI FOR G10) 6E1-19
1. TP sensor
2. TP sensor
adjusting holes
3. TP sensor
screw holes4. Turn TP sensor after
fitting and align holes.
1. Throttle stop screw
2. Throttle lever
3. Thickness gauge
THROTTLE POSITION SENSOR (TP SENSOR)
INSPECTION
Check TP sensor referring to step 2 of DTC P0121 Flow Table. If
malfunction is found, replace.
REMOVAL
1) Disconnect battery negative cable at battery.
2) Remove air cleaner assembly referring to Section 6A.
3) Disconnect coupler from TP sensor.
4) Remove TP sensor from throttle body.
INSTALLATION
1) Install TP sensor to throttle body.
Fit TP sensor to throttle body in such way that its adjusting holes
are a little away from TP sensor screw holes as shown in left fig-
ure and turn TP sensor clockwise so that those holes align.
Then hand-tighten TP sensor screws.
2) Connect coupler to TP sensor securely.
3) Install air cleaner assembly referring to Section 6A.
4) Connect battery negative cable battery.
5) Adjust installation angle of TP sensor according to procedure
described in item “ADJUSTMENT”.
ADJUSTMENT
1) Insert 3.5 mm (0.14 in.) thickness gauge between throttle stop
screw and throttle lever.
CAUTION:
As throttle stop screw is factory adjusted precisely, don’t
remove or adjust it.
Page 411 of 557
6E1-20 ENGINE AND EMISSION CONTROL SYSTEM (TBI FOR G10)
1. Plunger
2. Throttle lever screw
2) Check to make sure that plunger of ISC actuator and throttle le-
ver screw are not in contact with each other. If they are, warm
up engine.
3) Loosen TP sensor screws.
a) Connect SUZUKI scan tool to DLC with ignition switch OFF.
b) Select “Data List” mode on SUZUKI scan tool.
c) Observe TP sensor voltage.
4) Turn TP sensor clockwise or counterclockwise and tighten TP
sensor screw at a position where voltage as specified below is
obtained.
TP sensor voltage when lever-to-stop
screw clearance is 3.5 mm (0.14 in.) : 0.98 – 1.02 V
Tightening Torque
(a): 2.0 N
.m (0.20 kg-m, 1.5 lb-ft)
5) Install ECM and connect couplers securely.
INTAKE AIR TEMPERATURE SENSOR (IAT SENSOR)
REMOVAL
1) Disconnect battery negative cable at battery.
2) Disconnect coupler from IAT sensor.
3) Remove IAT sensor and gasket from air cleaner case.
Page 412 of 557
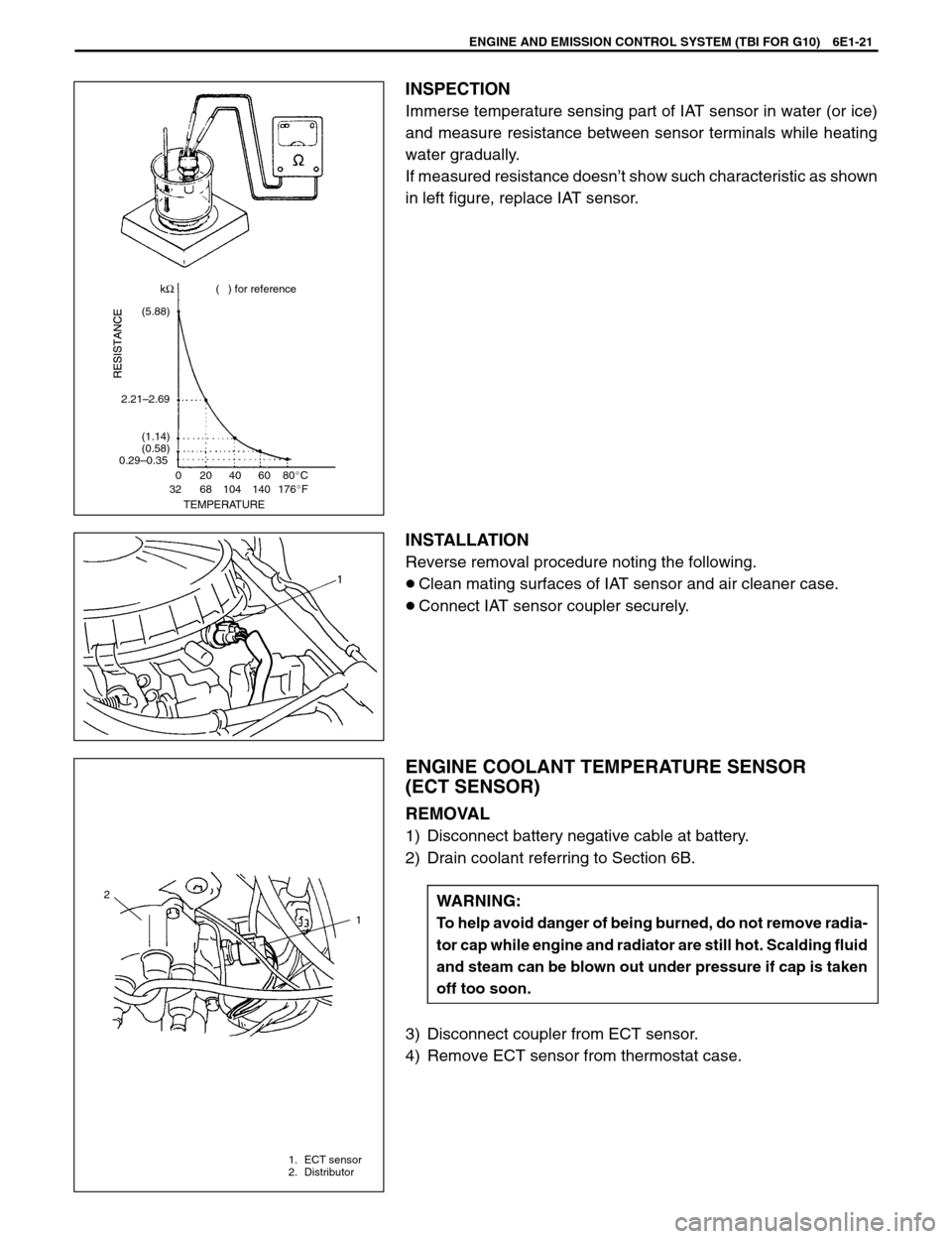
ENGINE AND EMISSION CONTROL SYSTEM (TBI FOR G10) 6E1-21
( ) for reference kΩ
TEMPERATURE 0
3220
6840
10460
14080C
176F (5.88)
2.21–2.69
(1.14)
(0.58)
0.29–0.35
2
1
1. ECT sensor
2. Distributor
INSPECTION
Immerse temperature sensing part of IAT sensor in water (or ice)
and measure resistance between sensor terminals while heating
water gradually.
If measured resistance doesn’t show such characteristic as shown
in left figure, replace IAT sensor.
INSTALLATION
Reverse removal procedure noting the following.
Clean mating surfaces of IAT sensor and air cleaner case.
Connect IAT sensor coupler securely.
ENGINE COOLANT TEMPERATURE SENSOR
(ECT SENSOR)
REMOVAL
1) Disconnect battery negative cable at battery.
2) Drain coolant referring to Section 6B.
WARNING:
To help avoid danger of being burned, do not remove radia-
tor cap while engine and radiator are still hot. Scalding fluid
and steam can be blown out under pressure if cap is taken
off too soon.
3) Disconnect coupler from ECT sensor.
4) Remove ECT sensor from thermostat case.
Page 413 of 557
6E1-22 ENGINE AND EMISSION CONTROL SYSTEM (TBI FOR G10)
( ) for reference kΩ
TEMPERATURE 0
3220
6840
10460
14080C
176F (5.74)
2.28–2.61
(1.15)
(0.584)
0.303–0.326
1. ECT sensor
2. Distributor
INSPECTION
Immerse temperature sensing part of ECT sensor in water (or ice)
and measure resistance between sensor terminals while heating
water gradually.
If measured resistance doesn’t show such characteristic as shown
in left figure, replace ECT sensor.
INSTALLATION
Reverse removal procedure noting the following.
Clean mating surfaces of ECT sensor and thermostat case.
Check O-ring for damage and replace if necessary.
Tighten ECT sensor to specified torque.
Tightening Torque
(a): 15 N
.m (1.5 kg-m, 11.0 lb-ft)
Connect coupler to ECT sensor securely.
Refill coolant referring to Section 6B.