Page 326 of 557
(a)
1. Oil pump
1. No. 1 bolts (short)
2. No. 2 bolts (long)
ENGINE MECHANICAL (G13B, 1-CAM 16-VALVES ENGINE) 6A1-31
4) Install rotor plate. Tighten 5 screw securely.
After installing plate, check to be sure that gears turn smoothly
by hand.
Tightening Torque
(a): 11 N
.m (1.1 kg-m, 8.0 lb-ft)
5) Apply engine oil to guide seal (3) and install guide seal and guide
(2).
INSTALLATION
1) Install two oil pump pins and oil pump gasket to cylinder block.
Use a new gasket.
2) To prevent oil seal lip from being damaged or upturned when
installing oil pump to crankshaft, fit special tool (Oil seal guide)
to crankshaft, and apply engine oil to special tool.
Special Tool
(A): 09926-18210
3) Install oil pump to cylinder block.
As there are 2 types of oil pump bolts, refer to figure for their cor-
rect use and tighten them to specified torque.
Tightening Torque
(a): 11 N
.m (1.1 kg-m, 8.0 lb-ft)
4) Install rubber seal between oil pump and water pump.
Page 334 of 557
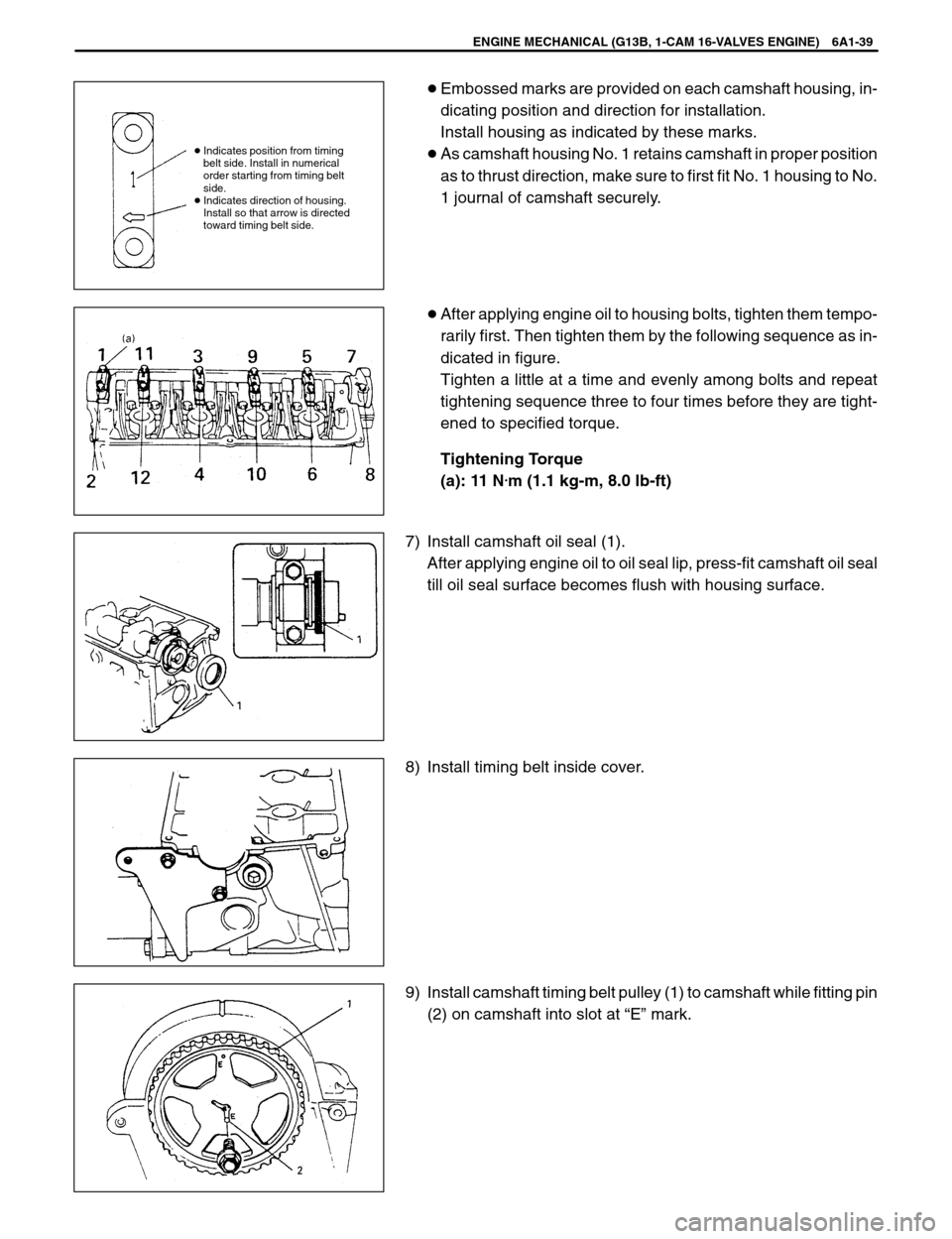
ENGINE MECHANICAL (G13B, 1-CAM 16-VALVES ENGINE) 6A1-39
Indicates position from timing
belt side. Install in numerical
order starting from timing belt
side.
Indicates direction of housing.
Install so that arrow is directed
toward timing belt side.
Embossed marks are provided on each camshaft housing, in-
dicating position and direction for installation.
Install housing as indicated by these marks.
As camshaft housing No. 1 retains camshaft in proper position
as to thrust direction, make sure to first fit No. 1 housing to No.
1 journal of camshaft securely.
After applying engine oil to housing bolts, tighten them tempo-
rarily first. Then tighten them by the following sequence as in-
dicated in figure.
Tighten a little at a time and evenly among bolts and repeat
tightening sequence three to four times before they are tight-
ened to specified torque.
Tightening Torque
(a): 11 N
.m (1.1 kg-m, 8.0 lb-ft)
7) Install camshaft oil seal (1).
After applying engine oil to oil seal lip, press-fit camshaft oil seal
till oil seal surface becomes flush with housing surface.
8) Install timing belt inside cover.
9) Install camshaft timing belt pulley (1) to camshaft while fitting pin
(2) on camshaft into slot at “E” mark.
Page 362 of 557
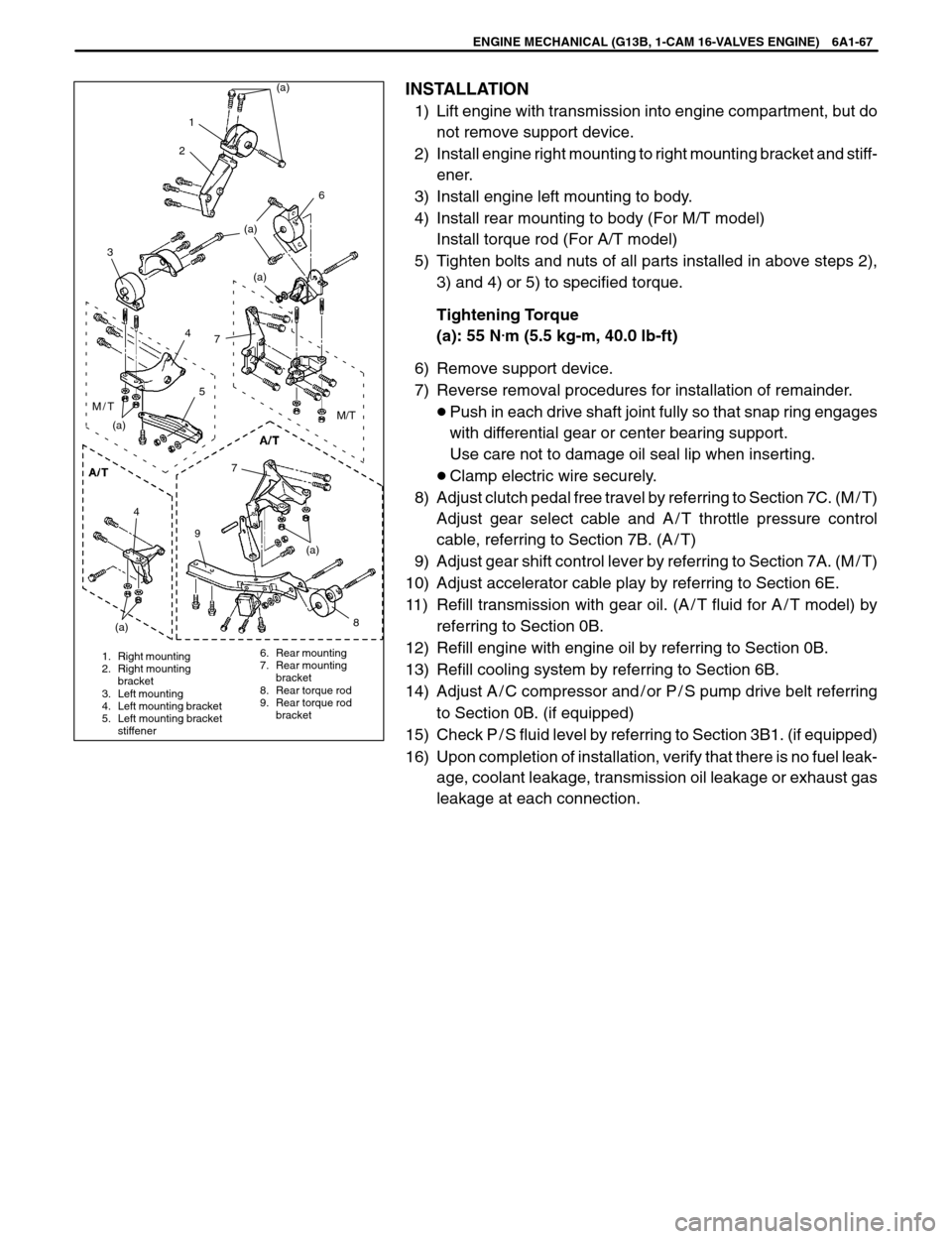
(a)
1
2
3
(a)
(a)
6
74
5
(a)
M/TM/T
9
(a)
4
7
(a)
8
1. Right mounting
2. Right mounting
bracket
3. Left mounting
4. Left mounting bracket
5. Left mounting bracket
stiffener6. Rear mounting
7. Rear mounting
bracket
8. Rear torque rod
9. Rear torque rod
bracket
ENGINE MECHANICAL (G13B, 1-CAM 16-VALVES ENGINE) 6A1-67
INSTALLATION
1) Lift engine with transmission into engine compartment, but do
not remove support device.
2) Install engine right mounting to right mounting bracket and stiff-
ener.
3) Install engine left mounting to body.
4) Install rear mounting to body (For M/T model)
Install torque rod (For A/T model)
5) Tighten bolts and nuts of all parts installed in above steps 2),
3) and 4) or 5) to specified torque.
Tightening Torque
(a): 55 N
.m (5.5 kg-m, 40.0 lb-ft)
6) Remove support device.
7) Reverse removal procedures for installation of remainder.
Push in each drive shaft joint fully so that snap ring engages
with differential gear or center bearing support.
Use care not to damage oil seal lip when inserting.
Clamp electric wire securely.
8) Adjust clutch pedal free travel by referring to Section 7C. (M / T)
Adjust gear select cable and A / T throttle pressure control
cable, referring to Section 7B. (A / T)
9) Adjust gear shift control lever by referring to Section 7A. (M / T)
10) Adjust accelerator cable play by referring to Section 6E.
11) Refill transmission with gear oil. (A / T fluid for A / T model) by
referring to Section 0B.
12) Refill engine with engine oil by referring to Section 0B.
13) Refill cooling system by referring to Section 6B.
14) Adjust A / C compressor and / or P / S pump drive belt referring
to Section 0B. (if equipped)
15) Check P / S fluid level by referring to Section 3B1. (if equipped)
16) Upon completion of installation, verify that there is no fuel leak-
age, coolant leakage, transmission oil leakage or exhaust gas
leakage at each connection.
Page 384 of 557
1. Radiator hose
2. Clamp
ENGINE COOLING 6B-7
ON-VEHICLE SERVICE
WARNING:
Check to make sure that engine coolant temperature is
cold before removing any part of cooling system.
Also be sure to disconnect negative cord from battery ter-
minal before removing any part.
COOLING WATER PIPES OR HOSES
REMOVAL
1) Drain cooling system.
2) To remove these pipes or hoses, loosen screw on each pipe or
hose clip and pull hose end off.
INSTALLATION
Install removed parts in reverse order of removal procedure, noting
the following.
Tighten each clamp bolt securely.
Refill cooling system with proper coolant, referring to description
on COOLANT of MAINTENANCE.
THERMOSTAT
REMOVAL
1) Disconnect negative cable at battery.
2) Drain cooling system and tighten drain plug.
3) Disconnect thermostat cap (1) from thermostat case (2).
Page 389 of 557
1. Fuel tank
2. Fuel pump and level gauge
3. Fuel filler cap
4. 2-way check valve
5. Breather hose
6. Fuel feed line
7. Fuel return line
8. Fuel vapor line
9. Fuel cut valve
10. Fuel tank pad
11. Fuel tank fixer bolt
: Tightening Torque
6C-2 ENGINE FUEL
ON-VEHICLE SERVICE
FUEL LINES
INSPECTION
Visually inspect fuel lines for evidence of fuel leakage, hose crack
and deterioration, or damage.
Make sure all clamps are secure.
Replace parts as needed.
FUEL TANK
REMOVAL
1) Relieve fuel pressure in fuel feed line according to procedure de-
scribed in Section 6.
2) Disconnect negative cable at battery.
3) Remove rear seat cushion referring to Section 9.
4) Disconnect connectors (1) of fuel tank wire harness.
5) Hoist vehicle.
6) Disconnect fuel filler hose (3) from fuel tank and breather hose
(2) from filler neck (1).
Page 391 of 557
6C-4 ENGINE FUEL
FUEL PUMP ASSEMBLY
REMOVAL
1) Remove fuel tank (1) from vehicle referring to “FUEL TANK” in
this section.
2) Disconnect fuel feed hose (2), fuel return hose (3) and breather
hose (4) from fuel pump assembly (5).
3) Remove fuel pump assembly from fuel tank by removing
screws.
INSPECTION
Check fuel pump assembly for damage.
Check fuel suction filter (1) for evidence of dirt and contamination.
If present, replace or clean and check for presence of dirt in fuel
tank.
INSTALLATION
Reverse removal procedure for installation noting the followings.
Use new gasket.
Clamp hoses securely.
Page 399 of 557
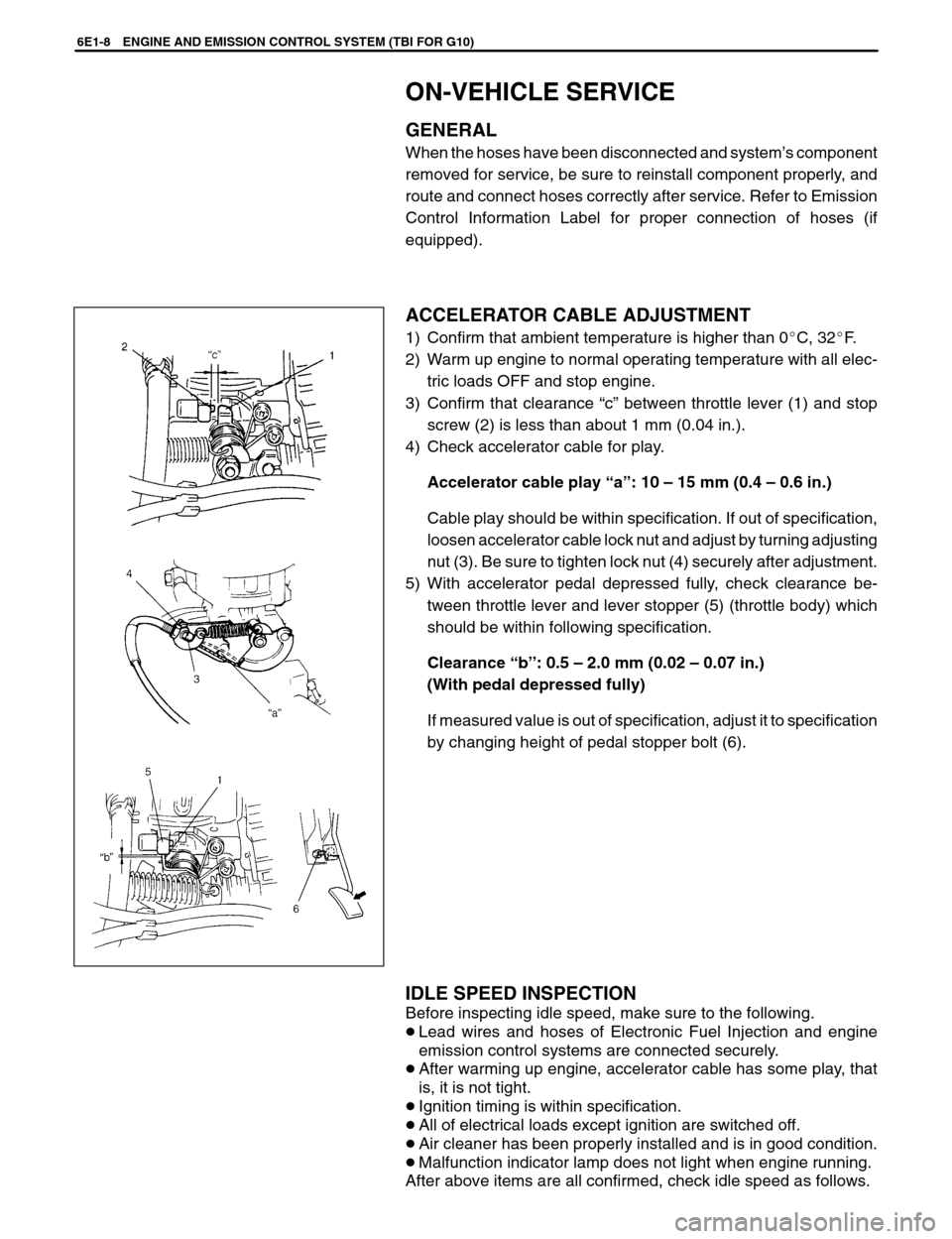
6E1-8 ENGINE AND EMISSION CONTROL SYSTEM (TBI FOR G10)
ON-VEHICLE SERVICE
GENERAL
When the hoses have been disconnected and system’s component
removed for service, be sure to reinstall component properly, and
route and connect hoses correctly after service. Refer to Emission
Control Information Label for proper connection of hoses (if
equipped).
ACCELERATOR CABLE ADJUSTMENT
1) Confirm that ambient temperature is higher than 0C, 32F.
2) Warm up engine to normal operating temperature with all elec-
tric loads OFF and stop engine.
3) Confirm that clearance “c” between throttle lever (1) and stop
screw (2) is less than about 1 mm (0.04 in.).
4) Check accelerator cable for play.
Accelerator cable play “a”: 10 – 15 mm (0.4 – 0.6 in.)
Cable play should be within specification. If out of specification,
loosen accelerator cable lock nut and adjust by turning adjusting
nut (3). Be sure to tighten lock nut (4) securely after adjustment.
5) With accelerator pedal depressed fully, check clearance be-
tween throttle lever and lever stopper (5) (throttle body) which
should be within following specification.
Clearance “b”: 0.5 – 2.0 mm (0.02 – 0.07 in.)
(With pedal depressed fully)
If measured value is out of specification, adjust it to specification
by changing height of pedal stopper bolt (6).
IDLE SPEED INSPECTION
Before inspecting idle speed, make sure to the following.
Lead wires and hoses of Electronic Fuel Injection and engine
emission control systems are connected securely.
After warming up engine, accelerator cable has some play, that
is, it is not tight.
Ignition timing is within specification.
All of electrical loads except ignition are switched off.
Air cleaner has been properly installed and is in good condition.
Malfunction indicator lamp does not light when engine running.
After above items are all confirmed, check idle speed as follows.
Page 400 of 557
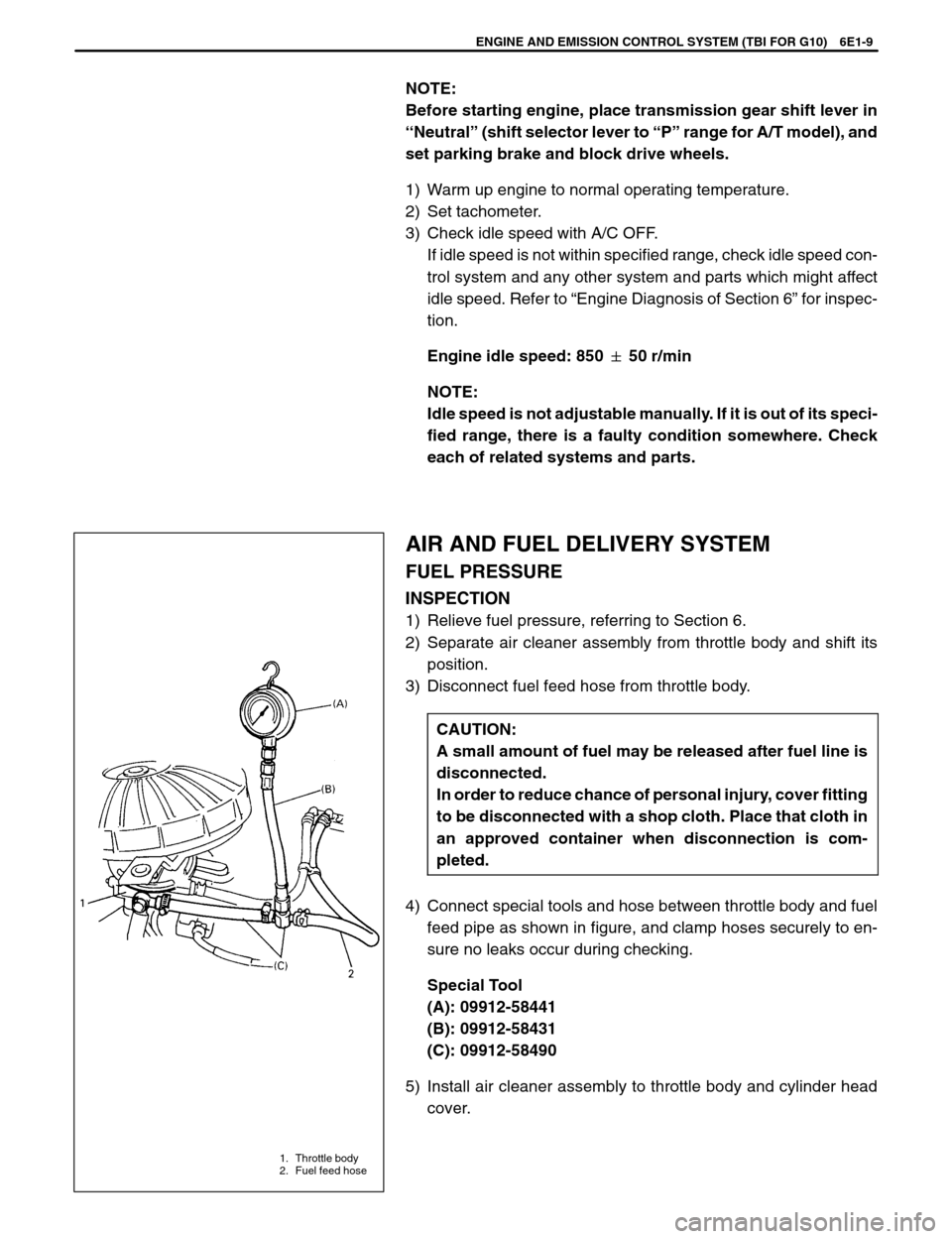
ENGINE AND EMISSION CONTROL SYSTEM (TBI FOR G10) 6E1-9
1. Throttle body
2. Fuel feed hose
NOTE:
Before starting engine, place transmission gear shift lever in
“Neutral” (shift selector lever to “P” range for A/T model), and
set parking brake and block drive wheels.
1) Warm up engine to normal operating temperature.
2) Set tachometer.
3) Check idle speed with A/C OFF.
If idle speed is not within specified range, check idle speed con-
trol system and any other system and parts which might affect
idle speed. Refer to “Engine Diagnosis of Section 6” for inspec-
tion.
Engine idle speed: 850 50 r/min
NOTE:
Idle speed is not adjustable manually. If it is out of its speci-
fied range, there is a faulty condition somewhere. Check
each of related systems and parts.
AIR AND FUEL DELIVERY SYSTEM
FUEL PRESSURE
INSPECTION
1) Relieve fuel pressure, referring to Section 6.
2) Separate air cleaner assembly from throttle body and shift its
position.
3) Disconnect fuel feed hose from throttle body.
CAUTION:
A small amount of fuel may be released after fuel line is
disconnected.
In order to reduce chance of personal injury, cover fitting
to be disconnected with a shop cloth. Place that cloth in
an approved container when disconnection is com-
pleted.
4) Connect special tools and hose between throttle body and fuel
feed pipe as shown in figure, and clamp hoses securely to en-
sure no leaks occur during checking.
Special Tool
(A): 09912-58441
(B): 09912-58431
(C): 09912-58490
5) Install air cleaner assembly to throttle body and cylinder head
cover.