Page 261 of 557
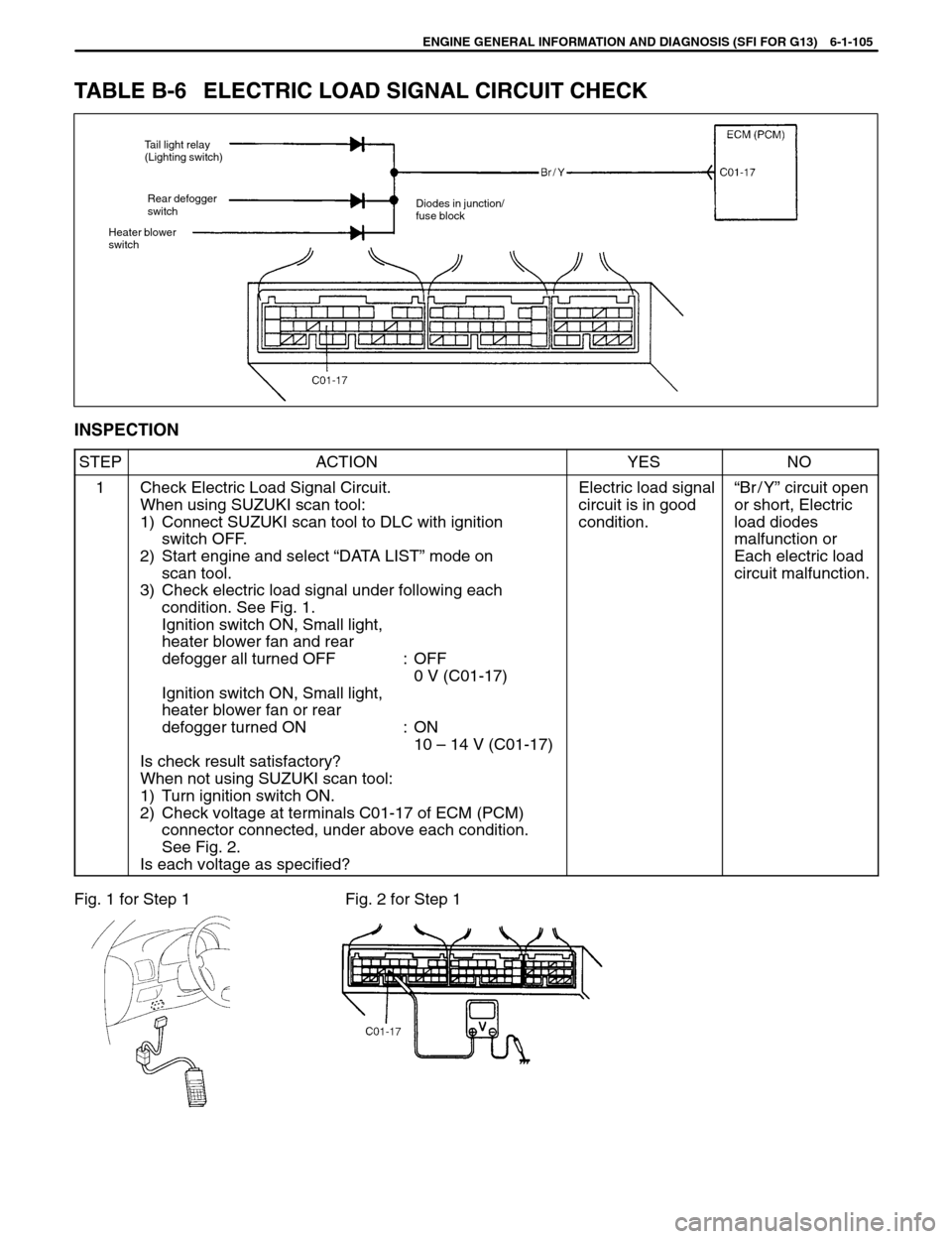
ENGINE GENERAL INFORMATION AND DIAGNOSIS (SFI FOR G13) 6-1-105
Heater blower
switchRear defogger
switch Tail light relay
(Lighting switch)
Diodes in junction/
fuse block
Fig. 1 for Step 1 Fig. 2 for Step 1
TABLE B-6 ELECTRIC LOAD SIGNAL CIRCUIT CHECK
INSPECTION
STEPACTIONYESNO
1Check Electric Load Signal Circuit.
When using SUZUKI scan tool:
1) Connect SUZUKI scan tool to DLC with ignition
switch OFF.
2) Start engine and select “DATA LIST” mode on
scan tool.
3) Check electric load signal under following each
condition. See Fig. 1.
Ignition switch ON, Small light,
heater blower fan and rear
defogger all turned OFF : OFF
0 V (C01-17)
Ignition switch ON, Small light,
heater blower fan or rear
defogger turned ON : ON
10 – 14 V (C01-17)
Is check result satisfactory?
When not using SUZUKI scan tool:
1) Turn ignition switch ON.
2) Check voltage at terminals C01-17 of ECM (PCM)
connector connected, under above each condition.
See Fig. 2.
Is each voltage as specified?Electric load signal
circuit is in good
condition.“Br / Y” circuit open
or short, Electric
load diodes
malfunction or
Each electric load
circuit malfunction.
Page 262 of 557
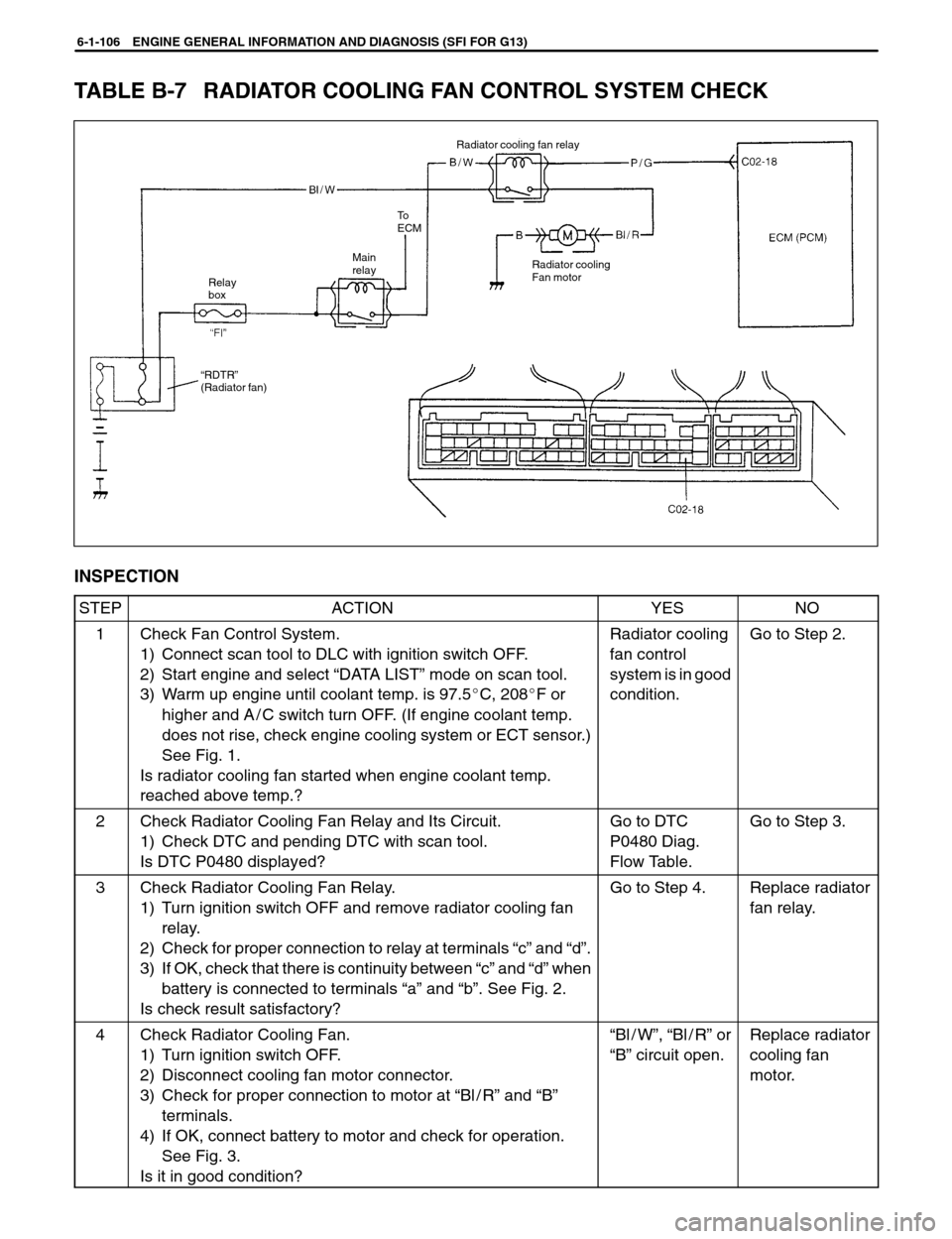
6-1-106 ENGINE GENERAL INFORMATION AND DIAGNOSIS (SFI FOR G13)
Radiator cooling fan relay
To
ECM
Main
relay
Relay
box
“RDTR”
(Radiator fan)Radiator cooling
Fan motor
TABLE B-7 RADIATOR COOLING FAN CONTROL SYSTEM CHECK
INSPECTION
STEPACTIONYESNO
1Check Fan Control System.
1) Connect scan tool to DLC with ignition switch OFF.
2) Start engine and select “DATA LIST” mode on scan tool.
3) Warm up engine until coolant temp. is 97.5C, 208F or
higher and A / C switch turn OFF. (If engine coolant temp.
does not rise, check engine cooling system or ECT sensor.)
See Fig. 1.
Is radiator cooling fan started when engine coolant temp.
reached above temp.?Radiator cooling
fan control
system is in good
condition.Go to Step 2.
2Check Radiator Cooling Fan Relay and Its Circuit.
1) Check DTC and pending DTC with scan tool.
Is DTC P0480 displayed?Go to DTC
P0480 Diag.
Flow Table.Go to Step 3.
3Check Radiator Cooling Fan Relay.
1) Turn ignition switch OFF and remove radiator cooling fan
relay.
2) Check for proper connection to relay at terminals “c” and “d”.
3) If OK, check that there is continuity between “c” and “d” when
battery is connected to terminals “a” and “b”. See Fig. 2.
Is check result satisfactory?Go to Step 4.Replace radiator
fan relay.
4Check Radiator Cooling Fan.
1) Turn ignition switch OFF.
2) Disconnect cooling fan motor connector.
3) Check for proper connection to motor at “Bl / R” and “B”
terminals.
4) If OK, connect battery to motor and check for operation.
See Fig. 3.
Is it in good condition?“Bl / W”, “Bl / R” or
“B” circuit open.Replace radiator
cooling fan
motor.
Page 263 of 557
ENGINE GENERAL INFORMATION AND DIAGNOSIS (SFI FOR G13) 6-1-107
Fig. 1 for Step 1 Fig. 2 for Step 3
Fig. 3 for Step 4When using SUZUKI scan tool:
1. Radiator cooling fan relay
1. Battery
2. Radiator fan motor coupler
Page 264 of 557
6-1-108 ENGINE GENERAL INFORMATION AND DIAGNOSIS (SFI FOR G13)
09917-47910
Vacuum pump gauge09930-88530
Injector test lead09931-76011
SUZUKI scan tool (Tech 1 A) kit
Mass storage cartridge09931-76030
16 / 14 pin DLC cable1. Storage case
2. Operator’s manual
3. Tech 1 A
4. DLC cable (14 / 26 pin,
09931-76040)
5. Test lead / probe
6. Power source cable
7. DLC cable adaptor
8. Self-test adaptor -1. Pressure gauge
09912-58441
-2. Pressure hose
09912-58431
-3. 3-way joint & hose
09912-58490
-4. Checking tool set
09912-58421
4-1. Tool body & washer
4-2. Body plug
4-3. Body attachment-1
4-4. Holder
4-5. Return hose & clamp
4-6. Body attachment-2 & washer
4-7. Hose attachment-1
4-8. Hose attachment-2
-5. Checking tool plate
09912-57610
SPECIAL TOOLS
Page 265 of 557
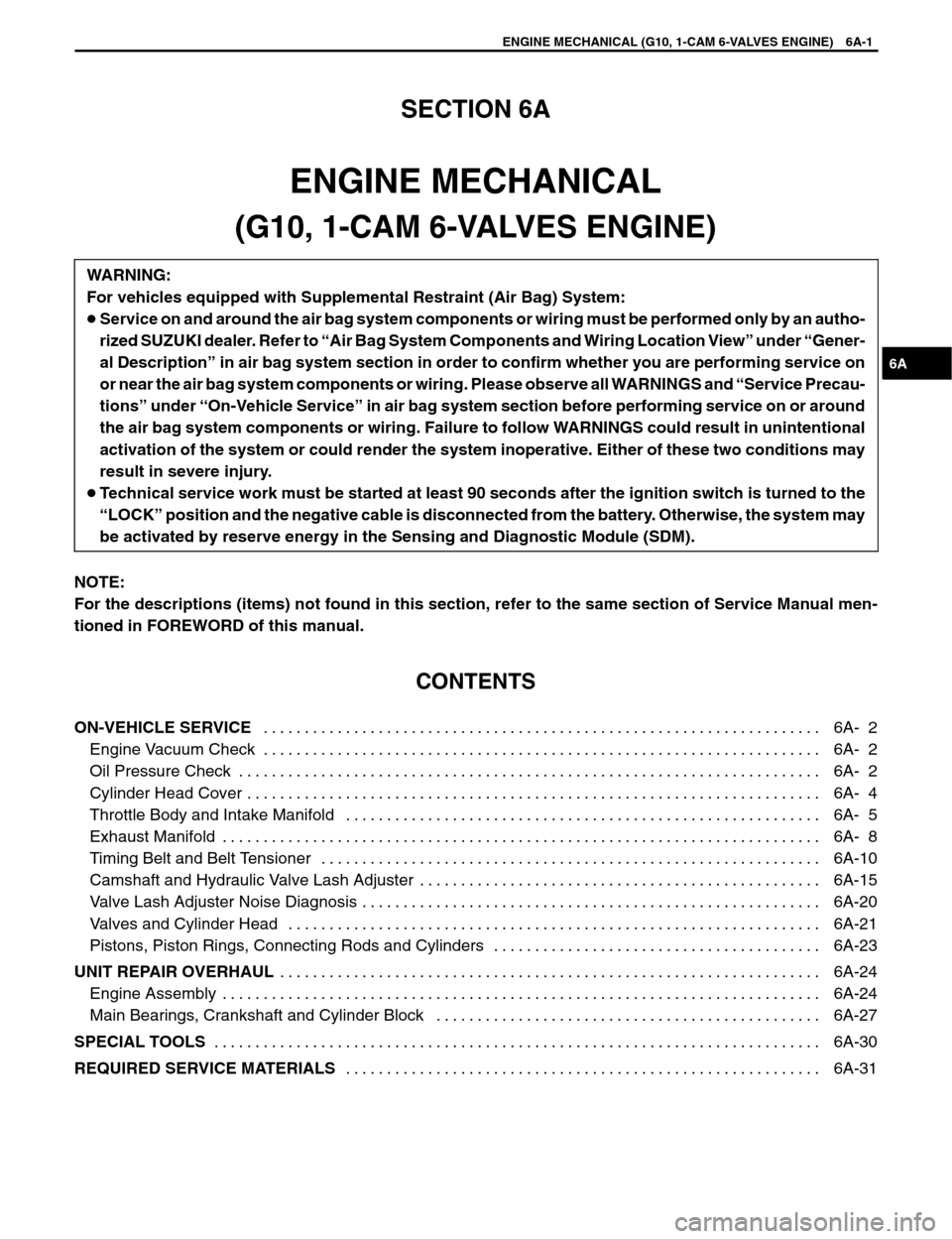
6A
ENGINE MECHANICAL (G10, 1-CAM 6-VALVES ENGINE) 6A-1
SECTION 6A
ENGINE MECHANICAL
(G10, 1-CAM 6-VALVES ENGINE)
WARNING:
For vehicles equipped with Supplemental Restraint (Air Bag) System:
Service on and around the air bag system components or wiring must be performed only by an autho-
rized SUZUKI dealer. Refer to “Air Bag System Components and Wiring Location View” under “Gener-
al Description” in air bag system section in order to confirm whether you are performing service on
or near the air bag system components or wiring. Please observe all WARNINGS and “Service Precau-
tions” under “On-Vehicle Service” in air bag system section before performing service on or around
the air bag system components or wiring. Failure to follow WARNINGS could result in unintentional
activation of the system or could render the system inoperative. Either of these two conditions may
result in severe injury.
Technical service work must be started at least 90 seconds after the ignition switch is turned to the
“LOCK” position and the negative cable is disconnected from the battery. Otherwise, the system may
be activated by reserve energy in the Sensing and Diagnostic Module (SDM).
NOTE:
For the descriptions (items) not found in this section, refer to the same section of Service Manual men-
tioned in FOREWORD of this manual.
CONTENTS
ON-VEHICLE SERVICE6A- 2 . . . . . . . . . . . . . . . . . . . . . . . . . . . . . . . . . . . . . . . . . . . . . . . . . . . . . . . . . . . . . . . . . . . .
Engine Vacuum Check6A- 2 . . . . . . . . . . . . . . . . . . . . . . . . . . . . . . . . . . . . . . . . . . . . . . . . . . . . . . . . . . . . . . . . . . . .
Oil Pressure Check6A- 2 . . . . . . . . . . . . . . . . . . . . . . . . . . . . . . . . . . . . . . . . . . . . . . . . . . . . . . . . . . . . . . . . . . . . . . .
Cylinder Head Cover6A- 4 . . . . . . . . . . . . . . . . . . . . . . . . . . . . . . . . . . . . . . . . . . . . . . . . . . . . . . . . . . . . . . . . . . . . . .
Throttle Body and Intake Manifold 6A- 5. . . . . . . . . . . . . . . . . . . . . . . . . . . . . . . . . . . . . . . . . . . . . . . . . . . . . . . . . .
Exhaust Manifold6A- 8 . . . . . . . . . . . . . . . . . . . . . . . . . . . . . . . . . . . . . . . . . . . . . . . . . . . . . . . . . . . . . . . . . . . . . . . . .
Timing Belt and Belt Tensioner 6A-10. . . . . . . . . . . . . . . . . . . . . . . . . . . . . . . . . . . . . . . . . . . . . . . . . . . . . . . . . . . . .
Camshaft and Hydraulic Valve Lash Adjuster 6A-15. . . . . . . . . . . . . . . . . . . . . . . . . . . . . . . . . . . . . . . . . . . . . . . . .
Valve Lash Adjuster Noise Diagnosis 6A-20. . . . . . . . . . . . . . . . . . . . . . . . . . . . . . . . . . . . . . . . . . . . . . . . . . . . . . . .
Valves and Cylinder Head6A-21 . . . . . . . . . . . . . . . . . . . . . . . . . . . . . . . . . . . . . . . . . . . . . . . . . . . . . . . . . . . . . . . . .
Pistons, Piston Rings, Connecting Rods and Cylinders 6A-23. . . . . . . . . . . . . . . . . . . . . . . . . . . . . . . . . . . . . . . .
UNIT REPAIR OVERHAUL6A-24 . . . . . . . . . . . . . . . . . . . . . . . . . . . . . . . . . . . . . . . . . . . . . . . . . . . . . . . . . . . . . . . . . .
Engine Assembly6A-24 . . . . . . . . . . . . . . . . . . . . . . . . . . . . . . . . . . . . . . . . . . . . . . . . . . . . . . . . . . . . . . . . . . . . . . . . .
Main Bearings, Crankshaft and Cylinder Block 6A-27. . . . . . . . . . . . . . . . . . . . . . . . . . . . . . . . . . . . . . . . . . . . . . .
SPECIAL TOOLS6A-30 . . . . . . . . . . . . . . . . . . . . . . . . . . . . . . . . . . . . . . . . . . . . . . . . . . . . . . . . . . . . . . . . . . . . . . . . . .
REQUIRED SERVICE MATERIALS6A-31 . . . . . . . . . . . . . . . . . . . . . . . . . . . . . . . . . . . . . . . . . . . . . . . . . . . . . . . . . .
Page 266 of 557
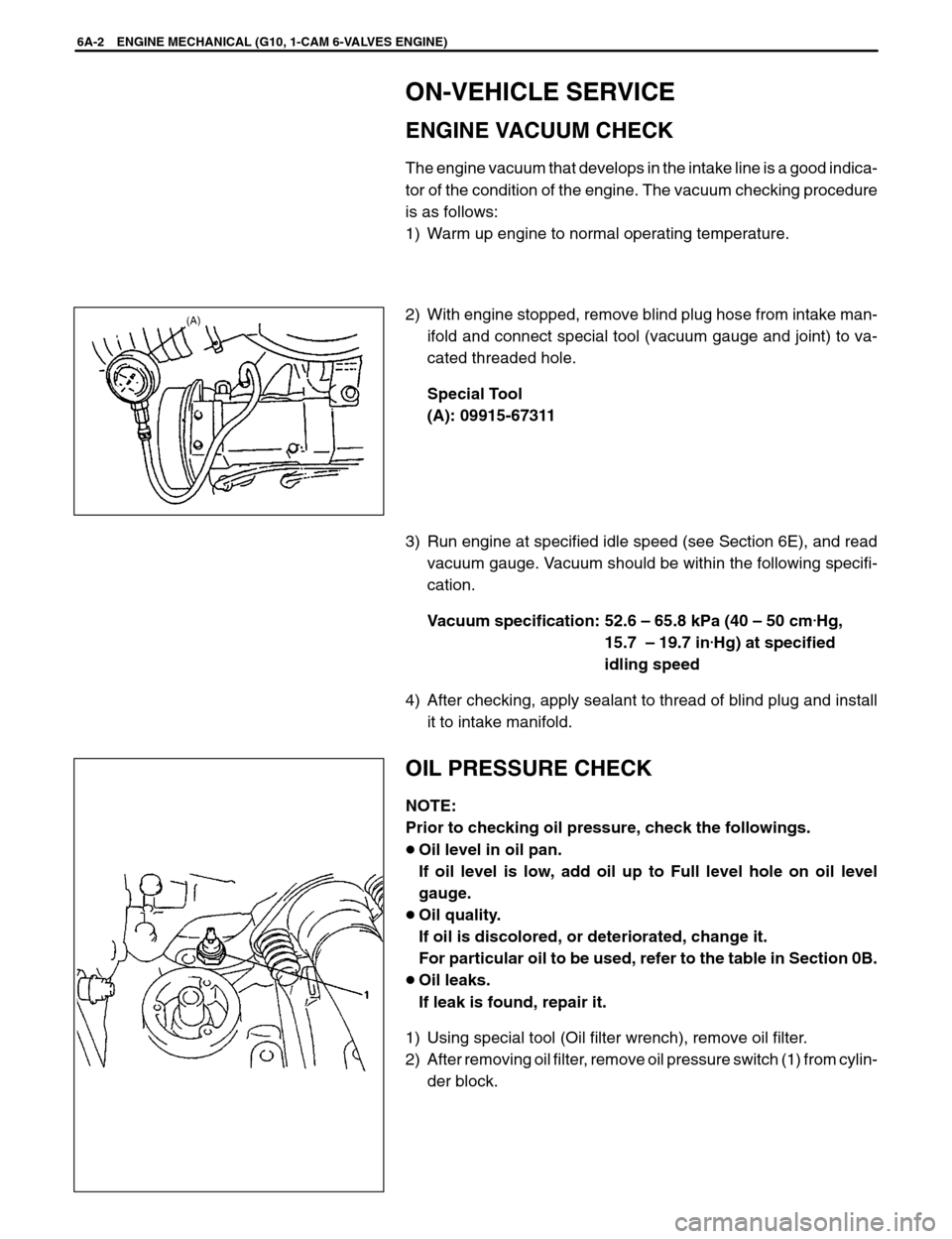
6A-2 ENGINE MECHANICAL (G10, 1-CAM 6-VALVES ENGINE)
ON-VEHICLE SERVICE
ENGINE VACUUM CHECK
The engine vacuum that develops in the intake line is a good indica-
tor of the condition of the engine. The vacuum checking procedure
is as follows:
1) Warm up engine to normal operating temperature.
2) With engine stopped, remove blind plug hose from intake man-
ifold and connect special tool (vacuum gauge and joint) to va-
cated threaded hole.
Special Tool
(A): 09915-67311
3) Run engine at specified idle speed (see Section 6E), and read
vacuum gauge. Vacuum should be within the following specifi-
cation.
Vacuum specification: 52.6 – 65.8 kPa (40 – 50 cm
.Hg,
15.7 – 19.7 in
.Hg) at specified
idling speed
4) After checking, apply sealant to thread of blind plug and install
it to intake manifold.
OIL PRESSURE CHECK
NOTE:
Prior to checking oil pressure, check the followings.
Oil level in oil pan.
If oil level is low, add oil up to Full level hole on oil level
gauge.
Oil quality.
If oil is discolored, or deteriorated, change it.
For particular oil to be used, refer to the table in Section 0B.
Oil leaks.
If leak is found, repair it.
1) Using special tool (Oil filter wrench), remove oil filter.
2) After removing oil filter, remove oil pressure switch (1) from cylin-
der block.
Page 267 of 557
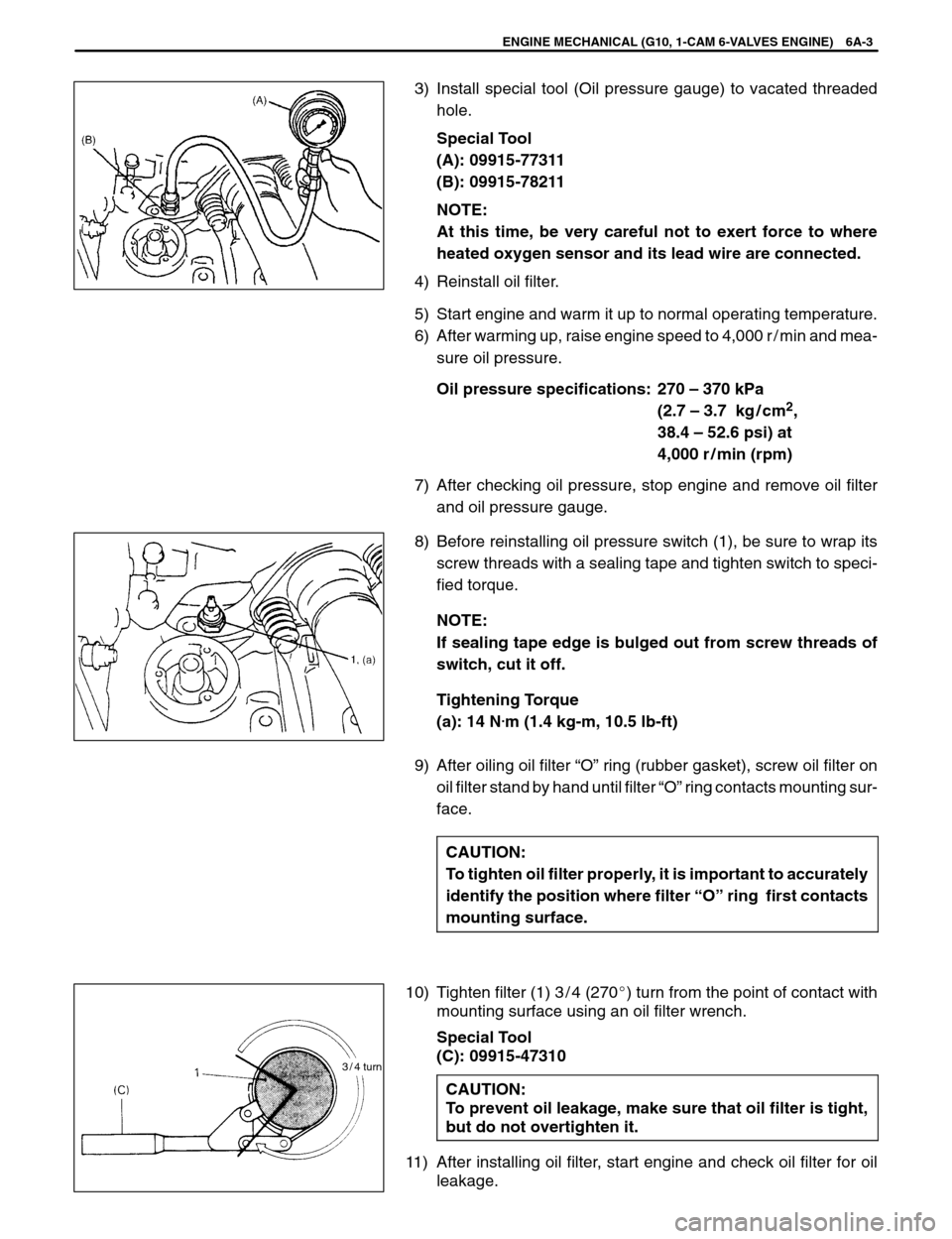
3 / 4 turn
ENGINE MECHANICAL (G10, 1-CAM 6-VALVES ENGINE) 6A-3
3) Install special tool (Oil pressure gauge) to vacated threaded
hole.
Special Tool
(A): 09915-77311
(B): 09915-78211
NOTE:
At this time, be very careful not to exert force to where
heated oxygen sensor and its lead wire are connected.
4) Reinstall oil filter.
5) Start engine and warm it up to normal operating temperature.
6) After warming up, raise engine speed to 4,000 r / min and mea-
sure oil pressure.
Oil pressure specifications: 270 – 370 kPa
(2.7 – 3.7 kg / cm
2,
38.4 – 52.6 psi) at
4,000 r / min (rpm)
7) After checking oil pressure, stop engine and remove oil filter
and oil pressure gauge.
8) Before reinstalling oil pressure switch (1), be sure to wrap its
screw threads with a sealing tape and tighten switch to speci-
fied torque.
NOTE:
If sealing tape edge is bulged out from screw threads of
switch, cut it off.
Tightening Torque
(a): 14 N
.m (1.4 kg-m, 10.5 lb-ft)
9) After oiling oil filter “O” ring (rubber gasket), screw oil filter on
oil filter stand by hand until filter “O” ring contacts mounting sur-
face.
CAUTION:
To tighten oil filter properly, it is important to accurately
identify the position where filter “O” ring first contacts
mounting surface.
10) Tighten filter (1) 3 / 4 (270) turn from the point of contact with
mounting surface using an oil filter wrench.
Special Tool
(C): 09915-47310
CAUTION:
To prevent oil leakage, make sure that oil filter is tight,
but do not overtighten it.
11) After installing oil filter, start engine and check oil filter for oil
leakage.
Page 268 of 557
6A-4 ENGINE MECHANICAL (G10, 1-CAM 6-VALVES ENGINE)
CYLINDER HEAD COVER
REMOVAL
1) Disconnect negative cable at battery.
2) Remove air cleaner assembly.
3) Remove high-tension cord clamps (2) from cylinder head cover.
4) Disconnect breather hose from cylinder head cover.
5) Remove cylinder head cover nuts and then seal washers (1).
6) Remove cylinder head cover (3) from cylinder head.
INSTALLATION
1) Install cylinder head cover gasket to head cover.
Before installing gasket, check it for deterioration or damage,
and replace as necessary.
2) Install cylinder head cover (1).
Before installing seal washers, check each one for deterioration
or damage, and replace as necessary.
Tighten cover nuts to specified torque.
Tightening Torque
(a): 4.5 N
.m (0.45 kg-m, 3.5 lb-ft)
3) Install high-tension cord clamps (2) to cylinder head cover.
4) Connect breather hose to cylinder head cover.
5) Install air cleaner assembly.
6) Connect negative cable at battery.