Page 300 of 557
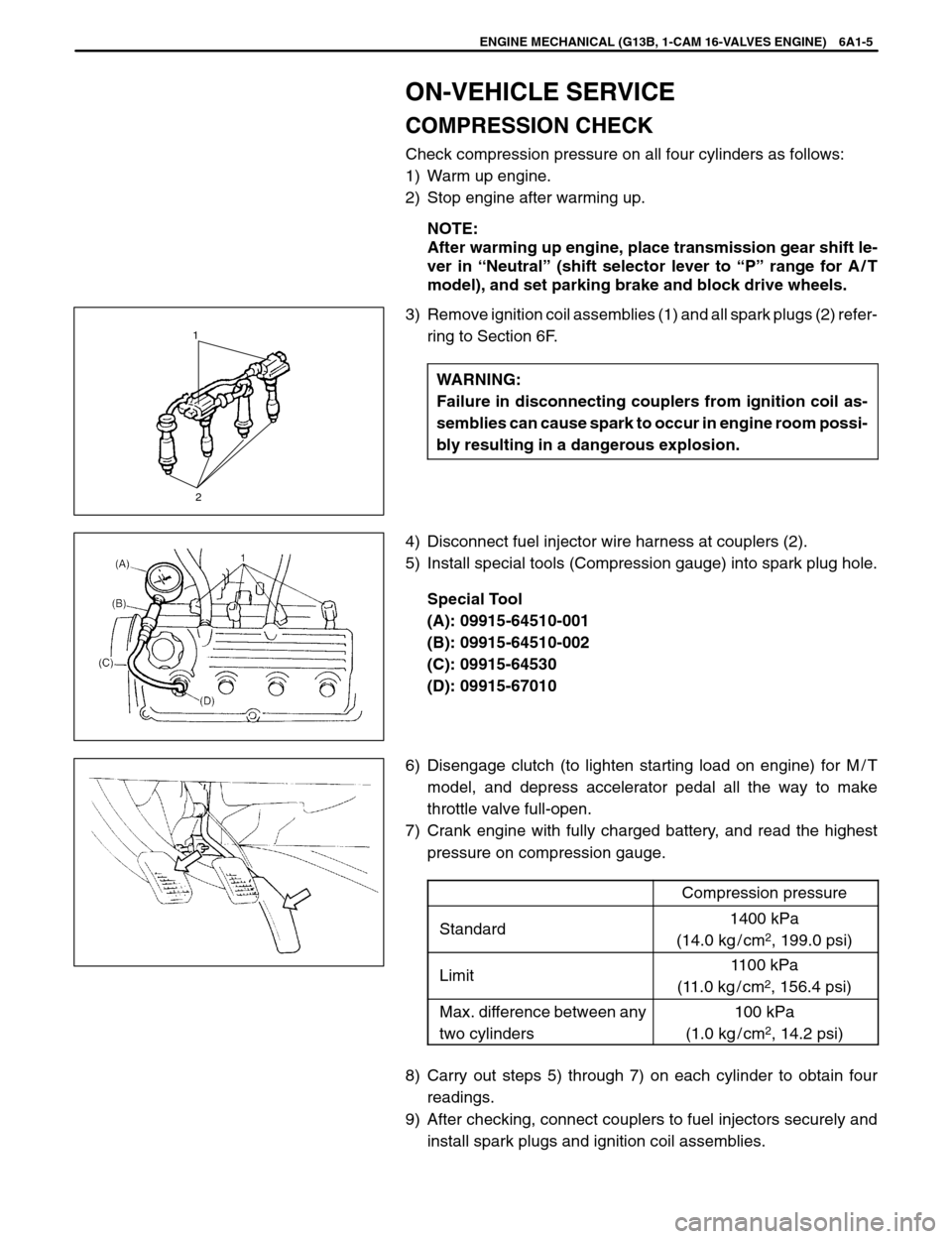
1
2
ENGINE MECHANICAL (G13B, 1-CAM 16-VALVES ENGINE) 6A1-5
ON-VEHICLE SERVICE
COMPRESSION CHECK
Check compression pressure on all four cylinders as follows:
1) Warm up engine.
2) Stop engine after warming up.
NOTE:
After warming up engine, place transmission gear shift le-
ver in “Neutral” (shift selector lever to “P” range for A / T
model), and set parking brake and block drive wheels.
3) Remove ignition coil assemblies (1) and all spark plugs (2) refer-
ring to Section 6F.
WARNING:
Failure in disconnecting couplers from ignition coil as-
semblies can cause spark to occur in engine room possi-
bly resulting in a dangerous explosion.
4) Disconnect fuel injector wire harness at couplers (2).
5) Install special tools (Compression gauge) into spark plug hole.
Special Tool
(A): 09915-64510-001
(B): 09915-64510-002
(C): 09915-64530
(D): 09915-67010
6) Disengage clutch (to lighten starting load on engine) for M / T
model, and depress accelerator pedal all the way to make
throttle valve full-open.
7) Crank engine with fully charged battery, and read the highest
pressure on compression gauge.
Compression pressure
Standard1400 kPa
(14.0 kg / cm
2, 199.0 psi)
Limit1100 kPa
(11.0 kg / cm
2, 156.4 psi)
Max. difference between any
two cylinders100 kPa
(1.0 kg / cm
2, 14.2 psi)
8) Carry out steps 5) through 7) on each cylinder to obtain four
readings.
9) After checking, connect couplers to fuel injectors securely and
install spark plugs and ignition coil assemblies.
Page 315 of 557
1.“V” mark on cylinder
head cover
2. Timing mark by “E” on
camshaft timing belt pulley
3. Arrow mark on oil
pump case
4. Punch mark on crankshaft
timing belt pulley
4. Tensioner stud
6. Damper
6
6A1-20 ENGINE MECHANICAL (G13B, 1-CAM 16-VALVES ENGINE)
8) Lock crankshaft inserting flat end rod or the like (2) between fly-
wheel ring gear and transmission case, after removing clutch
housing (torque converter housing for A / T) lower plate.
With crankshaft locked, remove crankshaft timing belt pulley
bolt (3).
9) Remove crankshaft pulley bolts (1).
10) Remove crankshaft pulley (4).
11) Install crankshaft timing belt pulley bolt temporarily to turn
crankshaft.
12) Release harness clamps.
13) Remove timing belt outside cover.
14) For installation of timing belt, align 4 timing marks as shown in
figure by turning crankshaft.
15) Remove timing belt tensioner (3), tensioner plate (2), tensioner
spring (5) and timing belt (1).
Page 319 of 557
6A1-24 ENGINE MECHANICAL (G13B, 1-CAM 16-VALVES ENGINE)
12) Install water pump pulley (1) and drive belt.
Tightening Torque
(a): 11 N
.m (1.1 kg-m, 8.0 lb-ft)
13) Adjust drive belt tension referring to Section 6B.
14) Adjust power steering pump belt tension or A/C compressor
belt tension, if equipped.
Refer to Section 0B.
15) Install P / S hose stay (if equipped).
16) Install air cleaner case with air cleaner outlet hose.
17) Install right side of engine under cover.
18) Install clutch housing (torque converter housing for A / T) lower
plate.
19) Connect negative cable at battery.
Page 320 of 557
1. Oil pan:
Apply sealant 99000-31150 to
oil pan mating surface.
2. Oil pump strainer
3. Seal
4. Drain plug gasket
5. Drain plug
6. CKP sensor : Tightening Torque
: Do not reuse
ENGINE MECHANICAL (G13B, 1-CAM 16-VALVES ENGINE) 6A1-25
OIL PAN AND OIL PUMP STRAINER
REMOVAL
1) Raise vehicle.
2) Drain engine oil by removing drain plug (1).
3) Remove right side of engine under cover.
4) Disconnect CKP sensor coupler and remove CKP sensor (1) by
removing its bolt. Then remove CKP sensor wire harness from
clamp.
5) Remove clutch housing (torque converter housing for A / T) low-
er plate.
Page 322 of 557
ENGINE MECHANICAL (G13B, 1-CAM 16-VALVES ENGINE) 6A1-27
3) Install new gasket and drain plug to oil pan.
Tighten drain plug to specified torque.
Tightening Torque
(a): 50 N
.m (5.0 kg-m, 36 lb-ft)
4) Install clutch (torque converter) housing lower plate.
5) Install CKP sensor (1) and connect its coupler, then clamp its
harness.
Tightening Torque
(a): 10 N
.m (1.0 kg-m, 7.5 lb-ft)
6) Install right side of engine under cover.
7) Refill engine with engine oil referring to “ENGINE OIL CHANGE”
in Section 0B.
Page 359 of 557
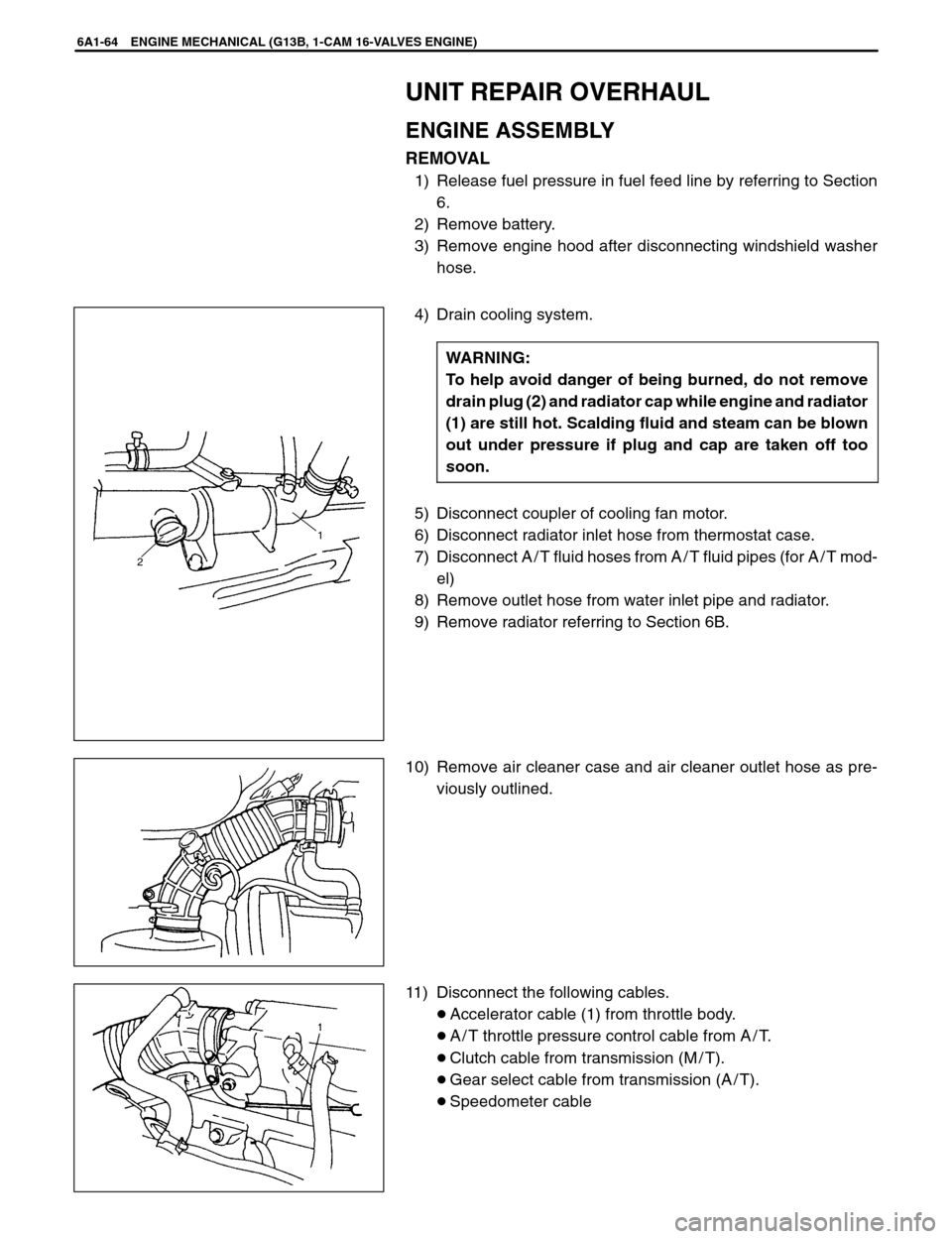
1
2
6A1-64 ENGINE MECHANICAL (G13B, 1-CAM 16-VALVES ENGINE)
UNIT REPAIR OVERHAUL
ENGINE ASSEMBLY
REMOVAL
1) Release fuel pressure in fuel feed line by referring to Section
6.
2) Remove battery.
3) Remove engine hood after disconnecting windshield washer
hose.
4) Drain cooling system.
WARNING:
To help avoid danger of being burned, do not remove
drain plug (2) and radiator cap while engine and radiator
(1) are still hot. Scalding fluid and steam can be blown
out under pressure if plug and cap are taken off too
soon.
5) Disconnect coupler of cooling fan motor.
6) Disconnect radiator inlet hose from thermostat case.
7) Disconnect A / T fluid hoses from A / T fluid pipes (for A / T mod-
el)
8) Remove outlet hose from water inlet pipe and radiator.
9) Remove radiator referring to Section 6B.
10) Remove air cleaner case and air cleaner outlet hose as pre-
viously outlined.
11) Disconnect the following cables.
Accelerator cable (1) from throttle body.
A / T throttle pressure control cable from A / T.
Clutch cable from transmission (M / T).
Gear select cable from transmission (A / T).
Speedometer cable
Page 362 of 557
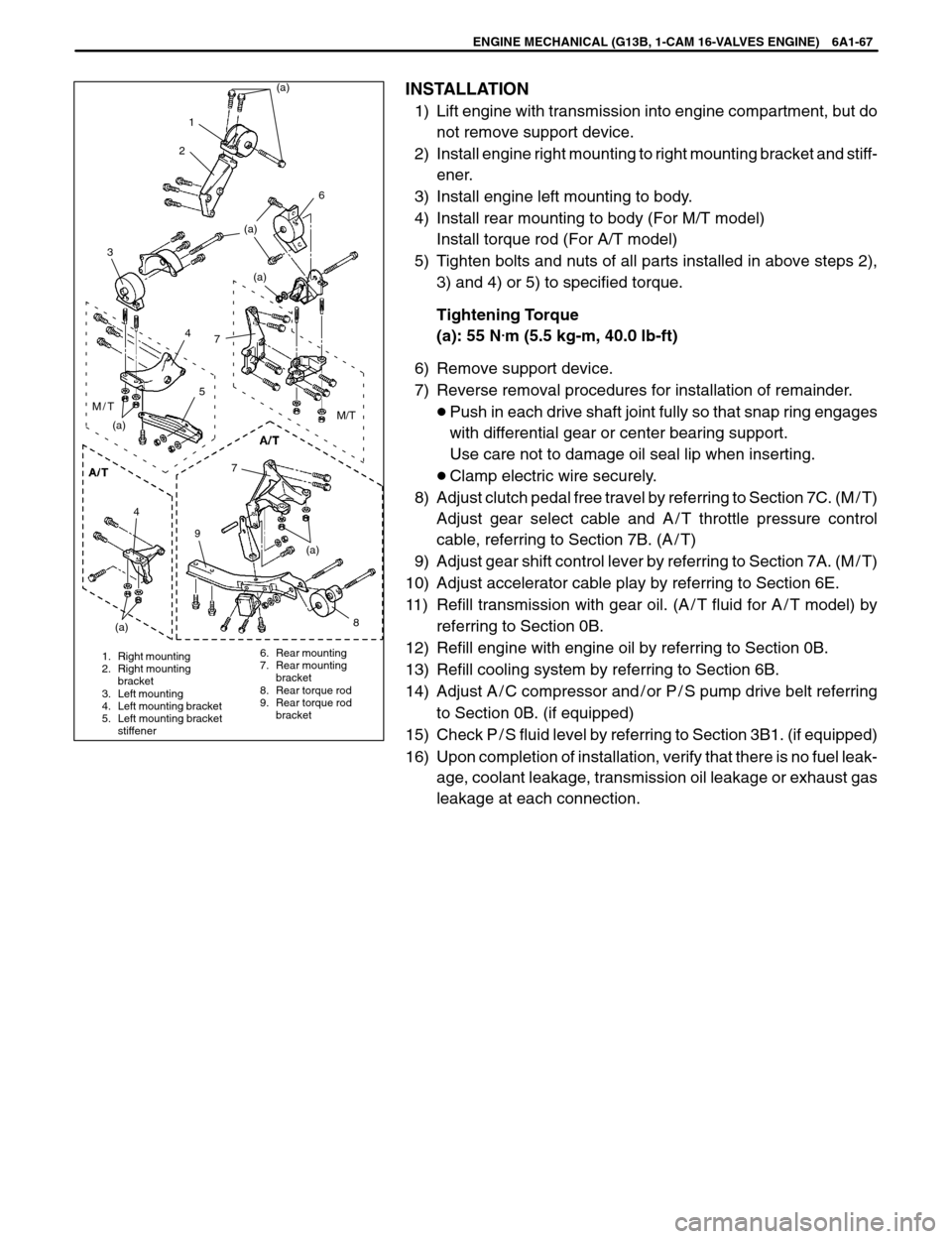
(a)
1
2
3
(a)
(a)
6
74
5
(a)
M/TM/T
9
(a)
4
7
(a)
8
1. Right mounting
2. Right mounting
bracket
3. Left mounting
4. Left mounting bracket
5. Left mounting bracket
stiffener6. Rear mounting
7. Rear mounting
bracket
8. Rear torque rod
9. Rear torque rod
bracket
ENGINE MECHANICAL (G13B, 1-CAM 16-VALVES ENGINE) 6A1-67
INSTALLATION
1) Lift engine with transmission into engine compartment, but do
not remove support device.
2) Install engine right mounting to right mounting bracket and stiff-
ener.
3) Install engine left mounting to body.
4) Install rear mounting to body (For M/T model)
Install torque rod (For A/T model)
5) Tighten bolts and nuts of all parts installed in above steps 2),
3) and 4) or 5) to specified torque.
Tightening Torque
(a): 55 N
.m (5.5 kg-m, 40.0 lb-ft)
6) Remove support device.
7) Reverse removal procedures for installation of remainder.
Push in each drive shaft joint fully so that snap ring engages
with differential gear or center bearing support.
Use care not to damage oil seal lip when inserting.
Clamp electric wire securely.
8) Adjust clutch pedal free travel by referring to Section 7C. (M / T)
Adjust gear select cable and A / T throttle pressure control
cable, referring to Section 7B. (A / T)
9) Adjust gear shift control lever by referring to Section 7A. (M / T)
10) Adjust accelerator cable play by referring to Section 6E.
11) Refill transmission with gear oil. (A / T fluid for A / T model) by
referring to Section 0B.
12) Refill engine with engine oil by referring to Section 0B.
13) Refill cooling system by referring to Section 6B.
14) Adjust A / C compressor and / or P / S pump drive belt referring
to Section 0B. (if equipped)
15) Check P / S fluid level by referring to Section 3B1. (if equipped)
16) Upon completion of installation, verify that there is no fuel leak-
age, coolant leakage, transmission oil leakage or exhaust gas
leakage at each connection.
Page 364 of 557
1. Flywheel bolt
2. Bolt
ENGINE MECHANICAL (G13B, 1-CAM 16-VALVES ENGINE) 6A1-69
REMOVAL
1) Remove engine assembly from body as previously outlined.
2) Remove clutch cover, clutch disc and flywheel (drive plate for
A / T).
Special Tool
(A): 09924-17810
3) Remove crankshaft pulley, timing belt and crankshaft timing
pulley.
4) Remove cylinder head assembly.
5) Remove oil pan and oil pump strainer.
6) Remove oil pump (1).
7) Remove oil seal housing.
8) Remove connecting rod bearing caps.
9) Loosen crankshaft bearing cap bolts in such order as indicated
in figure a little at a time and remove bearing caps.
10) Remove crankshaft from cylinder block.