Page 300 of 557
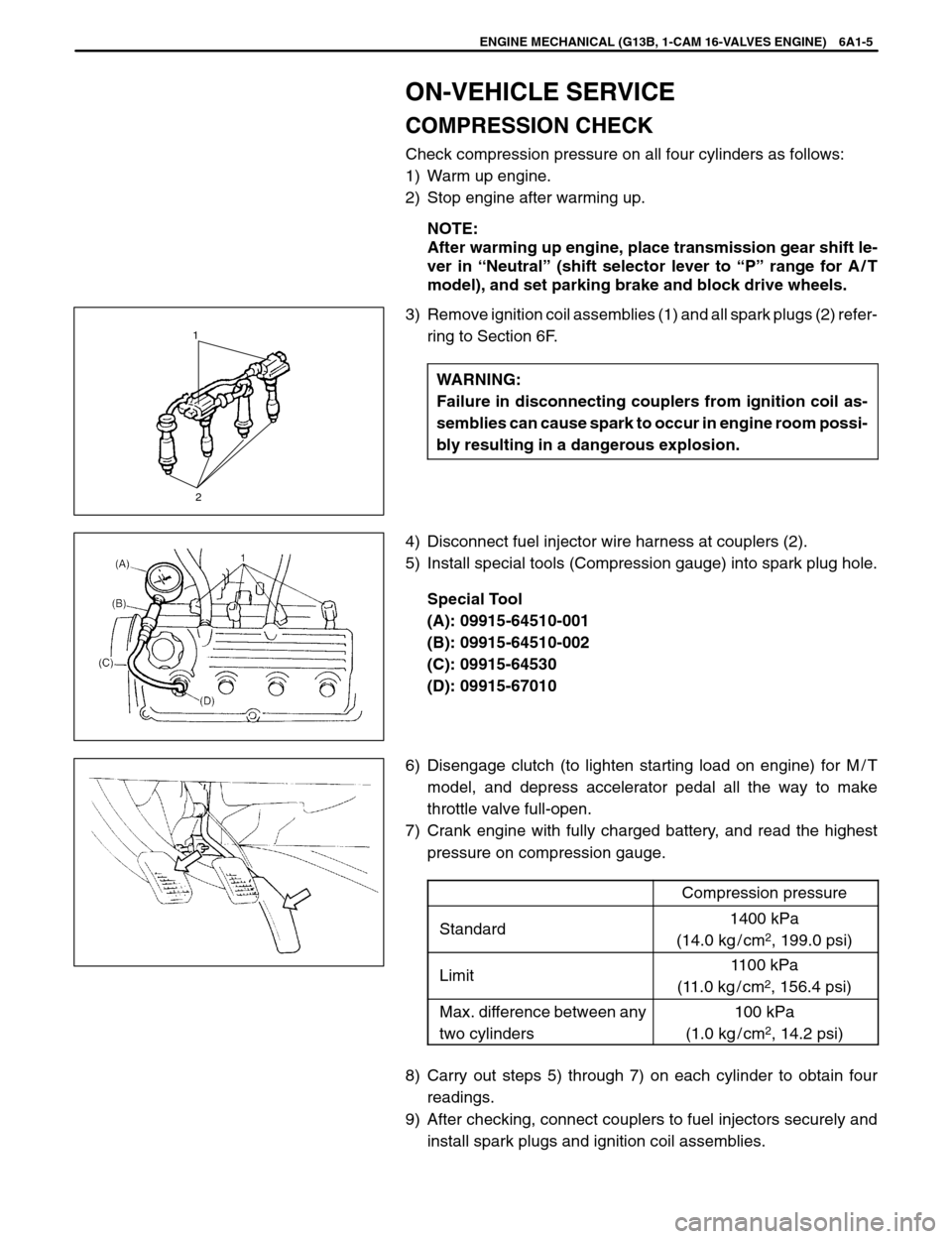
1
2
ENGINE MECHANICAL (G13B, 1-CAM 16-VALVES ENGINE) 6A1-5
ON-VEHICLE SERVICE
COMPRESSION CHECK
Check compression pressure on all four cylinders as follows:
1) Warm up engine.
2) Stop engine after warming up.
NOTE:
After warming up engine, place transmission gear shift le-
ver in “Neutral” (shift selector lever to “P” range for A / T
model), and set parking brake and block drive wheels.
3) Remove ignition coil assemblies (1) and all spark plugs (2) refer-
ring to Section 6F.
WARNING:
Failure in disconnecting couplers from ignition coil as-
semblies can cause spark to occur in engine room possi-
bly resulting in a dangerous explosion.
4) Disconnect fuel injector wire harness at couplers (2).
5) Install special tools (Compression gauge) into spark plug hole.
Special Tool
(A): 09915-64510-001
(B): 09915-64510-002
(C): 09915-64530
(D): 09915-67010
6) Disengage clutch (to lighten starting load on engine) for M / T
model, and depress accelerator pedal all the way to make
throttle valve full-open.
7) Crank engine with fully charged battery, and read the highest
pressure on compression gauge.
Compression pressure
Standard1400 kPa
(14.0 kg / cm
2, 199.0 psi)
Limit1100 kPa
(11.0 kg / cm
2, 156.4 psi)
Max. difference between any
two cylinders100 kPa
(1.0 kg / cm
2, 14.2 psi)
8) Carry out steps 5) through 7) on each cylinder to obtain four
readings.
9) After checking, connect couplers to fuel injectors securely and
install spark plugs and ignition coil assemblies.
Page 360 of 557
ENGINE MECHANICAL (G13B, 1-CAM 16-VALVES ENGINE) 6A1-65
12) Disconnect the following electric wires:
Ignition coil assembly
Ground wires from intake manifold
Engine oil pressure switch
EVAP canister purge valve (if equipped)
Engine coolant temp. sensor
Fuel injectors
Power steering pressure switch (if equipped)
Oxygen sensor-1
Back-up light switch (M / T)
Transmission range switch (A / T)
A/T vehicle speed sensor (A / T)
Solenoid coupler (A / T)
Generator
Starter
Battery negative cable from transmission
TP sensor
IAC valve
CMP sensor
MAP sensor
and then release wire harnesses from clamps.
13) Disconnect the following hoses:
Canister purge hose (2) from EVAP canister purge valve
Brake booster hose (1) from intake manifold
Radiator outlet hose from inlet pipe
Heater inlet and outlet hose from heater unit
14) Disconnect fuel feed (2) and return hoses (3) from fuel delivery
pipe (1).
Page 442 of 557
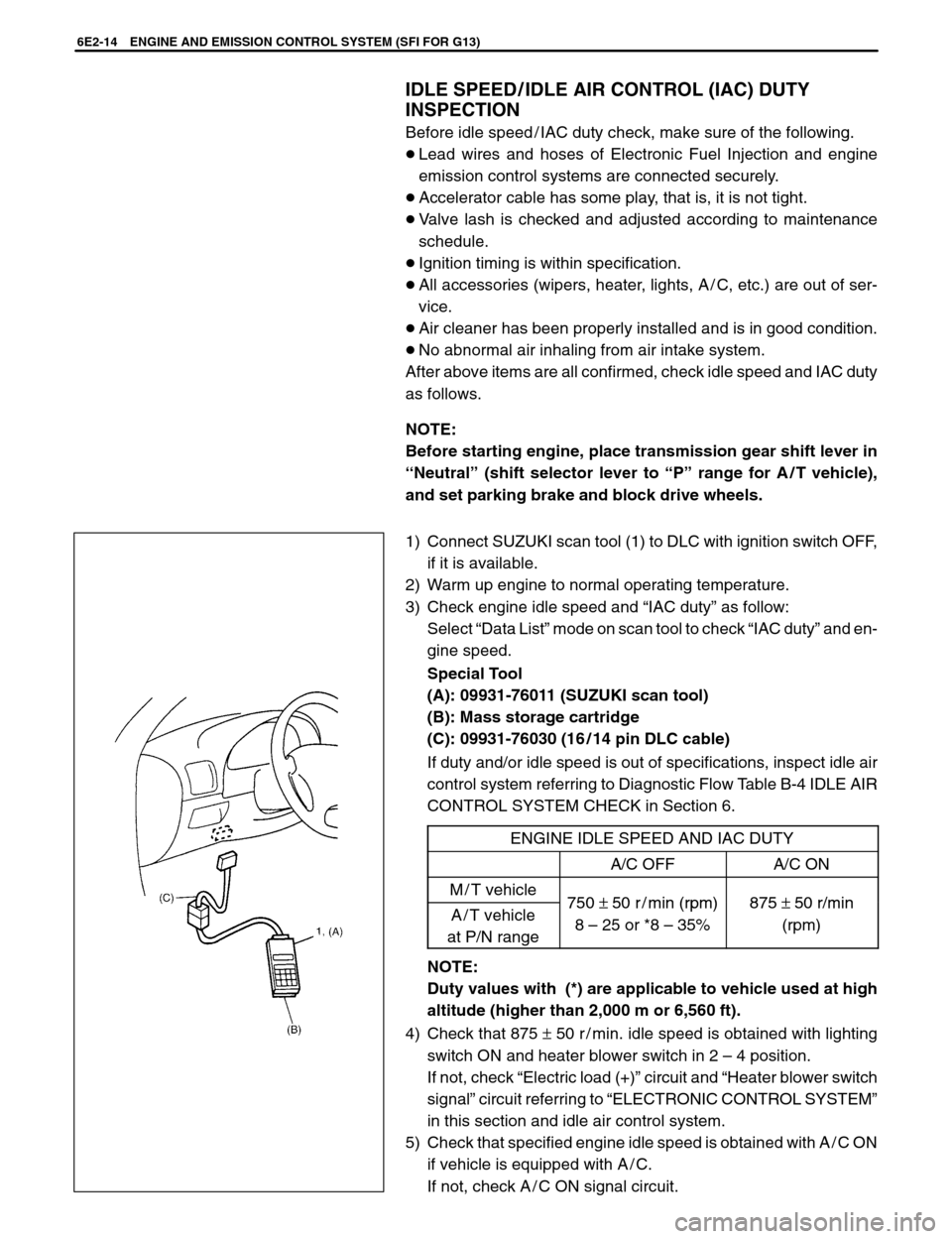
6E2-14 ENGINE AND EMISSION CONTROL SYSTEM (SFI FOR G13)
IDLE SPEED / IDLE AIR CONTROL (IAC) DUTY
INSPECTION
Before idle speed / IAC duty check, make sure of the following.
Lead wires and hoses of Electronic Fuel Injection and engine
emission control systems are connected securely.
Accelerator cable has some play, that is, it is not tight.
Valve lash is checked and adjusted according to maintenance
schedule.
Ignition timing is within specification.
All accessories (wipers, heater, lights, A / C, etc.) are out of ser-
vice.
Air cleaner has been properly installed and is in good condition.
No abnormal air inhaling from air intake system.
After above items are all confirmed, check idle speed and IAC duty
as follows.
NOTE:
Before starting engine, place transmission gear shift lever in
“Neutral” (shift selector lever to “P” range for A / T vehicle),
and set parking brake and block drive wheels.
1) Connect SUZUKI scan tool (1) to DLC with ignition switch OFF,
if it is available.
2) Warm up engine to normal operating temperature.
3) Check engine idle speed and “IAC duty” as follow:
Select “Data List” mode on scan tool to check “IAC duty” and en-
gine speed.
Special Tool
(A): 09931-76011 (SUZUKI scan tool)
(B): Mass storage cartridge
(C): 09931-76030 (16 / 14 pin DLC cable)
If duty and/or idle speed is out of specifications, inspect idle air
control system referring to Diagnostic Flow Table B-4 IDLE AIR
CONTROL SYSTEM CHECK in Section 6.
ENGINE IDLE SPEED AND IAC DUTY
A/C OFFA/C ON
M / T vehicle750±50 r / min (rpm)875±50 r/minA / T vehicle
at P/N range750 ±50 r/min (rpm)
8 – 25 or *8 – 35%
875 ±50 r/min
(rpm)
NOTE:
Duty values with (*) are applicable to vehicle used at high
altitude (higher than 2,000 m or 6,560 ft).
4) Check that 875 ± 50 r / min. idle speed is obtained with lighting
switch ON and heater blower switch in 2 – 4 position.
If not, check “Electric load (+)” circuit and “Heater blower switch
signal” circuit referring to “ELECTRONIC CONTROL SYSTEM”
in this section and idle air control system.
5) Check that specified engine idle speed is obtained with A / C ON
if vehicle is equipped with A / C.
If not, check A / C ON signal circuit.
Page 476 of 557
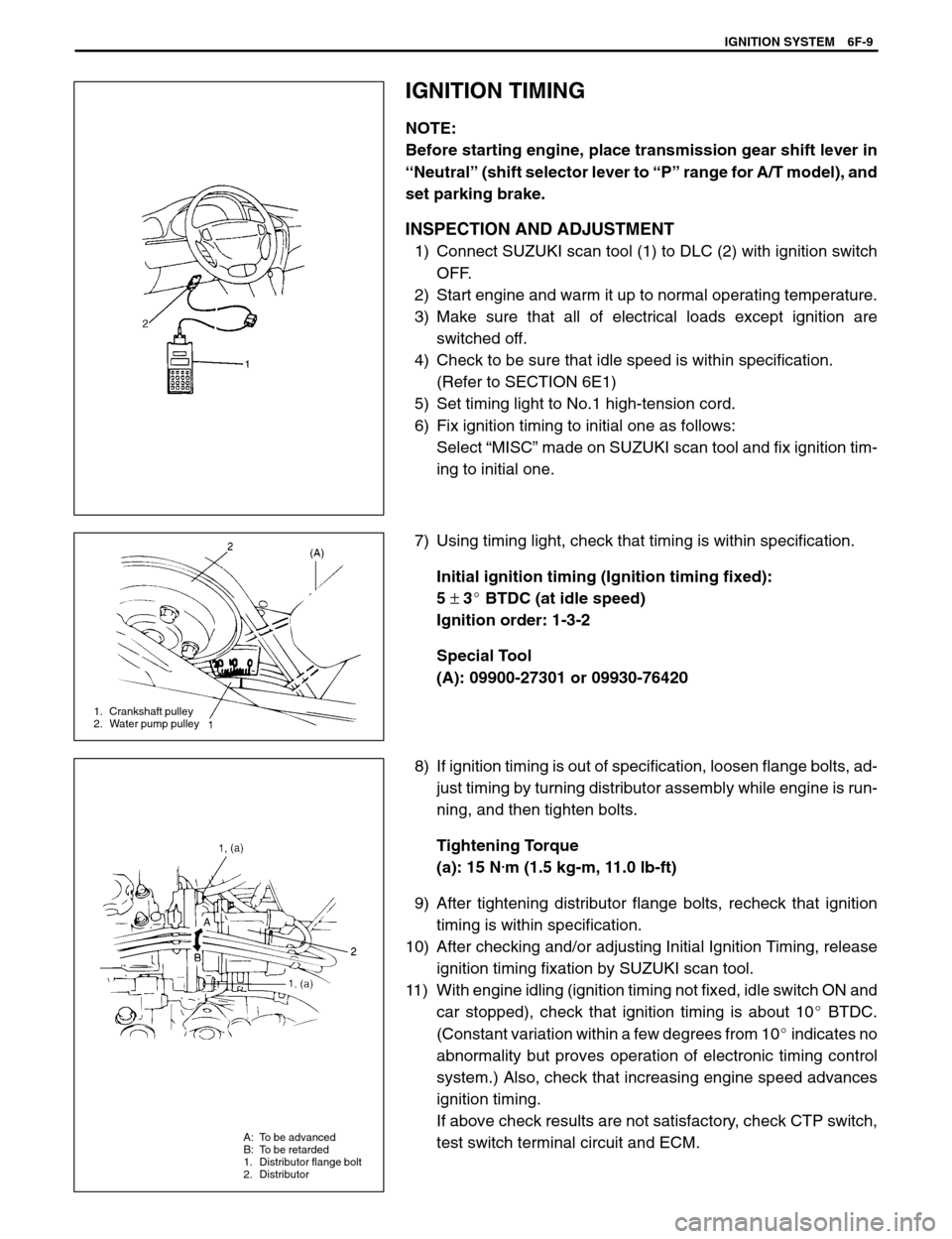
1. Crankshaft pulley
2. Water pump pulley
A: To be advanced
B: To be retarded
1. Distributor flange bolt
2. Distributor
IGNITION SYSTEM 6F-9
IGNITION TIMING
NOTE:
Before starting engine, place transmission gear shift lever in
“Neutral” (shift selector lever to “P” range for A/T model), and
set parking brake.
INSPECTION AND ADJUSTMENT
1) Connect SUZUKI scan tool (1) to DLC (2) with ignition switch
OFF.
2) Start engine and warm it up to normal operating temperature.
3) Make sure that all of electrical loads except ignition are
switched off.
4) Check to be sure that idle speed is within specification.
(Refer to SECTION 6E1)
5) Set timing light to No.1 high-tension cord.
6) Fix ignition timing to initial one as follows:
Select “MISC” made on SUZUKI scan tool and fix ignition tim-
ing to initial one.
7) Using timing light, check that timing is within specification.
Initial ignition timing (Ignition timing fixed):
5 ±3 BTDC (at idle speed)
Ignition order: 1-3-2
Special Tool
(A): 09900-27301 or 09930-76420
8) If ignition timing is out of specification, loosen flange bolts, ad-
just timing by turning distributor assembly while engine is run-
ning, and then tighten bolts.
Tightening Torque
(a): 15 N
.m (1.5 kg-m, 11.0 lb-ft)
9) After tightening distributor flange bolts, recheck that ignition
timing is within specification.
10) After checking and/or adjusting Initial Ignition Timing, release
ignition timing fixation by SUZUKI scan tool.
11) With engine idling (ignition timing not fixed, idle switch ON and
car stopped), check that ignition timing is about 10 BTDC.
(Constant variation within a few degrees from 10 indicates no
abnormality but proves operation of electronic timing control
system.) Also, check that increasing engine speed advances
ignition timing.
If above check results are not satisfactory, check CTP switch,
test switch terminal circuit and ECM.
Page 499 of 557
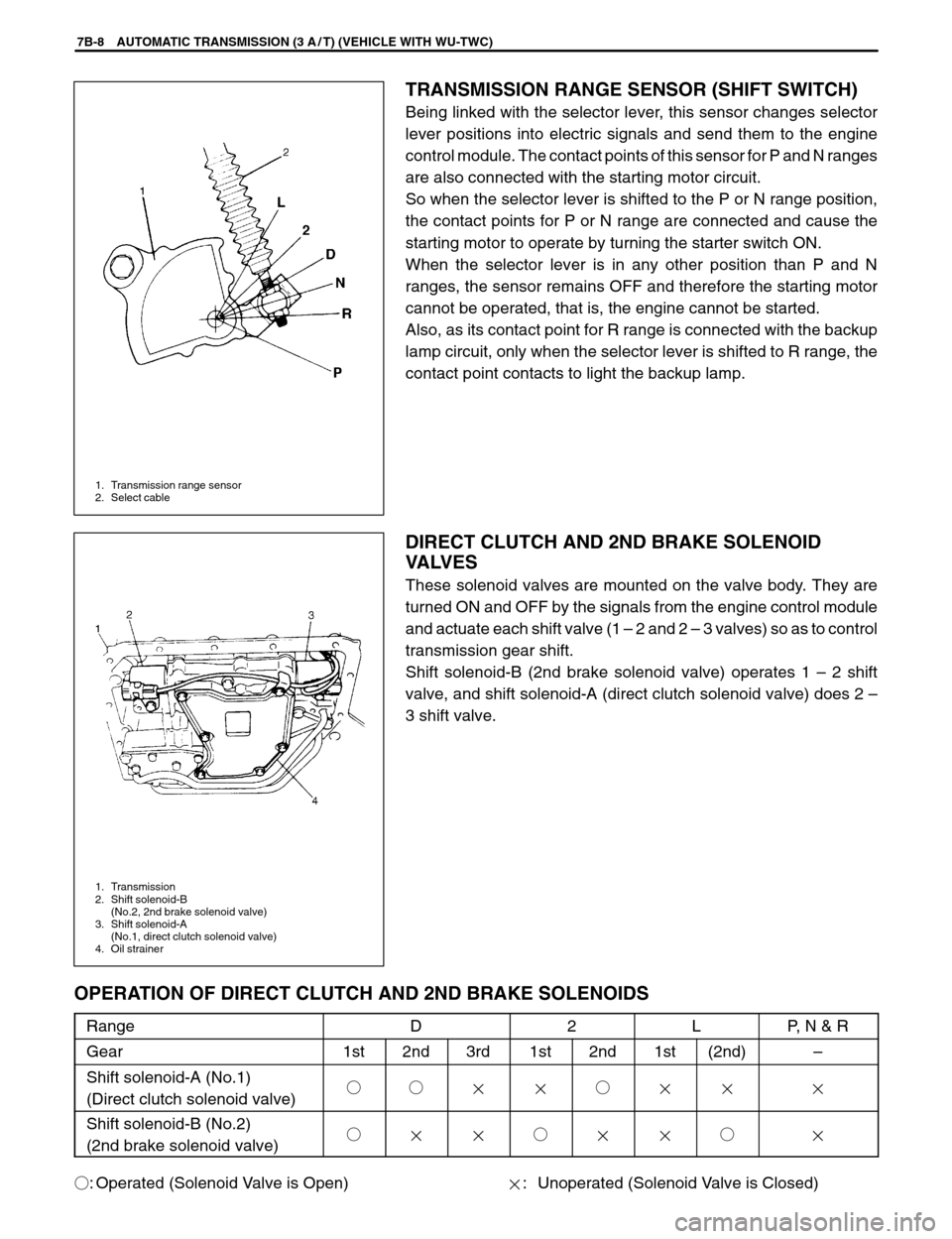
1. Transmission range sensor
2. Select cable
1. Transmission
2. Shift solenoid-B
(No.2, 2nd brake solenoid valve)
3. Shift solenoid-A
(No.1, direct clutch solenoid valve)
4. Oil strainer
7B-8 AUTOMATIC TRANSMISSION (3 A / T) (VEHICLE WITH WU-TWC)
TRANSMISSION RANGE SENSOR (SHIFT SWITCH)
Being linked with the selector lever, this sensor changes selector
lever positions into electric signals and send them to the engine
control module. The contact points of this sensor for P and N ranges
are also connected with the starting motor circuit.
So when the selector lever is shifted to the P or N range position,
the contact points for P or N range are connected and cause the
starting motor to operate by turning the starter switch ON.
When the selector lever is in any other position than P and N
ranges, the sensor remains OFF and therefore the starting motor
cannot be operated, that is, the engine cannot be started.
Also, as its contact point for R range is connected with the backup
lamp circuit, only when the selector lever is shifted to R range, the
contact point contacts to light the backup lamp.
DIRECT CLUTCH AND 2ND BRAKE SOLENOID
VALVES
These solenoid valves are mounted on the valve body. They are
turned ON and OFF by the signals from the engine control module
and actuate each shift valve (1 – 2 and 2 – 3 valves) so as to control
transmission gear shift.
Shift solenoid-B (2nd brake solenoid valve) operates 1 – 2 shift
valve, and shift solenoid-A (direct clutch solenoid valve) does 2 –
3 shift valve.
OPERATION OF DIRECT CLUTCH AND 2ND BRAKE SOLENOIDS
RangeD2LP, N & R
Gear1st2nd3rd1st2nd1st(2nd)–
Shift solenoid-A (No.1)
(Direct clutch solenoid valve)
Shift solenoid-B (No.2)
(2nd brake solenoid valve)
: Operated (Solenoid Valve is Open): Unoperated (Solenoid Valve is Closed)