Page 258 of 557
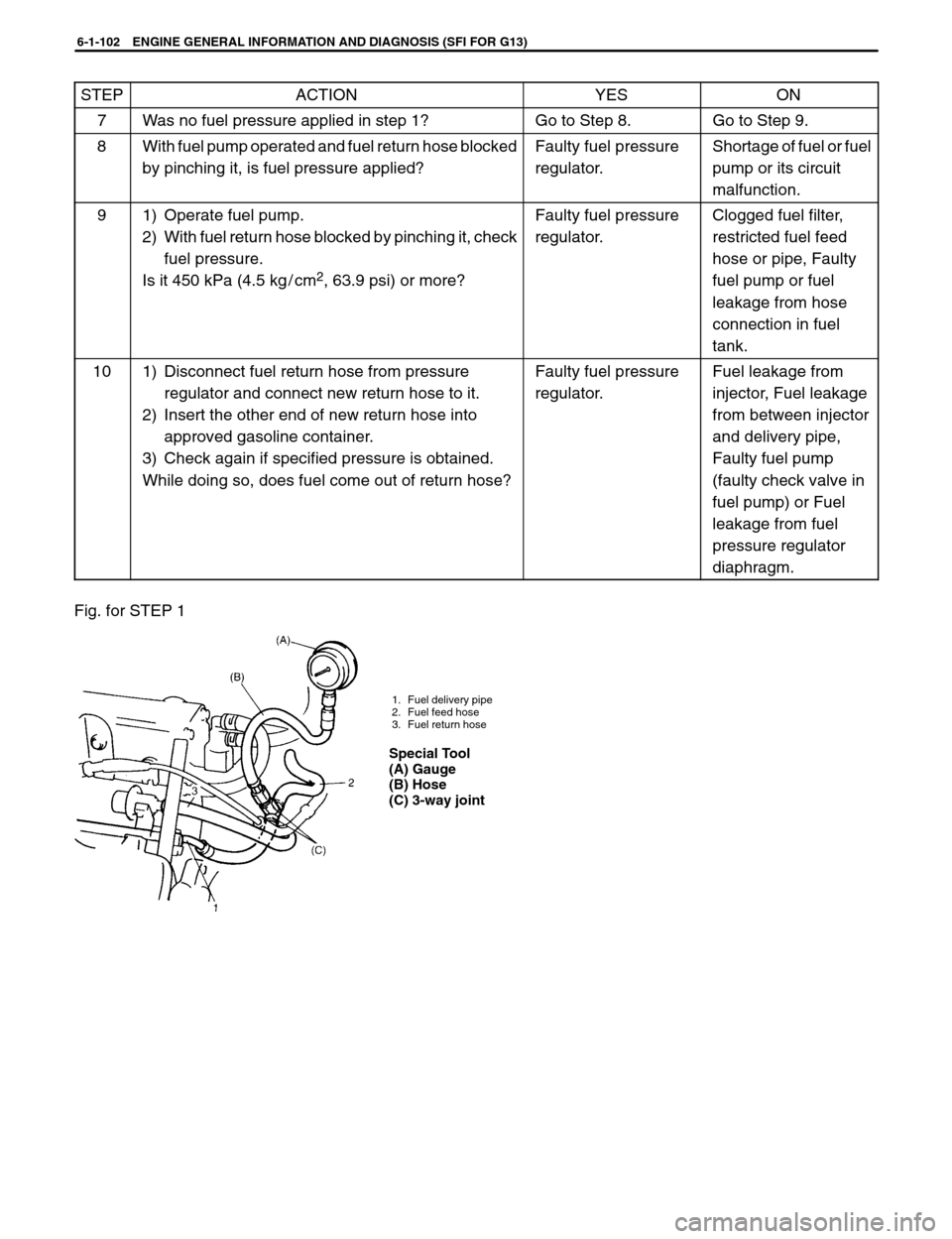
6-1-102 ENGINE GENERAL INFORMATION AND DIAGNOSIS (SFI FOR G13)
1. Fuel delivery pipe
2. Fuel feed hose
3. Fuel return hose
Special Tool
(A) Gauge
(B) Hose
(C) 3-way joint
STEPACTIONYESON
7Was no fuel pressure applied in step 1?Go to Step 8.Go to Step 9.
8With fuel pump operated and fuel return hose blocked
by pinching it, is fuel pressure applied?Faulty fuel pressure
regulator.Shortage of fuel or fuel
pump or its circuit
malfunction.
91) Operate fuel pump.
2) With fuel return hose blocked by pinching it, check
fuel pressure.
Is it 450 kPa (4.5 kg / cm
2, 63.9 psi) or more?
Faulty fuel pressure
regulator.Clogged fuel filter,
restricted fuel feed
hose or pipe, Faulty
fuel pump or fuel
leakage from hose
connection in fuel
tank.
101) Disconnect fuel return hose from pressure
regulator and connect new return hose to it.
2) Insert the other end of new return hose into
approved gasoline container.
3) Check again if specified pressure is obtained.
While doing so, does fuel come out of return hose?Faulty fuel pressure
regulator.Fuel leakage from
injector, Fuel leakage
from between injector
and delivery pipe,
Faulty fuel pump
(faulty check valve in
fuel pump) or Fuel
leakage from fuel
pressure regulator
diaphragm.
Fig. for STEP 1
Page 269 of 557
1. Stay
2. Throttle body
3. Gasket
4. EFE heater
5. Intake manifold
6. Gasket : Tightening Torque
: Do not reuse
ENGINE MECHANICAL (G10, 1-CAM 6-VALVES ENGINE) 6A-5
THROTTLE BODY AND INTAKE MANIFOLD
REMOVAL
1) Relieve fuel pressure according to procedure described in
“FUEL PRESSURE RELIEF PROCEDURE” of Section 6.
2) Disconnect negative cable at battery.
3) Drain cooling system.
WARNING:
To help avoid danger of being burned, do not remove
drain plug (2) and radiator cap while engine and radiator
(1) are still hot. Scalding fluid and steam can be blown out
under pressure if plug and cap are taken off too soon.
Page 270 of 557
1. Throttle body
1. Throttle body
2. ISC actuator
5. Clamp
6A-6 ENGINE MECHANICAL (G10, 1-CAM 6-VALVES ENGINE)
4) Remove air cleaner assembly.
5) Disconnect the following electric lead wires:
EGR valve
ISC actuator (2)
Ground wires from intake manifold
Fuel injector (4)
TP sensor (3)
EFE heater (5)
Engine coolant temp. gauge
6) Disconnect fuel return (4) and feed hoses (3) from fuel pipes.
7) Disconnect coolant hoses from intake manifold.
8) Disconnect the following vacuum hoses.
Canister purge hose from intake manifold.
EGR pressure transducer hoses from EGR valve.
EGR valve hose from EGR valve.
Pressure sensor hose from intake manifold.
Brake booster hose from intake manifold.
9) Disconnect breather hose from PCV valve.
10) Disconnect accelerator cable from throttle body.
11) Disconnect other connected to throttle body and intake man-
ifold, if any.
12) Remove intake manifold with throttle body from cylinder head.
13) Remove throttle body from intake manifold.
Page 271 of 557
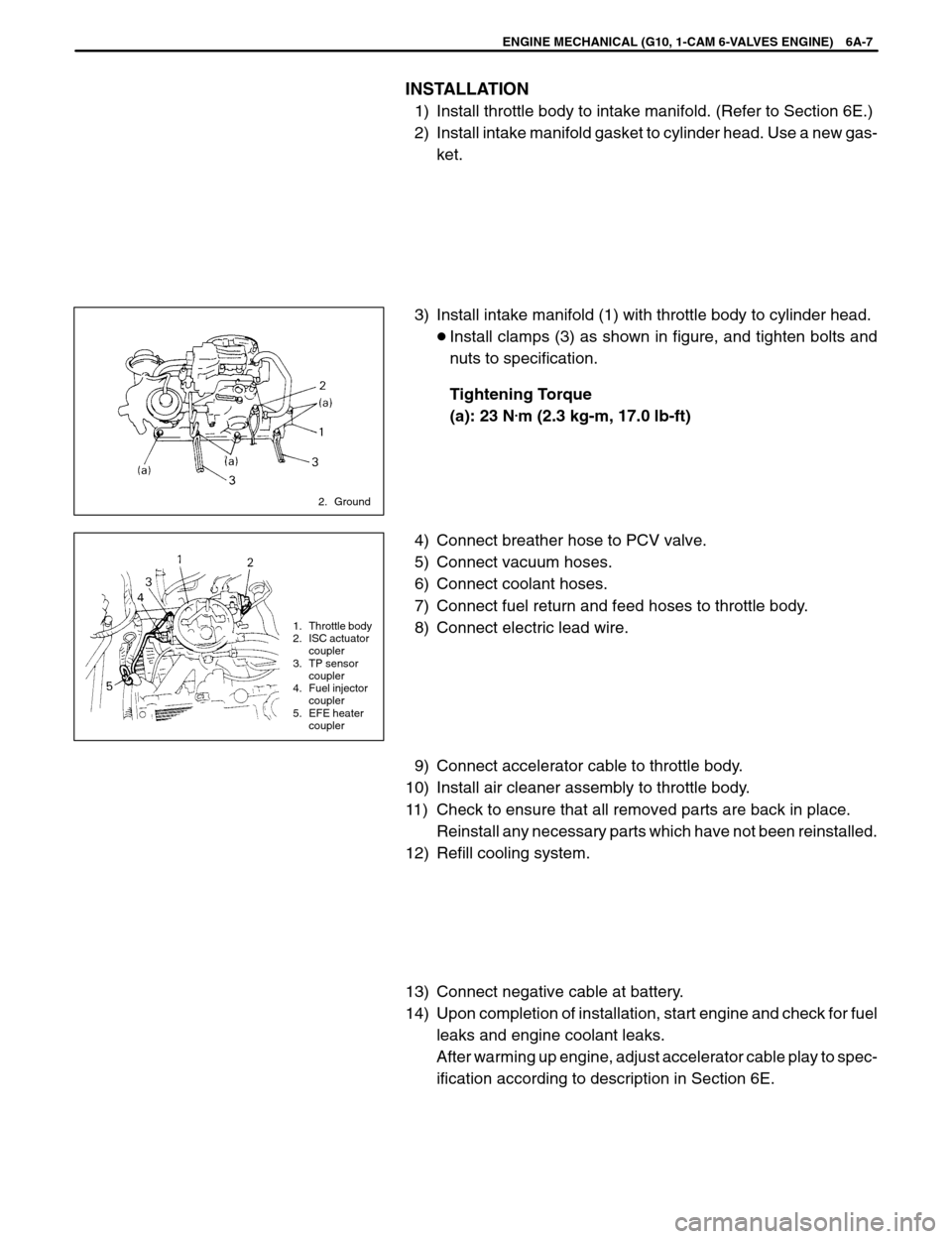
2. Ground
1. Throttle body
2. ISC actuator
coupler
3. TP sensor
coupler
4. Fuel injector
coupler
5. EFE heater
coupler
ENGINE MECHANICAL (G10, 1-CAM 6-VALVES ENGINE) 6A-7
INSTALLATION
1) Install throttle body to intake manifold. (Refer to Section 6E.)
2) Install intake manifold gasket to cylinder head. Use a new gas-
ket.
3) Install intake manifold (1) with throttle body to cylinder head.
Install clamps (3) as shown in figure, and tighten bolts and
nuts to specification.
Tightening Torque
(a): 23 N
.m (2.3 kg-m, 17.0 lb-ft)
4) Connect breather hose to PCV valve.
5) Connect vacuum hoses.
6) Connect coolant hoses.
7) Connect fuel return and feed hoses to throttle body.
8) Connect electric lead wire.
9) Connect accelerator cable to throttle body.
10) Install air cleaner assembly to throttle body.
11) Check to ensure that all removed parts are back in place.
Reinstall any necessary parts which have not been reinstalled.
12) Refill cooling system.
13) Connect negative cable at battery.
14) Upon completion of installation, start engine and check for fuel
leaks and engine coolant leaks.
After warming up engine, adjust accelerator cable play to spec-
ification according to description in Section 6E.
Page 288 of 557
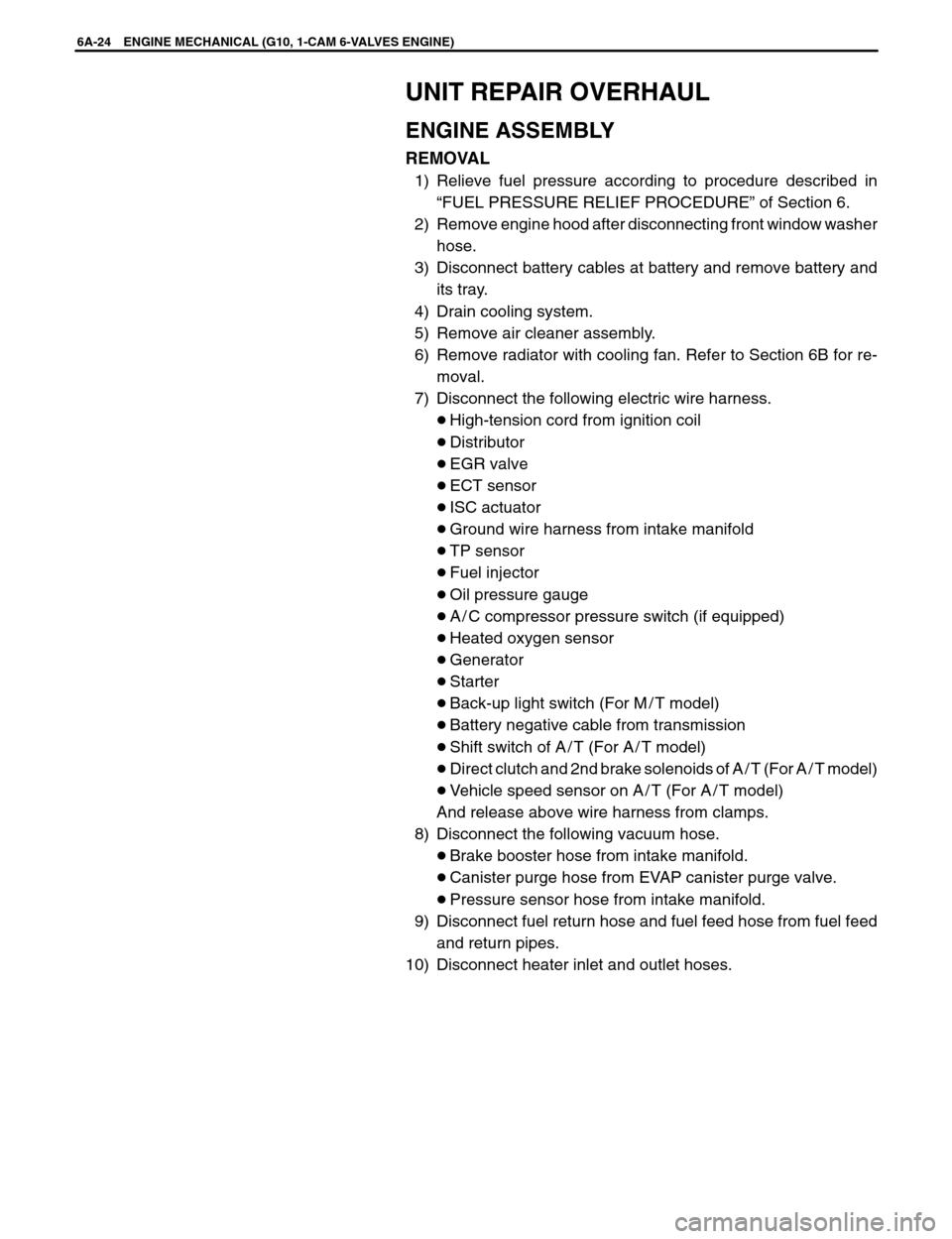
6A-24 ENGINE MECHANICAL (G10, 1-CAM 6-VALVES ENGINE)
UNIT REPAIR OVERHAUL
ENGINE ASSEMBLY
REMOVAL
1) Relieve fuel pressure according to procedure described in
“FUEL PRESSURE RELIEF PROCEDURE” of Section 6.
2) Remove engine hood after disconnecting front window washer
hose.
3) Disconnect battery cables at battery and remove battery and
its tray.
4) Drain cooling system.
5) Remove air cleaner assembly.
6) Remove radiator with cooling fan. Refer to Section 6B for re-
moval.
7) Disconnect the following electric wire harness.
High-tension cord from ignition coil
Distributor
EGR valve
ECT sensor
ISC actuator
Ground wire harness from intake manifold
TP sensor
Fuel injector
Oil pressure gauge
A / C compressor pressure switch (if equipped)
Heated oxygen sensor
Generator
Starter
Back-up light switch (For M / T model)
Battery negative cable from transmission
Shift switch of A / T (For A / T model)
Direct clutch and 2nd brake solenoids of A / T (For A / T model)
Vehicle speed sensor on A / T (For A / T model)
And release above wire harness from clamps.
8) Disconnect the following vacuum hose.
Brake booster hose from intake manifold.
Canister purge hose from EVAP canister purge valve.
Pressure sensor hose from intake manifold.
9) Disconnect fuel return hose and fuel feed hose from fuel feed
and return pipes.
10) Disconnect heater inlet and outlet hoses.
Page 290 of 557
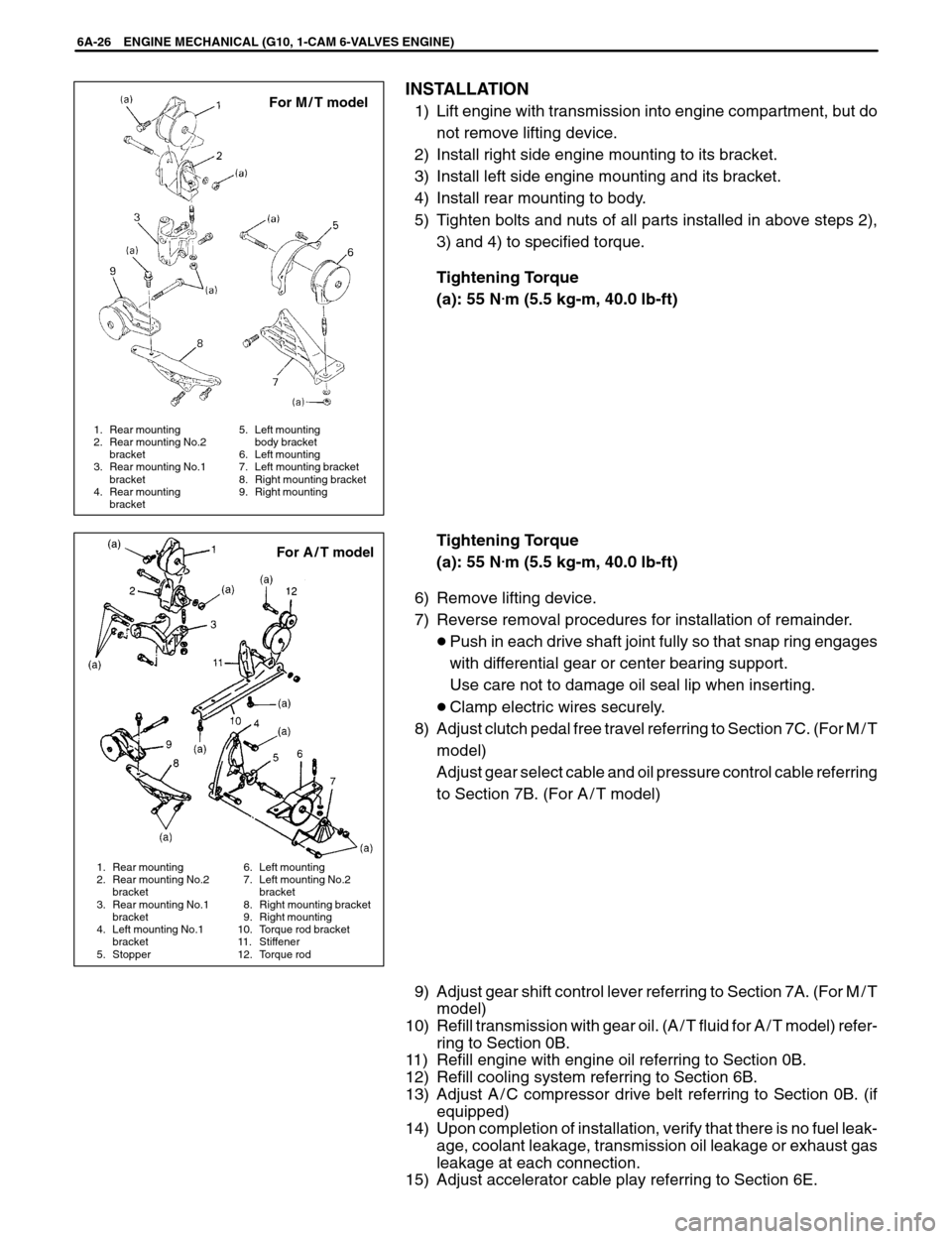
1. Rear mounting
2. Rear mounting No.2
bracket
3. Rear mounting No.1
bracket
4. Rear mounting
bracket5. Left mounting
body bracket
6. Left mounting
7. Left mounting bracket
8. Right mounting bracket
9. Right mounting
For M / T model
For A / T model
1. Rear mounting
2. Rear mounting No.2
bracket
3. Rear mounting No.1
bracket
4. Left mounting No.1
bracket
5. Stopper6. Left mounting
7. Left mounting No.2
bracket
8. Right mounting bracket
9. Right mounting
10. Torque rod bracket
11. Stiffener
12. Torque rod
6A-26 ENGINE MECHANICAL (G10, 1-CAM 6-VALVES ENGINE)
INSTALLATION
1) Lift engine with transmission into engine compartment, but do
not remove lifting device.
2) Install right side engine mounting to its bracket.
3) Install left side engine mounting and its bracket.
4) Install rear mounting to body.
5) Tighten bolts and nuts of all parts installed in above steps 2),
3) and 4) to specified torque.
Tightening Torque
(a): 55 N
.m (5.5 kg-m, 40.0 lb-ft)
Tightening Torque
(a): 55 N
.m (5.5 kg-m, 40.0 lb-ft)
6) Remove lifting device.
7) Reverse removal procedures for installation of remainder.
Push in each drive shaft joint fully so that snap ring engages
with differential gear or center bearing support.
Use care not to damage oil seal lip when inserting.
Clamp electric wires securely.
8) Adjust clutch pedal free travel referring to Section 7C. (For M / T
model)
Adjust gear select cable and oil pressure control cable referring
to Section 7B. (For A / T model)
9) Adjust gear shift control lever referring to Section 7A. (For M / T
model)
10) Refill transmission with gear oil. (A / T fluid for A / T model) refer-
ring to Section 0B.
11) Refill engine with engine oil referring to Section 0B.
12) Refill cooling system referring to Section 6B.
13) Adjust A / C compressor drive belt referring to Section 0B. (if
equipped)
14) Upon completion of installation, verify that there is no fuel leak-
age, coolant leakage, transmission oil leakage or exhaust gas
leakage at each connection.
15) Adjust accelerator cable play referring to Section 6E.
Page 300 of 557
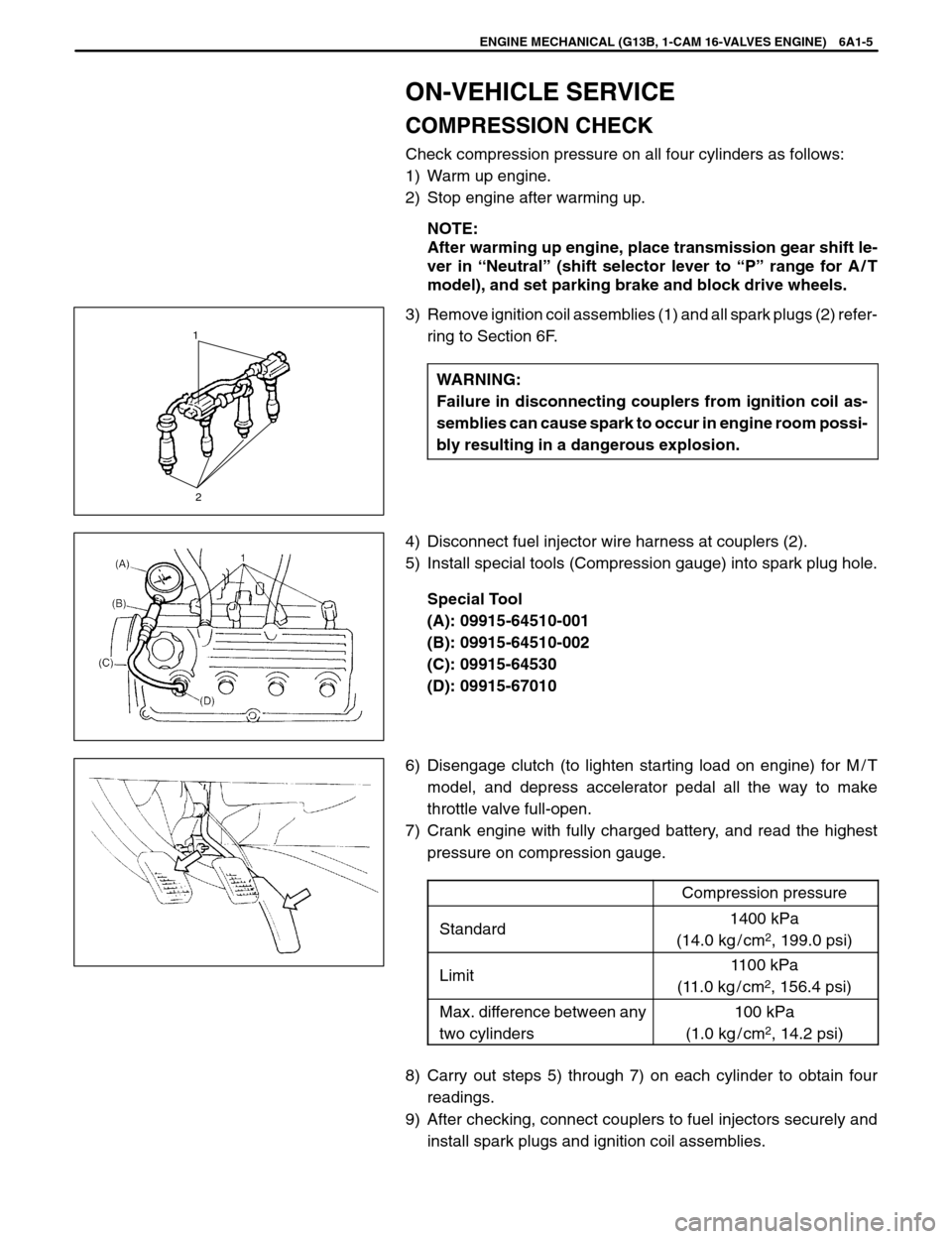
1
2
ENGINE MECHANICAL (G13B, 1-CAM 16-VALVES ENGINE) 6A1-5
ON-VEHICLE SERVICE
COMPRESSION CHECK
Check compression pressure on all four cylinders as follows:
1) Warm up engine.
2) Stop engine after warming up.
NOTE:
After warming up engine, place transmission gear shift le-
ver in “Neutral” (shift selector lever to “P” range for A / T
model), and set parking brake and block drive wheels.
3) Remove ignition coil assemblies (1) and all spark plugs (2) refer-
ring to Section 6F.
WARNING:
Failure in disconnecting couplers from ignition coil as-
semblies can cause spark to occur in engine room possi-
bly resulting in a dangerous explosion.
4) Disconnect fuel injector wire harness at couplers (2).
5) Install special tools (Compression gauge) into spark plug hole.
Special Tool
(A): 09915-64510-001
(B): 09915-64510-002
(C): 09915-64530
(D): 09915-67010
6) Disengage clutch (to lighten starting load on engine) for M / T
model, and depress accelerator pedal all the way to make
throttle valve full-open.
7) Crank engine with fully charged battery, and read the highest
pressure on compression gauge.
Compression pressure
Standard1400 kPa
(14.0 kg / cm
2, 199.0 psi)
Limit1100 kPa
(11.0 kg / cm
2, 156.4 psi)
Max. difference between any
two cylinders100 kPa
(1.0 kg / cm
2, 14.2 psi)
8) Carry out steps 5) through 7) on each cylinder to obtain four
readings.
9) After checking, connect couplers to fuel injectors securely and
install spark plugs and ignition coil assemblies.
Page 309 of 557
1. Intake manifold
2. Throttle body
3. Gasket
4. EGR valve
5. Fuel delivery pipe
6. Fuel injector7. Fuel pressure regulator
8. EVAP canister purge valve
9. MAP sensor
10. O-ring
11. Gasket
12. Cushion : Tightening Torque
: Do not reuse
1
2
6A1-14 ENGINE MECHANICAL (G13B, 1-CAM 16-VALVES ENGINE)
THROTTLE BODY AND INTAKE MANIFOLD
REMOVAL
1) Relieve fuel pressure according to procedure described in Sec-
tion 6.
2) Disconnect negative cable at battery.
3) Drain cooling system.
WARNING:
To help avoid danger of being burned, do not remove
drain plug (2) and radiator cap while engine and radiator
(1) are still hot. Scalding fluid and steam can be blown out
under pressure if plug and cap are taken off too soon.
4) Disconnect IAT sensor at coupler.
5) Remove air cleaner outlet hose (2) with resonator.
6) Disconnect accelerator cable (1) from throttle body.