Page 99 of 698
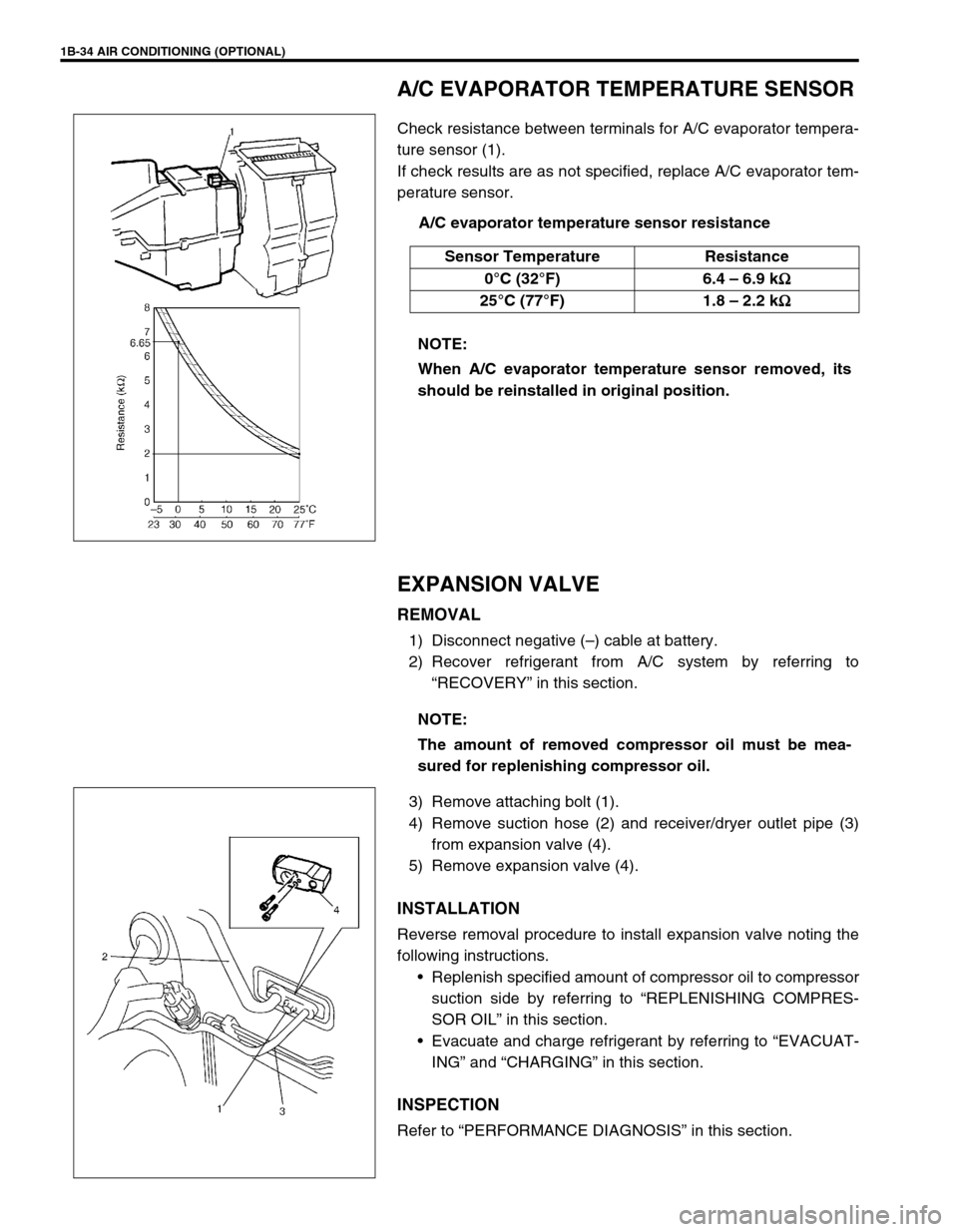
1B-34 AIR CONDITIONING (OPTIONAL)
A/C EVAPORATOR TEMPERATURE SENSOR
Check resistance between terminals for A/C evaporator tempera-
ture sensor (1).
If check results are as not specified, replace A/C evaporator tem-
perature sensor.
A/C evaporator temperature sensor resistance
EXPANSION VALVE
REMOVAL
1) Disconnect negative (–) cable at battery.
2) Recover refrigerant from A/C system by referring to
“RECOVERY” in this section.
3) Remove attaching bolt (1).
4) Remove suction hose (2) and receiver/dryer outlet pipe (3)
from expansion valve (4).
5) Remove expansion valve (4).
INSTALLATION
Reverse removal procedure to install expansion valve noting the
following instructions.
Replenish specified amount of compressor oil to compressor
suction side by referring to “REPLENISHING COMPRES-
SOR OIL” in this section.
Evacuate and charge refrigerant by referring to “EVACUAT-
ING” and “CHARGING” in this section.
INSPECTION
Refer to “PERFORMANCE DIAGNOSIS” in this section. Sensor Temperature Resistance
0°C (32°F) 6.4 – 6.9 k
Ω
ΩΩ Ω
25°C (77°F) 1.8 – 2.2 k
Ω
ΩΩ Ω
NOTE:
When A/C evaporator temperature sensor removed, its
should be reinstalled in original position.
NOTE:
The amount of removed compressor oil must be mea-
sured for replenishing compressor oil.
Page 100 of 698
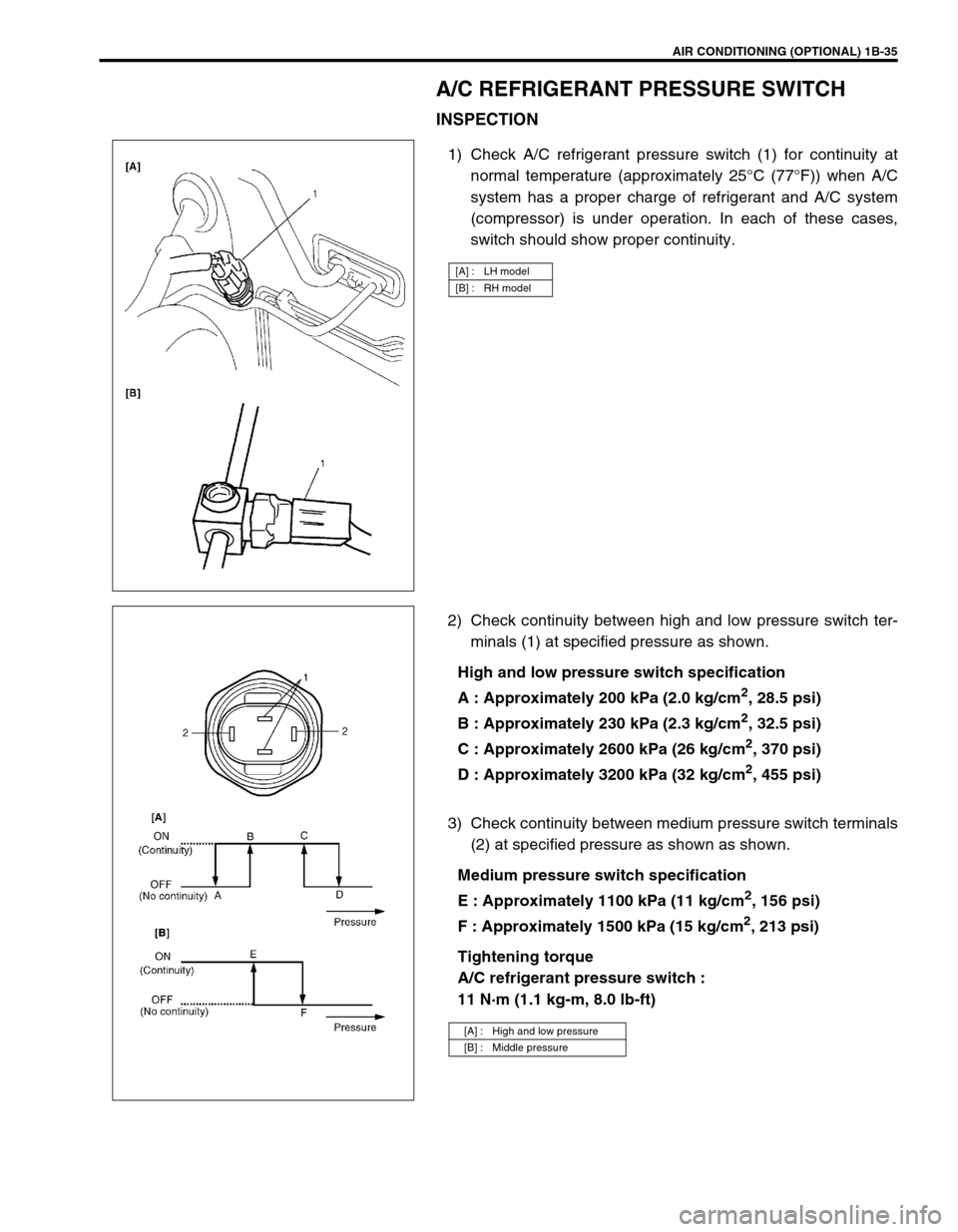
AIR CONDITIONING (OPTIONAL) 1B-35
A/C REFRIGERANT PRESSURE SWITCH
INSPECTION
1) Check A/C refrigerant pressure switch (1) for continuity at
normal temperature (approximately 25°C (77°F)) when A/C
system has a proper charge of refrigerant and A/C system
(compressor) is under operation. In each of these cases,
switch should show proper continuity.
2) Check continuity between high and low pressure switch ter-
minals (1) at specified pressure as shown.
High and low pressure switch specification
A : Approximately 200 kPa (2.0 kg/cm
2, 28.5 psi)
B : Approximately 230 kPa (2.3 kg/cm
2, 32.5 psi)
C : Approximately 2600 kPa (26 kg/cm
2, 370 psi)
D : Approximately 3200 kPa (32 kg/cm
2, 455 psi)
3) Check continuity between medium pressure switch terminals
(2) at specified pressure as shown as shown.
Medium pressure switch specification
E : Approximately 1100 kPa (11 kg/cm
2, 156 psi)
F : Approximately 1500 kPa (15 kg/cm
2, 213 psi)
Tightening torque
A/C refrigerant pressure switch :
11 N·m (1.1 kg-m, 8.0 lb-ft)
[A] : LH model
[B] : RH model
[A] : High and low pressure
[B] : Middle pressure
Page 101 of 698
1B-36 AIR CONDITIONING (OPTIONAL)
A/C SWITCH
REMOVAL AND INSTALLATION
Refer to “HEATER CONTROL ASSEMBLY” in Section 1A.
INSPECTION
Press A/C switch button and check if there is continuity
between terminals “A” and “B”.
Connect battery voltage (+) to terminal “C” and (–) to termi-
nal “A”, and then press A/C Switch button and check if indi-
cator lamp lights.
RADIATOR/CONDENSER COOLING FAN
MOTOR RELAY No.1, No.2 and No.3
INSPECTION
Refer to “RADIATOR FAN RELAY” in Section 6B.
COMPRESSOR
REMOVAL
1) Run engine at idle speed with air conditioning ON for 10 min-
utes. After that stop the engine.
2) Disconnect negative (–) cable at battery.
3) Recover refrigerant from refrigeration system by referring to
“RECOVERY” in this section.
4) Remove front bumper by referring to “FRONT BUMPER” in
Section 8.
5) Remove engine food cover (1) from vehicle body.
NOTE:
The amount of removed compressor oil must be mea-
sured for replenishing compressor oil.
Page 102 of 698
AIR CONDITIONING (OPTIONAL) 1B-37
6) Remove compressor drive belt (1) by loosening tension pul-
ley nut (2) and adjusting bolt (3).
7) Disconnect magnet clutch lead wire coupler.
8) Disconnect suction pipe (4) and discharge hose (5) from
compressor (6).
9) Remove compressor mounting bolts (7), and then remove
compressor (6) from its bracket.
INSTALLATION
Reverse removal procedure to install compressor noting the fol-
lowing instructions.
If compressor is replaced, pour new compressor oil by refer-
ring to “REPLENISHING COMPRESSOR OIL” in this sec-
tion.
Evacuate and charge system by referring to “RECOVERY”
in this section.
Adjust drive belt tension by referring to “COMPRESSOR
DRIVE BELT” in this section. NOTE:
Cap open fittings immediately to keep moisture out of
system.
Page 103 of 698
1B-38 AIR CONDITIONING (OPTIONAL)
MAGNET CLUTCH
INSPECTION
Check clutch plate and clutch pulley for wear and oil soaked
conditions respectively.
Check clutch pulley bearing for noise, wear and grease leak-
age.
Measure clutch coil for resistance at 20°C (68°F).
If the measured resistance does not remain within tolerance,
replace magnet clutch assembly.
Clutch coil resistance
: 3.4 – 4.1
Ω
ΩΩ Ω
1. Compressor thermal switch 6. Clutch coil a. Front head bolt
: Tighten bolt (a) first, and next (b)
2. Compressor body 7. Clutch pulley b. Front head bolt
: Tighten bolt (a) first, and next (b)
3. O-ring 8. Circlip c. Clutch plate bolt
4. Lip type seal 9. Circlip Tightening torque
5. Front head 10. Clutch plate Do not reuse.
Page 104 of 698
AIR CONDITIONING (OPTIONAL) 1B-39
Use an ohmmeter to check thermal switch (1) for continuity.
If it is no continuity, replace it.
REMOVAL
1) Remove compressor from vehicle. Refer to “COMPRES-
SOR” in this section.
2) Fix clutch plate (1) with special tool and remove clutch plate
bolt (2) and washer (3).
Special tool
(A) : 09991-06020
3) Using special tool, remove clutch plate (1).
Special tool
(A) : 09991-06030
4) Remove shims from shaft.
5) Using special tool, remove circlip.
Special tool
(A) : 09900-06107
6) Remove clutch coil lead wire clamp by loosening its screw
and disconnect clutch coil lead wire from thermal switch lead
wire.
Page 105 of 698
1B-40 AIR CONDITIONING (OPTIONAL)
7) Remove clutch pulley (2) with puller (1).
8) Remove clutch coil.
9) Remove circlip (1) by using special tool.
Special tool
(A) : 09900-06107
10) Remove clutch coil (2) from compressor (3).
INSTALLATION
1) Install clutch coil (2).
Protrusion on under side of clutch coil must match hole in
compressor (3) to prevent movement ant correctly locate
lead wire.
2) Using special tool, install new circlip (1) as shown.
Special tool
(A) : 09900-06107
3) Install clutch pulley (1).
a) Set clutch pulley (1) squarely over clutch pulley installation
boss.
b) Place special tool onto clutch coil bearing.
Ensure that edge rests only on inner race of bearing.
Special tool
(A) : 09991-06010
c) Install circlip. NOTE:
Be careful not to damage pulley when tapping clutch
pulley.
Be careful not to scratch bearing.
CAUTION:
Be careful not to scratch bearing seal.
Page 106 of 698
AIR CONDITIONING (OPTIONAL) 1B-41
4) Adjust clearance, between clutch plate (1) and clutch pulley
(2) by putting shim on compressor shaft.
Clearance between clutch plate and clutch pulley
“a” : 0.3 – 0.6 mm (0.012 - 0.024 in.)
5) Tighten new clutch plate bolt (2) to specified torque as
shown.
Tightening torque
Clutch plate bolt (a) : 14 N·m (1.4 kg-m, 10.5 lb-ft)
Special tool
(A) : 09991-06020
LIP TYPE SEAL
REMOVAL
1) Remove magnet clutch referring to “MAGNET CLUTCH” in
this section.
2) Remove front head (1) mounting bolts (2).
3) Remove front head (1) by pushing cylinder shaft (2).
4) Remove O-ring (3).
1. Clutch plate
3. Washer
NOTE:
Be careful not to remove cylinder from front head.