Page 35 of 558
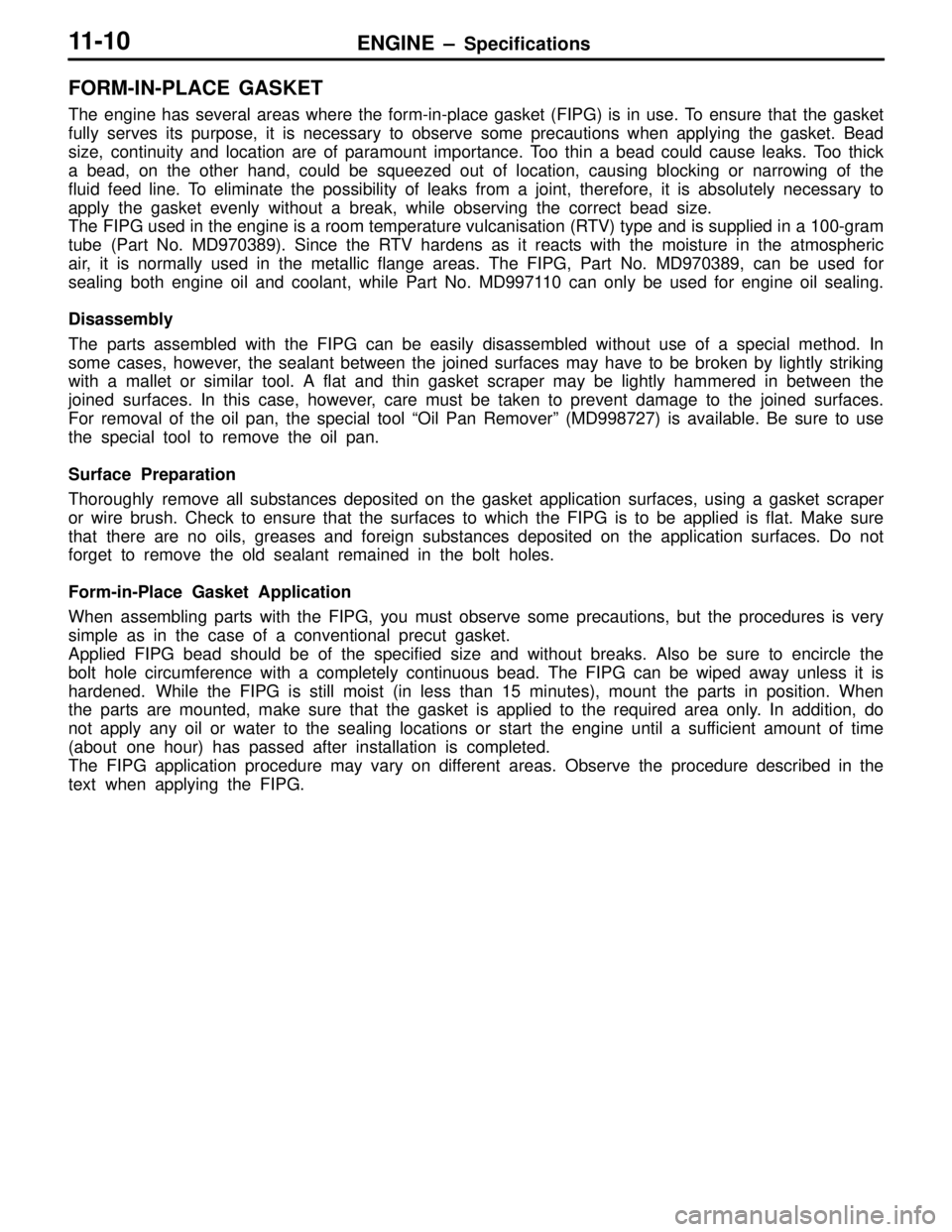
ENGINE – Specifications11-10
FORM-IN-PLACE GASKET
The engine has several areas where the form-in-place gasket (FIPG) is in use. To ensure that the gasket
fully serves its purpose, it is necessary to observe some precautions when applying the gasket. Bead
size, continuity and location are of paramount importance. Too thin a bead could cause leaks. Too thick
a bead, on the other hand, could be squeezed out of location, causing blocking or narrowing of the
fluid feed line. To eliminate the possibility of leaks from a joint, therefore, it is absolutely necessary to
apply the gasket evenly without a break, while observing the correct bead size.
The FIPG used in the engine is a room temperature vulcanisation (RTV) type and is supplied in a 100-gram
tube (Part No. MD970389). Since the RTV hardens as it reacts with the moisture in the atmospheric
air, it is normally used in the metallic flange areas. The FIPG, Part No. MD970389, can be used for
sealing both engine oil and coolant, while Part No. MD997110 can only be used for engine oil sealing.
Disassembly
The parts assembled with the FIPG can be easily disassembled without use of a special method. In
some cases, however, the sealant between the joined surfaces may have to be broken by lightly striking
with a mallet or similar tool. A flat and thin gasket scraper may be lightly hammered in between the
joined surfaces. In this case, however, care must be taken to prevent damage to the joined surfaces.
For removal of the oil pan, the special tool “Oil Pan Remover” (MD998727) is available. Be sure to use
the special tool to remove the oil pan.
Surface Preparation
Thoroughly remove all substances deposited on the gasket application surfaces, using a gasket scraper
or wire brush. Check to ensure that the surfaces to which the FIPG is to be applied is flat. Make sure
that there are no oils, greases and foreign substances deposited on the application surfaces. Do not
forget to remove the old sealant remained in the bolt holes.
Form-in-Place Gasket Application
When assembling parts with the FIPG, you must observe some precautions, but the procedures is very
simple as in the case of a conventional precut gasket.
Applied FIPG bead should be of the specified size and without breaks. Also be sure to encircle the
bolt hole circumference with a completely continuous bead. The FIPG can be wiped away unless it is
hardened. While the FIPG is still moist (in less than 15 minutes), mount the parts in position. When
the parts are mounted, make sure that the gasket is applied to the required area only. In addition, do
not apply any oil or water to the sealing locations or start the engine until a sufficient amount of time
(about one hour) has passed after installation is completed.
The FIPG application procedure may vary on different areas. Observe the procedure described in the
text when applying the FIPG.
Page 36 of 558
ENGINE – Special Tools11-11
SPECIAL TOOLS
ToolNumberNameUse
MD998781Flywheel stopperHolding of flywheel and drive plate
MD998778Crankshaft
sprocket pullerRemoval of crankshaft sprocket
MD998719Pulley holder pinHolding camshaft sprocket
MB990767Crankshaft pulley
holder
MD998785Sprocket stopperHolding silent shaft sprocket
MD998767Tensioner puller
socket wrenchAdjustment of timing belt tension
MD998738Set screw
MD998713Camshaft oil seal
installerInstallation of camshaft oil seal
MD998442Lash adjuster wireAir bleeding of lash adjuster
Page 37 of 558
ENGINE – Special Tools11-12
Tool UseName Number
MB991654Cylinder head bolt
wrench (12)Removal and installation of cylinder head bolt
MD998772Valve spring
compressorRemoval and installation of valve and related
parts
MD998735Valve spring
compressor
MD998737Valve stem seal
installerInstallation of valve stem seal
MD998727Oil pan removerRemoval of oil pan
MD998162Plug wrenchRemoval and installation of front case cap plug
Use with MD998783.
MD998783Plug wrench
retainerRemoval and installation of front case cap plug
MD998371Silent shaft bearing
pullerRemoval of counterbalance shaft front bearing
MD998372Silent shaft bearing
pullerRemoval of counterbalance shaft rear bearing
Page 38 of 558
ENGINE – Special Tools11-13
Tool UseName Number
MB991603Silent shaft bearing
puller stopperGuide stopper for removal and installation of
counterbalance shaft rear bearing
Use with MD998372.
MD998705Silent shaft bearing
installerInstallation of counterbalance shaft front and
rear bearing
MD998375Crankshaft front
seal installerInstallation of crankshaft front oil seal
MD998285Crankshaft front oil
seal guideGuide for installation of crankshaft front oil seal
Use with MD998375.
MD998780Piston setting toolRemoval and installation of piston pin
MB990938HandleInstallation of crankshaft rear oil seal
MD998776Crankshaft rear oil
seal installer
Page 39 of 558
ENGINE – Alternator and Ignition System11-14
ALTERNATOR AND IGNITION SYSTEM
REMOVAL AND INSTALLATION
44 Nm 10 Nm
25 Nm
21 Nm
9 Nm 13 Nm
23 Nm
25 Nm 3 Nm
2
1
34
5 67
89
10
11
12
13 1415
16
Removal steps
1. Oil level gauge
2. O-ring
3. Oil level gauge guide
4. O-ring
5. Water pump pulley
6. Alternator brace
7. Alternator
8. Crankshaft pulley9. Center cover
10. Spark plug cable
11. Ignition coil
12. Spark plug
13. Breather hose
14. PCV hose
15. PCV valve
16. PCV valve gasket
Page 40 of 558
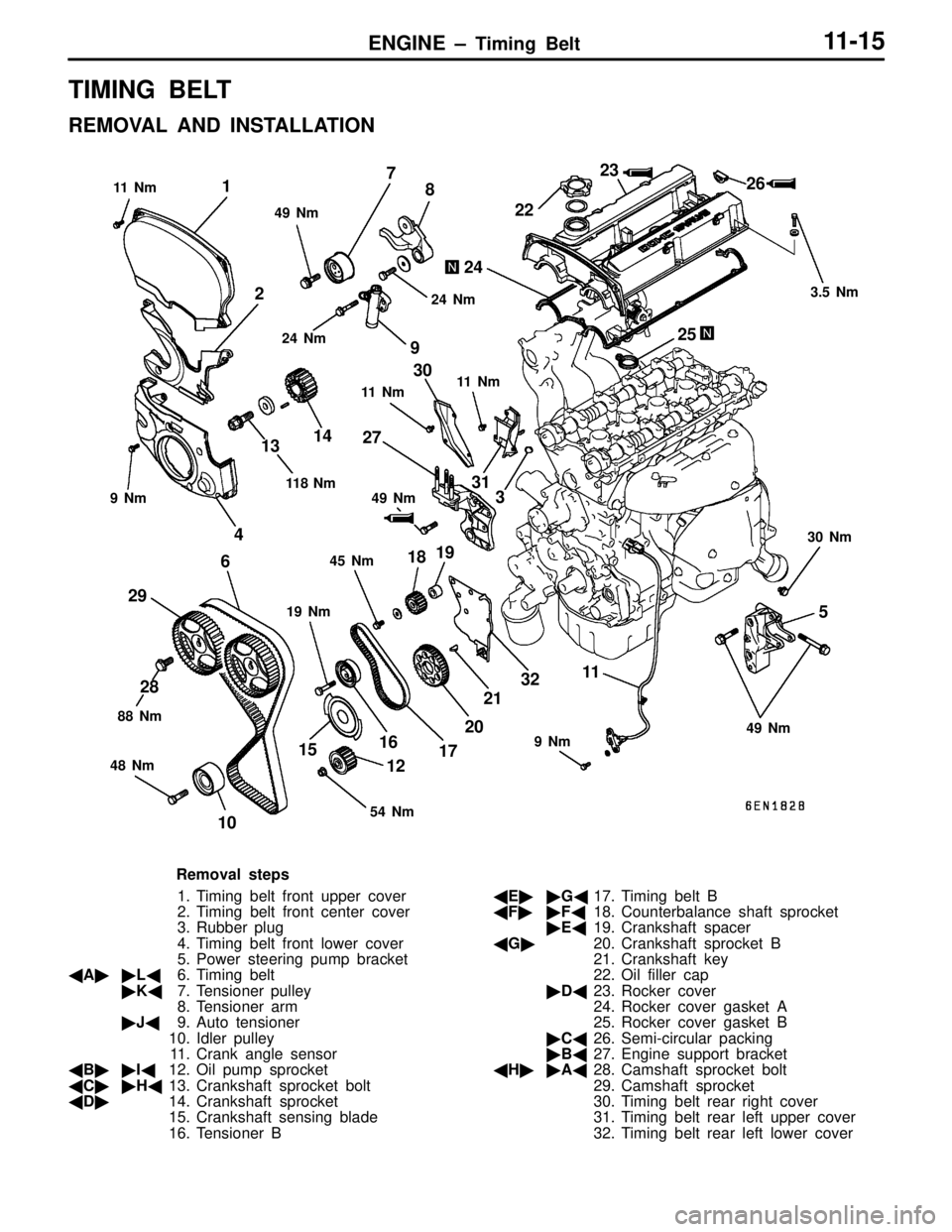
ENGINE – Timing Belt11-15
TIMING BELT
REMOVAL AND INSTALLATION
1
2
3
4
5 67
8
9
1011
12 1314
1516
17 1819
20212223
24
2526
27
28 2930
31
32
9 Nm
9 Nm 49 Nm 11 N m
11 N m
19 Nm 3.5 Nm
30 Nm
45 Nm 49 Nm 11 8 N m
88 Nm
48 Nm 49 Nm 11 N m
24 Nm
24 Nm
54 Nm
Removal steps
1. Timing belt front upper cover
2. Timing belt front center cover
3. Rubber plug
4. Timing belt front lower cover
5. Power steering pump bracket
AL6. Timing belt
K7. Tensioner pulley
8. Tensioner arm
J9. Auto tensioner
10. Idler pulley
11. Crank angle sensor
BI12. Oil pump sprocket
CH13. Crankshaft sprocket bolt
D14. Crankshaft sprocket
15. Crankshaft sensing blade
16. Tensioner BEG17. Timing belt B
FF18. Counterbalance shaft sprocket
E19. Crankshaft spacer
G20. Crankshaft sprocket B
21. Crankshaft key
22. Oil filler cap
D23. Rocker cover
24. Rocker cover gasket A
25. Rocker cover gasket B
C26. Semi-circular packing
B27. Engine support bracket
HA28. Camshaft sprocket bolt
29. Camshaft sprocket
30. Timing belt rear right cover
31. Timing belt rear left upper cover
32. Timing belt rear left lower cover
Page 41 of 558
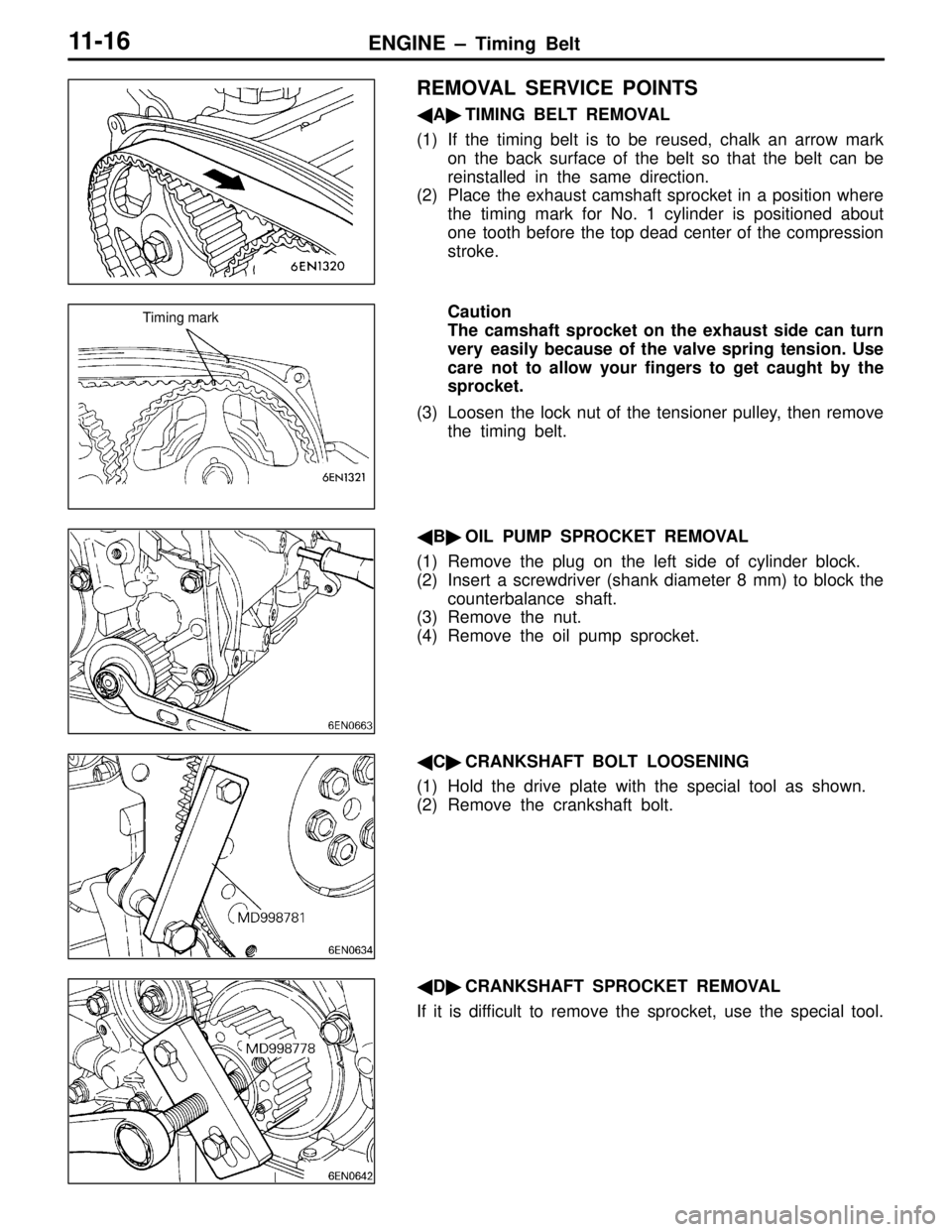
ENGINE – Timing Belt11-16
REMOVAL SERVICE POINTS
ATIMING BELT REMOVAL
(1) If the timing belt is to be reused, chalk an arrow mark
on the back surface of the belt so that the belt can be
reinstalled in the same direction.
(2) Place the exhaust camshaft sprocket in a position where
the timing mark for No. 1 cylinder is positioned about
one tooth before the top dead center of the compression
stroke.
Caution
The camshaft sprocket on the exhaust side can turn
very easily because of the valve spring tension. Use
care not to allow your fingers to get caught by the
sprocket.
(3) Loosen the lock nut of the tensioner pulley, then remove
the timing belt.
BOIL PUMP SPROCKET REMOVAL
(1) Remove the plug on the left side of cylinder block.
(2) Insert a screwdriver (shank diameter 8 mm) to block the
counterbalance shaft.
(3) Remove the nut.
(4) Remove the oil pump sprocket.
CCRANKSHAFT BOLT LOOSENING
(1) Hold the drive plate with the special tool as shown.
(2) Remove the crankshaft bolt.
DCRANKSHAFT SPROCKET REMOVAL
If it is difficult to remove the sprocket, use the special tool.
Timing mark
Page 42 of 558
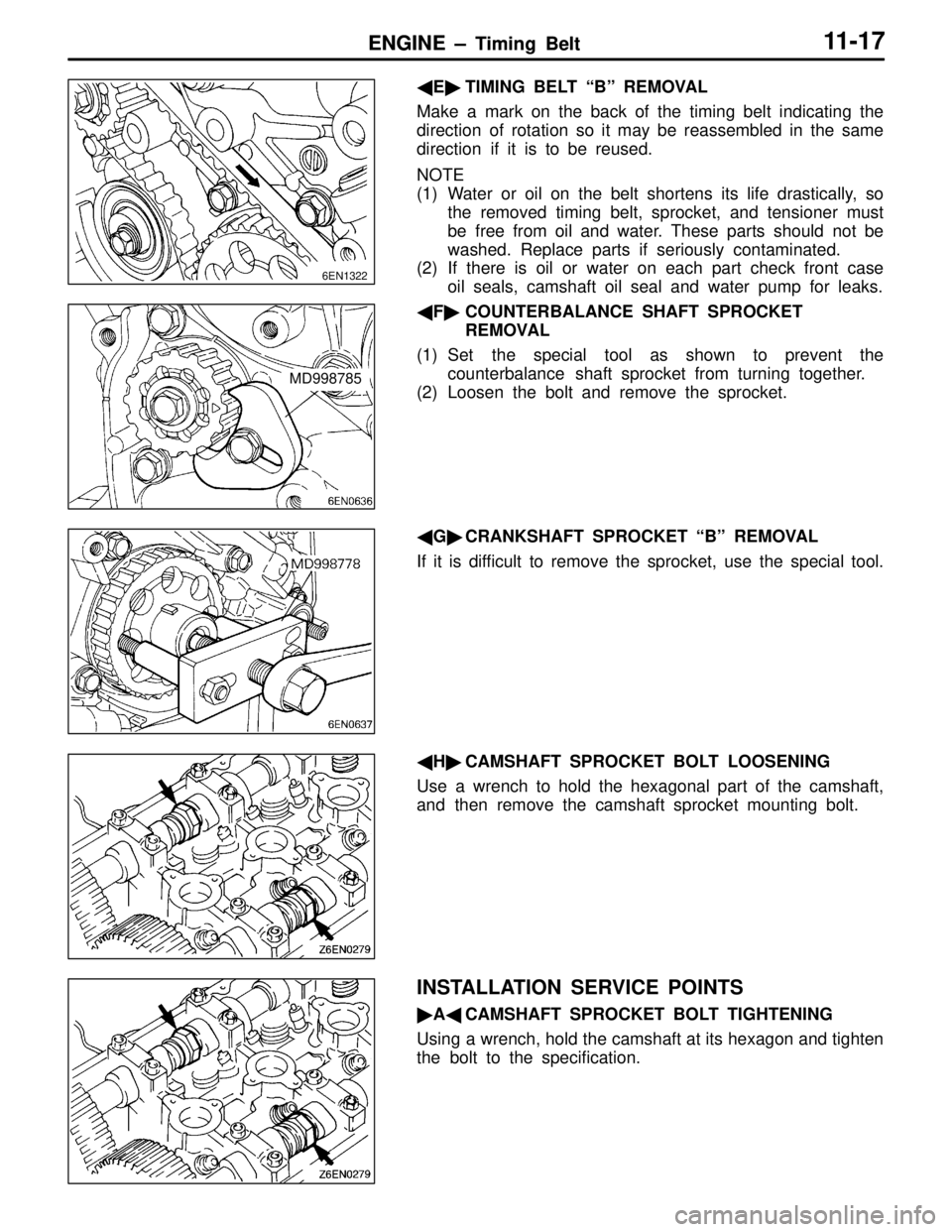
ENGINE – Timing BeltENGINE – Timing Belt11-17
ETIMING BELT “B” REMOVAL
Make a mark on the back of the timing belt indicating the
direction of rotation so it may be reassembled in the same
direction if it is to be reused.
NOTE
(1) Water or oil on the belt shortens its life drastically, so
the removed timing belt, sprocket, and tensioner must
be free from oil and water. These parts should not be
washed. Replace parts if seriously contaminated.
(2) If there is oil or water on each part check front case
oil seals, camshaft oil seal and water pump for leaks.
FCOUNTERBALANCE SHAFT SPROCKET
REMOVAL
(1) Set the special tool as shown to prevent the
counterbalance shaft sprocket from turning together.
(2) Loosen the bolt and remove the sprocket.
GCRANKSHAFT SPROCKET “B” REMOVAL
If it is difficult to remove the sprocket, use the special tool.
HCAMSHAFT SPROCKET BOLT LOOSENING
Use a wrench to hold the hexagonal part of the camshaft,
and then remove the camshaft sprocket mounting bolt.
INSTALLATION SERVICE POINTS
ACAMSHAFT SPROCKET BOLT TIGHTENING
Using a wrench, hold the camshaft at its hexagon and tighten
the bolt to the specification.
6EN1322
MD998785