Page 46 of 558
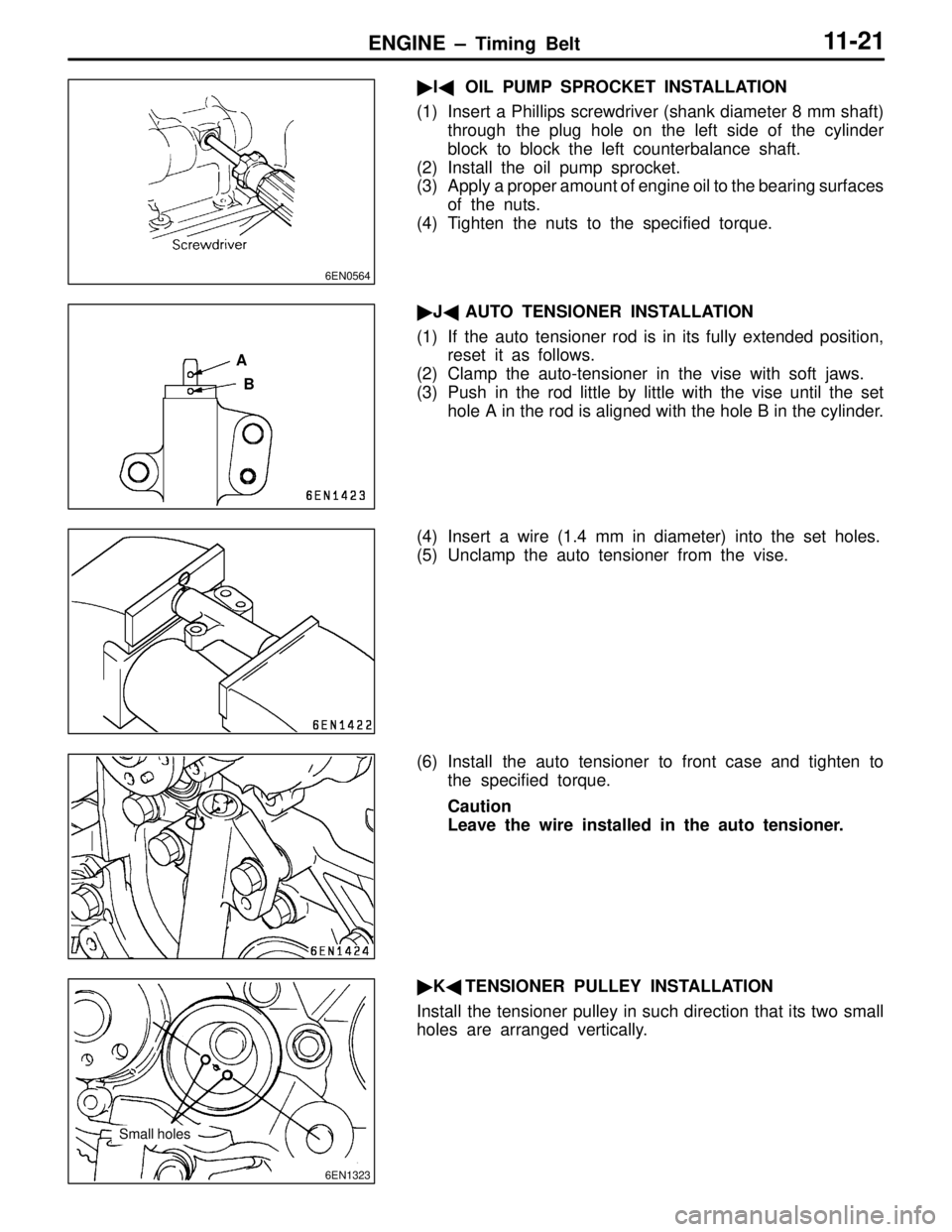
ENGINE – Timing Belt11-21
IOIL PUMP SPROCKET INSTALLATION
(1) Insert a Phillips screwdriver (shank diameter 8 mm shaft)
through the plug hole on the left side of the cylinder
block to block the left counterbalance shaft.
(2) Install the oil pump sprocket.
(3) Apply a proper amount of engine oil to the bearing surfaces
of the nuts.
(4) Tighten the nuts to the specified torque.
JAUTO TENSIONER INSTALLATION
(1) If the auto tensioner rod is in its fully extended position,
reset it as follows.
(2) Clamp the auto-tensioner in the vise with soft jaws.
(3) Push in the rod little by little with the vise until the set
hole A in the rod is aligned with the hole B in the cylinder.
(4) Insert a wire (1.4 mm in diameter) into the set holes.
(5) Unclamp the auto tensioner from the vise.
(6) Install the auto tensioner to front case and tighten to
the specified torque.
Caution
Leave the wire installed in the auto tensioner.
KTENSIONER PULLEY INSTALLATION
Install the tensioner pulley in such direction that its two small
holes are arranged vertically.
6EN0564
A
B
6EN1323
Small holes
Page 50 of 558
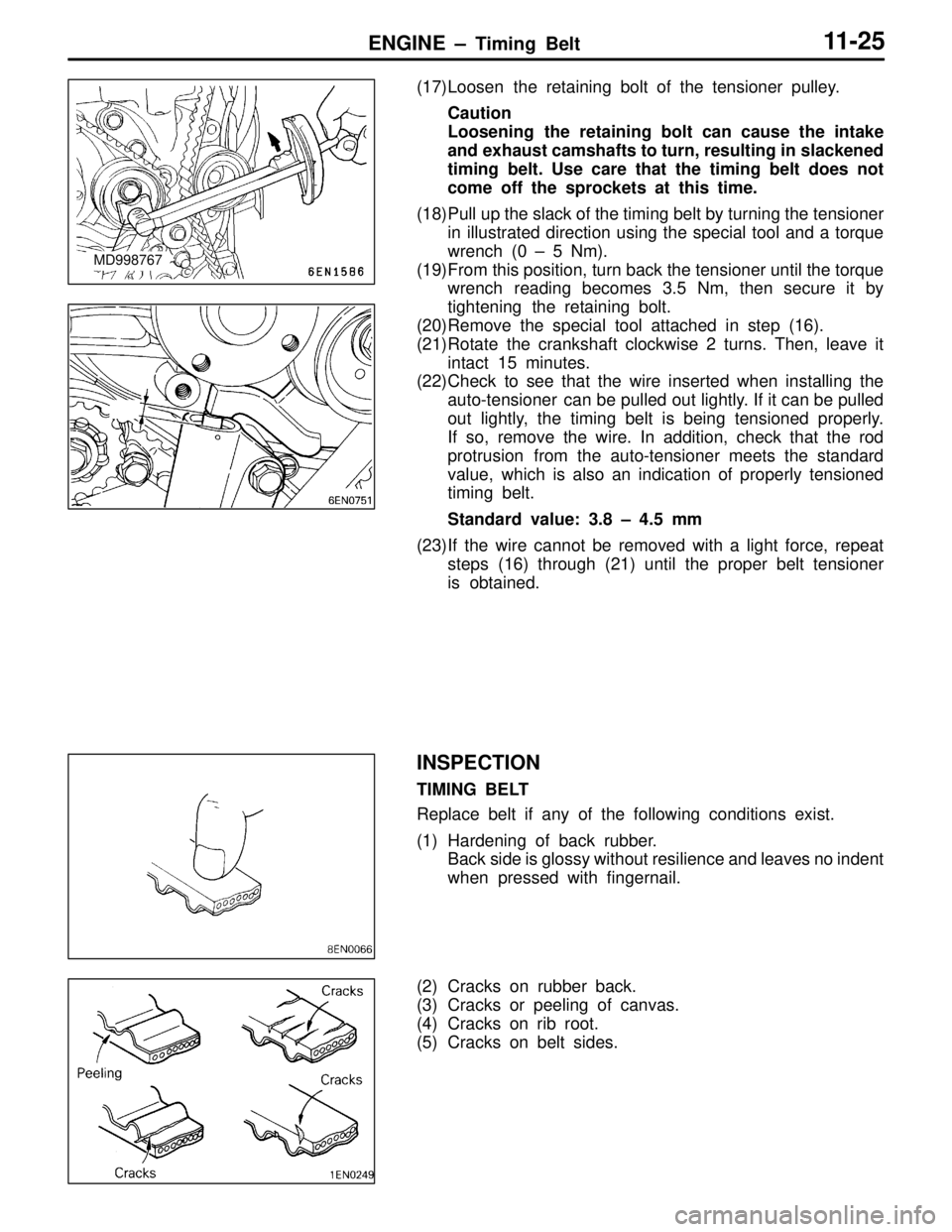
ENGINE – Timing Belt11-25
(17)Loosen the retaining bolt of the tensioner pulley.
Caution
Loosening the retaining bolt can cause the intake
and exhaust camshafts to turn, resulting in slackened
timing belt. Use care that the timing belt does not
come off the sprockets at this time.
(18)Pull up the slack of the timing belt by turning the tensioner
in illustrated direction using the special tool and a torque
wrench (0 – 5 Nm).
(19)From this position, turn back the tensioner until the torque
wrench reading becomes 3.5 Nm, then secure it by
tightening the retaining bolt.
(20)Remove the special tool attached in step (16).
(21)Rotate the crankshaft clockwise 2 turns. Then, leave it
intact 15 minutes.
(22)Check to see that the wire inserted when installing the
auto-tensioner can be pulled out lightly. If it can be pulled
out lightly, the timing belt is being tensioned properly.
If so, remove the wire. In addition, check that the rod
protrusion from the auto-tensioner meets the standard
value, which is also an indication of properly tensioned
timing belt.
Standard value: 3.8 – 4.5 mm
(23)If the wire cannot be removed with a light force, repeat
steps (16) through (21) until the proper belt tensioner
is obtained.
INSPECTION
TIMING BELT
Replace belt if any of the following conditions exist.
(1) Hardening of back rubber.
Back side is glossy without resilience and leaves no indent
when pressed with fingernail.
(2) Cracks on rubber back.
(3) Cracks or peeling of canvas.
(4) Cracks on rib root.
(5) Cracks on belt sides.
MD998767
Page 55 of 558
ENGINE – Secondary Air System and Intake Manifold11-30
INSTALLATION SERVICE POINTS
AAIR CONTROL VALVE BRACKET INSTALLATION
(1) Attach the air control valve bracket and the engine hanger
to the intake manifold using bolts and nuts with which
the intake manifold is also installed to the engine.
(2) Tighten the bolts and nuts to the specified torque in the
sequence given in the illustration.
BAIR PIPE ASSEMBLY INSTALLATION
(1) Install the air pipe assembly to the exhaust manifold and
to the air control valve and secure it provisionally by
tightening the fasteners handtight.
(2) Tighten the fasteners to the specified torque in the
sequence given in the illustration.
(3)
(2) (1)
(3)
(2)(1)(4)
Page 57 of 558
ENGINE – Exhaust Manifold11-32
INSTALLATION SERVICE POINTS
AEXHAUST MANIFOLD INSTALLATION
Tighten the exhaust manifold mounting nuts to the specified
torque in the sequence given in the illustration.
BGASKET / OIL RETURN GASKET INSTALLATION
EVOLUTION IV AND V
Install the gasket with the silicon-printed side toward the oil
pan and with the tabbed end directed as shown.
EVOLUTION VI
(1) Install the gasket with the tabbed end directed as shown.
(2) Apply sealant to both sides of the oil return pipe gasket
and leave it for 20 minutes to dry before installing. Tighten
the mounting bolts to the specified torque.
Specified sealant:
3M
TM AAD Part No. 8731 or equivalent
NOTE
If mounting bolts with head mark 7 have been used,
be sure to replace them with bolts having head mark
10.
1234 5 6
789
Timing belt side
Oil pan
Oil return
pipe gasket Silicon print
Timing belt side
Oil pan
Oil return
pipe gasket
Oil pan
Oil return
pipe
Gasket
Page 71 of 558
ENGINE – Cylinder Head and Valves11-46
BVALVE SPRING INSTALLATION
Direct the valve spring end with identification color toward
the spring retainer.
CRETAINER LOCK INSTALLATION
The valve spring, if excessively compressed, causes the
bottom end of the retainer to be in contact with, and damage,
the stem seal.
DCYLINDER HEAD BOLT INSTALLATION
(1) When installing the cylinder head bolts, check that the
shank length of each bolt meets the limit. If the limit is
exceeded, replace the bolt.
Limit: Max. 99.4 mm
(2) Apply engine oil to the bolt threads and to the washers.
(3) Using the special tool (MB991654) and according to the
tightening sequence, tighten the bolts to the specified
torque.
Tightening torque: 78 Nm
(4) Loosen all bolts fully.
(5) Retighten the loosened bolts to a torque of 20 Nm in
the specified tightening sequence.
MD998772
MD998735
6EN0782
Shank length
Timing belt side
Page 81 of 558
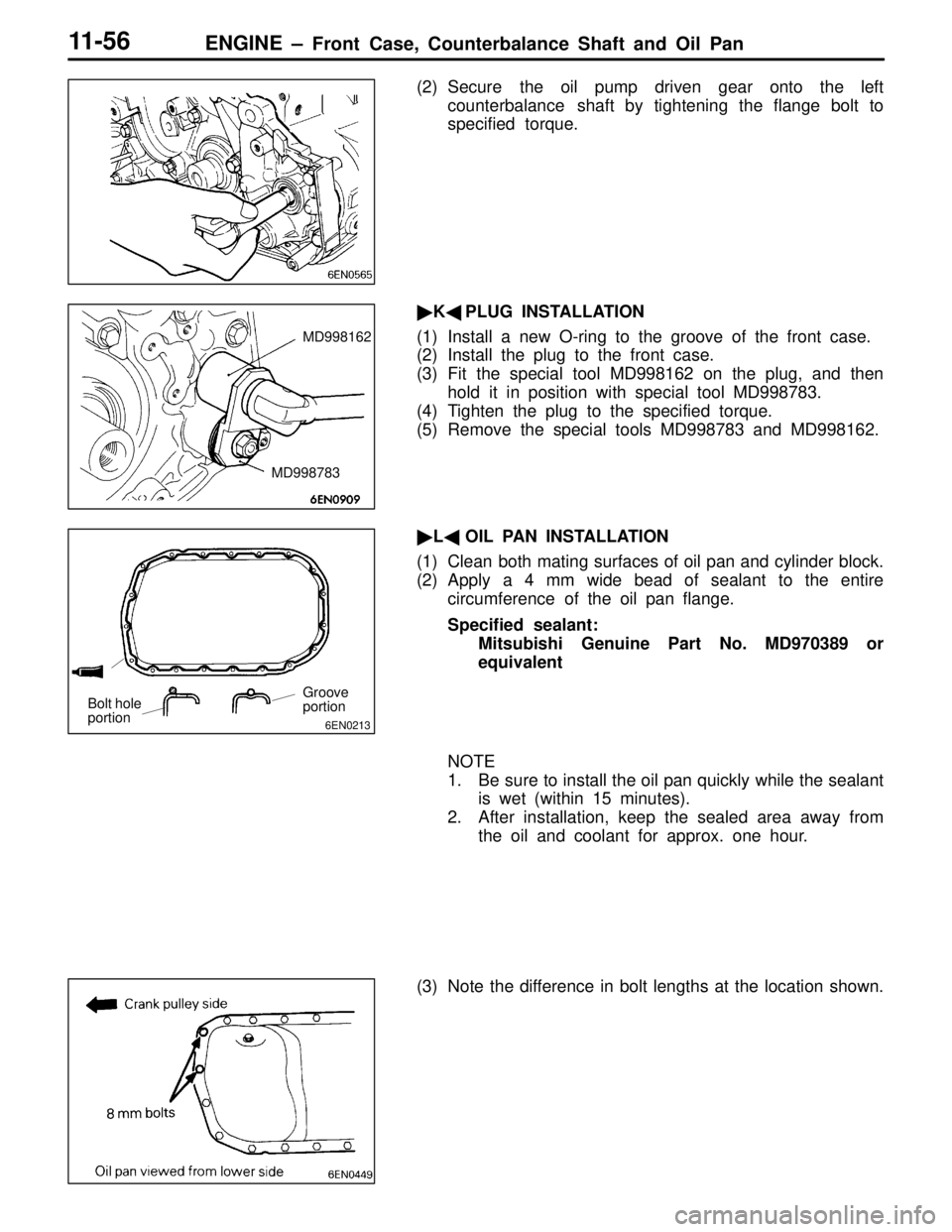
ENGINE – Front Case, Counterbalance Shaft and Oil Pan11-56
(2) Secure the oil pump driven gear onto the left
counterbalance shaft by tightening the flange bolt to
specified torque.
KPLUG INSTALLATION
(1) Install a new O-ring to the groove of the front case.
(2) Install the plug to the front case.
(3) Fit the special tool MD998162 on the plug, and then
hold it in position with special tool MD998783.
(4) Tighten the plug to the specified torque.
(5) Remove the special tools MD998783 and MD998162.
LOIL PAN INSTALLATION
(1) Clean both mating surfaces of oil pan and cylinder block.
(2) Apply a 4 mm wide bead of sealant to the entire
circumference of the oil pan flange.
Specified sealant:
Mitsubishi Genuine Part No. MD970389 or
equivalent
NOTE
1. Be sure to install the oil pan quickly while the sealant
is wet (within 15 minutes).
2. After installation, keep the sealed area away from
the oil and coolant for approx. one hour.
(3) Note the difference in bolt lengths at the location shown.
MD998162
MD998783
6EN0213
Bolt hole
portionGroove
portion
Page 82 of 558
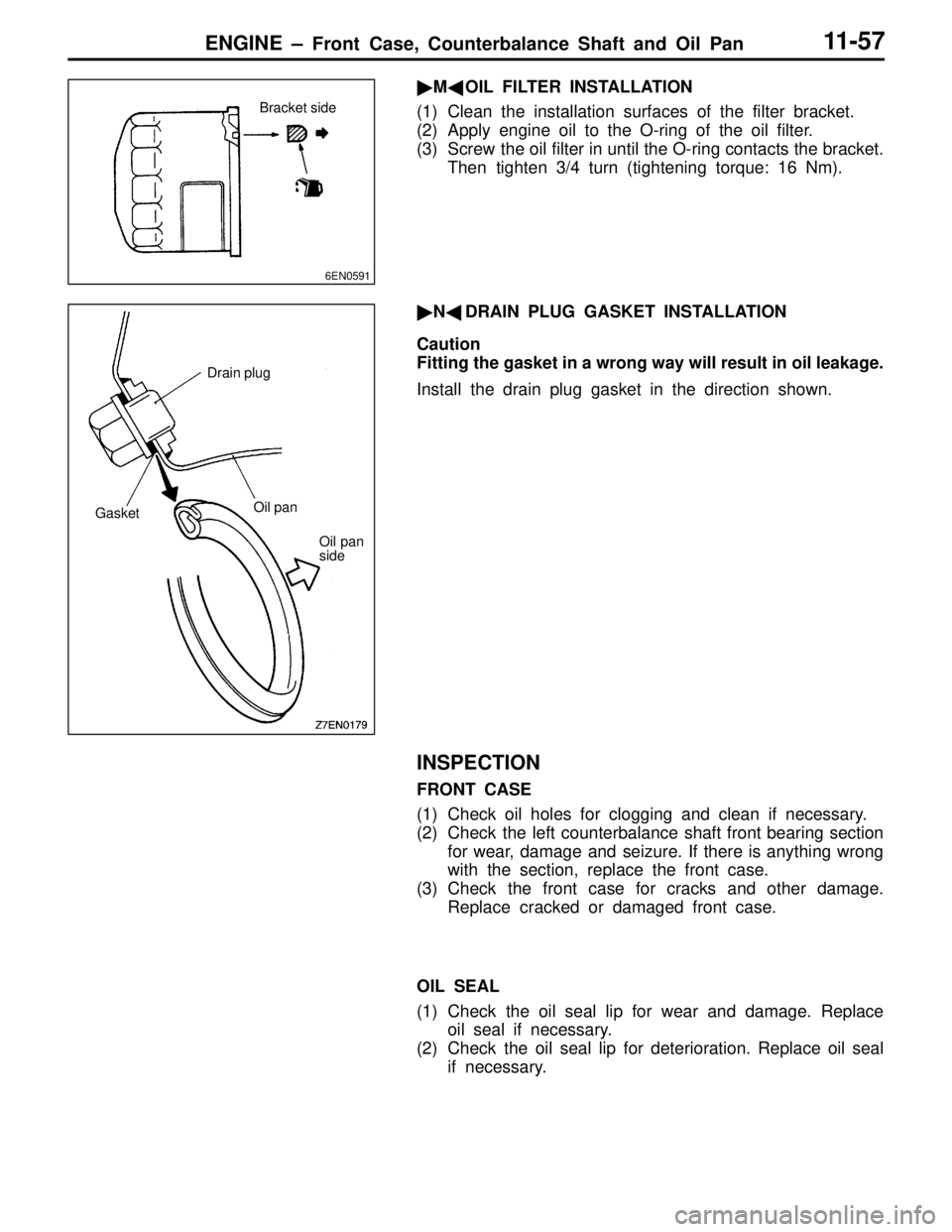
ENGINE – Front Case, Counterbalance Shaft and Oil Pan11-57
MOIL FILTER INSTALLATION
(1) Clean the installation surfaces of the filter bracket.
(2) Apply engine oil to the O-ring of the oil filter.
(3) Screw the oil filter in until the O-ring contacts the bracket.
Then tighten 3/4 turn (tightening torque: 16 Nm).
NDRAIN PLUG GASKET INSTALLATION
Caution
Fitting the gasket in a wrong way will result in oil leakage.
Install the drain plug gasket in the direction shown.
INSPECTION
FRONT CASE
(1) Check oil holes for clogging and clean if necessary.
(2) Check the left counterbalance shaft front bearing section
for wear, damage and seizure. If there is anything wrong
with the section, replace the front case.
(3) Check the front case for cracks and other damage.
Replace cracked or damaged front case.
OIL SEAL
(1) Check the oil seal lip for wear and damage. Replace
oil seal if necessary.
(2) Check the oil seal lip for deterioration. Replace oil seal
if necessary.
6EN0591
Bracket side
Oil pan
side Drain plug
GasketOil pan
Page 90 of 558
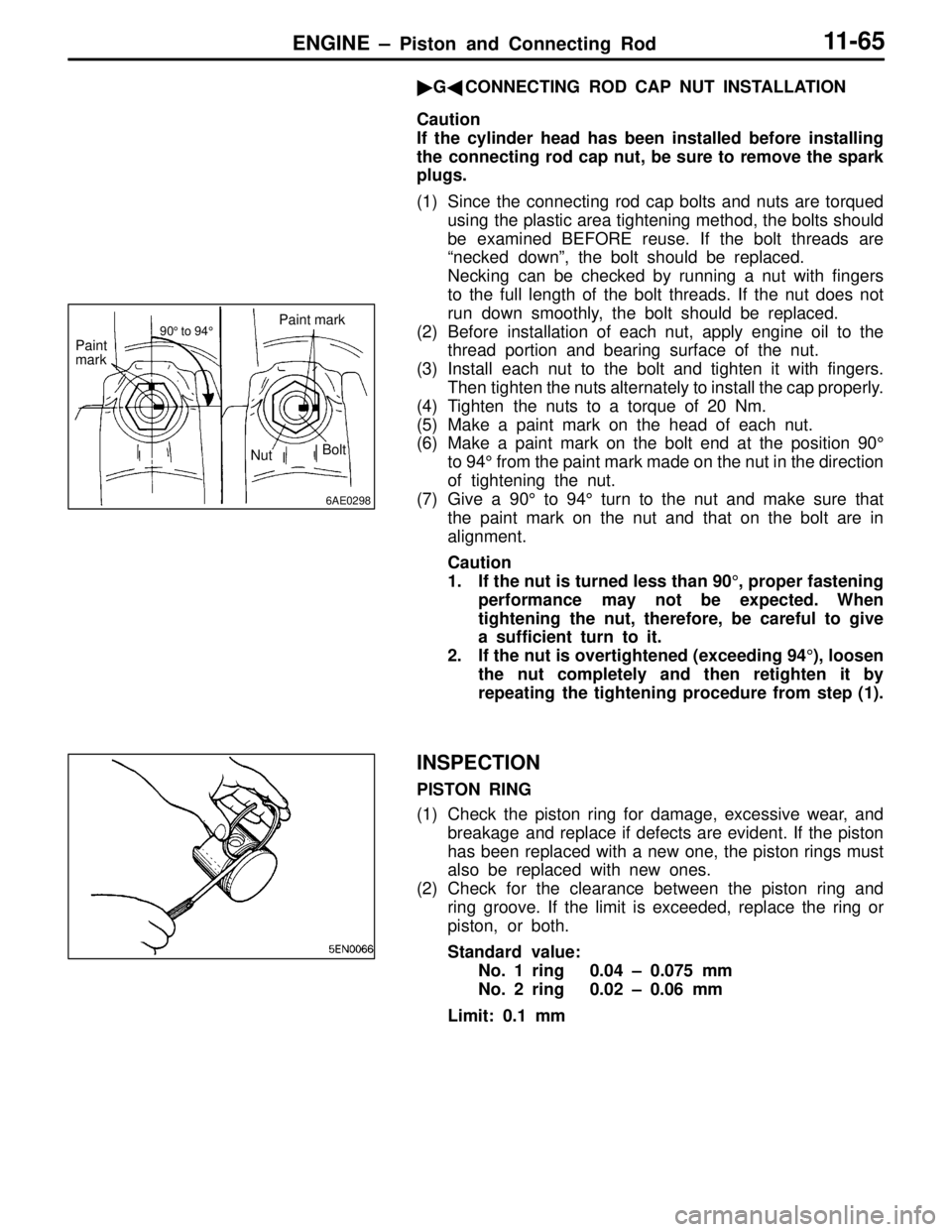
ENGINE – Piston and Connecting Rod11-65
GCONNECTING ROD CAP NUT INSTALLATION
Caution
If the cylinder head has been installed before installing
the connecting rod cap nut, be sure to remove the spark
plugs.
(1) Since the connecting rod cap bolts and nuts are torqued
using the plastic area tightening method, the bolts should
be examined BEFORE reuse. If the bolt threads are
“necked down”, the bolt should be replaced.
Necking can be checked by running a nut with fingers
to the full length of the bolt threads. If the nut does not
run down smoothly, the bolt should be replaced.
(2) Before installation of each nut, apply engine oil to the
thread portion and bearing surface of the nut.
(3) Install each nut to the bolt and tighten it with fingers.
Then tighten the nuts alternately to install the cap properly.
(4) Tighten the nuts to a torque of 20 Nm.
(5) Make a paint mark on the head of each nut.
(6) Make a paint mark on the bolt end at the position 90°
to 94° from the paint mark made on the nut in the direction
of tightening the nut.
(7) Give a 90° to 94° turn to the nut and make sure that
the paint mark on the nut and that on the bolt are in
alignment.
Caution
1. If the nut is turned less than 90°, proper fastening
performance may not be expected. When
tightening the nut, therefore, be careful to give
a sufficient turn to it.
2. If the nut is overtightened (exceeding 94°), loosen
the nut completely and then retighten it by
repeating the tightening procedure from step (1).
INSPECTION
PISTON RING
(1) Check the piston ring for damage, excessive wear, and
breakage and replace if defects are evident. If the piston
has been replaced with a new one, the piston rings must
also be replaced with new ones.
(2) Check for the clearance between the piston ring and
ring groove. If the limit is exceeded, replace the ring or
piston, or both.
Standard value:
No. 1 ring 0.04 – 0.075 mm
No. 2 ring 0.02 – 0.06 mm
Limit: 0.1 mm
6AE0298
90° to 94°Paint mark
Paint
mark
NutBolt