Page 186 of 667
ENGINE
27
OVERHAUL
7.Noting their fitted positions, remove 8 bolts
securing timing chain cover.
8.Remove timing chain cover.
NOTE: Dowel located.
9.Remove bolt securing oil pump drive sprocket.
10.Remove oil pump drive sprocket.
11.Remove camshaft and crankshaft sprockets
together with timing and oil pump drive chains.
12.Remove Woodruff key from crankshaft.
13.Remove 2 bolts and remove timing chain fixed
guide.
14.Remove bolt and remove timing chain adjustable
guide.
15.Remove bolt and remove timing chain lubrication
jet.
16.Using toolLRT-12-092, remove and discard oil
seal from timing cover.
ProCarManuals.com
Page 187 of 667
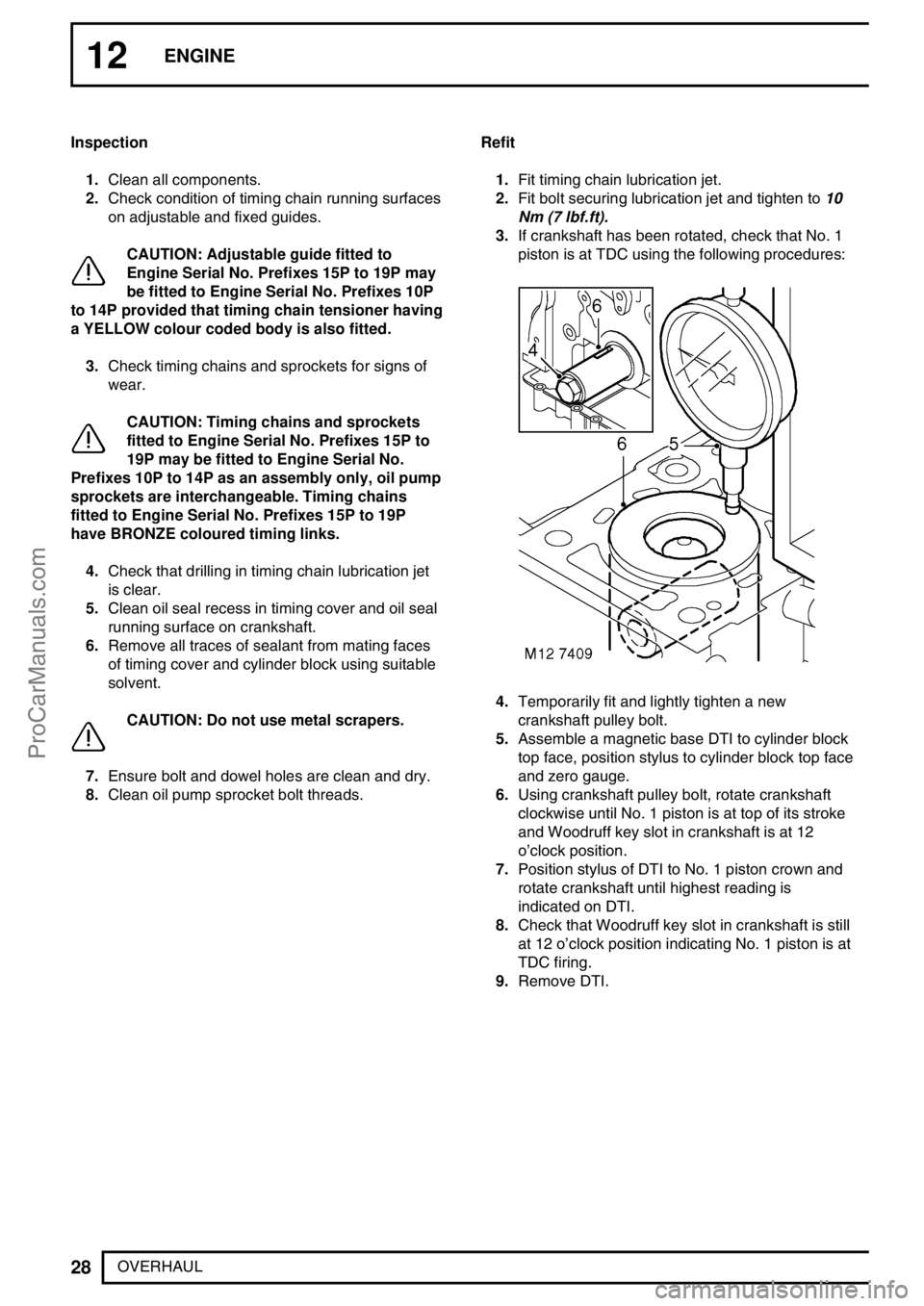
12ENGINE
28
OVERHAUL Inspection
1.Clean all components.
2.Check condition of timing chain running surfaces
on adjustable and fixed guides.
CAUTION: Adjustable guide fitted to
Engine Serial No. Prefixes 15P to 19P may
be fitted to Engine Serial No. Prefixes 10P
to 14P provided that timing chain tensioner having
a YELLOW colour coded body is also fitted.
3.Check timing chains and sprockets for signs of
wear.
CAUTION: Timing chains and sprockets
fitted to Engine Serial No. Prefixes 15P to
19P may be fitted to Engine Serial No.
Prefixes 10P to 14P as an assembly only, oil pump
sprockets are interchangeable. Timing chains
fitted to Engine Serial No. Prefixes 15P to 19P
have BRONZE coloured timing links.
4.Check that drilling in timing chain lubrication jet
is clear.
5.Clean oil seal recess in timing cover and oil seal
running surface on crankshaft.
6.Remove all traces of sealant from mating faces
of timing cover and cylinder block using suitable
solvent.
CAUTION: Do not use metal scrapers.
7.Ensure bolt and dowel holes are clean and dry.
8.Clean oil pump sprocket bolt threads.Refit
1.Fit timing chain lubrication jet.
2.Fit bolt securing lubrication jet and tighten to10
Nm (7 lbf.ft).
3.If crankshaft has been rotated, check that No. 1
piston is at TDC using the following procedures:
4.Temporarily fit and lightly tighten a new
crankshaft pulley bolt.
5.Assemble a magnetic base DTI to cylinder block
top face, position stylus to cylinder block top face
and zero gauge.
6.Using crankshaft pulley bolt, rotate crankshaft
clockwise until No. 1 piston is at top of its stroke
and Woodruff key slot in crankshaft is at 12
o’clock position.
7.Position stylus of DTI to No. 1 piston crown and
rotate crankshaft until highest reading is
indicated on DTI.
8.Check that Woodruff key slot in crankshaft is still
at 12 o’clock position indicating No. 1 piston is at
TDC firing.
9.Remove DTI.
ProCarManuals.com
Page 188 of 667
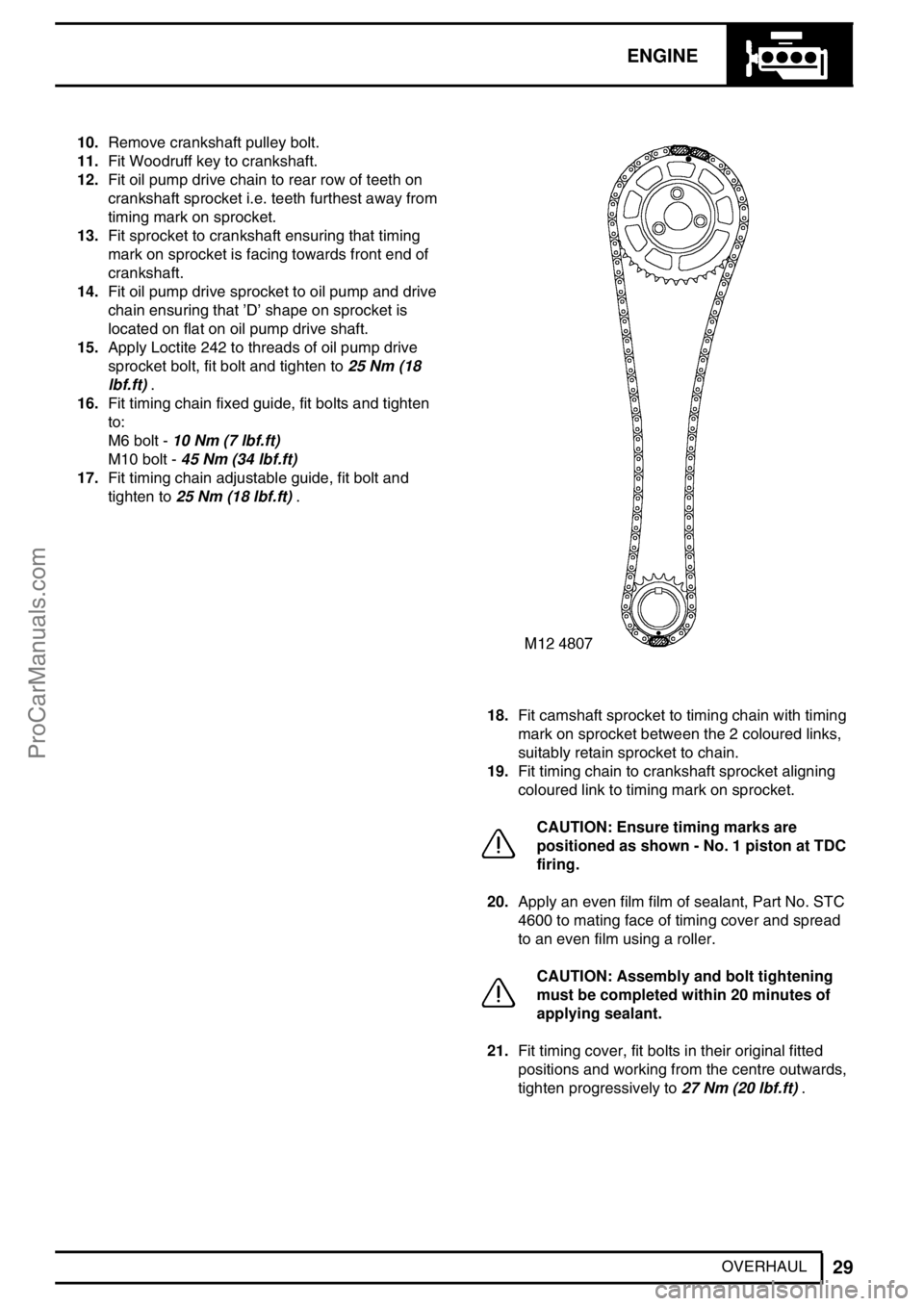
ENGINE
29
OVERHAUL 10.Remove crankshaft pulley bolt.
11.Fit Woodruff key to crankshaft.
12.Fit oil pump drive chain to rear row of teeth on
crankshaft sprocket i.e. teeth furthest away from
timing mark on sprocket.
13.Fit sprocket to crankshaft ensuring that timing
mark on sprocket is facing towards front end of
crankshaft.
14.Fit oil pump drive sprocket to oil pump and drive
chain ensuring that’D’shape on sprocket is
located on flat on oil pump drive shaft.
15.Apply Loctite 242 to threads of oil pump drive
sprocket bolt, fit bolt and tighten to25 Nm (18
lbf.ft).
16.Fit timing chain fixed guide, fit bolts and tighten
to:
M6 bolt -10 Nm (7 lbf.ft)
M10 bolt -45 Nm (34 lbf.ft)
17.Fit timing chain adjustable guide, fit bolt and
tighten to25 Nm (18 lbf.ft).
18.Fit camshaft sprocket to timing chain with timing
mark on sprocket between the 2 coloured links,
suitably retain sprocket to chain.
19.Fit timing chain to crankshaft sprocket aligning
coloured link to timing mark on sprocket.
CAUTION: Ensure timing marks are
positioned as shown - No. 1 piston at TDC
firing.
20.Apply an even film film of sealant, Part No. STC
4600 to mating face of timing cover and spread
to an even film using a roller.
CAUTION: Assembly and bolt tightening
must be completed within 20 minutes of
applying sealant.
21.Fit timing cover, fit bolts in their original fitted
positions and working from the centre outwards,
tighten progressively to27 Nm (20 lbf.ft).
ProCarManuals.com
Page 268 of 667
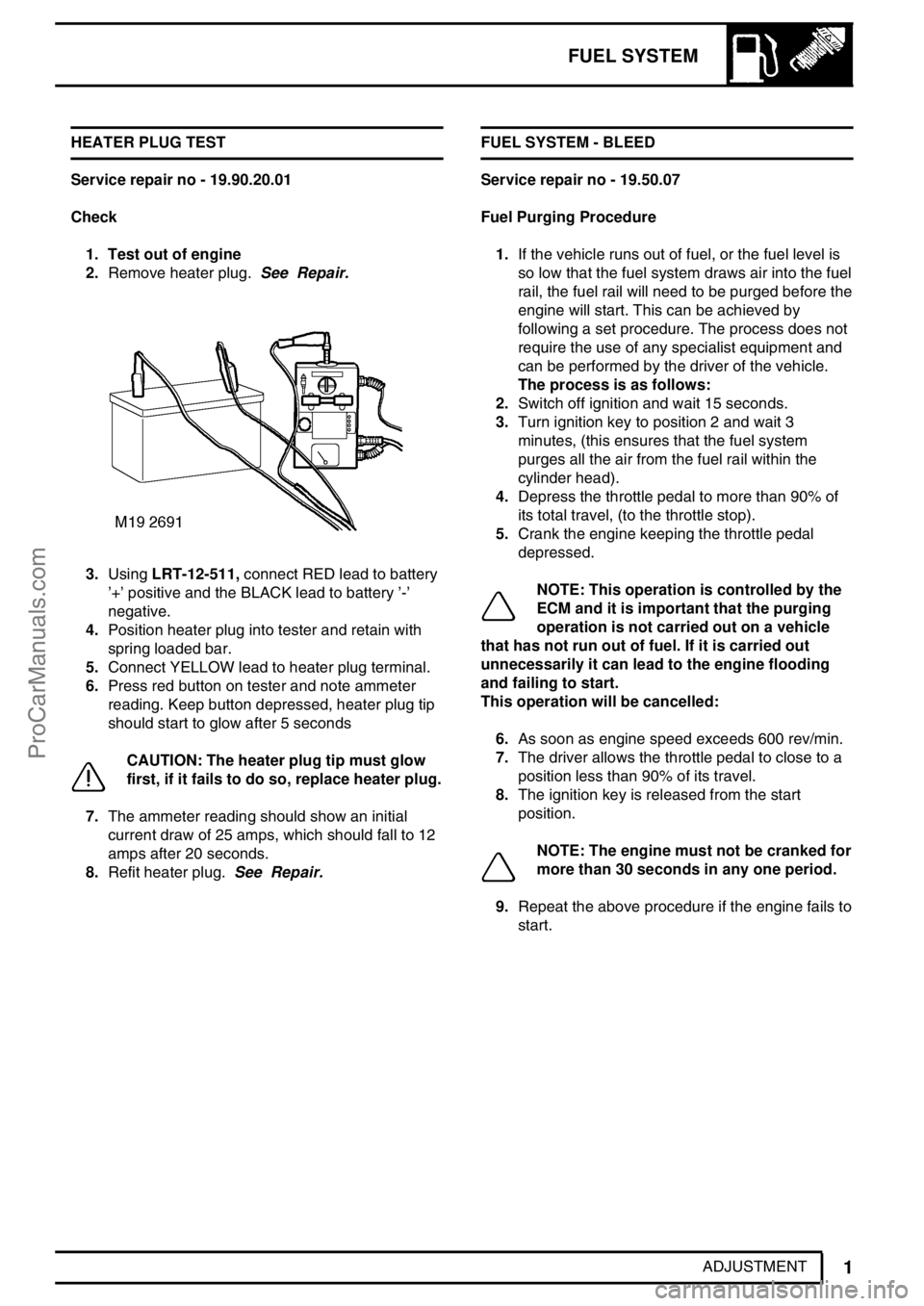
FUEL SYSTEM
1
ADJUSTMENT HEATER PLUG TEST
Service repair no - 19.90.20.01
Check
1. Test out of engine
2.Remove heater plug.See Repair.
3.UsingLRT-12-511,connect RED lead to battery
’+’positive and the BLACK lead to battery’-’
negative.
4.Position heater plug into tester and retain with
spring loaded bar.
5.Connect YELLOW lead to heater plug terminal.
6.Press red button on tester and note ammeter
reading. Keep button depressed, heater plug tip
should start to glow after 5 seconds
CAUTION: The heater plug tip must glow
first, if it fails to do so, replace heater plug.
7.The ammeter reading should show an initial
current draw of 25 amps, which should fall to 12
amps after 20 seconds.
8.Refit heater plug.See Repair.FUEL SYSTEM - BLEED
Service repair no - 19.50.07
Fuel Purging Procedure
1.If the vehicle runs out of fuel, or the fuel level is
so low that the fuel system draws air into the fuel
rail, the fuel rail will need to be purged before the
engine will start. This can be achieved by
following a set procedure. The process does not
require the use of any specialist equipment and
can be performed by the driver of the vehicle.
The process is as follows:
2.Switch off ignition and wait 15 seconds.
3.Turn ignition key to position 2 and wait 3
minutes, (this ensures that the fuel system
purges all the air from the fuel rail within the
cylinder head).
4.Depress the throttle pedal to more than 90% of
its total travel, (to the throttle stop).
5.Crank the engine keeping the throttle pedal
depressed.
NOTE: This operation is controlled by the
ECM and it is important that the purging
operation is not carried out on a vehicle
that has not run out of fuel. If it is carried out
unnecessarily it can lead to the engine flooding
and failing to start.
This operation will be cancelled:
6.As soon as engine speed exceeds 600 rev/min.
7.The driver allows the throttle pedal to close to a
position less than 90% of its travel.
8.The ignition key is released from the start
position.
NOTE: The engine must not be cranked for
more than 30 seconds in any one period.
9.Repeat the above procedure if the engine fails to
start.
ProCarManuals.com
Page 504 of 667
CHASSIS AND BODY
35
REPAIR LOCK - TAIL DOOR - FROM 02MY
Service repair no - 76.37.16
Remove
1.Remove tail door trim casing.See this Section.
2.Remove 4 nuts securing tail door lock.
3.Partially withdraw lock assembly, carefully
disconnect central door locking rod from fulcrum
arm.
4.Remove lock assembly.
5.Remove door lock gasket.
NOTE: Do not carry out further
dismantling if component is removed for
access only.
6.Insert key in lock, depress lock barrel plunger
and withdraw barrel from lock.Refit
7.Fit new barrel to lock.
8.Fit new door lock gasket.
9.Fit door locking rod to fulcrum, align lock. Fit and
tighten nuts to10 Nm (7 lbf.ft ).
10.Close door and check for correct latching with
striker. Adjust striker if necessary.See
Adjustment.
11.Fit tail door trim casing.See this Section.
ProCarManuals.com
Page 515 of 667
77PANEL REPAIRS
2
BODY DIMENSIONS CHASSIS FRAME ALIGNMENT
With the vehicle assembled, a check for chassis
squareness can be made as follows:
1.Place the vehicle on a level floor.
2.Mark measuring points at approximately the
locations shown in LR4412M ensuring that the
marks are exactly opposite on each side of the
chassis frame.3.Hold a plumb line against each of the measuring
points in turn and mark the floor directly beneath
the plumb-bob.
4.Move the vehicle and measure diagonally
between the marks made on the floor, if the
chassis is square the diagonals between the
related measuring points should be within 9,50
mm.
5.Chassis frame dimensional checks can be
made, with the vehicle upper structure removed,
referring to the applicable illustration and
associated key.
ProCarManuals.com
Page 581 of 667
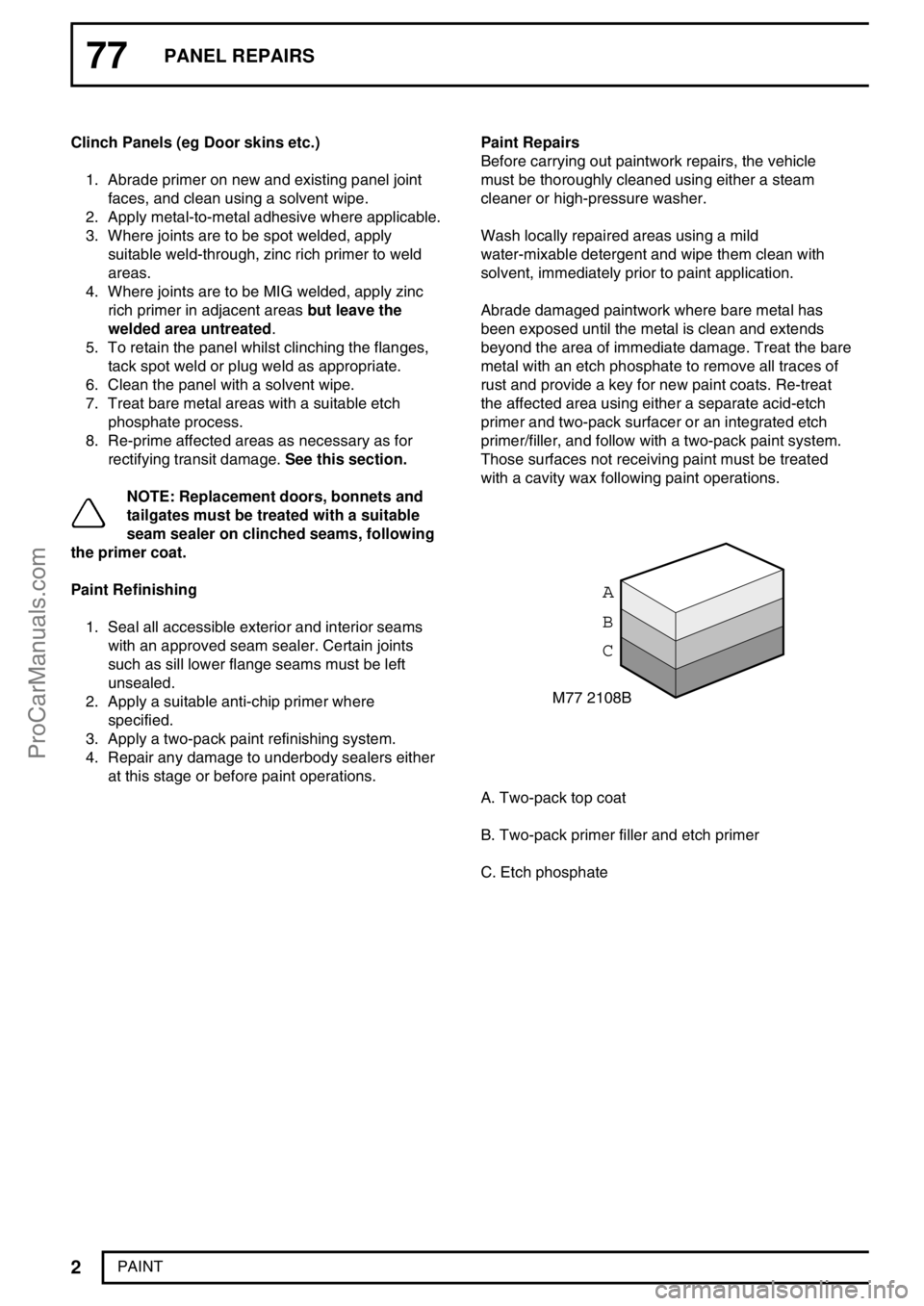
77PANEL REPAIRS
2
PAINT Clinch Panels (eg Door skins etc.)
1. Abrade primer on new and existing panel joint
faces, and clean using a solvent wipe.
2. Apply metal-to-metal adhesive where applicable.
3. Where joints are to be spot welded, apply
suitable weld-through, zinc rich primer to weld
areas.
4. Where joints are to be MIG welded, apply zinc
rich primer in adjacent areasbut leave the
welded area untreated.
5. To retain the panel whilst clinching the flanges,
tack spot weld or plug weld as appropriate.
6. Clean the panel with a solvent wipe.
7. Treat bare metal areas with a suitable etch
phosphate process.
8. Re-prime affected areas as necessary as for
rectifying transit damage.See this section.
NOTE: Replacement doors, bonnets and
tailgates must be treated with a suitable
seam sealer on clinched seams, following
the primer coat.
Paint Refinishing
1. Seal all accessible exterior and interior seams
with an approved seam sealer. Certain joints
such as sill lower flange seams must be left
unsealed.
2. Apply a suitable anti-chip primer where
specified.
3. Apply a two-pack paint refinishing system.
4. Repair any damage to underbody sealers either
at this stage or before paint operations.Paint Repairs
Before carrying out paintwork repairs, the vehicle
must be thoroughly cleaned using either a steam
cleaner or high-pressure washer.
Wash locally repaired areas using a mild
water-mixable detergent and wipe them clean with
solvent, immediately prior to paint application.
Abrade damaged paintwork where bare metal has
been exposed until the metal is clean and extends
beyond the area of immediate damage. Treat the bare
metal with an etch phosphate to remove all traces of
rust and provide a key for new paint coats. Re-treat
the affected area using either a separate acid-etch
primer and two-pack surfacer or an integrated etch
primer/filler, and follow with a two-pack paint system.
Those surfaces not receiving paint must be treated
with a cavity wax following paint operations.
M77 2108B
A
B
C
A. Two-pack top coat
B. Two-pack primer filler and etch primer
C. Etch phosphate
ProCarManuals.com
Page 610 of 667
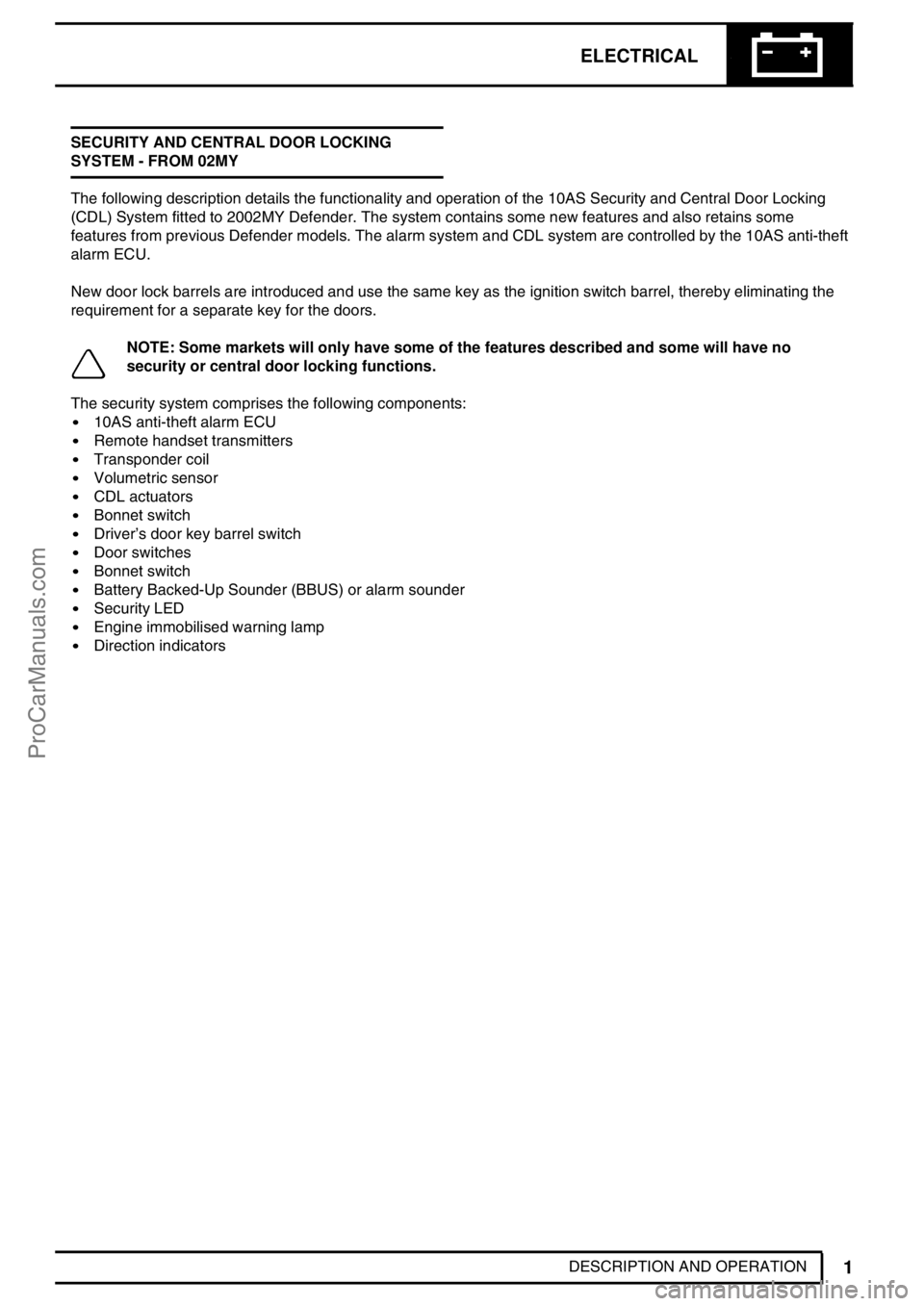
ELECTRICAL
1
DESCRIPTION AND OPERATION SECURITY AND CENTRAL DOOR LOCKING
SYSTEM - FROM 02MY
The following description details the functionality and operation of the 10AS Security and Central Door Locking
(CDL) System fitted to 2002MY Defender. The system contains some new features and also retains some
features from previous Defender models. The alarm system and CDL system are controlled by the 10AS anti-theft
alarm ECU.
New door lock barrels are introduced and use the same key as the ignition switch barrel, thereby eliminating the
requirement for a separate key for the doors.
NOTE: Some markets will only have some of the features described and some will have no
security or central door locking functions.
The security system comprises the following components:
10AS anti-theft alarm ECU
Remote handset transmitters
Transponder coil
Volumetric sensor
CDL actuators
Bonnet switch
Driver’s door key barrel switch
Door switches
Bonnet switch
Battery Backed-Up Sounder (BBUS) or alarm sounder
Security LED
Engine immobilised warning lamp
Direction indicators
ProCarManuals.com