Page 1230 of 1463
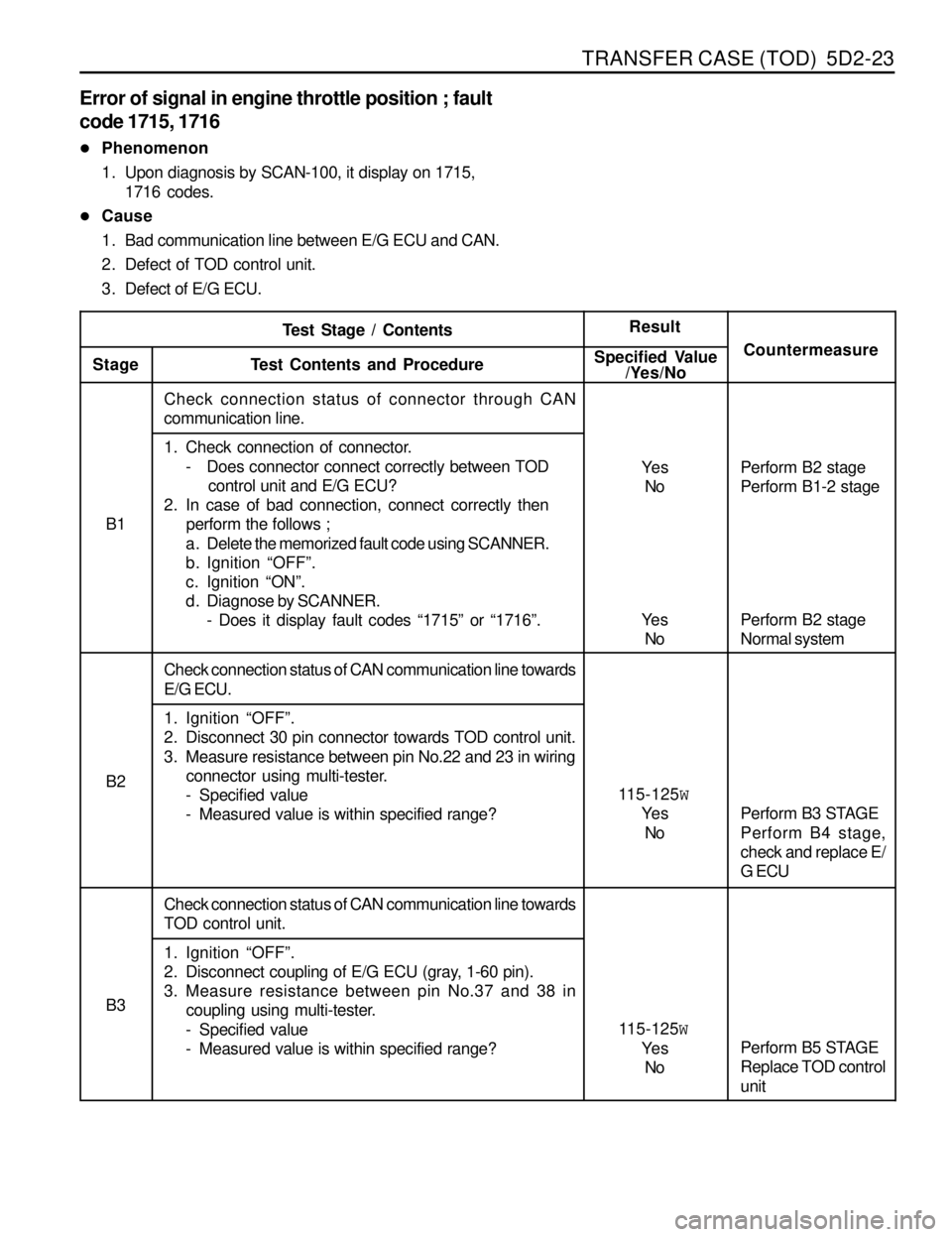
TRANSFER CASE (TOD) 5D2-23
Error of signal in engine throttle position ; fault
code 1715, 1716
lPhenomenon
1. Upon diagnosis by SCAN-100, it display on 1715,
1716 codes.
lCause
1. Bad communication line between E/G ECU and CAN.
2. Defect of TOD control unit.
3. Defect of E/G ECU.
Check connection status of connector through CAN
communication line.
1. Check connection of connector.
- Does connector connect correctly between TOD
control unit and E/G ECU?
2. In case of bad connection, connect correctly then
perform the follows ;
a. Delete the memorized fault code using SCANNER.
b. Ignition “OFF”.
c. Ignition “ON”.
d. Diagnose by SCANNER.
- Does it display fault codes “1715” or “1716”.Ye s
No
B1
Ye s
No
Check connection status of CAN communication line towards
E/G ECU.
1. Ignition “OFF”.
2. Disconnect 30 pin connector towards TOD control unit.
3. Measure resistance between pin No.22 and 23 in wiring
connector using multi-tester.
- Specified value
- Measured value is within specified range? B2
115-125W
Ye s
No
Check connection status of CAN communication line towards
TOD control unit.
1. Ignition “OFF”.
2. Disconnect coupling of E/G ECU (gray, 1-60 pin).
3. Measure resistance between pin No.37 and 38 in
coupling using multi-tester.
- Specified value
- Measured value is within specified range? B3
115-125W
Ye s
No Test Stage / Contents
Result
Stage Test Contents and ProcedureSpecified Value
/Yes/NoCountermeasure
Perform B2 stage
Perform B1-2 stage
Perform B2 stage
Normal system
Perform B3 STAGE
Perform B4 stage,
check and replace E/
G ECU
Perform B5 STAGE
Replace TOD control
unit
Page 1242 of 1463
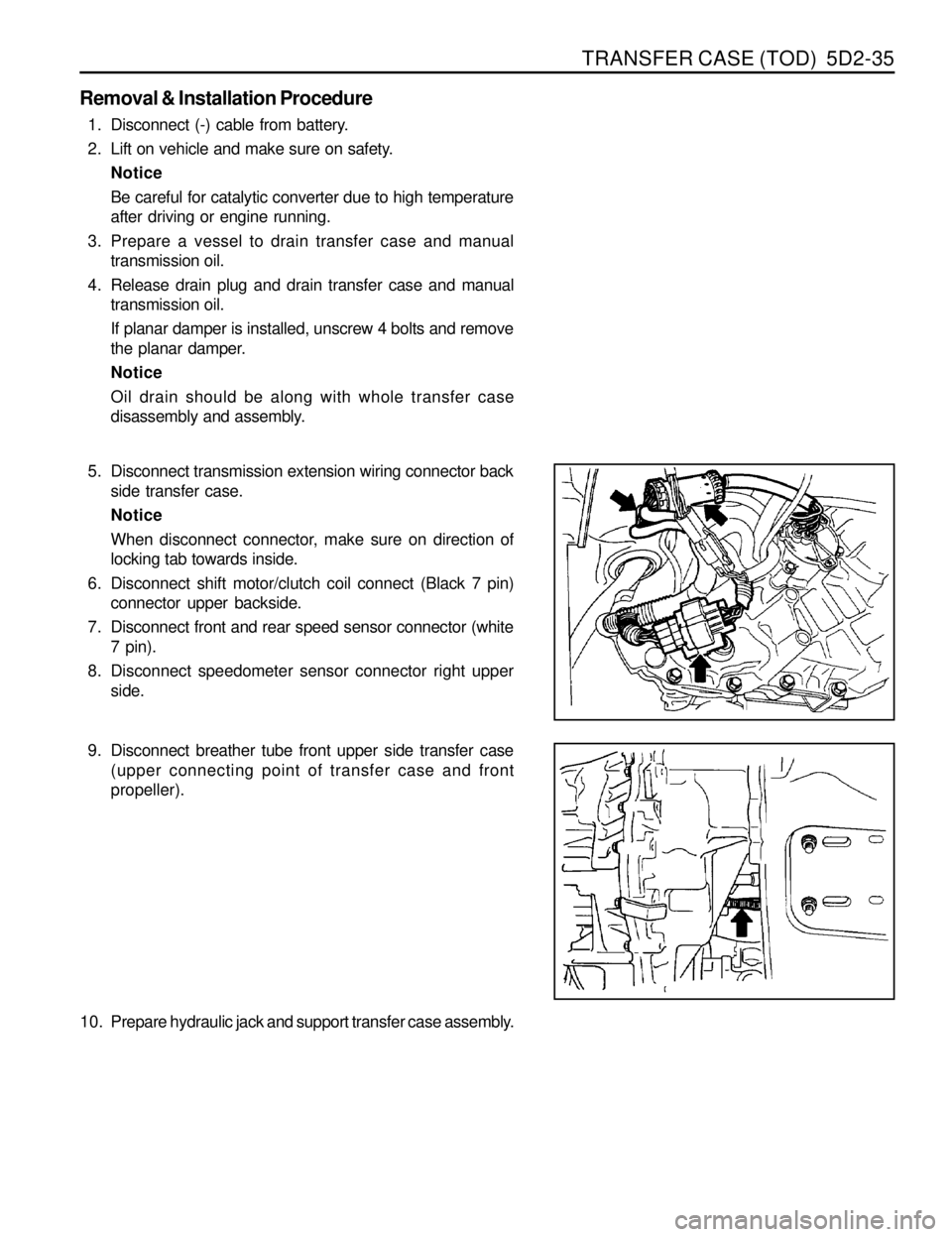
TRANSFER CASE (TOD) 5D2-35
Removal & Installation Procedure
1. Disconnect (-) cable from battery.
2. Lift on vehicle and make sure on safety.
Notice
Be careful for catalytic converter due to high temperature
after driving or engine running.
3. Prepare a vessel to drain transfer case and manual
transmission oil.
4. Release drain plug and drain transfer case and manual
transmission oil.
If planar damper is installed, unscrew 4 bolts and remove
the planar damper.
Notice
Oil drain should be along with whole transfer case
disassembly and assembly.
5. Disconnect transmission extension wiring connector back
side transfer case.
Notice
When disconnect connector, make sure on direction of
locking tab towards inside.
6. Disconnect shift motor/clutch coil connect (Black 7 pin)
connector upper backside.
7. Disconnect front and rear speed sensor connector (white
7 pin).
8. Disconnect speedometer sensor connector right upper
side.
9. Disconnect breather tube front upper side transfer case
(upper connecting point of transfer case and front
propeller).
10. Prepare hydraulic jack and support transfer case assembly.
Page 1265 of 1463
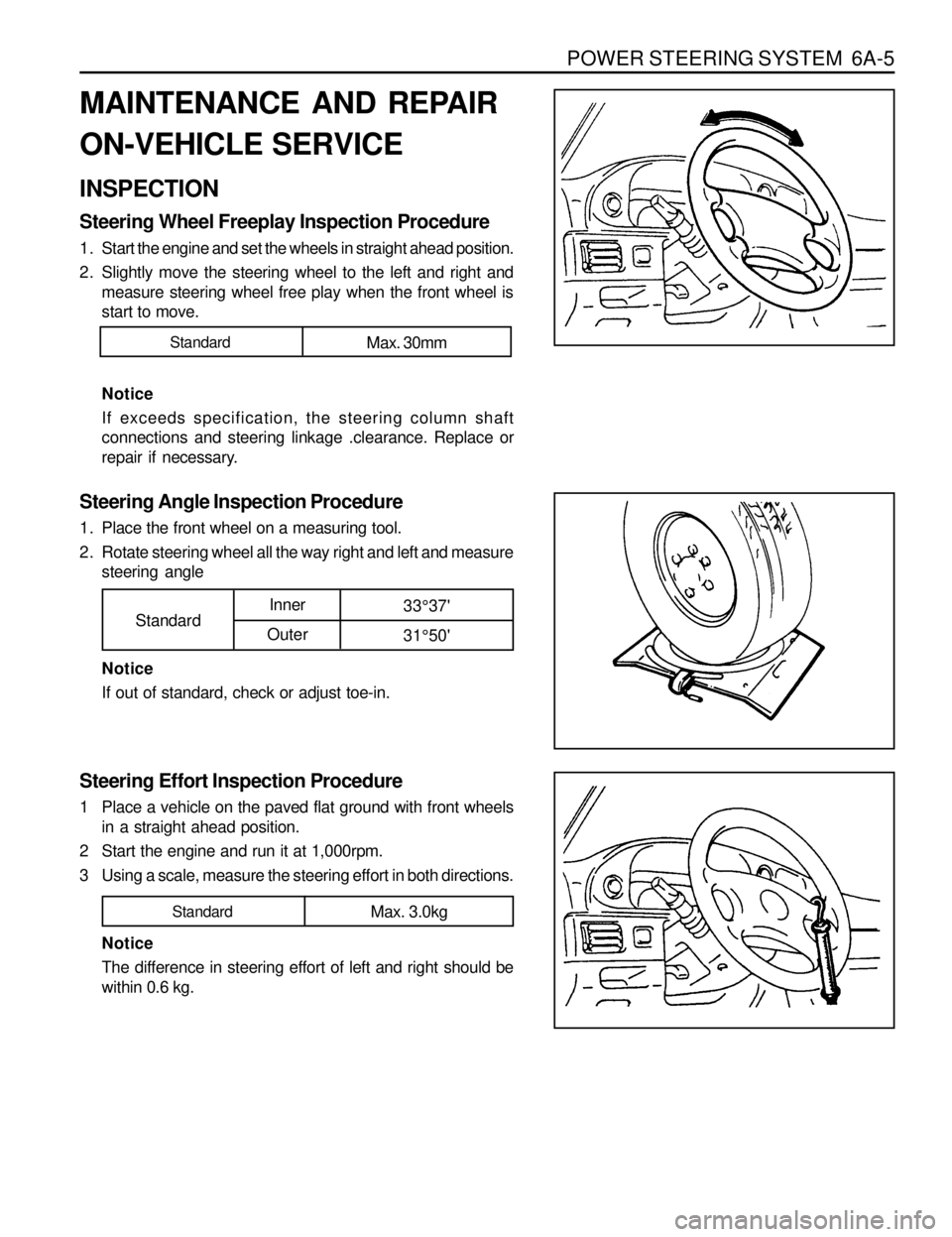
POWER STEERING SYSTEM 6A-5
MAINTENANCE AND REPAIR
ON-VEHICLE SERVICE
INSPECTION
Steering Wheel Freeplay Inspection Procedure
1. Start the engine and set the wheels in straight ahead position.
2. Slightly move the steering wheel to the left and right and
measure steering wheel free play when the front wheel is
start to move.
Notice
If exceeds specification, the steering column shaft
connections and steering linkage .clearance. Replace or
repair if necessary.
Steering Angle Inspection Procedure
1. Place the front wheel on a measuring tool.
2. Rotate steering wheel all the way right and left and measure
steering angle
Notice
If out of standard, check or adjust toe-in.
Standard33°37'
31°50'Inner
Outer
Steering Effort Inspection Procedure
1 Place a vehicle on the paved flat ground with front wheels
in a straight ahead position.
2 Start the engine and run it at 1,000rpm.
3 Using a scale, measure the steering effort in both directions.
Notice
The difference in steering effort of left and right should be
within 0.6 kg.
StandardMax. 3.0kg
StandardMax. 30mm
Page 1266 of 1463
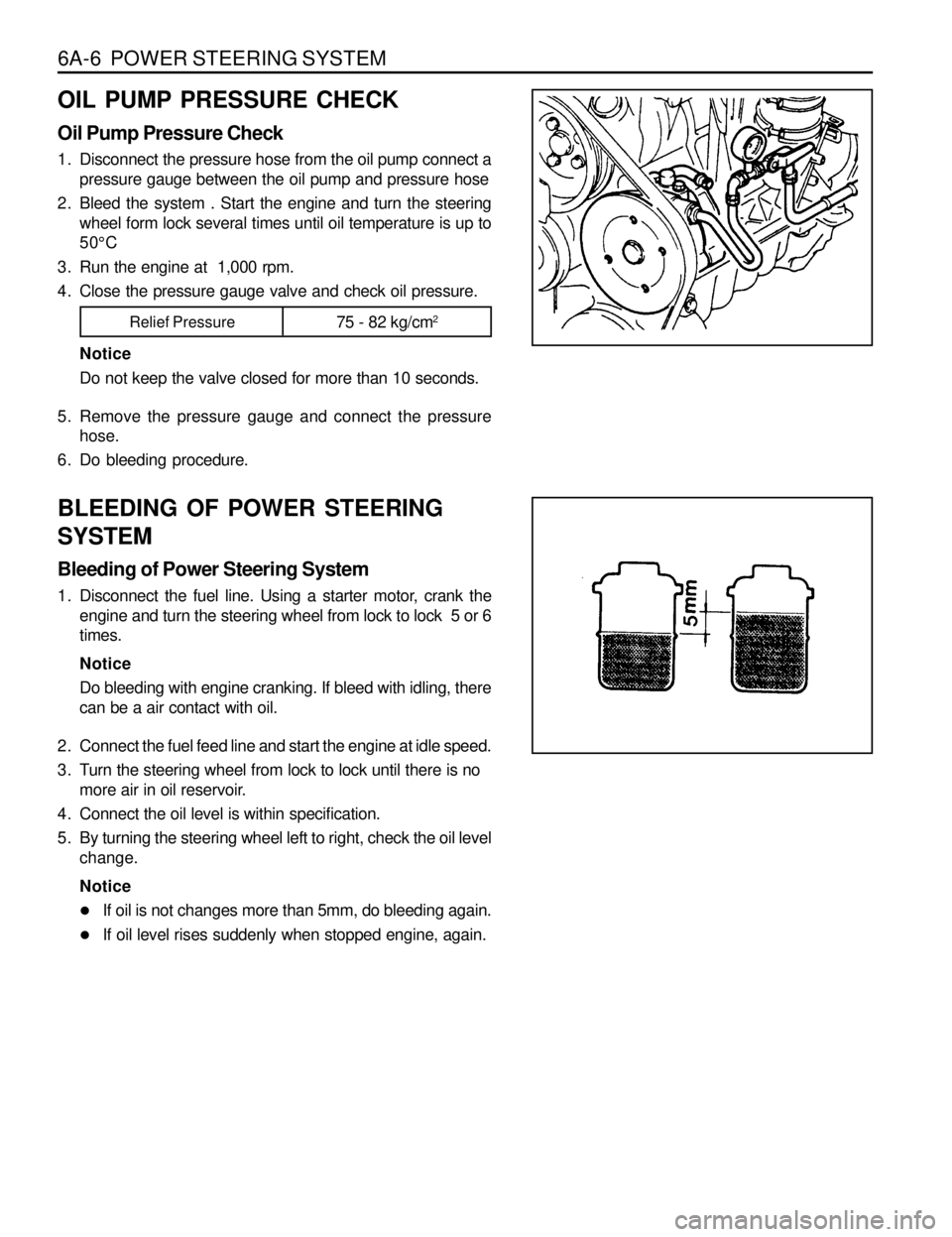
6A-6 POWER STEERING SYSTEM
OIL PUMP PRESSURE CHECK
Oil Pump Pressure Check
1. Disconnect the pressure hose from the oil pump connect a
pressure gauge between the oil pump and pressure hose
2. Bleed the system . Start the engine and turn the steering
wheel form lock several times until oil temperature is up to
50°C
3. Run the engine at 1,000 rpm.
4. Close the pressure gauge valve and check oil pressure.
Notice
Do not keep the valve closed for more than 10 seconds.
5. Remove the pressure gauge and connect the pressure
hose.
6. Do bleeding procedure.
BLEEDING OF POWER STEERING
SYSTEM
Bleeding of Power Steering System
1. Disconnect the fuel line. Using a starter motor, crank the
engine and turn the steering wheel from lock to lock 5 or 6
times.
Notice
Do bleeding with engine cranking. If bleed with idling, there
can be a air contact with oil.
2. Connect the fuel feed line and start the engine at idle speed.
3. Turn the steering wheel from lock to lock until there is no
more air in oil reservoir.
4. Connect the oil level is within specification.
5. By turning the steering wheel left to right, check the oil level
change.
Notice
lIf oil is not changes more than 5mm, do bleeding again.
lIf oil level rises suddenly when stopped engine, again.
Relief Pressure75 - 82 kg/cm2
Page 1275 of 1463
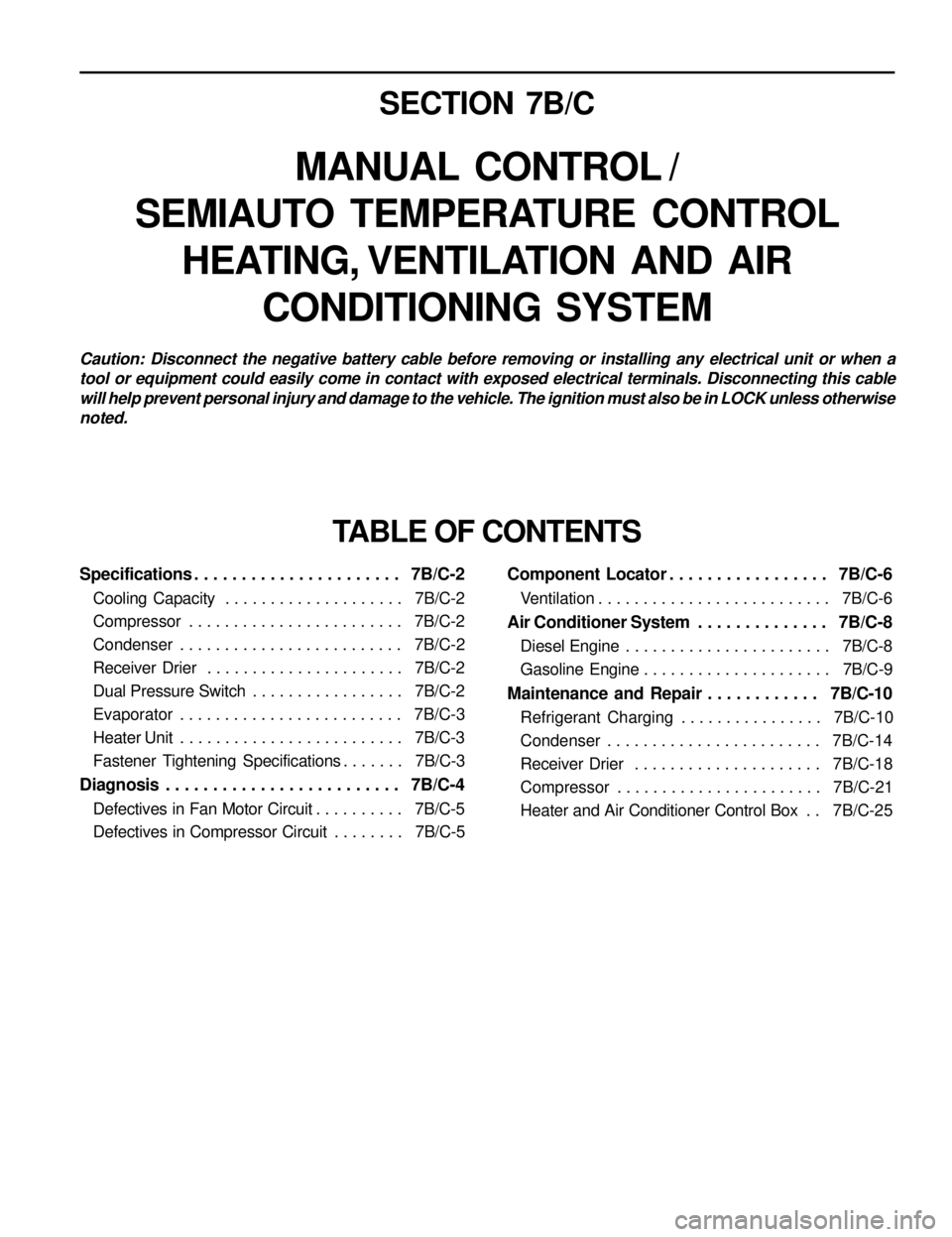
SECTION 7B/C
MANUAL CONTROL /
SEMIAUTO TEMPERATURE CONTROL
HEATING, VENTILATION AND AIR
CONDITIONING SYSTEM
Caution: Disconnect the negative battery cable before removing or installing any electrical unit or when a
tool or equipment could easily come in contact with exposed electrical terminals. Disconnecting this cable
will help prevent personal injury and damage to the vehicle. The ignition must also be in LOCK unless otherwise
noted.
Specifications . . . . . . . . . . . . . . . . . . . . . . 7B/C-2
Cooling Capacity . . . . . . . . . . . . . . . . . . . . 7B/C-2
Compressor . . . . . . . . . . . . . . . . . . . . . . . . 7B/C-2
Condenser . . . . . . . . . . . . . . . . . . . . . . . . . 7B/C-2
Receiver Drier . . . . . . . . . . . . . . . . . . . . . . 7B/C-2
Dual Pressure Switch . . . . . . . . . . . . . . . . . 7B/C-2
Evaporator . . . . . . . . . . . . . . . . . . . . . . . . . 7B/C-3
Heater Unit . . . . . . . . . . . . . . . . . . . . . . . . . 7B/C-3
Fastener Tightening Specifications . . . . . . . 7B/C-3
Diagnosis . . . . . . . . . . . . . . . . . . . . . . . . . 7B/C-4
Defectives in Fan Motor Circuit . . . . . . . . . . 7B/C-5
Defectives in Compressor Circuit . . . . . . . . 7B/C-5
TABLE OF CONTENTS
Component Locator . . . . . . . . . . . . . . . . . 7B/C-6
Ventilation . . . . . . . . . . . . . . . . . . . . . . . . . . 7B/C-6
Air Conditioner System . . . . . . . . . . . . . . 7B/C-8
Diesel Engine . . . . . . . . . . . . . . . . . . . . . . . 7B/C-8
Gasoline Engine . . . . . . . . . . . . . . . . . . . . . 7B/C-9
Maintenance and Repair . . . . . . . . . . . . 7B/C-10
Refrigerant Charging . . . . . . . . . . . . . . . . 7B/C-10
Condenser . . . . . . . . . . . . . . . . . . . . . . . . 7B/C-14
Receiver Drier . . . . . . . . . . . . . . . . . . . . . 7B/C-18
Compressor . . . . . . . . . . . . . . . . . . . . . . . 7B/C-21
Heater and Air Conditioner Control Box . . 7B/C-25
Page 1282 of 1463
7B/C-8 MANUAL & SEMIAUTO-HVAC
AIR CONDITIONER SYSTEM
DIESEL ENGINE
1 Compressor
2 High Pressure Hose
3 Condenser Fan
4 Condenser
5 Liquid Pipe (A)
6 Receiver Drier
7 Liquid (B)
8 Evaporator Assembly
9 Low Pressure Hose10 Water Inlet Hose
11 Water Outlet Hose
12 Control Assembly
13 Heater Unit Amplifier
14 Mix Actuator Assembly
15 Blower Unit
16 Heater Unit
17 Mode Actuator Assembly
Page 1283 of 1463
MANUAL & SEMIAUTO-HVAC 7B/C-9
GASOLINE ENGINE
1 Compressor
2 High Pressure Hose
3 Condenser
4 Main Condenser Fan
5 Sub Condenser Fan
6 Condenser Fan Resistor
7 Liquid Pipe(A)
8 Receiver Dryer
9 Liquid Pipe(B)
10 Grommet11 Evaporator Assembly
12 Control Assembly
13 Heater Unit Amp
14 Mix Actuator
15 Blower Unit
16 Heater Unit
17 Mode Actuator Assembly
18 Water Inlet Hose
19 Water Outlet Hose
Page 1286 of 1463
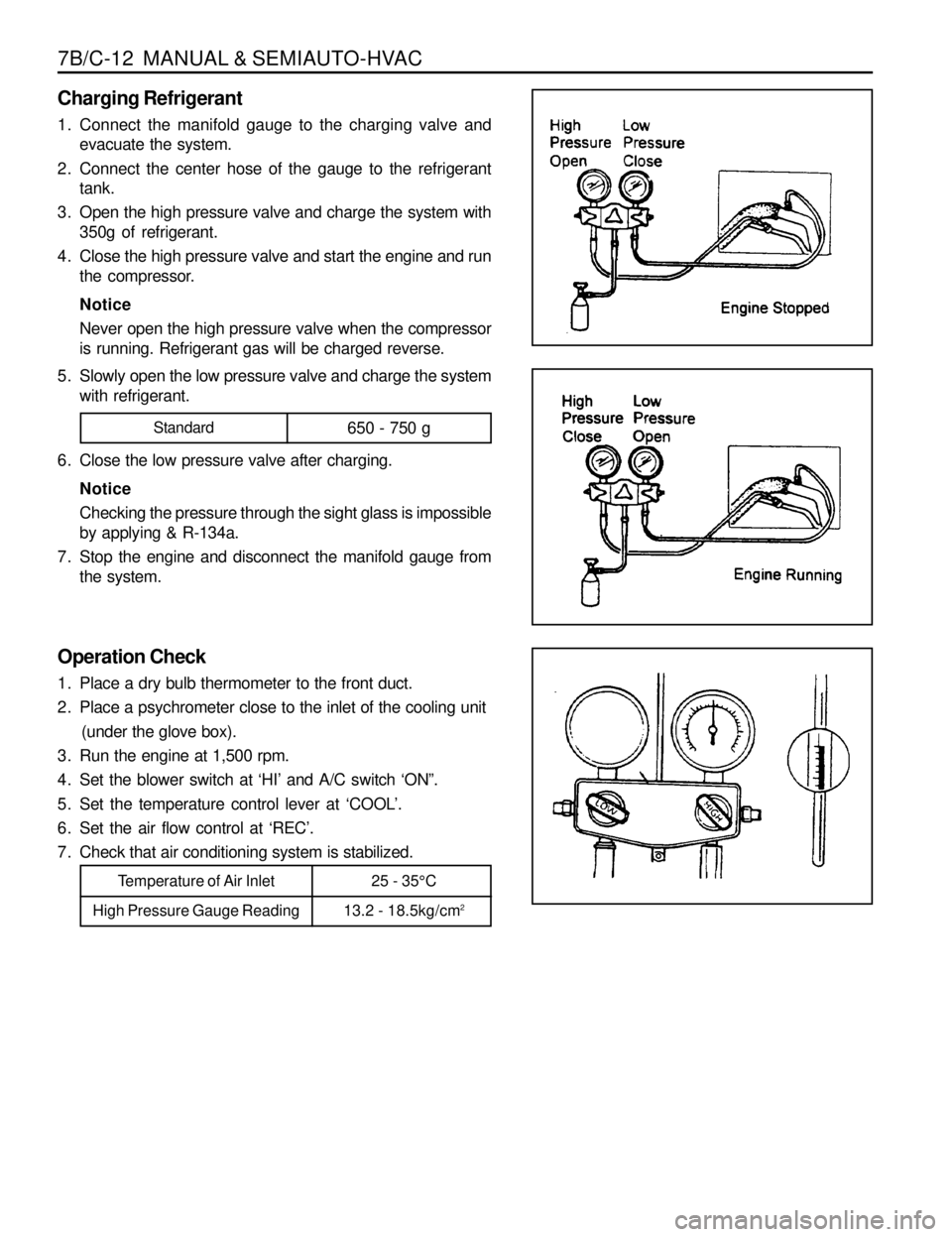
7B/C-12 MANUAL & SEMIAUTO-HVAC
Charging Refrigerant
1. Connect the manifold gauge to the charging valve and
evacuate the system.
2. Connect the center hose of the gauge to the refrigerant
tank.
3. Open the high pressure valve and charge the system with
350g of refrigerant.
4. Close the high pressure valve and start the engine and run
the compressor.
Notice
Never open the high pressure valve when the compressor
is running. Refrigerant gas will be charged reverse.
5. Slowly open the low pressure valve and charge the system
with refrigerant.
Standard650 - 750 g
6. Close the low pressure valve after charging.
Notice
Checking the pressure through the sight glass is impossible
by applying & R-134a.
7. Stop the engine and disconnect the manifold gauge from
the system.
Operation Check
1. Place a dry bulb thermometer to the front duct.
2. Place a psychrometer close to the inlet of the cooling unit
(under the glove box).
3. Run the engine at 1,500 rpm.
4. Set the blower switch at ‘HI’ and A/C switch ‘ON”.
5. Set the temperature control lever at ‘COOL’.
6. Set the air flow control at ‘REC’.
7. Check that air conditioning system is stabilized.
Temperature of Air Inlet
High Pressure Gauge Reading 25 - 35°C
13.2 - 18.5kg/cm
2