Page 8 of 2053
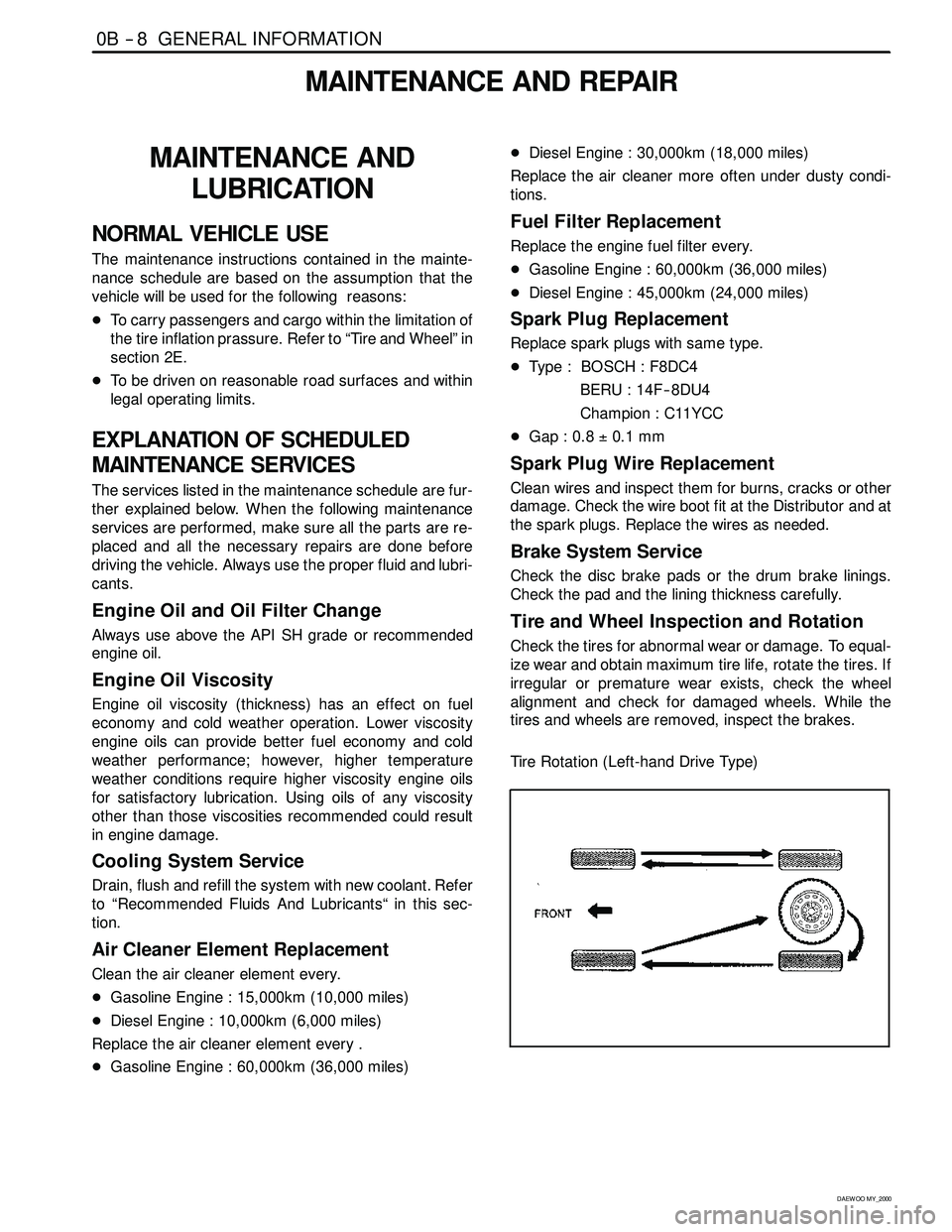
0B -- 8 GENERAL INFORMATION
D AEW OO M Y_2000
MAINTENANCE AND REPAIR
MAINTENANCE AND
LUBRICATION
NORMAL VEHICLE USE
The maintenance instructions contained in the mainte-
nance schedule are based on the assumption that the
vehicle will be used for the following reasons:
DTo carry passengers and cargo within the limitation of
the tire inflation prassure. Refer to “Tire and Wheel” in
section 2E.
DTo be driven on reasonable road surfaces and within
legal operating limits.
EXPLANATION OF SCHEDULED
MAINTENANCE SERVICES
The services listed in the maintenance schedule are fur-
ther explained below. When the following maintenance
services are performed, make sure all the parts are re-
placed and all the necessary repairs are done before
driving the vehicle. Always use the proper fluid and lubri-
cants.
Engine Oil and Oil Filter Change
Always use above the API SH grade or recommended
engine oil.
Engine Oil Viscosity
Engine oil viscosity (thickness) has an effect on fuel
economy and cold weather operation. Lower viscosity
engine oils can provide better fuel economy and cold
weather performance; however, higher temperature
weather conditions require higher viscosity engine oils
for satisfactory lubrication. Using oils of any viscosity
other than those viscosities recommended could result
in engine damage.
Cooling System Service
Drain, flush and refill the system with new coolant. Refer
to “Recommended Fluids And Lubricants“ in this sec-
tion.
Air Cleaner Element Replacement
Clean the air cleaner element every.
DGasoline Engine : 15,000km (10,000 miles)
DDiesel Engine : 10,000km (6,000 miles)
Replace the air cleaner element every .
DGasoline Engine : 60,000km (36,000 miles)DDiesel Engine : 30,000km (18,000 miles)
Replace the air cleaner more often under dusty condi-
tions.
Fuel Filter Replacement
Replace the engine fuel filter every.
DGasoline Engine : 60,000km (36,000 miles)
DDiesel Engine : 45,000km (24,000 miles)
Spark Plug Replacement
Replace spark plugs with same type.
DType : BOSCH : F8DC4
BERU : 14F-- 8DU4
Champion : C11YCC
DGap : 0.8±0.1 mm
Spark Plug Wire Replacement
Clean wires and inspect them for burns, cracks or other
damage. Check the wire boot fit at the Distributor and at
the spark plugs. Replace the wires as needed.
Brake System Service
Check the disc brake pads or the drum brake linings.
Check the pad and the lining thickness carefully.
Tire and Wheel Inspection and Rotation
Check the tires for abnormal wear or damage. To equal-
ize wear and obtain maximum tire life, rotate the tires. If
irregular or premature wear exists, check the wheel
alignment and check for damaged wheels. While the
tires and wheels are removed, inspect the brakes.
Tire Rotation (Left-hand Drive Type)
Page 9 of 2053
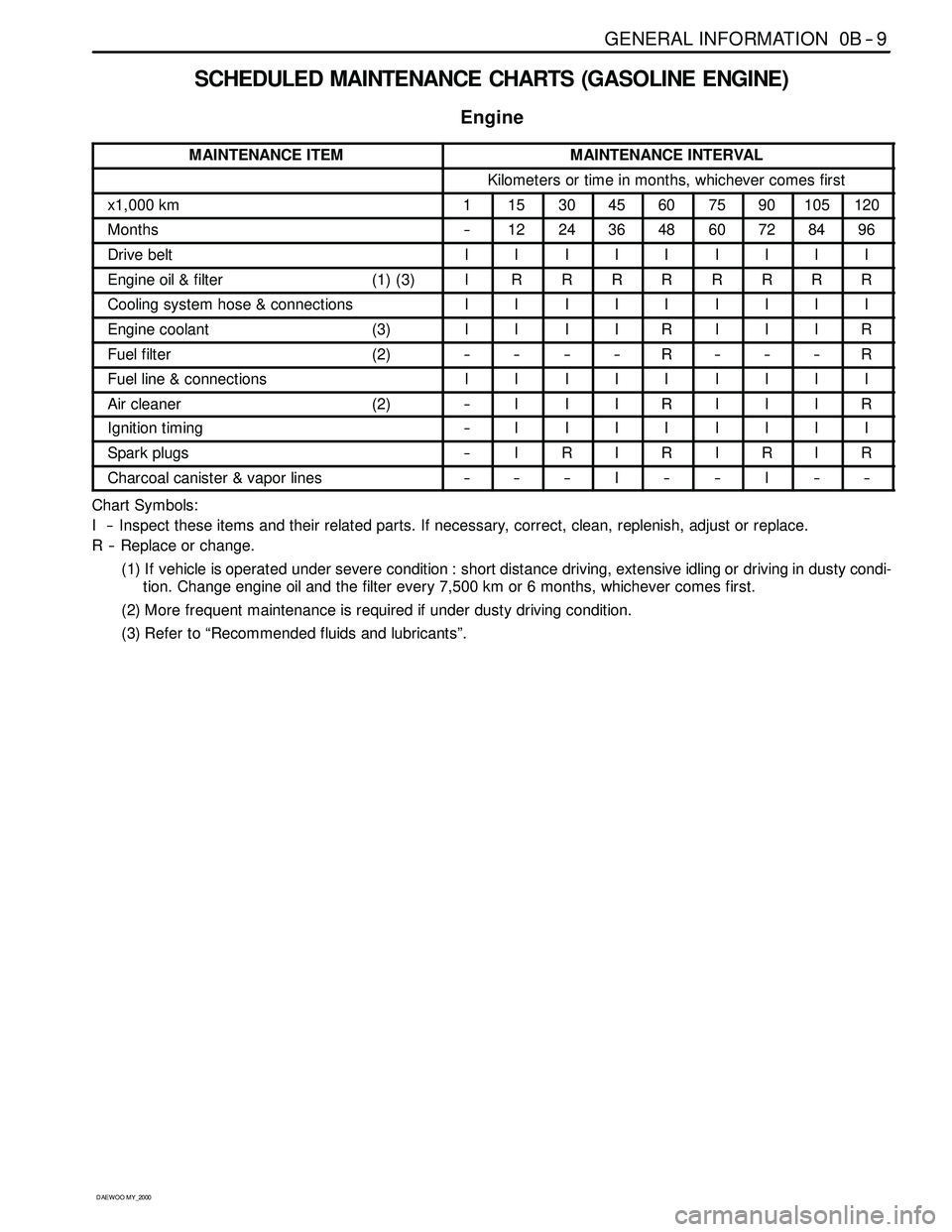
GENERAL INFORMATION 0B -- 9
D AEW OO M Y_2000
SCHEDULED MAINTENANCE CHARTS (GASOLINE ENGINE)
Engine
MAINTENANCE ITEMMAINTENANCE INTERVAL
Kilometers or time in months, whichever comes first
x1,000 km1153045607590105120
Months--1224364860728496
Drive beltIIIIIIIII
Engine oil & filter (1) (3)IRRRRRRRR
Cooling system hose & connectionsIIIIIIIII
Engine coolant (3)IIIIRIIIR
Fuel filter (2)--------R------R
Fuel line & connectionsIIIIIIIII
Air cleaner (2)--IIIRIIIR
Ignition timing--IIIIIIII
Spark plugs--IRIRIRIR
Charcoal canister & vapor lines------I----I----
Chart Symbols:
I -- Inspect these items and their related parts. If necessary, correct, clean, replenish, adjust or replace.
R -- Replace or change.
(1) If vehicle is operated under severe condition : short distance driving, extensive idling or driving in dusty condi-
tion. Change engine oil and the filter every 7,500 km or 6 months, whichever comes first.
(2) More frequent maintenance is required if under dusty driving condition.
(3) Refer to “Recommended fluids and lubricants”.
Page 29 of 2053
GENERAL ENGINE INFORMATION 1A1 -- 9
D AEW OO M Y_2000
Measuring Procedure
1. Warm the engine up to normal operating tempera-
ture.
2. Remove the spark plugs.
3. Place the diagram sheet to compression pressure
tester.
4. Connect the adaptor to compression pressure tester
and install it into the spark plug hole.
5. Crank the engine approx. eight revolutions by using
the start motor.6. Compare the measurements of compression pres-
sure tester with the specifications.
7. Measure the compression pressure of the other cylin-
ders in the same way.
8. If measured value is not within the specifications, per-
form the cylinder pressure leakage test.
Notice
DDischarge the combustion residues in the cylinders
before testing the compression pressure.
DApply the parking brake before cranking the engine.
Page 31 of 2053
GENERAL ENGINE INFORMATION 1A1 -- 11
D AEW OO M Y_2000
Leakage Test
1. Warm the engine up to normal operating tempera-
ture.
2. Disconnect the negative battery cable.
3. Remove the spark plugs.
4. Check the coolant level by opening the coolant
surge tank cap and replenish if insufficient.
5. Open the engine oil filler cap.
6. Connect the tester to air pressure line and adjust the
scale of tester.
7. Install the connecting hose to spark plug hole.
8. Position the piston of No.1 cylinder at TDC by rotat-
ing the crankshaft.
9. Connect the connecting hose to tester and measure
the leakage volume after blowing up compressed
air.
Notice:Measure the leakage volume in the completely
opening condition of throttle valve by pulling the accel-
eration cable.
10. Perform the pressure test according to the firing or-
der.
Notice:
FiringOrder:1--5--3--6--2--4
11. Compare the leakage pressure with the specifica-
tions.
Page 161 of 2053
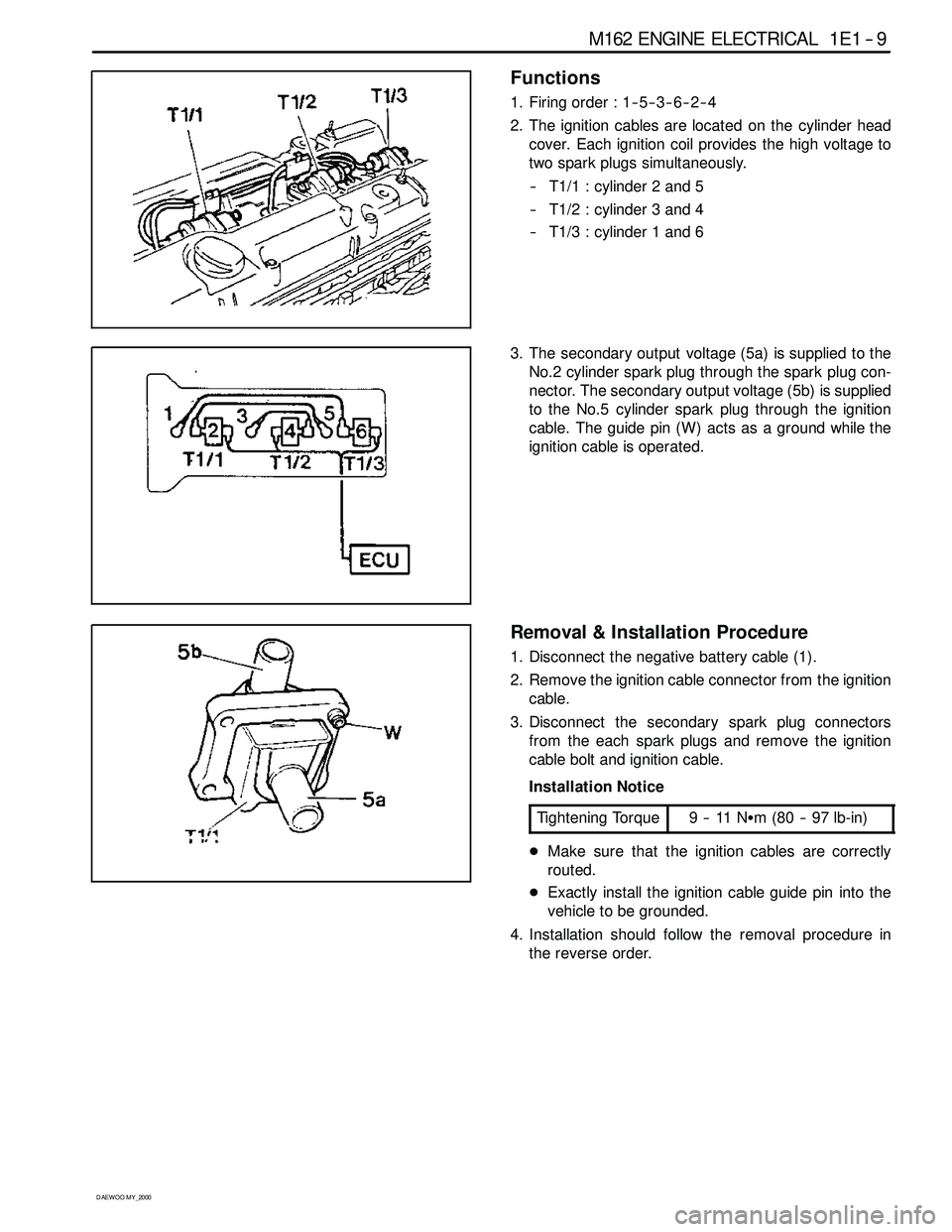
M162 ENGINE ELECTRICAL 1E 1 -- 9
D AEW OO M Y_2000
Functions
1. Firing order : 1 -- 5 -- 3 -- 6 -- 2 -- 4
2. The ignition cables are located on the cylinder head
cover. Each ignition coil provides the high voltage to
two spark plugs simultaneously.
-- T1/1 : cylinder 2 and 5
-- T1/2 : cylinder 3 and 4
-- T1/3 : cylinder 1 and 6
3. The secondary output voltage (5a) is supplied to the
No.2 cylinder spark plug through the spark plug con-
nector. The secondary output voltage (5b) is supplied
to the No.5 cylinder spark plug through the ignition
cable. The guide pin (W) acts as a ground while the
ignition cable is operated.
Removal & Installation Procedure
1. Disconnect the negative battery cable (1).
2. Remove the ignition cable connector from the ignition
cable.
3. Disconnect the secondary spark plug connectors
from the each spark plugs and remove the ignition
cable bolt and ignition cable.
Installation Notice
Tightening Torque
9--11NSm (80 -- 97 lb-in)
DMake sure that the ignition cables are correctly
routed.
DExactly install the ignition cable guide pin into the
vehicle to be grounded.
4. Installation should follow the removal procedure in
the reverse order.
Page 183 of 2053
1F1 -- 20 M162 ENGINE CONTROLS
D AEW OO M Y_2000
IGNITION COIL
YAA1F240
The Electronic Ignition (EI) system ignition coil is located on the cylinder head cover. The double ended coils receive
the signal for the Engine Control Module (ECM) which controls the spark advance.
Each EI system ignition coil provides the high voltage to two spark plugs simultaneously;
T1/1: cylinder 2 and 5
T1/2: cylinder 3 and 4
T1/3: cylinder 1 and 6
The EI system ignition coil is not serviceable and must be replaced as an assembly.
Page 184 of 2053
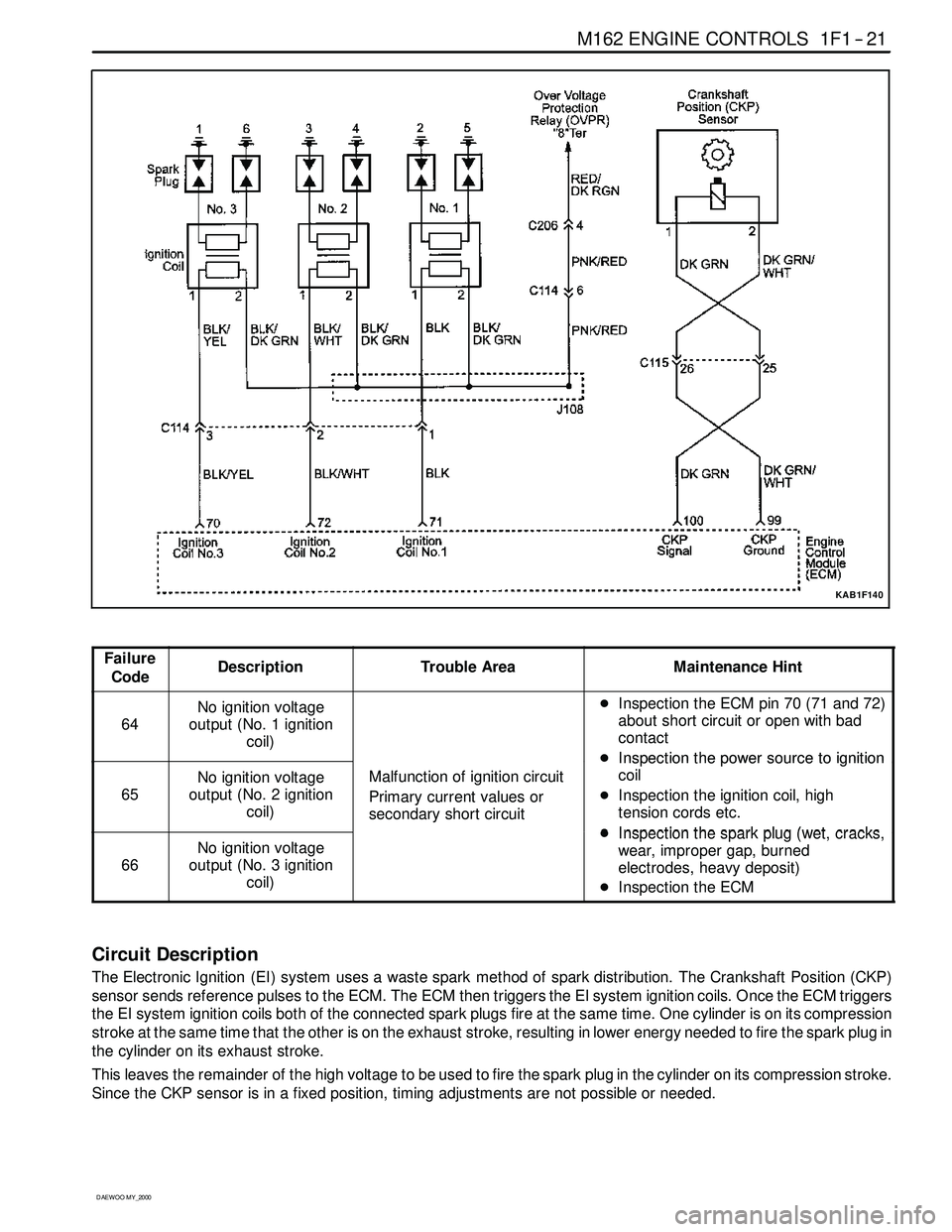
M162 ENGINE CONTROLS 1F1 -- 21
D AEW OO M Y_2000
KAB1F140
Failure
CodeDescriptionTrouble AreaMaintenance Hint
64
No ignition voltage
output (No. 1 ignition
coil)DInspectiontheECMpin70(71and72)
about short circuit or open with bad
contact
DInspectionthepowersourcetoignition
65
No ignition voltage
output (No. 2 ignition
coil)Malfunction of ignition circuit
Primary current values or
secondary short circuit
DInspectionthepowersourcetoignition
coil
DInspection the ignition coil, high
tension cords etc.
DInspectionthesparkplug(wetcracks
66
No ignition voltage
output (No. 3 ignition
coil)DInspection the spark plug (wet, cracks,
wear, improper gap, burned
electrodes, heavy deposit)
DInspection the ECM
Circuit Description
The Electronic Ignition (EI) system uses a waste spark method of spark distribution. The Crankshaft Position (CKP)
sensor sends reference pulses to the ECM. The ECM then triggers the EI system ignition coils. Once the ECM triggers
the EI system ignition coils both of the connected spark plugs fire at the same time. One cylinder is on its compression
stroke at the same time that the other is on the exhaust stroke, resulting in lower energy needed to fire the spark plug in
the cylinder on its exhaust stroke.
This leaves the remainder of the high voltage to be used to fire the spark plug in the cylinder on its compression stroke.
Since the CKP sensor is in a fixed position, timing adjustments are not possible or needed.
Page 284 of 2053
1A2 -- 12 GENERAL ENGINE INFORMATION
D AEW OO M Y_2000
Leakage Test
1. Warm the engine up to normal operating tempera-
ture.
2. Disconnect the negative battery cable.
3. Remove the spark plugs.
4. Check the coolant level by opening the coolant
surge tank cap and replenish if insufficient.
5. Open the engine oil filler cap.
6. Connect the tester to air pressure line and adjust the
scale of tester.
7. Install the connecting hose to spark plug hole.
YAA1A2080
8. Position the piston of No.1 cylinder at TDC by rotat-
ing the crankshaft.
9. Connect the connecting hose to tester and measure
the leakage volume after blowing up compressed
air.
Notice:Measure the leakage volume in the completely
opening condition of throttle valve by pulling the accel-
eration cable.
10. Perform the pressure test according to the firing or-
der.
Notice:Firing Order : 1 -- 3 -- 4 -- 2
11. Compare the leakage pressure with the specifica-
tions.