Page 150 of 363
Order of
operationsFunction to be
checkedAction Bargraph Display and notes Fault finding
1Flywheel signal
sensor StarterIlluminated if TDC
information is detected
DIAG 5
2Fuel pump
G10*Fuel pump should be
heard to operateDIAG 6
3 IgnitionConnect
Optima
StationStarting test.
Complete guide on
Optima StationUse Optima
5800 Station
4Fuel pressureConnect
pressure
gauge to
fuel inlet
and activate
starter
motorPressure gauge must
show
2.5 bars Fuel pressure,
see Workshop
Repair
Manual or
section
5Injector
commandStarterFuel must come out of
the injector
DIAG 11
6Engine
compressionConnect
Optima
StationComplete guide on
Optima StationUse Optima
5800 Station
7 FlywheelConnect
Optima
StationOscilloscope.
Complete guide on
Optima StationUse Optima
5800 Station
JSA051.0
INJECTION
Fault finding - Status and parameter checks
17
D7F 710
engine -
35 tracks
Carry out the actions below if the engine does not start.
Otherwise, refer to the following pages.NOTES
3
17-105
Page 151 of 363
JSA051.0
INJECTION
Fault finding - Status and parameter checks
17
D7F 710
engine -
35 tracks
Order of
operationsFunction to be
checkedAction Bargraph Display and notes Fault finding
1
Charging
circuit# 0413 < X < 14.5 V
DIAG 1
2Throttle
potentiometerNo load
Illuminated (does not
flash!)DIAG 2
3Idle speed
regulation# 06
# 12690 < X < 790 rpm
4 % < X < 14 %DIAG 7
4Anti-pinking
circuit# 13 (at
3500 rpm,
no load)X variable and not zeroDIAG 8
5 Pressure circuit# 01
# 16270 ≤ X ≤ 430 mb
X = atmospheric pressureDIAG 9
6Richness
regulation# 35
# 050 < X < 255
X varies around 128
50 ≤ X ≤ 900 V
DIAG 10
See also
DIAG 15
7Fuel pressureConnect a
pressure
gauge to the
fuel inlet
and activate
the starter
motorPressure gauge must
show
2.5 bars Fuel pressure,
see Workshop
Repair
Manual or
section
Carry out the actions below (engine warm, at idle speed, no consumers)
if the engine starts.
Otherwise refer to the previous pages.
NOTES
6
6
2
17-106
Page 159 of 363
Check the insulation and continuity of the wiring:
Fuel pump relay 5 Impact sensor
Impact sensor C1 Fuel pump
Repair if necessary.
Check the 25A fuel pump fuse.
Check the insulation and continuity of the wiring:
Fuel pump fuse 3 Fuel pump relay
Repair if necessary.
JSA051.0
INJECTION
Fault finding - Status and parameter interpretation17
D7F 710
engine -
35 tracks
AFTER REPAIRStart the status and parameter check again from the beginning.
DIAG 6
Fiche n° 27
FUEL PUMP
XR25 aid:The command mode should cause the fuel pump to operate
No fault bargraphs should be illuminated.NOTES
Check the hygiene and presence of earth on track C2 of the fuel pump.
If + 12 V is not reaching the fuel pump, replace the fuel pump relay.
If + 12 V is reaching the fuel pump, replace the fuel pump.
17-114
Page 160 of 363
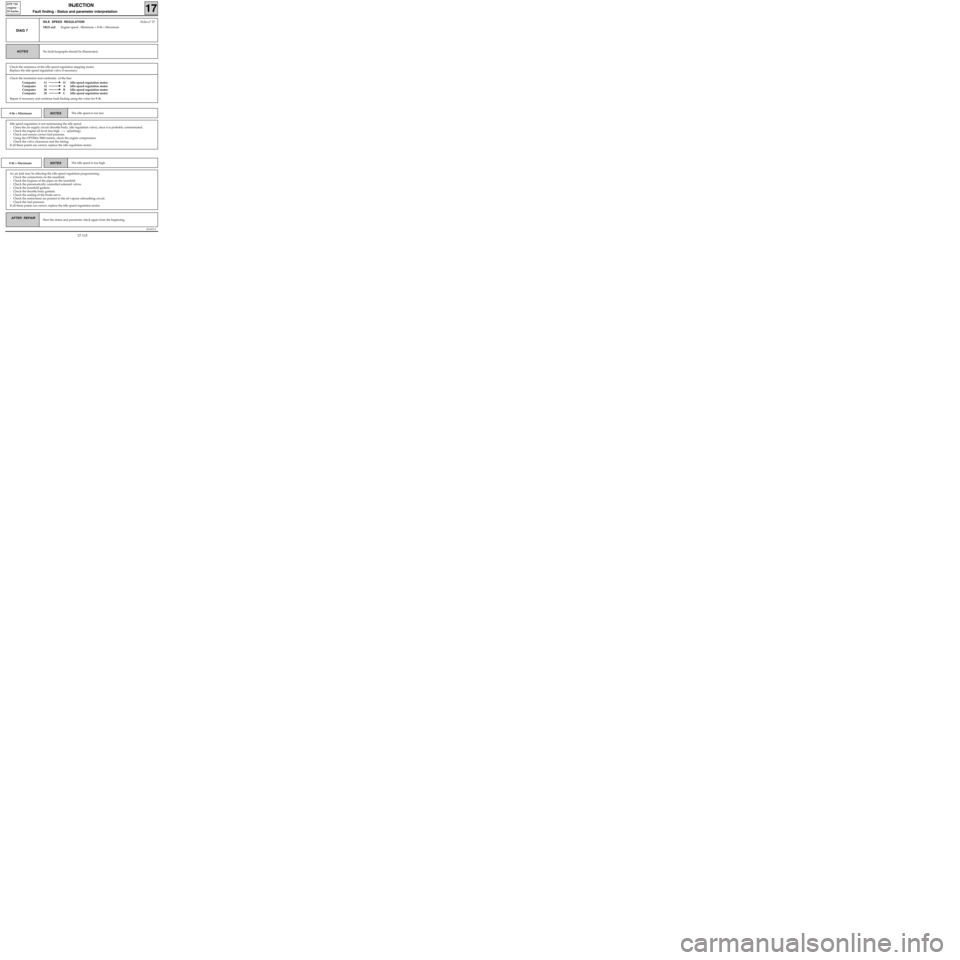
Check the insulation and continuity of the line:
Computer 11 D Idle speed regulation motor
Computer 12 A Idle speed regulation motor
Computer 28 B Idle speed regulation motor
Computer 29 C Idle speed regulation motor
Repair if necessary and continue fault finding using the value for # 06.
JSA051.0
INJECTION
Fault finding - Status and parameter interpretation17
D7F 710
engine -
35 tracks
AFTER REPAIRStart the status and parameter check again from the beginning.
DIAG 7
IDLE SPEED REGULATIONFiche n° 27
XR25 aid:Engine speed , Minimum < # 06 < Maximum
No fault bargraphs should be illuminated.NOTES
Check the resistance of the idle speed regulation stepping motor.
Replace the idle speed regulation valve if necessary.
# 06 < MinimumThe idle speed is too lowNOTES
Idle speed regulation is not maintaining the idle speed.
- Clean the air supply circuit (throttle body, idle regulation valve), since it is probably contaminated.
- Check the engine oil level (too high ---
> splashing).
- Check and ensure correct fuel pressure.
- Using the OPTIMA 5800 station, check the engine compression.
- Check the valve clearances and the timing.
If all these points are correct, replace the idle regulation motor.
# 06 > MaximumThe idle speed is too highNOTES
An air leak may be affecting the idle speed regulation programming.
- Check the connections on the manifold.
- Check the hygiene of the pipes on the manifold.
- Check the pneumatically controlled solenoid valves.
- Check the manifold gaskets.
- Check the throttle body gaskets.
- Check the sealing of the brake servo.
- Check the restrictions are present in the oil vapour rebreathing circuit.
- Check the fuel pressure.
If all these points are correct, replace the idle speed regulation motor.
17-115
Page 163 of 363
JSA051.0
INJECTION
Fault finding - Status and parameter interpretation17
D7F 710
engine -
35 tracks
AFTER REPAIRStart the status and parameter check again from the beginning.
DIAG 10
Fiche n° 27
RICHNESS REGULATION
XR25 aid:Richness regulation faulty
No fault bargraphs should be illuminated.
Ignition correct (a check may be made using the OPTIMA 5800 station).
No other status bargraph should show a fault.
NOTES
Check the sealing of the canister bleed valve (a leak can disrupt the richness considerably).
Check the sealing of the exhaust pipe upstream from the oxygen sensor.
Check the sealing of the inlet manifold.
If the vehicle has only been driven in town, the sensor is contaminated (try driving under load).
Check the fuel pressure.
If the idle speed is unstable, check the valve clearances.
Check the injectors (flow and shape of the jet).
If necessary, replace the oxygen sensor.
17-118
Page 167 of 363
JSA051.0
INJECTION
Fault finding - Status and parameter interpretation17
D7F 710
engine -
35 tracks
AFTER REPAIRStart the status and parameter check again from the beginning.
DIAG 14
Fiche n° 27 side 2/2
ADAPTIVE RICHNESS
XR25 aid:Minimum < # 30 < Maximum
Minimum < # 31 < Maximum
No fault bargraphs should be illuminated.
Carry out the programming operations.NOTES
Ensure the canister bleed valve is sealed.
Erase the computer memory.
Engine warm , running at idle speed, check the values for # 30 and # 31.
-If # 30 or # 31 is at a MAXIMUM, there is not enough fuel.
-If # 30 or # 31 is at a MINIMUM, there is too much fuel.
Ensure the hygiene, cleanliness and correct operation of :
- filter
- fuel pump
- fuel circuit
- fuel tank.
17-122
Page 169 of 363
JSA051.0
INJECTION
Fault finding - Status and parameter interpretation17
D7F 710
engine -
35 tracks
AFTER REPAIRStart the status and parameter check again from the beginning.
DIAG 15
CONT
Fiche n° 27
No fault bargraphs should be illuminated.NOTES
NOTES λ > 1.03
at 2500 rpmNone
The oxygen sensor loops correctly at 2500 rpm.
NOTES λ < 0.97
at 2500 rpm.The oxygen sensor does not loop correctly at 2500 rpm., CO >
0.3 % at 2500 rpm.
Check the pressure sensor.
Check the sensor.
Check that an injector is not faulty.
Check there is no leak at the exhaust.
Check that an injector has not seized.
Check the fuel pressure is not too low.
The oxygen sensor does not loop correctly at 2500 rpm.
Check there is not an injection fault.
Check there is not an ignition fault.
Check the sensor is not faulty.
Check the fuel pressure.
17-124
Page 174 of 363
JSA051.0
INJECTION
Fault finding - Fault charts
17
D7F 710
engine -
35 tracks
AFTER REPAIR
Chart 1
STARTING FAULTS
Only refer to this customer complaint after a complete check using the XR25.NOTES
Erase the computer memory using G0** and carry out a road test.
Check there is fuel present
(fuel gauge faulty).
Check the fuel is of the correct type.
Check the hosesCheck no hoses are pinched
(especially after a removal operation).
Disconnect the pipe connecting the canister bleed solenoid valve
to the inlet manifold.
Plug the pipe to prevent an air leak.
If there is no other effect, the canister bleed is faulty.
Check the fuel
Connect the OPTIMA 5800 station to carry out the compression
test and follow the instructions.
Connect the OPTIMA 5800 station to carry out the flywheel test
and follow the instructions.
Check the idle speed
regulation valveTap gently to release the valve.
Check the flywheel
Check the engine
compression
Check the canister bleed
17-129