Page 78 of 455
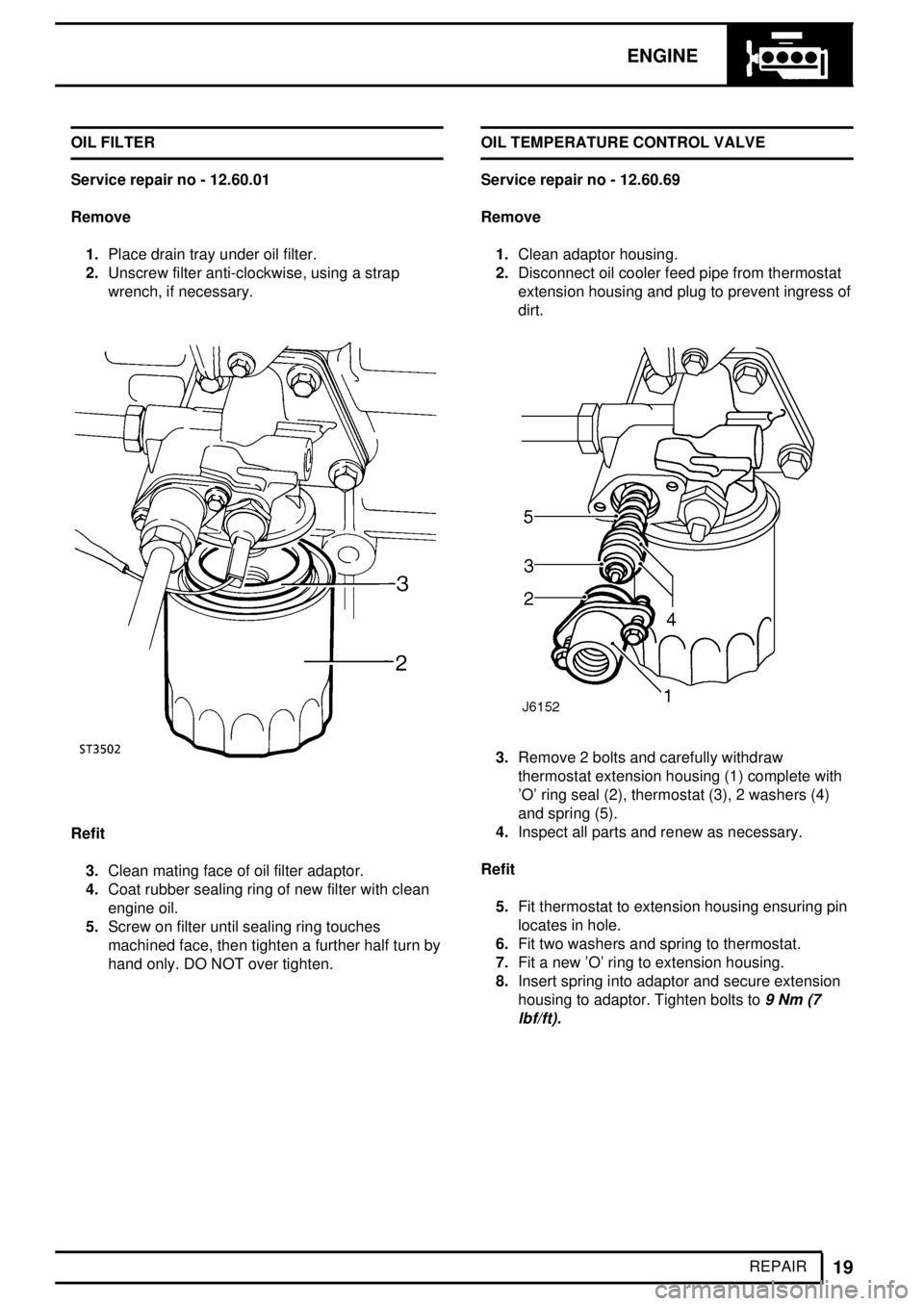
ENGINE
19
REPAIR OIL FILTER
Service repair no - 12.60.01
Remove
1.Place drain tray under oil filter.
2.Unscrew filter anti-clockwise, using a strap
wrench, if necessary.
Refit
3.Clean mating face of oil filter adaptor.
4.Coat rubber sealing ring of new filter with clean
engine oil.
5.Screw on filter until sealing ring touches
machined face, then tighten a further half turn by
hand only. DO NOT over tighten.OIL TEMPERATURE CONTROL VALVE
Service repair no - 12.60.69
Remove
1.Clean adaptor housing.
2.Disconnect oil cooler feed pipe from thermostat
extension housing and plug to prevent ingress of
dirt.
3.Remove 2 bolts and carefully withdraw
thermostat extension housing (1) complete with
'O' ring seal (2), thermostat (3), 2 washers (4)
and spring (5).
4.Inspect all parts and renew as necessary.
Refit
5.Fit thermostat to extension housing ensuring pin
locates in hole.
6.Fit two washers and spring to thermostat.
7.Fit a new 'O' ring to extension housing.
8.Insert spring into adaptor and secure extension
housing to adaptor. Tighten bolts to
9Nm(7
lbf/ft).
Page 79 of 455
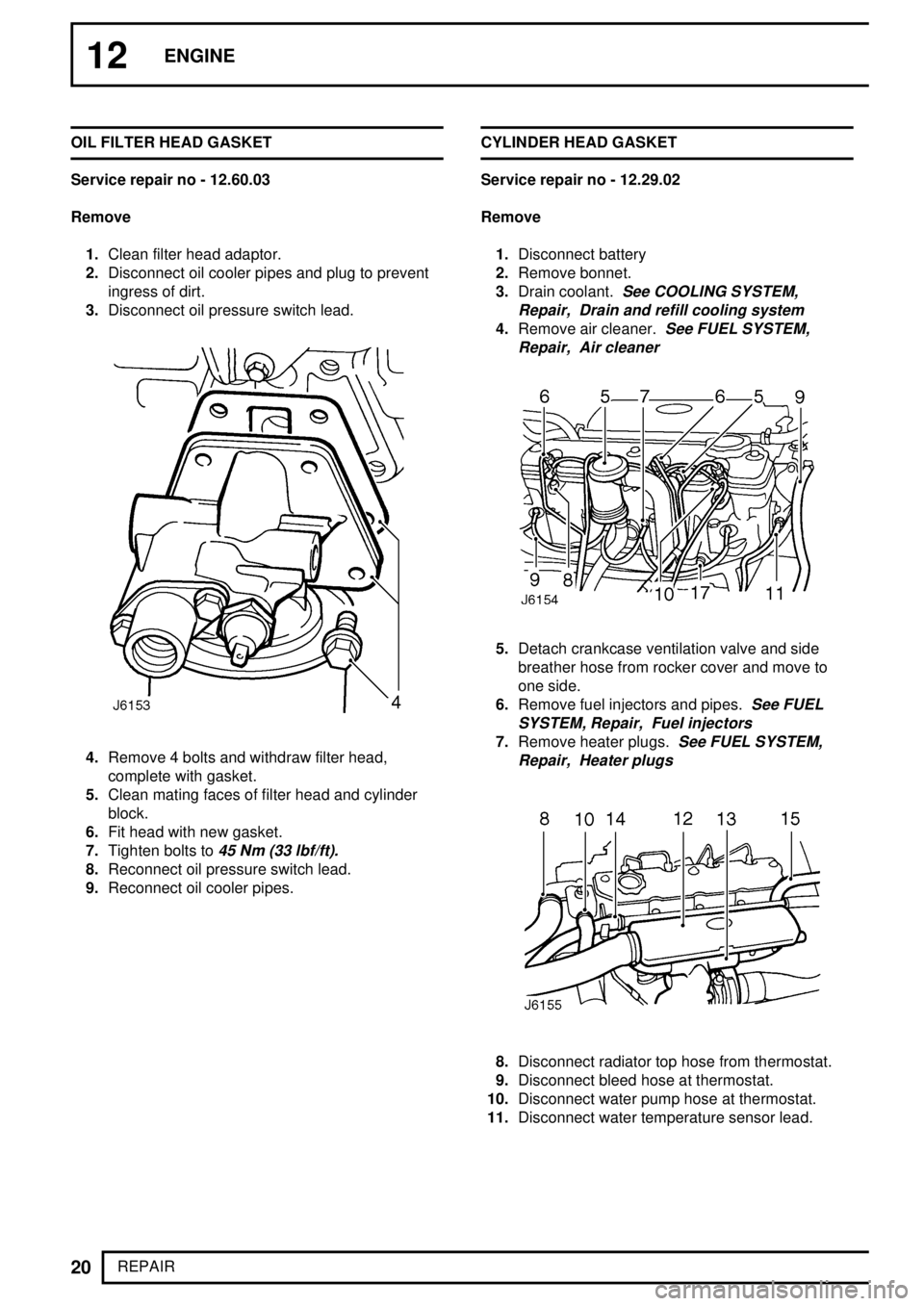
12ENGINE
20
REPAIR OIL FILTER HEAD GASKET
Service repair no - 12.60.03
Remove
1.Clean filter head adaptor.
2.Disconnect oil cooler pipes and plug to prevent
ingress of dirt.
3.Disconnect oil pressure switch lead.
4.Remove 4 bolts and withdraw filter head,
complete with gasket.
5.Clean mating faces of filter head and cylinder
block.
6.Fit head with new gasket.
7.Tighten bolts to
45 Nm (33 lbf/ft).
8.Reconnect oil pressure switch lead.
9.Reconnect oil cooler pipes.CYLINDER HEAD GASKET
Service repair no - 12.29.02
Remove
1.Disconnect battery
2.Remove bonnet.
3.Drain coolant.
See COOLING SYSTEM,
Repair, Drain and refill cooling system
4.Remove air cleaner.See FUEL SYSTEM,
Repair, Air cleaner
5.Detach crankcase ventilation valve and side
breather hose from rocker cover and move to
one side.
6.Remove fuel injectors and pipes.
See FUEL
SYSTEM, Repair, Fuel injectors
7.Remove heater plugs.See FUEL SYSTEM,
Repair, Heater plugs
8.Disconnect radiator top hose from thermostat.
9.Disconnect bleed hose at thermostat.
10.Disconnect water pump hose at thermostat.
11.Disconnect water temperature sensor lead.
Page 82 of 455
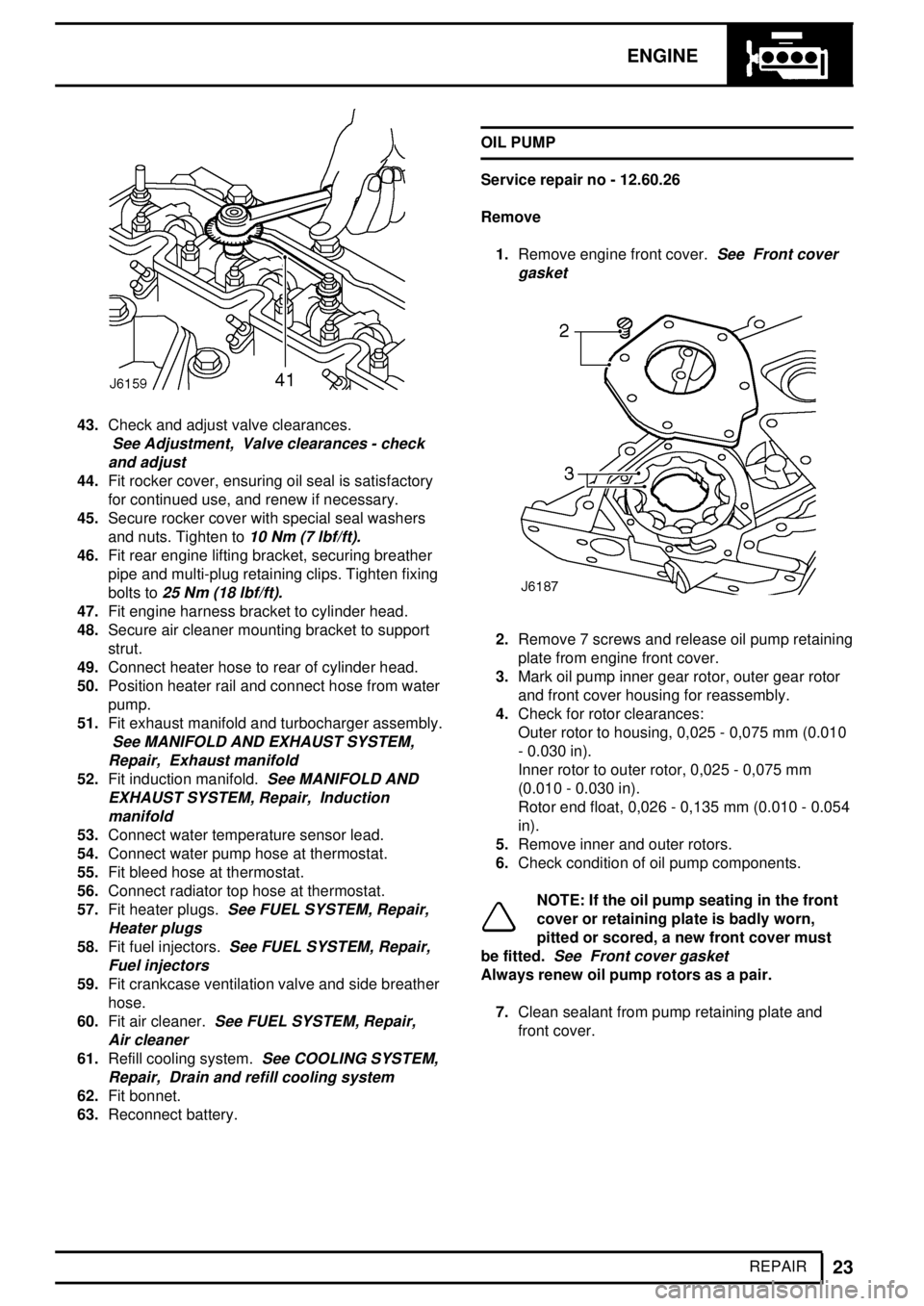
ENGINE
23
REPAIR
43.Check and adjust valve clearances.
See Adjustment, Valve clearances - check
and adjust
44.Fit rocker cover, ensuring oil seal is satisfactory
for continued use, and renew if necessary.
45.Secure rocker cover with special seal washers
and nuts. Tighten to
10 Nm (7 lbf/ft).
46.Fit rear engine lifting bracket, securing breather
pipe and multi-plug retaining clips. Tighten fixing
bolts to
25 Nm (18 lbf/ft).
47.Fit engine harness bracket to cylinder head.
48.Secure air cleaner mounting bracket to support
strut.
49.Connect heater hose to rear of cylinder head.
50.Position heater rail and connect hose from water
pump.
51.Fit exhaust manifold and turbocharger assembly.
See MANIFOLD AND EXHAUST SYSTEM,
Repair, Exhaust manifold
52.Fit induction manifold.See MANIFOLD AND
EXHAUST SYSTEM, Repair, Induction
manifold
53.Connect water temperature sensor lead.
54.Connect water pump hose at thermostat.
55.Fit bleed hose at thermostat.
56.Connect radiator top hose at thermostat.
57.Fit heater plugs.
See FUEL SYSTEM, Repair,
Heater plugs
58.Fit fuel injectors.See FUEL SYSTEM, Repair,
Fuel injectors
59.Fit crankcase ventilation valve and side breather
hose.
60.Fit air cleaner.
See FUEL SYSTEM, Repair,
Air cleaner
61.Refill cooling system.See COOLING SYSTEM,
Repair, Drain and refill cooling system
62.Fit bonnet.
63.Reconnect battery.OIL PUMP
Service repair no - 12.60.26
Remove
1.Remove engine front cover.
See Front cover
gasket
2.Remove 7 screws and release oil pump retaining
plate from engine front cover.
3.Mark oil pump inner gear rotor, outer gear rotor
and front cover housing for reassembly.
4.Check for rotor clearances:
Outer rotor to housing, 0,025 - 0,075 mm (0.010
- 0.030 in).
Inner rotor to outer rotor, 0,025 - 0,075 mm
(0.010 - 0.030 in).
Rotor end float, 0,026 - 0,135 mm (0.010 - 0.054
in).
5.Remove inner and outer rotors.
6.Check condition of oil pump components.
NOTE: If the oil pump seating in the front
cover or retaining plate is badly worn,
pitted or scored, a new front cover must
be fitted.
See Front cover gasket
Always renew oil pump rotors as a pair.
7.Clean sealant from pump retaining plate and
front cover.
Page 83 of 455
12ENGINE
24
REPAIR Refit
8.Fit oil pump rotors in front cover.
9.Apply a bead of RTV sealant around retaining
plate.
10.Fit oil pump retaining plate to front cover,
securely tighten screws.
11.Fit front cover to cylinder block.
See Front
cover gasket
OIL PRESSURE RELIEF VALVE
Service repair no - 12.60.56
Remove
1.Remove engine oil sump.
See Engine oil
sump
2.Unscrew relief valve retaining plug from base of
front cover.
3.Withdraw valve spring and plunger and check for
wear.
Valve spring free length, 68.00 mm (2.68 in).
NOTE: If the valve plunger sleeve is badly
worn, pitted or scored, a new front cover
must be fitted.
See Front cover gasket
Always renew valve spring and plunger as a pair.
Refit
4.Insert valve plunger and spring into sleeve in
front cover and secure with retaining plug.
5.Fit engine oil sump.
See Engine oil sump
Page 99 of 455
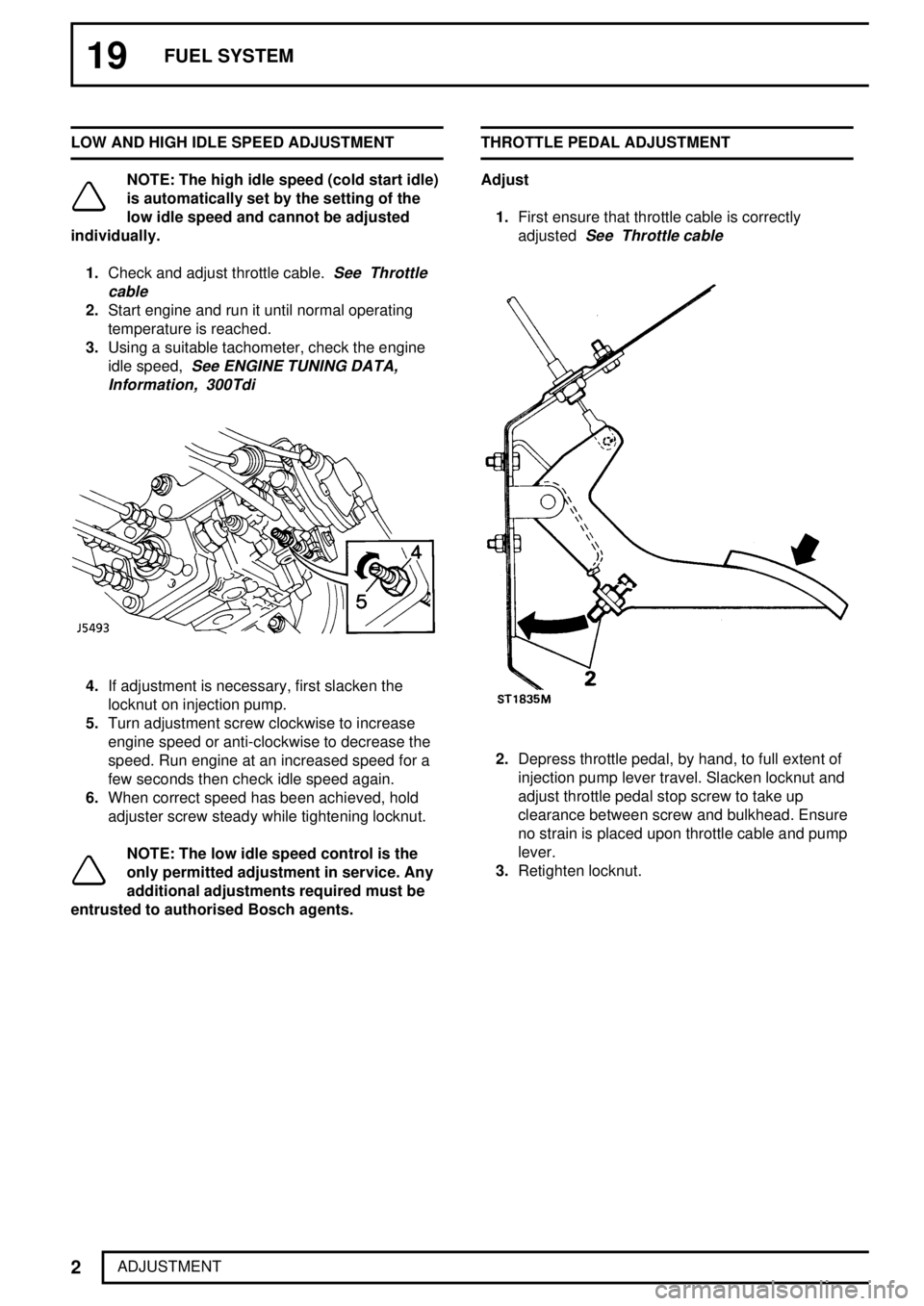
19FUEL SYSTEM
2
ADJUSTMENT LOW AND HIGH IDLE SPEED ADJUSTMENT
NOTE: The high idle speed (cold start idle)
is automatically set by the setting of the
low idle speed and cannot be adjusted
individually.
1.Check and adjust throttle cable.
See Throttle
cable
2.Start engine and run it until normal operating
temperature is reached.
3.Using a suitable tachometer, check the engine
idle speed,
See ENGINE TUNING DATA,
Information, 300Tdi
4.If adjustment is necessary, first slacken the
locknut on injection pump.
5.Turn adjustment screw clockwise to increase
engine speed or anti-clockwise to decrease the
speed. Run engine at an increased speed for a
few seconds then check idle speed again.
6.When correct speed has been achieved, hold
adjuster screw steady while tightening locknut.
NOTE: The low idle speed control is the
only permitted adjustment in service. Any
additional adjustments required must be
entrusted to authorised Bosch agents.THROTTLE PEDAL ADJUSTMENT
Adjust
1.First ensure that throttle cable is correctly
adjusted
See Throttle cable
2.Depress throttle pedal, by hand, to full extent of
injection pump lever travel. Slacken locknut and
adjust throttle pedal stop screw to take up
clearance between screw and bulkhead. Ensure
no strain is placed upon throttle cable and pump
lever.
3.Retighten locknut.
Page 100 of 455
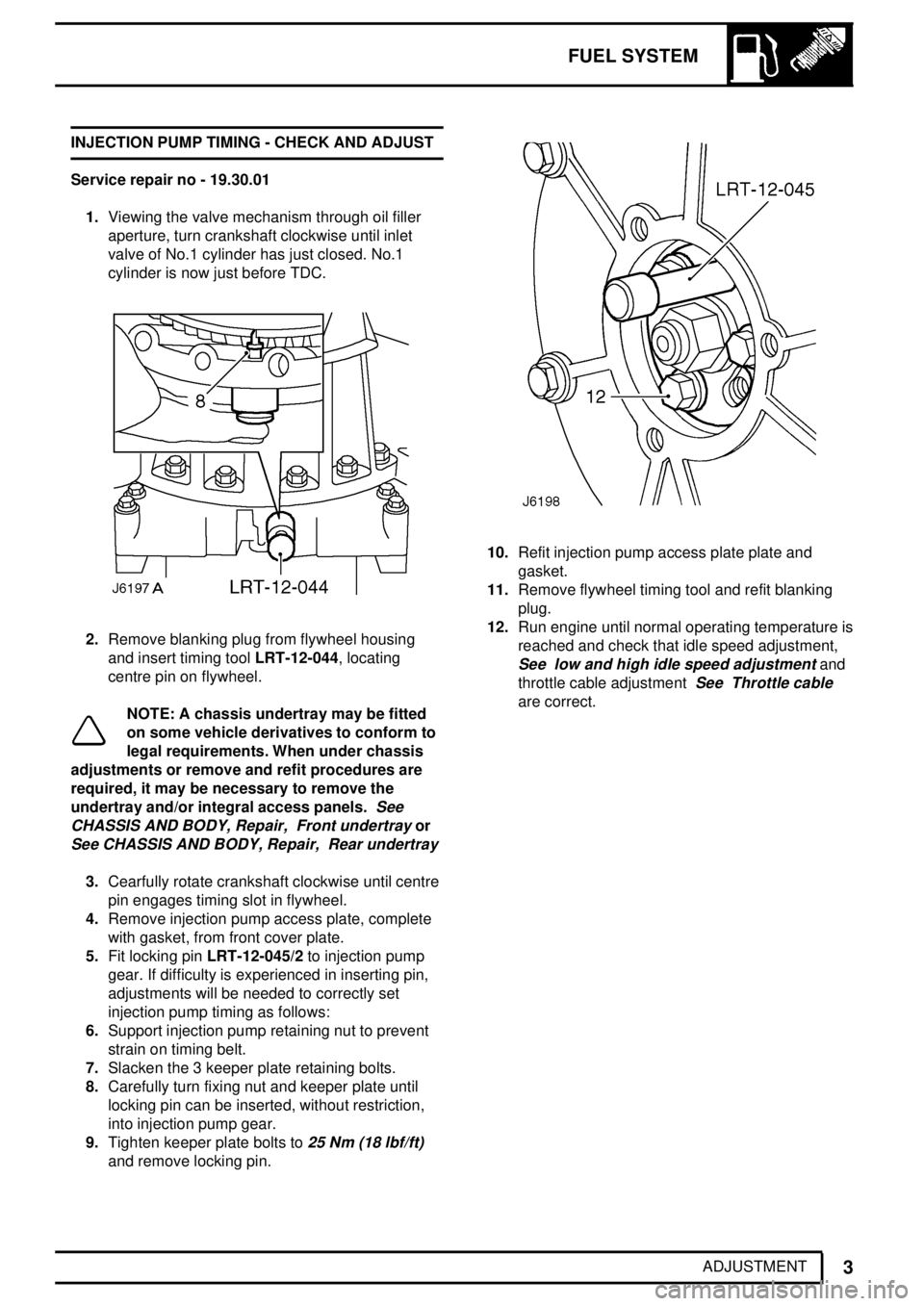
FUEL SYSTEM
3
ADJUSTMENT INJECTION PUMP TIMING - CHECK AND ADJUST
Service repair no - 19.30.01
1.Viewing the valve mechanism through oil filler
aperture, turn crankshaft clockwise until inlet
valve of No.1 cylinder has just closed. No.1
cylinder is now just before TDC.
2.Remove blanking plug from flywheel housing
and insert timing toolLRT-12-044, locating
centre pin on flywheel.
NOTE: A chassis undertray may be fitted
on some vehicle derivatives to conform to
legal requirements. When under chassis
adjustments or remove and refit procedures are
required, it may be necessary to remove the
undertray and/or integral access panels.
See
CHASSIS AND BODY, Repair, Front undertray
or
See CHASSIS AND BODY, Repair, Rear undertray
3.Cearfully rotate crankshaft clockwise until centre
pin engages timing slot in flywheel.
4.Remove injection pump access plate, complete
with gasket, from front cover plate.
5.Fit locking pinLRT-12-045/2to injection pump
gear. If difficulty is experienced in inserting pin,
adjustments will be needed to correctly set
injection pump timing as follows:
6.Support injection pump retaining nut to prevent
strain on timing belt.
7.Slacken the 3 keeper plate retaining bolts.
8.Carefully turn fixing nut and keeper plate until
locking pin can be inserted, without restriction,
into injection pump gear.
9.Tighten keeper plate bolts to
25 Nm (18 lbf/ft)
and remove locking pin.
10.Refit injection pump access plate plate and
gasket.
11.Remove flywheel timing tool and refit blanking
plug.
12.Run engine until normal operating temperature is
reached and check that idle speed adjustment,
See low and high idle speed adjustmentand
throttle cable adjustment
See Throttle cable
are correct.
Page 101 of 455
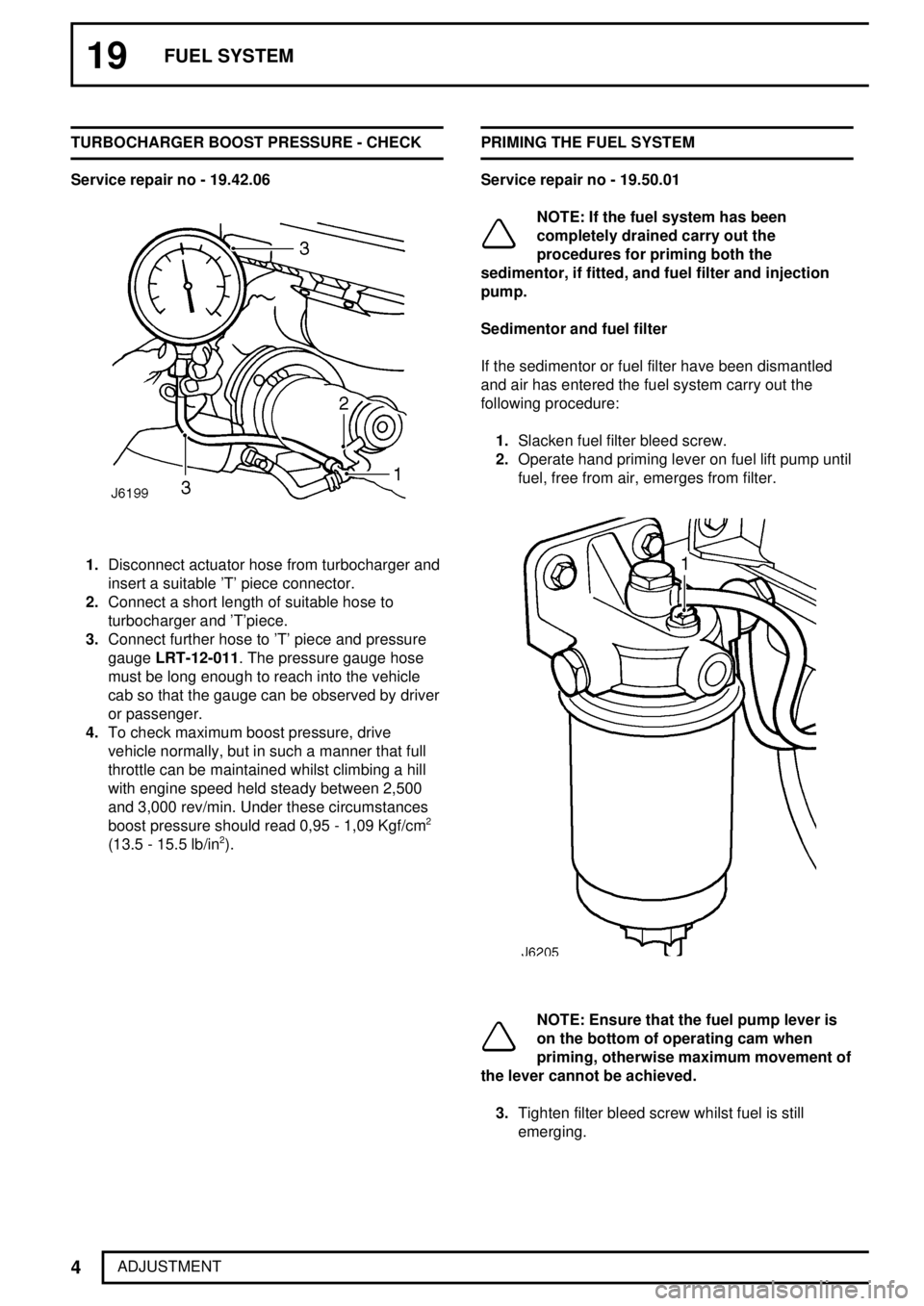
19FUEL SYSTEM
4
ADJUSTMENT TURBOCHARGER BOOST PRESSURE - CHECK
Service repair no - 19.42.06
1.Disconnect actuator hose from turbocharger and
insert a suitable 'T' piece connector.
2.Connect a short length of suitable hose to
turbocharger and 'T'piece.
3.Connect further hose to 'T' piece and pressure
gaugeLRT-12-011. The pressure gauge hose
must be long enough to reach into the vehicle
cab so that the gauge can be observed by driver
or passenger.
4.To check maximum boost pressure, drive
vehicle normally, but in such a manner that full
throttle can be maintained whilst climbing a hill
with engine speed held steady between 2,500
and 3,000 rev/min. Under these circumstances
boost pressure should read 0,95 - 1,09 Kgf/cm
2
(13.5 - 15.5 lb/in2).PRIMING THE FUEL SYSTEM
Service repair no - 19.50.01
NOTE: If the fuel system has been
completely drained carry out the
procedures for priming both the
sedimentor, if fitted, and fuel filter and injection
pump.
Sedimentor and fuel filter
If the sedimentor or fuel filter have been dismantled
and air has entered the fuel system carry out the
following procedure:
1.Slacken fuel filter bleed screw.
2.Operate hand priming lever on fuel lift pump until
fuel, free from air, emerges from filter.
NOTE: Ensure that the fuel pump lever is
on the bottom of operating cam when
priming, otherwise maximum movement of
the lever cannot be achieved.
3.Tighten filter bleed screw whilst fuel is still
emerging.
Page 103 of 455
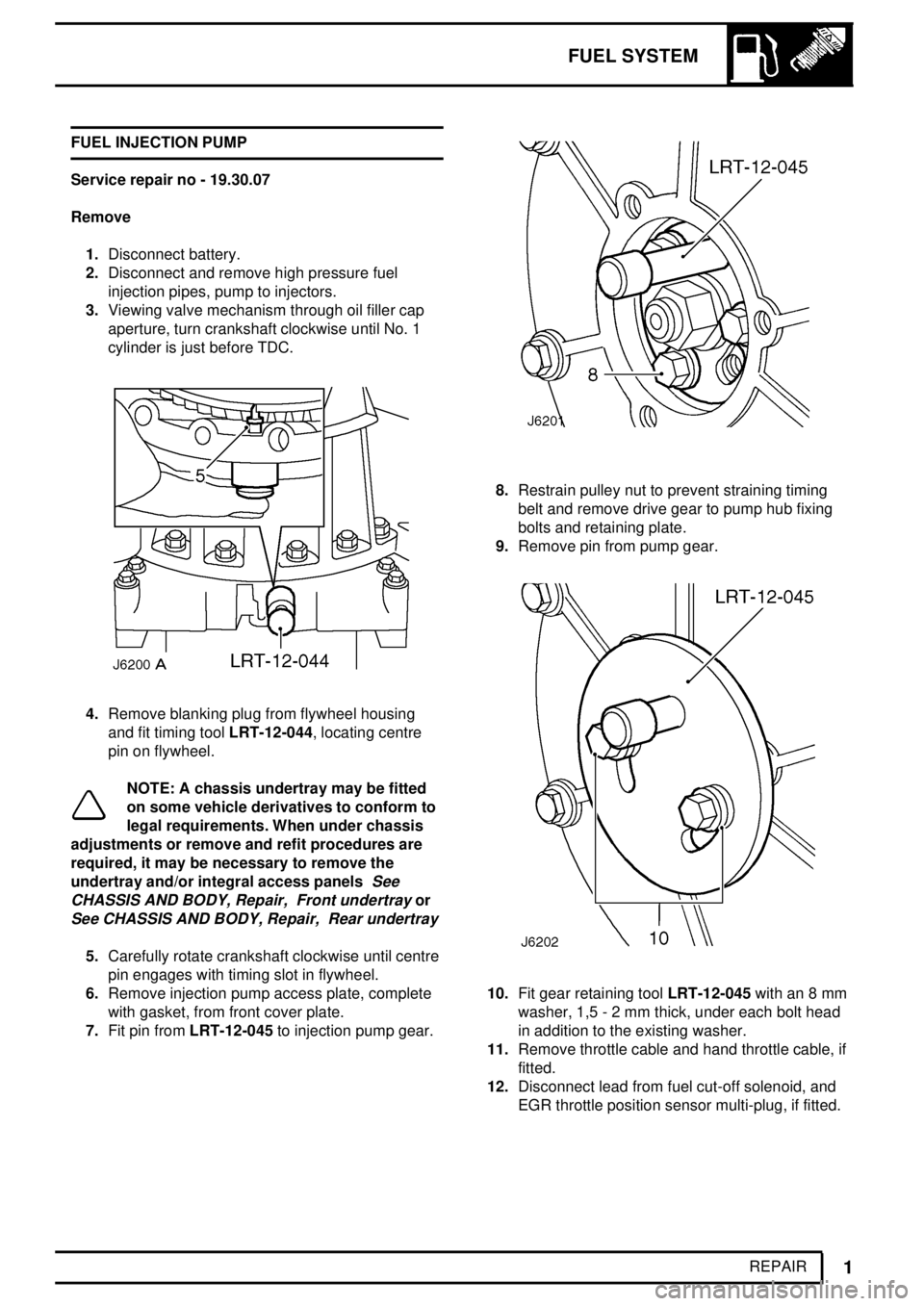
FUEL SYSTEM
1
REPAIR FUEL INJECTION PUMP
Service repair no - 19.30.07
Remove
1.Disconnect battery.
2.Disconnect and remove high pressure fuel
injection pipes, pump to injectors.
3.Viewing valve mechanism through oil filler cap
aperture, turn crankshaft clockwise until No. 1
cylinder is just before TDC.
4.Remove blanking plug from flywheel housing
and fit timing toolLRT-12-044, locating centre
pin on flywheel.
NOTE: A chassis undertray may be fitted
on some vehicle derivatives to conform to
legal requirements. When under chassis
adjustments or remove and refit procedures are
required, it may be necessary to remove the
undertray and/or integral access panels
See
CHASSIS AND BODY, Repair, Front undertray
or
See CHASSIS AND BODY, Repair, Rear undertray
5.Carefully rotate crankshaft clockwise until centre
pin engages with timing slot in flywheel.
6.Remove injection pump access plate, complete
with gasket, from front cover plate.
7.Fit pin fromLRT-12-045to injection pump gear.
8.Restrain pulley nut to prevent straining timing
belt and remove drive gear to pump hub fixing
bolts and retaining plate.
9.Remove pin from pump gear.
10.Fit gear retaining toolLRT-12-045with an 8 mm
washer, 1,5 - 2 mm thick, under each bolt head
in addition to the existing washer.
11.Remove throttle cable and hand throttle cable, if
fitted.
12.Disconnect lead from fuel cut-off solenoid, and
EGR throttle position sensor multi-plug, if fitted.