Page 136 of 455
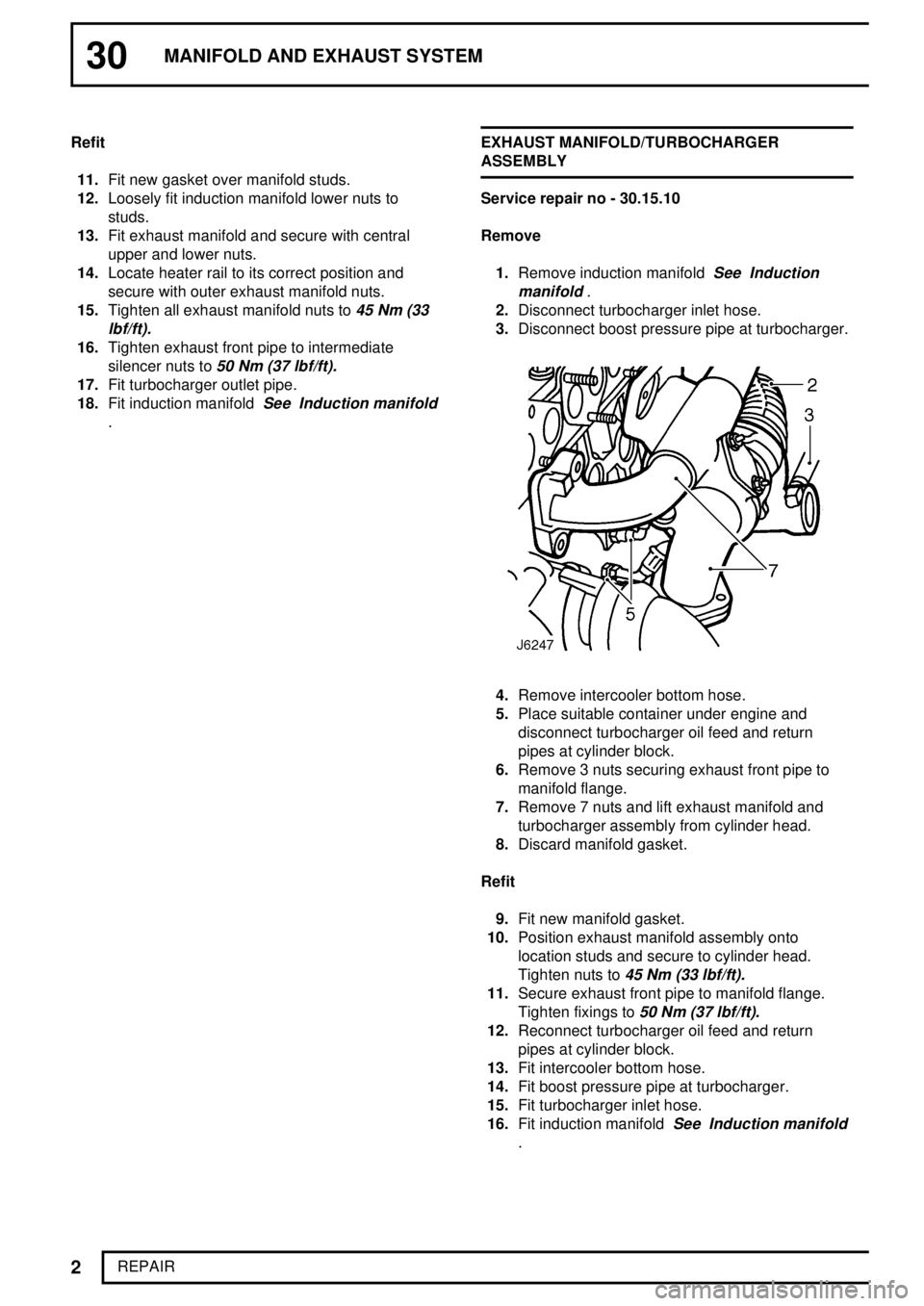
30MANIFOLD AND EXHAUST SYSTEM
2
REPAIR Refit
11.Fit new gasket over manifold studs.
12.Loosely fit induction manifold lower nuts to
studs.
13.Fit exhaust manifold and secure with central
upper and lower nuts.
14.Locate heater rail to its correct position and
secure with outer exhaust manifold nuts.
15.Tighten all exhaust manifold nuts to
45 Nm (33
lbf/ft).
16.Tighten exhaust front pipe to intermediate
silencer nuts to
50 Nm (37 lbf/ft).
17.Fit turbocharger outlet pipe.
18.Fit induction manifold
See Induction manifold
.EXHAUST MANIFOLD/TURBOCHARGER
ASSEMBLY
Service repair no - 30.15.10
Remove
1.Remove induction manifold
See Induction
manifold
.
2.Disconnect turbocharger inlet hose.
3.Disconnect boost pressure pipe at turbocharger.
4.Remove intercooler bottom hose.
5.Place suitable container under engine and
disconnect turbocharger oil feed and return
pipes at cylinder block.
6.Remove 3 nuts securing exhaust front pipe to
manifold flange.
7.Remove 7 nuts and lift exhaust manifold and
turbocharger assembly from cylinder head.
8.Discard manifold gasket.
Refit
9.Fit new manifold gasket.
10.Position exhaust manifold assembly onto
location studs and secure to cylinder head.
Tighten nuts to
45 Nm (33 lbf/ft).
11.Secure exhaust front pipe to manifold flange.
Tighten fixings to
50 Nm (37 lbf/ft).
12.Reconnect turbocharger oil feed and return
pipes at cylinder block.
13.Fit intercooler bottom hose.
14.Fit boost pressure pipe at turbocharger.
15.Fit turbocharger inlet hose.
16.Fit induction manifold
See Induction manifold
.
Page 137 of 455
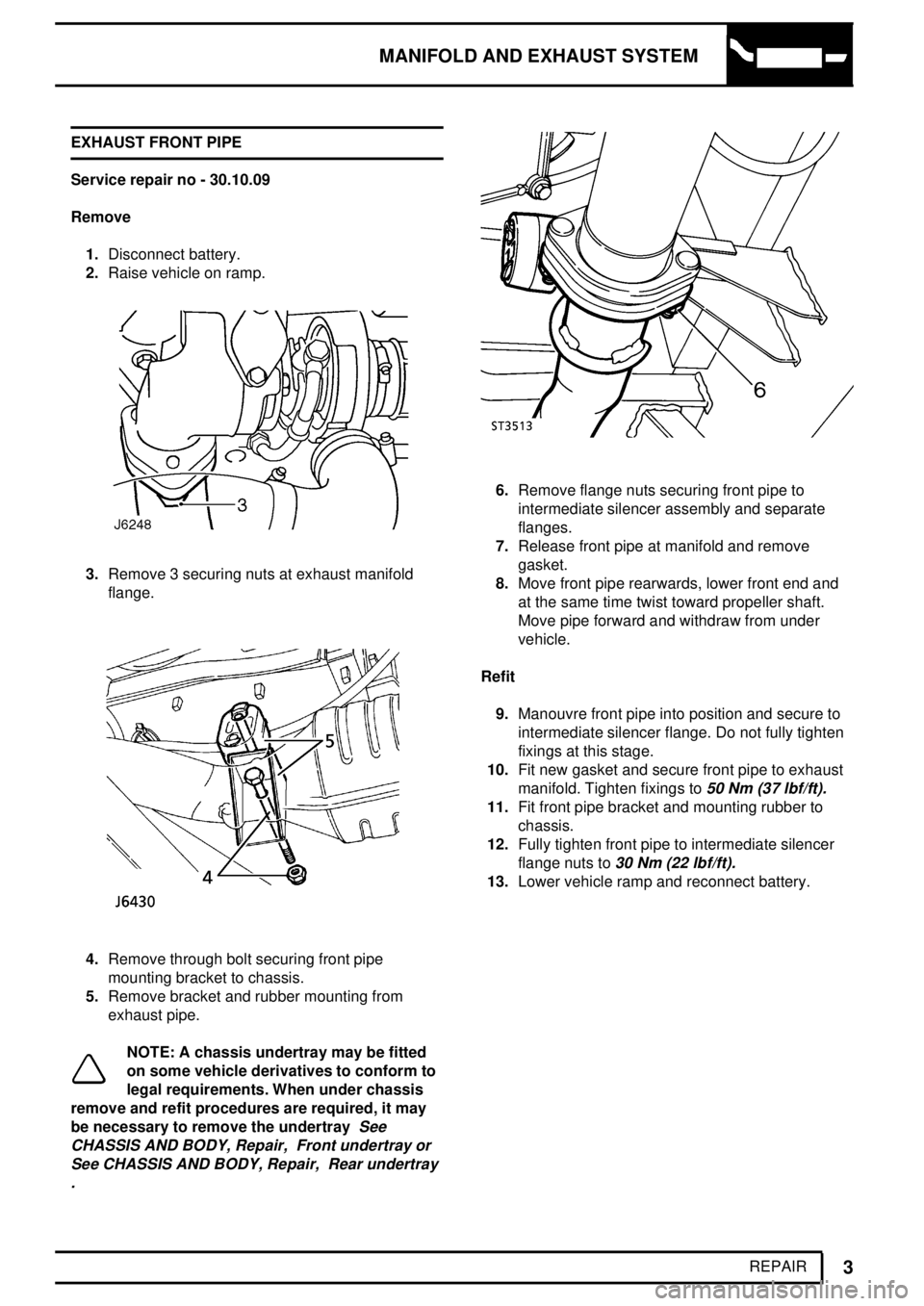
MANIFOLD AND EXHAUST SYSTEM
3
REPAIR EXHAUST FRONT PIPE
Service repair no - 30.10.09
Remove
1.Disconnect battery.
2.Raise vehicle on ramp.
3.Remove 3 securing nuts at exhaust manifold
flange.
4.Remove through bolt securing front pipe
mounting bracket to chassis.
5.Remove bracket and rubber mounting from
exhaust pipe.
NOTE: A chassis undertray may be fitted
on some vehicle derivatives to conform to
legal requirements. When under chassis
remove and refit procedures are required, it may
be necessary to remove the undertray
See
CHASSIS AND BODY, Repair, Front undertray or
See CHASSIS AND BODY, Repair, Rear undertray
.
6.Remove flange nuts securing front pipe to
intermediate silencer assembly and separate
flanges.
7.Release front pipe at manifold and remove
gasket.
8.Move front pipe rearwards, lower front end and
at the same time twist toward propeller shaft.
Move pipe forward and withdraw from under
vehicle.
Refit
9.Manouvre front pipe into position and secure to
intermediate silencer flange. Do not fully tighten
fixings at this stage.
10.Fit new gasket and secure front pipe to exhaust
manifold. Tighten fixings to
50 Nm (37 lbf/ft).
11.Fit front pipe bracket and mounting rubber to
chassis.
12.Fully tighten front pipe to intermediate silencer
flange nuts to
30 Nm (22 lbf/ft).
13.Lower vehicle ramp and reconnect battery.
Page 138 of 455
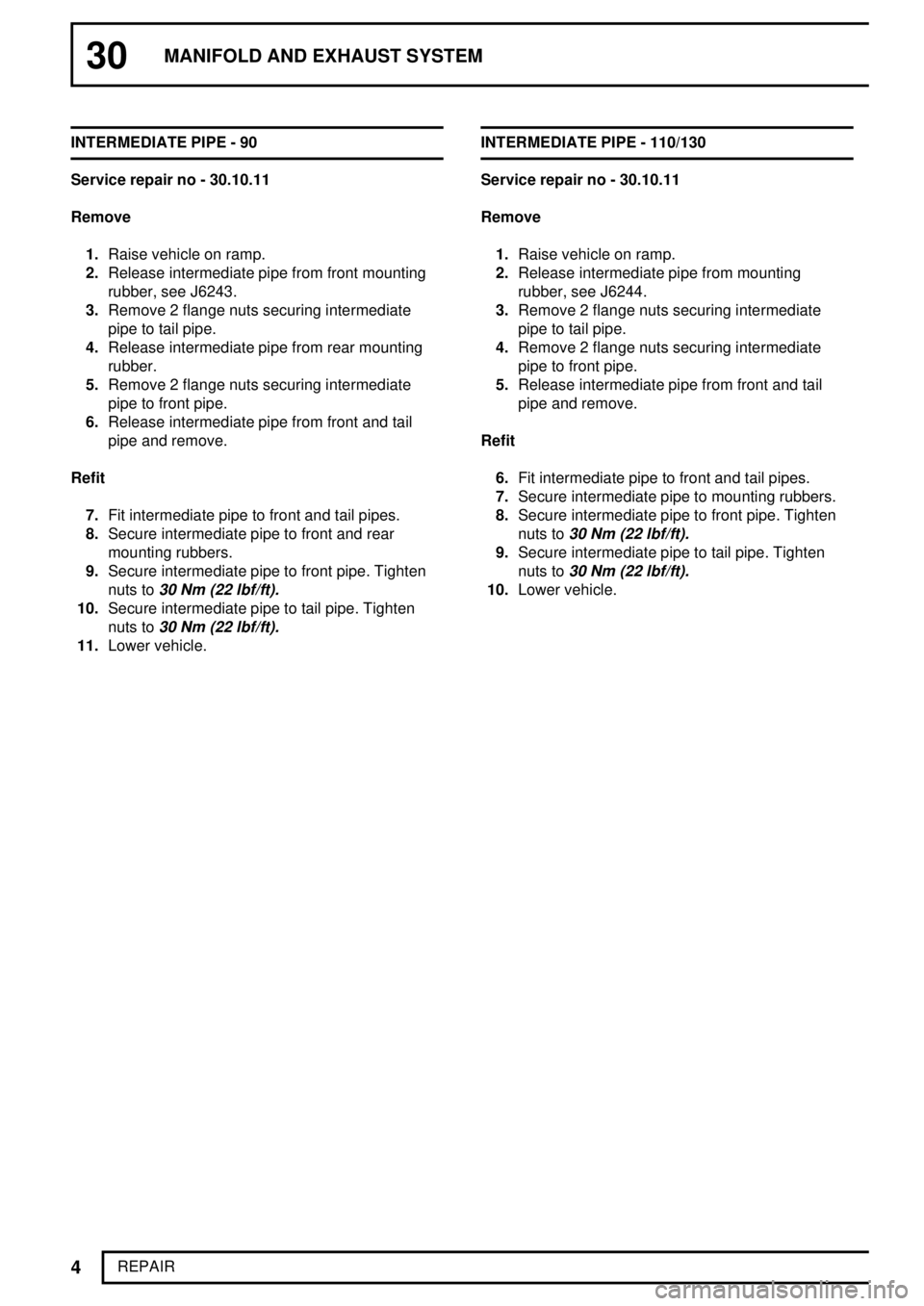
30MANIFOLD AND EXHAUST SYSTEM
4
REPAIR INTERMEDIATE PIPE - 90
Service repair no - 30.10.11
Remove
1.Raise vehicle on ramp.
2.Release intermediate pipe from front mounting
rubber, see J6243.
3.Remove 2 flange nuts securing intermediate
pipe to tail pipe.
4.Release intermediate pipe from rear mounting
rubber.
5.Remove 2 flange nuts securing intermediate
pipe to front pipe.
6.Release intermediate pipe from front and tail
pipe and remove.
Refit
7.Fit intermediate pipe to front and tail pipes.
8.Secure intermediate pipe to front and rear
mounting rubbers.
9.Secure intermediate pipe to front pipe. Tighten
nuts to
30 Nm (22 lbf/ft).
10.Secure intermediate pipe to tail pipe. Tighten
nuts to
30 Nm (22 lbf/ft).
11.Lower vehicle.INTERMEDIATE PIPE - 110/130
Service repair no - 30.10.11
Remove
1.Raise vehicle on ramp.
2.Release intermediate pipe from mounting
rubber, see J6244.
3.Remove 2 flange nuts securing intermediate
pipe to tail pipe.
4.Remove 2 flange nuts securing intermediate
pipe to front pipe.
5.Release intermediate pipe from front and tail
pipe and remove.
Refit
6.Fit intermediate pipe to front and tail pipes.
7.Secure intermediate pipe to mounting rubbers.
8.Secure intermediate pipe to front pipe. Tighten
nuts to
30 Nm (22 lbf/ft).
9.Secure intermediate pipe to tail pipe. Tighten
nuts to
30 Nm (22 lbf/ft).
10.Lower vehicle.
Page 139 of 455
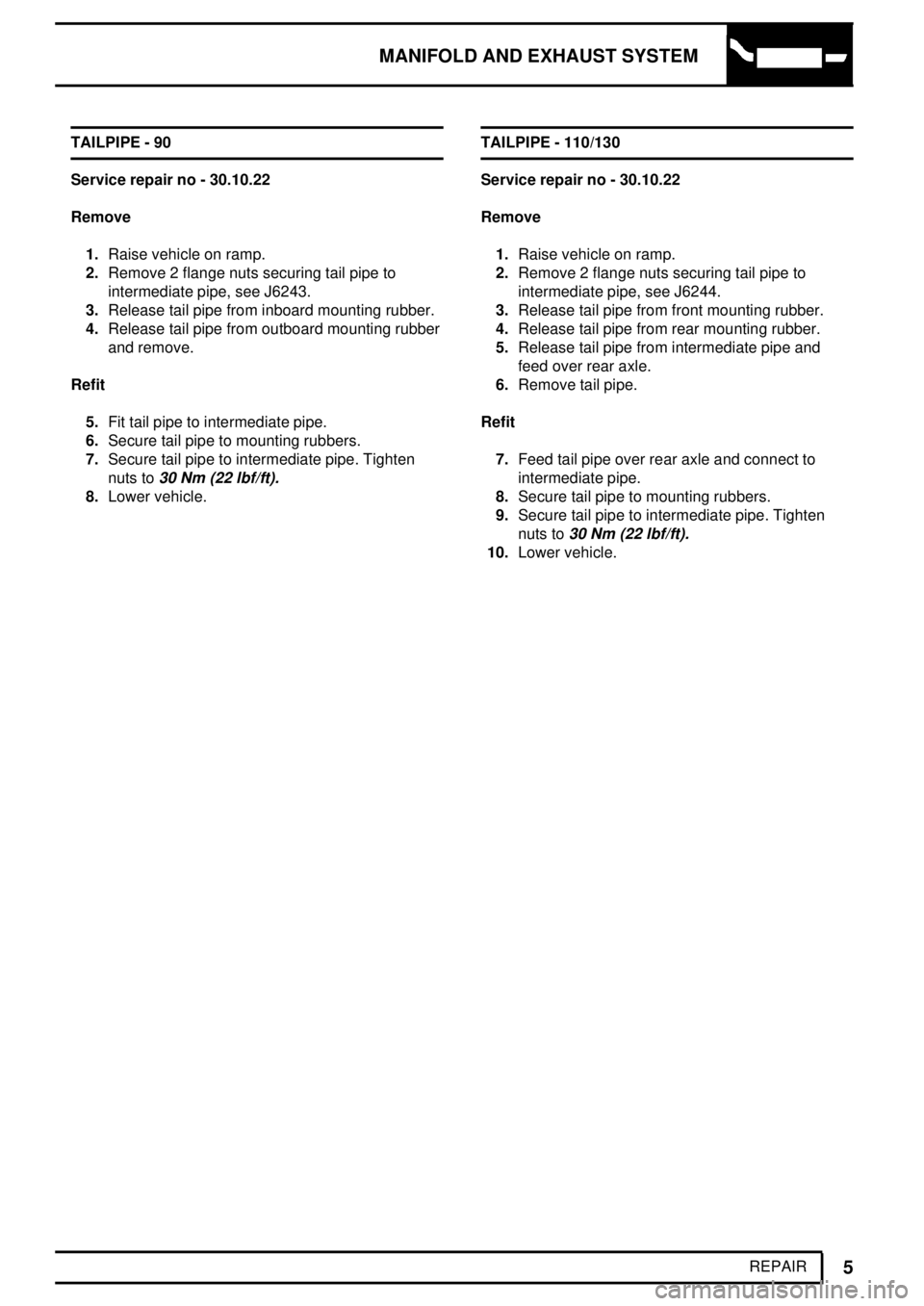
MANIFOLD AND EXHAUST SYSTEM
5
REPAIR TAILPIPE - 90
Service repair no - 30.10.22
Remove
1.Raise vehicle on ramp.
2.Remove 2 flange nuts securing tail pipe to
intermediate pipe, see J6243.
3.Release tail pipe from inboard mounting rubber.
4.Release tail pipe from outboard mounting rubber
and remove.
Refit
5.Fit tail pipe to intermediate pipe.
6.Secure tail pipe to mounting rubbers.
7.Secure tail pipe to intermediate pipe. Tighten
nuts to
30 Nm (22 lbf/ft).
8.Lower vehicle.TAILPIPE - 110/130
Service repair no - 30.10.22
Remove
1.Raise vehicle on ramp.
2.Remove 2 flange nuts securing tail pipe to
intermediate pipe, see J6244.
3.Release tail pipe from front mounting rubber.
4.Release tail pipe from rear mounting rubber.
5.Release tail pipe from intermediate pipe and
feed over rear axle.
6.Remove tail pipe.
Refit
7.Feed tail pipe over rear axle and connect to
intermediate pipe.
8.Secure tail pipe to mounting rubbers.
9.Secure tail pipe to intermediate pipe. Tighten
nuts to
30 Nm (22 lbf/ft).
10.Lower vehicle.
Page 145 of 455
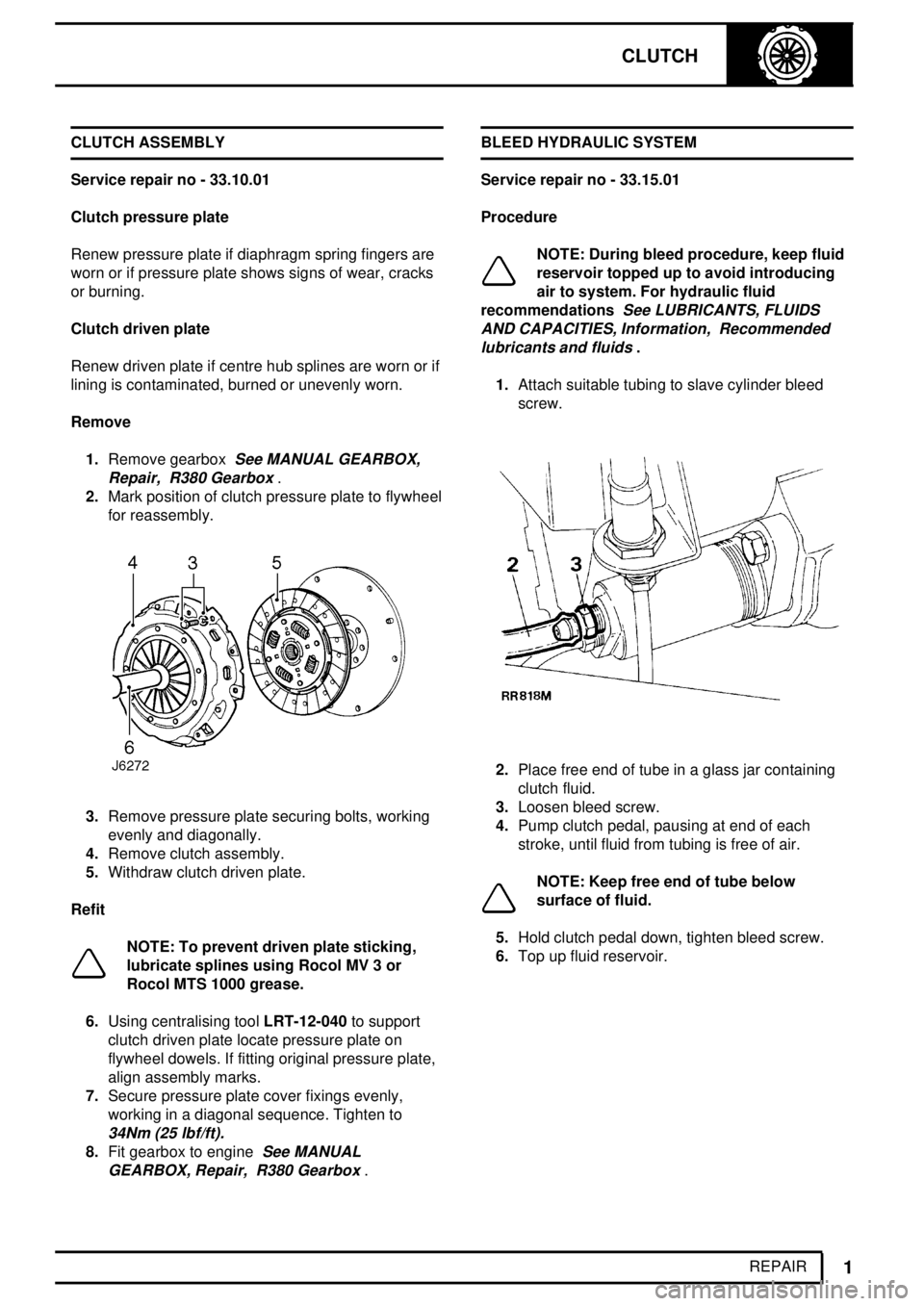
CLUTCH
1
REPAIR CLUTCH ASSEMBLY
Service repair no - 33.10.01
Clutch pressure plate
Renew pressure plate if diaphragm spring fingers are
worn or if pressure plate shows signs of wear, cracks
or burning.
Clutch driven plate
Renew driven plate if centre hub splines are worn or if
lining is contaminated, burned or unevenly worn.
Remove
1.Remove gearbox
See MANUAL GEARBOX,
Repair, R380 Gearbox
.
2.Mark position of clutch pressure plate to flywheel
for reassembly.
3.Remove pressure plate securing bolts, working
evenly and diagonally.
4.Remove clutch assembly.
5.Withdraw clutch driven plate.
Refit
NOTE: To prevent driven plate sticking,
lubricate splines using Rocol MV 3 or
Rocol MTS 1000 grease.
6.Using centralising toolLRT-12-040to support
clutch driven plate locate pressure plate on
flywheel dowels. If fitting original pressure plate,
align assembly marks.
7.Secure pressure plate cover fixings evenly,
working in a diagonal sequence. Tighten to
34Nm (25 lbf/ft).
8.Fit gearbox to engineSee MANUAL
GEARBOX, Repair, R380 Gearbox
.BLEED HYDRAULIC SYSTEM
Service repair no - 33.15.01
Procedure
NOTE: During bleed procedure, keep fluid
reservoir topped up to avoid introducing
air to system. For hydraulic fluid
recommendations
See LUBRICANTS, FLUIDS
AND CAPACITIES, Information, Recommended
lubricants and fluids
.
1.Attach suitable tubing to slave cylinder bleed
screw.
2.Place free end of tube in a glass jar containing
clutch fluid.
3.Loosen bleed screw.
4.Pump clutch pedal, pausing at end of each
stroke, until fluid from tubing is free of air.
NOTE: Keep free end of tube below
surface of fluid.
5.Hold clutch pedal down, tighten bleed screw.
6.Top up fluid reservoir.
Page 146 of 455
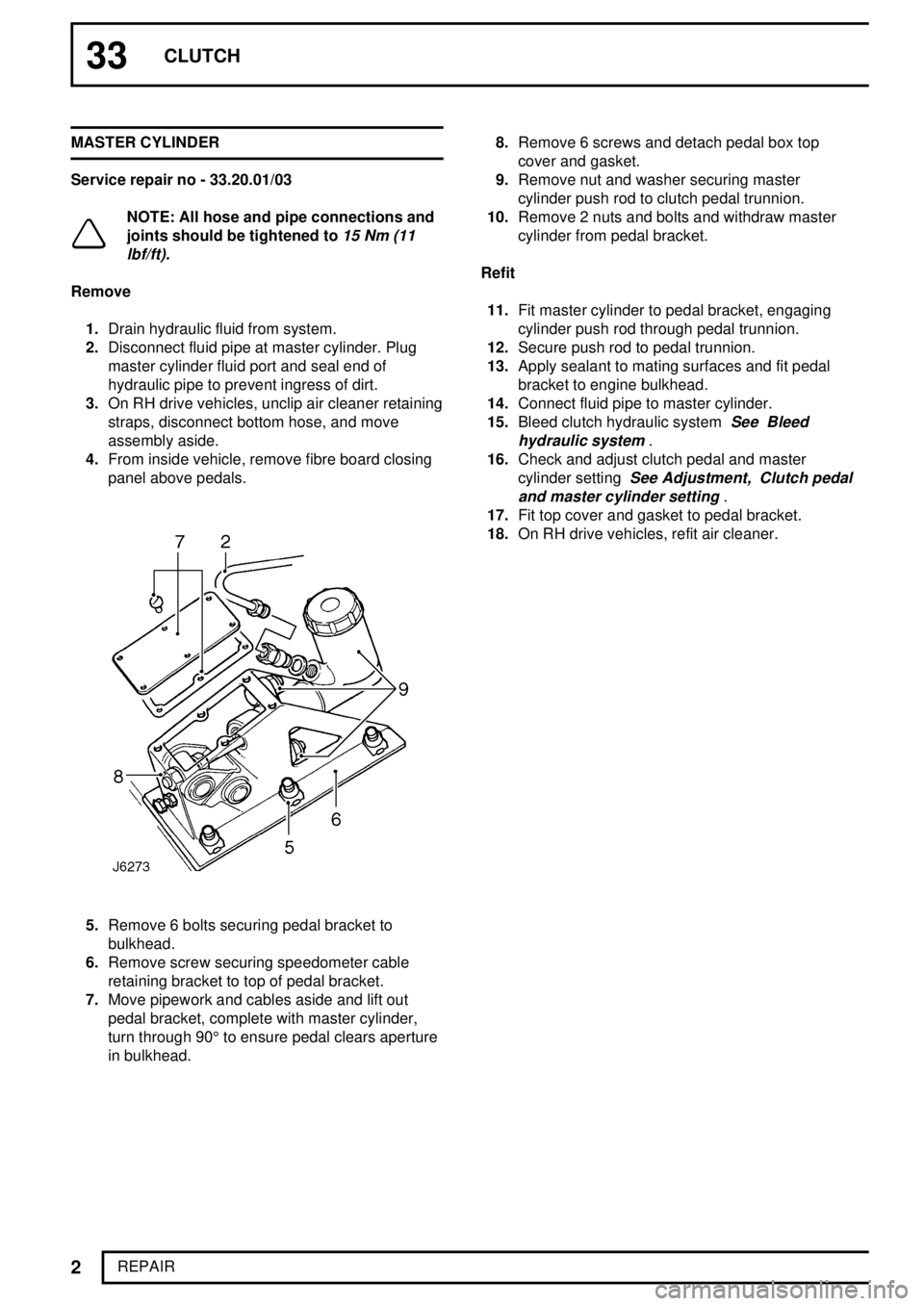
33CLUTCH
2
REPAIR MASTER CYLINDER
Service repair no - 33.20.01/03
NOTE: All hose and pipe connections and
joints should be tightened to
15 Nm (11
lbf/ft).
Remove
1.Drain hydraulic fluid from system.
2.Disconnect fluid pipe at master cylinder. Plug
master cylinder fluid port and seal end of
hydraulic pipe to prevent ingress of dirt.
3.On RH drive vehicles, unclip air cleaner retaining
straps, disconnect bottom hose, and move
assembly aside.
4.From inside vehicle, remove fibre board closing
panel above pedals.
5.Remove 6 bolts securing pedal bracket to
bulkhead.
6.Remove screw securing speedometer cable
retaining bracket to top of pedal bracket.
7.Move pipework and cables aside and lift out
pedal bracket, complete with master cylinder,
turn through 90°to ensure pedal clears aperture
in bulkhead.8.Remove 6 screws and detach pedal box top
cover and gasket.
9.Remove nut and washer securing master
cylinder push rod to clutch pedal trunnion.
10.Remove 2 nuts and bolts and withdraw master
cylinder from pedal bracket.
Refit
11.Fit master cylinder to pedal bracket, engaging
cylinder push rod through pedal trunnion.
12.Secure push rod to pedal trunnion.
13.Apply sealant to mating surfaces and fit pedal
bracket to engine bulkhead.
14.Connect fluid pipe to master cylinder.
15.Bleed clutch hydraulic system
See Bleed
hydraulic system
.
16.Check and adjust clutch pedal and master
cylinder setting
See Adjustment, Clutch pedal
and master cylinder setting
.
17.Fit top cover and gasket to pedal bracket.
18.On RH drive vehicles, refit air cleaner.
Page 147 of 455
CLUTCH
3
REPAIR CLUTCH PEDAL
Service repair no - 33.33.02
Remove
1.Remove pedal bracket assembly and master
cylinder
See Master cylinder.
2.Release return spring from clutch pedal.
3.Using a suitable punch, drift out securing pin and
withdraw pedal pivot shaft.
4.Withdraw clutch pedal, complete with trunnion
and bush.
5.If necessary remove pivot bushes.
6.Examine components for wear and damage,
renew as necessary.
NOTE: If new pedal pivot bushes are
required they must be reamed to 16 mm
(0.625 in).
Refit
7.If removed, fit trunnion bush and trunnion to
clutch pedal. Lubricate components with general
purpose grease on assembly.
8.Fit pedal to bracket, insert pivot shaft and secure
with new pin.
9.Fit pedal return spring.
10.Fit master cylinder and pedal bracket assembly
See Master cylinder.
11.Adjust clutch pedal and master cylinder setting
See Adjustment, Clutch pedal and master
cylinder setting
.
Page 148 of 455
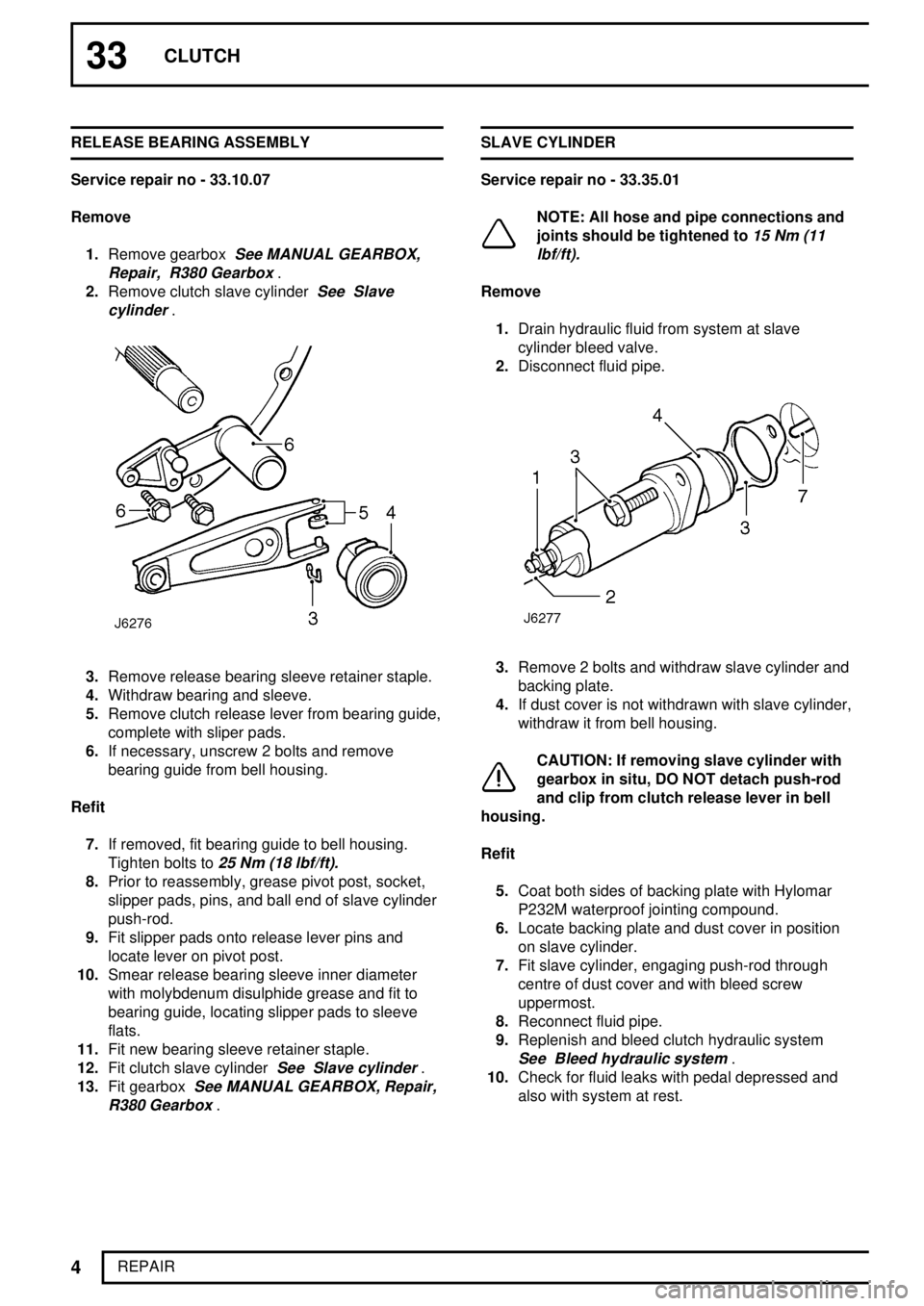
33CLUTCH
4
REPAIR RELEASE BEARING ASSEMBLY
Service repair no - 33.10.07
Remove
1.Remove gearbox
See MANUAL GEARBOX,
Repair, R380 Gearbox
.
2.Remove clutch slave cylinder
See Slave
cylinder
.
3.Remove release bearing sleeve retainer staple.
4.Withdraw bearing and sleeve.
5.Remove clutch release lever from bearing guide,
complete with sliper pads.
6.If necessary, unscrew 2 bolts and remove
bearing guide from bell housing.
Refit
7.If removed, fit bearing guide to bell housing.
Tighten bolts to
25 Nm (18 lbf/ft).
8.Prior to reassembly, grease pivot post, socket,
slipper pads, pins, and ball end of slave cylinder
push-rod.
9.Fit slipper pads onto release lever pins and
locate lever on pivot post.
10.Smear release bearing sleeve inner diameter
with molybdenum disulphide grease and fit to
bearing guide, locating slipper pads to sleeve
flats.
11.Fit new bearing sleeve retainer staple.
12.Fit clutch slave cylinder
See Slave cylinder.
13.Fit gearbox
See MANUAL GEARBOX, Repair,
R380 Gearbox
.SLAVE CYLINDER
Service repair no - 33.35.01
NOTE: All hose and pipe connections and
joints should be tightened to
15 Nm (11
lbf/ft).
Remove
1.Drain hydraulic fluid from system at slave
cylinder bleed valve.
2.Disconnect fluid pipe.
3.Remove 2 bolts and withdraw slave cylinder and
backing plate.
4.If dust cover is not withdrawn with slave cylinder,
withdraw it from bell housing.
CAUTION: If removing slave cylinder with
gearbox in situ, DO NOT detach push-rod
and clip from clutch release lever in bell
housing.
Refit
5.Coat both sides of backing plate with Hylomar
P232M waterproof jointing compound.
6.Locate backing plate and dust cover in position
on slave cylinder.
7.Fit slave cylinder, engaging push-rod through
centre of dust cover and with bleed screw
uppermost.
8.Reconnect fluid pipe.
9.Replenish and bleed clutch hydraulic system
See Bleed hydraulic system.
10.Check for fluid leaks with pedal depressed and
also with system at rest.