Page 149 of 455
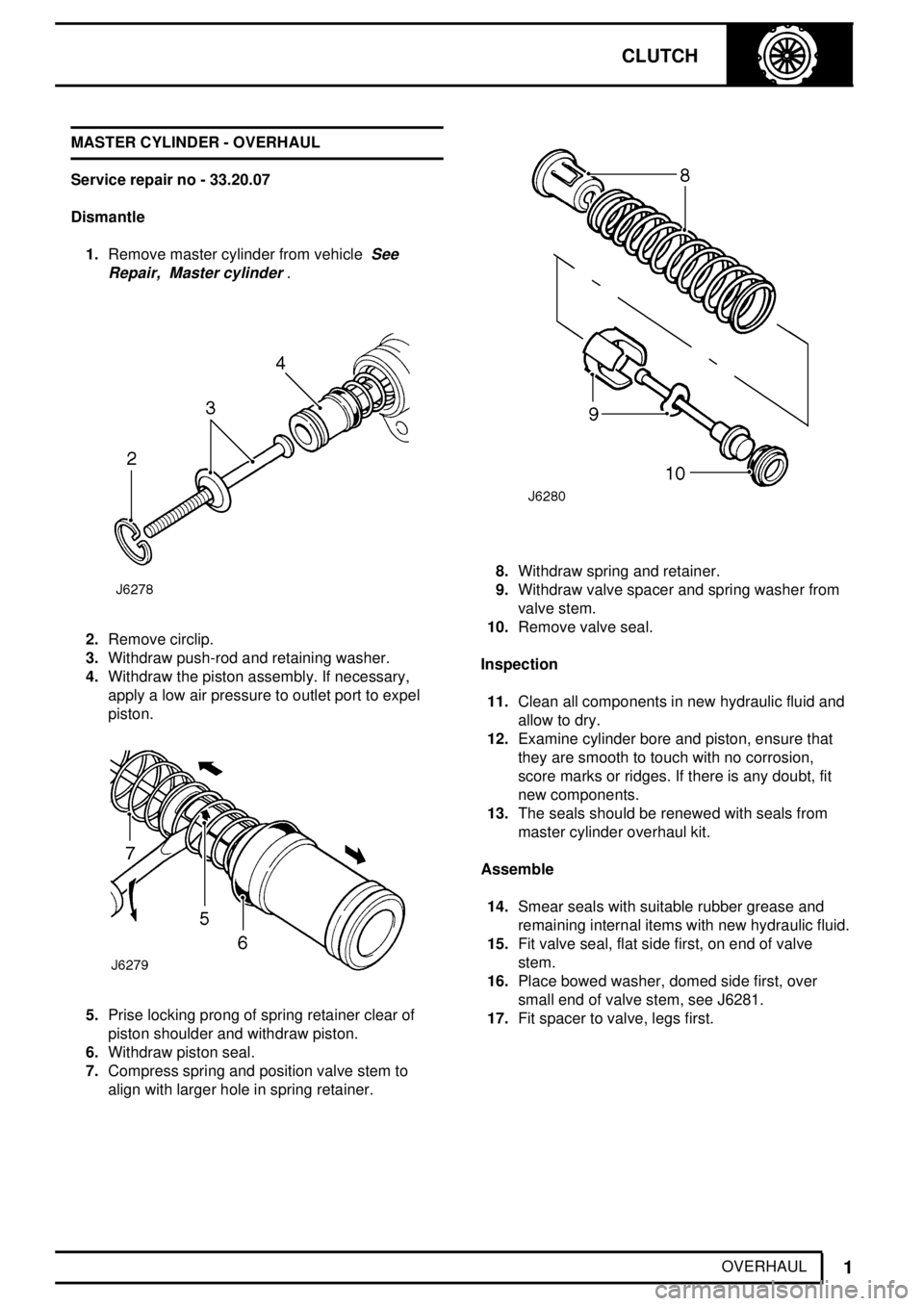
CLUTCH
1
OVERHAUL MASTER CYLINDER - OVERHAUL
Service repair no - 33.20.07
Dismantle
1.Remove master cylinder from vehicle
See
Repair, Master cylinder
.
2.Remove circlip.
3.Withdraw push-rod and retaining washer.
4.Withdraw the piston assembly. If necessary,
apply a low air pressure to outlet port to expel
piston.
5.Prise locking prong of spring retainer clear of
piston shoulder and withdraw piston.
6.Withdraw piston seal.
7.Compress spring and position valve stem to
align with larger hole in spring retainer.
8.Withdraw spring and retainer.
9.Withdraw valve spacer and spring washer from
valve stem.
10.Remove valve seal.
Inspection
11.Clean all components in new hydraulic fluid and
allow to dry.
12.Examine cylinder bore and piston, ensure that
they are smooth to touch with no corrosion,
score marks or ridges. If there is any doubt, fit
new components.
13.The seals should be renewed with seals from
master cylinder overhaul kit.
Assemble
14.Smear seals with suitable rubber grease and
remaining internal items with new hydraulic fluid.
15.Fit valve seal, flat side first, on end of valve
stem.
16.Place bowed washer, domed side first, over
small end of valve stem, see J6281.
17.Fit spacer to valve, legs first.
Page 150 of 455
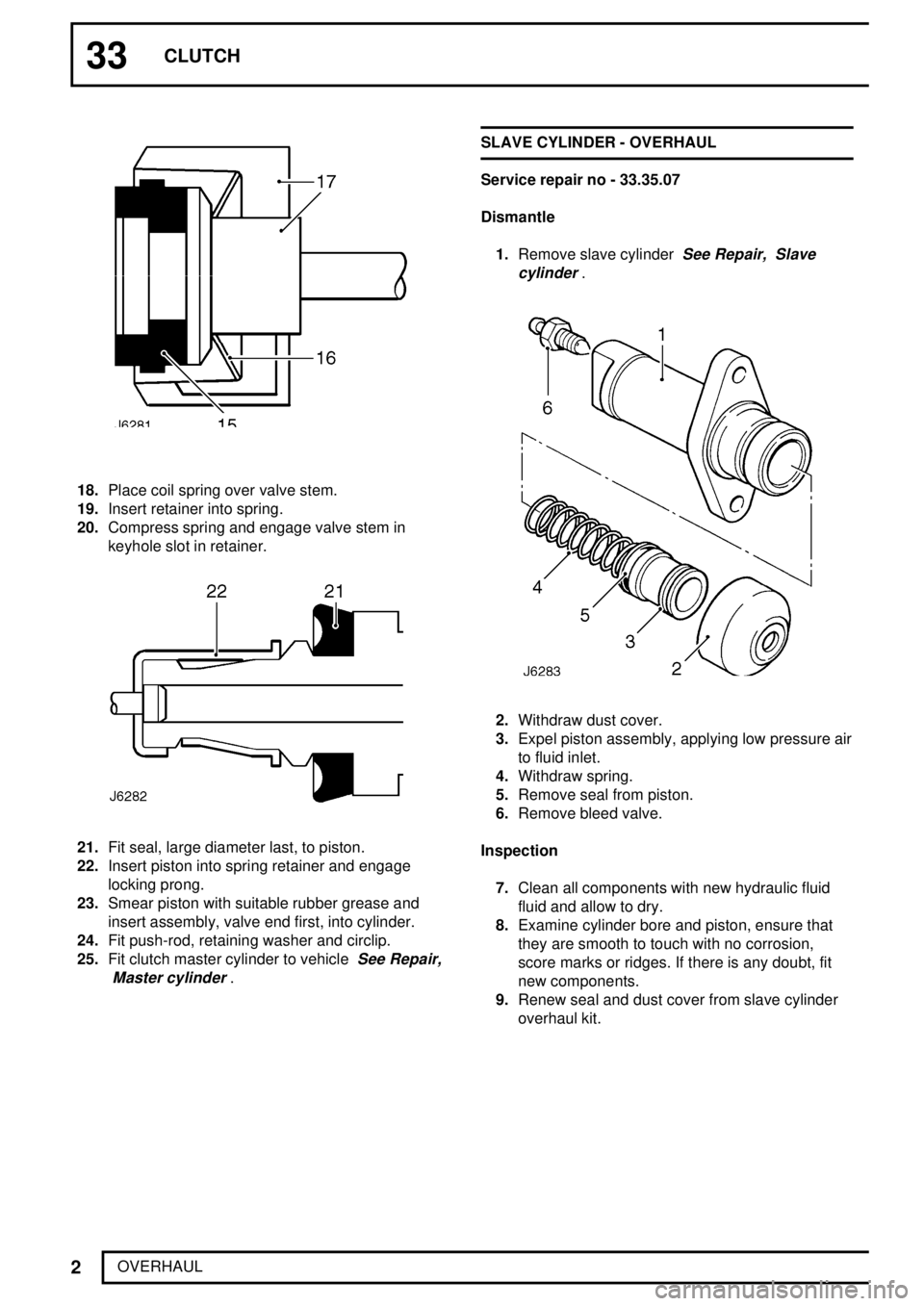
33CLUTCH
2
OVERHAUL
18.Place coil spring over valve stem.
19.Insert retainer into spring.
20.Compress spring and engage valve stem in
keyhole slot in retainer.
21.Fit seal, large diameter last, to piston.
22.Insert piston into spring retainer and engage
locking prong.
23.Smear piston with suitable rubber grease and
insert assembly, valve end first, into cylinder.
24.Fit push-rod, retaining washer and circlip.
25.Fit clutch master cylinder to vehicle
See Repair,
Master cylinder
.SLAVE CYLINDER - OVERHAUL
Service repair no - 33.35.07
Dismantle
1.Remove slave cylinder
See Repair, Slave
cylinder
.
2.Withdraw dust cover.
3.Expel piston assembly, applying low pressure air
to fluid inlet.
4.Withdraw spring.
5.Remove seal from piston.
6.Remove bleed valve.
Inspection
7.Clean all components with new hydraulic fluid
fluid and allow to dry.
8.Examine cylinder bore and piston, ensure that
they are smooth to touch with no corrosion,
score marks or ridges. If there is any doubt, fit
new components.
9.Renew seal and dust cover from slave cylinder
overhaul kit.
Page 155 of 455
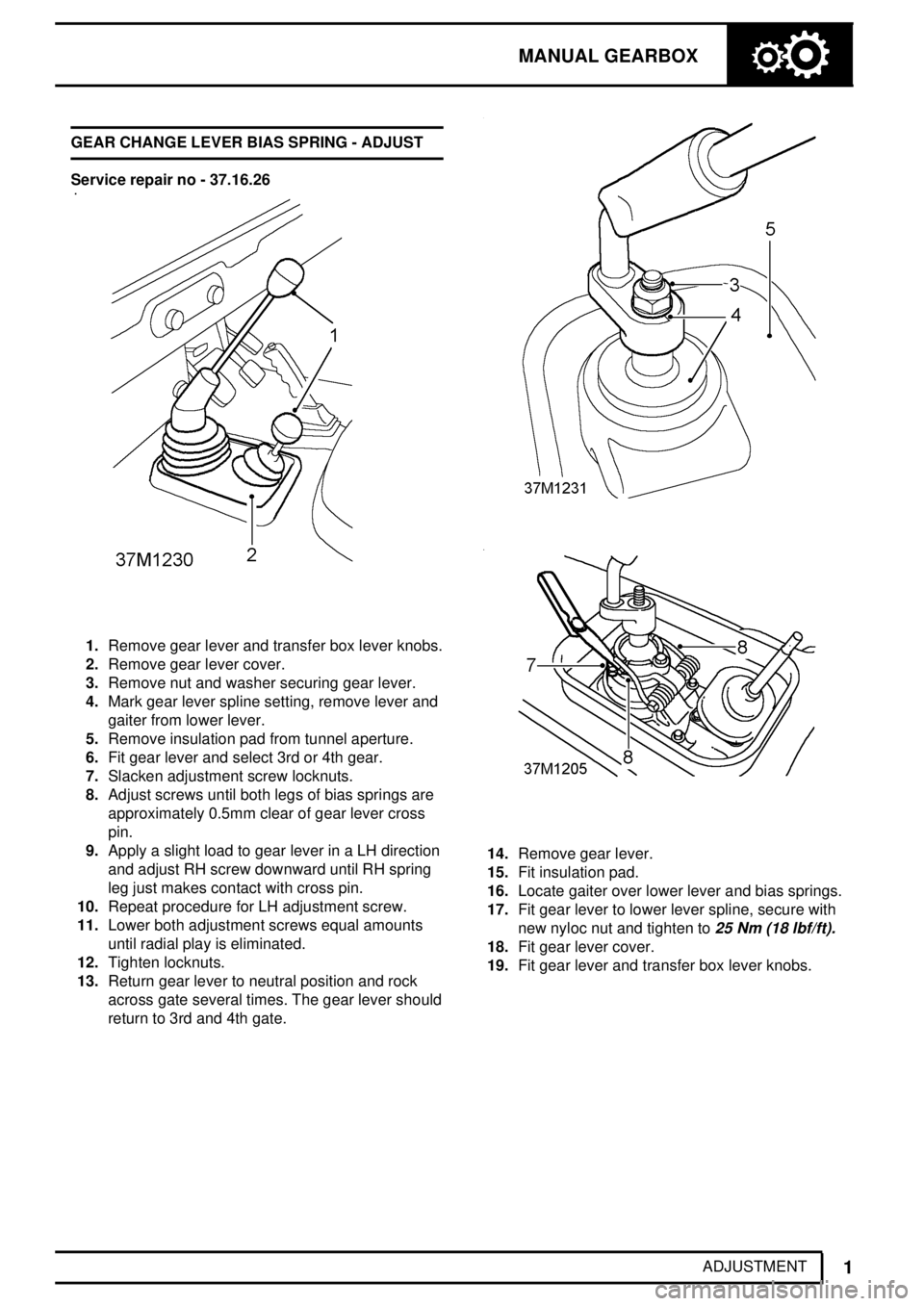
MANUAL GEARBOX
1
ADJUSTMENT GEAR CHANGE LEVER BIAS SPRING - ADJUST
Service repair no - 37.16.26
1.Remove gear lever and transfer box lever knobs.
2.Remove gear lever cover.
3.Remove nut and washer securing gear lever.
4.Mark gear lever spline setting, remove lever and
gaiter from lower lever.
5.Remove insulation pad from tunnel aperture.
6.Fit gear lever and select 3rd or 4th gear.
7.Slacken adjustment screw locknuts.
8.Adjust screws until both legs of bias springs are
approximately 0.5mm clear of gear lever cross
pin.
9.Apply a slight load to gear lever in a LH direction
and adjust RH screw downward until RH spring
leg just makes contact with cross pin.
10.Repeat procedure for LH adjustment screw.
11.Lower both adjustment screws equal amounts
until radial play is eliminated.
12.Tighten locknuts.
13.Return gear lever to neutral position and rock
across gate several times. The gear lever should
return to 3rd and 4th gate.
14.Remove gear lever.
15.Fit insulation pad.
16.Locate gaiter over lower lever and bias springs.
17.Fit gear lever to lower lever spline, secure with
new nyloc nut and tighten to
25 Nm (18 lbf/ft).
18.Fit gear lever cover.
19.Fit gear lever and transfer box lever knobs.
Page 156 of 455
37MANUAL GEARBOX
2
ADJUSTMENT FIFTH GEAR STOP SCREW - ADJUST
Service repair no - 37.16.67
1.Remove gear lever and transfer box lever knobs.
2.Remove gear lever cover.
3.Remove nut and washer securing gear lever.
4.Mark gear lever spline setting, remove lever and
gaiter from lower lever.
5.Remove insulation pad from tunnel aperture.
6.Remove tunnel carpet.
7.Remove retaining screws and release fuse box
cover.
8.Remove 2 screws and release fuse box from
bulkhead to assist next operation.
9.Remove 16 screws securing tunnel cover to
vehicle body.
10.Manouvre tunnel cover to clear handbrake lever
and remove from vehicle.
11.Fit gear lever and knob and select reverse gear.
Page 158 of 455
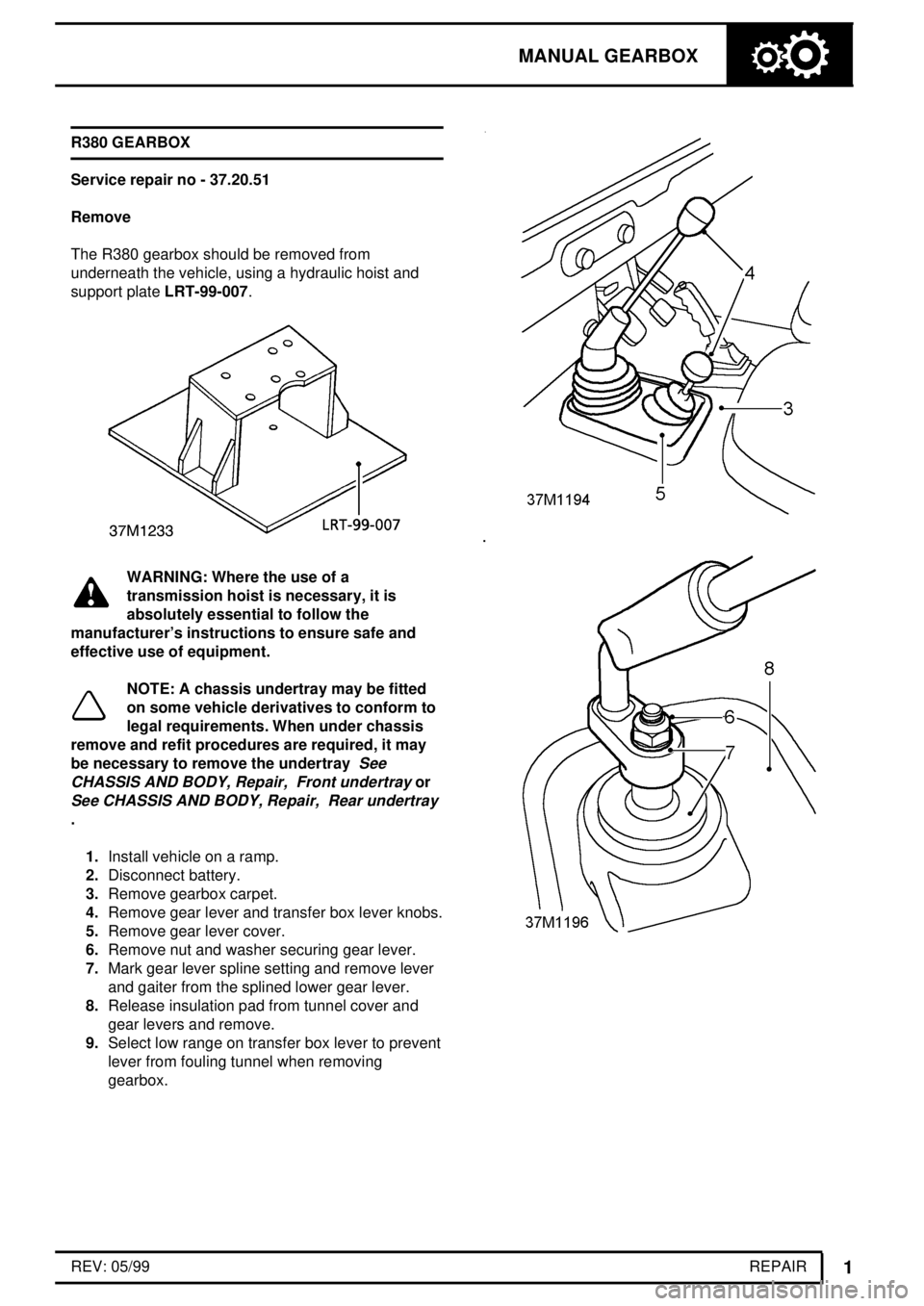
MANUAL GEARBOX
1
REPAIR REV: 05/99 R380 GEARBOX
Service repair no - 37.20.51
Remove
The R380 gearbox should be removed from
underneath the vehicle, using a hydraulic hoist and
support plateLRT-99-007.
WARNING: Where the use of a
transmission hoist is necessary, it is
absolutely essential to follow the
manufacturer's instructions to ensure safe and
effective use of equipment.
NOTE: A chassis undertray may be fitted
on some vehicle derivatives to conform to
legal requirements. When under chassis
remove and refit procedures are required, it may
be necessary to remove the undertray
See
CHASSIS AND BODY, Repair, Front undertray
or
See CHASSIS AND BODY, Repair, Rear undertray
.
1.Install vehicle on a ramp.
2.Disconnect battery.
3.Remove gearbox carpet.
4.Remove gear lever and transfer box lever knobs.
5.Remove gear lever cover.
6.Remove nut and washer securing gear lever.
7.Mark gear lever spline setting and remove lever
and gaiter from the splined lower gear lever.
8.Release insulation pad from tunnel cover and
gear levers and remove.
9.Select low range on transfer box lever to prevent
lever from fouling tunnel when removing
gearbox.
Page 168 of 455
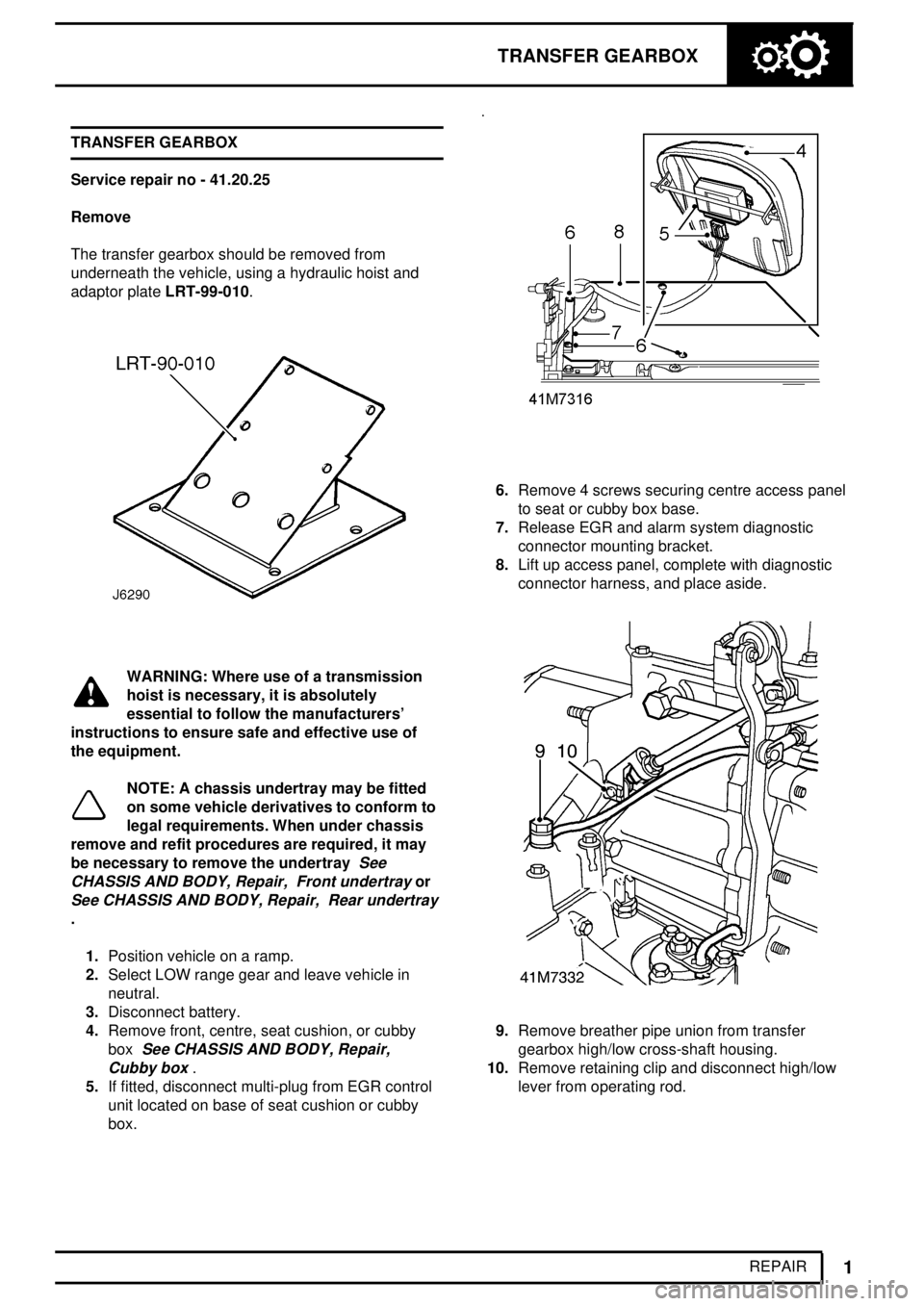
TRANSFER GEARBOX
1
REPAIR TRANSFER GEARBOX
Service repair no - 41.20.25
Remove
The transfer gearbox should be removed from
underneath the vehicle, using a hydraulic hoist and
adaptor plateLRT-99-010.
WARNING: Where use of a transmission
hoist is necessary, it is absolutely
essential to follow the manufacturers'
instructions to ensure safe and effective use of
the equipment.
NOTE: A chassis undertray may be fitted
on some vehicle derivatives to conform to
legal requirements. When under chassis
remove and refit procedures are required, it may
be necessary to remove the undertray
See
CHASSIS AND BODY, Repair, Front undertray
or
See CHASSIS AND BODY, Repair, Rear undertray
.
1.Position vehicle on a ramp.
2.Select LOW range gear and leave vehicle in
neutral.
3.Disconnect battery.
4.Remove front, centre, seat cushion, or cubby
box
See CHASSIS AND BODY, Repair,
Cubby box
.
5.If fitted, disconnect multi-plug from EGR control
unit located on base of seat cushion or cubby
box.
6.Remove 4 screws securing centre access panel
to seat or cubby box base.
7.Release EGR and alarm system diagnostic
connector mounting bracket.
8.Lift up access panel, complete with diagnostic
connector harness, and place aside.
9.Remove breather pipe union from transfer
gearbox high/low cross-shaft housing.
10.Remove retaining clip and disconnect high/low
lever from operating rod.
Page 176 of 455
PROPELLER SHAFTS
1
REPAIR REV: 05/99 PROPELLER SHAFT
Service repair no - 47.15.02 - Front
Service repair no - 47.15.03 - Rear
Remove
1.Place vehicle on ramp.
2.Mark drive flanges at each end of propeller shaft
for reassembly.
3.Remove 4 bolts/nuts from each end and remove
propeller shaft.
NOTE: A chassis under tray may be fitted
on some vehicle derivatives to conform to
legal requirements. When under chassis
remove and refit procedures are required, it may
be necessary to remove the under tray
See
CHASSIS AND BODY, Repair, Front under tray
or
See CHASSIS AND BODY, Repair, Rear under
tray.
Refit
4.Fit propeller shafts to vehicle with sliding joints to
transfer box and tighten nuts to
47 Nm (35
lbf/ft).
Page 178 of 455
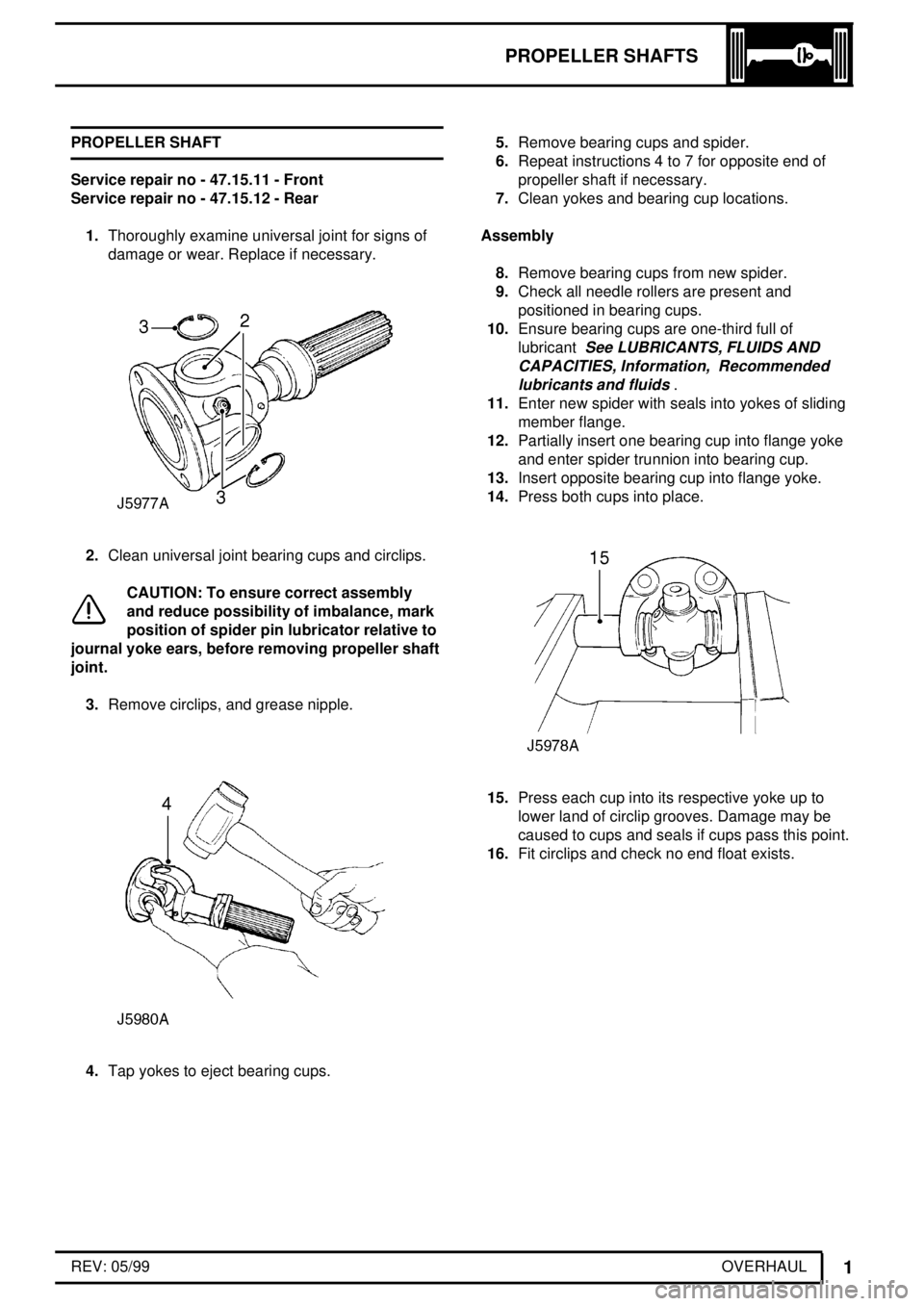
PROPELLER SHAFTS
1
OVERHAUL REV: 05/99 PROPELLER SHAFT
Service repair no - 47.15.11 - Front
Service repair no - 47.15.12 - Rear
1.Thoroughly examine universal joint for signs of
damage or wear. Replace if necessary.
2.Clean universal joint bearing cups and circlips.
CAUTION: To ensure correct assembly
and reduce possibility of imbalance, mark
position of spider pin lubricator relative to
journal yoke ears, before removing propeller shaft
joint.
3.Remove circlips, and grease nipple.
4.Tap yokes to eject bearing cups.5.Remove bearing cups and spider.
6.Repeat instructions 4 to 7 for opposite end of
propeller shaft if necessary.
7.Clean yokes and bearing cup locations.
Assembly
8.Remove bearing cups from new spider.
9.Check all needle rollers are present and
positioned in bearing cups.
10.Ensure bearing cups are one-third full of
lubricant
See LUBRICANTS, FLUIDS AND
CAPACITIES, Information, Recommended
lubricants and fluids
.
11.Enter new spider with seals into yokes of sliding
member flange.
12.Partially insert one bearing cup into flange yoke
and enter spider trunnion into bearing cup.
13.Insert opposite bearing cup into flange yoke.
14.Press both cups into place.
15.Press each cup into its respective yoke up to
lower land of circlip grooves. Damage may be
caused to cups and seals if cups pass this point.
16.Fit circlips and check no end float exists.