Page 295 of 1708
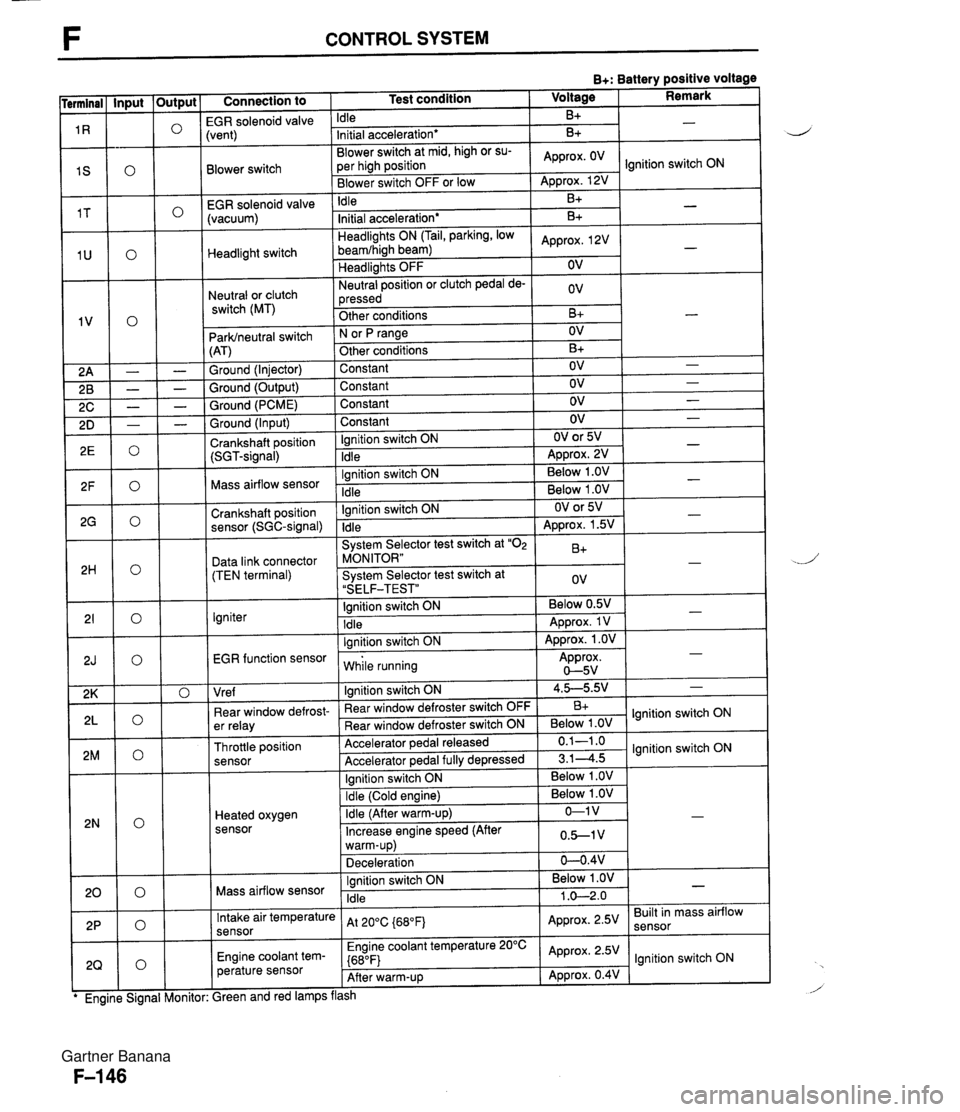
F CONTROL SYSTEM B+: Battery positive voltage Connection to 1 Test condition 1 Voltage I Remark I -- EGR solenoid valvi Idle B+ Blower switch -- EGR solenoid valve (vacuum) :vent) Initial acceleration* Blower switch at mid, high or su- per high position Blower switch OFF or low Headlight switch Neutral or clutch switch (MT) B+ Idle ParWneutral switch (AT) Ground (Injector) Ground (Output) Ground (PCME) Approx. OV - Approx. 12V B+ Headlights ON (Tail, parking, low beamfhigh beam) Headlights OFF Neutral position or clutch pedal de- pressed Other conditions Ground (Input) Crankshaft position (SGT-signal) Ignition switch ON N or fJ range Other conditions Constant Constant Constant -. Mass airflow sensor .. . . EGR function sensor I while running Approx. 0-5v Initial acceleration* Approx, 2V OV ov B+ Constant Ignition switch ON Idle Crankshaft position sensor (SGC-signal) Data link connector (TEN terminal) Igniter I I I Vre f I lanition switch ON 1 4.5-5.9.' 1 - B+ - OV B+ OV OV OV Ignition switch ON Idle - - - OV OV or 5V ADD~OX. 2V - - Ignition switch ON Idle System Selector test switch at "02 MONITOR" System Selector test switch at "SELF-TEST" Ignition switch ON Idle lanition switch ON I . . I I 1 Ignition switch ON I Below 1 .OV I I - - . . Below 1 .OV Below 1 .OV ear window defrost- er relay Throttle position sensor Heated oxygen sensor - OV or 5V Approx. 1.5V B+ ov Below 0.5V Approx. 1 V Approx. 1 .OV - - - " Rear window defroster switch OFF Rear window defroster switch ON Accelerator pedal released Accelerator ~edal fullv de~ressed Mass airflow sensor B+ Below 1 .OV 0.1-1 .o 3.14.5 Intake air temperature sensor Engine coolant tem- perature sensor lgnition switch ON lgnition switch ON Ignition switch ON Idle ireen and red lamps flash At 200C {680Fj Engine coolant temperature 20°C {680F) After warm-up Below 1 .OV 1 .O-2.0 - Approx. 2.5V Approx. 2.5V Approx. 0.4V Built in mass airflow lgnition switch ON Gartner Banana
Page 296 of 1708
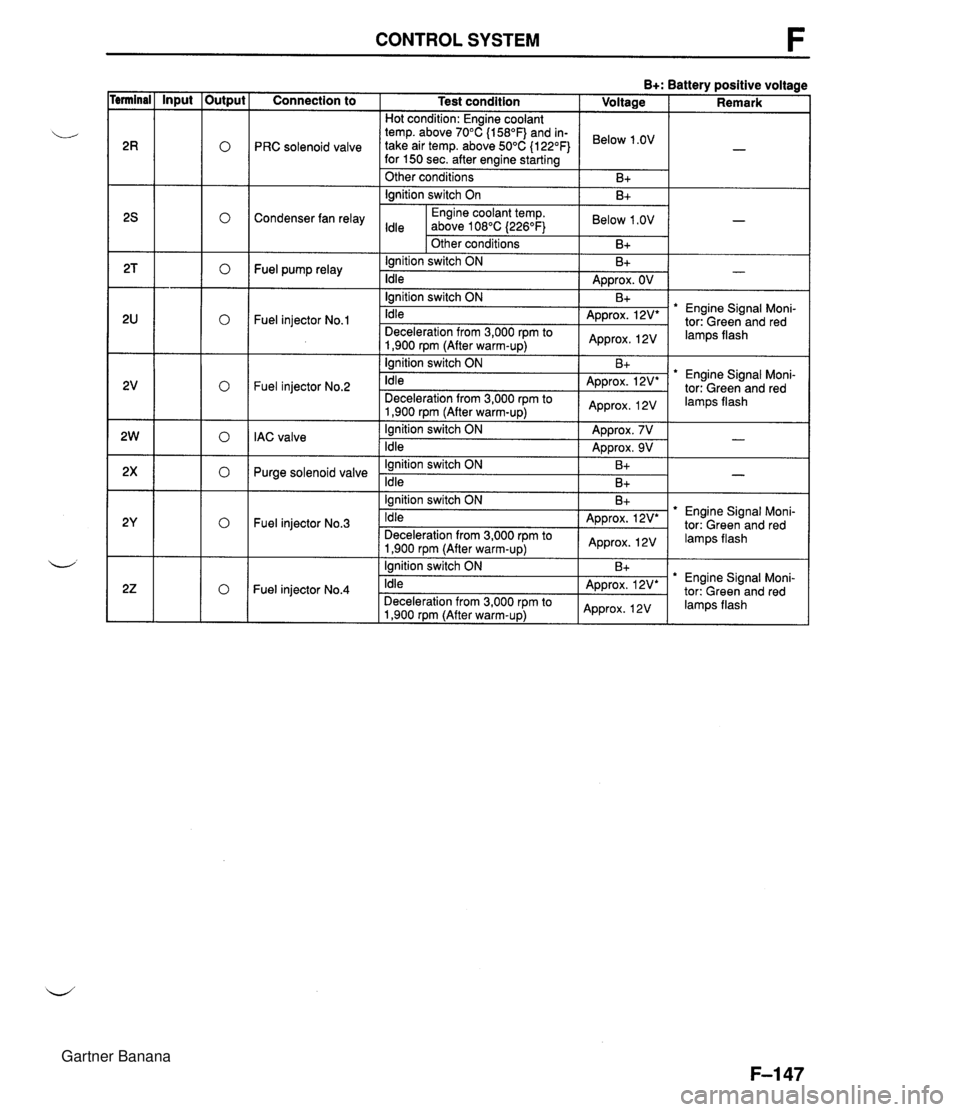
CONTROL SYSTEM F Connection to I Test condition I Hot condition: Enaine coolant Input - temp. above 70°C (1 58"~) and in- PRC solenoid valve take air temp. above 50°C (122°F) for 150 sec. after enaine startina Output 0 0 0 0 0 0 0 0 0 " " Other conditions lanition switch On - Condenser fan relay Engine coolant temp. Idle above 108°C 1226°F) I I Other conditions ' I lgnition switch ON Fuel pump relay ldle I I lanition switch ON Fuel injector No.1 1,900 rpm (After warm-UD) I lgnition switch ON Fuel injector No.2 ldle Deceleration from 3,000 rprn to 1,900 rpm (After warm-up) lgnition switch ON IAC valve ldle lgnition switch ON Purge solenoid valve ldle Fuel injector No.3 lgnition switch ON ldle Deceleration from 3,000 rpm to 1,900 rpm (After warm-up) lanition switch ON Fuel injector No.4 Idle Deceleration from 3,000 rpm to 1,900 rpm (After warm-up) Below 1 .OV -1 Below 1 .OV B+ - Approx. OV Engine Signal Moni- * Engine Signal Moni- tor: Green and red Approx. 12V I lamps flash B+: Battery positive voltage Voltage I Remark * Engine Signal Moni- tor: Green and red Engine Signal Moni- Gartner Banana
Page 300 of 1708
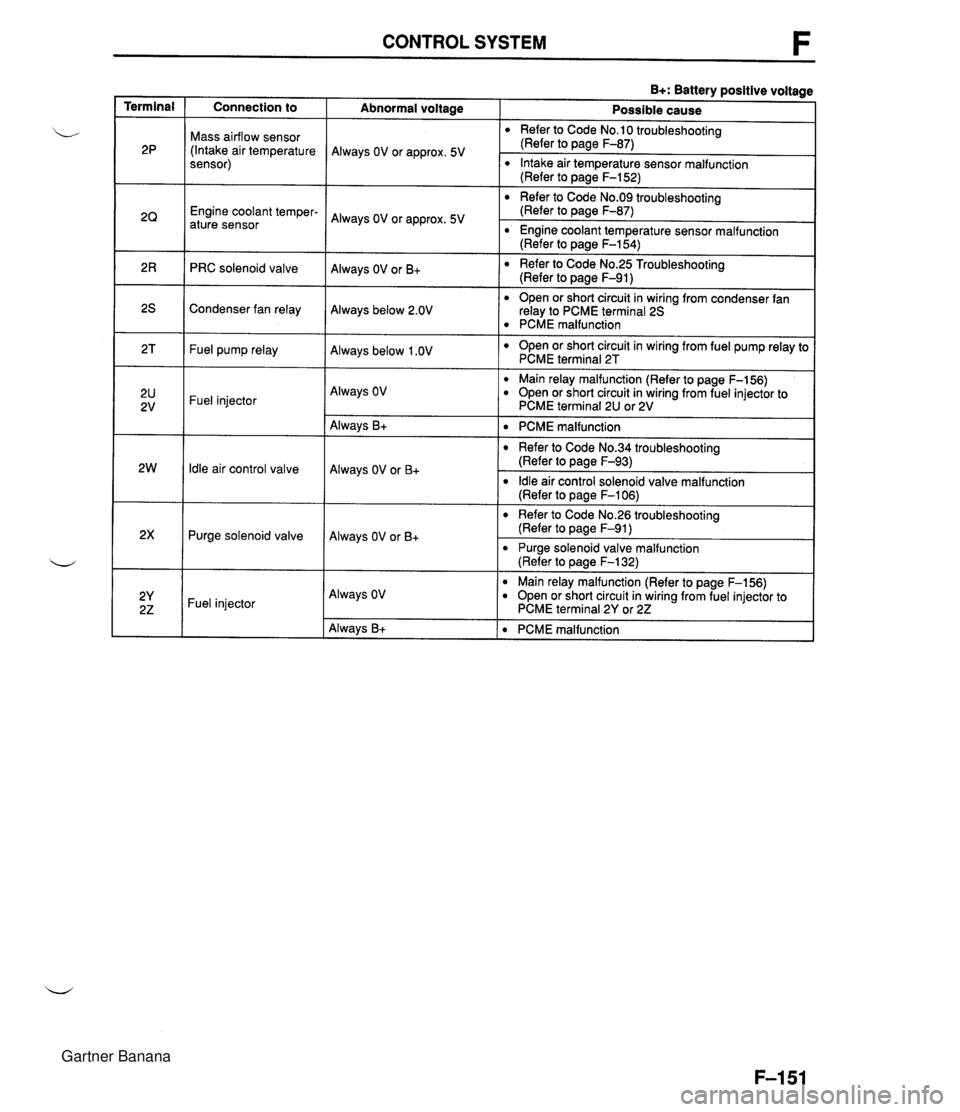
CONTROL SYSTEM B+: Battery positive voltage Terminal Connection to Abnormal voltaae Possible cause Mass airflow sensor (Intake air temperature sensor) Refer to Code No.10 troubleshooting (Refer to page F-87) Always OV or approx. 5V Intake air temperature sensor malfunction (Refer to page F-152) Refer to Code No.09 troubleshooting (Refer to page F-87) Engine coolant temper- ature sensor Always OV or approx. 5V r Engine coolant temperature sensor malfunction (Refer to page F-154) Refer to Code No.25 Troubleshooting (Refer to page F-91) Always OV or B+ PRC solenoid valve r Open or short circuit in wiring from condenser fan relay to PCME terminal 25 PCME malfunction Open or short circuit in wiring from fuel pump relay to PCME terminal 2T Condenser fan relay Always below 2.OV Fuel pump relay Always below 1 .OV Main relay malfunction (Refer to page F-156) r Open or short circuit in wiring from fuel injector to PCME terminal 2U or 2V Always OV Fuel injector ldle air control valve Purge solenoid valve Always B+ Always OV or B+ Always OV or B+ PCME malfunction r Refer to Code No.34 troubleshooting (Refer to page F-93) ldle air control solenoid valve malfunction (Refer to page F-I 06) r Refer to Code No.26 troubleshooting (Refer to page F-91) r Purge solenoid valve malfunction (Refer to pane F-132) -- Fuel injector Always OV Main relay malfunction (Refer to page F-156) Open or short circuit in wiring from fuel injector to PCME terminal 2Y or 22 Always B+ PCME malfunction Gartner Banana
Page 301 of 1708
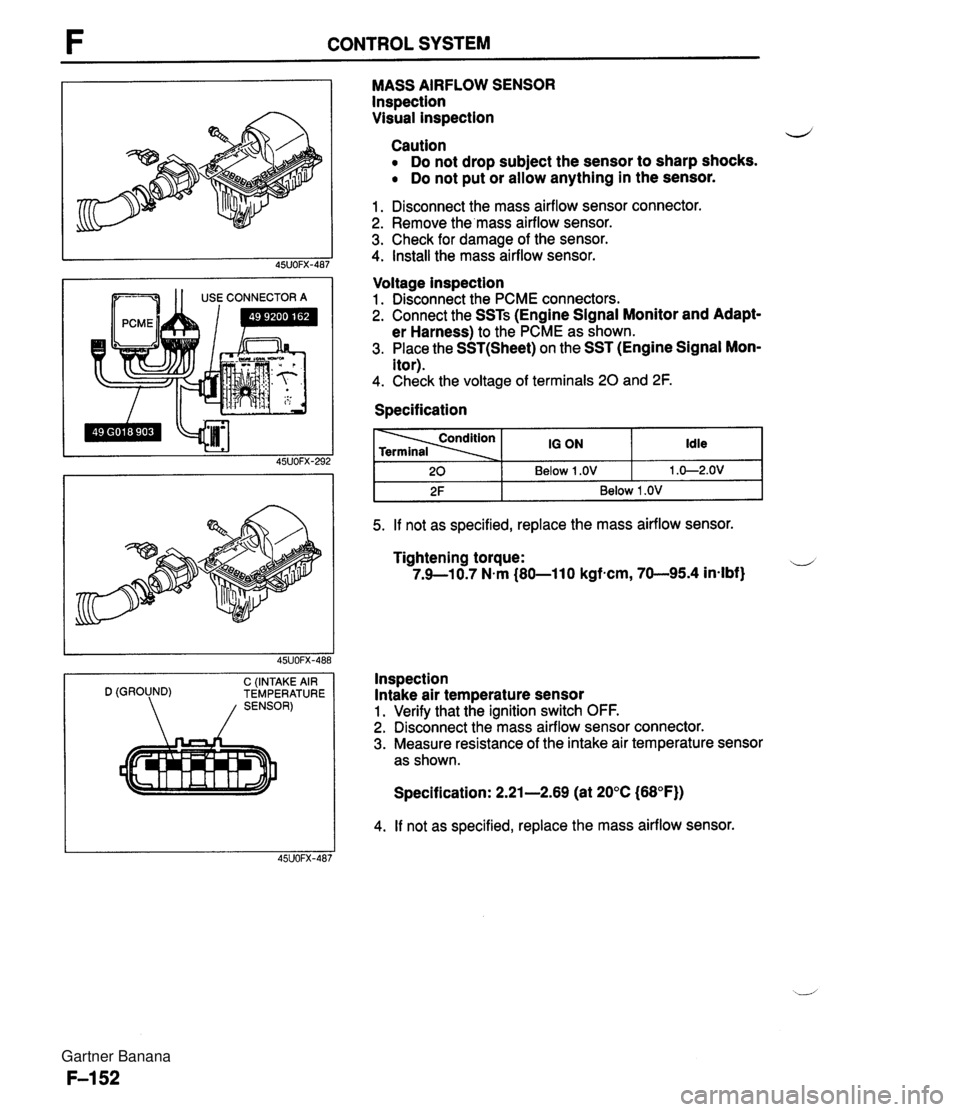
CONTROL SYSTEM --- 1 1 USE CONNECTOR A C (INTAKE AIR D (GROUND) TEMPERATURE MASS AIRFLOW SENSOR lnspection Visual inspection d Caution Do not drop subject the sensor to sharp shocks. Do not put or allow anything in the sensor. 1. Disconnect the mass airflow sensor connector. 2. Remove the'mass airflow sensor. 3. Check for damage of the sensor. 4. Install the mass airflow sensor. Voltage inspection 1. Disconnect the PCME connectors. 2. Connect the SSTs (Engine Signal Monitor and Adapt- er Harness) to the PCME as shown. 3. Place the SST(Sheet) on the SST (Engine Signal Mon- itor). 4. Check the voltage of terminals 20 and 2F. Specification I 2F I Below 1 .OV I 5. If not as specified, replace the mass airflow sensor. Idle 1 .O-2.OV 20 Tightening torque: u 7.9--10.7 N.m (80-11 0 kgfncm, 70-95.4 in-lbf} 10 ON Below 1 .OV Inspection Intake air temperature sensor 1. Verify that the ignition switch OFF. 2. Disconnect the mass airflow sensor connector. 3. Measure resistance of the intake air temperature sensor as shown. Specification: 2.21-2.69 (at 20°C (68°F)) 4. If not as specified, replace the mass airflow sensor. Gartner Banana
Page 302 of 1708
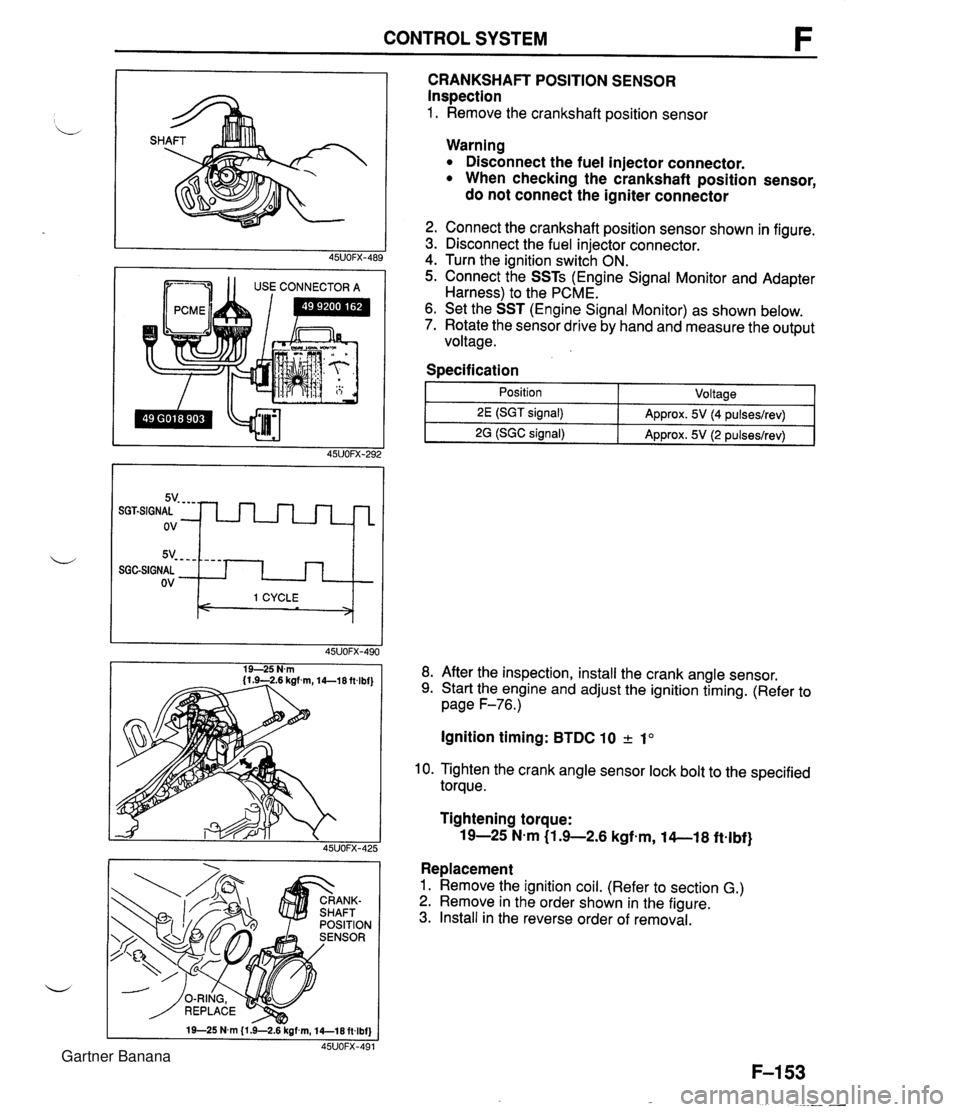
CONTROL SYSTEM 1 1 USE CONNECTOR A CRANKSHAFT POSITION SENSOR Inspection 1. Remove the crankshaft position sensor 5v- - - - SGGSIGNAL ov Warning Disconnect the fuel injector connector. When checking the crankshaft position sensor, do not connect the igniter connector - - - - I 1 CYCLE < > 2. Connect the crankshaft position sensor shown in figure. 3. Disconnect the fuel injector connector. 4. Turn the ignition switch ON. 5. Connect the SSTs (Engine Signal Monitor and Adapter Harness) to the PCME. 6. Set the SST (Engine Signal Monitor) as shown below. 7. Rotate the sensor drive by hand and measure the output voltage. Specification I 1 - Position - ~oltaael 8. After the inspection, install the crank angle sensor. 9. Start the engine and adjust the ignition timing. (Refer to page F-76.) 2E (SGT signal) 2G (SGC signal) Ignition timing: BTDC 10 2 1" Approx. 5V (4 pulseslrev) Approx. 5V (2 pulseslrev) 10. Tighten the crank angle sensor lock bolt to the specified torque. Tightening torque: 19-25 N-m (1 .+2.6 kgfem, 14-1 8 ftelbf} Replacement 1. Remove the ignition coil. (Refer to section G.) 2. Remove in the order shown in the figure. 3. Install in the reverse order of removal. Gartner Banana
Page 303 of 1708
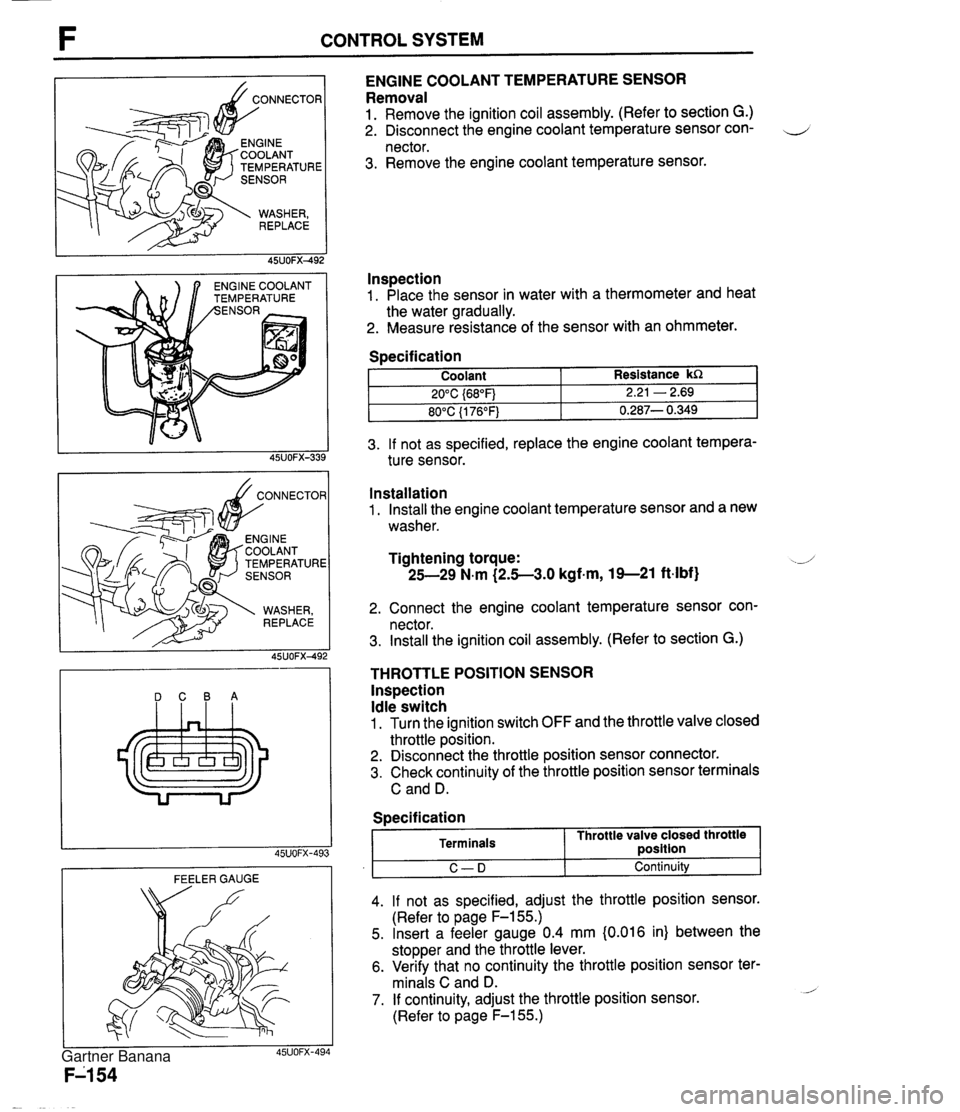
CONTROL SYSTEM TEMPERATURE NGlNE COOLANT EMPERATURE ENGINE COOLANT TEMPERATURE SENSOR Removal 1. Remove the ignition coil assembly. (Refer to section G.) 2. Disconnect the engine coolant temperature sensor con- 4 nector. 3. Remove the engine coolant temperature sensor. lnspection 1. Place the sensor in water with a thermometer and heat the water gradually. 2. Measure resistance of the sensor with an ohmmeter. 3. If not as specified, replace the engine coolant tempera- ture sensor. Specification DCBA Coolant 20°C {68"F) 80°C {I 76°F) FEELER GAUGE Resistance kR 2.21 - 2.69 0.287- 0.349 Installation 1. Install the engine coolant temperature sensor and a new washer. Tightening torque: -J 25-29 N.m (2.5-3.0 kgf-m, 19--21 ft-lbf) 2. Connect the engine coolant temperature sensor con- nector. 3. Install the ignition coil assembly. (Refer to section G.) THROTTLE POSITION SENSOR lnspection Idle switch 1. Turn the ignition switch OFF and the throttle valve closed throttle position. 2. Disconnect the throttle position sensor connector. 3. Check continuity of the throttle position sensor terminals C and D. I C-D I Continuity 4. If not as specified, adjust the throttle position sensor. (Refer to page F-155.) 5. Insert a feeler gauge 0.4 mm {0.016 in) between the stopper and the throttle lever. 6. Verify that no continuity the throttle position sensor ter- minals C and D. - 7. If continuity, adjust the throttle position sensor. (Refer to page F-155.) Specification Terminals Throttle valve closed throttle ~osition Gartner Banana
Page 304 of 1708
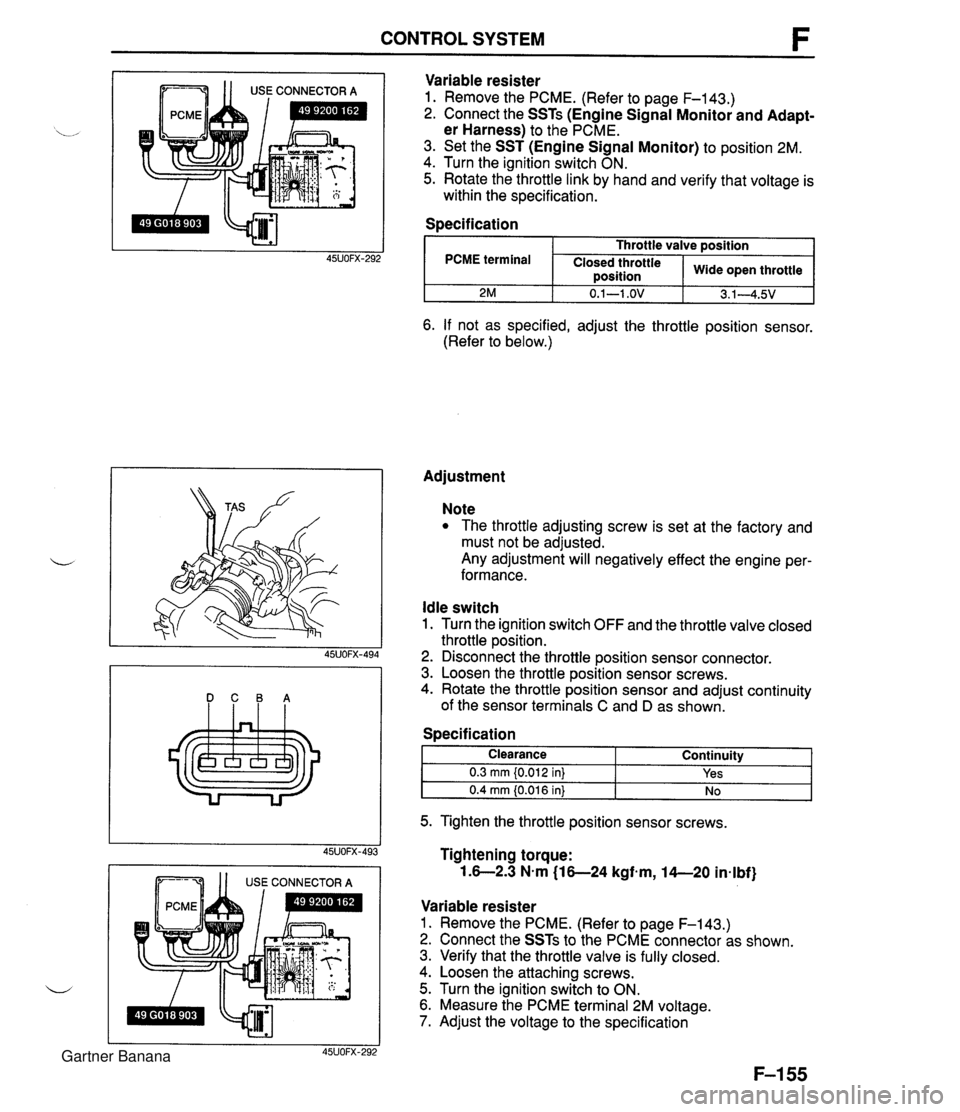
CONTROL SYSTEM DCB IIIf I 1 USECONNECTORA I Variable resister 1. Remove the PCME. (Refer to page F-143.) 2. Connect the SSTs (Engine Signal Monitor and Adapt- er Harness) to the PCME. 3. Set the SST (Engine Signal Monitor) to position 2M. 4. Turn the ignition switch ON. 5. Rotate the throttle link by hand and verify that voltage is within the specification. Specification 6. If not as specified, adjust the throttle position sensor. (Refer to below.) - PCME terminal Adjustment Throttle valve position I Wide open throttle ~osition Note The throttle adjusting screw is set at the factory and must not be adjusted. Any adjustment will negatively effect the engine per- formance. Idle switch 1. Turn the ignition switch OFF and the throttle valve closed throttle position. 2. Disconnect the throttle position sensor connector. 3. Loosen the throttle position sensor screws. 4. Rotate the throttle position sensor and adjust continuity of the sensor terminals C and D as shown. Specification I Clearance Continuity I 5. Tighten the throttle position sensor screws. 0.3 mm (0.012 in} Tightening torque: 1.6-2.3 N.m (16-24 kgf-m, 14--20 in-lbf) Yes Variable resister 1. Remove the PCME. (Refer to page F-143.) 2. Connect the SSTs to the PCME connector as shown. 3. Verify that the throttle valve is fully closed. 4. Loosen the attaching screws. 5. Turn the ignition switch to ON. 6. Measure the PCME terminal 2M voltage. 7. Adjust the voltage to the specification 0.4 mm (0.01 6 in) I No Gartner Banana
Page 305 of 1708
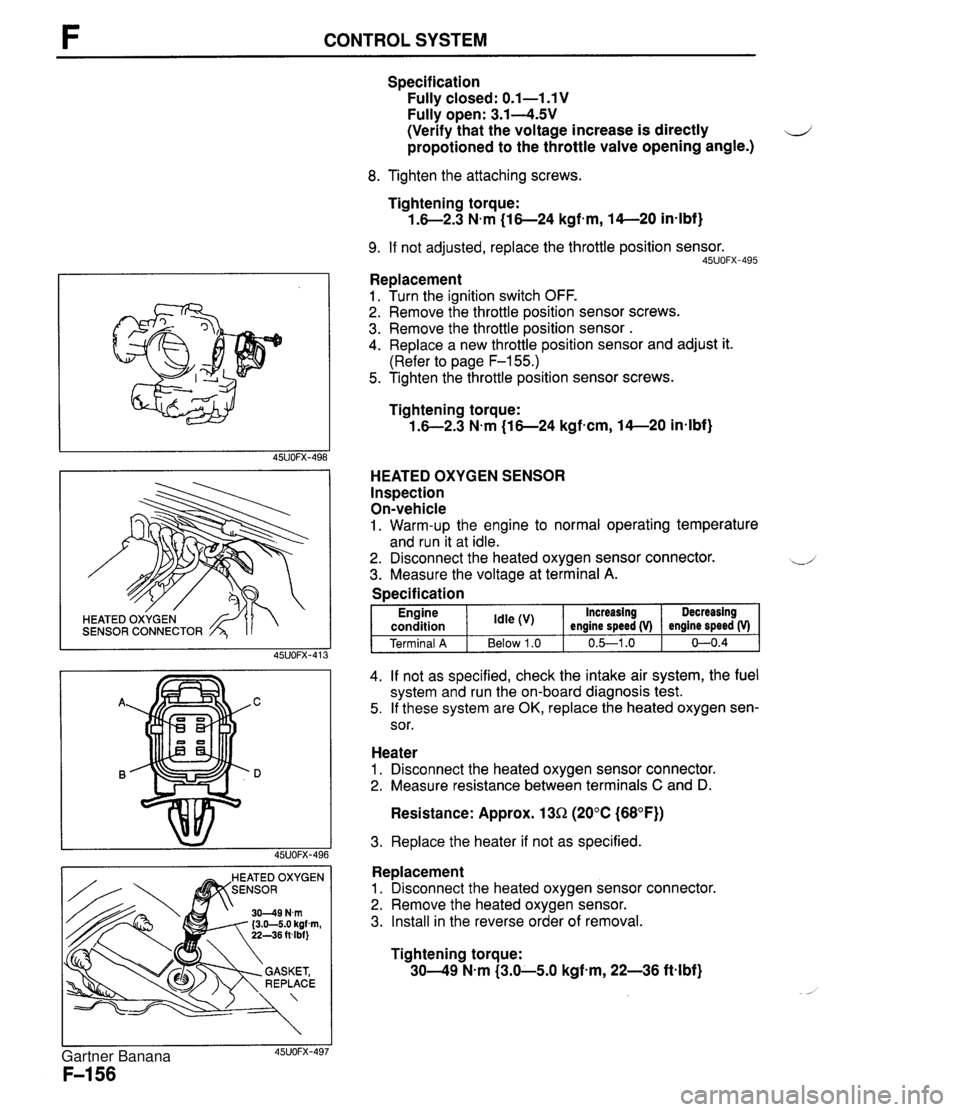
CONTROL SYSTEM SENSOR CONNECTOR EATED OXYGEN Specification Fully closed: 0.1-1.1 V Fully open: 3.14.5V (Verify that the voltage increase is directly d propotioned to the throttle valve opening angle.) 8. Tighten the attaching screws. Tightening torque: 1.6-2.3 N.m (16-24 kgfmm, 14-20 in-lbf} 9. If not adjusted, replace the throttle position sensor. 45UOFX-495 Replacement 1. Turn the ignition switch OFF. 2. Remove the throttle position sensor screws. 3. Remove the throttle position sensor . 4. Replace a new throttle position sensor and adjust it. (Refer to page F-155.) 5. Tighten the throttle position sensor screws. Tightening torque: 1.6-2.3 N.m (16-24 kgf-cm, 14-20 in-lbf} HEATED OXYGEN SENSOR Inspection On-vehicle 1. Warm-up the engine to normal operating temperature and run it at idle. 2. Disconnect the heated oxygen sensor connector. -.-' 3. Measure the voltage at terminal A. 4. If not as specified, check the intake air system, the fuel system and run the on-board diagnosis test. 5. If these system are OK, replace the heated oxygen sen- sor. Specification Heater 1. Disconnect the heated oxygen sensor connector. 2. Measure resistance between terminals C and D. Resistance: Approx. 13R (20°C (68°F)) Engine condition Terminal A 3. Replace the heater if not as specified. Increasing engine speed (V) 0.&1 .O Idle Below 1.0 Replacement 1. Disconnect the heated oxygen sensor connector. 2. Remove the heated oxygen sensor. 3. Install in the reverse order of removal. Decreasing engine speed (V) 0-0.4 Tightening torque: 3049 N-m (3.0-5.0 kgf-m, 22-36 ftlbf) Gartner Banana