Page 161 of 677
F2 lNTAKE AlR SYSTEM
I. Air cleaner
2. Air cleaner element
Inspect fur dirt, damage, or oil
3. Airflow meter
4. Air hose
5. Air pipe and air hose
6. Accelerator cable 7. Throttle body
8. ISC valve
9. Air valve
IO. Dynamic chamber
I 1. Intake manifold
Installation Note . . . . . . . . ..__..........._._..._._.. below
93GOF2-751
93GOF2-75:
F2-44
installation Note
Intake manifold 1. Tighten the bolts in steps in the order shown in the figure.
Tightening torque:
19-25 Nm (1.9-2.6 m-kg, 140-f9 ft-lb)
Page 162 of 677
TURBOCHARGER CONTROL SYSTEM F2
TURBOCHARGER CONTROL SYSTEM
PREPARATION
SST
49 HO80 740
Gauge. pressure
I 93GOF2-754
93GOF2-755
L I 93GOF2-756
93GOF2-757 93GOF2-753
SYSTEM OPERATION
1. Install a pressure gauge 149 kPa (0.5 kg/cm2, 7.1 psi)
min.1.
2. Connect a tachometer to the diagnosis connector lG-
terminal.
3. Start the engine.
4. Verify that the boost pressure when the engine speed is
4,000 rpm is within specification.
Specification: More than 2.0 kPa ( 0.02 kg/cm2, 0.3 psi)
5. If not within the specification, check for air Ieakage, exhaust
gas leakage, and for the wastegate stuck open.
6. if OK, replace the turbocharger.
WASTEGATE
Inspection
1. Remove the air hose from the wastegate actuator.
2 Connect the SST to the actuator.
3. Raise the front of the vehicle and support it on safety stands.
4. Remove the undercover.
F2-45
Page 163 of 677
F2 TURBOCHARGER CONTROL SYSTEM
I 93GOF2-756
93GOF2-75!
93GOF2-761
5. Mark the actuator rod.
Caution
l Do not apply compressed air over 98 kPa (1.0
kg/cm2, 14 psi).
6. Adjust the compressed air pressure to 83 kPa (0.85
kg/cm”, 12 psi).
7. Verify that the rod moves when applying and releasing air
pressure.
WASTEGATE SOLENOID VALVE
Inspection
1, Remove the ,solenoid valve.
2. Verify that air does nut flow from @ through @
3. Apply IN to the solenoid valve and verify that air flows from
@ through @
TURBUCHARGEFI
Inspection
1. Be sure tf7e engine is cool.
2. Remove the air hose.
3. Check that the compressor wheel assembly turns smoothly.
4. If there is excessive drag or noise, replace the turbocharger.
93GOF2-761
FZ-46
Page 164 of 677
TURSUCHARGER CONTROL SYSTEM F2
Removal I InstaIlation
Caution
l Be carefui of following points after turbocharger removal.
l Do not carry the turbocharger by the actuator rod or actuator hose.
l Do not drop the turbocharger.
l Set the turbocharger down with the turbine shaft horizontal.
9 Cover the intake, exhaust, and oil passages to prevent dirt or other materia1 from entering.
l Use the specified new studs when installing the turbocharger.
1. Disconnect the negative battery cable.
2. Lift up the vehicle.
3.
Remove the undercover.
4. Drain
the engine coolant.
5. Remove in
the order shown in the figure.
6. fnstall in the reverse order of removat, referring to Installation Note.
7.8-l 1 N-m (80-l 10 cm-kg, 69-95 in-lb)
G I’
/
43-61 (4.4-6.2, 3245)
36-42 (3.94.3, 28-
7.8-1 1 N-m (80-110 cm-kg, 6
cm-kg, 69-95
indb)
26-31
12.7~g-2. 20-231
w
19-26 (l-9-2.6, 14-19)
7.6-17 N-m (80-7 t d cm-kg, 69-95 in-lb)
N-m (m-kg, Mb]
I 93GOF2-762
F2-47
Page 165 of 677
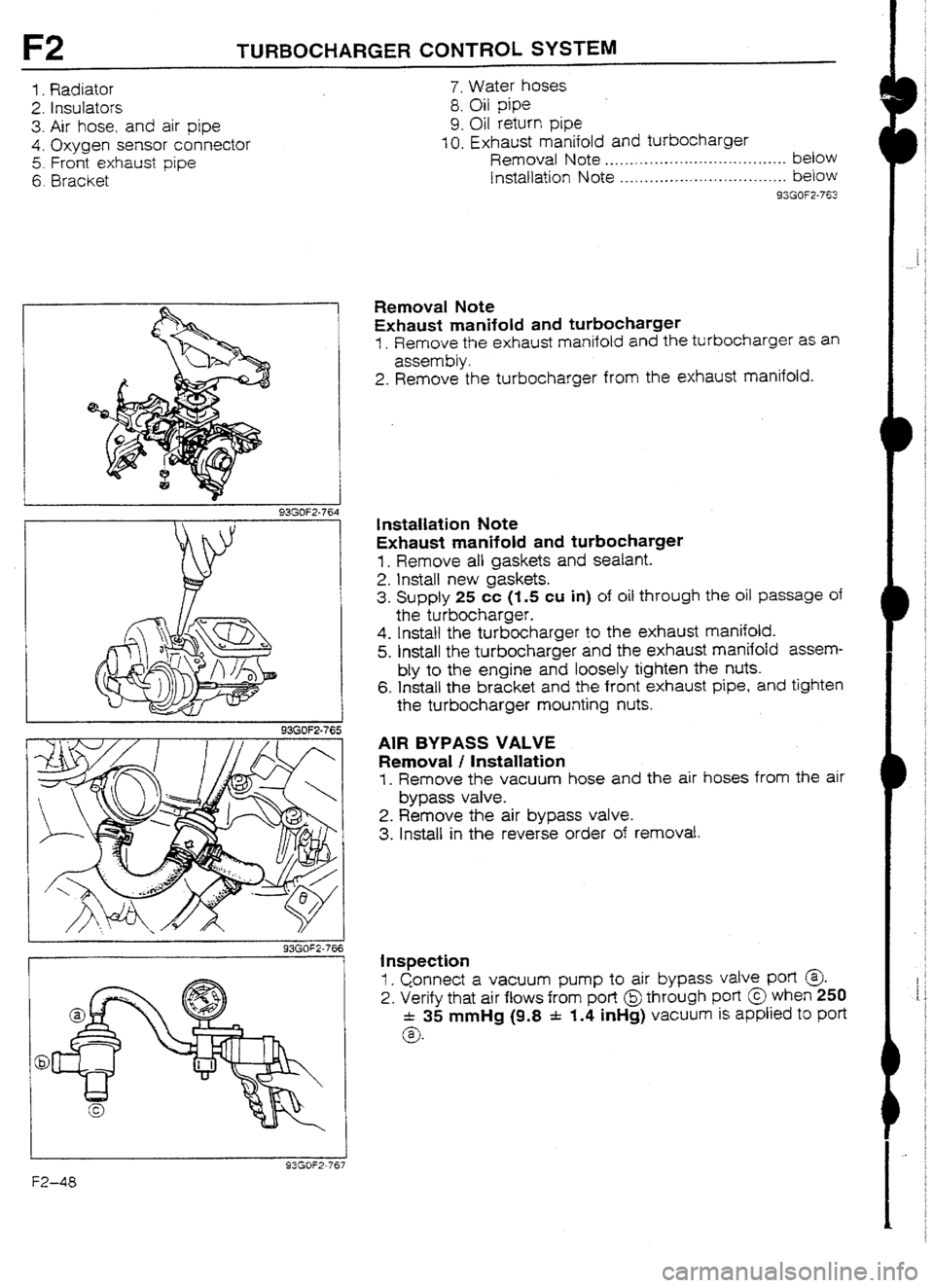
F2 TURBOCHARGERCONTROLSYSTEM
1. Radiator
2. Insulators
3.
Air hose, and air pipe
4. Oxygen
sensur connector
5. Front exhaust pipe
6. Bracket
1 I 93GOF2-765
93GOF2-761
7. Water hoses
8. Oil pipe
9. Oil return pipe
10. Exhaust
manifold and turbocharger
Removal Note . . . . . . . . . . . . . . . . . . . . . . .._.-........_ below
Installation Note . . . . ..__-.............._...___.._. below
93GOF2-763
Removal Note
Exhaust manifold and turbocharger
1. Remove the exhaust manifold and the turbocharger as an
assembly .
2. Remove the turbocharger from the exhaust
manifold.
InstaIlation Note
Exhaust manifold and turbocharger
1. Remove all gaskets and sealant.
2. Install new gaskets.
3. Supply 25 cc (1.5 cu in) of oil through the oil passage of
the turbocharger.
4. Install the turbocharger to the exhaust manifold.
5. Install the turbocharger and the exhaust manifold assem-
bly to the engine and loosely tighten the nuts.
6. install the bracket and the front exhaust pipe, and tighten
the turbocharger mounting nuts.
AIR BYPASS VALVE
Removal I Installation
1. Remove the vacuum hose and the air hoses from the air
bypass valve.
2. Remove the air bypass valve.
3. Install in the reverse order of removal.
Inspection
1. C_onnect a vacuum pump to air bypass valve port @-
2. Verify that air flows from port @through port @ when 250
f 35 mmHg (9.8 * 1.4 inHg) vacuum
is applied to port
0 a .
Page 166 of 677
TURBOCHARGER CONTROL SYSTEM F2
INTERCOOLER
RemovaI ! Inspection / Installation
1. Remove in the order shown in the figure.
2. Inspect the intercooler for crack or damage. Replace it if necessary.
3. Install in the reverse order of removal
19-25 (1.9-2.6,
(80-l 10 cm-kg, 69-95 in-lb)
cm-kg, 69-95 in-lb) 14-
1. Air cleaner and airflow meter assembly
2. Battery cooling duct
3. Air hose
4. Bracket 5 Undercover
6. Air hose
7. I ntercooler
N-m (m-kg, ft-lb)
93GOF2-761
F2-49
Page 167 of 677
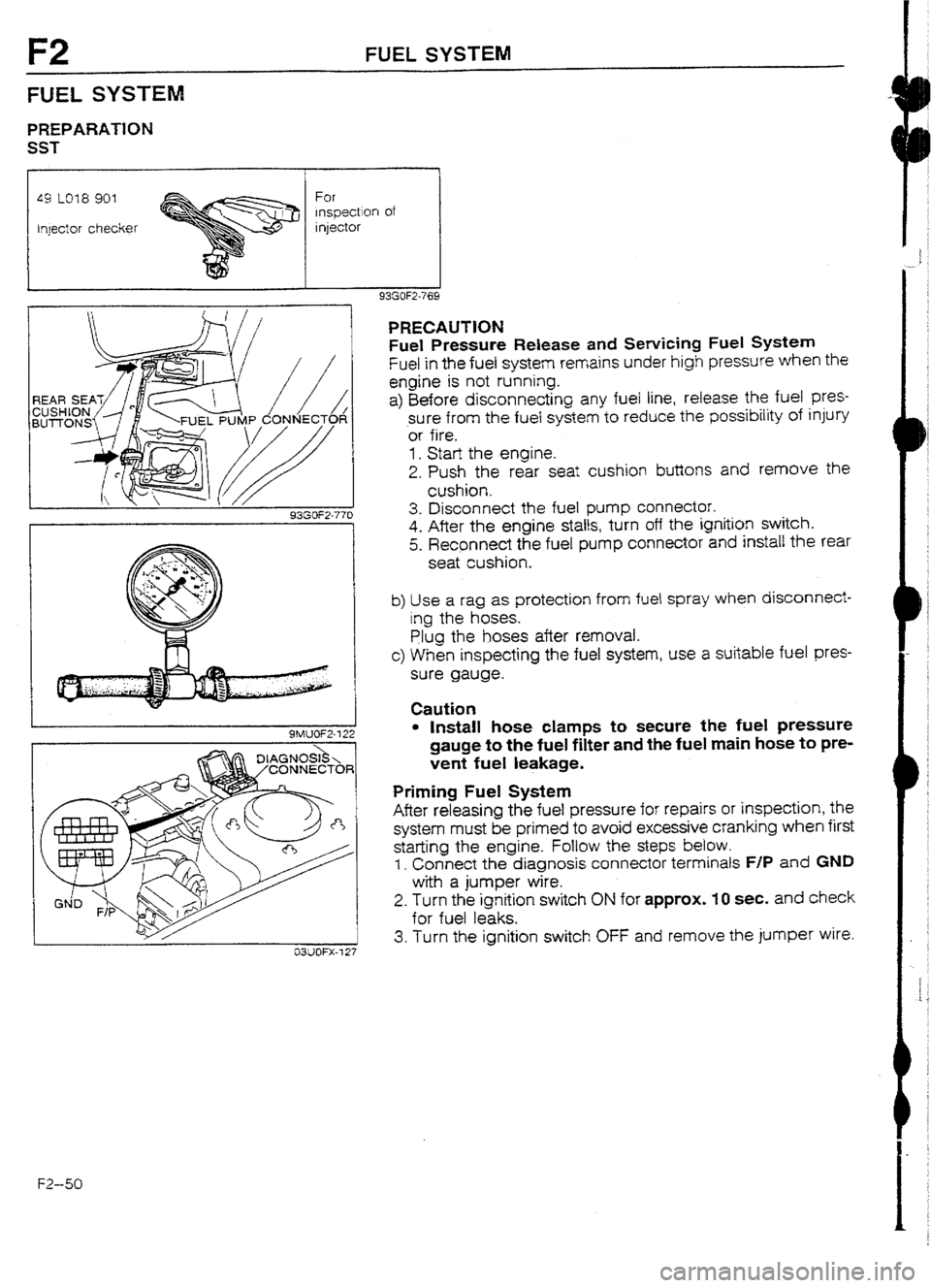
F2 FUEL SYSTEM
FUEL
SYSTEM
PREPARATlON
SST
49 LO18 901
Injector checker For
lnsgectlon of
injector
93GOF2.770
9MUOF2-722
03UOFX-7 27
F2-50
PRECAUTION
Fuel Pressure
Release and Servicing Fuel System
Fuel in the fuel system remains under high pressure when the
engine is not running.
a) Before disconnecting any fuel line, release the fuel pres-
sure from the fuel system to reduce the possibility of injury
‘or fife,
1. Start the engine.
2. Push the rear seat cushion buttons and remove the
cushion,
3. Disconnect the fuel pump connector.
4. After the engine stalts, turn off the ignition switch.
5. Recpnnect the fuel pump connector and install the rear
seat cushion.
b) Use a rag as protection from fuel spray when disconnect-
ing the hoses.
Plug the hoses after
removal.
c) When inspecting the fuel system, use a suitable fuel pres-
sure gauge.
Caution
l Install hose clamps to secure the fuel pressure
gauge to the fuel filter and the fuel main hose to pre-
vent fuet leakage.
Priming Fuel System
After releasing the fuel pressure for repairs or inspection, the
system must be primed to avoid excessive cranking when first
starting the engine. Follow the steps
below.
1. Connect the diagnosis connector terminals F/P and GND
with a jumper wire.
2. Turn the ignition switch
ON for approx. 10 set, and check
for fuel leaks.
3. Turn the ignition switch OFF and remove the jumper wire.
Page 168 of 677
FUEL SYSTEM F2
FUEL TANK
Removal I inspection / Instatlation
Warning
l Before performing the following operation, release the fue1 pressure from the fuet system to
reduce the possibitity of injury or fire. (Refer to page F2-50.)
l When removing the fuel tank, keep sparks, cigarettes, and open flames away from it.
l Before repairing the fuel tank, clean it throughly with steam to remove all explosive gas.
1. Remove in the order shown in the figure.
2. Inspect the fuel tank
components and repair or replace as necessary.
3. tnstall in the reverse order of removal, referring to Installation Note.
FUEL PUMP TRANSFER PUMP
0 SEAL RUBBER, REPLACE 7
A SSL
40-55 (4.1-56, 30-41)
N-m {m-kg, Mb)
93GOF2-771
F2-51