Page 583 of 751
10-34892-01
1. SPECIFICATION
Unit DescriptionSpecification
Remark
ABS ESP
HECU Clock frequency 32MHz 50MHz
Memory 128KB 256KB
S-sensor Operating voltage 4.75~5.25V
None (functions in
sensor cluster)Installed in IP
panel behind
audio (only for
4WD) Operating temperature-30 ~ 85℃
Operating range -1.5 ~ 1.5g
Output voltage 0.5 ~ 4.5V
Wheel speed
sensorSupplying voltage 4.5 ~ 16V←
Output current (approx. 2.7
km/h of vehicle speed)7mA(Lo) ~ 14mA
+20%←
Operating temperature-40 ~ 150℃ ←
Operating frequency 1~2500Hz←
Page 599 of 751
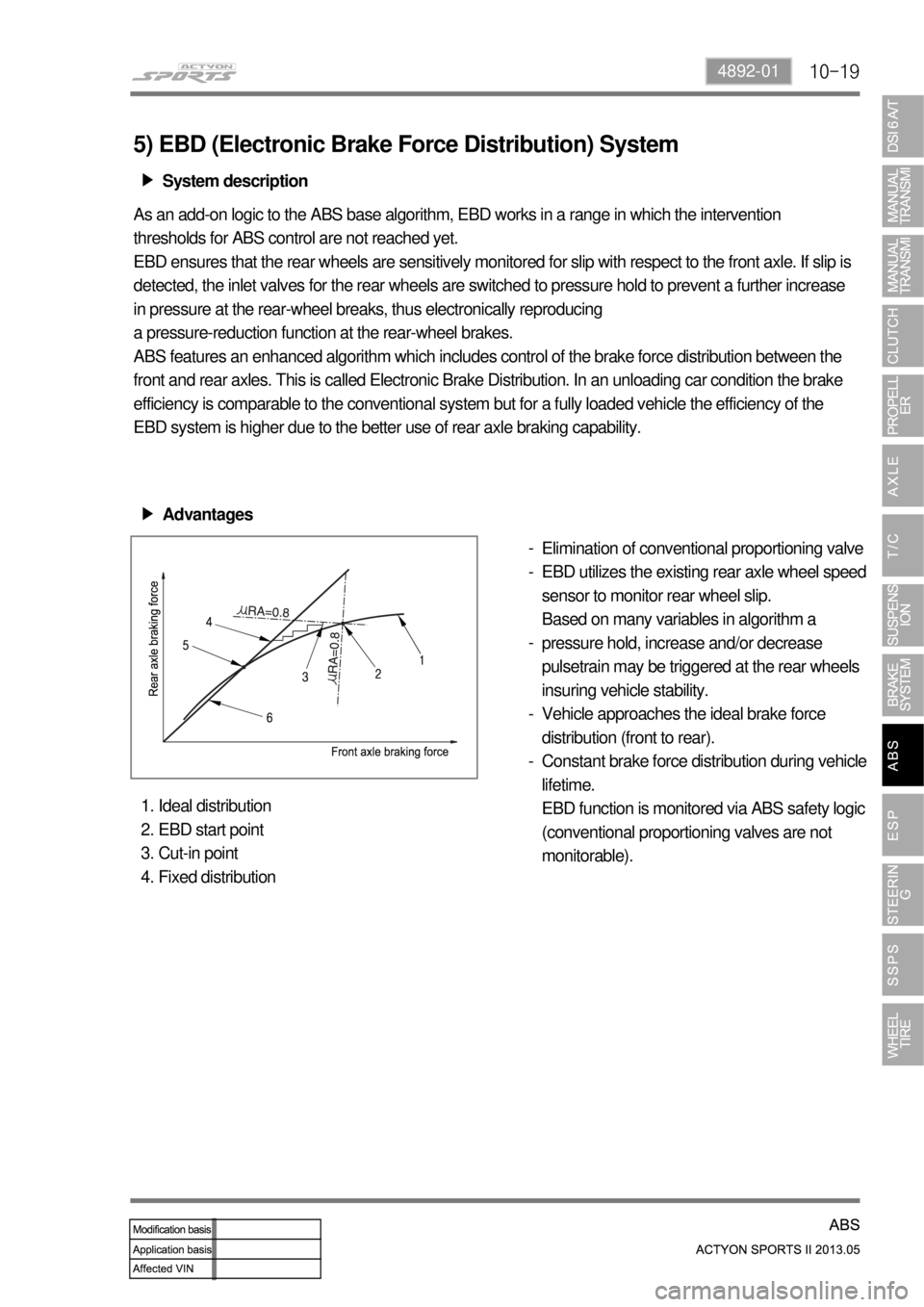
10-194892-01
5) EBD (Electronic Brake Force Distribution) System
System description ▶
As an add-on logic to the ABS base algorithm, EBD works in a range in which the intervention
thresholds for ABS control are not reached yet.
EBD ensures that the rear wheels are sensitively monitored for slip with respect to the front axle. If slip is
detected, the inlet valves for the rear wheels are switched to pressure hold to prevent a further increase
in pressure at the rear-wheel breaks, thus electronically reproducing
a pressure-reduction function at the rear-wheel brakes.
ABS features an enhanced algorithm which includes control of the brake force distribution between the
front and rear axles. This is called Electronic Brake Distribution. In an unloading car condition the brake
efficiency is comparable to the conventional system but for a fully loaded vehicle the efficiency of the
EBD system is higher due to the better use of rear axle braking capability.
Advantages ▶
Elimination of conventional proportioning valve
EBD utilizes the existing rear axle wheel speed
sensor to monitor rear wheel slip.
Based on many variables in algorithm a
pressure hold, increase and/or decrease
pulsetrain may be triggered at the rear wheels
insuring vehicle stability.
Vehicle approaches the ideal brake force
distribution (front to rear).
Constant brake force distribution during vehicle
lifetime.
EBD function is monitored via ABS safety logic
(conventional proportioning valves are not
monitorable). -
-
-
-
-
Ideal distribution
EBD start point
Cut-in point
Fixed distribution 1.
2.
3.
4.
Page 605 of 751
11-34890-10
1. SPECIFICATION
1) Specification of Active Wheel Sensor
Description Specification Remark
Supplying voltage 4.5 ~ 16.0V
Output current (at 2.75 km/h of vehicle
speed)7mA(Lo) ~ 14mA(Hi)
Tightening torqueFront: 7.8 to 11.8 Nm
Rear: 7.8 to 11.8 Nm
Operating temperature-40 ~ 150℃
Operating frequency 1 ~ 2,500Hz
UnitDescription
Specification
ABS ESP
HECU Clock frequency: 32 MHz Clock frequency: 50 MHz
Memory: 128 KB Memory: 256 KB
Wheel speed
sensorActive type Active type Output: 7~14 mA
Steering wheel
angle sensorNone Max. detection angle speed:
1500 °/SecPulse duty:
50±10%
Operating voltage: 9 to 12 V
Sensor cluster None Yaw rate sensor + lateral G
sensor + longitudinal G sensor
(4WD)Mounting
direction should
be kept (CAN
communcation)
Longitudinal G
sensor4WD only None
Pressure sensor None HECU integrated
Page 608 of 751
11-6
3. SYSTEM LAYOUT
ESP System ▶
Sensor - front wheel speed
Sensor - rear wheel speed
Screw (7.8~11.8 Nm)
Clip - cable holder
Clip - sensor cable mounting rear
Plug - blind
HECU
Sensor - cluster
Nut (9.8~10.8 Nm)
ESP OFF switch
Steering wheel sensor 1.
2.
3.
4.
5.
6.
9.
10.
11.
12.
13.
Page 610 of 751
11-8
1. OVERVIEW
The ESP (Electronic Stability Program) has been developed to help a driver avoid danger of losing
control of the vehicle stability due to understeer or oversteer during cornering. The yaw rate sensor,
lateral sensor and longitudinal sensor in the sensor cluster and the steering wheel angle sensor under
the steering column detect the vehicle conditions when the inner or outer wheels are spinning during
oversteer, understeer or cornering. The ESP ECU controls against oversteer or understeer during
cornering by controlling the vehicle stability using input values from these sensors and applying the
braking force to the corresponding wheels independently. The system also controls the engine power
right before the wheel spin synchronized to decelerate the vehicle automatically in order to maintain the
vehicle stable during cornering.
Page 611 of 751
11-94890-10
ESP OFF switch
Located on the left side of
instrument panel.
Rear wheel speed sensor
Located on the both ends of
rear axle.Front wheel speed sensor
Located on the hub assembly.Sensor cluster
Located at the bottom of center
fascia panel.
Steering wheel angle sensor
Located on column shaft with
contact coil.HECU assembly
Located near the brake booster
in engine compartment and
contains the pressure sensor.
2. COMPONENTS
Page 612 of 751
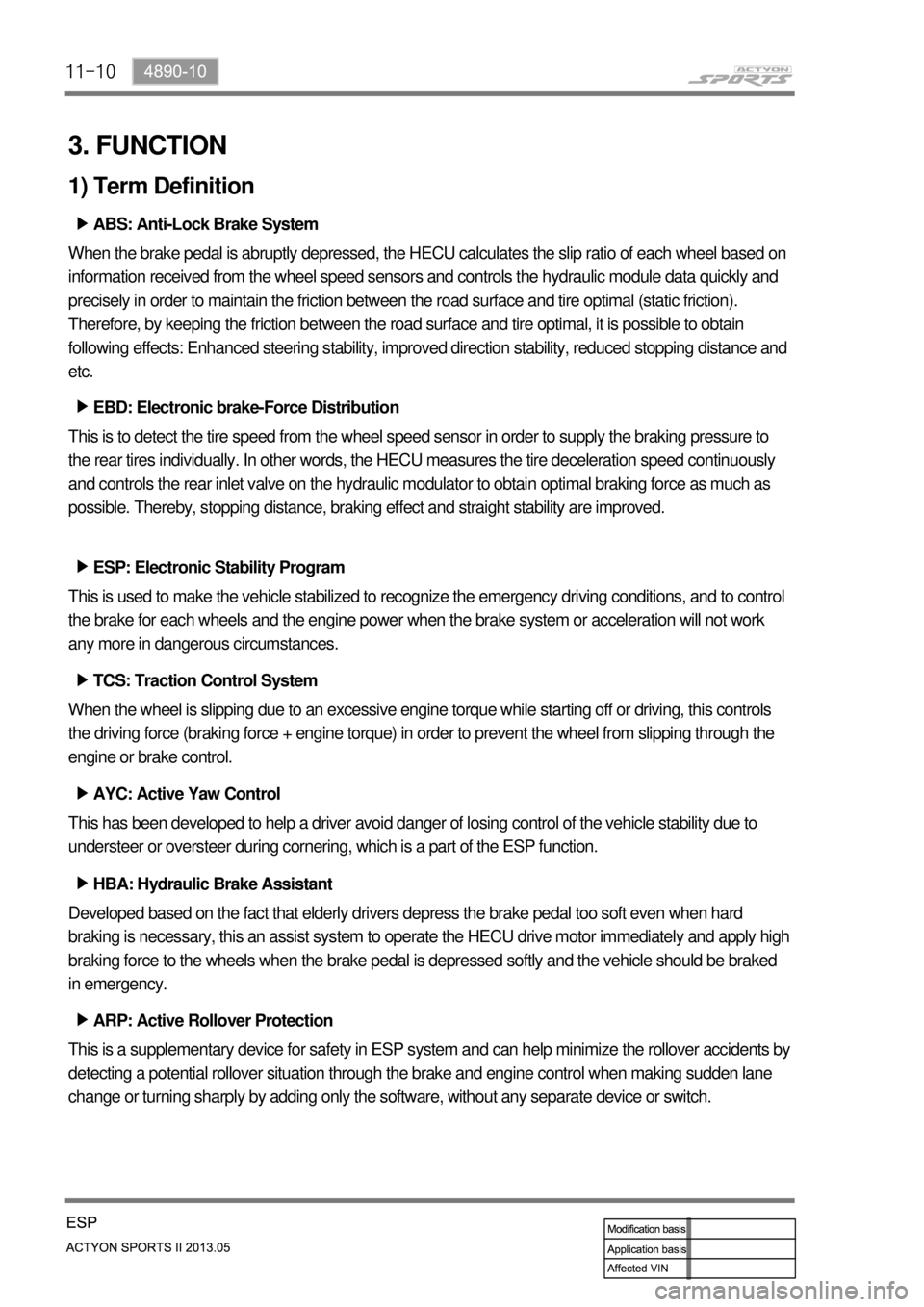
11-10
3. FUNCTION
1) Term Definition
ABS: Anti-Lock Brake System ▶
When the brake pedal is abruptly depressed, the HECU calculates the slip ratio of each wheel based on
information received from the wheel speed sensors and controls the hydraulic module data quickly and
precisely in order to maintain the friction between the road surface and tire optimal (static friction).
Therefore, by keeping the friction between the road surface and tire optimal, it is possible to obtain
following effects: Enhanced steering stability, improved direction stability, reduced stopping distance and
etc.
EBD: Electronic brake-Force Distribution ▶
This is to detect the tire speed from the wheel speed sensor in order to supply the braking pressure to
the rear tires individually. In other words, the HECU measures the tire deceleration speed continuously
and controls the rear inlet valve on the hydraulic modulator to obtain optimal braking force as much as
possible. Thereby, stopping distance, braking effect and straight stability are improved.
ESP: Electronic Stability Program ▶
This is used to make the vehicle stabilized to recognize the emergency driving conditions, and to control
the brake for each wheels and the engine power when the brake system or acceleration will not work
any more in dangerous circumstances.
TCS: Traction Control System ▶
When the wheel is slipping due to an excessive engine torque while starting off or driving, this controls
the driving force (braking force + engine torque) in order to prevent the wheel from slipping through the
engine or brake control.
AYC: Active Yaw Control ▶
This has been developed to help a driver avoid danger of losing control of the vehicle stability due to
understeer or oversteer during cornering, which is a part of the ESP function.
HBA: Hydraulic Brake Assistant ▶
Developed based on the fact that elderly drivers depress the brake pedal too soft even when hard
braking is necessary, this an assist system to operate the HECU drive motor immediately and apply high
braking force to the wheels when the brake pedal is depressed softly and the vehicle should be braked
in emergency.
ARP: Active Rollover Protection ▶
This is a supplementary device for safety in ESP system and can help minimize the rollover accidents by
detecting a potential rollover situation through the brake and engine control when making sudden lane
change or turning sharply by adding only the software, without any separate device or switch.
Page 613 of 751
11-114890-10
2) Component Overview By System
3) Part Overview By System
Part Vehicle with ABS Vehicle with ESP
HECU
Yes Yes Front wheel speed sensor
Rear wheel speed sensor
ABS warning lamp
EBD indicator lamp
G sensor (integrated in HECU) 4WD: Yes, 2WD: No No
Sensor cluster (Yaw rate sensor +
lateral sensor+ G sensor)
No Yes ESP operation indicator lamp and
warning lamp
ESP OFF switch and indicator
Steering wheel angle sensor
Function Vehicle with ABS Vehicle with ESP
ABS Yes
Yes EBD Yes
HBA
No
ARP