Page 501 of 751
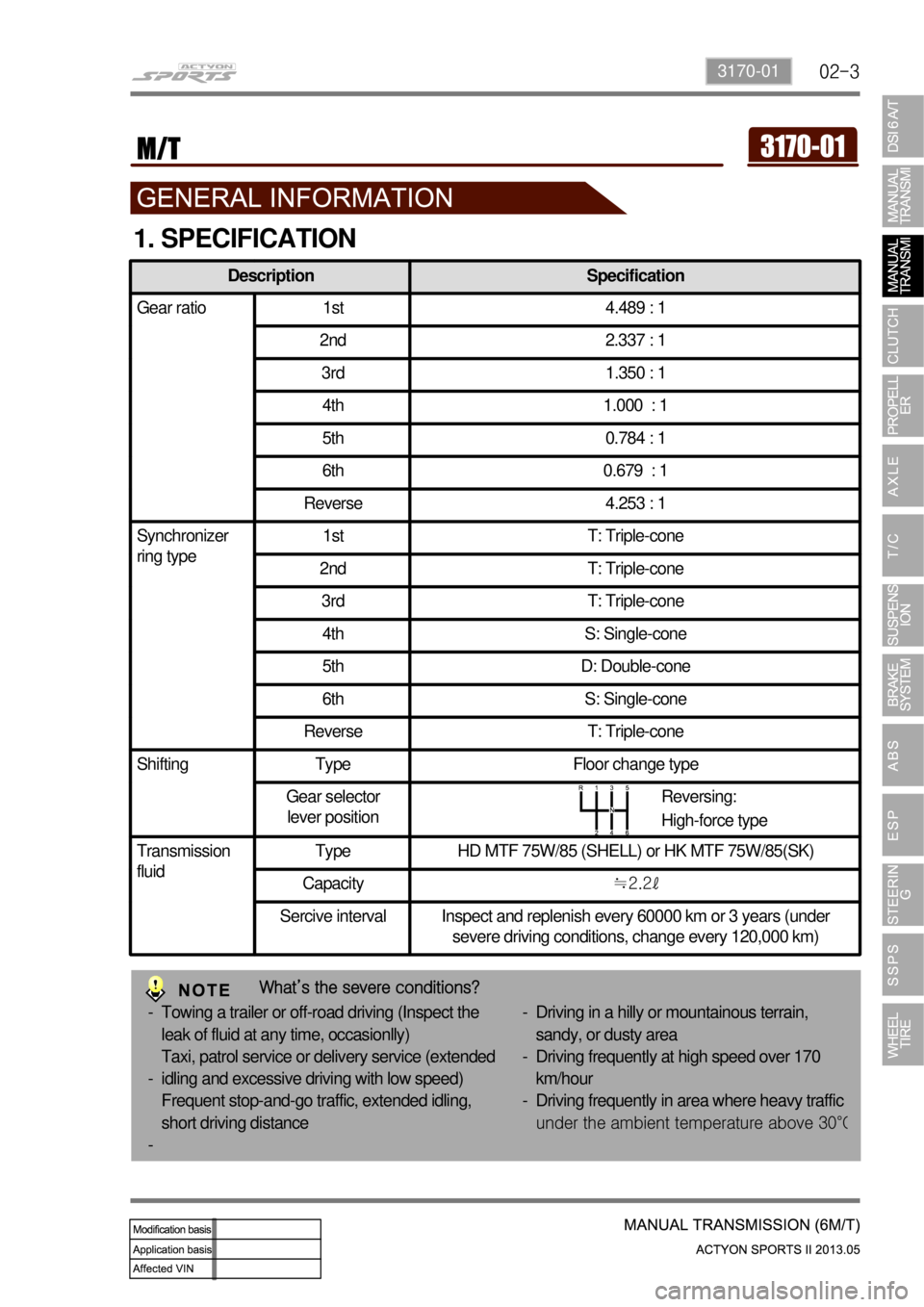
02-33170-01
Description Specification
Gear ratio 1st 4.489 : 1
2nd 2.337 : 1
3rd 1.350 : 1
4th 1.000 : 1
5th 0.784 : 1
6th 0.679 : 1
Reverse 4.253 : 1
Synchronizer
ring type1st T: Triple-cone
2nd T: Triple-cone
3rd T: Triple-cone
4th S: Single-cone
5th D: Double-cone
6th S: Single-cone
Reverse T: Triple-cone
Shifting Type Floor change type
Gear selector
lever position
Transmission
fluidType HD MTF 75W/85 (SHELL) or HK MTF 75W/85(SK)
Capacity≒2.2ℓ
Sercive interval Inspect and replenish every 60000 km or 3 years (under
severe driving conditions, change every 120,000 km)
1. SPECIFICATION
Reversing:
High-force type
What’s the severe conditions?
Towing a trailer or off-road driving (Inspect the
leak of fluid at any time, occasionlly)
Taxi, patrol service or delivery service (extended
idling and excessive driving with low speed)
Frequent stop-and-go traffic, extended idling,
short driving distance -
-
-Driving in a hilly or mountainous terrain,
sandy, or dusty area
Driving frequently at high speed over 170
km/hour
Driving frequently in area where heavy traffic
under the ambient tem
perature above 30°C
-
-
-
Page 553 of 751
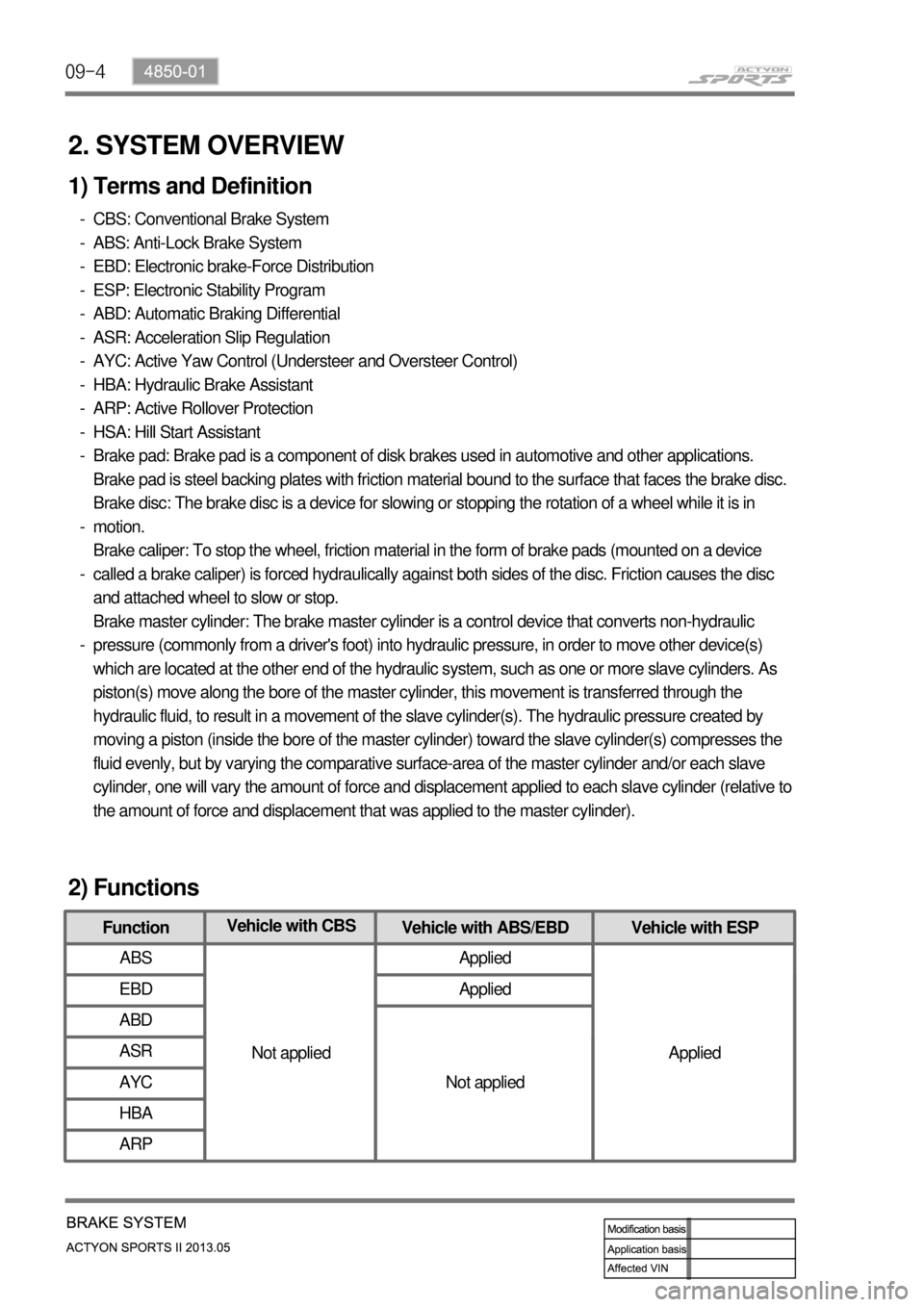
09-4
2. SYSTEM OVERVIEW
1) Terms and Definition
CBS: Conventional Brake System
ABS: Anti-Lock Brake System
EBD: Electronic brake-Force Distribution
ESP: Electronic Stability Program
ABD: Automatic Braking Differential
ASR: Acceleration Slip Regulation
AYC: Active Yaw Control (Understeer and Oversteer Control)
HBA: Hydraulic Brake Assistant
ARP: Active Rollover Protection
HSA: Hill Start Assistant
Brake pad: Brake pad is a component of disk brakes used in automotive and other applications.
Brake pad is steel backing plates with friction material bound to the surface that faces the brake disc.
Brake disc: The brake disc is a device for slowing or stopping the rotation of a wheel while it is in
motion.
Brake caliper: To stop the wheel, friction material in the form of brake pads (mounted on a device
called a brake caliper) is forced hydraulically against both sides of the disc. Friction causes the disc
and attached wheel to slow or stop.
Brake master cylinder: The brake master cylinder is a control device that converts non-hydraulic
pressure (commonly from a driver's foot) into hydraulic pressure, in order to move other device(s)
which are located at the other end of the hydraulic system, such as one or more slave cylinders. As
piston(s) move along the bore of the master cylinder, this movement is transferred through the
hydraulic fluid, to result in a movement of the slave cylinder(s). The hydraulic pressure created by
moving a piston (inside the bore of the master cylinder) toward the slave cylinder(s) compresses the
fluid evenly, but by varying the comparative surface-area of the master cylinder and/or each slave
cylinder, one will vary the amount of force and displacement applied to each slave cylinder (relative to
the amount of force and displacement that was applied to the master cylinder). -
-
-
-
-
-
-
-
-
-
-
-
-
-
FunctionVehicle with CBS
Vehicle with ABS/EBD Vehicle with ESP
ABS
Not appliedApplied
Applied EBD Applied
ABD
Not applied ASR
AYC
HBA
ARP
2) Functions
Page 618 of 751
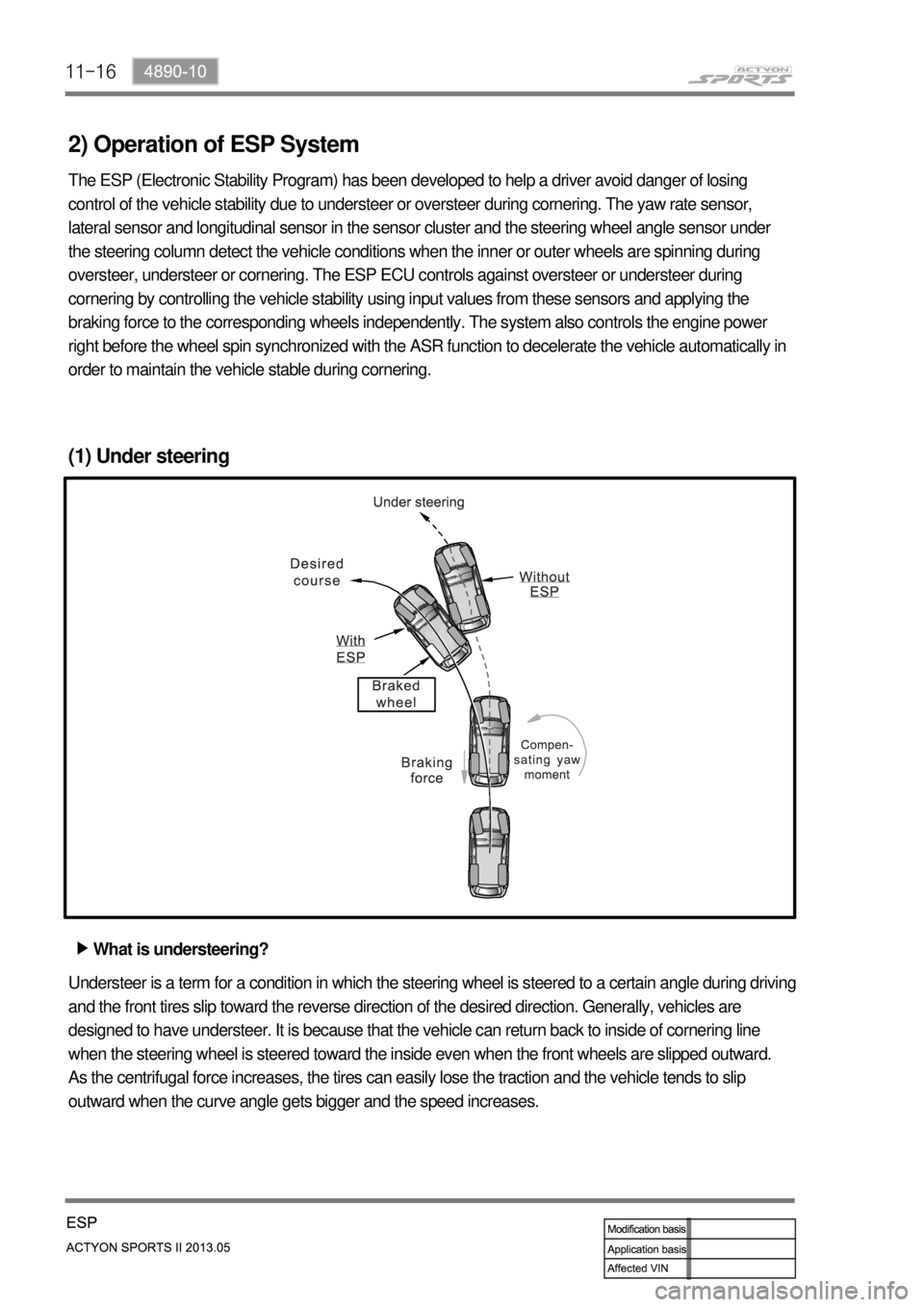
11-16
2) Operation of ESP System
The ESP (Electronic Stability Program) has been developed to help a driver avoid danger of losing
control of the vehicle stability due to understeer or oversteer during cornering. The yaw rate sensor,
lateral sensor and longitudinal sensor in the sensor cluster and the steering wheel angle sensor under
the steering column detect the vehicle conditions when the inner or outer wheels are spinning during
oversteer, understeer or cornering. The ESP ECU controls against oversteer or understeer during
cornering by controlling the vehicle stability using input values from these sensors and applying the
braking force to the corresponding wheels independently. The system also controls the engine power
right before the wheel spin synchronized with the ASR function to decelerate the vehicle automatically in
order to maintain the vehicle stable during cornering.
(1) Under steering
What is understeering? ▶
Understeer is a term for a condition in which the steering wheel is steered to a certain angle during driving
and the front tires slip toward the reverse direction of the desired direction. Generally, vehicles are
designed to have understeer. It is because that the vehicle can return back to inside of cornering line
when the steering wheel is steered toward the inside even when the front wheels are slipped outward.
As the centrifugal force increases, the tires can easily lose the traction and the vehicle tends to slip
outward when the curve angle gets bigger and the speed increases.
Page 619 of 751
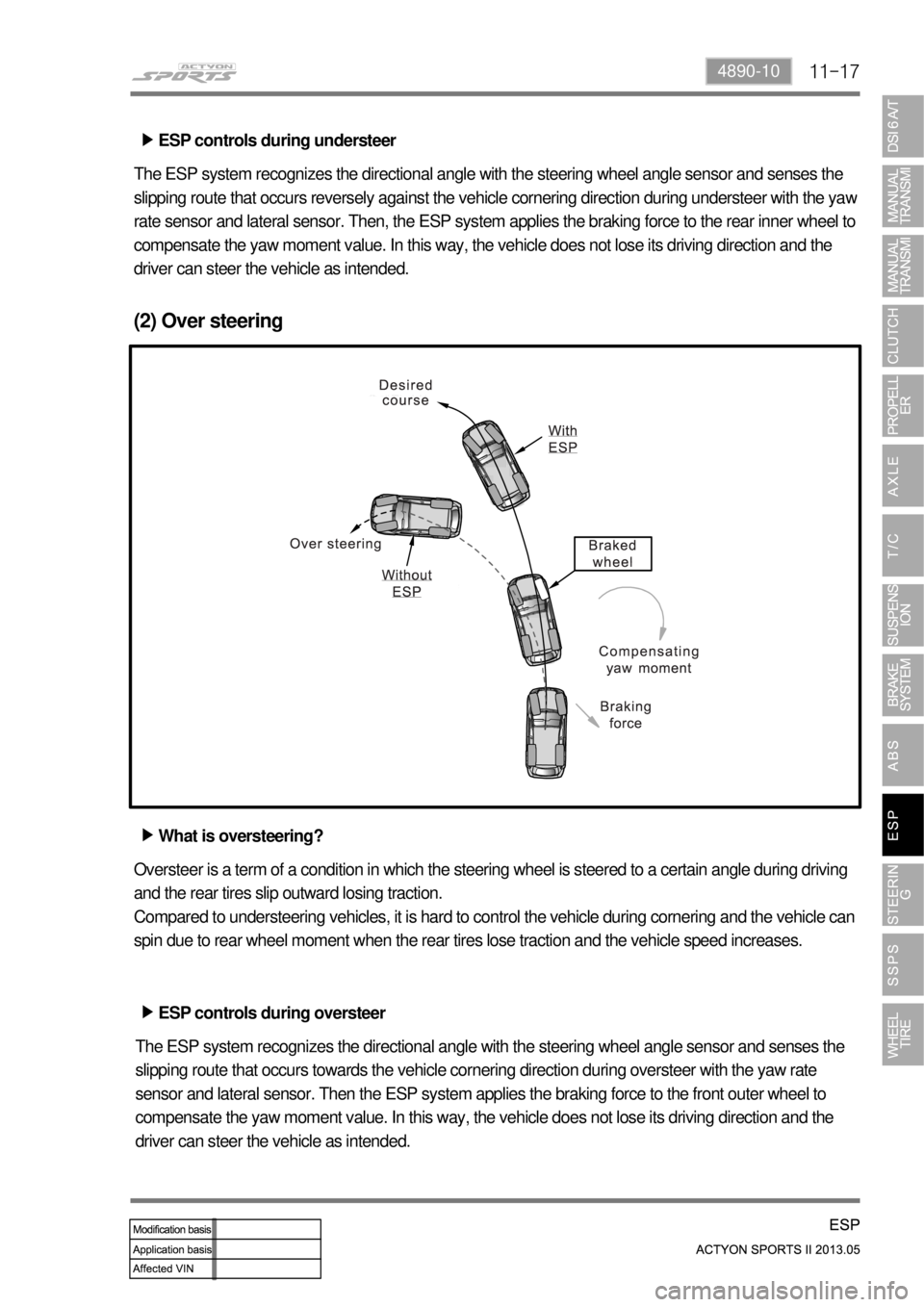
11-174890-10
ESP controls during understeer ▶
The ESP system recognizes the directional angle with the steering wheel angle sensor and senses the
slipping route that occurs reversely against the vehicle cornering direction during understeer with the ya
w
rate sensor and lateral sensor. Then, the ESP system applies the braking force to the rear inner wheel to
compensate the yaw moment value. In this way, the vehicle does not lose its driving direction and the
driver can steer the vehicle as intended.
(2) Over steering
What is oversteering? ▶
Oversteer is a term of a condition in which the steering wheel is steered to a certain angle during driving
and the rear tires slip outward losing traction.
Compared to understeering vehicles, it is hard to control the vehicle during cornering and the vehicle can
spin due to rear wheel moment when the rear tires lose traction and the vehicle speed increases.
ESP controls during oversteer ▶
The ESP system recognizes the directional angle with the steering wheel angle sensor and senses the
slipping route that occurs towards the vehicle cornering direction during oversteer with the yaw rate
sensor and lateral sensor. Then the ESP system applies the braking force to the front outer wheel to
compensate the yaw moment value. In this way, the vehicle does not lose its driving direction and the
driver can steer the vehicle as intended.
Page 660 of 751
13-10
▶ In medium and high speed driving
The shaft operation force of solenoid rod is reduced due to the reduction of output current from SSPS
control unit.
The coil spring pulls the PCV spool toward solenoid valve to open it.
The hydraulic pressure from pump flows to pinion reaction area through orifice and applies reaction
force to reaction plunger.
At this time, the reaction plunger transmits the reaction force to V-groove in input shaft to provide heavy
steerability. 1.
2.
3.
4.
Page 667 of 751
14-6
Symptom Possible Cause
Blade type wear from outer side
toward inner side of the tread
Excessive toe-in,
Deflection of knuckle arm,
Difference in tie rod length
between left and right sides
Blade type wear from inner side
toward outer side of the tread
Excessive toe-in,
Deflection of knuckle arm,
Difference in tie rod length
between left and right sides
Corrugation wear of tread
Poor wheel balance,
Loose wheel bearing,
poor wheel alignment
InsideOutside
Inside
Outside
Inside
Outside
Page 679 of 751
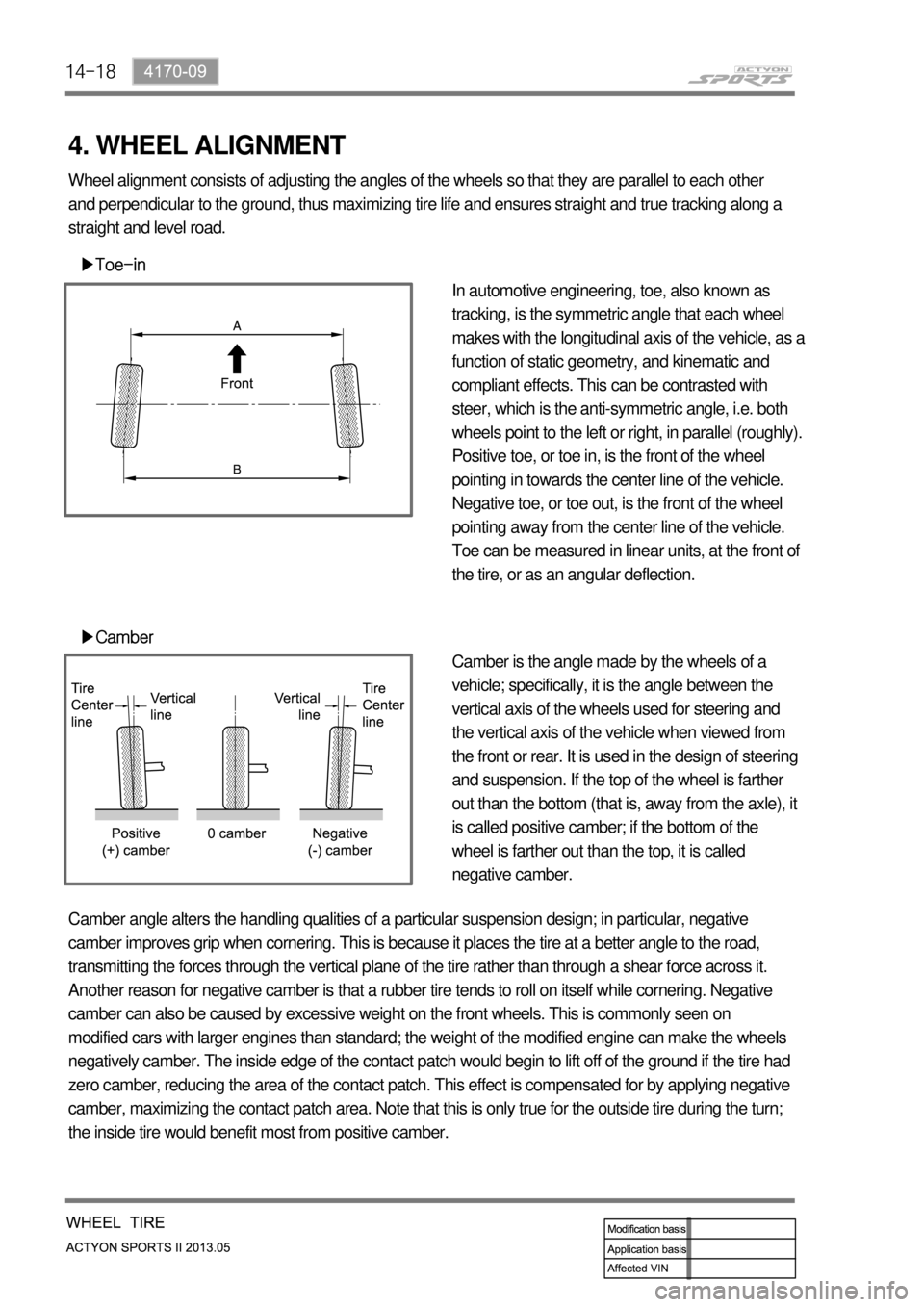
14-18
4. WHEEL ALIGNMENT
▶Toe-in
▶Camber
In automotive engineering, toe, also known as
tracking, is the symmetric angle that each wheel
makes with the longitudinal axis of the vehicle, as a
function of static geometry, and kinematic and
compliant effects. This can be contrasted with
steer, which is the anti-symmetric angle, i.e. both
wheels point to the left or right, in parallel (roughly).
Positive toe, or toe in, is the front of the wheel
pointing in towards the center line of the vehicle.
Negative toe, or toe out, is the front of the wheel
pointing away from the center line of the vehicle.
Toe can be measured in linear units, at the front of
the tire, or as an angular deflection.
Camber is the angle made by the wheels of a
vehicle; specifically, it is the angle between the
vertical axis of the wheels used for steering and
the vertical axis of the vehicle when viewed from
the front or rear. It is used in the design of steering
and suspension. If the top of the wheel is farther
out than the bottom (that is, away from the axle), it
is called positive camber; if the bottom of the
wheel is farther out than the top, it is called
negative camber. Wheel alignment consists of adjusting the angles of the wheels so that they are parallel to each other
and perpendicular to the ground, thus maximizing tire life and ensures straight and true tracking along a
straight and level road.
Camber angle alters the handling qualities of a particular suspension design; in particular, negative
camber improves grip when cornering. This is because it places the tire at a better angle to the road,
transmitting the forces through the vertical plane of the tire rather than through a shear force across it.
Another reason for negative camber is that a rubber tire tends to roll on itself while cornering. Negative
camber can also be caused by excessive weight on the front wheels. This is commonly seen on
modified cars with larger engines than standard; the weight of the modified engine can make the wheels
negatively camber. The inside edge of the contact patch would begin to lift off of the ground if the tire had
zero camber, reducing the area of the contact patch. This effect is compensated for by applying negative
camber, maximizing the contact patch area. Note that this is only true for the outside tire during the turn;
the inside tire would benefit most from positive camber.
Page 688 of 751
01-96810-01
▶ Step 5
Ambient
temperature
display
51
Interior
temperature
displayIntake air
temperature display
Ambient
temperature
sensorInterior
temperature
sensorIntake air temperature
sensor
▶ Step 6
To enter the step 6 from 5, turn the fan speed dial lightly toward the right not using the
temperature control dial. In this step, you can decrease or increase by up to 3 degrees from the
temperature set on the A/C controller. -You can check that the temperature value from each temperature sensor is displayed properly in
this step. Pressing the defroster switch changes the temperature value that appears on the
display in the order as follows: -
2) Self-diagnosis step
(1) Step 1
Turn the ignition ON and press the OFF switch for 5 sec. or more within 10 sec.
Then the first step of the self-diagnosis is started as shown in the below figure.
2. Display for checking VFD and all LED segments
1. Press OFF switch for 5 sec. or more