Page 589 of 715
07-6
(1) Shock Absorber and Coil Spring
4. DIMENSIONS OF FRONT SUSPENSION
Page 591 of 715
07-8
Shock Absorber ▶
Fully extended length
547.0 ± 0.3 (mm)
Fully compressed
length462.0 + 0.3 (mm)
Operating distance85.0 (mm)
Page 592 of 715
07-94411-01
5. DIMENSIONS OF REAR SUSPENSION
(1) Shock Absorber
Keep the suitable distance when compressed and extended.
Minimum length should be 10 mm longer than the fully compressed length. -
-
Dimension ▶
Maximum operating length Minimum operating length
Operating distance
487.0 ± 0.3 (mm) 326.0 + 0.3 (mm) 160.4 (mm)
Marking ▶
X: Part number
Y: Lot number
Ex:
3C12
12.............(Day)
3...............(Month)
2003......(Year)
Page 611 of 715
09-34891-01
1. SPECIFICATIONS
1) Pressure Sensor
UnitDescription
Location
ABS ESP
HECU
(Hydraulic &
Electronic Control
Unit) CPU:MCU60 (32bit)
Clock Frequency: 28MHz
Memory: 128~256 KB CPU:MCU60 (32bit)
Clock Frequency: 28MHz
Memory:256~512 KB Under the front
washer reservoir
Wheel Speed
SensorActive type wheel speed
sensorActive type wheel speed
sensorOn each wheel
Front air gap:
0.335~0.945mm,
Rear air gap:
0.309~0.958
Steering Wheel
Angle SensorN/AMaximum angular speed:
1500°/sec
Operating voltage: 9~16VUnder the steering
wheel
Sensor ClusterN/AIntegrated with yaw rate
sensor and lateral sensorUnder the audio
assembly
Pressure Sensor
N/A Analog outputUnder the master
cylinder
Description Specification
Supplying voltage approx. 5V (4.75~5.25V)
Max. pressure 350bar
Page 613 of 715
09-54891-01
1. ESP (Electronic Stability Program)
ESP system contains the ABS (Anti-Lock Brake System), ABD (Automatic Braking Differential),
ASR (Acceleration Slip Regulation), Cornering Control and HBA (Hydraulic Brake Assist System)
functions.
▶Cornering Control (Understeer and Overersteer) Function
This function controls the vehicle stability by applying the braking pressure on each wheel
according to the yaw rate, lateral sensing value and driver’s steering wheel control.
▶HBA (Hydraulic Brake Assist System) Function
HBA (Hydraulic Brake Assist) system helps in an emergency braking situation when the driver
applies the brake fast, but not with sufficient pressure, which leads to dangerously long braking
distance. ECU recognizes the attempt at full braking and transmits the signal calling for full brake
pressure from the hydraulic booster.
Page 614 of 715
09-6
HECU(Hydraulic & Electronic Control Unit)
ESP ABS
2. LAYOUT
Name ESP ABS Location
1 HECU O O Under the battery
2 Pressure Sensor O X Under the master cylinder
3 Wheel Speed Sensor O O On wheels
4 Sensor Cluster O X Under the audio assembly
5 Steering Wheel Angle Sensor O X Under the steering wheel
Pressure Sensor
Installed Removed
Page 620 of 715
09-12
(4) Vehicle Control During Cornering
The figure below shows the vehicle controls by the ESP system under various situations such as
when the brake pedal is depressed or not depressed during cornering, when the ABS is operating
and when braking without the ABS. It also includes the vehicle conditions when the TCS, a part of
the ESP system, is operating.
Condition Understeer control Oversteer control
Only ESP in
operation
No braking by
driver
ESP
+
Normal braking
(no ABS operation)
ESP
+
ABS brake
ESP + ASR
Page 623 of 715
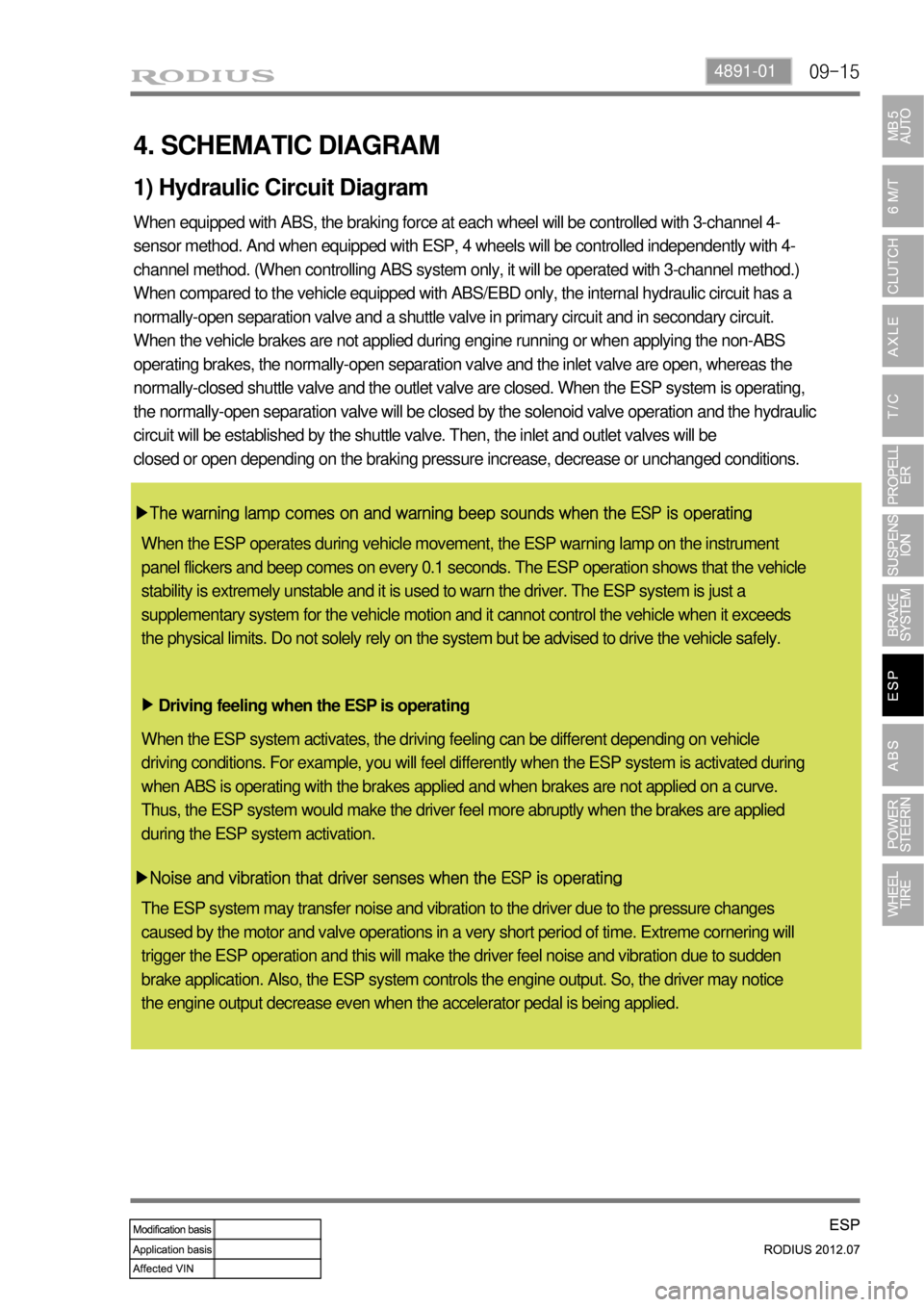
09-154891-01
4. SCHEMATIC DIAGRAM
When equipped with ABS, the braking force at each wheel will be controlled with 3-channel 4-
sensor method. And when equipped with ESP, 4 wheels will be controlled independently with 4-
channel method. (When controlling ABS system only, it will be operated with 3-channel method.)
When compared to the vehicle equipped with ABS/EBD only, the internal hydraulic circuit has a
normally-open separation valve and a shuttle valve in primary circuit and in secondary circuit.
When the vehicle brakes are not applied during engine running or when applying the non-ABS
operating brakes, the normally-open separation valve and the inlet valve are open, whereas the
normally-closed shuttle valve and the outlet valve are closed. When the ESP system is operating,
the normally-open separation valve will be closed by the solenoid valve operation and the hydraulic
circuit will be established by the shuttle valve. Then, the inlet and outlet valves will be
closed or open depending on the braking pressure increase, decrease or unchanged conditions.
▶The warning lamp comes on and warning beep sounds when the ESP is operating
Driving feeling when the ESP is operating ▶
▶Noise and vibration that driver senses when the ESP is operating
1) Hydraulic Circuit Diagram
When the ESP operates during vehicle movement, the ESP warning lamp on the instrument
panel flickers and beep comes on every 0.1 seconds. The ESP operation shows that the vehicle
stability is extremely unstable and it is used to warn the driver. The ESP system is just a
supplementary system for the vehicle motion and it cannot control the vehicle when it exceeds
the physical limits. Do not solely rely on the system but be advised to drive the vehicle safely.
When the ESP system activates, the driving feeling can be different depending on vehicle
driving conditions. For example, you will feel differently when the ESP system is activated during
when ABS is operating with the brakes applied and when brakes are not applied on a curve.
Thus, the ESP system would make the driver feel more abruptly when the brakes are applied
during the ESP system activation.
The ESP system may transfer noise and vibration to the driver due to the pressure changes
caused by the motor and valve operations in a very short period of time. Extreme cornering will
trigger the ESP operation and this will make the driver feel noise and vibration due to sudden
brake application. Also, the ESP system controls the engine output. So, the driver may notice
the engine output decrease even when the accelerator pedal is being applied.