Page 273 of 600
Component SizeBolt
QuantitySpecified torque
(Nm)Remark
(Total torque)
Glow plug M5 4
-
Vacuum pump
3 -
Timing gear case cover
3 -
7 -
1 -
3 -
Cylinder head cover
21 -
Oil gauge tube
1 -
Oil filter cap 1
-
Fuel rail
2 -
Injector clamp bolt
2 -
High pressure pipe
(between HP pump and
fuel rail)M17 1
-
High pressure pipe
(between fuel rail and
injector)M17 4
-
Crank position sensor
1 -
Main wiring
5 -
Intake duct M8x25 4
-
Power steering pump
3 -
Cylinder head front cover
5 -
Ladder frame
5 -
Oil pump
3 -
Page 279 of 600
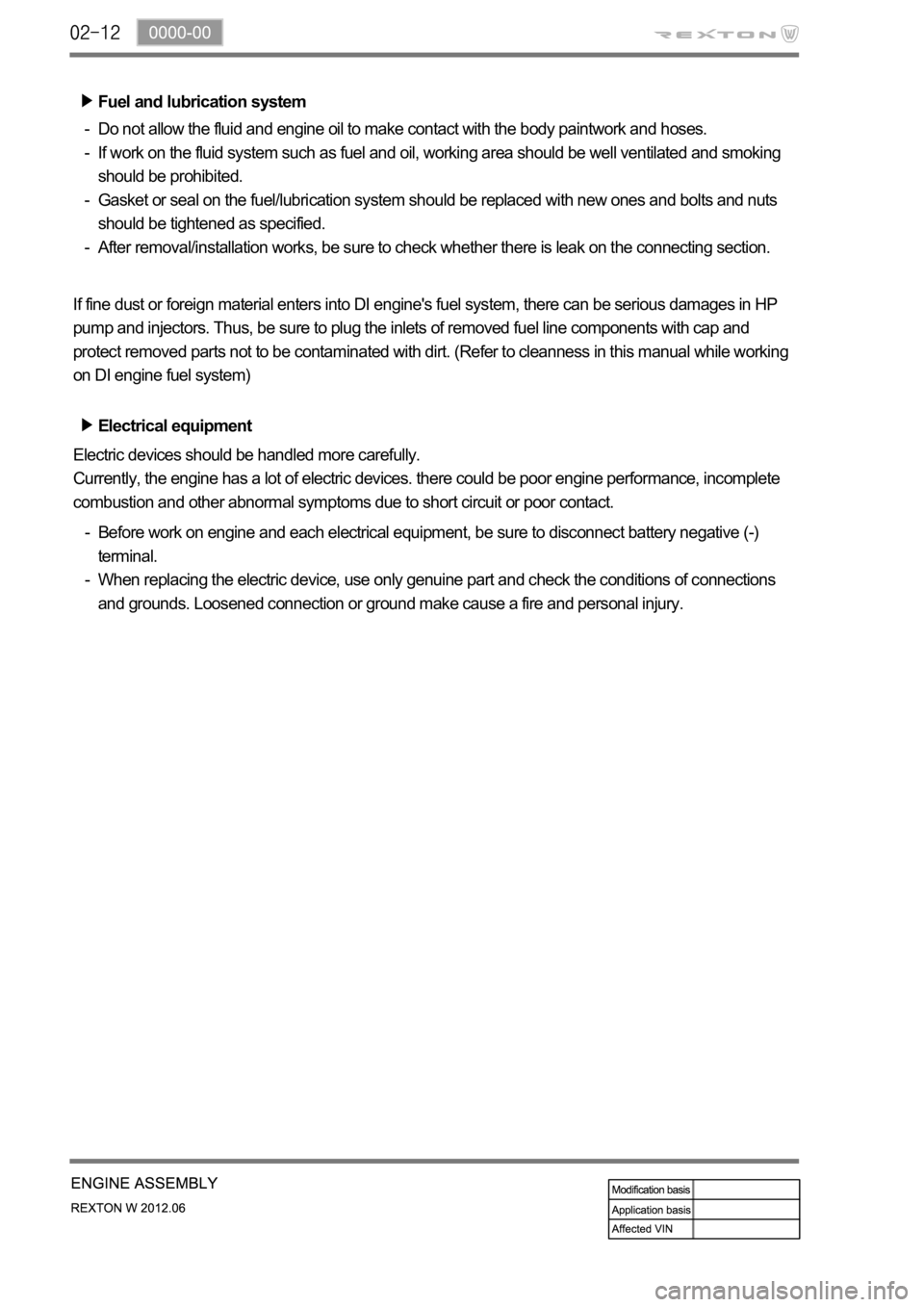
Electrical equipment
Electric devices should be handled more carefully.
Currently, the engine has a lot of electric devices. there could be poor engine performance, incomplete
combustion and other abnormal symptoms due to short circuit or poor contact.
Before work on engine and each electrical equipment, be sure to disconnect battery negative (-)
terminal.
When replacing the electric device, use only genuine part and check the conditions of connections
and grounds. Loosened connection or ground make cause a fire and personal injury. -
-Fuel and lubrication system
Do not allow the fluid and engine oil to make contact with the body paintwork and hoses.
If work on the fluid system such as fuel and oil, working area should be well ventilated and smoking
should be prohibited.
Gasket or seal on the fuel/lubrication system should be replaced with new ones and bolts and nuts
should be tightened as specified.
After removal/installation works, be sure to check whether there is leak on the connecting section. -
-
-
-
If fine dust or foreign material enters into DI engine's fuel system, there can be serious damages in HP
pump and injectors. Thus, be sure to plug the inlets of removed fuel line components with cap and
protect removed parts not to be contaminated with dirt. (Refer to cleanness in this manual while working
on DI engine fuel system)
Page 317 of 600
2210-01
1. SPECIFICATION
Description Specification
Fuel Diesel
Fuel filterType Fuel heater + priming pump + water
separator integrated type
Filter type Changeable filter element type
Water accumulating capacity 200 cc
Heater capacity 250W 13.5V
Injector System pressure 1800 bar
High pressure fuel
pumpType Eccentric cam/Plunger type
Operating type Gear driven type
Normal operating temperature
Operating pressure 1800 bar
Operating temperature
Low pressure fuel
pumpType Vane type
Gear ratio (pump/engine) 0.5 : 1
Pressure 6 bar
Fuel tankCapacity 75 L
Material Steel
Fuel sender Single sender type
Change interval EU every 40,000 km
GEN every 45,000 km
Water separation
intervalEU every 20,000 km
GEN every 15,000 km
Page 318 of 600
2. MAINTENANCE AND INSPECTION
1) Maintenance Procedures for DI Engine Fuel System
Always keep the workshop and lift clean (especially, from dust).
Always keep the tools clean (from oil or foreign materials).
Wear a clean vinyl apron to prevent the fuzz, dust and foreign materials from getting into fuel system.
Wash your hands and do not wear working gloves. 1.
2.
3.
Follow the below procedures before starting service works for fuel system.
If the problem is from HP pump, fuel supply line or injector, prepare the clean special tools and sealing
caps to perform the diagnosis for DI engine fuel system in this manual. At this point, thoroughly clean
the related area in engine compartment. 4.
Clean the engine compartment before starting service works.
Tool kit for high pressure lineTook kit for low pressure line
Page 319 of 600
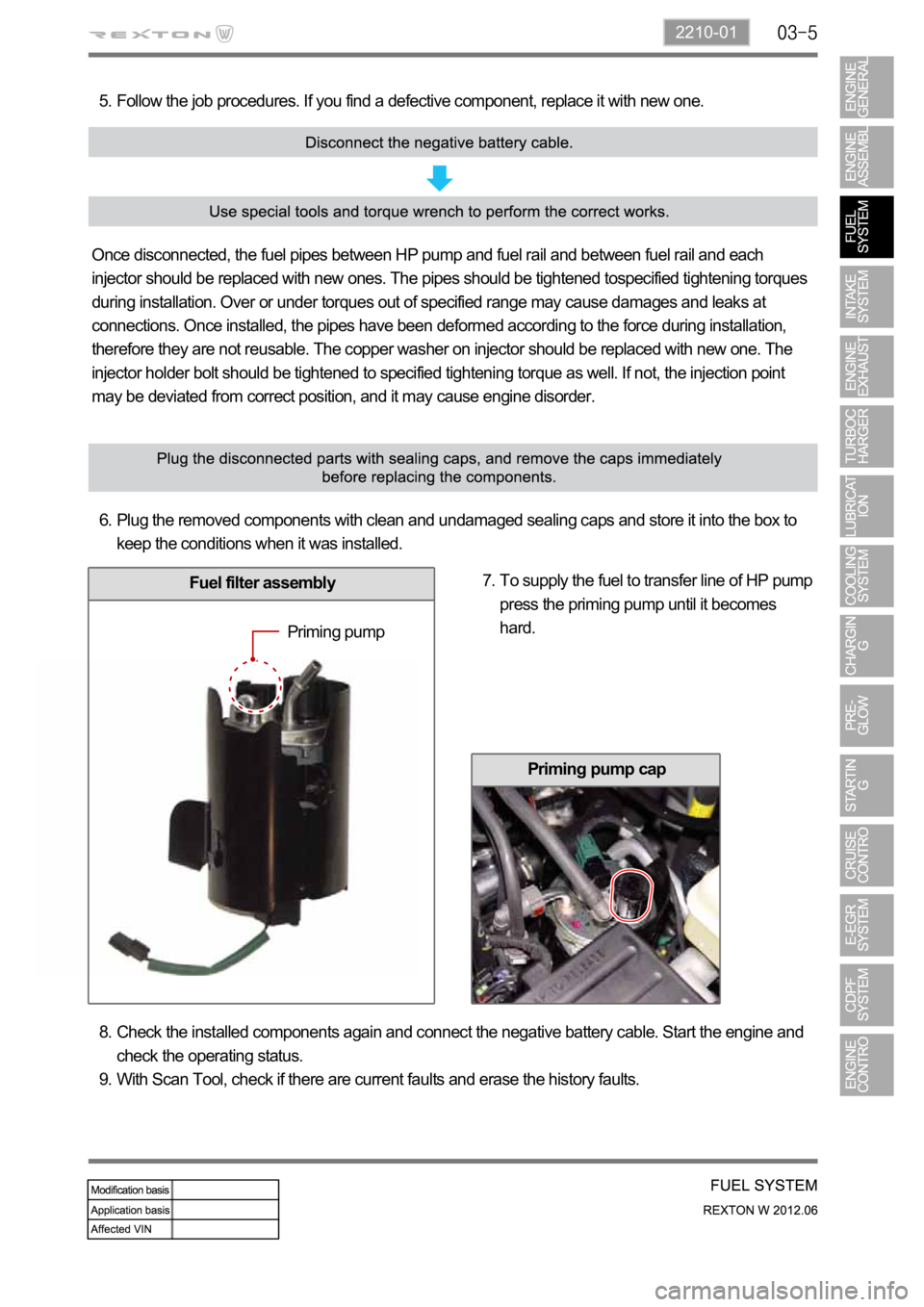
2210-01
Priming pump cap
Follow the job procedures. If you find a defective component, replace it with new one. 5.
Once disconnected, the fuel pipes between HP pump and fuel rail and between fuel rail and each
injector should be replaced with new ones. The pipes should be tightened tospecified tightening torques
during installation. Over or under torques out of specified range may cause damages and leaks at
connections. Once installed, the pipes have been deformed according to the force during installation,
therefore they are not reusable. The copper washer on injector should be replaced with new one. The
injector holder bolt should be tightened to specified tightening torque as well. If not, the injection point
may be deviated from correct position, and it may cause engine disorder.
Plug the removed components with clean and undamaged sealing caps and store it into the box to
keep the conditions when it was installed. 6.
To supply the fuel to transfer line of HP pump
press the priming pump until it becomes
hard. 7.
Priming pump
Fuel filter assembly
Check the installed components again and connect the negative battery cable. Start the engine and
check the operating status.
With Scan Tool, check if there are current faults and erase the history faults. 8.
9.
Page 322 of 600
(4) Loss of pump pressure/flow
Loss of HP pump pressure/flow
Faulty fuel supply line, or damaged or worn pump causes the lack of flow pressure and flow volume
Example:
Air in fuel supply line
Burned out and mechanical worn pump
-
-
-
-
Page 329 of 600
2210-01
Static test for backleak of injector
Disconnect the injector return hose and cover
the openings with caps shaped screw (included
in the special tool). 1.
Connect the hose of the container for
measuring backleak to the return nipple of the
injector.
(prevent air entry to the low pressure line) 2.
Disconnect the IMV connector of the high
pressure pump and then fuel pressure
sensor connector. 3.
The connector of the injector can be easily
contaminated. Always keep it clean.
Crank the engine 2 times for 5 seconds.
Check the time for flow if injector backleak and
confirm that it is within the specified range. 4.
5.
If the value is out of the specified range,
replace the injector.
SpecificationBelow 20 sec.
Page 331 of 600
2210-01
HP pump pressure test
Prepare a special tool for high pressure test
and clean it thoroughly to prevent foreign
materials from entering. 1.
Disconnect the high pressure fuel supply pipe
on the HP pump and install the close rail in the
tool kit. 2.
Connect the other end of the close rail to the
fuel rail for test. 3.
Disconnect the return hose for HP pump and
connect the clear hose and connect its the
other end to the return port of the fuel rail for
test. 4.
Connect the digital tester connector to the
sensor connector of the fuel rail for test.
Crank the engine 2 times for 5 seconds after
removing the IMV connector and fuel rail
pressure sensor connector.
Read the pressure value displayed on the
tester display is within the specified 5.
6.
7.
Specification1,050 bar or more