Page 362 of 600
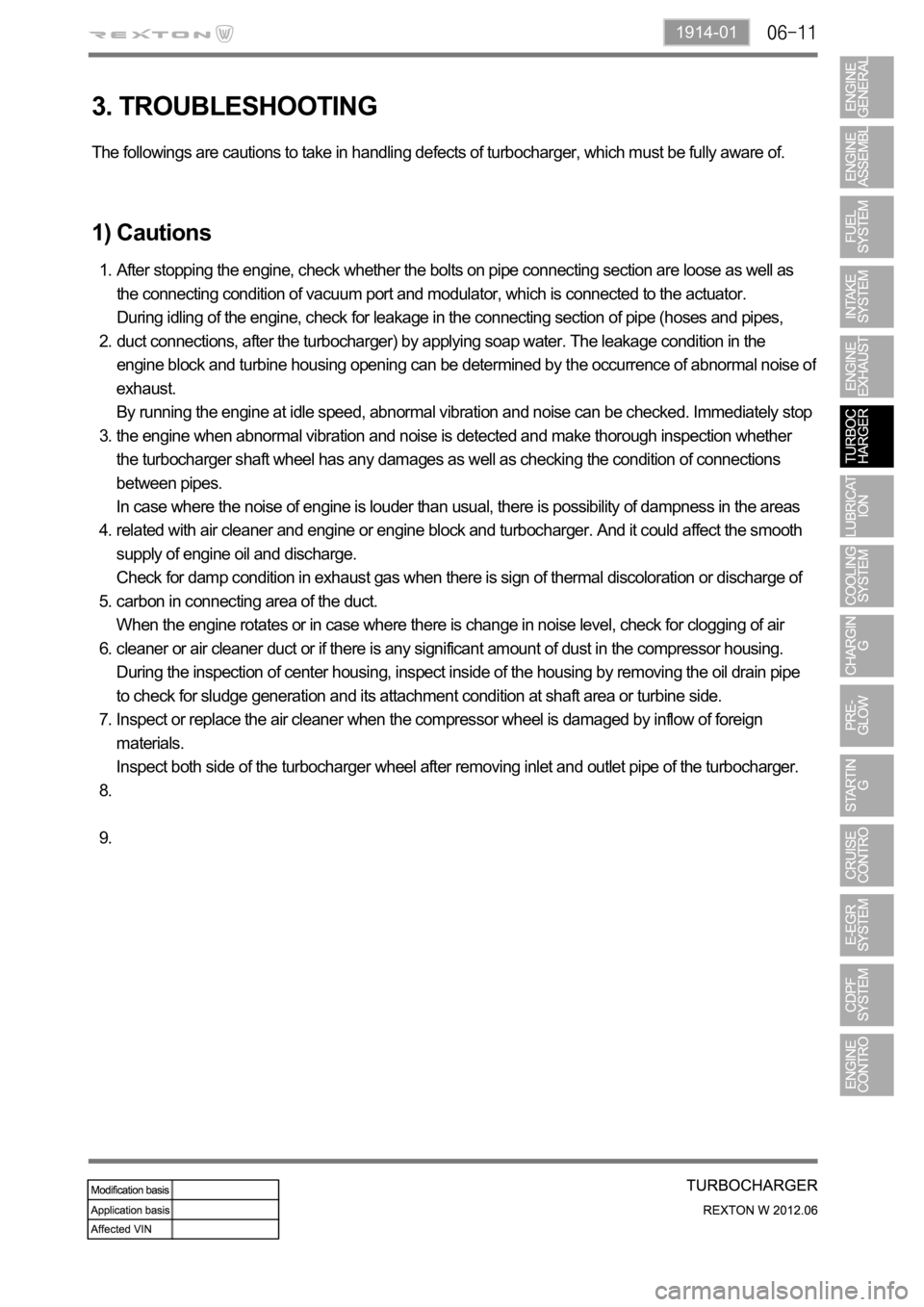
1914-01
3. TROUBLESHOOTING
The followings are cautions to take in handling defects of turbocharger, which must be fully aware of.
1) Cautions
After stopping the engine, check whether the bolts on pipe connecting section are loose as well as
the connecting condition of vacuum port and modulator, which is connected to the actuator.
During idling of the engine, check for leakage in the connecting section of pipe (hoses and pipes,
duct connections, after the turbocharger) by applying soap water. The leakage condition in the
engine block and turbine housing opening can be determined by the occurrence of abnormal noise o
f
exhaust.
By running the engine at idle speed, abnormal vibration and noise can be checked. Immediately stop
the engine when abnormal vibration and noise is detected and make thorough inspection whether
the turbocharger shaft wheel has any damages as well as checking the condition of connections
between pipes.
In case where the noise of engine is louder than usual, there is possibility of dampness in the areas
related with air cleaner and engine or engine block and turbocharger. And it could affect the smooth
supply of engine oil and discharge.
Check for damp condition in exhaust gas when there is sign of thermal discoloration or discharge of
carbon in connecting area of the duct.
When the engine rotates or in case where there is change in noise level, check for clogging of air
cleaner or air cleaner duct or if there is any significant amount of dust in the compressor housing.
During the inspection of center housing, inspect inside of the housing by removing the oil drain pipe
to check for sludge generation and its attachment condition at shaft area or turbine side.
Inspect or replace the air cleaner when the compressor wheel is damaged by inflow of foreign
materials.
Inspect both side of the turbocharger wheel after removing inlet and outlet pipe of the turbocharger. 1.
2.
3.
4.
5.
6.
7.
8.
9.
Page 372 of 600
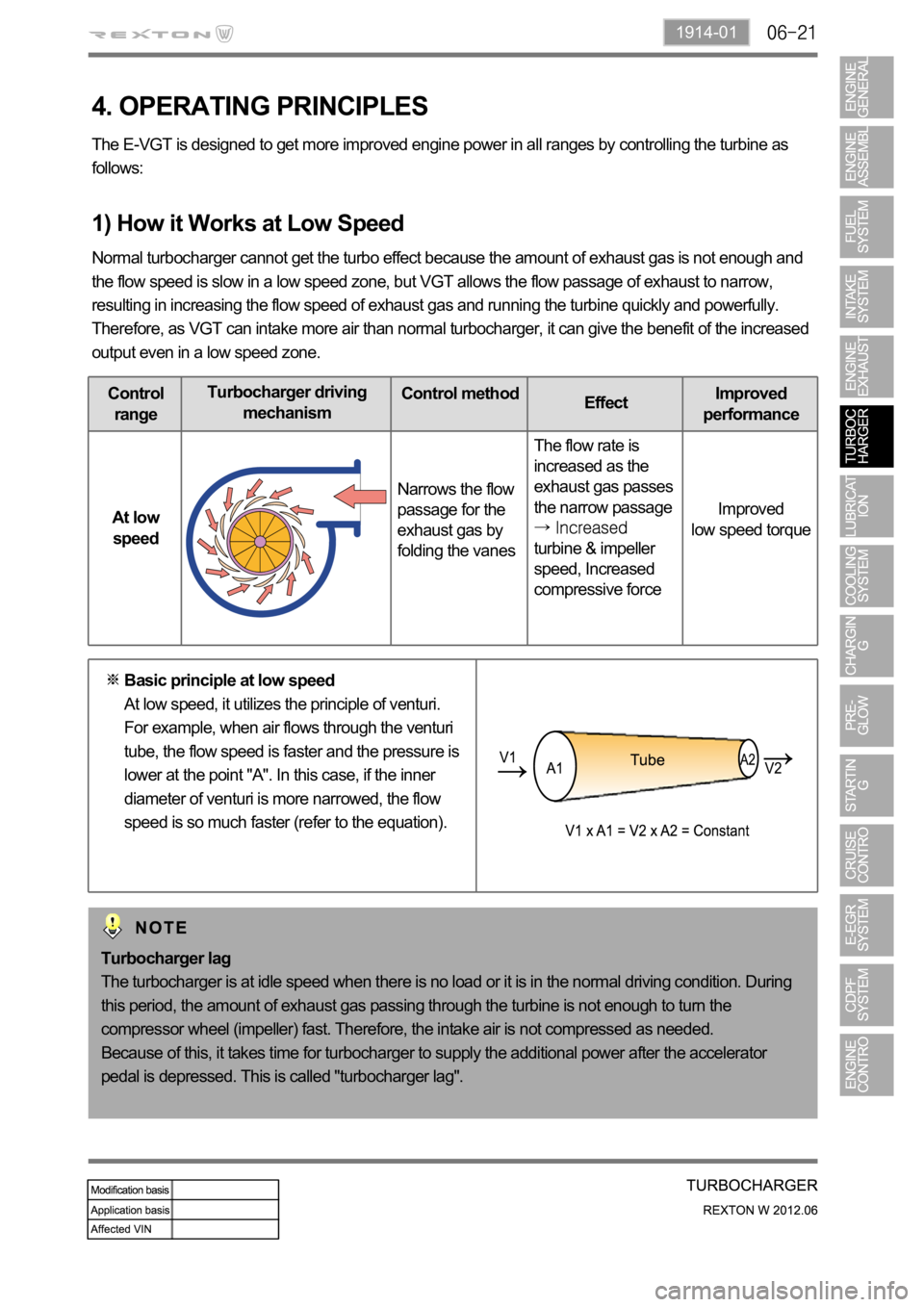
1914-01
Control
rangeTurbocharger driving
mechanismControl method
EffectImproved
performance
At low
speedNarrows the flow
passage for the
exhaust gas by
folding the vanesThe flow rate is
increased as the
exhaust gas passes
the narrow passage
turbine & impeller
speed, Increased
compressive forceImproved
low speed torque
4. OPERATING PRINCIPLES
The E-VGT is designed to get more improved engine power in all ranges by controlling the turbine as
follows:
1) How it Works at Low Speed
Normal turbocharger cannot get the turbo effect because the amount of exhaust gas is not enough and
the flow speed is slow in a low speed zone, but VGT allows the flow passage of exhaust to narrow,
resulting in increasing the flow speed of exhaust gas and running the turbine quickly and powerfully.
Therefore, as VGT can intake more air than normal turbocharger, it can give the benefit of the increased
output even in a low speed zone.
Turbocharger lag
The turbocharger is at idle speed when there is no load or it is in the normal driving condition. During
this period, the amount of exhaust gas passing through the turbine is not enough to turn the
compressor wheel (impeller) fast. Therefore, the intake air is not compressed as needed.
Because of this, it takes time for turbocharger to supply the additional power after the accelerator
pedal is depressed. This is called "turbocharger lag". Basic principle at low speed
At low speed, it utilizes the principle of venturi.
For example, when air flows through the venturi
tube, the flow speed is faster and the pressure is
lower at the point "A". In this case, if the inner
diameter of venturi is more narrowed, the flow
speed is so much faster (refer to the equation).
Page 397 of 600
1. OVERVIEW
The pre-heating system for D20DTR engine has the glow plug to the cylinder head (combustion
chamber), and improves the cold start performance and reduces the emission level.
The pre-heating resistor (air heater) is used to heat the intake air.
This enables the diesel fuel to be ignited in low temperature condition.
The ECU receives the information such as, engine rpm, coolant temperature, engine torque, etc.,
through CAN communication during pre-heating process; and the pre-heating control unit controls the
pre-heating, heating during cranking and post-heating by the PWM control.
Glow plug
Glow indicatorEngine ECU (D20DTR)
Glow plug control unit
(GCU)
Page 424 of 600
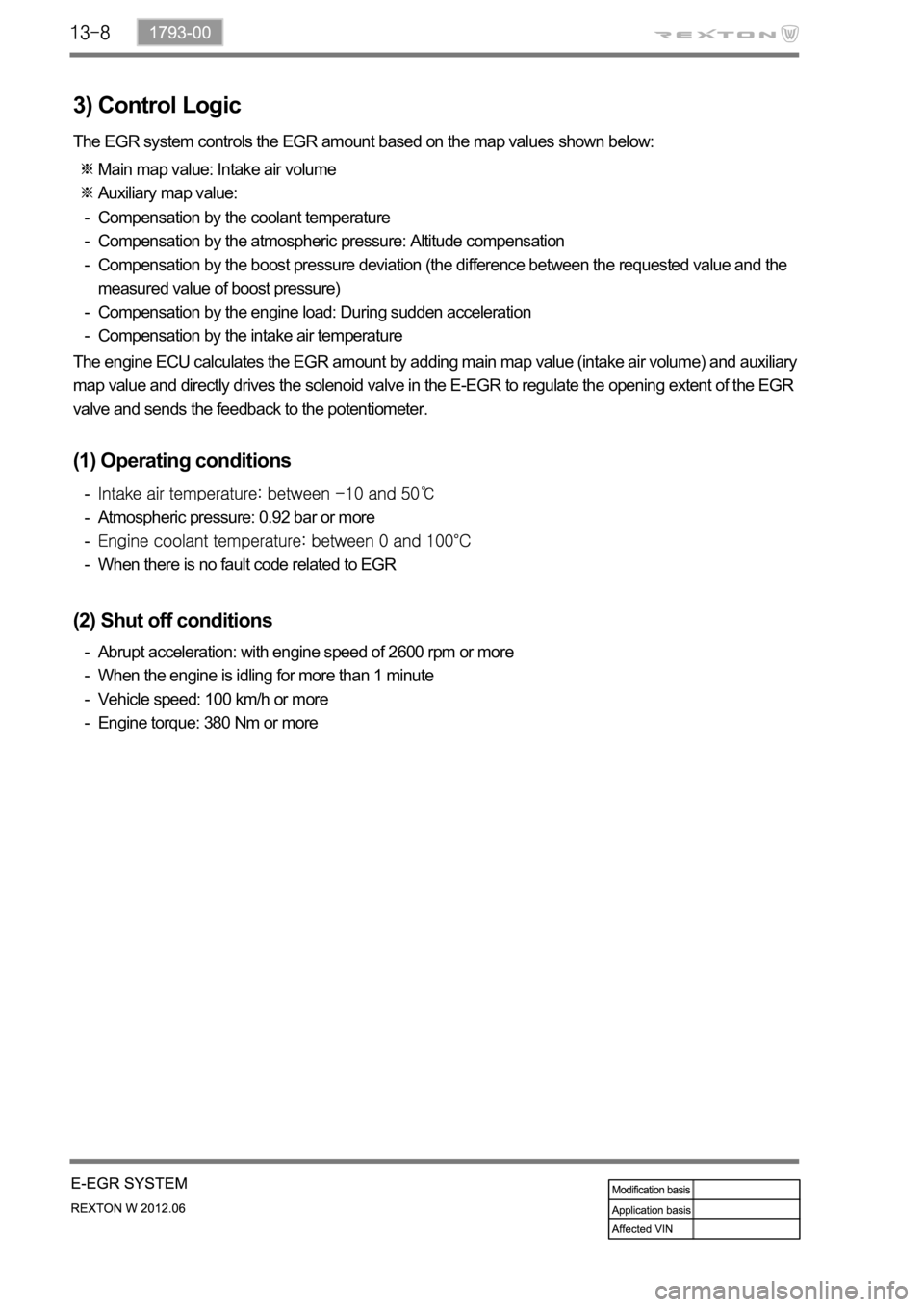
3) Control Logic
The EGR system controls the EGR amount based on the map values shown below:
Main map value: Intake air volume
Auxiliary map value:
Compensation by the coolant temperature
Compensation by the atmospheric pressure: Altitude compensation
Compensation by the boost pressure deviation (the difference between the requested value and the
measured value of boost pressure)
Compensation by the engine load: During sudden acceleration
Compensation by the intake air temperature -
-
-
-
-
The engine ECU calculates the EGR amount by adding main map value (intake air volume) and auxiliary
map value and directly drives the solenoid valve in the E-EGR to regulate the opening extent of the EGR
valve and sends the feedback to the potentiometer.
(1) Operating conditions
Atmospheric pressure: 0.92 bar or more
When there is no fault code related to EGR -
-
-
-
(2) Shut off conditions
Abrupt acceleration: with engine speed of 2600 rpm or more
When the engine is idling for more than 1 minute
Vehicle speed: 100 km/h or more
Engine torque: 380 Nm or more -
-
-
-
Page 427 of 600
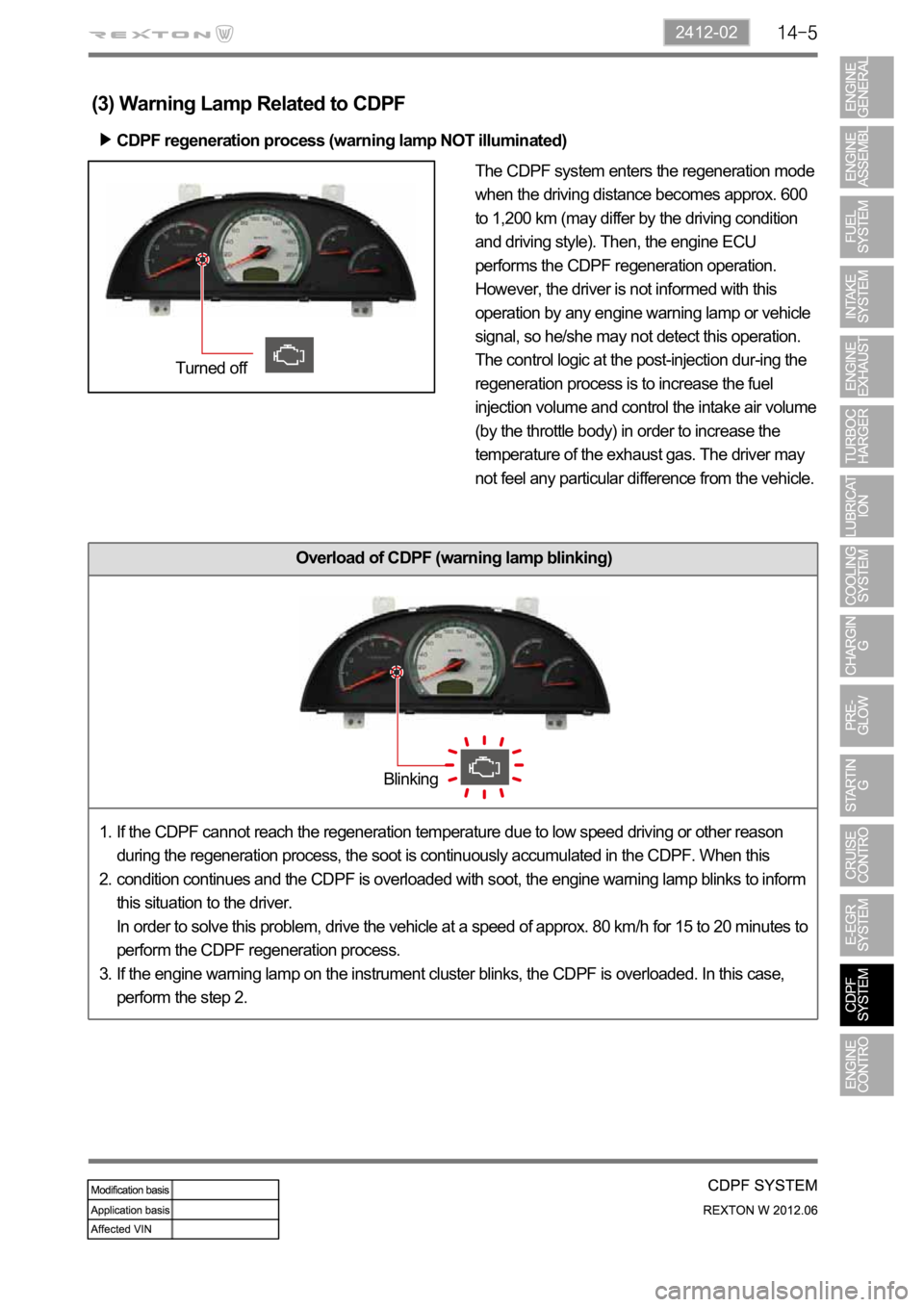
2412-02
The CDPF system enters the regeneration mode
when the driving distance becomes approx. 600
to 1,200 km (may differ by the driving condition
and driving style). Then, the engine ECU
performs the CDPF regeneration operation.
However, the driver is not informed with this
operation by any engine warning lamp or vehicle
signal, so he/she may not detect this operation.
The control logic at the post-injection dur-ing the
regeneration process is to increase the fuel
injection volume and control the intake air volume
(by the throttle body) in order to increase the
temperature of the exhaust gas. The driver may
not feel any particular difference from the vehicle.
Overload of CDPF (warning lamp blinking)
(3) Warning Lamp Related to CDPF
CDPF regeneration process (warning lamp NOT illuminated)
If the CDPF cannot reach the regeneration temperature due to low speed driving or other reason
during the regeneration process, the soot is continuously accumulated in the CDPF. When this
condition continues and the CDPF is overloaded with soot, the engine warning lamp blinks to inform
this situation to the driver.
In order to solve this problem, drive the vehicle at a speed of approx. 80 km/h for 15 to 20 minutes to
perform the CDPF regeneration process.
If the engine warning lamp on the instrument cluster blinks, the CDPF is overloaded. In this case,
perform the step 2. 1.
2.
3.
Turned off
Blinking
Page 441 of 600
0000-00
1. ENGINE DATA LIST
Data Unit Value
Coolant temperature
Intake air temperature
temperature or engine mode)
Idle speed rpm
Engine load % 18~25%
Mass air flow kg/h 16 to 25 kg/h
Throttle position angle
Engine torque Nm varies by engine conditions
Injection time ms 3 to 5ms
Battery voltage V 13.5 V to 14.1 V
Accelerator pedal position 1 V 0.4. to 4.8V
Accelerator pedal position 2 V 0.2 to 2.4 V
Throttle position 1 V 0.3 to 4.6 V
Throttle position 2 V 0.3 to 4.6 V
Oxygen sensor mV 0 to 5 V
A/C compressor switch 1=ON / 0=OFF -
Full load 1=ON / 0=OFF -
Gear selection (A/T) 1=ON / 0=OFF -
Knocking control 1=ON / 0=OFF -
Brake switch 1=ON / 0=OFF -
Cruise control 1=ON / 0=OFF -
Page 450 of 600
b. Pilot Injection
Injection before main injection. Consists of 1st and 2nd pilot injection, and Pre-injection
Inject a small amount of fuel before main injection to make the combustion smooth. Also, called as
preliminary injection or ignition injection. This helps to reduce Nox, engine noise and vibration, and to
stabilize the idling.
The injected fuel volume is changed and stopped according to the coolant temperature and intake air
volume.
Pilot injection is much earlier than main injection due to higher engine rpm
Too small injection volume (insufficient injection pressure, insufficient fuel injection volume in main
injection, engine braking)
System failure (fuel system, engine control system) -
-
-
Pilot injection
Main injection
Combustion pressure with pilot injection
Combustion pressure without pilot injection 1.
2.
1a.
2b. Stop conditions
Combustion pressure characteristic curve for pilot injection
Page 453 of 600
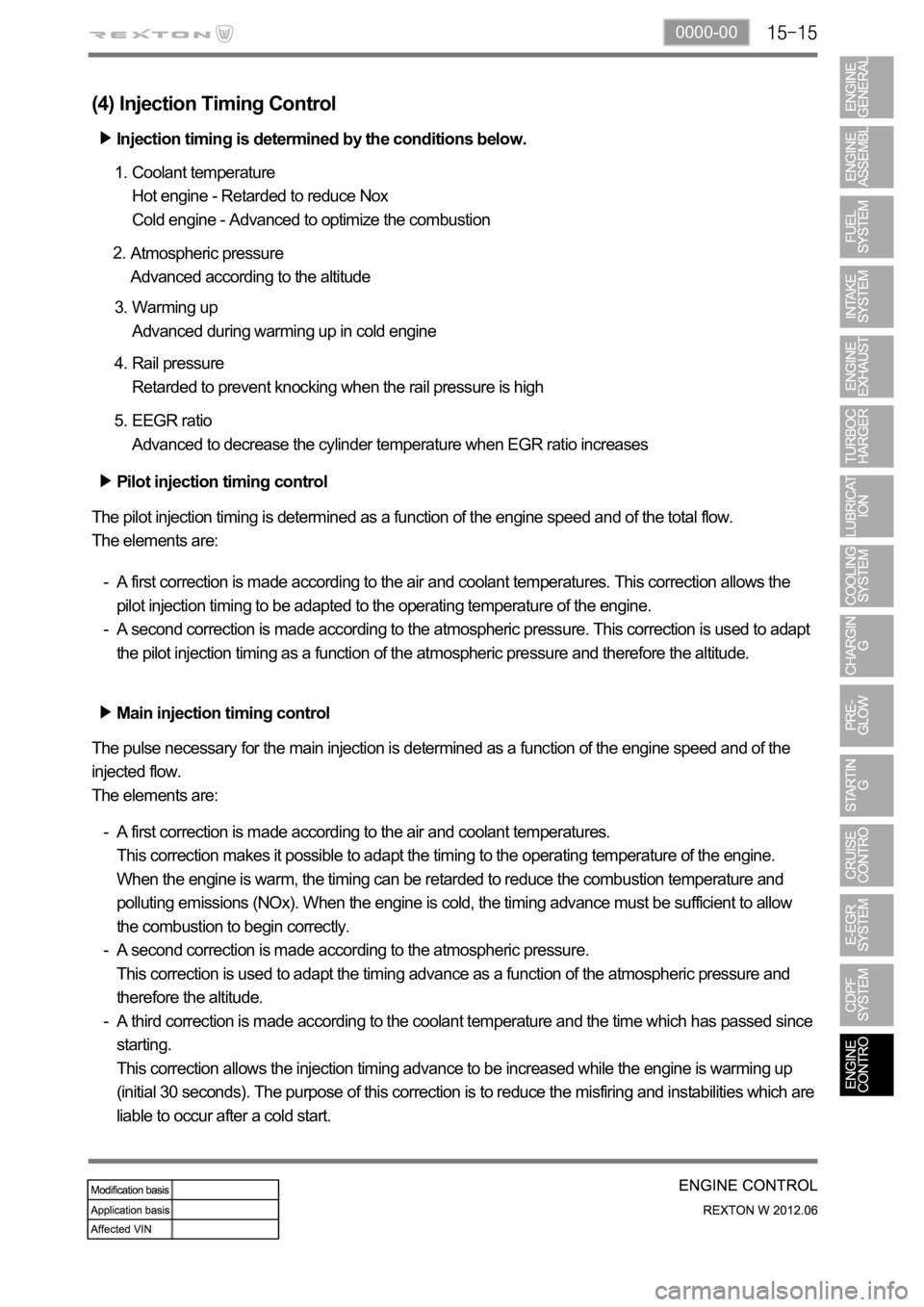
0000-00
Pilot injection timing control
The pilot injection timing is determined as a function of the engine speed and of the total flow.
The elements are:
A first correction is made according to the air and coolant temperatures. This correction allows the
pilot injection timing to be adapted to the operating temperature of the engine.
A second correction is made according to the atmospheric pressure. This correction is used to adapt
the pilot injection timing as a function of the atmospheric pressure and therefore the altitude. -
-
(4) Injection Timing Control
Injection timing is determined by the conditions below.
Coolant temperature
Hot engine - Retarded to reduce Nox
Cold engine - Advanced to optimize the combustion 1.
Atmospheric pressure
Advanced according to the altitude 2.
Warming up
Advanced during warming up in cold engine 3.
Rail pressure
Retarded to prevent knocking when the rail pressure is high 4.
EEGR ratio
Advanced to decrease the cylinder temperature when EGR ratio increases 5.
Main injection timing control
The pulse necessary for the main injection is determined as a function of the engine speed and of the
injected flow.
The elements are:
A first correction is made according to the air and coolant temperatures.
This correction makes it possible to adapt the timing to the operating temperature of the engine.
When the engine is warm, the timing can be retarded to reduce the combustion temperature and
polluting emissions (NOx). When the engine is cold, the timing advance must be sufficient to allow
the combustion to begin correctly.
A second correction is made according to the atmospheric pressure.
This correction is used to adapt the timing advance as a function of the atmospheric pressure and
therefore the altitude.
A third correction is made according to the coolant temperature and the time which has passed since
starting.
This correction allows the injection timing advance to be increased while the engine is warming up
(initial 30 seconds). The purpose of this correction is to reduce the misfiring and instabilities which are
liable to occur after a cold start. -
-
-