Page 417 of 431
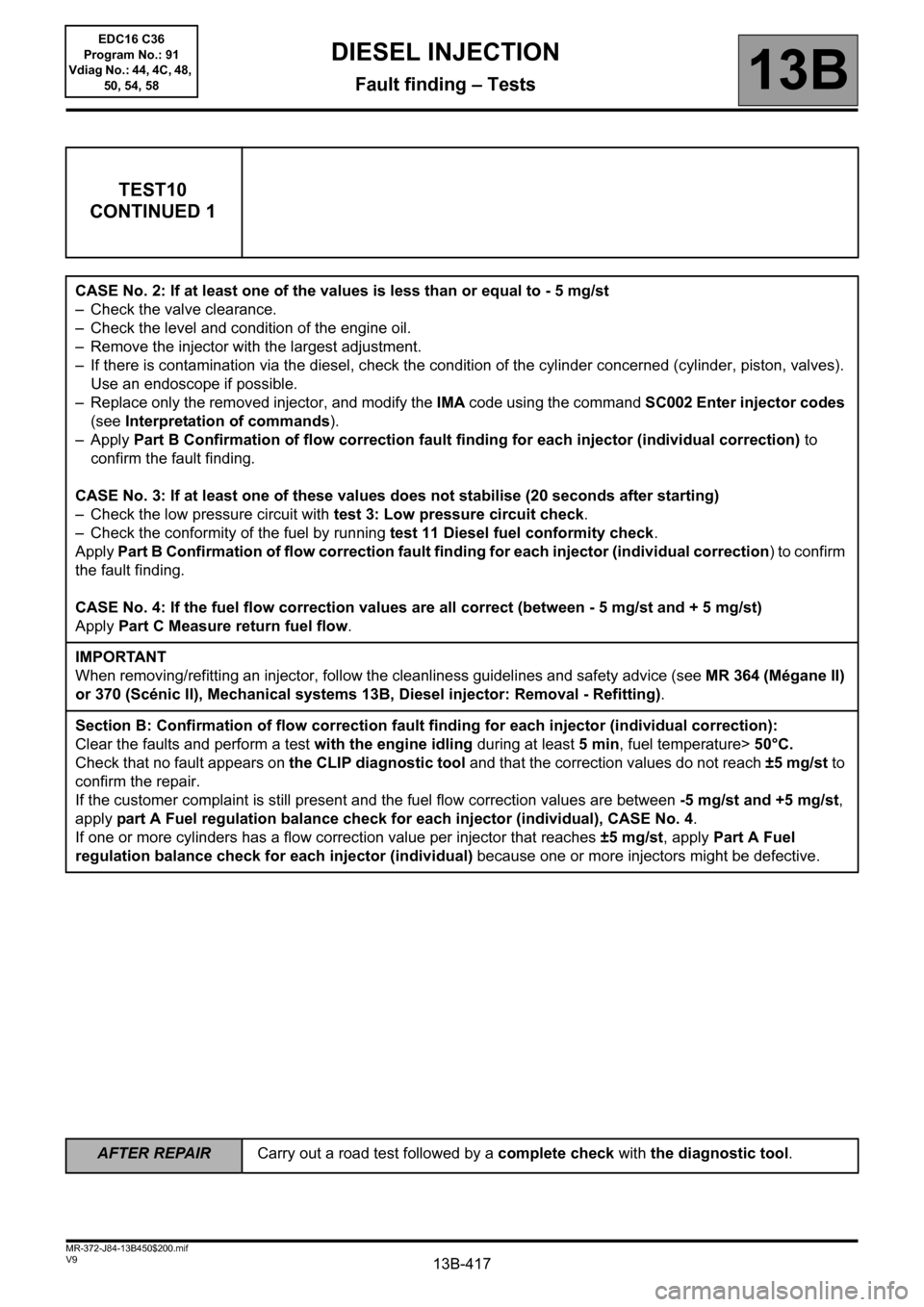
13B-417V9 MR-372-J84-13B450$200.mif
DIESEL INJECTION
Fault finding – Tests13B
TEST10
CONTINUED 1
CASE No. 2: If at least one of the values is less than or equal to - 5 mg/st
– Check the valve clearance.
– Check the level and condition of the engine oil.
– Remove the injector with the largest adjustment.
– If there is contamination via the diesel, check the condition of the cylinder concerned (cylinder, piston, valves).
Use an endoscope if possible.
– Replace only the removed injector, and modify the IMA code using the command SC002 Enter injector codes
(see Interpretation of commands).
–Apply Part B Confirmation of flow correction fault finding for each injector (individual correction) to
confirm the fault finding.
CASE No. 3: If at least one of these values does not stabilise (20 seconds after starting)
– Check the low pressure circuit with test 3: Low pressure circuit check.
– Check the conformity of the fuel by running test 11 Diesel fuel conformity check.
Apply Part B Confirmation of flow correction fault finding for each injector (individual correction) to confirm
the fault finding.
CASE No. 4: If the fuel flow correction values are all correct (between - 5 mg/st and + 5 mg/st)
Apply Part C Measure return fuel flow.
IMPORTANT
When removing/refitting an injector, follow the cleanliness guidelines and safety advice (see MR 364 (Mégane II)
or 370 (Scénic II), Mechanical systems 13B, Diesel injector: Removal - Refitting).
Section B: Confirmation of flow correction fault finding for each injector (individual correction):
Clear the faults and perform a test with the engine idling during at least 5 min, fuel temperature> 50°C.
Check that no fault appears on the CLIP diagnostic tool and that the correction values do not reach ±5 mg/st to
confirm the repair.
If the customer complaint is still present and the fuel flow correction values are between -5 mg/st and +5 mg/st,
apply part A Fuel regulation balance check for each injector (individual), CASE No. 4.
If one or more cylinders has a flow correction value per injector that reaches ±5 mg/st, apply Part A Fuel
regulation balance check for each injector (individual) because one or more injectors might be defective.
AFTER REPAIRCarry out a road test followed by a complete check with the diagnostic tool.
EDC16 C36
Program No.: 91
Vdiag No.: 44, 4C, 48,
50, 54, 58
Page 418 of 431
13B-418V9 MR-372-J84-13B450$200.mif
DIESEL INJECTION
Fault finding – Tests13B
TEST10
CONTINUED 2
Part C: Measuring fuel return flow
1. Fitting the tool:
Carry out this part only if the PR063 Fuel temperature is greater than 50C (see step 2 of part C of this test).
Remove the engine undertray
Disconnect the entire fuel return pipe in accordance with the following procedure (do not remove the clips):
– press the clip,
– Pull vertically the end piece of the fuel return pipe (see arrow the illustration).
IMPORTANT
The end piece is fragile. Be careful not to break it by pulling it too hard. Replace all removed clips
AFTER REPAIRCarry out a road test followed by a complete check with the diagnostic tool.
EDC16 C36
Program No.: 91
Vdiag No.: 44, 4C, 48,
50, 54, 58
Page 423 of 431
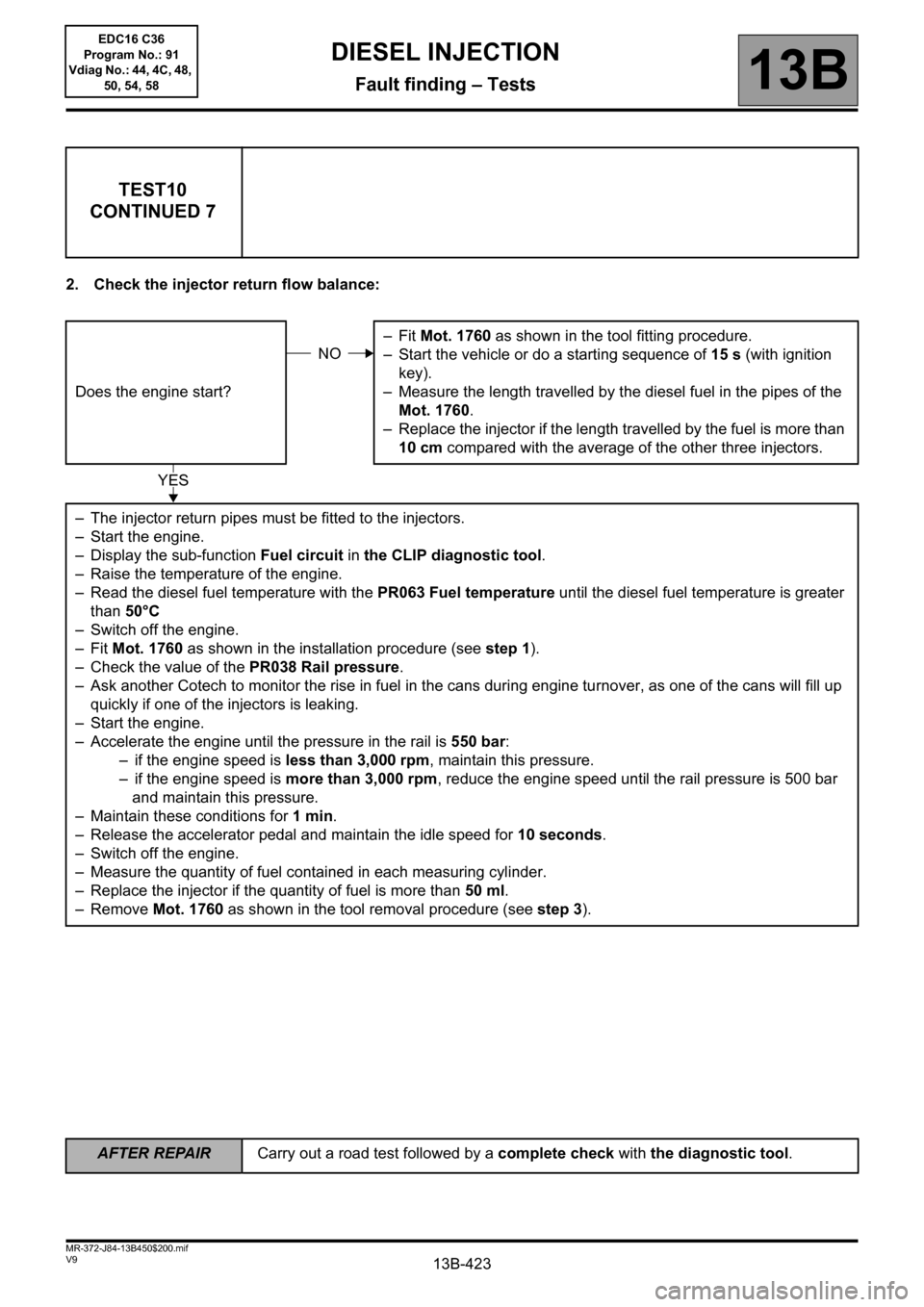
13B-423V9 MR-372-J84-13B450$200.mif
DIESEL INJECTION
Fault finding – Tests13B
2. Check the injector return flow balance:
TEST10
CONTINUED 7
Does the engine start?–Fit Mot. 1760 as shown in the tool fitting procedure.
– Start the vehicle or do a starting sequence of 15 s (with ignition
key).
– Measure the length travelled by the diesel fuel in the pipes of the
Mot. 1760.
– Replace the injector if the length travelled by the fuel is more than
10 cm compared with the average of the other three injectors.
– The injector return pipes must be fitted to the injectors.
– Start the engine.
– Display the sub-function Fuel circuit in the CLIP diagnostic tool.
– Raise the temperature of the engine.
– Read the diesel fuel temperature with the PR063 Fuel temperature until the diesel fuel temperature is greater
than 50°C
– Switch off the engine.
–Fit Mot. 1760 as shown in the installation procedure (see step 1).
– Check the value of the PR038 Rail pressure.
– Ask another Cotech to monitor the rise in fuel in the cans during engine turnover, as one of the cans will fill up
quickly if one of the injectors is leaking.
– Start the engine.
– Accelerate the engine until the pressure in the rail is 550 bar:
– if the engine speed is less than 3,000 rpm, maintain this pressure.
– if the engine speed is more than 3,000 rpm, reduce the engine speed until the rail pressure is 500 bar
and maintain this pressure.
– Maintain these conditions for 1min.
– Release the accelerator pedal and maintain the idle speed for 10 seconds.
– Switch off the engine.
– Measure the quantity of fuel contained in each measuring cylinder.
– Replace the injector if the quantity of fuel is more than 50 ml.
– Remove Mot. 1760 as shown in the tool removal procedure (see step 3).
NO
YES
AFTER REPAIRCarry out a road test followed by a complete check with the diagnostic tool.
EDC16 C36
Program No.: 91
Vdiag No.: 44, 4C, 48,
50, 54, 58
Page 429 of 431
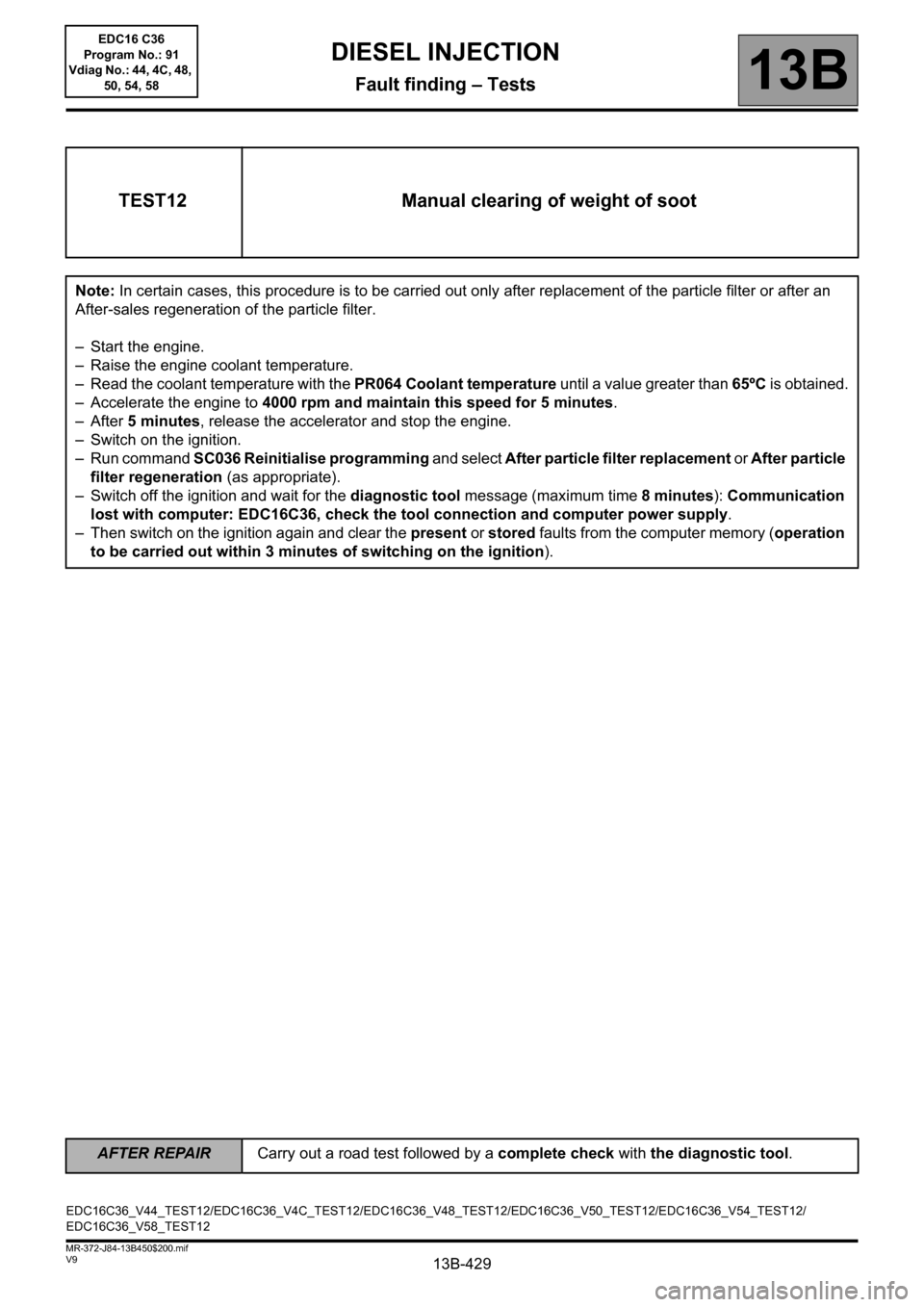
13B-429V9 MR-372-J84-13B450$200.mif
DIESEL INJECTION
Fault finding – Tests13B
TEST12 Manual clearing of weight of soot
Note: In certain cases, this procedure is to be carried out only after replacement of the particle filter or after an
After-sales regeneration of the particle filter.
– Start the engine.
– Raise the engine coolant temperature.
– Read the coolant temperature with the PR064 Coolant temperature until a value greater than 65ºC is obtained.
– Accelerate the engine to 4000 rpm and maintain this speed for 5 minutes.
–After 5 minutes, release the accelerator and stop the engine.
– Switch on the ignition.
– Run command SC036 Reinitialise programming and select After particle filter replacement or After particle
filter regeneration (as appropriate).
– Switch off the ignition and wait for the diagnostic tool message (maximum time 8 minutes): Communication
lost with computer: EDC16C36, check the tool connection and computer power supply.
– Then switch on the ignition again and clear the present or stored faults from the computer memory (operation
to be carried out within 3 minutes of switching on the ignition).
EDC16C36_V44_TEST12/EDC16C36_V4C_TEST12/EDC16C36_V48_TEST12/EDC16C36_V50_TEST12/EDC16C36_V54_TEST12/
EDC16C36_V58_TEST12EDC16 C36
Program No.: 91
Vdiag No.: 44, 4C, 48,
50, 54, 58
AFTER REPAIRCarry out a road test followed by a complete check with the diagnostic tool.
Page 430 of 431
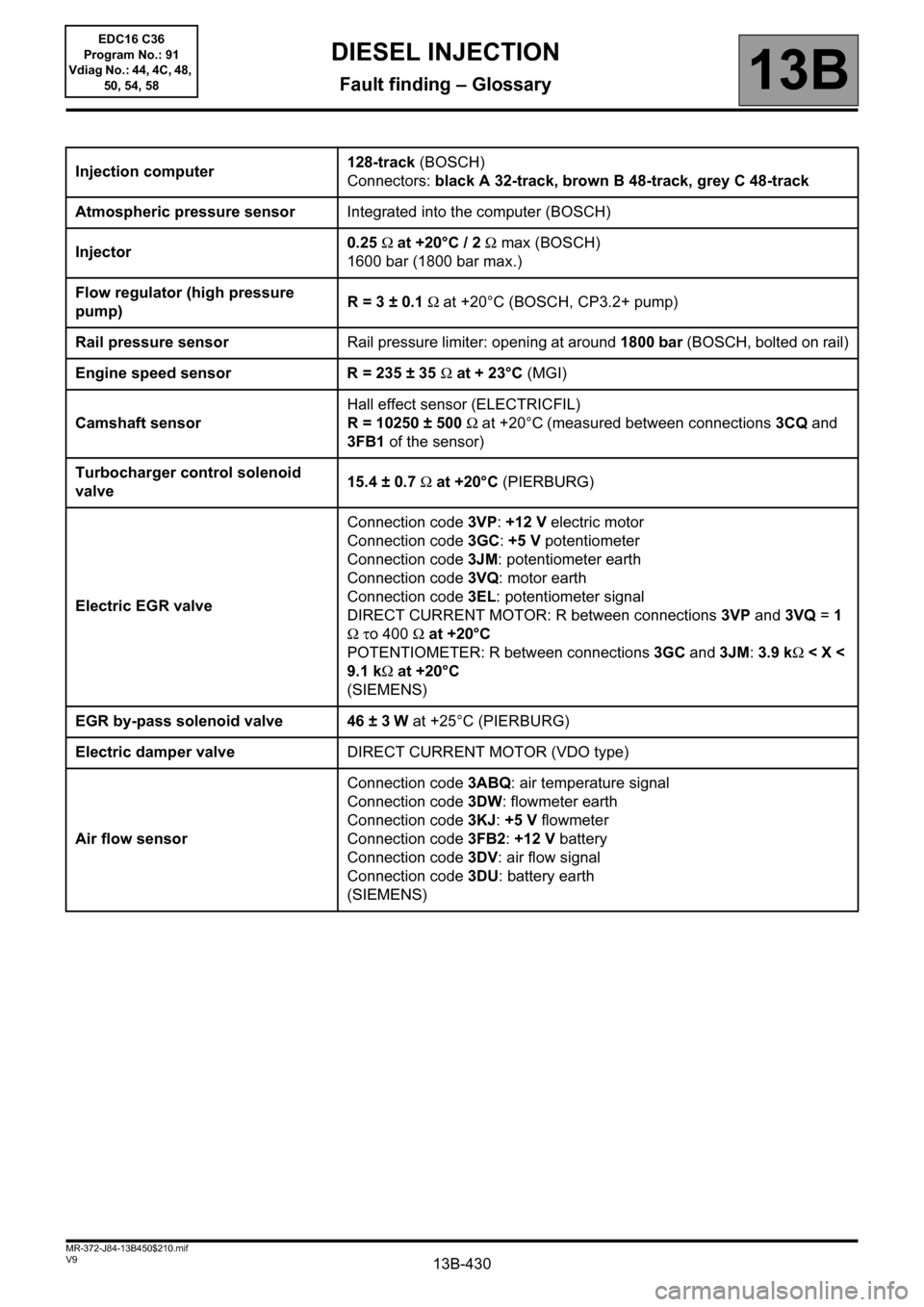
13B-430V9 MR-372-J84-13B450$210.mif
13B
EDC16 C36
Program No.: 91
Vdiag No.: 44, 4C, 48,
50, 54, 58
Injection computer128-track (BOSCH)
Connectors: black A 32-track, brown B 48-track, grey C 48-track
Atmospheric pressure sensorIntegrated into the computer (BOSCH)
Injector0.25 Ω at +20°C / 2 Ω max (BOSCH)
1600 bar (1800 bar max.)
Flow regulator (high pressure
pump)R = 3 ± 0.1 Ω at +20°C (BOSCH, CP3.2+ pump)
Rail pressure sensorRail pressure limiter: opening at around 1800 bar (BOSCH, bolted on rail)
Engine speed sensor R = 235 ± 35 Ω at + 23°C (MGI)
Camshaft sensorHall effect sensor (ELECTRICFIL)
R = 10250 ± 500 Ω at +20°C (measured between connections 3CQ and
3FB1 of the sensor)
Turbocharger control solenoid
valve15.4 ± 0.7 Ω at +20°C (PIERBURG)
Electric EGR valveConnection code 3VP: +12 V electric motor
Connection code 3GC: +5 V potentiometer
Connection code 3JM: potentiometer earth
Connection code 3VQ: motor earth
Connection code 3EL: potentiometer signal
DIRECT CURRENT MOTOR: R between connections 3VP and 3VQ = 1
Ω τo 400 Ω at +20°C
POTENTIOMETER: R between connections 3GC and 3JM: 3.9 kΩ < X <
9.1 kΩ at +20°C
(SIEMENS)
EGR by-pass solenoid valve 46 ± 3 W at +25°C (PIERBURG)
Electric damper valveDIRECT CURRENT MOTOR (VDO type)
Air flow sensorConnection code 3ABQ: air temperature signal
Connection code
3DW: flowmeter earth
Connection code 3KJ: +5 V flowmeter
Connection code 3FB2: +12 V battery
Connection code 3DV: air flow signal
Connection code 3DU: battery earth
(SIEMENS)
DIESEL INJECTION
Fault finding – Glossary