Page 20 of 431
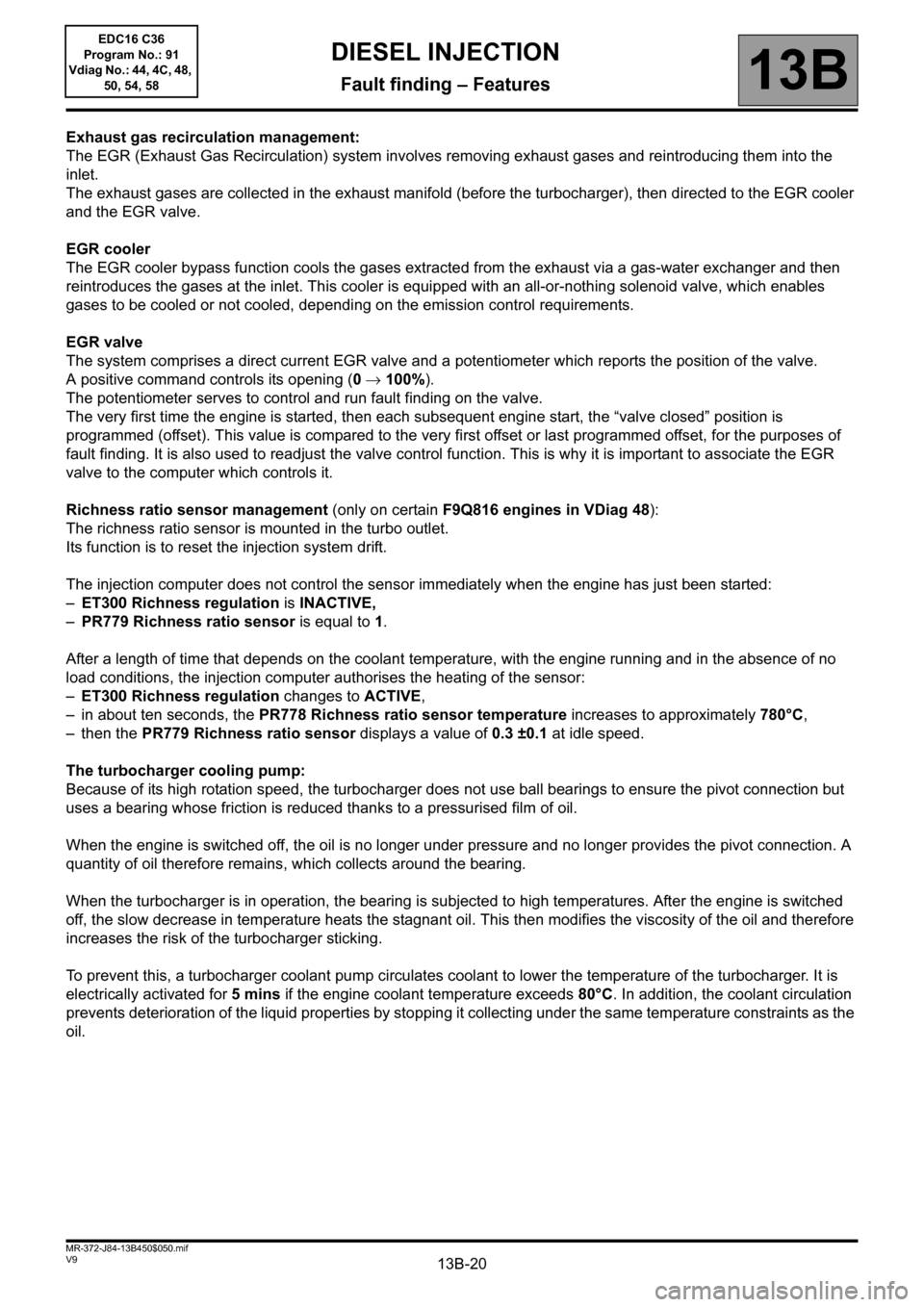
13B-20V9 MR-372-J84-13B450$050.mif
DIESEL INJECTION
Fault finding – Features13B
EDC16 C36
Program No.: 91
Vdiag No.: 44, 4C, 48,
50, 54, 58
Exhaust gas recirculation management:
The EGR (Exhaust Gas Recirculation) system involves removing exhaust gases and reintroducing them into the
inlet.
The exhaust gases are collected in the exhaust manifold (before the turbocharger), then directed to the EGR cooler
and the EGR valve.
EGR cooler
The EGR cooler bypass function cools the gases extracted from the exhaust via a gas-water exchanger and then
reintroduces the gases at the inlet. This cooler is equipped with an all-or-nothing solenoid valve, which enables
gases to be cooled or not cooled, depending on the emission control requirements.
EGR valve
The system comprises a direct current EGR valve and a potentiometer which reports the position of the valve.
A positive command controls its opening (0 → 100%).
The potentiometer serves to control and run fault finding on the valve.
The very first time the engine is started, then each subsequent engine start, the “valve closed” position is
programmed (offset). This value is compared to the very first offset or last programmed offset, for the purposes of
fault finding. It is also used to readjust the valve control function. This is why it is important to associate the EGR
valve to the computer which controls it.
Richness ratio sensor management (only on certain F9Q816 engines in VDiag 48):
The richness ratio sensor is mounted in the turbo outlet.
Its function is to reset the injection system drift.
The injection computer does not control the sensor immediately when the engine has just been started:
–ET300 Richness regulation is INACTIVE,
–PR779 Richness ratio sensor is equal to 1.
After a length of time that depends on the coolant temperature, with the engine running and in the absence of no
load conditions, the injection computer authorises the heating of the sensor:
–ET300 Richness regulation changes to ACTIVE,
– in about ten seconds, the PR778 Richness ratio sensor temperature increases to approximately 780°C,
– then the PR779 Richness ratio sensor displays a value of 0.3 ±0.1 at idle speed.
The turbocharger cooling pump:
Because of its high rotation speed, the turbocharger does not use ball bearings to ensure the pivot connection but
uses a bearing whose friction is reduced thanks to a pressurised film of oil.
When the engine is switched off, the oil is no longer under pressure and no longer provides the pivot connection. A
quantity of oil therefore remains, which collects around the bearing.
When the turbocharger is in operation, the bearing is subjected to high temperatures. After the engine is switched
off, the slow decrease in temperature heats the stagnant oil. This then modifies the viscosity of the oil and therefore
increases the risk of the turbocharger sticking.
To prevent this, a turbocharger coolant pump circulates coolant to lower the temperature of the turbocharger. It is
electrically activated for 5 mins if the engine coolant temperature exceeds 80°C. In addition, the coolant circulation
prevents deterioration of the liquid properties by stopping it collecting under the same temperature constraints as the
oil.
Page 367 of 431
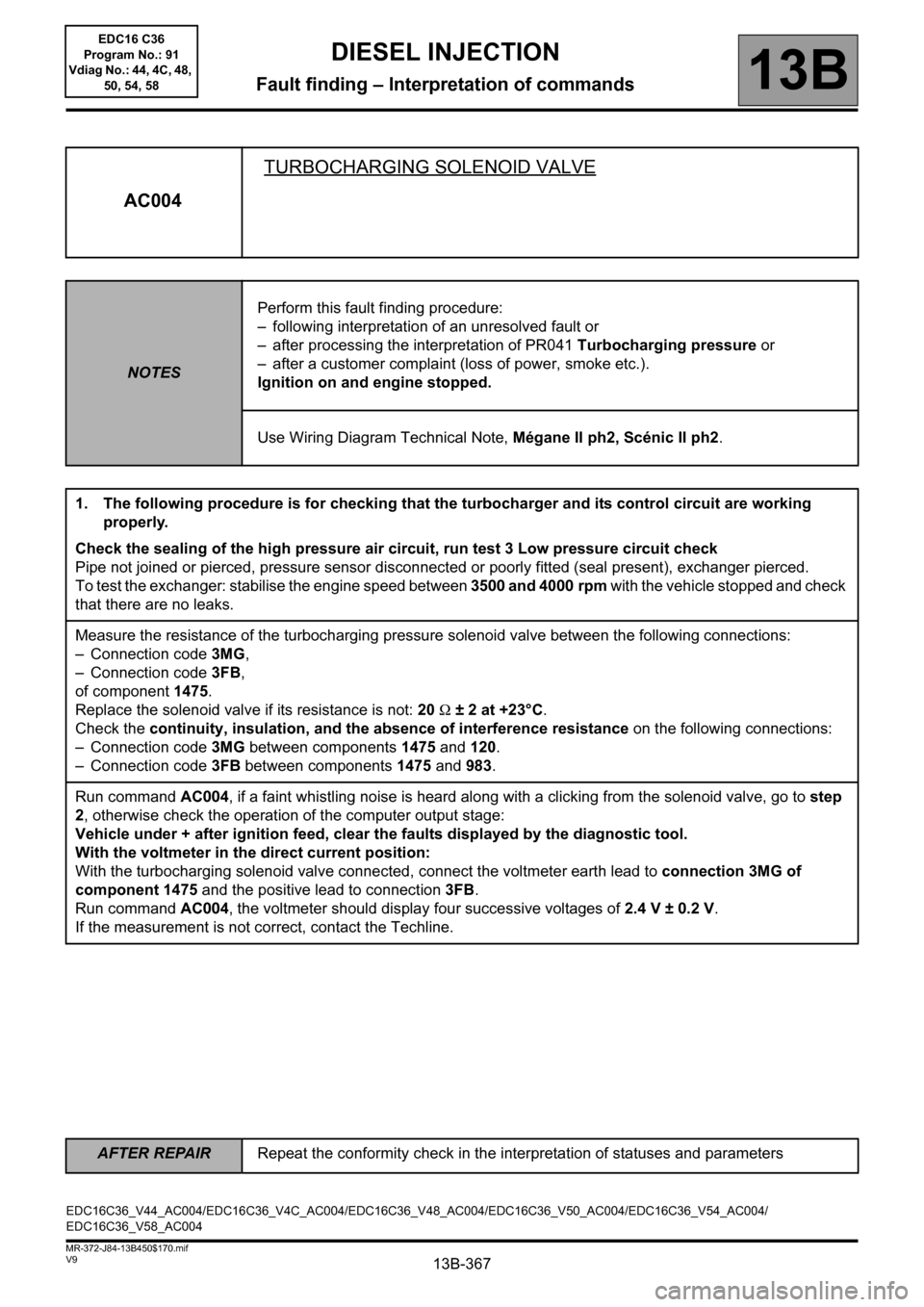
13B-367
AFTER REPAIRRepeat the conformity check in the interpretation of statuses and parameters
V9 MR-372-J84-13B450$170.mif
DIESEL INJECTION
Fault finding – Interpretation of commands13B
AC004TURBOCHARGING SOLENOID VALVE
NOTESPerform this fault finding procedure:
– following interpretation of an unresolved fault or
– after processing the interpretation of PR041 Turbocharging pressure or
– after a customer complaint (loss of power, smoke etc.).
Ignition on and engine stopped.
Use Wiring Diagram Technical Note, Mégane II ph2, Scénic II ph2.
1. The following procedure is for checking that the turbocharger and its control circuit are working
properly.
Check the sealing of the high pressure air circuit, run test 3 Low pressure circuit check
Pipe not joined or pierced, pressure sensor disconnected or poorly fitted (seal present), exchanger pierced.
To test the exchanger: stabilise the engine speed between 3500 and 4000 rpm with the vehicle stopped and check
that there are no leaks.
Measure the resistance of the turbocharging pressure solenoid valve between the following connections:
– Connection code 3MG,
– Connection code 3FB,
of component 1475.
Replace the solenoid valve if its resistance is not: 20 Ω ± 2 at +23°C.
Check the continuity, insulation, and the absence of interference resistance on the following connections:
– Connection code 3MG between components 1475 and 120.
– Connection code 3FB between components 1475 and 983.
Run command AC004, if a faint whistling noise is heard along with a clicking from the solenoid valve, go to step
2, otherwise check the operation of the computer output stage:
Vehicle under + after ignition feed, clear the faults displayed by the diagnostic tool.
With the voltmeter in the direct current position:
With the turbocharging solenoid valve connected, connect the voltmeter earth lead to connection 3MG of
component 1475 and the positive lead to connection3FB.
Run command AC004, the voltmeter should display four successive voltages of 2.4 V ± 0.2 V.
If the measurement is not correct, contact the Techline.
EDC16C36_V44_AC004/EDC16C36_V4C_AC004/EDC16C36_V48_AC004/EDC16C36_V50_AC004/EDC16C36_V54_AC004/
EDC16C36_V58_AC004EDC16 C36
Program No.: 91
Vdiag No.: 44, 4C, 48,
50, 54, 58
Page 411 of 431
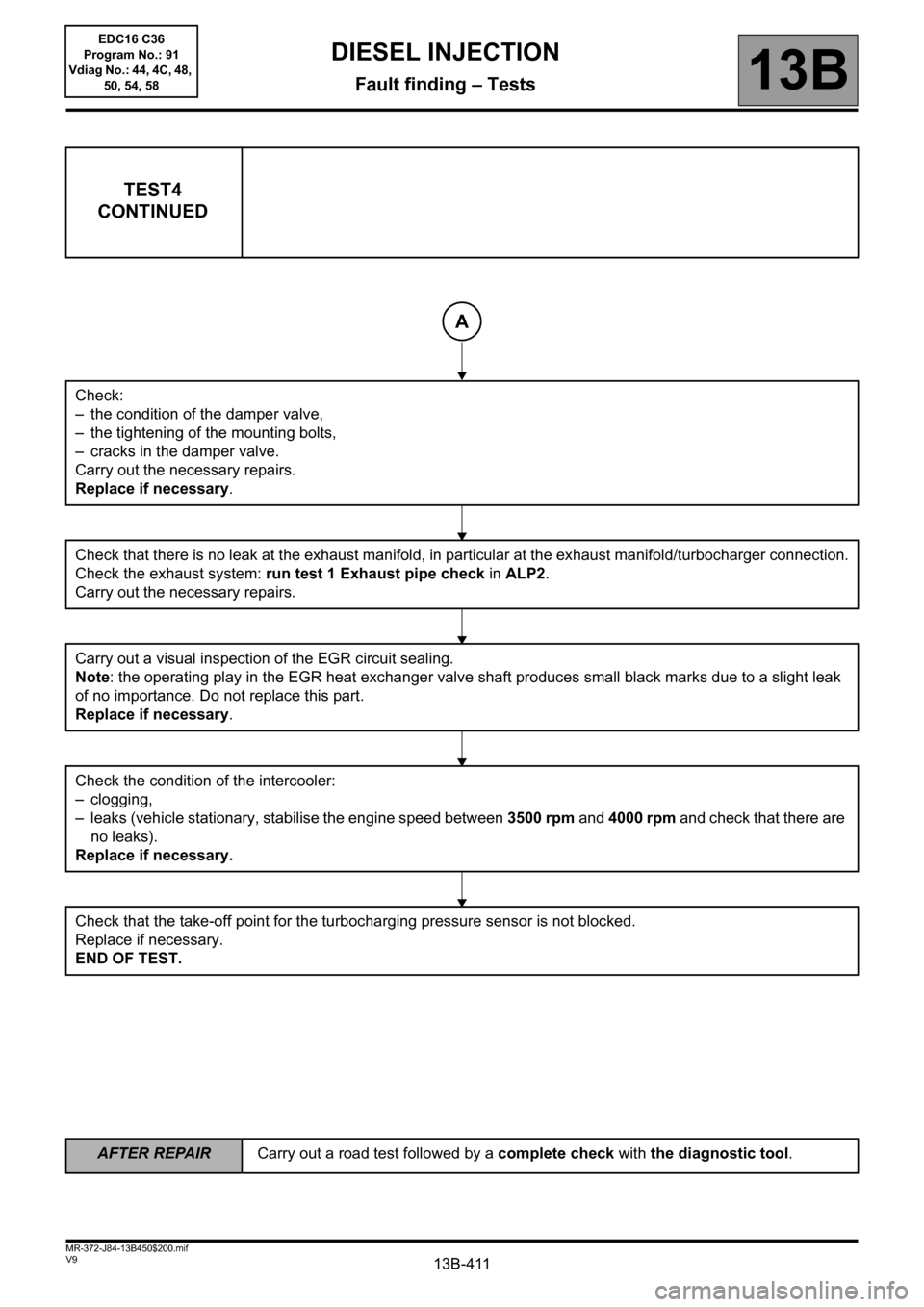
13B-411V9 MR-372-J84-13B450$200.mif
DIESEL INJECTION
Fault finding – Tests13B
TEST4
CONTINUED
Check:
– the condition of the damper valve,
– the tightening of the mounting bolts,
– cracks in the damper valve.
Carry out the necessary repairs.
Replace if necessary.
Check that there is no leak at the exhaust manifold, in particular at the exhaust manifold/turbocharger connection.
Check the exhaust system: run test 1 Exhaust pipe check in ALP2.
Carry out the necessary repairs.
Carry out a visual inspection of the EGR circuit sealing.
Note: the operating play in the EGR heat exchanger valve shaft produces small black marks due to a slight leak
of no importance. Do not replace this part.
Replace if necessary.
Check the condition of the intercooler:
– clogging,
– leaks (vehicle stationary, stabilise the engine speed between 3500 rpm and 4000 rpm and check that there are
no leaks).
Replace if necessary.
Check that the take-off point for the turbocharging pressure sensor is not blocked.
Replace if necessary.
END OF TEST.
A
AFTER REPAIRCarry out a road test followed by a complete check with the diagnostic tool.
EDC16 C36
Program No.: 91
Vdiag No.: 44, 4C, 48,
50, 54, 58