Page 3835 of 4083
TM-288
< DISASSEMBLY AND ASSEMBLY >
ASSEMBLY
• Assemble it so that manual valve cutout is engaged withmanual plate projection.
h. Install bolts (A), (B) and (C) to control valve with TCM.
i. Tighten bolt (1A), (2B) and (3A) temporarily to prevent disloca- tion. After that tighten them in order (1 → 2 → 3), and then
tighten other bolts.
10. Connect A/T fluid temperature sensor 2 connector (A).
11. Securely fasten terminal cord assembly and A/T fluid tempera- ture sensor 2 harness with terminal clips.
SCIA5035E
: Front
Bolt symbol Length mm (in) Number of bolts
A 42 (1.65) 5
B 55 (2.17) 6
C 40 (1.57) 1
SCIA8077E
: Front
Bolt symbol A B C
Number of bolts 56 1
Length mm (in) 42 (1.65) 55 (2.17) 40 (1.57)
Tightening torque
N·m (km-g, in-lb) 7.9 (0.81, 70)With ATF applied
7.9 (0.81, 70)
SCIA8078E
SCIA8124E
Revision: March 2010 2008 QX56
Page 3837 of 4083
TM-290
< DISASSEMBLY AND ASSEMBLY >
ASSEMBLY
17. Install oil pan to transmission case. Refer to TM-199, "Oil Pan".
18. Install torque converter.
a. Pour ATF into torque converter. NOTE:
• Approximately 2 liters (2-1/8 US qt. 1-3/4 Imp qt) of fluid isrequired for a new torque converter.
• When reusing old torque converter, add the same amount of fluid as was drained.
b. Install torque converter while aligning notches of torque con- verter with notches of oil pump.
CAUTION:
Install torque converter while rotating it.
c. Measure distance "A" to make sure that torque converter is in proper position.
SAT428DA
SCIA5010E
Distance "A" : 24.0 mm (0.94 in) or more
SCIA5694E
Revision: March 2010 2008 QX56
Page 3838 of 4083
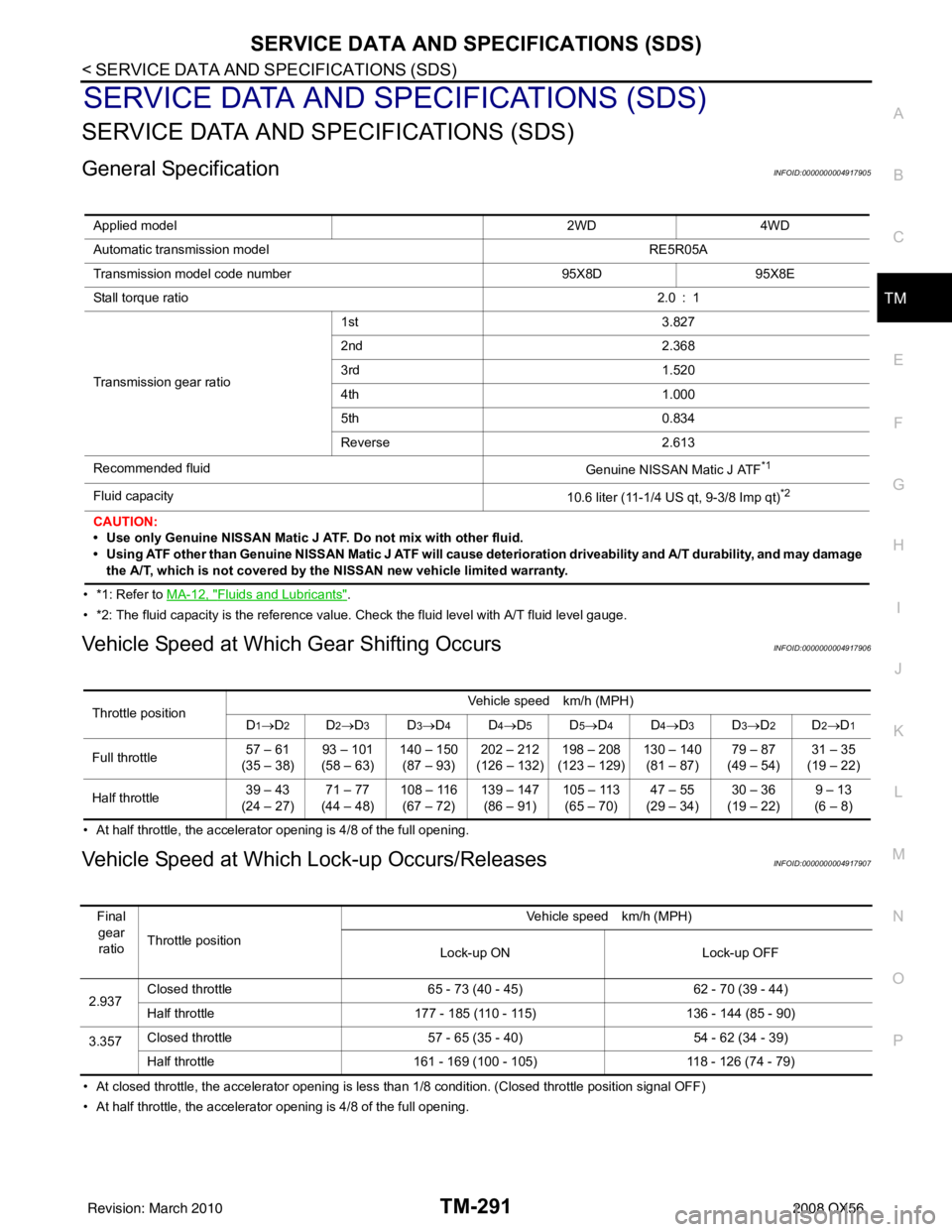
SERVICE DATA AND SPECIFICATIONS (SDS)TM-291
< SERVICE DATA AND SPECIFICATIONS (SDS)
CEF
G H
I
J
K L
M A
B
TM
N
O P
SERVICE DATA AND SPECIFICATIONS (SDS)
SERVICE DATA AND SPECIFICATIONS (SDS)
General SpecificationINFOID:0000000004917905
• *1: Refer to MA-12, "Fluids and Lubricants".
• *2: The fluid capacity is the reference value. Check the fluid level with A/T fluid level gauge.
Vehicle Speed at Which Gear Shifting OccursINFOID:0000000004917906
• At half throttle, the accelerator opening is 4/8 of the full opening.
Vehicle Speed at Which Lock-up Occurs/ReleasesINFOID:0000000004917907
• At closed throttle, the accelerator opening is less than 1/8 condition. (Closed throttle position signal OFF)
• At half throttle, the accelerator opening is 4/8 of the full opening. Applied model
2WD4WD
Automatic transmission model RE5R05A
Transmission model code number 95X8D95X8E
Stall torque ratio 2.0 : 1
Transmission gear ratio 1st
3.827
2nd 2.368
3rd 1.520
4th 1.000
5th 0.834
Reverse 2.613
Recommended fluid Genuine NISSAN Matic J ATF
*1
Fluid capacity10.6 liter (11-1/4 US qt, 9-3/8 Imp qt)*2
CAUTION:
• Use only Genuine NISSAN Matic J ATF. Do not mix with other fluid.
• Using ATF other than Genuine NISSAN Matic J ATF will cause deterioration driveability and A/ T durability, and may damage
the A/T, which is not covered by the NISSAN new vehicle limited warranty.
Throttle position Vehicle speed km/h (MPH)
D1→D2D2→ D3D3→D4D4→D5D5→D4D4→D3D3→D2D2→D1
Full throttle 57 – 61
(35 – 38) 93 – 101
(58 – 63) 140 – 150
(87 – 93) 202 – 212
(126 – 132) 198 – 208
(123 – 129) 130 – 140
(81 – 87) 79 – 87
(49 – 54) 31 – 35
(19 – 22)
Half throttle 39 – 43
(24 – 27) 71 – 77
(44 – 48) 108 – 116
(67 – 72) 139 – 147
(86 – 91) 105 – 113
(65 – 70) 47 – 55
(29 – 34) 30 – 36
(19 – 22) 9 – 13
(6 – 8)
Final gear ratio Throttle position Vehicle speed km/h (MPH)
Lock-up ON Lock-up OFF
2.937 Closed throttle
65 - 73 (40 - 45) 62 - 70 (39 - 44)
Half throttle 177 - 185 (110 - 115) 136 - 144 (85 - 90)
3.357 Closed throttle
57 - 65 (35 - 40) 54 - 62 (34 - 39)
Half throttle 161 - 169 (100 - 105) 118 - 126 (74 - 79)
Revision: March 2010 2008 QX56
Page 3840 of 4083
SERVICE DATA AND SPECIFICATIONS (SDS)TM-293
< SERVICE DATA AND SPECIFICATIONS (SDS)
CEF
G H
I
J
K L
M A
B
TM
N
O P
Torque ConverterINFOID:0000000004917915
Thickness mm (in) 0.8 (0.031)
1.0 (0.039)
1.2 (0.047)
1.4 (0.055)
1.6 (0.063)
1.8 (0.071)
Distance between end of converter housing and torque
converter mm (in) 24.0 (0.94) or more
Revision: March 2010
2008 QX56
Page 3856 of 4083
VTL-16
< ON-VEHICLE REPAIR >
HEATER & COOLING UNIT ASSEMBLY
Rear A/C System
NOTE:
Refer to HA-5, "
Precaution for Refrigerant Connection".
Removal and InstallationINFOID:0000000001516611
FRONT HEATER AND COOLING UNIT ASSEMBLY
Removal
7. High-pressure flexible hose 8. Low-pressure flexible hose 9. Low-pressure service valve
10. Low-pressure pipe 11. Expansion valve (front) 12. Drain hose
AWIIA0134GB
1. Rear heater and cooling unit assembly 2. Rear A/C pipes 3. Rear A/C heater core pipes
4. Rear heater core hose 5. Rear blower motor6. Underfloor rear A/C pipes
7. Underfloor rear heater core pipes A. Bolt torque specification B. Leak checking order (l - r)
C. Tightening torque D. Wrench sizeE. O-ring size
⇐ Front
NOTE: The O-ring size 8 is the high-side and the O-ring size 16 is the low-side.
Revision: March 2010 2008 QX56
Page 3993 of 4083
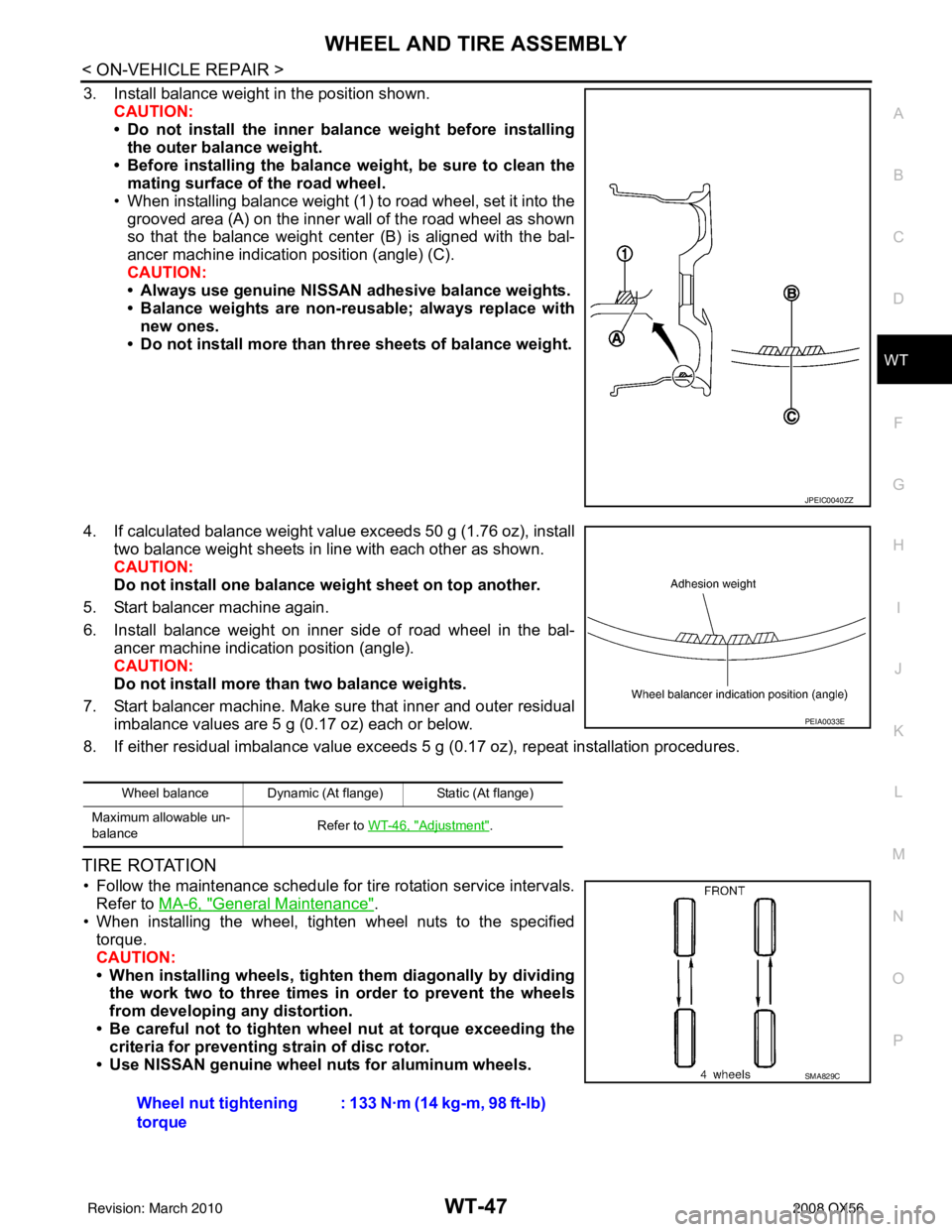
WHEEL AND TIRE ASSEMBLYWT-47
< ON-VEHICLE REPAIR >
C
DF
G H
I
J
K L
M A
B
WT
N
O P
3. Install balance weight in the position shown. CAUTION:
• Do not install the inner bala nce weight before installing
the outer balance weight.
• Before installing the balance weight, be sure to clean the mating surface of the road wheel.
• When installing balance weight (1) to road wheel, set it into the grooved area (A) on the inner wall of the road wheel as shown
so that the balance weight cent er (B) is aligned with the bal-
ancer machine indication position (angle) (C).
CAUTION:
• Always use genuine NISSAN adhesive balance weights.
• Balance weights are non-re usable; always replace with
new ones.
• Do not install more than th ree sheets of balance weight.
4. If calculated balance weight value exceeds 50 g (1.76 oz), install two balance weight sheets in line with each other as shown.
CAUTION:
Do not install one balance weight sheet on top another.
5. Start balancer machine again.
6. Install balance weight on inner side of road wheel in the bal- ancer machine indication position (angle).
CAUTION:
Do not install more than two balance weights.
7. Start balancer machine. Make sure that inner and outer residual imbalance values are 5 g (0.17 oz) each or below.
8. If either residual imbalance value exceeds 5 g (0.17 oz), repeat installation procedures.
TIRE ROTATION
• Follow the maintenance schedule for tire rotation service intervals.
Refer to MA-6, "
General Maintenance".
• When installing the wheel, tighten wheel nuts to the specified torque.
CAUTION:
• When installing wheels, tighte n them diagonally by dividing
the work two to three times in order to prevent the wheels
from developing any distortion.
• Be careful not to tighten wh eel nut at torque exceeding the
criteria for preventing strain of disc rotor.
• Use NISSAN genuine wheel nuts for aluminum wheels.
JPEIC0040ZZ
Wheel balance Dynamic (At flange) Static (At flange)
Maximum allowable un-
balance Refer to WT-46, "
Adjustment".
PEIA0033E
Wheel nut tightening
torque: 133 N·m (14 kg-m, 98 ft-lb)
SMA829C
Revision: March 2010
2008 QX56
Page 3994 of 4083
WT-48
< ON-VEHICLE REPAIR >
WHEEL AND TIRE ASSEMBLY
Rotation
INFOID:0000000001534678
NOTE:
Follow the maintenance schedule for tire rotation service intervals. Refer to MA-29, "
Tire Rotation" .
1. Rotate the tires on each side from front to back as shown. Do not include the spare tire when rotating the tires.
CAUTION:
When installing wheel s, tighten them diagonally by dividing
the work two to three times in order to prevent the wheels
from developing any distortion.
2. Adjust the tire pressure to specification. Refer to WT-51, "
Tire" .
3. After the tire rotation, retighten the wheel nuts after the vehicle has been driven for 1,000 km (600 miles), and also after every
wheel and tire have been installed such as after repairing a flat tire. Wheel nut torque : 133 N·m (14 kg-m, 98 ft-lb)
SMA829C
Revision: March 2010
2008 QX56
Page 4073 of 4083

WW-76
< ON-VEHICLE REPAIR >
FRONT WIPER ARM
ON-VEHICLE REPAIR
FRONT WIPER ARM
Front Wiper ArmsINFOID:0000000001601860
REMOVAL AND INSTALLATION
Removal
1. Remove wiper arm covers and wiper arm nuts.
2. Remove front RH wiper arm and front LH wiper arm.
3. Remove front RH blade assembly and front LH blade assembly.
Installation
1. Operate wiper motor one full cycle, then turn "OFF" (Auto Stop).
2. Clean up the pivot area as shown. This will reduce possibility ofwiper arm looseness.
3. Install front RH blade assembly and front LH blade assembly on the wiper arms .
4. Install front RH wiper arm and front LH wiper arm.
5. Tighten wiper arm nuts to specified torque, and install wiper arm covers. Refer to WW-77, "
Wiper Motor
and Linkage".
6. Ensure that wiper blades stop within proper clearance. Refer to WW-76, "
Front Wiper Arms".
FRONT WIPER ARM ADJUSTMENT
1. Operate wiper motor one full cycle, then turn "OFF" (Auto Stop).
2. Lift the wiper blade up and then rest it onto glass surface, check
the blade clearance "L1" and "L2".
3. Remove wiper arm covers and wiper arm nuts.
4. Adjust front wiper arms on wiper motor pivot shafts to obtain above specified blade clearances.
5. Tighten wiper arm nuts to specified torque, and install wiper arm covers. Refer to WW-77, "
Wiper Motor
and Linkage".
SEL024J
Clearance "L1" : 41.5 - 56.5 mm (1.634 - 2.224 in)
Clearance "L2" : 52.5 - 67.5 mm (2.067 - 2.657 in)
SEL543TA
Revision: March 2010 2008 QX56