Page 61 of 419
Engine mechanism - Timing chain assembly34. Install speed sensor.Torque: 35. Install engine fixing bracketTorque: 36. Install water pump mounting components
[4G18-1307100].(a) Install new o-ring on water pump.
(b) Install water pump with 6 bolts.
Torque: bolt A: m37. Install drive belt tensioner device.Torque: nut: Bolt: m38. Install right engine mounting assembly.Torque: 39. Install cylinder head cover components.(a) Install gasket to cylinder head cover.
(b) Eliminate all old seal materials.
(c) Coat sealant on 2 positions shown in the diagram.
Sealant: silicon rubber flange sealant 1596
(Kesaixin 1596).
Notes:Eliminate all grease on contact surface.After coating sealant, finish installation of cylinder
head cover within 3 minutes.After installing, do not refill engine oil within 2
minutes.
(d) Install cylinder head cover and cable bracket with 9 bolts,
2 seal washers and 2 nuts.
Torque: nut: Bolt: m40. Install ignition coil mounting components.Torque: 50
Page 63 of 419
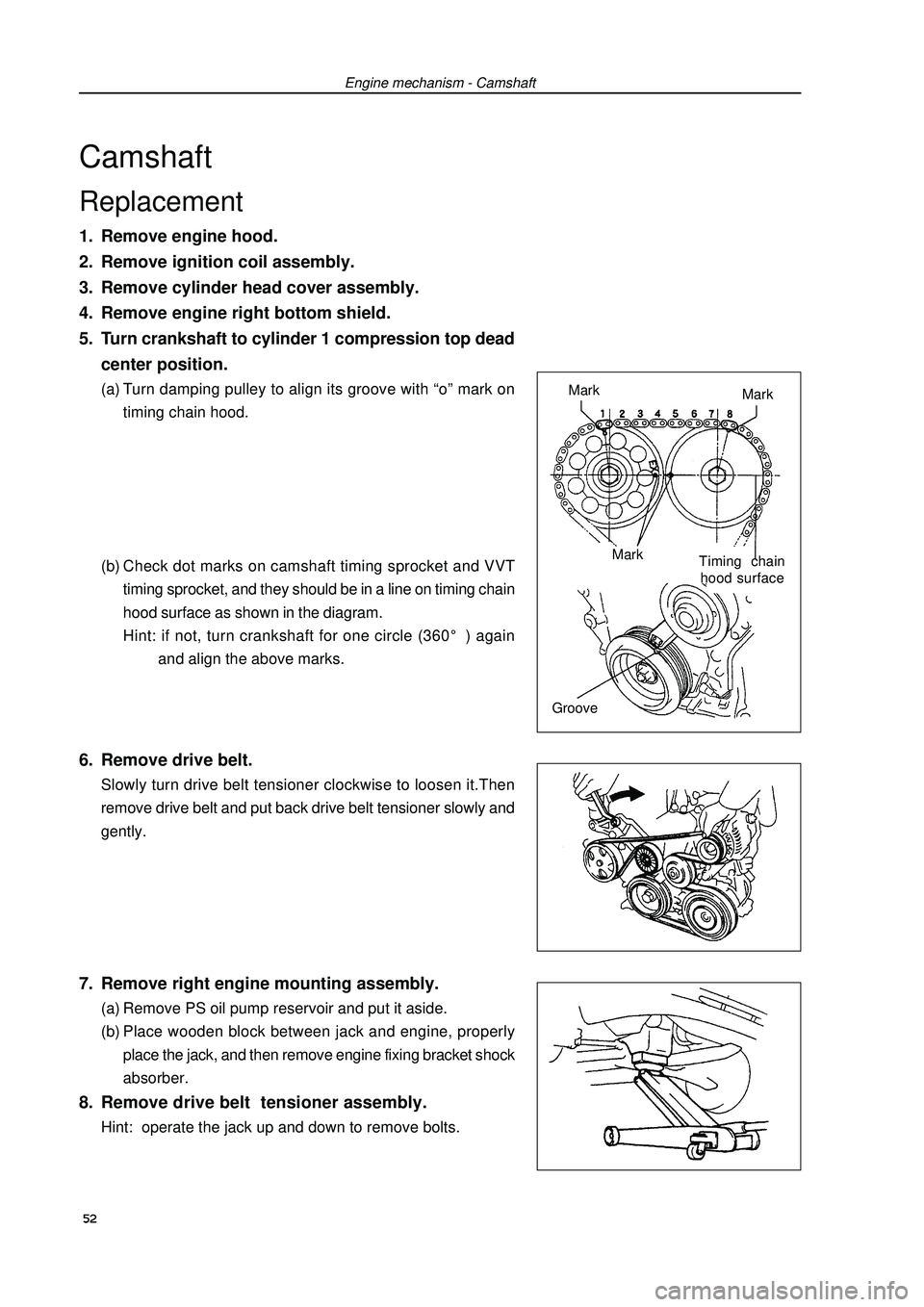
Engine mechanism - CamshaftCamshaftReplacement1. Remove engine hood.
2. Remove ignition coil assembly.
3. Remove cylinder head cover assembly.
4. Remove engine right bottom shield.
5. Turn crankshaft to cylinder 1 compression top dead
center position.(a) Turn damping pulley to align its groove with “o” mark on
timing chain hood.
(b) Check dot marks on camshaft timing sprocket and VVT
timing sprocket, and they should be in a line on timing chain
hood surface as shown in the diagram.
Hint: if not, turn crankshaft for one circle (360) again
and align the above marks.6. Remove drive belt.Slowly turn drive belt tensioner clockwise to loosen it.Then
remove drive belt and put back drive belt tensioner slowly and
gently.7. Remove right engine mounting assembly.(a) Remove PS oil pump reservoir and put it aside.
(b) Place wooden block between jack and engine, properly
place the jack, and then remove engine fixing bracket shock
absorber.8. Remove drive belt tensioner assembly.Hint: operate the jack up and down to remove bolts. 52Mark
Mark
Mark
Timing chain
hood surface
Groove
Page 75 of 419
Engine mechanism - Cylinder cover gasket components(c) Tighten each cylinder head bolt in turn again.
Torque: m
(d) Install heating air water outlet pipe components.
Torque: 8. Install camshaft.(a) Coat engine oil on camshaft journal.
(b) Put 2 camshafts on cylinder head and with cylinder 1 cam-
shaft end toward the direction shown in the diagram.
(c) Check forward remarks and figures of all bearing cover, and
tighten the bolts as sequences shown in the diagram.
Torque:
Camshaft front bearing cover: Camshaft bearing cover: 9. Check idle speed and ignition timing.
10. Check compression pressure.
11. Check CO/HC.64
Page 79 of 419
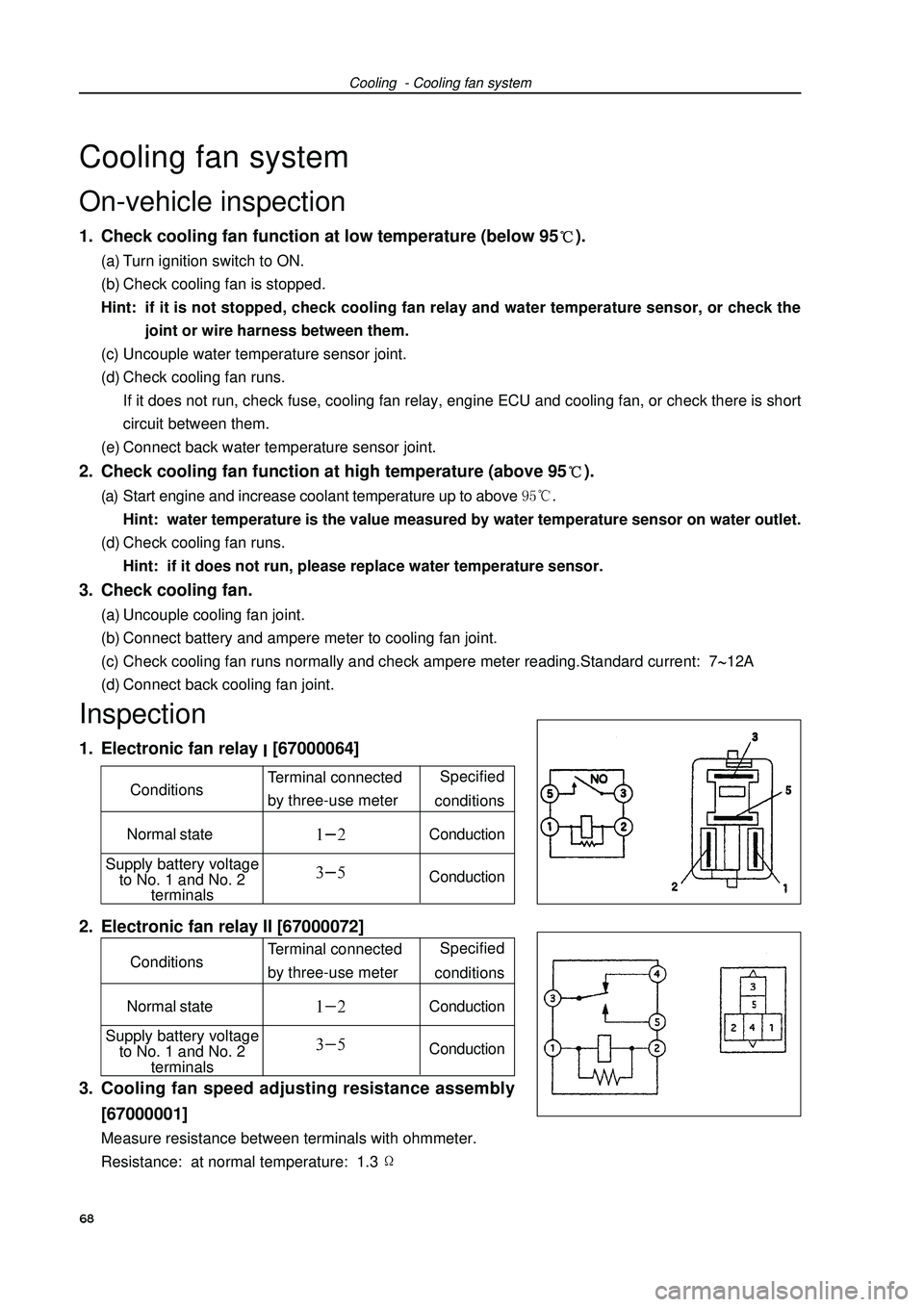
Cooling - Cooling fan systemCooling fan systemOn-vehicle inspection1. Check cooling fan function at low temperature (below 95).(a) Turn ignition switch to ON.
(b) Check cooling fan is stopped.
Hint: if it is not stopped, check cooling fan relay and water temperature sensor, or check the
joint or wire harness between them.
(c) Uncouple water temperature sensor joint.
(d) Check cooling fan runs.
If it does not run, check fuse, cooling fan relay, engine ECU and cooling fan, or check there is short
circuit between them.
(e) Connect back water temperature sensor joint.2. Check cooling fan function at high temperature (above 95).(a) Start engine and increase coolant temperature up to above Hint: water temperature is the value measured by water temperature sensor on water outlet.
(d) Check cooling fan runs.
Hint: if it does not run, please replace water temperature sensor.3. Check cooling fan.(a) Uncouple cooling fan joint.
(b) Connect battery and ampere meter to cooling fan joint.
(c) Check cooling fan runs normally and check ampere meter reading.Standard current: 712A
(d) Connect back cooling fan joint.Inspection1. Electronic fan relay [67000064]
2. Electronic fan relay II [67000072]
3. Cooling fan speed adjusting resistance assembly
[67000001]Measure resistance between terminals with ohmmeter.
Resistance: at normal temperature: 1.368 Specified
conditions
Normal stateConductionConductionTerminal connected
by three-use meter Conditions
Supply battery voltage
to No. 1 and No. 2
terminals
Specified
conditions
Normal stateConductionConductionTerminal connected
by three-use meter Conditions
Supply battery voltage
to No. 1 and No. 2
terminals
Page 88 of 419
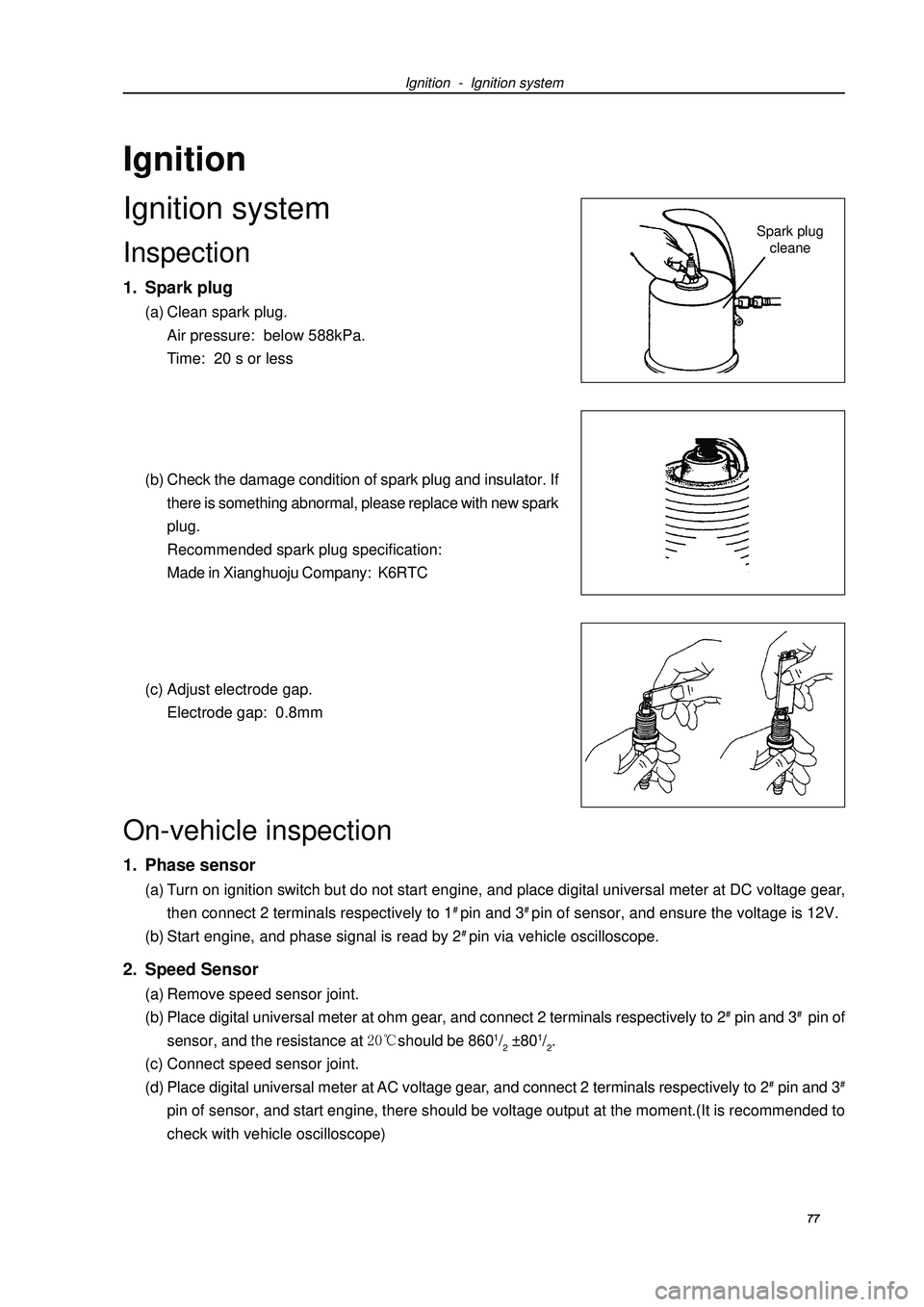
Ignition - Ignition systemSpark plug
cleaneOn-vehicle inspection1. Phase sensor(a) Turn on ignition switch but do not start engine, and place digital universal meter at DC voltage gear,
then connect 2 terminals respectively to 1# pin and 3# pin of sensor, and ensure the voltage is 12V.
(b) Start engine, and phase signal is read by 2# pin via vehicle oscilloscope.2. Speed Sensor(a) Remove speed sensor joint.
(b) Place digital universal meter at ohm gear, and connect 2 terminals respectively to 2# pin and 3# pin of
sensor, and the resistance at should be 8601/2 ±801/2.
(c) Connect speed sensor joint.
(d) Place digital universal meter at AC voltage gear, and connect 2 terminals respectively to 2# pin and 3#pin of sensor, and start engine, there should be voltage output at the moment.(It is recommended to
check with vehicle oscilloscope)IgnitionIgnition systemInspection1. Spark plug(a) Clean spark plug.
Air pressure: below 588kPa.
Time: 20 s or less
(b) Check the damage condition of spark plug and insulator. If
there is something abnormal, please replace with new spark
plug.
Recommended spark plug specification:
Made in Xianghuoju Company: K6RTC
(c) Adjust electrode gap.
Electrode gap: 0.8mm77
Page 89 of 419
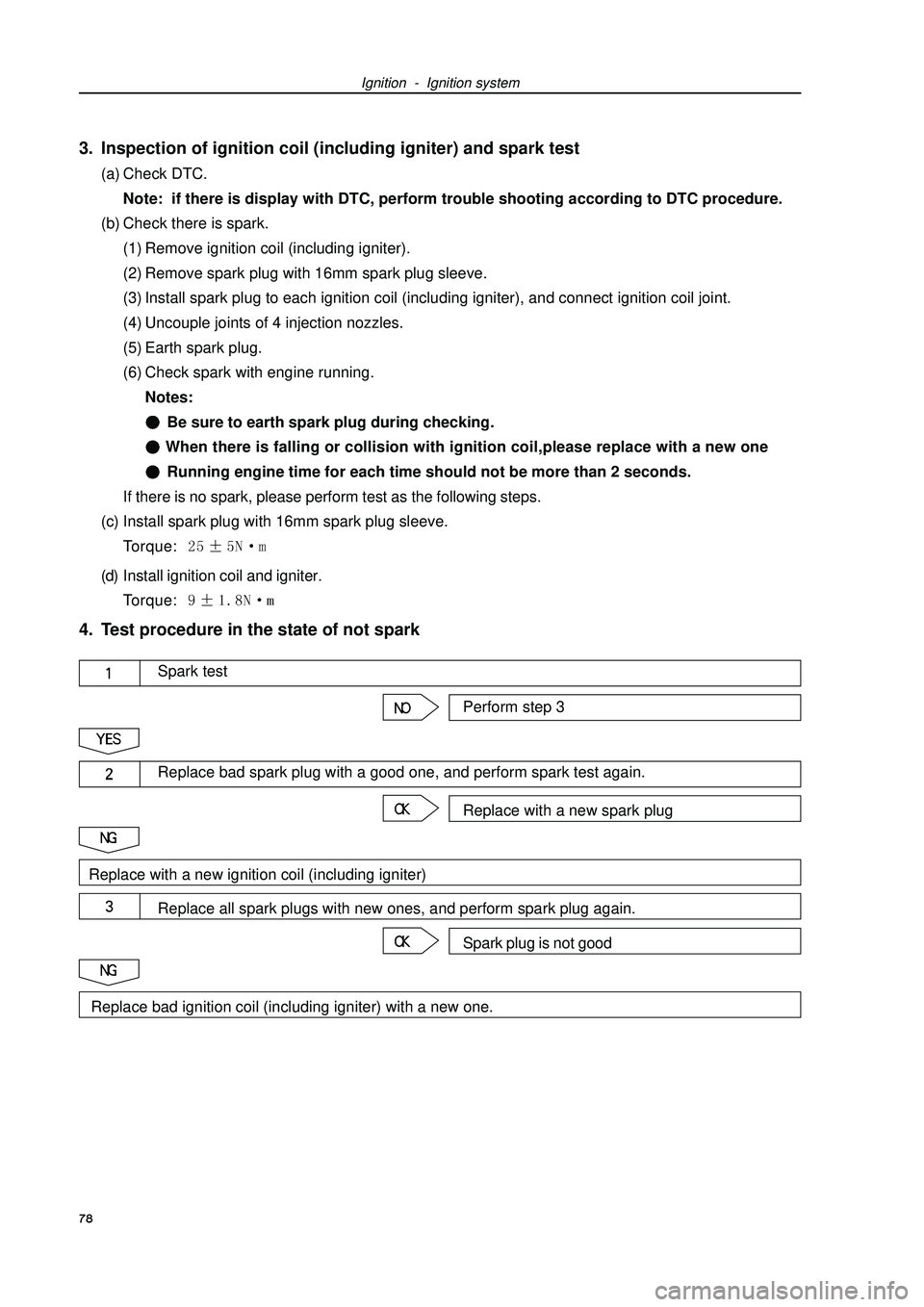
Ignition - Ignition system3. Inspection of ignition coil (including igniter) and spark test(a) Check DTC.
Note: if there is display with DTC, perform trouble shooting according to DTC procedure.
(b) Check there is spark.
(1) Remove ignition coil (including igniter).
(2) Remove spark plug with 16mm spark plug sleeve.
(3) Install spark plug to each ignition coil (including igniter), and connect ignition coil joint.
(4) Uncouple joints of 4 injection nozzles.
(5) Earth spark plug.
(6) Check spark with engine running.
Notes:Be sure to earth spark plug during checking. When there is falling or collision with ignition coil,please replace with a new oneRunning engine time for each time should not be more than 2 seconds.
If there is no spark, please perform test as the following steps.
(c) Install spark plug with 16mm spark plug sleeve.
Torque: (d) Install ignition coil and igniter.
Torque: 4. Test procedure in the state of not spark
78Perform step 3Spark testReplace with a new spark plugReplace bad spark plug with a good one, and perform spark test again.Spark plug is not goodReplace all spark plugs with new ones, and perform spark plug again.Replace with a new ignition coil (including igniter)Replace bad ignition coil (including igniter) with a new one.
Page 93 of 419
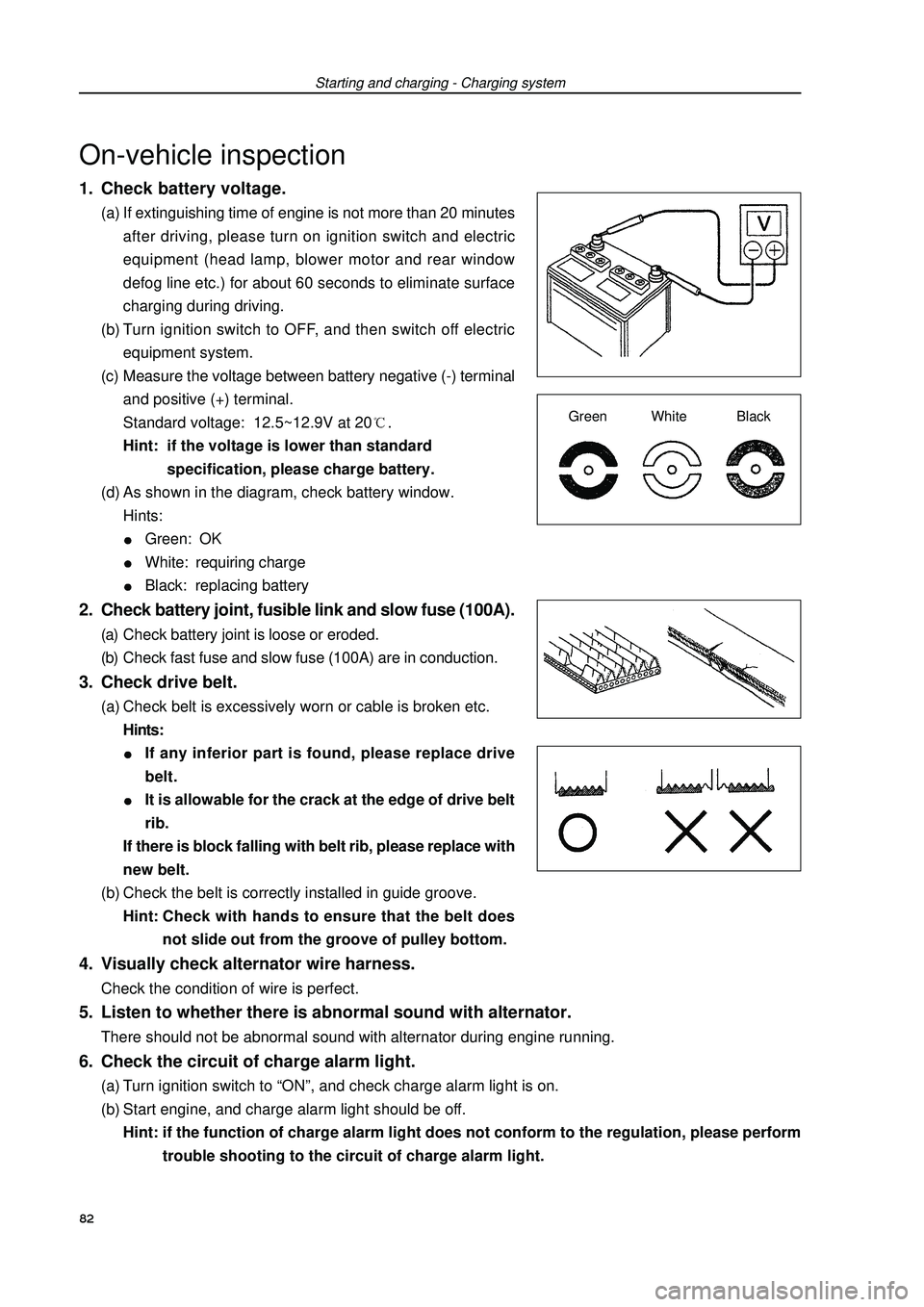
1. Check battery voltage.(a) If extinguishing time of engine is not more than 20 minutes
after driving, please turn on ignition switch and electric
equipment (head lamp, blower motor and rear window
defog line etc.) for about 60 seconds to eliminate surface
charging during driving.
(b) Turn ignition switch to OFF, and then switch off electric
equipment system.
(c) Measure the voltage between battery negative (-) terminal
and positive (+) terminal.
Standard voltage: 12.5~12.9V at 20.
Hint: if the voltage is lower than standard
specification, please charge battery.
(d) As shown in the diagram, check battery window.
Hints:Green: OKWhite: requiring chargeBlack: replacing battery2. Check battery joint, fusible link and slow fuse (100A).(a) Check battery joint is loose or eroded.
(b) Check fast fuse and slow fuse (100A) are in conduction.3. Check drive belt.(a) Check belt is excessively worn or cable is broken etc.
Hints:If any inferior part is found, please replace drive
belt.It is allowable for the crack at the edge of drive belt
rib.
If there is block falling with belt rib, please replace with
new belt.
(b) Check the belt is correctly installed in guide groove.
Hint:Check with hands to ensure that the belt does
not slide out from the groove of pulley bottom.4. Visually check alternator wire harness.Check the condition of wire is perfect.Starting and charging - Charging systemOn-vehicle inspectionGreen White Black5. Listen to whether there is abnormal sound with alternator.There should not be abnormal sound with alternator during engine running.6. Check the circuit of charge alarm light.(a) Turn ignition switch to “ON”, and check charge alarm light is on.
(b) Start engine, and charge alarm light should be off.
Hint: if the function of charge alarm light does not conform to the regulation, please perform
trouble shooting to the circuit of charge alarm light.82
Page 205 of 419
![GEELY FC 2008 Workshop Manual Steering column system
Overhaul
1. Put the front wheels towards the front.
2. Disassemble safety airbag assembly at the side of
driver (equipping with SRS) [67000179]
Note: if disconnecting airbag joi GEELY FC 2008 Workshop Manual Steering column system
Overhaul
1. Put the front wheels towards the front.
2. Disassemble safety airbag assembly at the side of
driver (equipping with SRS) [67000179]
Note: if disconnecting airbag joi](/manual-img/58/57161/w960_57161-204.png)
Steering column system
Overhaul
1. Put the front wheels towards the front.
2. Disassemble safety airbag assembly at the side of
driver (equipping with SRS) [67000179]
Note: if disconnecting airbag joint when ignition switch
locates at ON position, checking number will record it.
(a) Put the front wheels towards the front.
(b) Use planetary sleeve wrench to loosen two planetary
screws until the concave slot around the screw contacts
the screw shell.
(c) Pull out airbag assemble from steering wheel, and
disassemble airbag joint.
(d) Disassemble the terminal.
Warning:
¡ñ¡ñ
¡ñ¡ñ¡ñWhen storing safety airbag assembly at the side
of driver, it is necessary to put the surface of
airbag assembly towards the upside.
¡ñ¡ñ
¡ñ¡ñ¡ñDo not disassemble airbag assembly.
Note: when disassembling airbag assembly, pay
attention not to pull airbag wiring harness.
3. Disassemble steering wheel assembly [67100001]
(a) Disassemble the fixed screw cap of steering wheel.
(b) Make corresponding marks on steering wheel and main
shaft assembly.
(c) Use special tool to disassemble steering wheel.
4. Disassemble upper/lower decoration plate of
steering column [64000128/64000129]
5. Disassemble left combination switch assembly
[67000078] (referring to page 298)
Steering column--Steering systemSteering column--Steering system
Steering column--Steering systemSteering column--Steering systemSteering column--Steering system
airbag joint
Correct Wrongplanetary
screws screw shell
194
Align the mark