Page 28 of 419
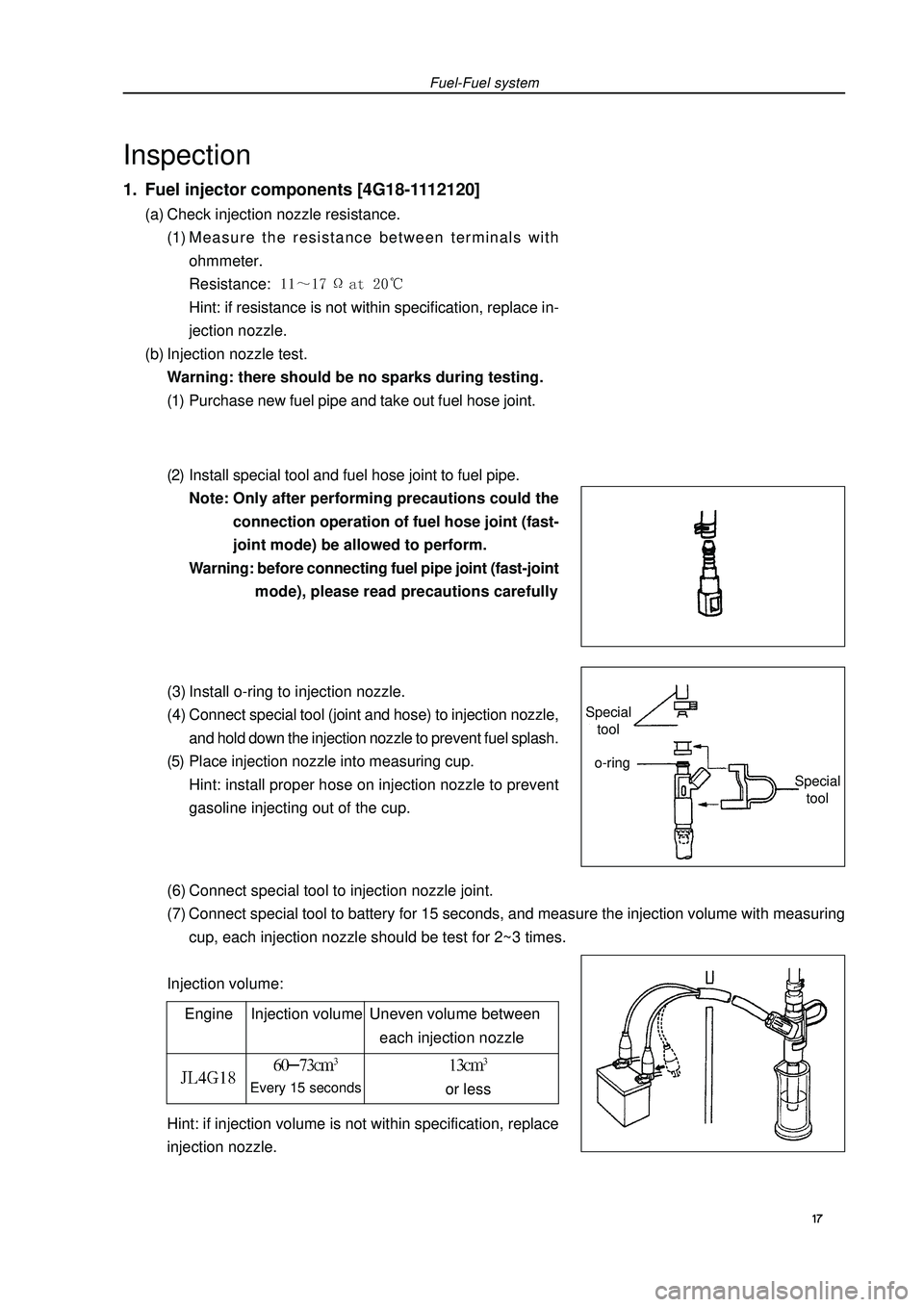
(6) Connect special tool to injection nozzle joint.
(7) Connect special tool to battery for 15 seconds, and measure the injection volume with measuring
cup, each injection nozzle should be test for 2~3 times.
Injection volume:Fuel-Fuel systemInspection1. Fuel injector components [4G18-1112120](a) Check injection nozzle resistance.
(1) Measure the resistance between terminals with
ohmmeter.
Resistance: Hint: if resistance is not within specification, replace in-
jection nozzle.
(b) Injection nozzle test.
Warning: there should be no sparks during testing.
(1) Purchase new fuel pipe and take out fuel hose joint.
(2) Install special tool and fuel hose joint to fuel pipe.
Note: Only after performing precautions could the
connection operation of fuel hose joint (fast-
joint mode) be allowed to perform.
Warning: before connecting fuel pipe joint (fast-joint
mode), please read precautions carefully
(3) Install o-ring to injection nozzle.
(4) Connect special tool (joint and hose) to injection nozzle,
and hold down the injection nozzle to prevent fuel splash.
(5) Place injection nozzle into measuring cup.
Hint: install proper hose on injection nozzle to prevent
gasoline injecting out of the cup.
Engine Injection volume Uneven volume between
each injection nozzleEvery 15 secondsor lessHint: if injection volume is not within specification, replace
injection nozzle. 17 Special
toolSpecial
toolo-ring
Page 29 of 419
![GEELY FC 2008 Workshop Manual Fuel-Injection nozzle assemblyInjection nozzle assemblyReplacement1. Take measures to prevent gasoline leaking.
2. Remove engine plastic hood components.
3. Uncouple engine wire harness [4G18-3724100] GEELY FC 2008 Workshop Manual Fuel-Injection nozzle assemblyInjection nozzle assemblyReplacement1. Take measures to prevent gasoline leaking.
2. Remove engine plastic hood components.
3. Uncouple engine wire harness [4G18-3724100]](/manual-img/58/57161/w960_57161-28.png)
Fuel-Injection nozzle assemblyInjection nozzle assemblyReplacement1. Take measures to prevent gasoline leaking.
2. Remove engine plastic hood components.
3. Uncouple engine wire harness [4G18-3724100].(a) Remove injection nozzle joint.
(b) Remove exhaust gas hose.4. Remove fuel pipe assembly(a) Loosen oil feed hose clips.
(b) Pull oil feed hose away from fuse distribution pipe.
Notes: zCheck there is dirt on fuel pipe and its joint before removing, and clean it off in the case of dirt. zIt is only allowed to remove with hands. zCheck there are foreign matters with the removed fuel pipe seal surface, and clean them off in the
case of foreign matters. zCover the fuel pipe with plastic bag to avoid pipe damage and foreign matters entering.5. Remove fuel pipe assemblyRemove 2 bolts and oil feed pipe (together with injection nozzle).6. Remove injection nozzle components.Pull out 4 injection nozzles from oil feed pipe.7. Install injection nozzle components.Coat a thin layer of gasoline on o-ring and rotate left and right to push injection nozzle into oil feed pipe.
Notes:
zBe careful not to rotate o-ring.
zCheck injection nozzle could rotate smoothly after it is installed, and if not replace with new o-ring.8. Install fuel hose assembly.Install fuel hose to oil feed pipe.
Notes:
zCheck there are damage or foreign matters in the binding site of fuel pipe.
zAfter installing, pull the fuel pump with hands to check the fuel pipe is bound firmly with joint. 18
Page 30 of 419
Fuel-Injection nozzle assembly9. Install fuel rail component [4G18-1112110].(a) Check injection nozzle o-ring and replace if there is damage.
(b) Install isolator on cylinder head.
(c) Install fuel rail component together with injection nozzle.
Torque:(d) Install fuel pipe fixing clip.
Torque: m10. Check the function of electric fuel pump and check there is fuel leakage.
19
Page 31 of 419
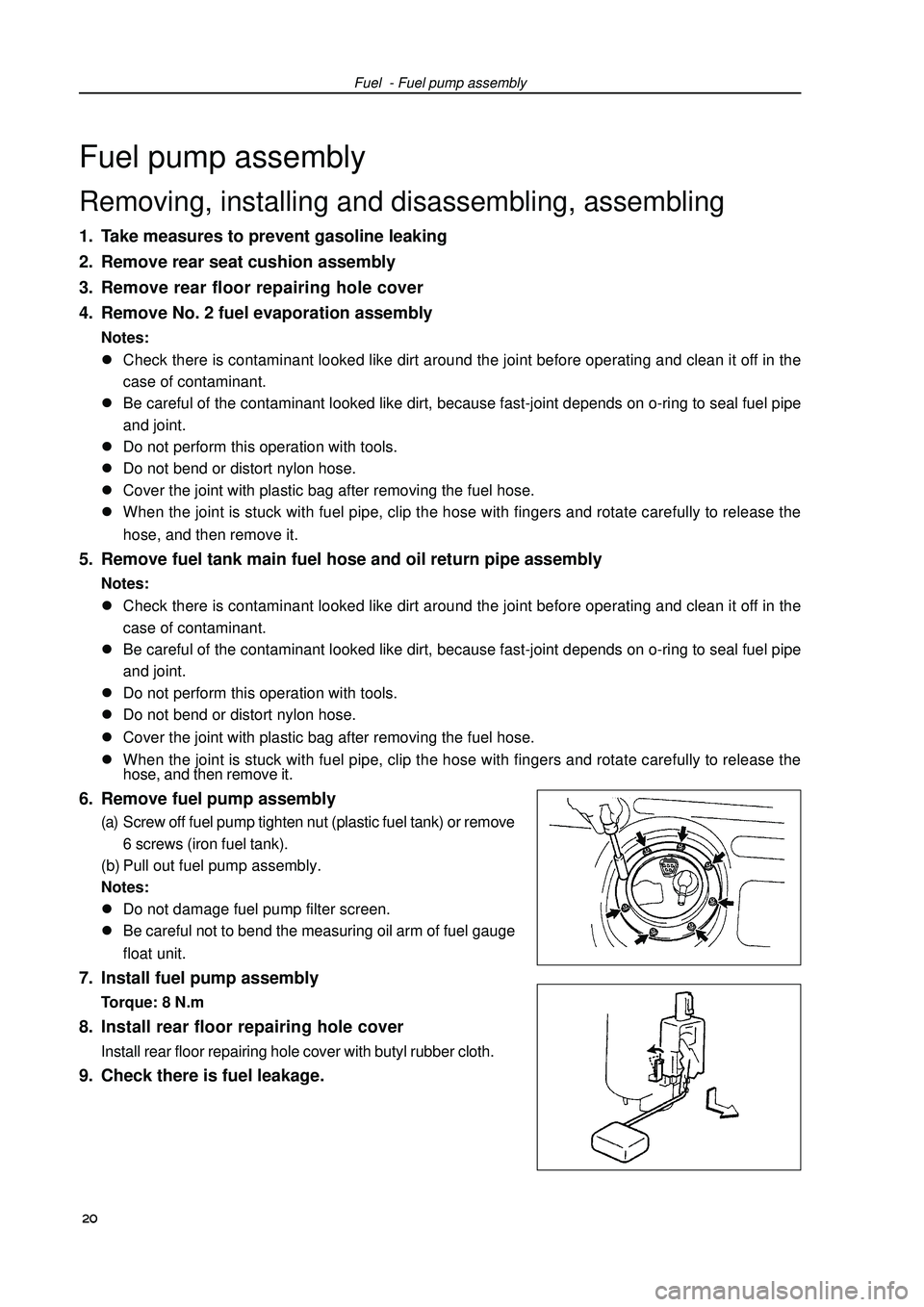
Fuel - Fuel pump assemblyFuel pump assemblyRemoving, installing and disassembling, assembling1. Take measures to prevent gasoline leaking
2. Remove rear seat cushion assembly
3. Remove rear floor repairing hole cover
4. Remove No. 2 fuel evaporation assemblyNotes:
zCheck there is contaminant looked like dirt around the joint before operating and clean it off in the
case of contaminant.
zBe careful of the contaminant looked like dirt, because fast-joint depends on o-ring to seal fuel pipe
and joint.
zDo not perform this operation with tools.
zDo not bend or distort nylon hose.
zCover the joint with plastic bag after removing the fuel hose.
zWhen the joint is stuck with fuel pipe, clip the hose with fingers and rotate carefully to release the
hose, and then remove it.5. Remove fuel tank main fuel hose and oil return pipe assemblyNotes:
zCheck there is contaminant looked like dirt around the joint before operating and clean it off in the
case of contaminant.
zBe careful of the contaminant looked like dirt, because fast-joint depends on o-ring to seal fuel pipe
and joint.
zDo not perform this operation with tools.
zDo not bend or distort nylon hose.
zCover the joint with plastic bag after removing the fuel hose.
zWhen the joint is stuck with fuel pipe, clip the hose with fingers and rotate carefully to release the
hose, and then remove it.6. Remove fuel pump assembly(a) Screw off fuel pump tighten nut (plastic fuel tank) or remove
6 screws (iron fuel tank).
(b) Pull out fuel pump assembly.
Notes:
zDo not damage fuel pump filter screen.
zBe careful not to bend the measuring oil arm of fuel gauge
float unit.7. Install fuel pump assemblyTorque: 8 N.m8. Install rear floor repairing hole coverInstall rear floor repairing hole cover with butyl rubber cloth.9. Check there is fuel leakage. 20
Page 32 of 419
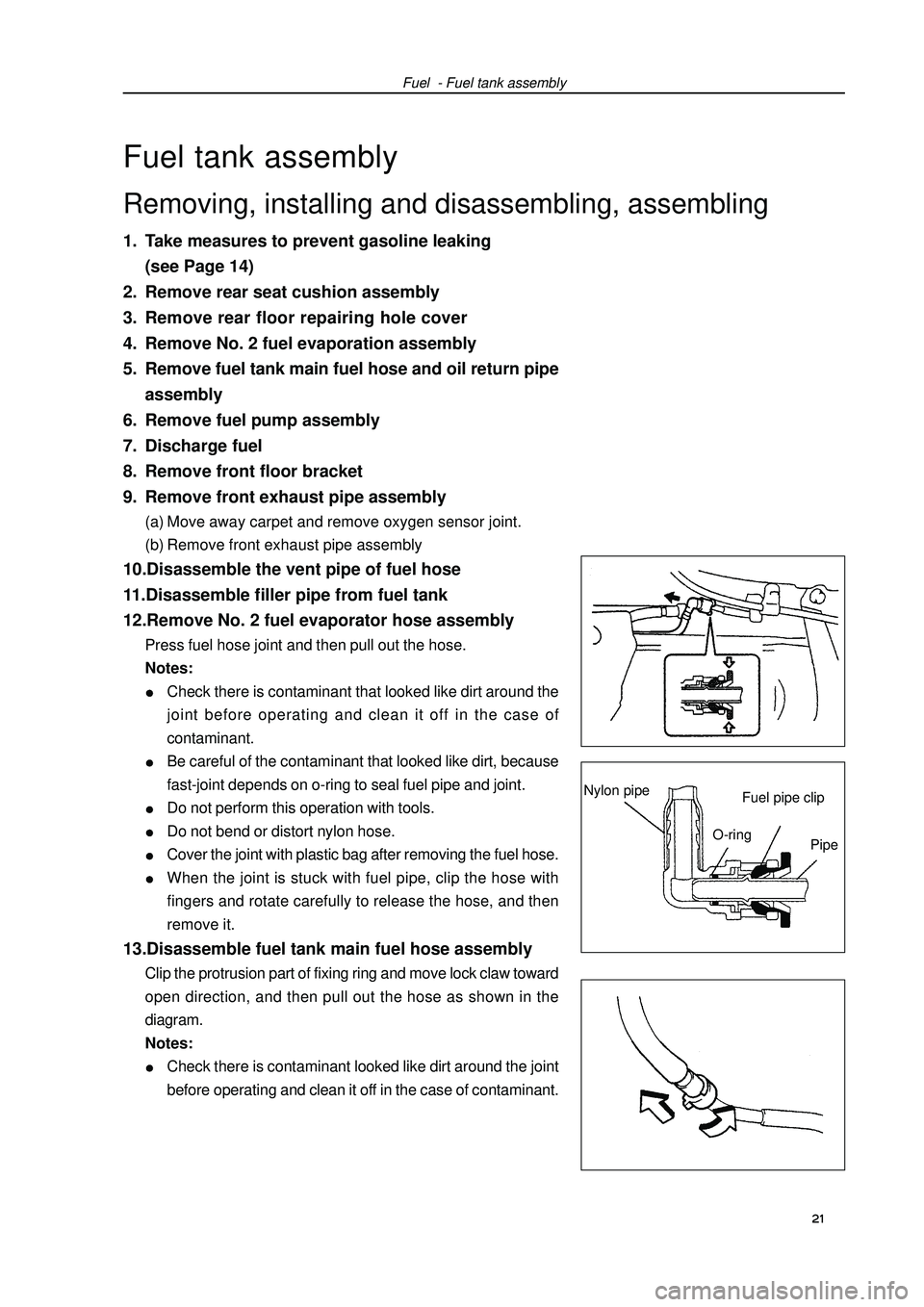
Fuel - Fuel tank assemblyFuel tank assembly1. Take measures to prevent gasoline leaking
(see Page 14)
2. Remove rear seat cushion assembly
3. Remove rear floor repairing hole cover
4. Remove No. 2 fuel evaporation assembly
5. Remove fuel tank main fuel hose and oil return pipe
assembly
6. Remove fuel pump assembly
7. Discharge fuel
8. Remove front floor bracket
9. Remove front exhaust pipe assembly(a) Move away carpet and remove oxygen sensor joint.
(b) Remove front exhaust pipe assembly10.Disassemble the vent pipe of fuel hose
11.Disassemble filler pipe from fuel tank
12.Remove No. 2 fuel evaporator hose assemblyPress fuel hose joint and then pull out the hose.
Notes:Check there is contaminant that looked like dirt around the
joint before operating and clean it off in the case of
contaminant.Be careful of the contaminant that looked like dirt, because
fast-joint depends on o-ring to seal fuel pipe and joint.Do not perform this operation with tools.Do not bend or distort nylon hose.Cover the joint with plastic bag after removing the fuel hose.When the joint is stuck with fuel pipe, clip the hose with
fingers and rotate carefully to release the hose, and then
remove it.13.Disassemble fuel tank main fuel hose assemblyClip the protrusion part of fixing ring and move lock claw toward
open direction, and then pull out the hose as shown in the
diagram.
Notes:Check there is contaminant looked like dirt around the joint
before operating and clean it off in the case of contaminant. 21 Removing, installing and disassembling, assemblingFuel pipe clipNylon pipeO-ring
Pipe
Page 33 of 419
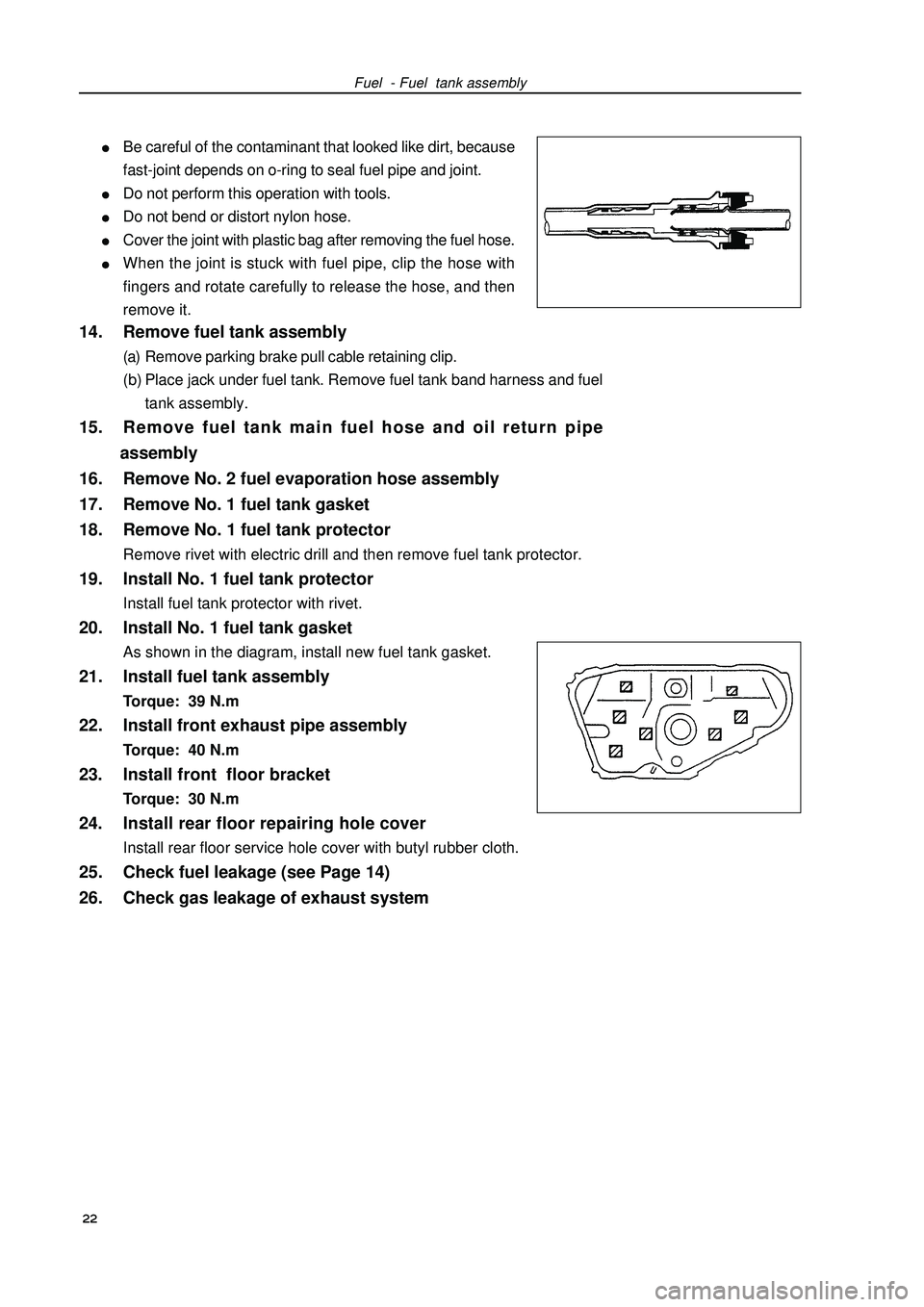
Fuel - Fuel tank assemblyBe careful of the contaminant that looked like dirt, because
fast-joint depends on o-ring to seal fuel pipe and joint.Do not perform this operation with tools.Do not bend or distort nylon hose.Cover the joint with plastic bag after removing the fuel hose.When the joint is stuck with fuel pipe, clip the hose with
fingers and rotate carefully to release the hose, and then
remove it.14. Remove fuel tank assembly(a) Remove parking brake pull cable retaining clip.
(b) Place jack under fuel tank. Remove fuel tank band harness and fuel
tank assembly.15. Remove fuel tank main fuel hose and oil return pipe
assembly
16. Remove No. 2 fuel evaporation hose assembly
17. Remove No. 1 fuel tank gasket
18. Remove No. 1 fuel tank protectorRemove rivet with electric drill and then remove fuel tank protector.19. Install No. 1 fuel tank protectorInstall fuel tank protector with rivet.20. Install No. 1 fuel tank gasketAs shown in the diagram, install new fuel tank gasket.21. Install fuel tank assemblyTorque: 39 N.m22. Install front exhaust pipe assemblyTorque: 40 N.m23. Install front floor bracketTorque: 30 N.m24. Install rear floor repairing hole coverInstall rear floor service hole cover with butyl rubber cloth.25. Check fuel leakage (see Page 14)
26. Check gas leakage of exhaust system
22
Page 34 of 419
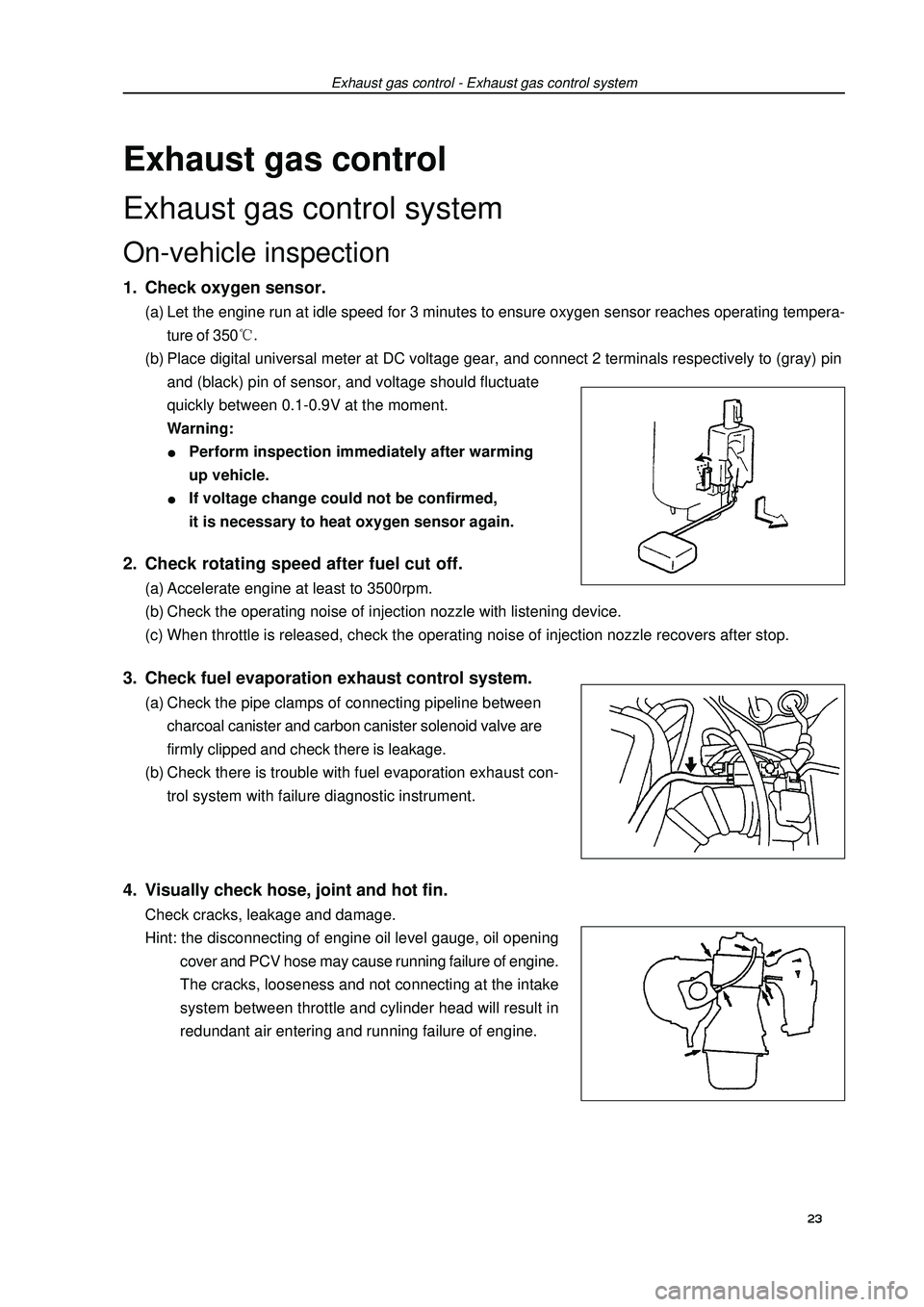
Exhaust gas controlExhaust gas control systemOn-vehicle inspection1. Check oxygen sensor.(a) Let the engine run at idle speed for 3 minutes to ensure oxygen sensor reaches operating tempera-
ture of 350(b) Place digital universal meter at DC voltage gear, and connect 2 terminals respectively to (gray) pin
and (black) pin of sensor, and voltage should fluctuate
quickly between 0.1-0.9V at the moment.
Warning:Perform inspection immediately after warming
up vehicle.If voltage change could not be confirmed,
it is necessary to heat oxygen sensor again.Exhaust gas control - Exhaust gas control system2. Check rotating speed after fuel cut off.(a) Accelerate engine at least to 3500rpm.
(b) Check the operating noise of injection nozzle with listening device.
(c) When throttle is released, check the operating noise of injection nozzle recovers after stop.3. Check fuel evaporation exhaust control system.(a) Check the pipe clamps of connecting pipeline between
charcoal canister and carbon canister solenoid valve are
firmly clipped and check there is leakage.
(b) Check there is trouble with fuel evaporation exhaust con-
trol system with failure diagnostic instrument.4. Visually check hose, joint and hot fin.Check cracks, leakage and damage.
Hint: the disconnecting of engine oil level gauge, oil opening
cover and PCV hose may cause running failure of engine.
The cracks, looseness and not connecting at the intake
system between throttle and cylinder head will result in
redundant air entering and running failure of engine.23
Page 35 of 419
5. Check heater resistance of heated oxygen sensor.(a) Uncouple oxygen sensor joint.
(b) Place digital universal meter at ohm gear, and connect 2 terminals respectively to 1# (white) pin and
2# (black) pin, and the resistance under normal temperature is 166. Check fuel tank cover.Visually check fuel tank cover and gasket are distorted or damaged.Exhaust gas control - Exhaust gas control system 24 Oxygen sensor
Main relay