Page 1970 of 3383
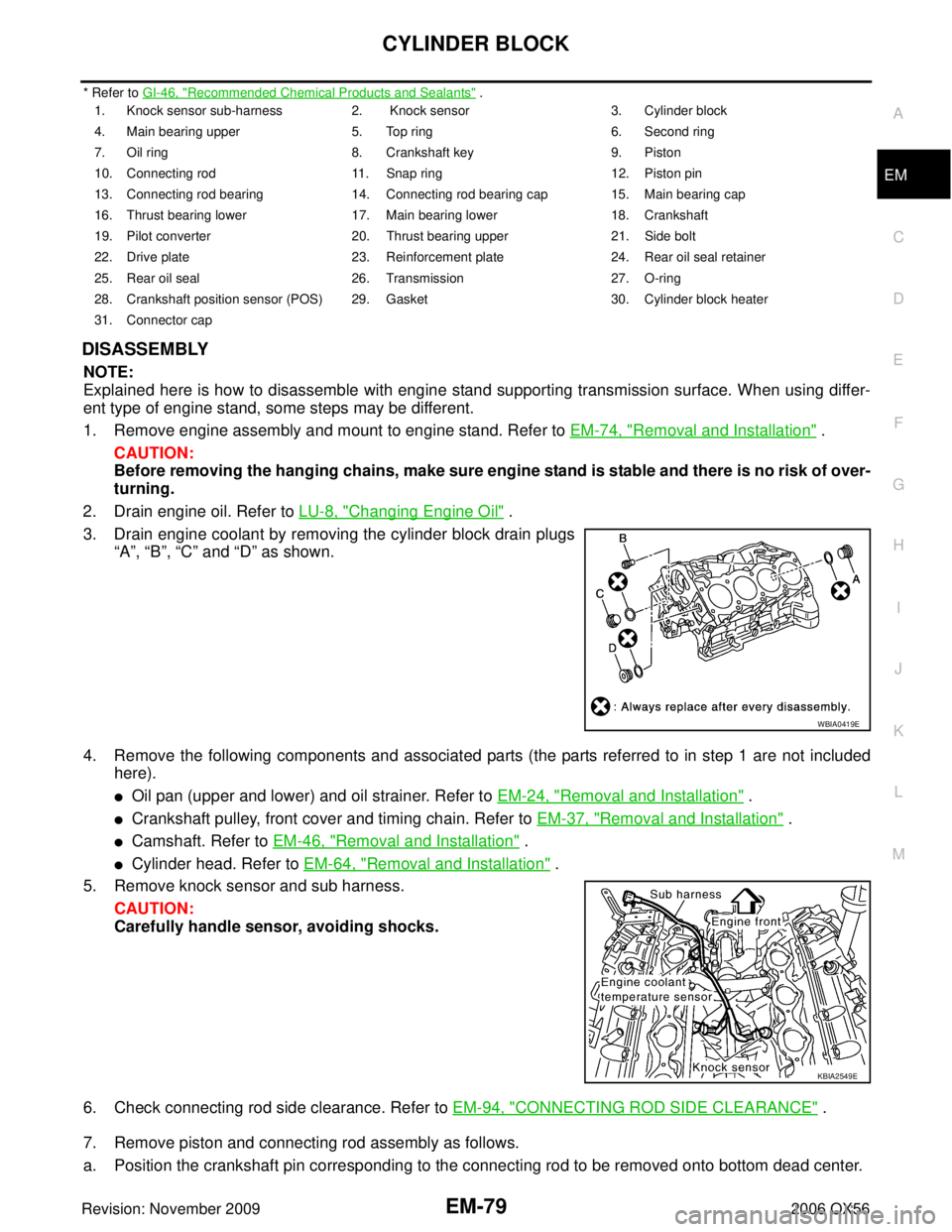
CYLINDER BLOCKEM-79
C
DE
F
G H
I
J
K L
M A
EM
Revision: November 2009 2006 QX56
* Refer to GI-46, "Recommended Chemical Products and Sealants" .
DISASSEMBLY
NOTE:
Explained here is how to disassemble with engine stand supporting transmission surface. When using differ-
ent type of engine stand, some steps may be different.
1. Remove engine assembly and mount to engine stand. Refer to EM-74, "
Removal and Installation" .
CAUTION:
Before removing the hanging chains, make sure engine stand is stable and there is no risk of over-
turning.
2. Drain engine oil. Refer to LU-8, "
Changing Engine Oil" .
3. Drain engine coolant by removing the cylinder block drain plugs “A”, “B ”, “C” and “D ” as shown.
4. Remove the following components and associated parts (the parts referred to in step 1 are not included here).
Oil pan (upper and lower) and oil strainer. Refer to EM-24, "Removal and Installation" .
Crankshaft pulley, front cover and timing chain. Refer to EM-37, "Removal and Installation" .
Camshaft. Refer to EM-46, "Removal and Installation" .
Cylinder head. Refer to EM-64, "Removal and Installation" .
5. Remove knock sensor and sub harness.
CAUTION:
Carefully handle sensor, avoiding shocks.
6. Check connecting rod side clearance. Refer to EM-94, "
CONNECTING ROD SIDE CLEARANCE" .
7. Remove piston and connecting rod assembly as follows.
a. Position the crankshaft pin corresponding to the connecting rod to be removed onto bottom dead center.
1. Knock sensor sub-harness 2. Knock sensor 3. Cylinder block
4. Main bearing upper 5. Top ring 6. Second ring
7. Oil ring 8. Crankshaft key 9. Piston
10. Connecting rod 11. Snap ring 12. Piston pin
13. Connecting rod bearing 14. Connecting rod bearing cap 15. Main bearing cap
16. Thrust bearing lower 17. Main bearing lower 18. Crankshaft
19. Pilot converter 20. Thrust bearing upper 21. Side bolt
22. Drive plate 23. Reinforcement plate 24. Rear oil seal retainer
25. Rear oil seal 26. Transmission 27. O-ring
28. Crankshaft position sensor (POS) 29. Gasket 30. Cylinder block heater
31. Connector cap
WBIA0419E
KBIA2549E
Page 1974 of 3383
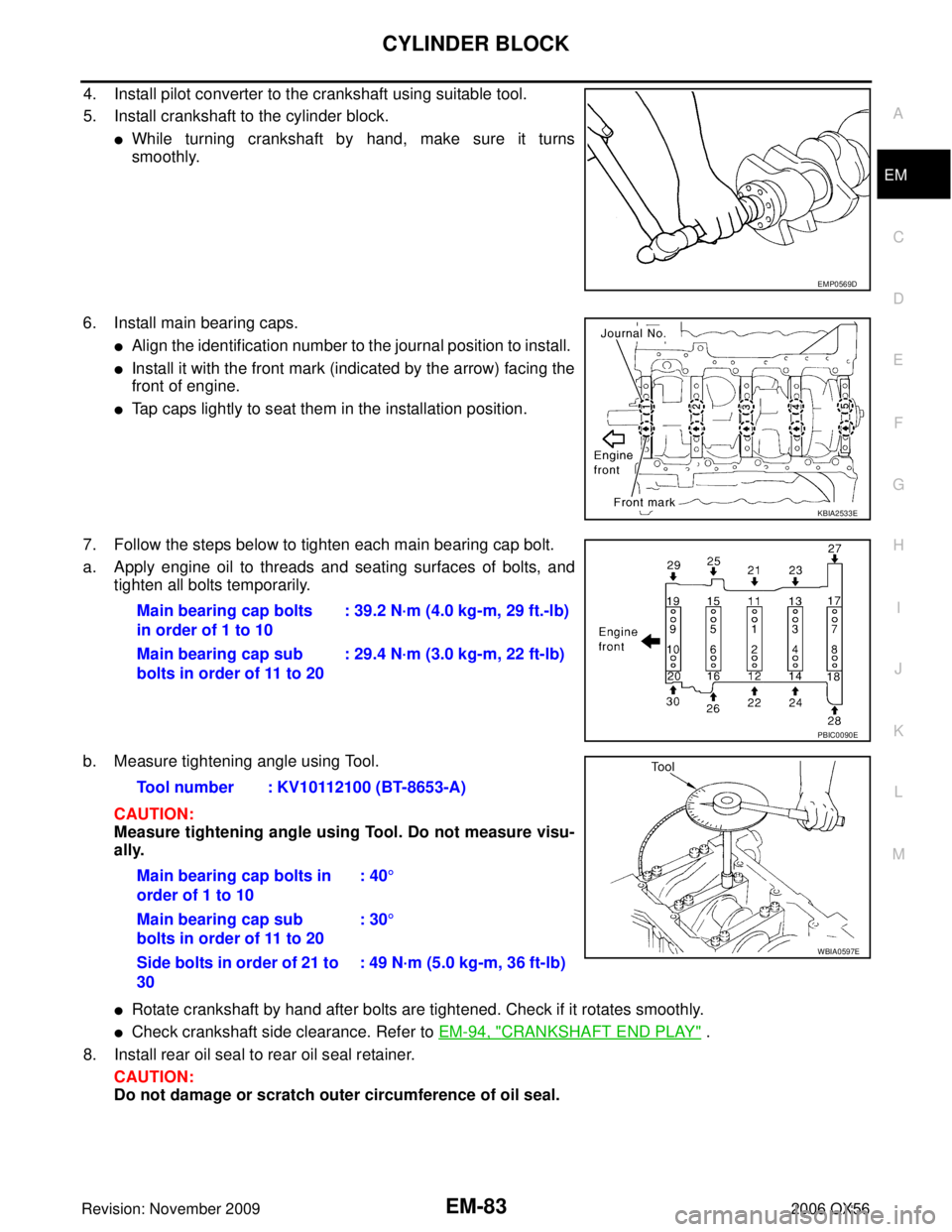
CYLINDER BLOCKEM-83
C
DE
F
G H
I
J
K L
M A
EM
Revision: November 2009 2006 QX56
4. Install pilot converter to the crankshaft using suitable tool.
5. Install crankshaft to the cylinder block.
While turning crankshaft by hand, make sure it turns
smoothly.
6. Install main bearing caps.
Align the identification number to the journal position to install.
Install it with the front mark (indicated by the arrow) facing the
front of engine.
Tap caps lightly to seat them in the installation position.
7. Follow the steps below to tighten each main bearing cap bolt.
a. Apply engine oil to threads and seating surfaces of bolts, and tighten all bolts temporarily.
b. Measure tightening angle using Tool. CAUTION:
Measure tightening angle using Tool. Do not measure visu-
ally.
Rotate crankshaft by hand after bolts are tightened. Check if it rotates smoothly.
Check crankshaft side clearance. Refer to EM-94, "CRANKSHAFT END PLAY" .
8. Install rear oil seal to rear oil seal retainer. CAUTION:
Do not damage or scratch outer circumference of oil seal.
EMP0569D
KBIA2533E
Main bearing cap bolts
in order of 1 to 10 : 39.2 N·m (4.0 kg-m, 29 ft.-lb)
Main bearing cap sub
bolts in order of 11 to 20 : 29.4 N·m (3.0 kg-m, 22 ft-lb)
PBIC0090E
Tool number : KV10112100 (BT-8653-A)
Main bearing cap bolts in
order of 1 to 10 : 40
°
Main bearing cap sub
bolts in order of 11 to 20 : 30
°
Side bolts in order of 21 to
30 : 49 N·m (5.0 kg-m, 36 ft-lb)
WBIA0597E
Page 1976 of 3383
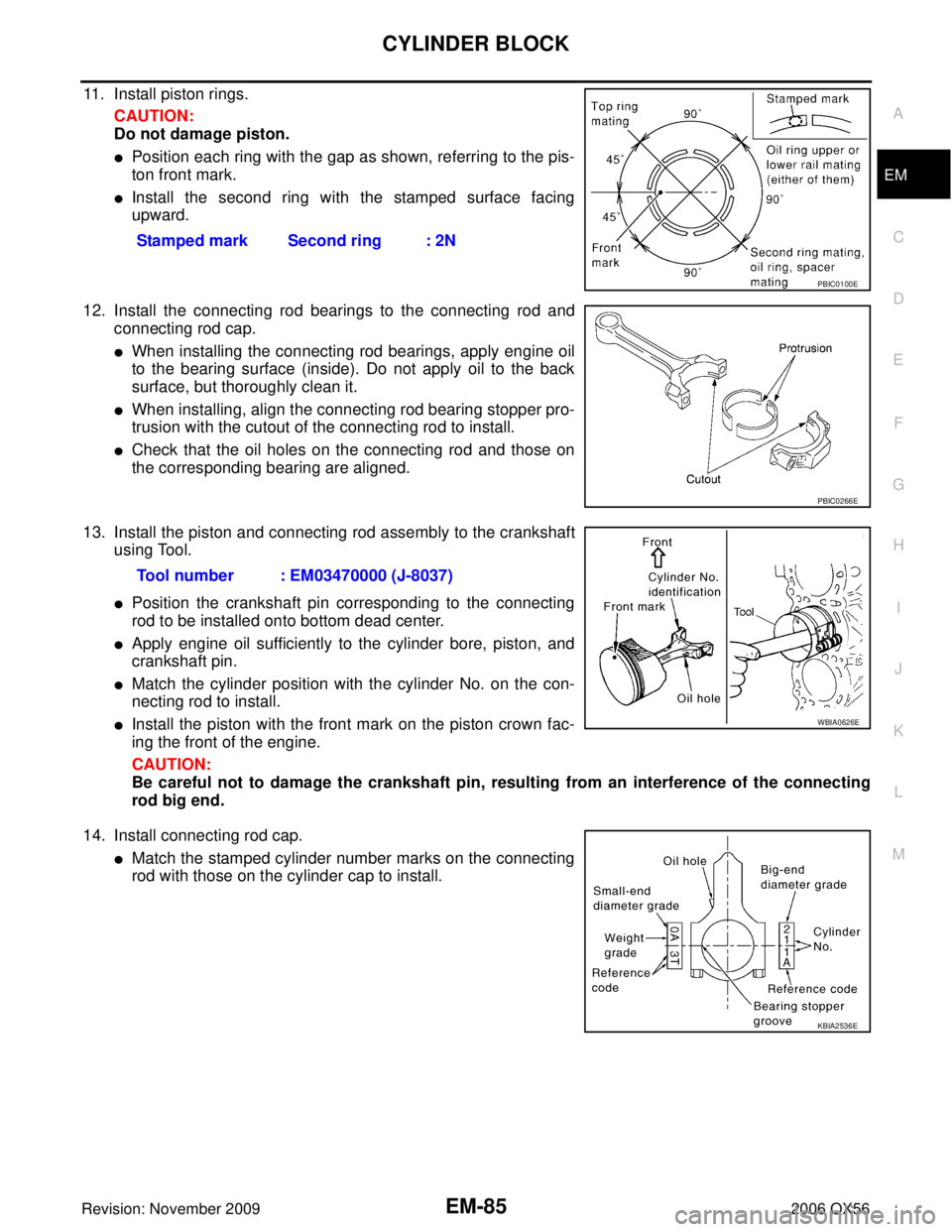
CYLINDER BLOCKEM-85
C
DE
F
G H
I
J
K L
M A
EM
Revision: November 2009 2006 QX56
11. Install piston rings.
CAUTION:
Do not damage piston.
Position each ring with the gap as shown, referring to the pis-
ton front mark.
Install the second ring with the stamped surface facing
upward.
12. Install the connecting rod bearings to the connecting rod and connecting rod cap.
When installing the connecting rod bearings, apply engine oil
to the bearing surface (inside). Do not apply oil to the back
surface, but thoroughly clean it.
When installing, align the connecting rod bearing stopper pro-
trusion with the cutout of the connecting rod to install.
Check that the oil holes on the connecting rod and those on
the corresponding bearing are aligned.
13. Install the piston and connecting rod assembly to the crankshaft using Tool.
Position the crankshaft pin corresponding to the connecting
rod to be installed onto bottom dead center.
Apply engine oil sufficiently to the cylinder bore, piston, and
crankshaft pin.
Match the cylinder position with the cylinder No. on the con-
necting rod to install.
Install the piston with the front mark on the piston crown fac-
ing the front of the engine.
CAUTION:
Be careful not to damage the crankshaft pin, resulting from an interference of the connecting
rod big end.
14. Install connecting rod cap.
Match the stamped cylinder number marks on the connecting
rod with those on the cylinder cap to install. Stamped mark Second ring : 2N
PBIC0100E
PBIC0266E
Tool number : EM03470000 (J-8037)
WBIA0626E
KBIA2536E
Page 1977 of 3383
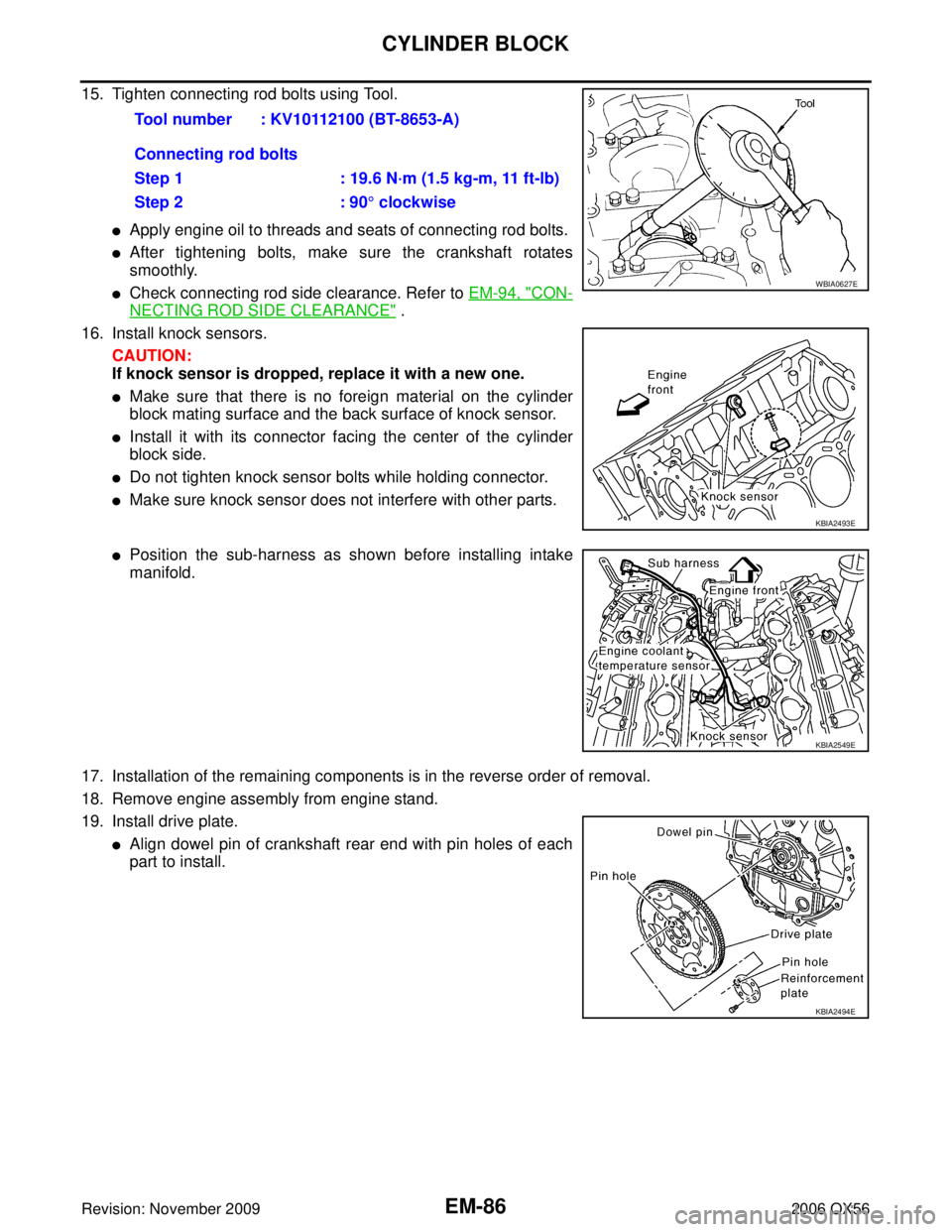
EM-86Revision: November 2009
CYLINDER BLOCK
2006 QX56
15. Tighten connecting rod bolts using Tool.
Apply engine oil to threads and seats of connecting rod bolts.
After tightening bolts, make sure the crankshaft rotates
smoothly.
Check connecting rod side clearance. Refer to EM-94, "CON-
NECTING ROD SIDE CLEARANCE" .
16. Install knock sensors. CAUTION:
If knock sensor is dropped, replace it with a new one.
Make sure that there is no foreign material on the cylinder
block mating surface and the back surface of knock sensor.
Install it with its connector facing the center of the cylinder
block side.
Do not tighten knock sensor bolts while holding connector.
Make sure knock sensor does not interfere with other parts.
Position the sub-harness as shown before installing intake
manifold.
17. Installation of the remaining components is in the reverse order of removal.
18. Remove engine assembly from engine stand.
19. Install drive plate.
Align dowel pin of crankshaft rear end with pin holes of each
part to install. Tool number : KV10112100 (BT-8653-A)
Connecting rod bolts
Step 1
: 19.6 N·m (1.5 kg-m, 11 ft-lb)
Step 2 : 90° clockwise
WBIA0627E
KBIA2493E
KBIA2549E
KBIA2494E
Page 2006 of 3383
EX-1
EXHAUST SYSTEM
B ENGINE
CONTENTS
C
DE
F
G H
I
J
K L
M
SECTION
A
EX
Revision: November 2009 2006 QX56
PREPARATION ......................................................
..... 2
Special Service Tool ............................................ ..... 2
Commercial Service Tools ................................... ..... 2
EXHAUST SYSTEM ................................................... 3 Checking Exhaust System ...................................
..... 3
Removal and Installation ..................................... ..... 3
REMOVAL ........................................................ ..... 4
INSTALLATION ................................................ ..... 4
INSPECTION AFTER INSTALLATION ............. ..... 4
Page 2008 of 3383
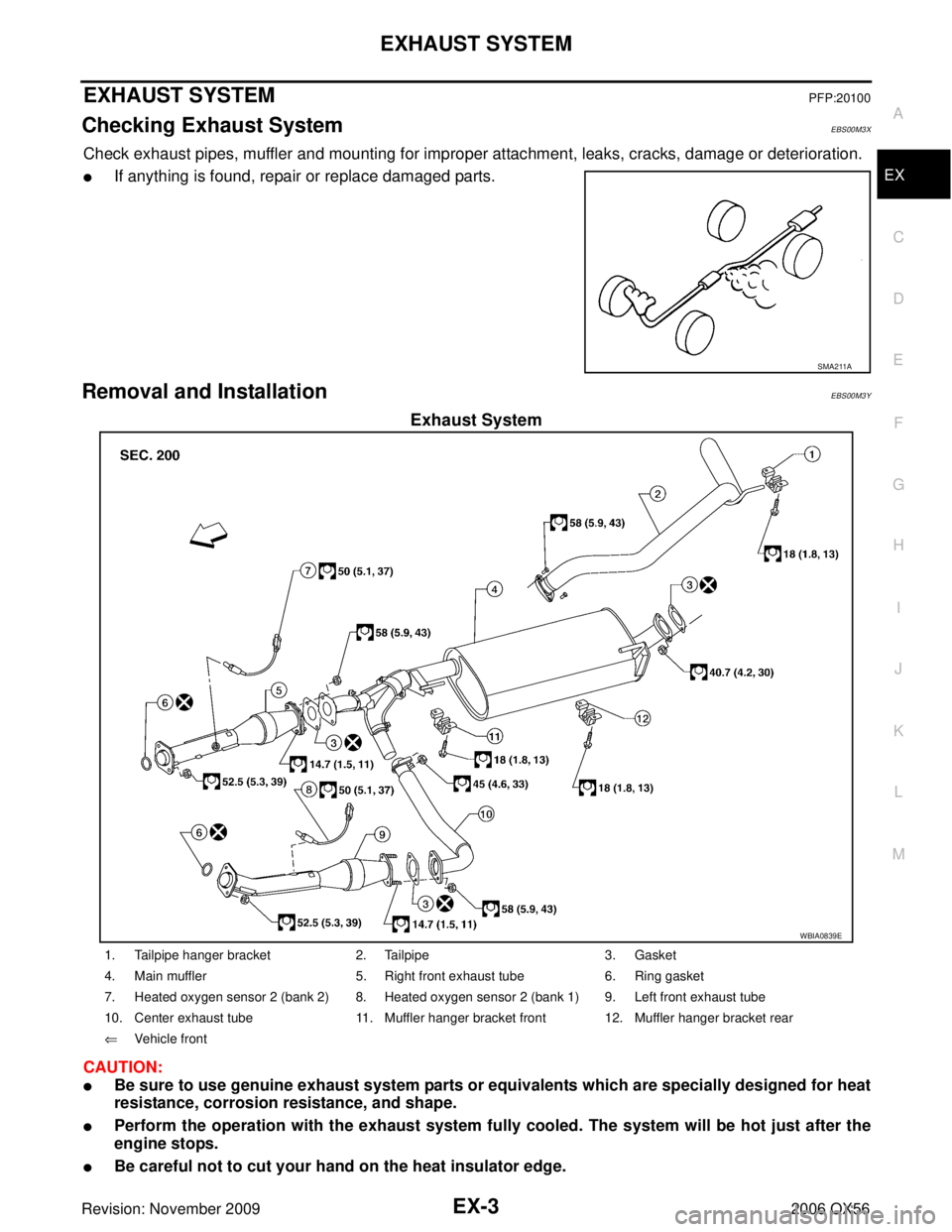
EXHAUST SYSTEMEX-3
C
DE
F
G H
I
J
K L
M A
EX
Revision: November 2009 2006 QX56
EXHAUST SYSTEMPFP:20100
Checking Exhaust SystemEBS00M3X
Check exhaust pipes, muffler and mounting for improper attachment, leaks, cracks, damage or deterioration.
If anything is found, repair or replace damaged parts.
Removal and InstallationEBS00M3Y
Exhaust System
CAUTION:
Be sure to use genuine exhaust system parts or equivalents which are specially designed for heat
resistance, corrosion resistance, and shape.
Perform the operation with the exhaust system fully cooled. The system will be hot just after the
engine stops.
Be careful not to cut your hand on the heat insulator edge.
SMA211A
WBIA0839E
1. Tailpipe hanger bracket2. Tailpipe3. Gasket
4. Main muffler 5. Right front exhaust tube6. Ring gasket
7. Heated oxygen sensor 2 (bank 2) 8. Heated oxygen sensor 2 (bank 1) 9. Left front exhaust tube
10. Center exhaust tube 11. Muffler hanger bracket front 12. Muffler hanger bracket rear
⇐ Vehicle front
Page 2009 of 3383
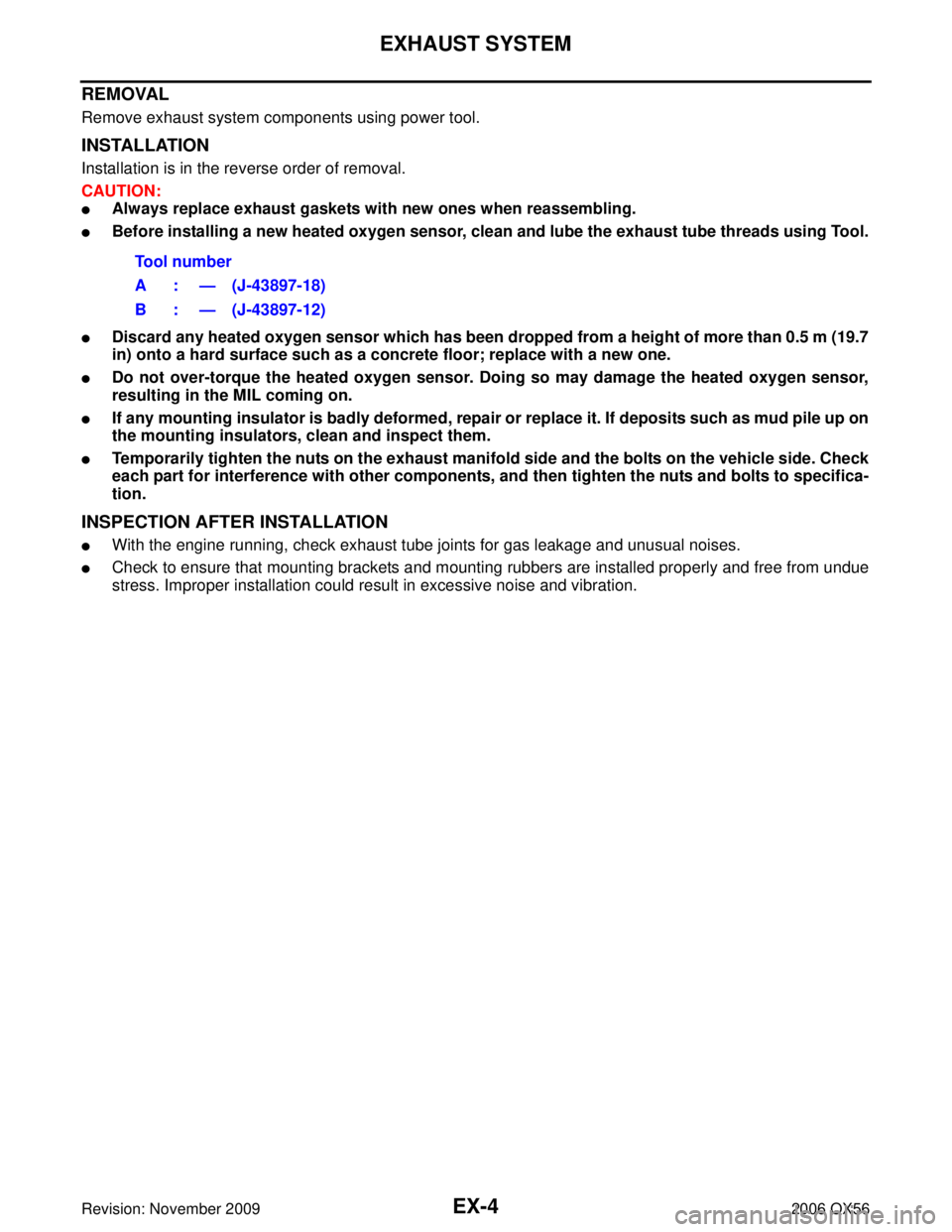
EX-4Revision: November 2009
EXHAUST SYSTEM
2006 QX56
REMOVAL
Remove exhaust system components using power tool.
INSTALLATION
Installation is in the reverse order of removal.
CAUTION:
Always replace exhaust gaskets with new ones when reassembling.
Before installing a new heated oxygen sensor, clean and lube the exhaust tube threads using Tool.
Discard any heated oxygen sensor which has been dropped from a height of more than 0.5 m (19.7
in) onto a hard surface such as a concrete floor; replace with a new one.
Do not over-torque the heated oxygen sensor. Doing so may damage the heated oxygen sensor,
resulting in the MIL coming on.
If any mounting insulator is badly deformed, repair or replace it. If deposits such as mud pile up on
the mounting insulators, clean and inspect them.
Temporarily tighten the nuts on the exhaust manifold side and the bolts on the vehicle side. Check
each part for interference with other components, and then tighten the nuts and bolts to specifica-
tion.
INSPECTION AFTER INSTALLATION
With the engine running, check exhaust tube joints for gas leakage and unusual noises.
Check to ensure that mounting brackets and mounting rubbers are installed properly and free from undue
stress. Improper installation could result in excessive noise and vibration. Tool number
A : — (J-43897-18)
B : — (J-43897-12)
Page 2016 of 3383
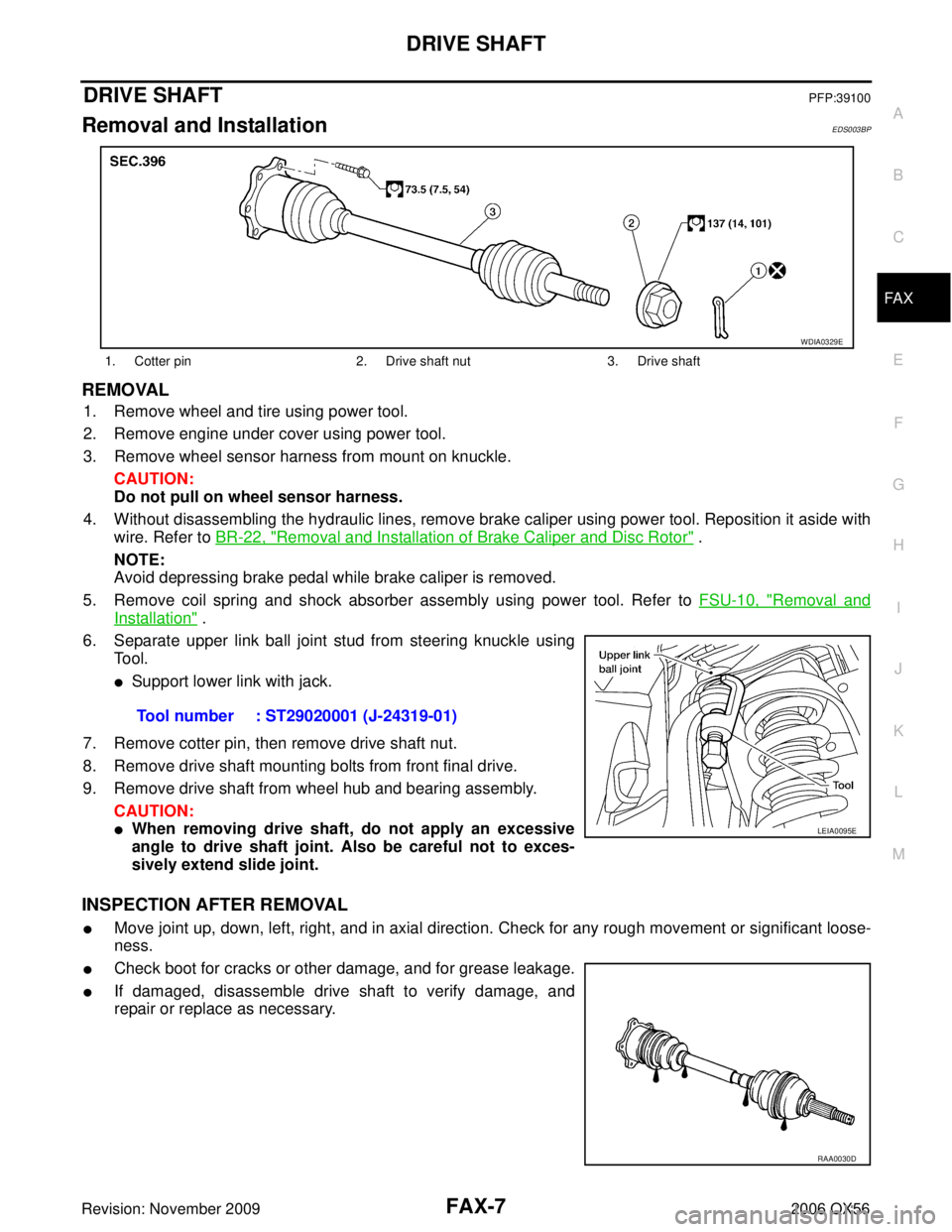
DRIVE SHAFTFAX-7
CE F
G H
I
J
K L
M A
B
FA X
Revision: November 2009 2006 QX56
DRIVE SHAFTPFP:39100
Removal and InstallationEDS003BP
REMOVAL
1. Remove wheel and tire using power tool.
2. Remove engine under cover using power tool.
3. Remove wheel sensor harness from mount on knuckle.
CAUTION:
Do not pull on wheel sensor harness.
4. Without disassembling the hydraulic lines, remove brake caliper using power tool. Reposition it aside with wire. Refer to BR-22, "
Removal and Installation of Brake Caliper and Disc Rotor" .
NOTE:
Avoid depressing brake pedal while brake caliper is removed.
5. Remove coil spring and shock absorber assembly using power tool. Refer to FSU-10, "
Removal and
Installation" .
6. Separate upper link ball joint stud from steering knuckle using To o l .
Support lower link with jack.
7. Remove cotter pin, then remove drive shaft nut.
8. Remove drive shaft mounting bolts from front final drive.
9. Remove drive shaft from wheel hub and bearing assembly. CAUTION:
When removing drive shaft, do not apply an excessive
angle to drive shaft joint. Also be careful not to exces-
sively extend slide joint.
INSPECTION AFTER REMOVAL
Move joint up, down, left, right, and in axial direction. Check for any rough movement or significant loose-
ness.
Check boot for cracks or other damage, and for grease leakage.
If damaged, disassemble drive shaft to verify damage, and
repair or replace as necessary.
1. Cotter pin 2. Drive shaft nut3. Drive shaft
WDIA0329E
Tool number : ST29020001 (J-24319-01)
LEIA0095E
RAA0030D