Page 2566 of 3383
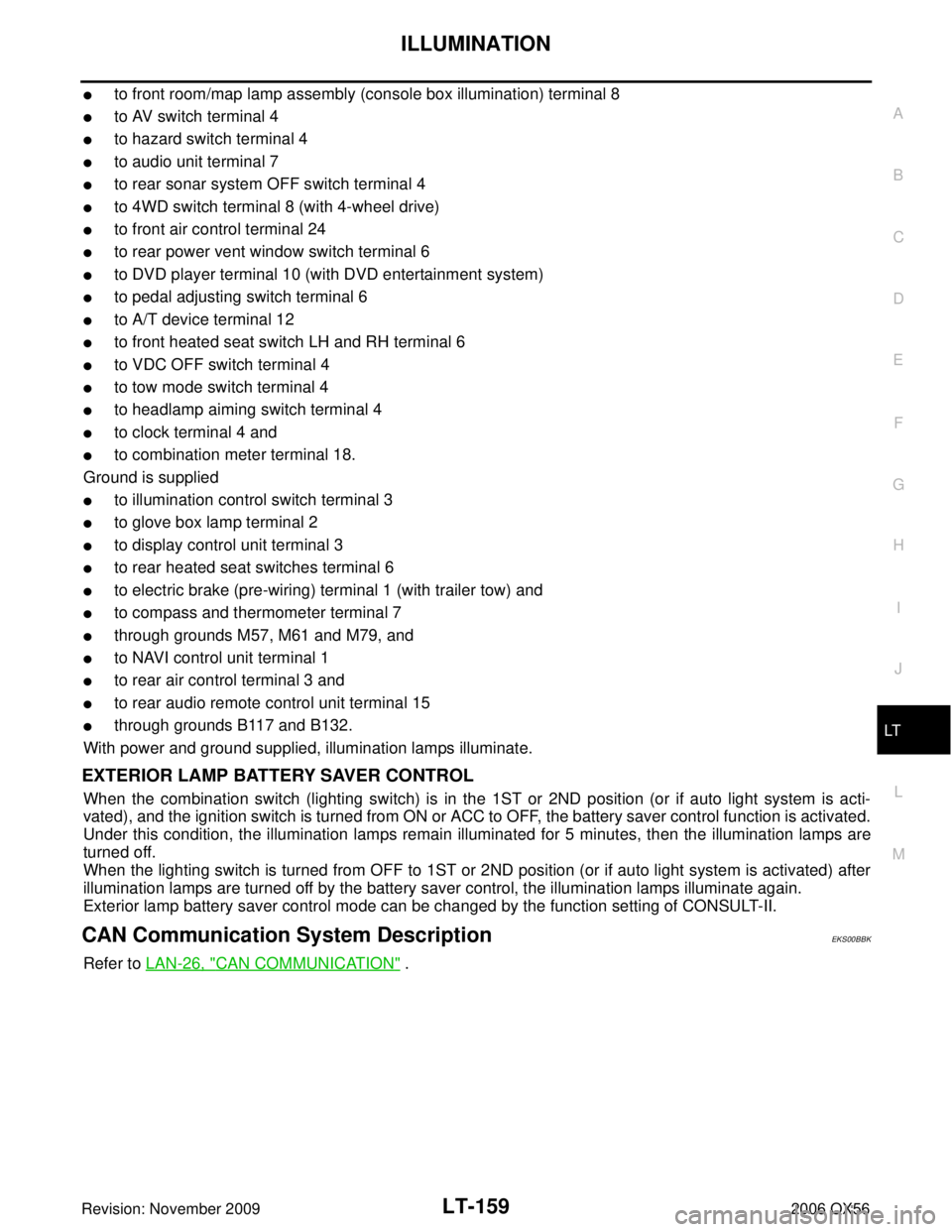
ILLUMINATIONLT-159
C
DE
F
G H
I
J
L
M A
B
LT
Revision: November 2009 2006 QX56
to front room/map lamp assembly (console box illumination) terminal 8
to AV switch terminal 4
to hazard switch terminal 4
to audio unit terminal 7
to rear sonar system OFF switch terminal 4
to 4WD switch terminal 8 (with 4-wheel drive)
to front air control terminal 24
to rear power vent window switch terminal 6
to DVD player terminal 10 (with DVD entertainment system)
to pedal adjusting switch terminal 6
to A/T device terminal 12
to front heated seat switch LH and RH terminal 6
to VDC OFF switch terminal 4
to tow mode switch terminal 4
to headlamp aiming switch terminal 4
to clock terminal 4 and
to combination meter terminal 18.
Ground is supplied
to illumination control switch terminal 3
to glove box lamp terminal 2
to display control unit terminal 3
to rear heated seat switches terminal 6
to electric brake (pre-wiring) terminal 1 (with trailer tow) and
to compass and thermometer terminal 7
through grounds M57, M61 and M79, and
to NAVI control unit terminal 1
to rear air control terminal 3 and
to rear audio remote control unit terminal 15
through grounds B117 and B132.
With power and ground supplied, illumination lamps illuminate.
EXTERIOR LAMP BATTERY SAVER CONTROL
When the combination switch (lighting switch) is in the 1ST or 2ND position (or if auto light system is acti-
vated), and the ignition switch is turned from ON or ACC to OFF, the battery saver control function is activated.
Under this condition, the illumination lamps remain illuminated for 5 minutes, then the illumination lamps are
turned off.
When the lighting switch is turned from OFF to 1ST or 2ND position (or if auto light system is activated) after
illumination lamps are turned off by the battery saver control, the illumination lamps illuminate again.
Exterior lamp battery saver control mode can be changed by the function setting of CONSULT-II.
CAN Communication System DescriptionEKS00BBK
Refer to LAN-26, "CAN COMMUNICATION" .
Page 2585 of 3383
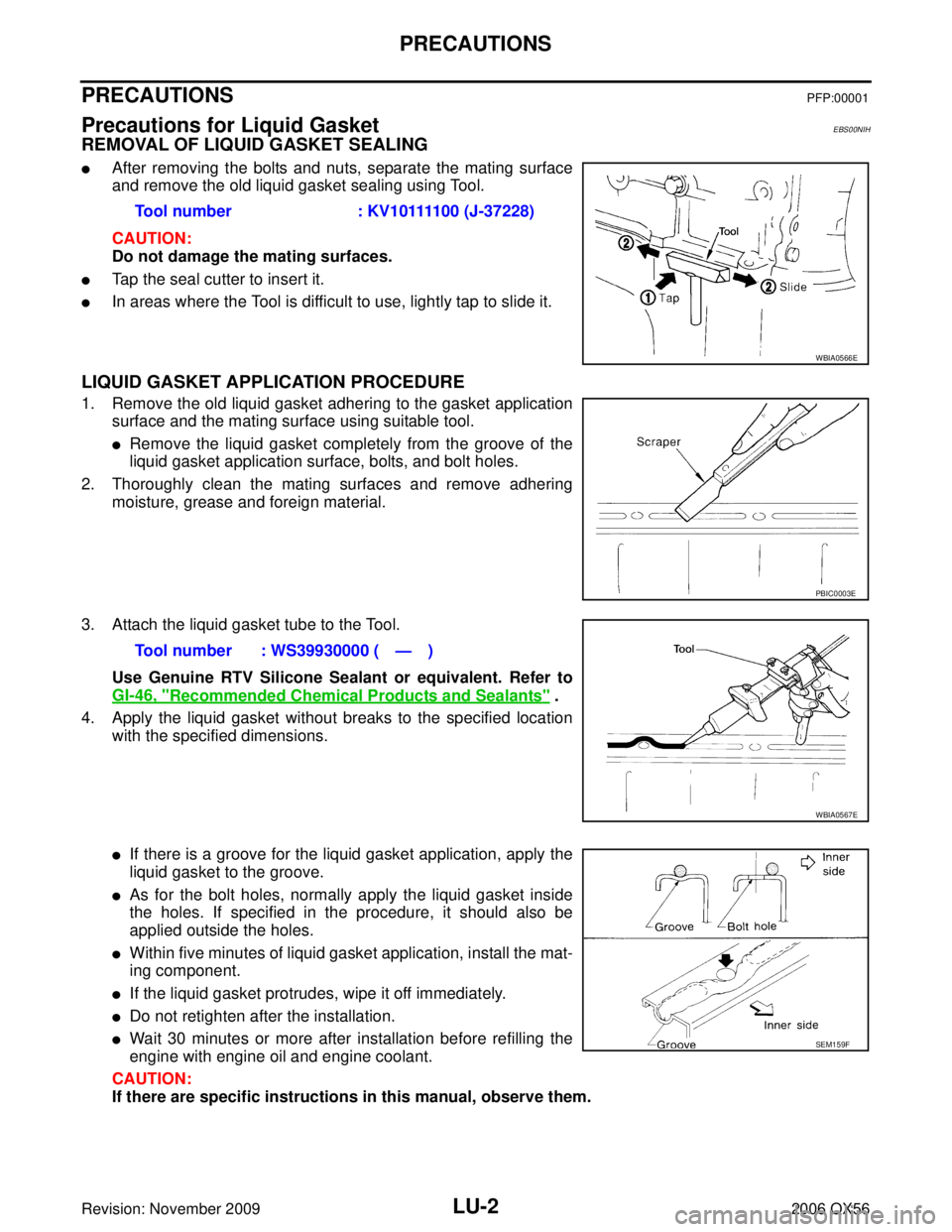
LU-2Revision: November 2009
PRECAUTIONS
2006 QX56
PRECAUTIONSPFP:00001
Precautions for Liquid GasketEBS00NIH
REMOVAL OF LIQUID GASKET SEALING
After removing the bolts and nuts, separate the mating surface
and remove the old liquid gasket sealing using Tool.
CAUTION:
Do not damage the mating surfaces.
Tap the seal cutter to insert it.
In areas where the Tool is difficult to use, lightly tap to slide it.
LIQUID GASKET APPLICATION PROCEDURE
1. Remove the old liquid gasket adhering to the gasket applicationsurface and the mating surface using suitable tool.
Remove the liquid gasket completely from the groove of the
liquid gasket application surface, bolts, and bolt holes.
2. Thoroughly clean the mating surfaces and remove adhering moisture, grease and foreign material.
3. Attach the liquid gasket tube to the Tool. Use Genuine RTV Silicone Sealant or equivalent. Refer to
GI-46, "
Recommended Chemical Products and Sealants" .
4. Apply the liquid gasket without breaks to the specified location with the specified dimensions.
If there is a groove for the liquid gasket application, apply the
liquid gasket to the groove.
As for the bolt holes, normally apply the liquid gasket inside
the holes. If specified in the procedure, it should also be
applied outside the holes.
Within five minutes of liquid gasket application, install the mat-
ing component.
If the liquid gasket protrudes, wipe it off immediately.
Do not retighten after the installation.
Wait 30 minutes or more after installation before refilling the
engine with engine oil and engine coolant.
CAUTION:
If there are specific instructions in this manual, observe them. Tool number
: KV10111100 (J-37228)
WBIA0566E
PBIC0003E
Tool number : WS39930000 ( — )
WBIA0567E
SEM159F
Page 2596 of 3383
OIL PUMPLU-13
C
DE
F
G H
I
J
K L
M A
LU
Revision: November 2009 2006 QX56
OIL PUMPPFP:15010
Removal and InstallationEBS00LMW
REMOVAL
1. Remove front cover. Refer to EM-38, "REMOVAL" .
2. Remove the oil pump drive spacer.
3. Remove the oil pump.
INSTALLATION
Installation is in the reverse order of removal, paying attention of the following:
When inserting the oil pump drive spacer, align the crankshaft
key and the flat face of the inner rotor.
If they are not aligned, rotate the oil pump inner rotor by hand.
Make sure that the each part is aligned and tap lightly until it
reaches the end.
WBIA0415E
1. Oil pump body 2. Outer rotor3. Inner rotor
4. Oil pump cover 5. Oil pump drive spacer6. Regulator valve
7. Regulator spring 8. Regulator plug
KBIA2512E
KBIA2490E
Page 2614 of 3383
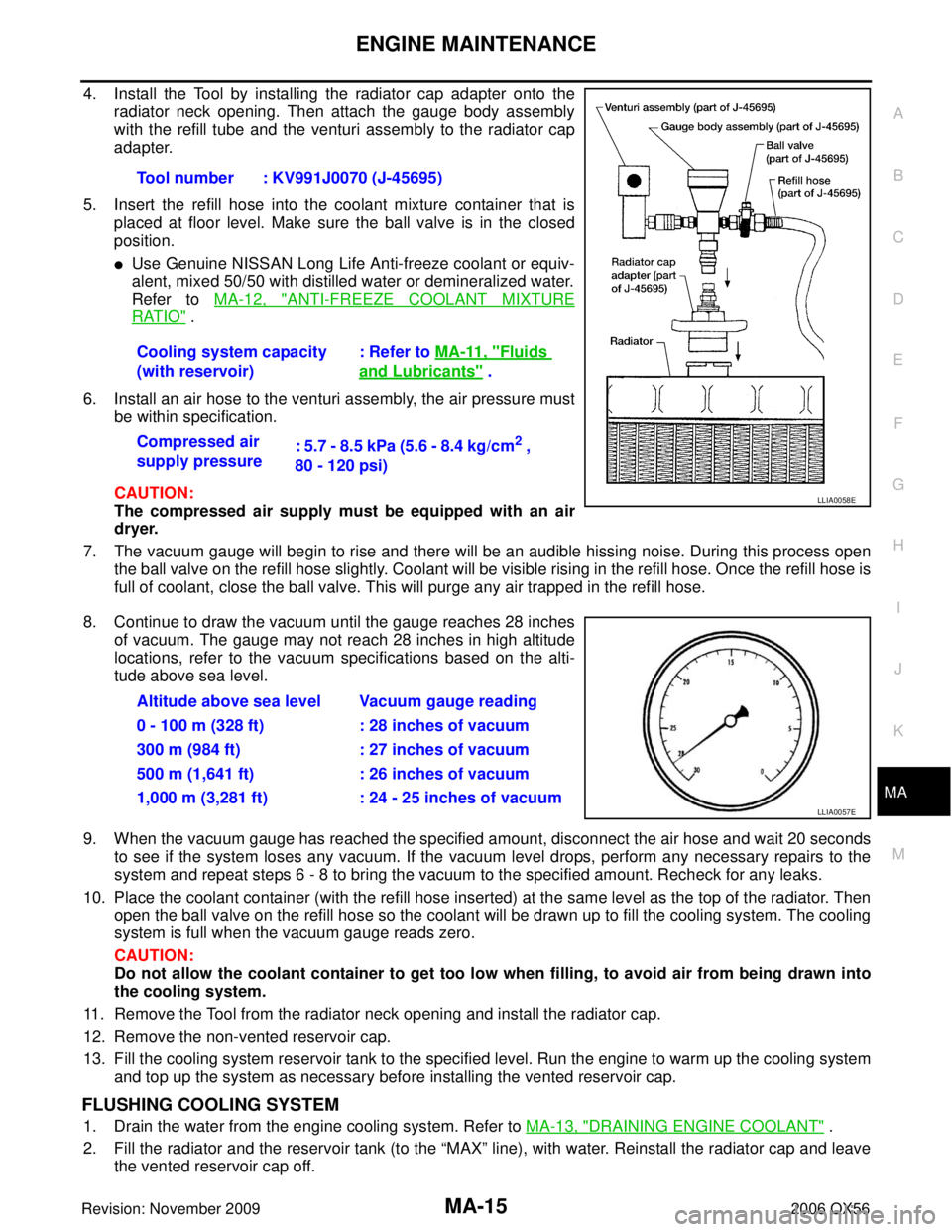
ENGINE MAINTENANCEMA-15
C
DE
F
G H
I
J
K
M A
B
MA
Revision: November 2009 2006 QX56
4. Install the Tool by installing the radiator cap adapter onto the
radiator neck opening. Then attach the gauge body assembly
with the refill tube and the venturi assembly to the radiator cap
adapter.
5. Insert the refill hose into the coolant mixture container that is placed at floor level. Make sure the ball valve is in the closed
position.
Use Genuine NISSAN Long Life Anti-freeze coolant or equiv-
alent, mixed 50/50 with distilled water or demineralized water.
Refer to MA-12, "
ANTI-FREEZE COOLANT MIXTURE
RATIO" .
6. Install an air hose to the venturi assembly, the air pressure must be within specification.
CAUTION:
The compressed air supply must be equipped with an air
dryer.
7. The vacuum gauge will begin to rise and there will be an audible hissing noise. During this process open the ball valve on the refill hose slightly. Coolant will be visible rising in the refill hose. Once the refill hose is
full of coolant, close the ball valve. This will purge any air trapped in the refill hose.
8. Continue to draw the vacuum until the gauge reaches 28 inches of vacuum. The gauge may not reach 28 inches in high altitude
locations, refer to the vacuum specifications based on the alti-
tude above sea level.
9. When the vacuum gauge has reached the specified amount, disconnect the air hose and wait 20 seconds to see if the system loses any vacuum. If the vacuum level drops, perform any necessary repairs to the
system and repeat steps 6 - 8 to bring the vacuum to the specified amount. Recheck for any leaks.
10. Place the coolant container (with the refill hose inserted) at the same level as the top of the radiator. Then open the ball valve on the refill hose so the coolant will be drawn up to fill the cooling system. The cooling
system is full when the vacuum gauge reads zero.
CAUTION:
Do not allow the coolant container to get too low when filling, to avoid air from being drawn into
the cooling system.
11. Remove the Tool from the radiator neck opening and install the radiator cap.
12. Remove the non-vented reservoir cap.
13. Fill the cooling system reservoir tank to the specified level. Run the engine to warm up the cooling system and top up the system as necessary before installing the vented reservoir cap.
FLUSHING COOLING SYSTEM
1. Drain the water from the engine cooling system. Refer to MA-13, "DRAINING ENGINE COOLANT" .
2. Fill the radiator and the reservoir tank (to the “MAX” line), with water. Reinstall the radiator cap and leave
the vented reservoir cap off. Tool number : KV991J0070 (J-45695)
Cooling system capacity
(with reservoir)
: Refer to
MA-11, "
Fluids
and Lubricants" .
Compressed air
supply pressure : 5.7 - 8.5 kPa (5.6 - 8.4 kg/cm
2 ,
80 - 120 psi)
LLIA0058E
Altitude above sea level Vacuum gauge reading
0 - 100 m (328 ft) : 28 inches of vacuum
300 m (984 ft) : 27 inches of vacuum
500 m (1,641 ft) : 26 inches of vacuum
1,000 m (3,281 ft) : 24 - 25 inches of vacuum
LLIA0057E
Page 2703 of 3383
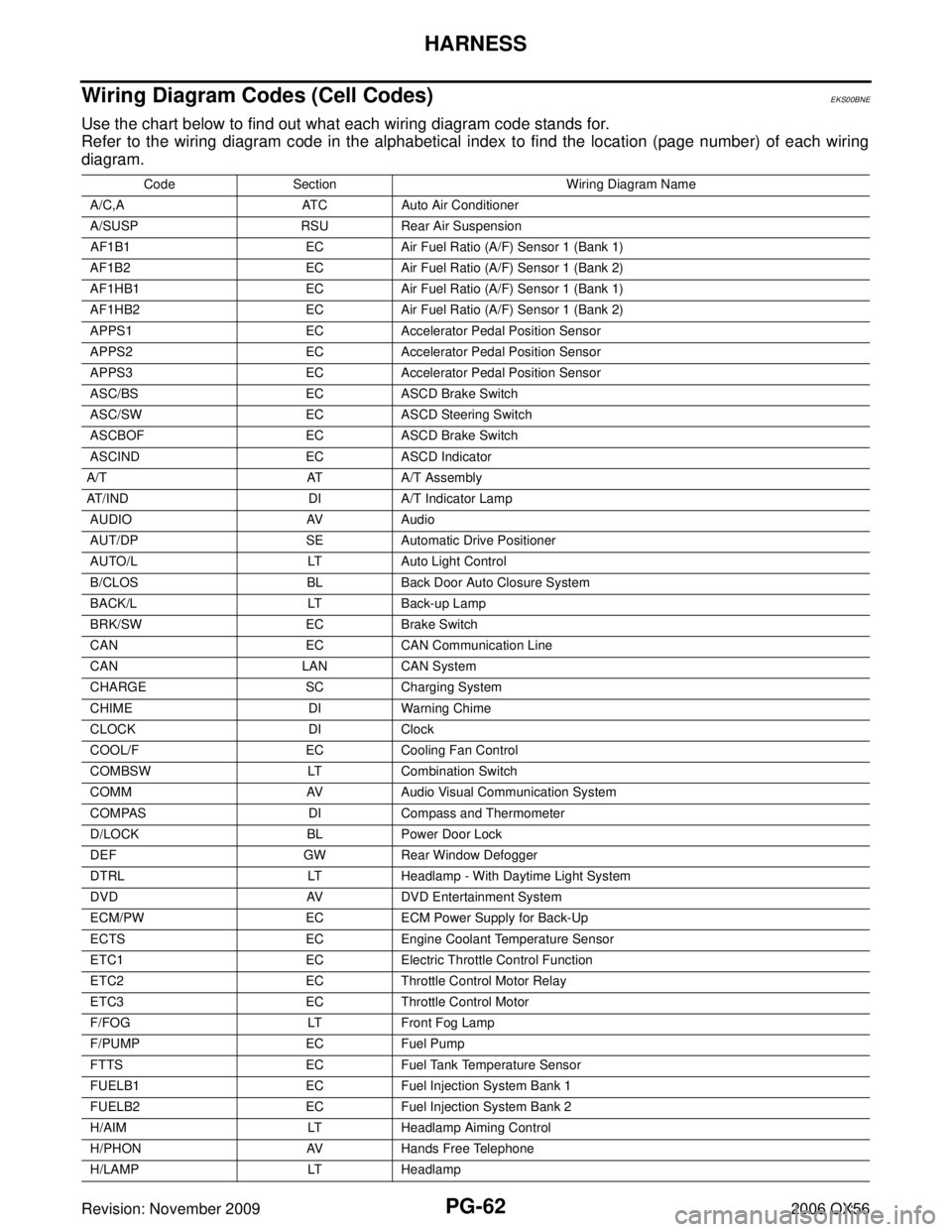
PG-62
HARNESS
Revision: November 20092006 QX56
Wiring Diagram Codes (Cell Codes)EKS00BNE
Use the chart below to find out what each wiring diagram code stands for.
Refer to the wiring diagram code in the alphabetical index to find the location (page number) of each wiring
diagram.
CodeSection Wiring Diagram Name
A/C,A ATC Auto Air Conditioner
A/SUSP RSU Rear Air Suspension
AF1B1 EC Air Fuel Ratio (A/F) Sensor 1 (Bank 1)
AF1B2 EC Air Fuel Ratio (A/F) Sensor 1 (Bank 2)
AF1HB1 EC Air Fuel Ratio (A/F) Sensor 1 (Bank 1)
AF1HB2 EC Air Fuel Ratio (A/F) Sensor 1 (Bank 2)
APPS1 EC Accelerator Pedal Position Sensor
APPS2 EC Accelerator Pedal Position Sensor
APPS3 EC Accelerator Pedal Position Sensor
ASC/BS EC ASCD Brake Switch
ASC/SW EC ASCD Steering Switch
ASCBOF EC ASCD Brake Switch
ASCIND EC ASCD Indicator
A/T AT A/T Assembly
AT/IND DI A/T Indicator Lamp
AUDIO AV Audio
AUT/DP SE Automatic Drive Positioner
AUTO/L LT Auto Light Control
B/CLOS BL Back Door Auto Closure System
BACK/L LT Back-up Lamp
BRK/SW EC Brake Switch
CAN EC CAN Communication Line
CAN LAN CAN System
CHARGE SC Charging System
CHIME DI Warning Chime
CLOCK DI Clock
COOL/F EC Cooling Fan Control
COMBSW LT Combination Switch
COMM AV Audio Visual Communication System
COMPAS DI Compass and Thermometer
D/LOCK BL Power Door Lock
DEF GW Rear Window Defogger
DTRL LT Headlamp - With Daytime Light System
DVD AV DVD Entertainment System
ECM/PW EC ECM Power Supply for Back-Up
ECTS EC Engine Coolant Temperature Sensor
ETC1 EC Electric Throttle Control Function
ETC2 EC Throttle Control Motor Relay
ETC3 EC Throttle Control Motor
F/FOG LT Front Fog Lamp
F/PUMP EC Fuel Pump
FTTS EC Fuel Tank Temperature Sensor
FUELB1 EC Fuel Injection System Bank 1
FUELB2 EC Fuel Injection System Bank 2
H/AIM LT Headlamp Aiming Control
H/PHON AV Hands Free Telephone
H/LAMP LT Headlamp
Page 2725 of 3383
PR-6
FRONT PROPELLER SHAFT
Revision: November 20092006 QX56
2. Remove the snap ring.
3. Push out and remove the journal bearing by lightly tapping the
yoke with a hammer, taking care not to damage the journal or
yoke hole.
4. Remove the bearing at the opposite side in above operation. NOTE:
Put marks on the disassembled parts so that they can be rein-
stalled in their original positions from which they were removed.
ASSEMBLY
Journal
1. Assemble the journal bearings. Apply multipurpose grease onthe bearing inner surface.
NOTE:
During assembly, use caution so that the needle bearings do not
fall down.
APD011
SPD732
SPD131
WPD019
Page 2729 of 3383
PR-10
REAR PROPELLER SHAFT
Revision: November 20092006 QX56
Disassembly and AssemblyEDS001WA
DISASSEMBLY
Journal
1. Put matching marks on the rear propeller shaft and flange yoke
as shown.
CAUTION:
For matching marks use paint. Never damage the rear pro-
peller shaft or flange yoke.
2. Remove the snap ring.
3. Push out and remove the journal bearing by lightly tapping the yoke with a hammer, taking care not to damage the journal or
yoke hole.
4. Remove the bearing at the opposite side of above operation. NOTE:
Put marks on the disassembled parts so that they can be rein-
stalled in their original positions from which they were removed.
SPD128
APD011
SPD732
SPD131
Page 2732 of 3383
SERVICE DATA AND SPECIFICATIONS (SDS)PR-13
CE F
G H
I
J
K L
M A
B
PR
Revision: November 2009 2006 QX56
Snap RingEDS001WC
Model 2F1310
Unit: mm (in)
*Always check with the Parts Department for the latest parts information.
Model 2S1350
Unit: mm (in)
*Always check with the Parts Department for the latest parts information. Thickness
ColorPart Number*
1.99 (0.0783) White37146-C9400
2.02 (0.0795) Yellow37147-C9400
2.05 (0.0807) Red37148-C9400
2.08 (0.0819) Green37149-C9400
2.11 (0.0831) Blue37150-C9400
2.14 (0.0843) Light brown 37151-C9400
2.17 (0.0854) Black37152-C9400
2.20 (0.0866) No paint37153-C9400
Thickness ColorPart Number*
1.600 - 1.638 (0.0630 - 0.0645) Black37146-7S000
1.549 - 1.588 (0.0610 - 0.0625) Black37147-7S000
1.524 - 1.562 (0.0600 - 0.0615) Black37148-7S000
1.499 - 1.537 (0.0590 - 0.0605) Black37149-7S000