Page 40 of 364
ENGINE – ENGINE ASSY11-34
D
Fitting the O-ring and the fuel high pressure hose
1. Apply a little fresh engine oil to the O-ring.
Caution
Ensure that no engine oil gets inside the deliver pipe.
2. Without damaging the O-ring, fit the fuel high pressure hose to
the delivery pipe by twisting it from left to right. Ensure that the
hose is twisted smoothly.
3. If the hose cannot be twisted smoothly, there is a possibility that
it may be biting into the O-ring, so remove the fuel high pressure
hose, and check for any damage to the O-ring. If the O-ring is
undamaged, reinsert it into the delivery pipe and check once
more whether the hose can be turned smoothly.
4. Tighten the mounting bolts for the fuel high pressure hose, to
the specified torque.
Tightening torque: 5.0 ± 1.0 N•m.
Page 70 of 364
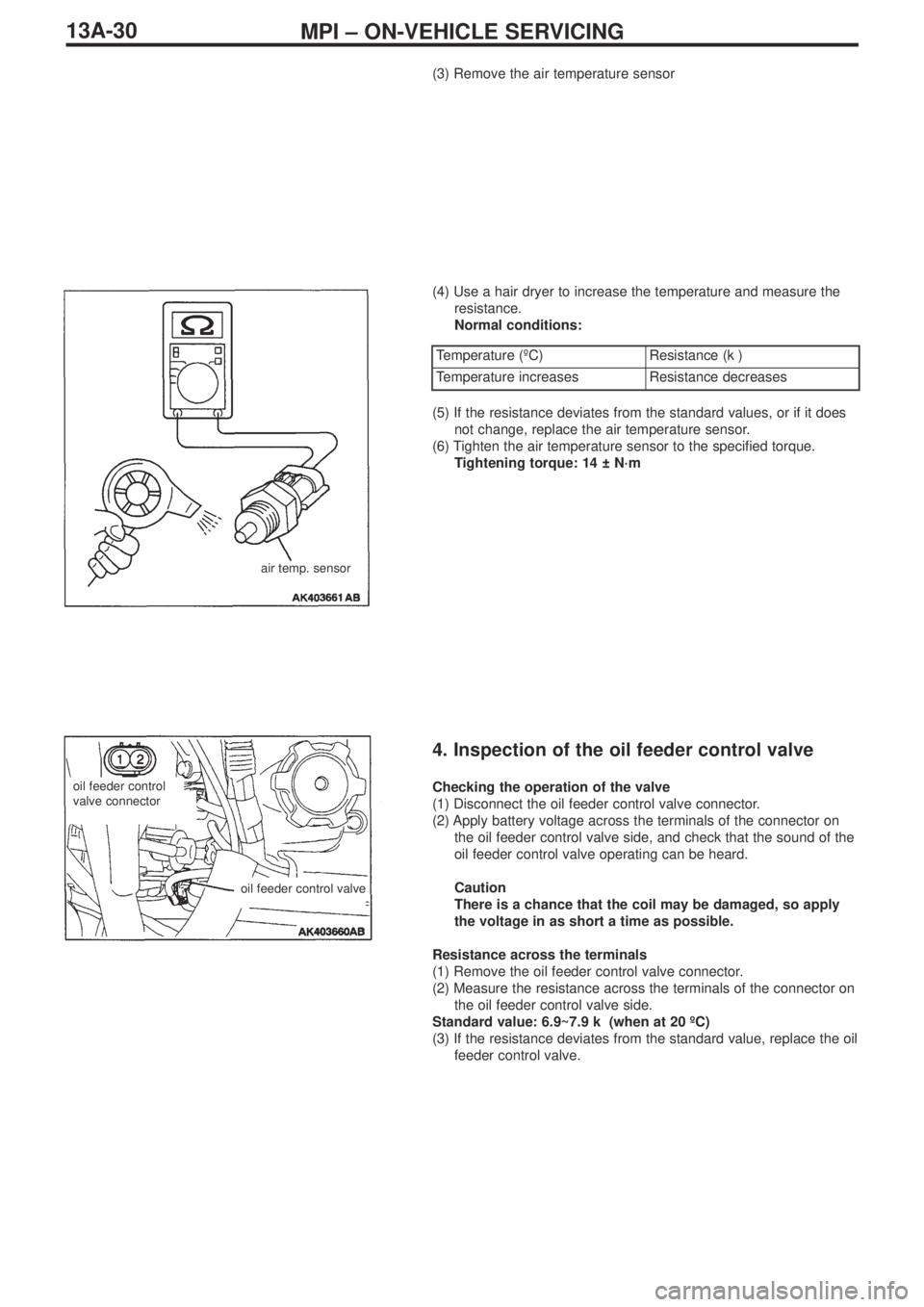
MPI – ON-VEHICLE SERVICING13A-30
(3) Remove the air temperature sensor
(4) Use a hair dryer to increase the temperature and measure the
resistance.
Normal conditions:
air temp. sensor
Temperature (ºC)Resistance (kΩ)
Temperature increasesResistance decreases
(5) If the resistance deviates from the standard values, or if it does
not change, replace the air temperature sensor.
(6) Tighten the air temperature sensor to the specified torque.
Tightening torque: 14 ± N·m
4. Inspection of the oil feeder control valve
Checking the operation of the valve
(1) Disconnect the oil feeder control valve connector.
(2) Apply battery voltage across the terminals of the connector on
the oil feeder control valve side, and check that the sound of the
oil feeder control valve operating can be heard.
Caution
There is a chance that the coil may be damaged, so apply
the voltage in as short a time as possible.
Resistance across the terminals
(1) Remove the oil feeder control valve connector.
(2) Measure the resistance across the terminals of the connector on
the oil feeder control valve side.
Standard value: 6.9~7.9 kΩ (when at 20 ºC)
(3) If the resistance deviates from the standard value, replace the oil
feeder control valve.oil feeder control
valve connector
oil feeder control valve
Page 81 of 364
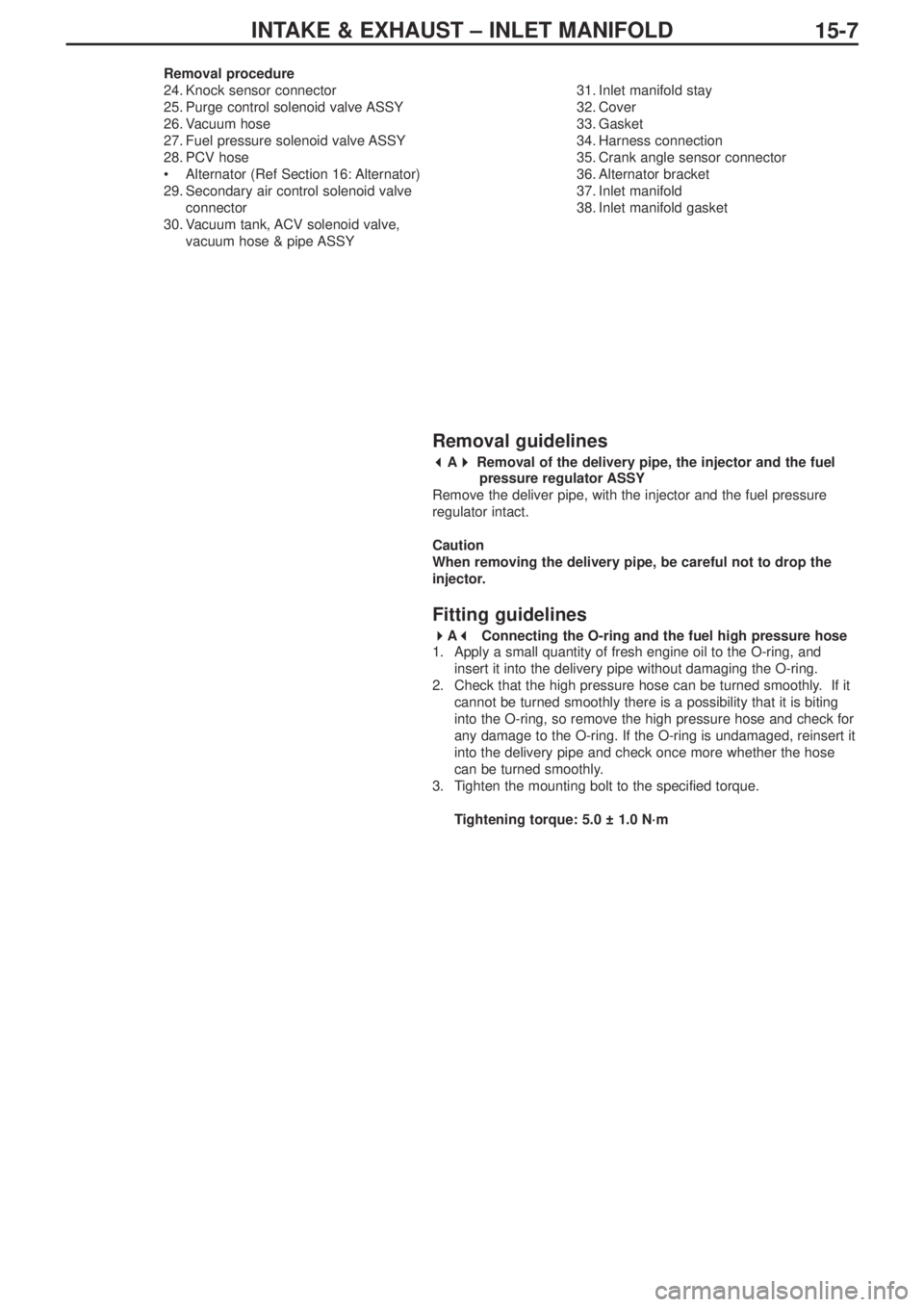
INTAKE & EXHAUST – INLET MANIFOLD
15-7
Removal procedure
24. Knock sensor connector
25. Purge control solenoid valve ASSY
26. Vacuum hose
27. Fuel pressure solenoid valve ASSY
28. PCV hose
•Alternator (Ref Section 16: Alternator)
29. Secondary air control solenoid valve
connector
30. Vacuum tank, ACV solenoid valve,
vacuum hose & pipe ASSY31. Inlet manifold stay
32. Cover
33. Gasket
34. Harness connection
35. Crank angle sensor connector
36. Alternator bracket
37. Inlet manifold
38. Inlet manifold gasket
Removal guidelines
A
Removal of the delivery pipe, the injector and the fuel
pressure regulator ASSY
Remove the deliver pipe, with the injector and the fuel pressure
regulator intact.
Caution
When removing the delivery pipe, be careful not to drop the
injector.
Fitting guidelines
A
Connecting the O-ring and the fuel high pressure hose
1. Apply a small quantity of fresh engine oil to the O-ring, and
insert it into the delivery pipe without damaging the O-ring.
2. Check that the high pressure hose can be turned smoothly. If it
cannot be turned smoothly there is a possibility that it is biting
into the O-ring, so remove the high pressure hose and check for
any damage to the O-ring. If the O-ring is undamaged, reinsert it
into the delivery pipe and check once more whether the hose
can be turned smoothly.
3. Tighten the mounting bolt to the specified torque.
Tightening torque: 5.0 ± 1.0 N·m
Page 89 of 364
REAR AXLE – GENERAL, DIFFERENTIAL CARRIER 27B-1
SECTION 27B
REAR AXLE
CONTENTS
General........................................................1 Differential carrier
AYC system> ..............................................1
General
The tightening torque for the flare nut which joins the fuel pressure unit hose ASSY and the differential carrier ASSY, has been
changed. Other servicing guidelines remain unchanged.
Differential carrier
Removal and fitting
Note
*1: When the screw is dry.
*2: When the screw is lubricated.
NEWOLDfuel pressure unit hose ASSY
differential carrier ASSY
Page 94 of 364
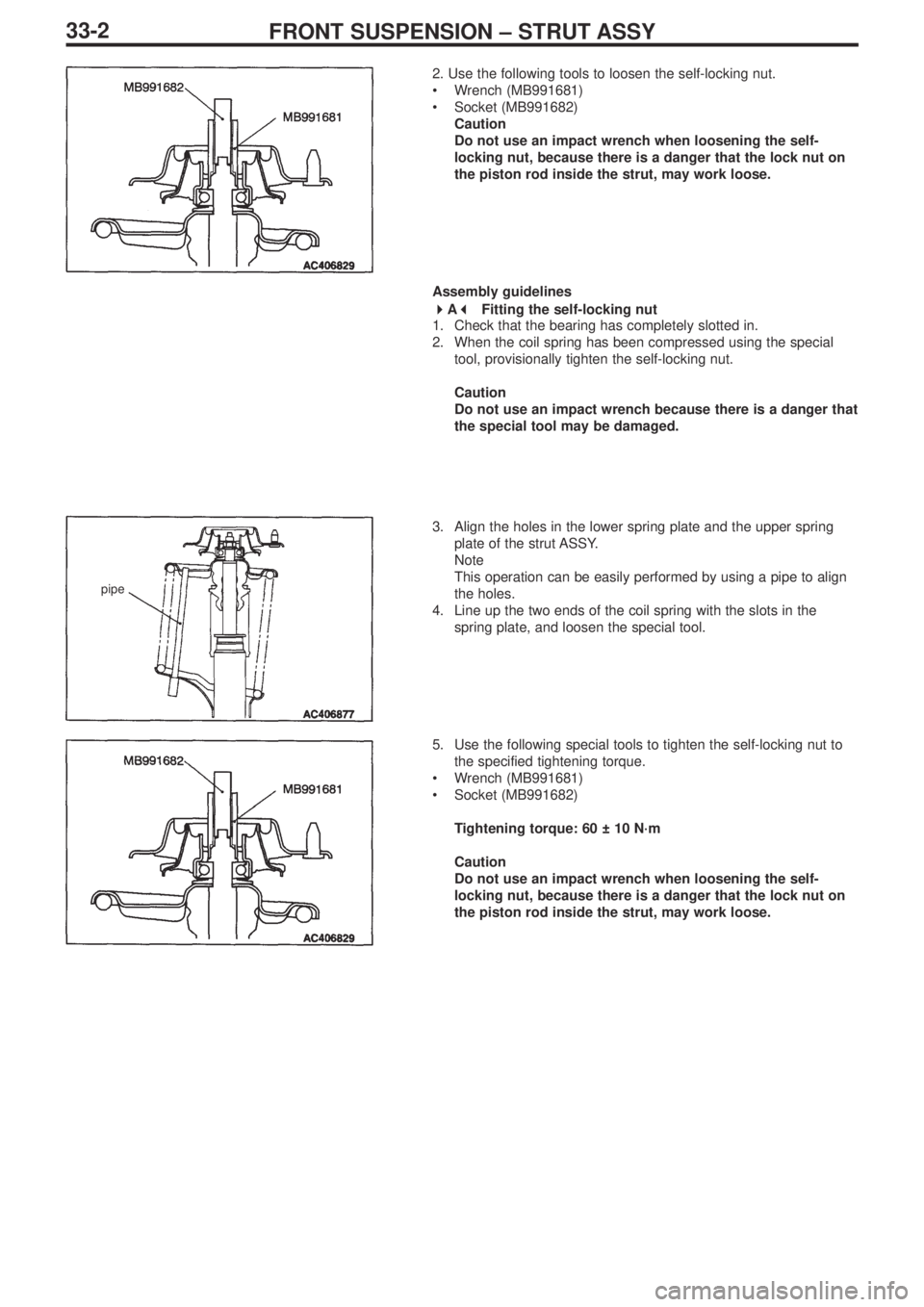
FRONT SUSPENSION – STRUT ASSY33-2
pipe
2. Use the following tools to loosen the self-locking nut.
•Wrench (MB991681)
•Socket (MB991682)
Caution
Do not use an impact wrench when loosening the self-
locking nut, because there is a danger that the lock nut on
the piston rod inside the strut, may work loose.
Assembly guidelines
A
Fitting the self-locking nut
1. Check that the bearing has completely slotted in.
2. When the coil spring has been compressed using the special
tool, provisionally tighten the self-locking nut.
Caution
Do not use an impact wrench because there is a danger that
the special tool may be damaged.
3. Align the holes in the lower spring plate and the upper spring
plate of the strut ASSY.
Note
This operation can be easily performed by using a pipe to align
the holes.
4. Line up the two ends of the coil spring with the slots in the
spring plate, and loosen the special tool.
5. Use the following special tools to tighten the self-locking nut to
the specified tightening torque.
•Wrench (MB991681)
•Socket (MB991682)
Tightening torque: 60 ± 10 N·m
Caution
Do not use an impact wrench when loosening the self-
locking nut, because there is a danger that the lock nut on
the piston rod inside the strut, may work loose.
Page 108 of 364
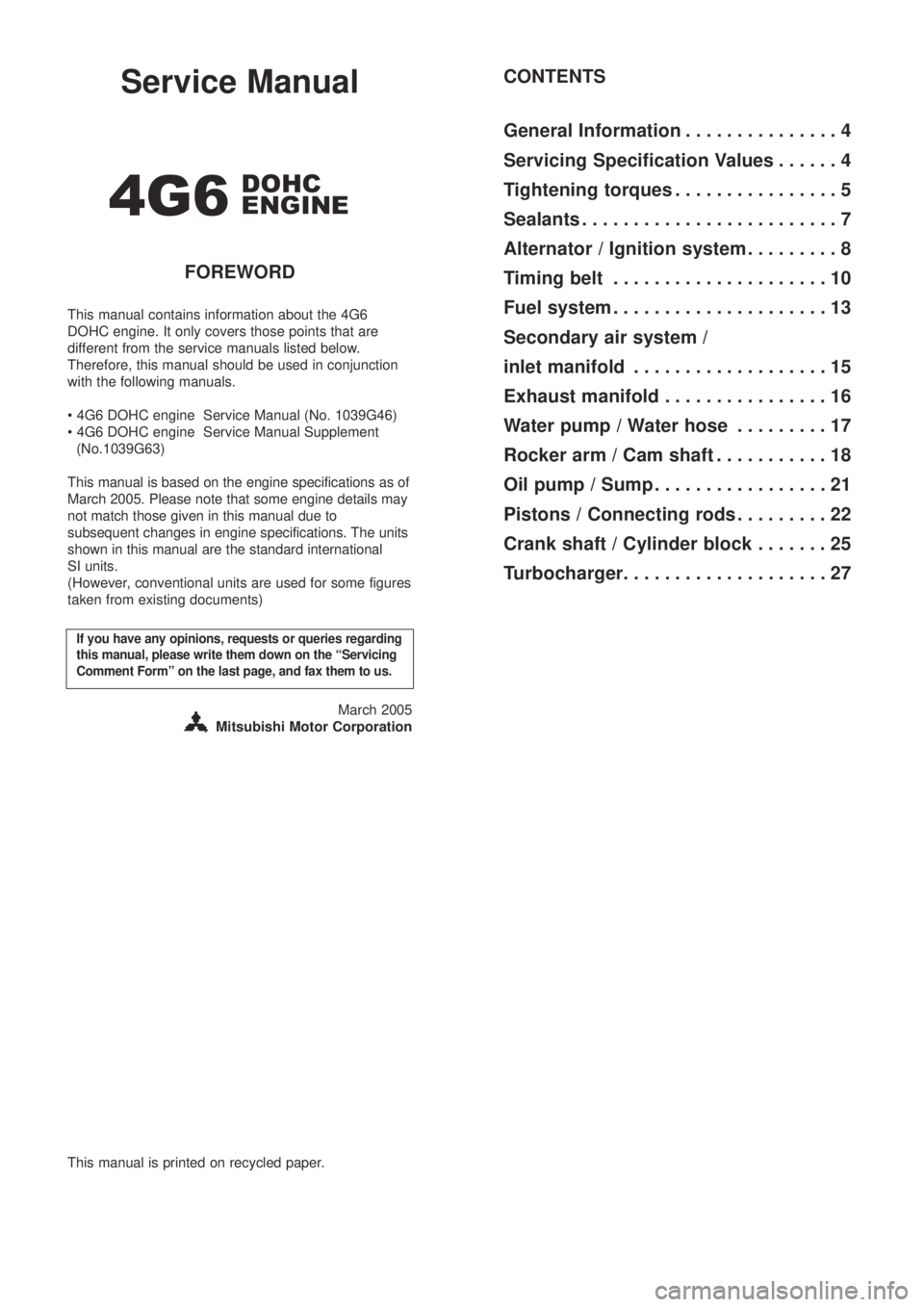
Service Manual
4G6
FOREWORD
This manual contains information about the 4G6
DOHC engine. It only covers those points that are
different from the service manuals listed below.
Therefore, this manual should be used in conjunction
with the following manuals.
• 4G6 DOHC engine Service Manual (No. 1039G46)
• 4G6 DOHC engine Service Manual Supplement
(No.1039G63)
This manual is based on the engine specifications as of
March 2005. Please note that some engine details may
not match those given in this manual due to
subsequent changes in engine specifications. The units
shown in this manual are the standard international
SI units.
(However, conventional units are used for some figures
taken from existing documents)
If you have any opinions, requests or queries regarding
this manual, please write them down on the “Servicing
Comment Form” on the last page, and fax them to us.
March 2005
Mitsubishi Motor Corporation
This manual is printed on recycled paper.
CONTENTS
General Information . . . . . . . . . . . . . . . 4
Servicing Specification Values . . . . . . 4
Tightening torques . . . . . . . . . . . . . . . . 5
Sealants . . . . . . . . . . . . . . . . . . . . . . . . . 7
Alternator / Ignition system . . . . . . . . . 8
Timing belt . . . . . . . . . . . . . . . . . . . . . 10
Fuel system . . . . . . . . . . . . . . . . . . . . . 13
Secondary air system /
inlet manifold . . . . . . . . . . . . . . . . . . . 15
Exhaust manifold . . . . . . . . . . . . . . . . 16
Water pump / Water hose . . . . . . . . . 17
Rocker arm / Cam shaft . . . . . . . . . . . 18
Oil pump / Sump . . . . . . . . . . . . . . . . . 21
Pistons / Connecting rods . . . . . . . . . 22
Crank shaft / Cylinder block . . . . . . . 25
Turbocharger. . . . . . . . . . . . . . . . . . . . 27
DOHC
ENGINE
Page 109 of 364
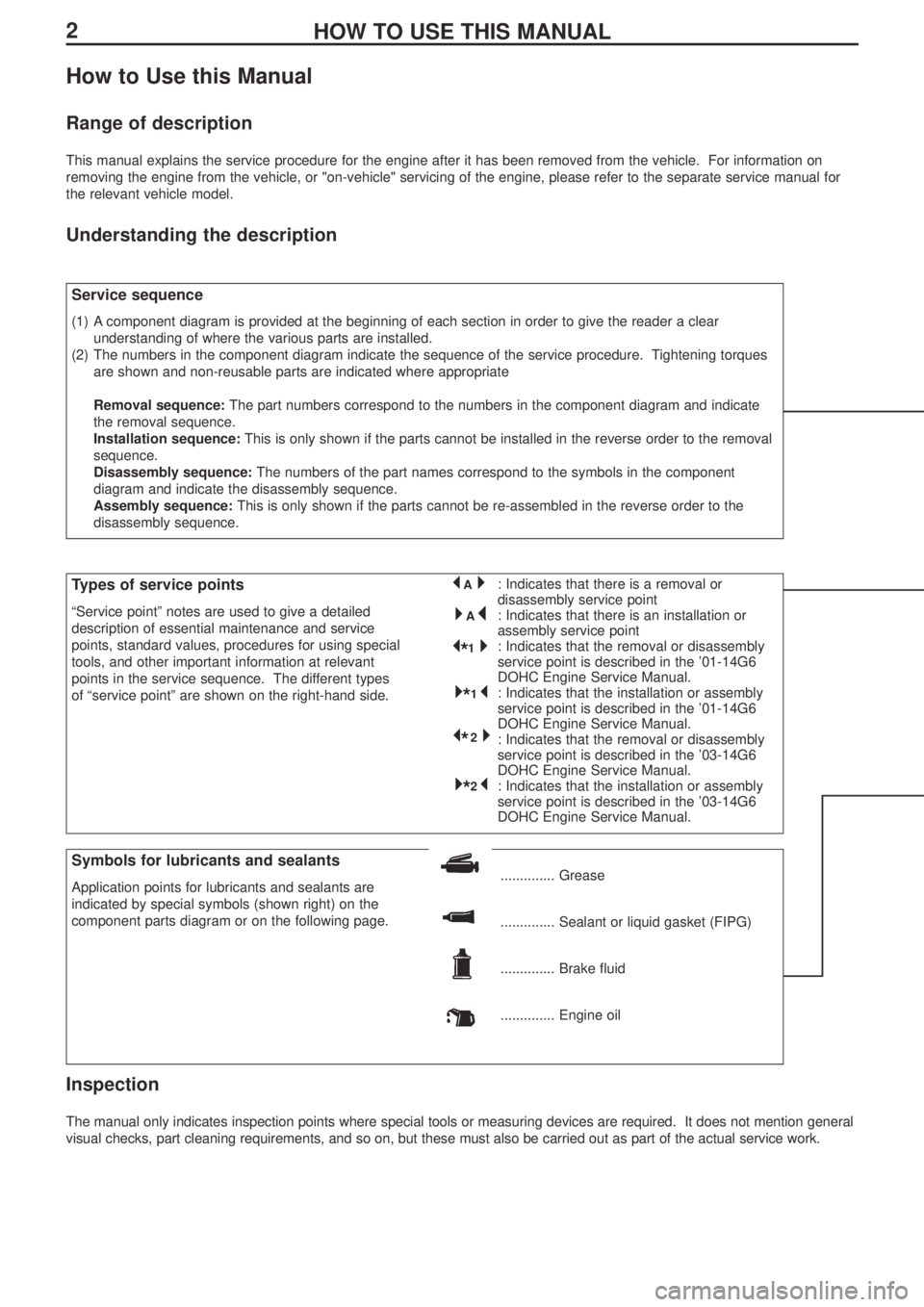
2HOW TO USE THIS MANUAL
How to Use this Manual
Range of description
This manual explains the service procedure for the engine after it has been removed from the vehicle. For information on
removing the engine from the vehicle, or "on-vehicle" servicing of the engine, please refer to the separate service manual for
the relevant vehicle model.
Understanding the description
Inspection
The manual only indicates inspection points where special tools or measuring devices are required. It does not mention general
visual checks, part cleaning requirements, and so on, but these must also be carried out as part of the actual service work.
Service sequence
(1) A component diagram is provided at the beginning of each section in order to give the reader a clear
understanding of where the various parts are installed.
(2) The numbers in the component diagram indicate the sequence of the service procedure. Tightening torques
are shown and non-reusable parts are indicated where appropriate
Removal sequence:The part numbers correspond to the numbers in the component diagram and indicate
the removal sequence.
Installation sequence:This is only shown if the parts cannot be installed in the reverse order to the removal
sequence.
Disassembly sequence: The numbers of the part names correspond to the symbols in the component
diagram and indicate the disassembly sequence.
Assembly sequence:This is only shown if the parts cannot be re-assembled in the reverse order to the
disassembly sequence.
Symbols for lubricants and sealants
Application points for lubricants and sealants are
indicated by special symbols (shown right) on the
component parts diagram or on the following page............... Grease
.............. Sealant or liquid gasket (FIPG)
.............. Brake fluid
.............. Engine oil
Types of service points
“Service point” notes are used to give a detailed
description of essential maintenance and service
points, standard values, procedures for using special
tools, and other important information at relevant
points in the service sequence. The different types
of “service point” are shown on the right-hand side.: Indicates that there is a removal or
disassembly service point
: Indicates that there is an installation or
assembly service point
: Indicates that the removal or disassembly
service point is described in the ’01-14G6
DOHC Engine Service Manual.
: Indicates that the installation or assembly
service point is described in the ’01-14G6
DOHC Engine Service Manual.
: Indicates that the removal or disassembly
service point is described in the ’03-14G6
DOHC Engine Service Manual.
: Indicates that the installation or assembly
service point is described in the ’03-14G6
DOHC Engine Service Manual.
* * 1
* * 2
*
1*
* 2*
A *
* A
Page 112 of 364
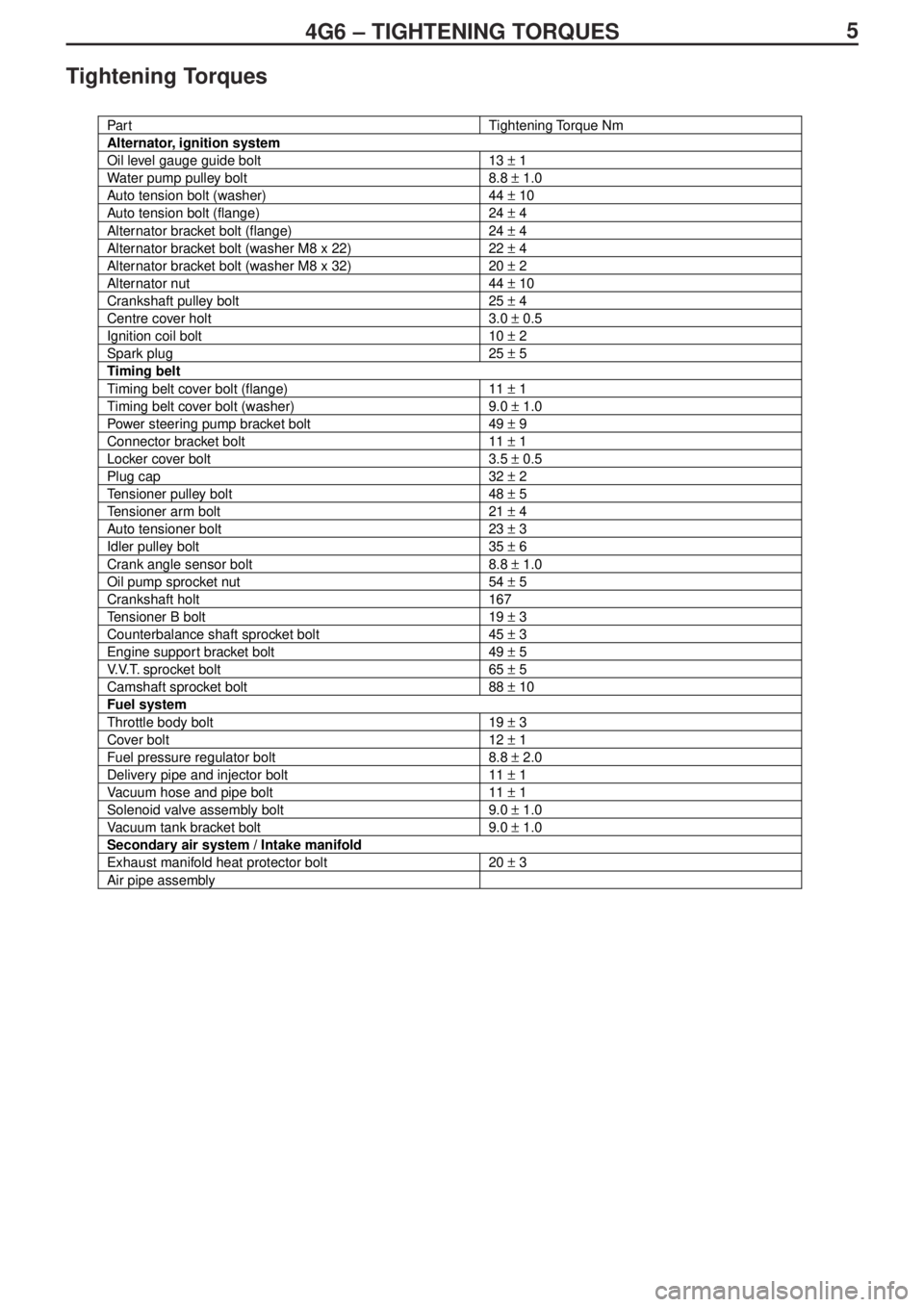
54G6 – TIGHTENING TORQUES
Tightening Torques
Par tTightening Torque Nm
Alternator, ignition system
Oil level gauge guide bolt13 ± 1
Water pump pulley bolt8.8 ± 1.0
Auto tension bolt (washer)44 ± 10
Auto tension bolt (flange)24 ± 4
Alternator bracket bolt (flange)24 ± 4
Alternator bracket bolt (washer M8 x 22)22 ± 4
Alternator bracket bolt (washer M8 x 32)20 ± 2
Alternator nut44 ± 10
Crankshaft pulley bolt25 ± 4
Centre cover holt3.0 ± 0.5
Ignition coil bolt10 ± 2
Spark plug25 ± 5
Timing belt
Timing belt cover bolt (flange)11 ± 1
Timing belt cover bolt (washer)9.0 ± 1.0
Power steering pump bracket bolt49 ± 9
Connector bracket bolt11 ± 1
Locker cover bolt3.5 ± 0.5
Plug cap32 ± 2
Tensioner pulley bolt48 ± 5
Tensioner arm bolt21 ± 4
Auto tensioner bolt23 ± 3
Idler pulley bolt35 ± 6
Crank angle sensor bolt8.8 ± 1.0
Oil pump sprocket nut54 ± 5
Crankshaft holt167
Tensioner B bolt19 ± 3
Counterbalance shaft sprocket bolt45 ± 3
Engine support bracket bolt49 ± 5
V.V.T. sprocket bolt65 ± 5
Camshaft sprocket bolt88 ± 10
Fuel system
Throttle body bolt19 ± 3
Cover bolt12 ± 1
Fuel pressure regulator bolt8.8 ± 2.0
Delivery pipe and injector bolt11 ± 1
Vacuum hose and pipe bolt11 ± 1
Solenoid valve assembly bolt9.0 ± 1.0
Vacuum tank bracket bolt9.0 ± 1.0
Secondary air system / Intake manifold
Exhaust manifold heat protector bolt20 ± 3
Air pipe assembly