Page 1186 of 1500

ON-VEHICLE SERVICE
BASIC BRAKE SYSTEM35A-21
After a new brake disc is installed, always grind the
brake disc with an on-the-car type brake lathe. If this
step is not carried out, the brake disc run-out exceeds
the specified value, resulting in judder.
When the on-the-car type lathe is used, first install a
M12 flat washer on the stud bolt in the brake disc side
according to the figure, and then install the adapter. If
the adapter is installed with M12 flat washer not seated,
the brake disc rotor may be deformed, resulting in inac-
curate grinding.
Grind the brake disc with all wheel nuts diagonally and
equally tightened to the specified torque 100 N
m (74
ft-lb). If all of the wheel nuts are not used, or the tight-
ening torque is excessive or not equal, the brake disc
rotor or drum may be deformed, resulting in judder.
2. If the disc thickness is less than the limit, replace it with a
new one. If thickness variation exceeds the specification,
turn rotor with an on-the-car type brake lathe
("Accuturn-8750" or equivalent). If the calculated final
thickness after turning the rotor is less than the standard
value, replace the disc.
.
Page 1188 of 1500
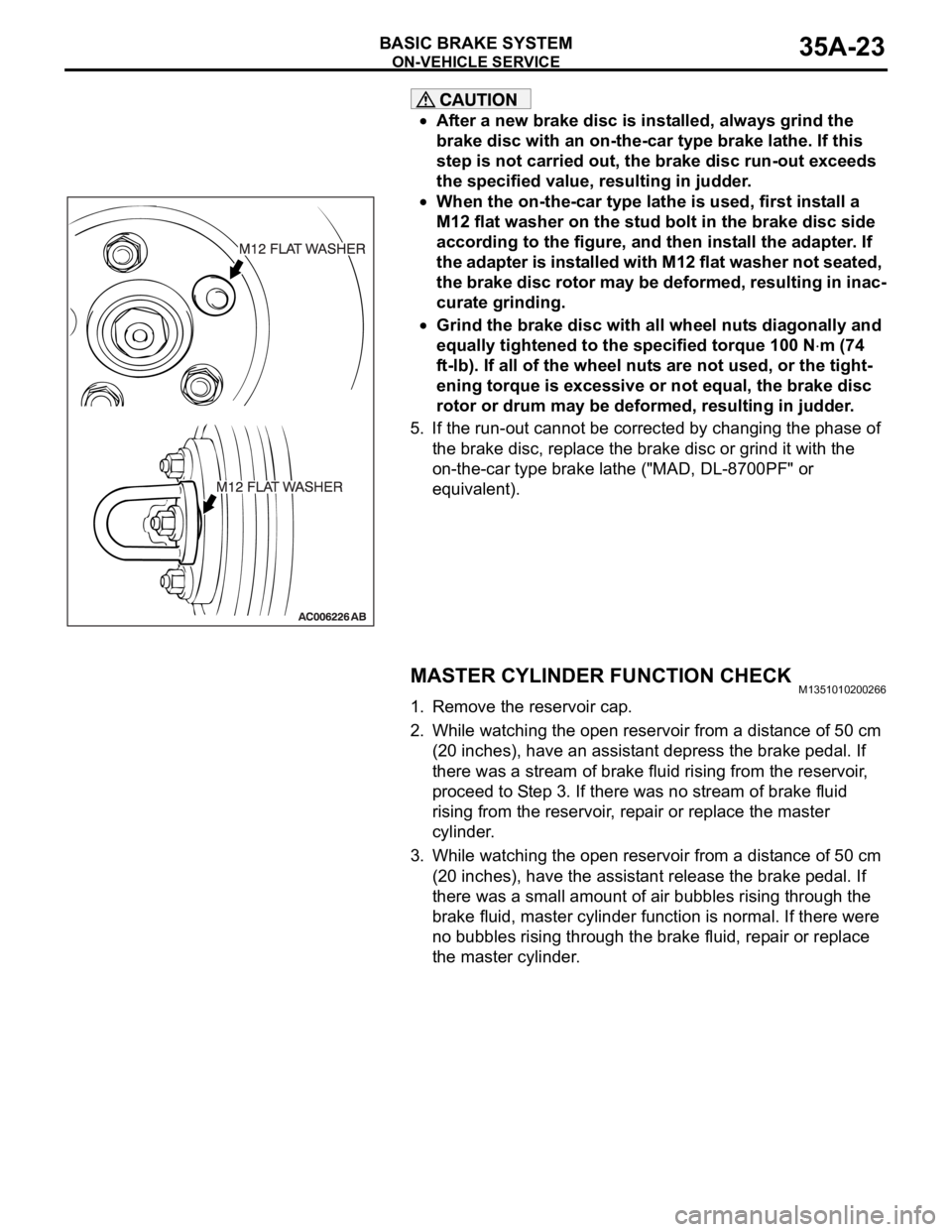
ON-VEHICLE SERVICE
BASIC BRAKE SYSTEM35A-23
After a new brake disc is installed, always grind the
brake disc with an on-the-car type brake lathe. If this
step is not carried out, the brake disc run-out exceeds
the specified value, resulting in judder.
When the on-the-car type lathe is used, first install a
M12 flat washer on the stud bolt in the brake disc side
according to the figure, and then install the adapter. If
the adapter is installed with M12 flat washer not seated,
the brake disc rotor may be deformed, resulting in inac-
curate grinding.
Grind the brake disc with all wheel nuts diagonally and
equally tightened to the specified torque 100 N
m (74
ft-lb). If all of the wheel nuts are not used, or the tight-
ening torque is excessive or not equal, the brake disc
rotor or drum may be deformed, resulting in judder.
5. If the run-out cannot be corrected by changing the phase of
the brake disc, replace the brake disc or grind it with the
on-the-car type brake lathe ("MAD, DL-8700PF" or
equivalent).
MASTER CYLINDER FUNCTION CHECKM1351010200266
1. Remove the reservoir cap.
2. While watching the open reservoir from a distance of 50 cm
(20 inches), have an assistant depress the brake pedal. If
there was a stream of brake fluid rising from the reservoir,
proceed to Step 3. If there was no stream of brake fluid
rising from the reservoir, repair or replace the master
cylinder.
3. While watching the open reservoir from a distance of 50 cm
(20 inches), have the assistant release the brake pedal. If
there was a small amount of air bubbles rising through the
brake fluid, master cylinder function is normal. If there were
no bubbles rising through the brake fluid, repair or replace
the master cylinder.
Page 1281 of 1500
GENERAL DESCRIPTION
TRACTION CONTROL SYSTEM (TCL)13C-2
GENERAL DESCRIPTIONM1136000100029
Traction Control systems are a significant safety fea-
ture designed to prevent wheel spin during accelera-
tion. This results in improved vehicle stability and
steer ability. When excessive wheel spin is detected,
the system will automatically reduce engine torque
via the engine management system. The Engine
ECU can reduce throttle position, cut fuel injection
and retard ignition to one or more cylinders depend-ing on how much torque reduction is required and
will continue to occur until the wheels are no longer
spinning. During traction control operation the TCL
warning lamp will flash to inform the driver that the
vehicle is under traction control. This will continue
until traction control is finished.
CONSTRUCTION DIAGRAM
91011
1213141516 12345
678
Page 1316 of 1500
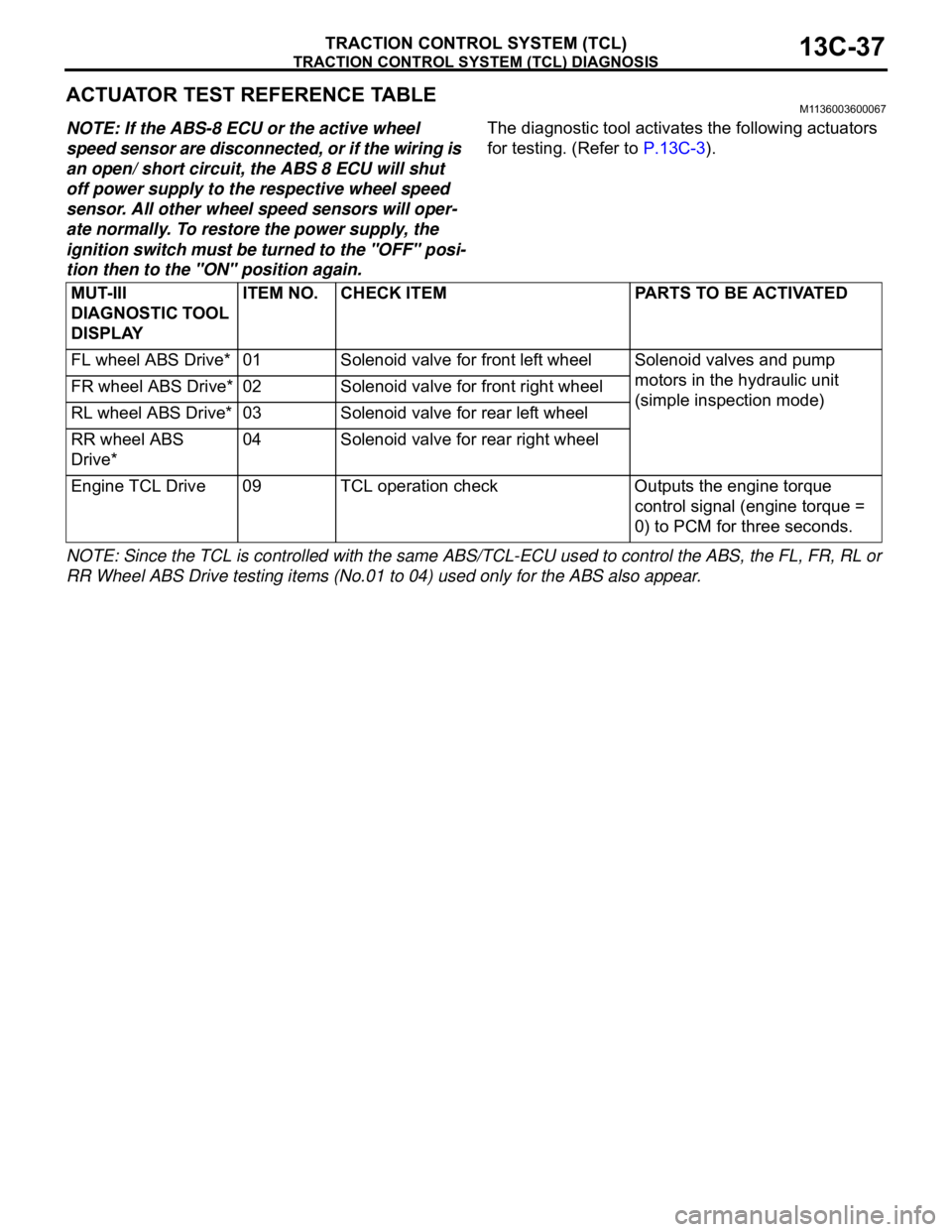
TRACTION CONTROL SYSTEM (TCL) DIAGNOSIS
TRACTION CONTROL SYSTEM (TCL)13C-37
ACTUATOR TEST REFERENCE TABLEM1136003600067
NOTE: If the ABS-8 ECU or the active wheel
speed sensor are disconnected, or if the wiring is
an open/ short circuit, the ABS 8 ECU will shut
off power supply to the respective wheel speed
sensor. All other wheel speed sensors will oper-
ate normally. To restore the power supply, the
ignition switch must be turned to the "OFF" posi-
tion then to the "ON" position again.The diagnostic tool activates the following actuators
for testing. (Refer to P.13C-3).
NOTE: Since the TCL is controlled with the same ABS/TCL-ECU used to control the ABS, the FL, FR, RL or
RR Wheel ABS Drive testing items (No.01 to 04) used only for the ABS also appear. MUT-III
DIAGNOSTIC TOOL
DISPLAYITEM NO. CHECK ITEM PARTS TO BE ACTIVATED
FL wheel ABS Drive* 01 Solenoid valve for front left wheel Solenoid valves and pump
motors in the hydraulic unit
(simple inspection mode) FR wheel ABS Drive* 02 Solenoid valve for front right wheel
RL wheel ABS Drive* 03 Solenoid valve for rear left wheel
RR wheel ABS
Drive*04 Solenoid valve for rear right wheel
Engine TCL Drive 09 TCL operation check Outputs the engine torque
control signal (engine torque =
0) to PCM for three seconds.
Page 1419 of 1500
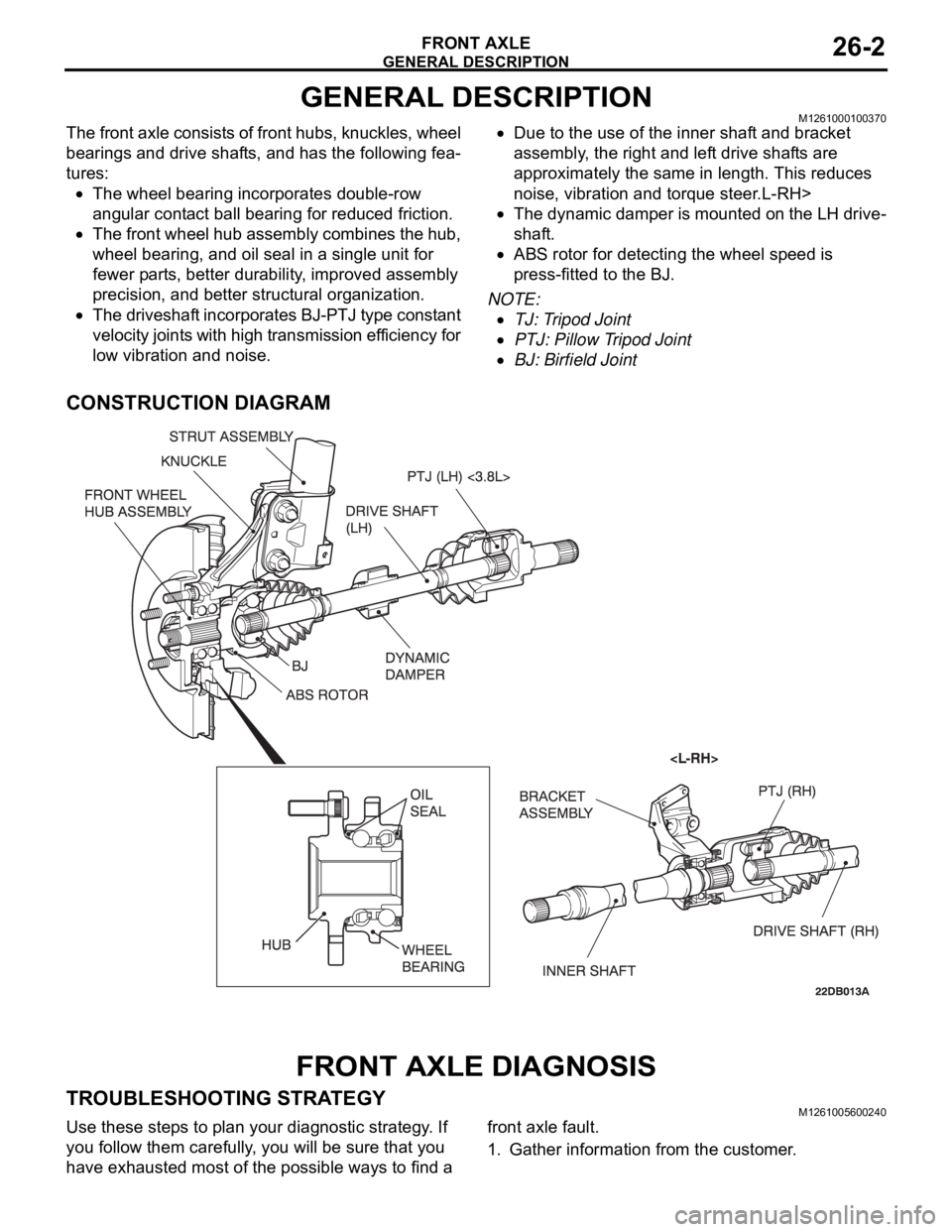
GENERAL DESCRIPTION
FRONT AXLE26-2
GENERAL DESCRIPTIONM1261000100370
The front axle consists of front hubs, knuckles, wheel
bearings and drive shafts, and has the following fea-
tures:
The wheel bearing incorporates double-row
angular contact ball bearing for reduced friction.
The front wheel hub assembly combines the hub,
wheel bearing, and oil seal in a single unit for
fewer parts, better durability, improved assembly
precision, and better structural organization.
The driveshaft incorporates BJ-PTJ type constant
velocity joints with high transmission efficiency for
low vibration and noise.
Due to the use of the inner shaft and bracket
assembly, the right and left drive shafts are
approximately the same in length. This reduces
noise, vibration and torque steer.L-RH>
The dynamic damper is mounted on the LH drive-
shaft.
ABS rotor for detecting the wheel speed is
press-fitted to the BJ.
NOTE: .
TJ: Tripod Joint
PTJ: Pillow Tripod Joint
BJ: Birfield Joint
CONSTRUCTION DIAGRAM
FRONT AXLE DIAGNOSIS
TROUBLESHOOTING STRATEGYM1261005600240
Use these steps to plan your diagnostic strategy. If
you follow them carefully, you will be sure that you
have exhausted most of the possible ways to find a front axle fault.
1. Gather information from the customer.
Page 1422 of 1500
SPECIAL TOOLS
FRONT AXLE26-5
MB990241 Axle
shaft puller
A: MB990242
Puller shaft
B: MB990244
Puller barMB990241-01 or
General service
toolRemoval of the drive shaft
MB991354
Puller bodyGeneral service
tool
MB990590 Rear
axle shaft oil seal
remover
A: MB990212
Adapter
B: MB990211
Slide hammer
Removal of the front wheel hub
A: MB991017
B: MB990998
C: MB991000
A, B: Front hub
remover and
installer
C: SpacerMB990998-01
Removal of the hub
Provisional holding of the wheel
bearing
Measurement of hub starting torque
Measurement of wheel bearing end
play
NOTE: MB991000, which belongs to
MB990998, should be used as a
spacer.
MB990685
Torque wrenchGeneral service
toolMeasurement of hub starting torque
MB990326
Preload socketGeneral service
tool
MB990810
Side bearing
pullerGeneral service
tool
Removal of the center bearing
bracket
Removal of the wheel bearing inner
race (outside) TOOL TOOL NUMBER
AND NAMESUPERSESSION APPLICATION
Page 1425 of 1500
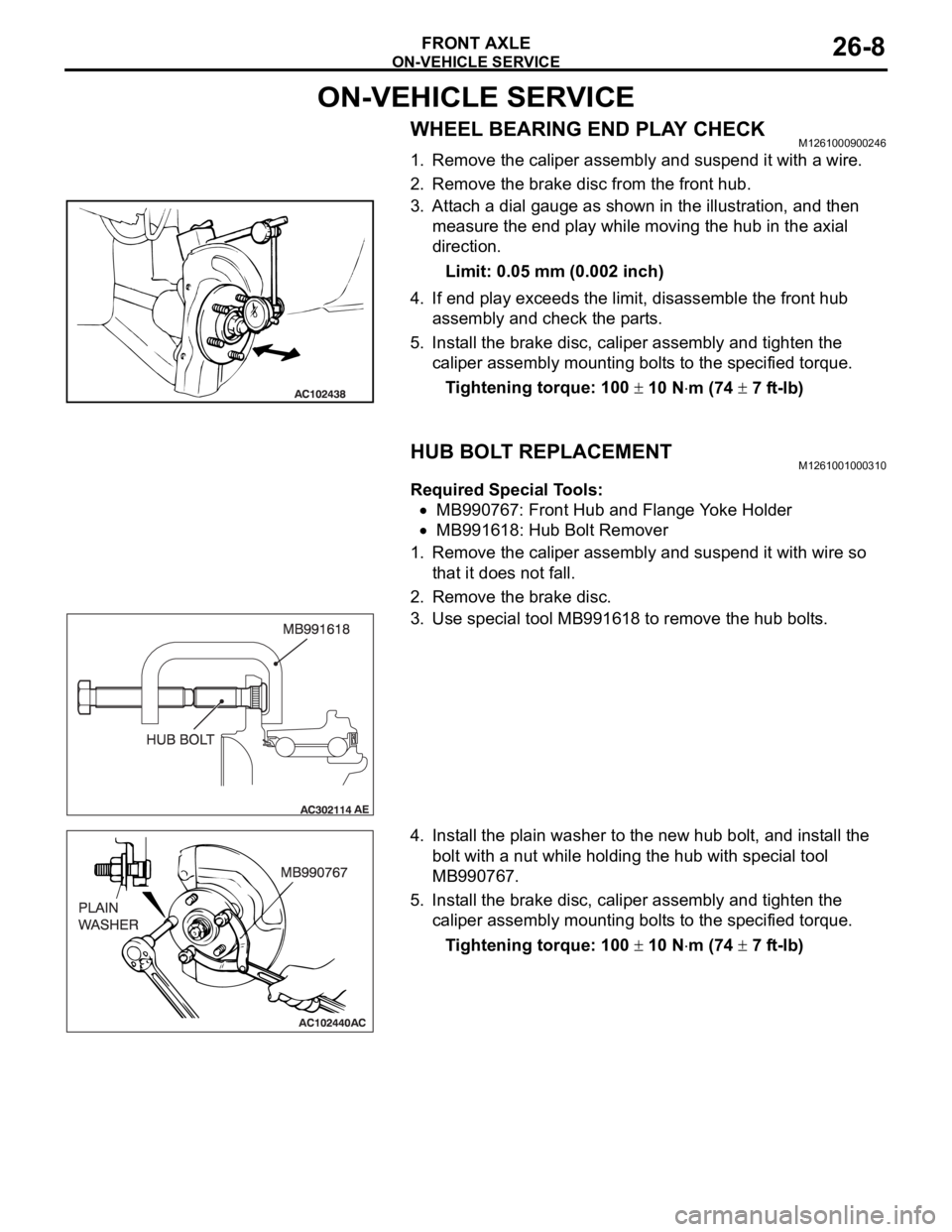
ON-VEHICLE SERVICE
FRONT AXLE26-8
ON-VEHICLE SERVICE
WHEEL BEARING END PLAY CHECKM1261000900246
1. Remove the caliper assembly and suspend it with a wire.
2. Remove the brake disc from the front hub.
3. Attach a dial gauge as shown in the illustration, and then
measure the end play while moving the hub in the axial
direction.
Limit: 0.05 mm (0.002 inch)
4. If end play exceeds the limit, disassemble the front hub
assembly and check the parts.
5. Install the brake disc, caliper assembly and tighten the
caliper assembly mounting bolts to the specified torque.
Tightening torque: 100
10 Nm (74 7 ft-lb)
HUB BOLT REPLACEMENTM1261001000310
Required Special Tools:
MB990767: Front Hub and Flange Yoke Holder
MB991618: Hub Bolt Remover
1. Remove the caliper assembly and suspend it with wire so
that it does not fall.
2. Remove the brake disc.
3. Use special tool MB991618 to remove the hub bolts.
4. Install the plain washer to the new hub bolt, and install the
bolt with a nut while holding the hub with special tool
MB990767.
5. Install the brake disc, caliper assembly and tighten the
caliper assembly mounting bolts to the specified torque.
Tightening torque: 100
10 Nm (74 7 ft-lb)
Page 1429 of 1500
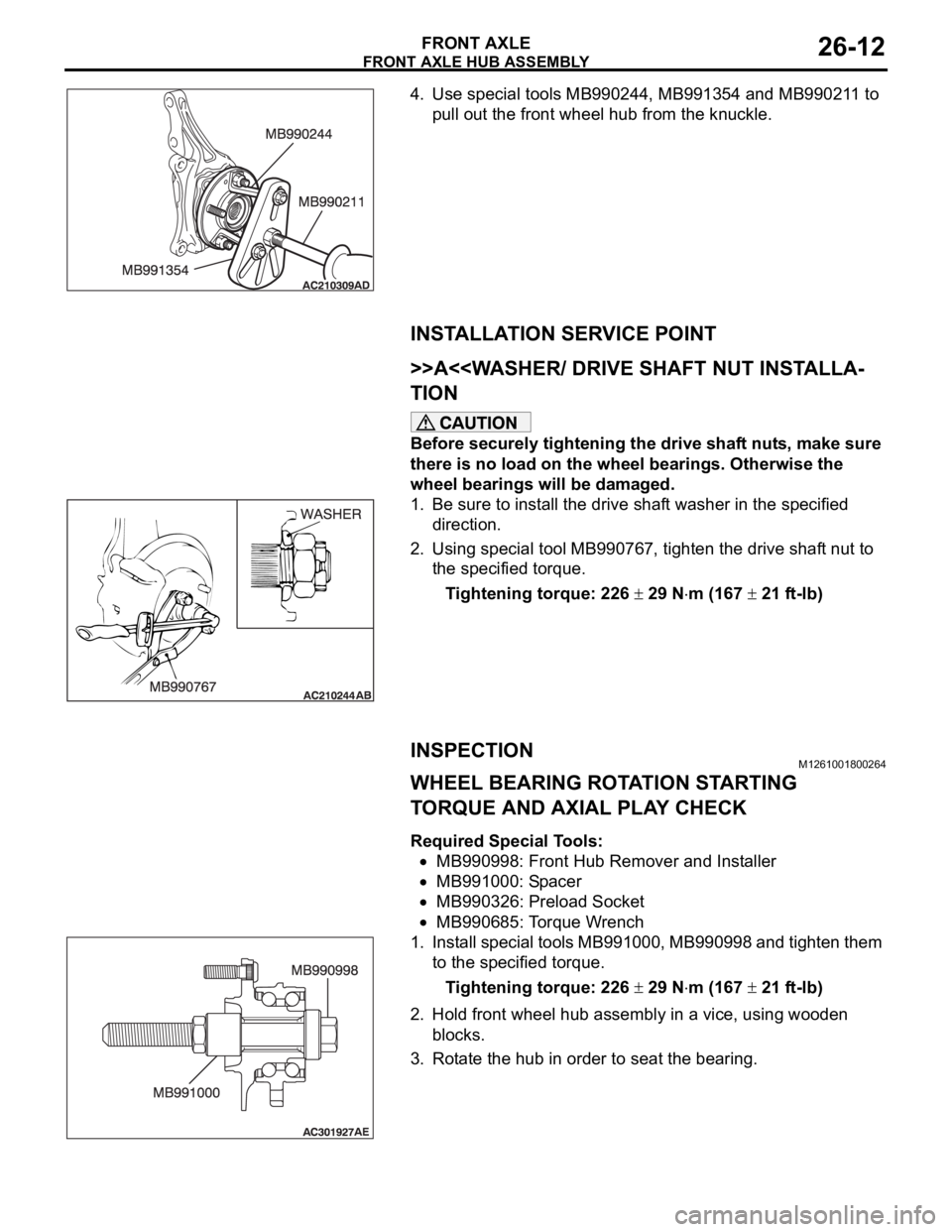
FRONT AXLE HUB ASSEMBLY
FRONT AXLE26-12
4. Use special tools MB990244, MB991354 and MB990211 to
pull out the front wheel hub from the knuckle.
INSTALLATION SERVICE POINT
.
>>A<
TION
Before securely tightening the drive shaft nuts, make sure
there is no load on the wheel bearings. Otherwise the
wheel bearings will be damaged.
1. Be sure to install the drive shaft washer in the specified
direction.
2. Using special tool MB990767, tighten the drive shaft nut to
the specified torque.
Tightening torque: 226
29 Nm (167 21 ft-lb)
INSPECTIONM1261001800264
WHEEL BEARING ROTATION STARTING
TORQUE AND AXIAL PLAY CHECK
Required Special Tools:
MB990998: Front Hub Remover and Installer
MB991000: Spacer
MB990326: Preload Socket
MB990685: Torque Wrench
1. Install special tools MB991000, MB990998 and tighten them
to the specified torque.
Tightening torque: 226
29 Nm (167 21 ft-lb)
2. Hold front wheel hub assembly in a vice, using wooden
blocks.
3. Rotate the hub in order to seat the bearing.