Page 6 of 136
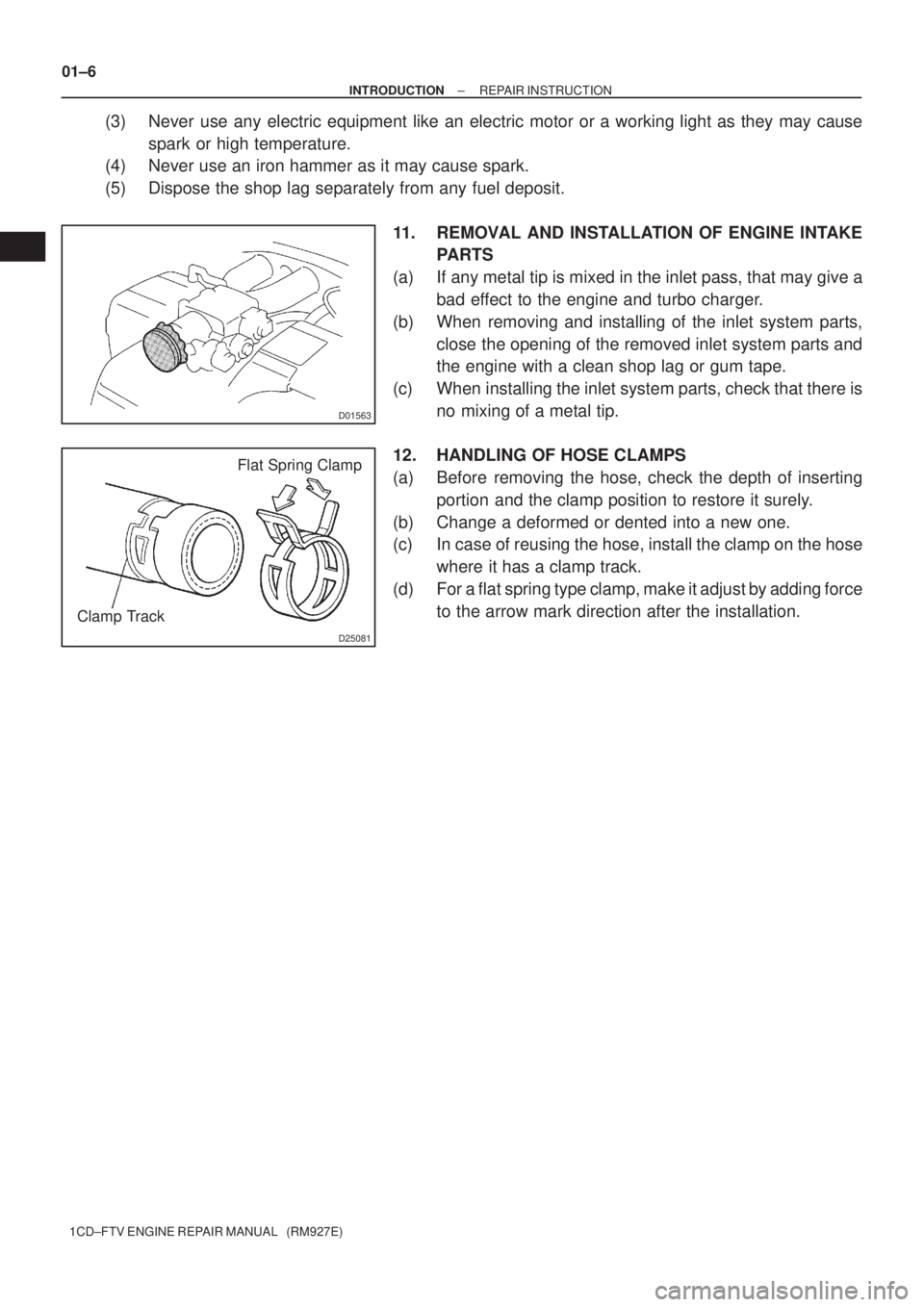
D01563
D25081
Flat Spring Clamp
Clamp Track 01±6
± INTRODUCTIONREPAIR INSTRUCTION
1CD±FTV ENGINE REPAIR MANUAL (RM927E)
(3) Never use any electric equipment like an electric motor or a working light as they may cause
spark or high temperature.
(4) Never use an iron hammer as it may cause spark.
(5) Dispose the shop lag separately from any fuel deposit.
11. REMOVAL AND INSTALLATION OF ENGINE INTAKE
PARTS
(a) If any metal tip is mixed in the inlet pass, that may give a
bad effect to the engine and turbo charger.
(b) When removing and installing of the inlet system parts,
close the opening of the removed inlet system parts and
the engine with a clean shop lag or gum tape.
(c) When installing the inlet system parts, check that there is
no mixing of a metal tip.
12. HANDLING OF HOSE CLAMPS
(a) Before removing the hose, check the depth of inserting
portion and the clamp position to restore it surely.
(b) Change a deformed or dented into a new one.
(c) In case of reusing the hose, install the clamp on the hose
where it has a clamp track.
(d) For a flat spring type clamp, make it adjust by adding force
to the arrow mark direction after the installation.
Page 37 of 136
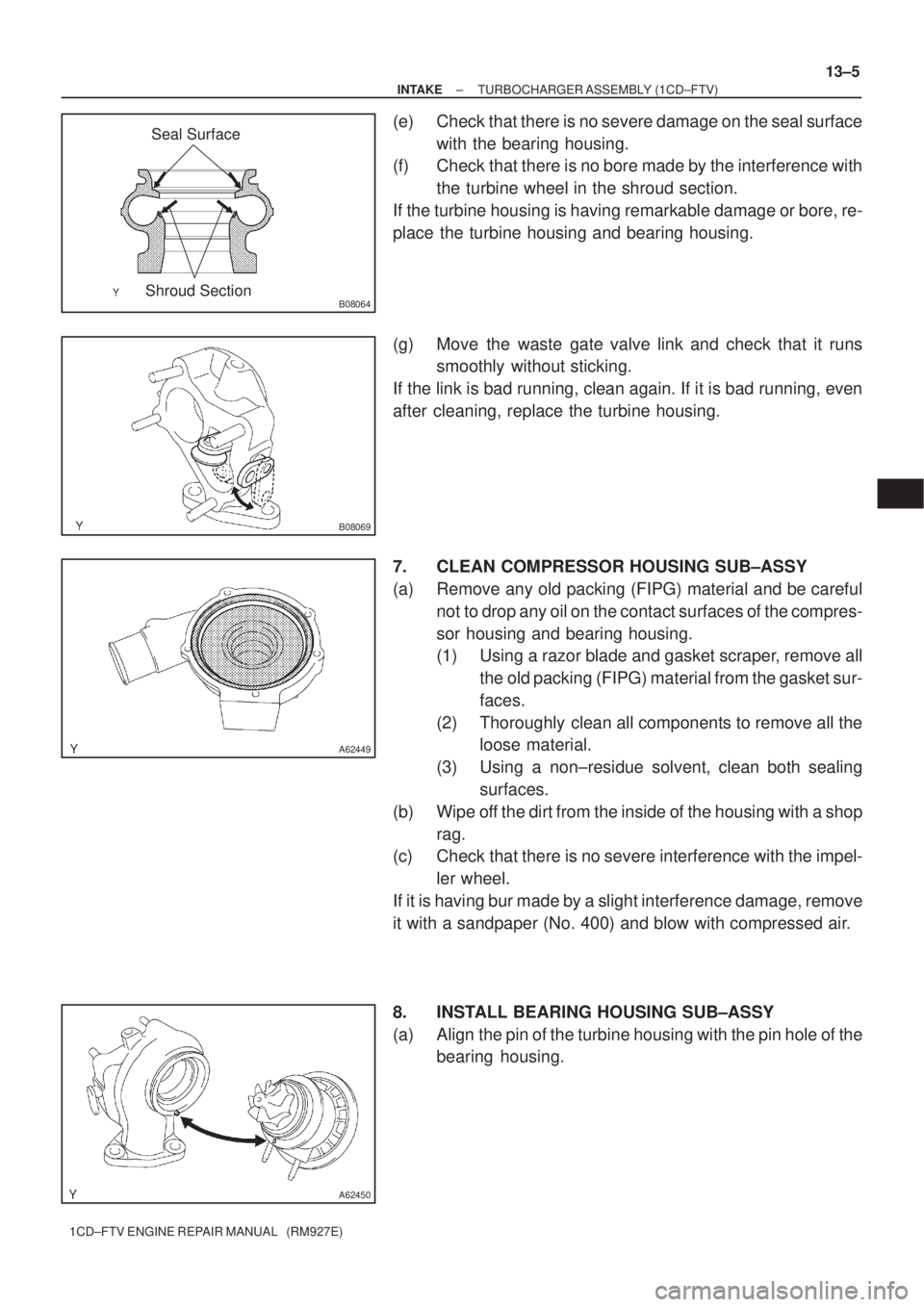
B08064
Seal Surface
Shroud Section
B08069
A62449
A62450
± INTAKETURBOCHARGER ASSEMBLY (1CD±FTV)
13±5
1CD±FTV ENGINE REPAIR MANUAL (RM927E)
(e) Check that there is no severe damage on the seal surface
with the bearing housing.
(f) Check that there is no bore made by the interference with
the turbine wheel in the shroud section.
If the turbine housing is having remarkable damage or bore, re-
place the turbine housing and bearing housing.
(g) Move the waste gate valve link and check that it runs
smoothly without sticking.
If the link is bad running, clean again. If it is bad running, even
after cleaning, replace the turbine housing.
7. CLEAN COMPRESSOR HOUSING SUB±ASSY
(a) Remove any old packing (FIPG) material and be careful
not to drop any oil on the contact surfaces of the compres-
sor housing and bearing housing.
(1) Using a razor blade and gasket scraper, remove all
the old packing (FIPG) material from the gasket sur-
faces.
(2) Thoroughly clean all components to remove all the
loose material.
(3) Using a non±residue solvent, clean both sealing
surfaces.
(b) Wipe off the dirt from the inside of the housing with a shop
rag.
(c) Check that there is no severe interference with the impel-
ler wheel.
If it is having bur made by a slight interference damage, remove
it with a sandpaper (No. 400) and blow with compressed air.
8. INSTALL BEARING HOUSING SUB±ASSY
(a) Align the pin of the turbine housing with the pin hole of the
bearing housing.
Page 58 of 136
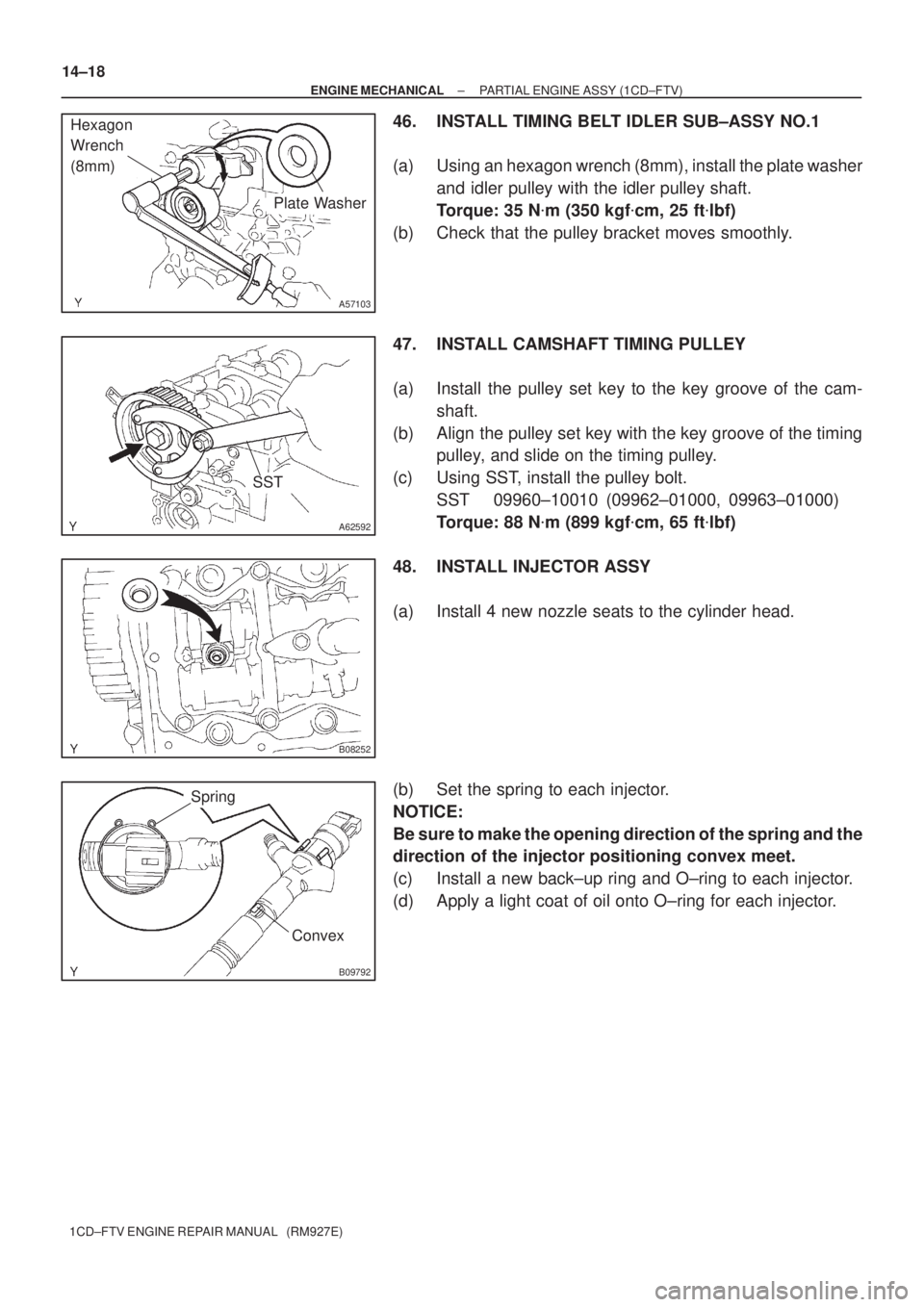
A57103
Plate Washer
Hexagon
Wrench
(8mm)
A62592
SST
B08252
B09792
Spring
Convex
14±18
± ENGINE MECHANICALPARTIAL ENGINE ASSY (1CD±FTV)
1CD±FTV ENGINE REPAIR MANUAL (RM927E)
46. INSTALL TIMING BELT IDLER SUB±ASSY NO.1
(a) Using an hexagon wrench (8mm), install the plate washer
and idler pulley with the idler pulley shaft.
Torque: 35 Nm (350 kgfcm, 25 ftlbf)
(b) Check that the pulley bracket moves smoothly.
47. INSTALL CAMSHAFT TIMING PULLEY
(a) Install the pulley set key to the key groove of the cam-
shaft.
(b) Align the pulley set key with the key groove of the timing
pulley, and slide on the timing pulley.
(c) Using SST, install the pulley bolt.
SST 09960±10010 (09962±01000, 09963±01000)
Torque: 88 Nm (899 kgfcm, 65 ftlbf)
48. INSTALL INJECTOR ASSY
(a) Install 4 new nozzle seats to the cylinder head.
(b) Set the spring to each injector.
NOTICE:
Be sure to make the opening direction of the spring and the
direction of the injector positioning convex meet.
(c) Install a new back±up ring and O±ring to each injector.
(d) Apply a light coat of oil onto O±ring for each injector.
Page 60 of 136
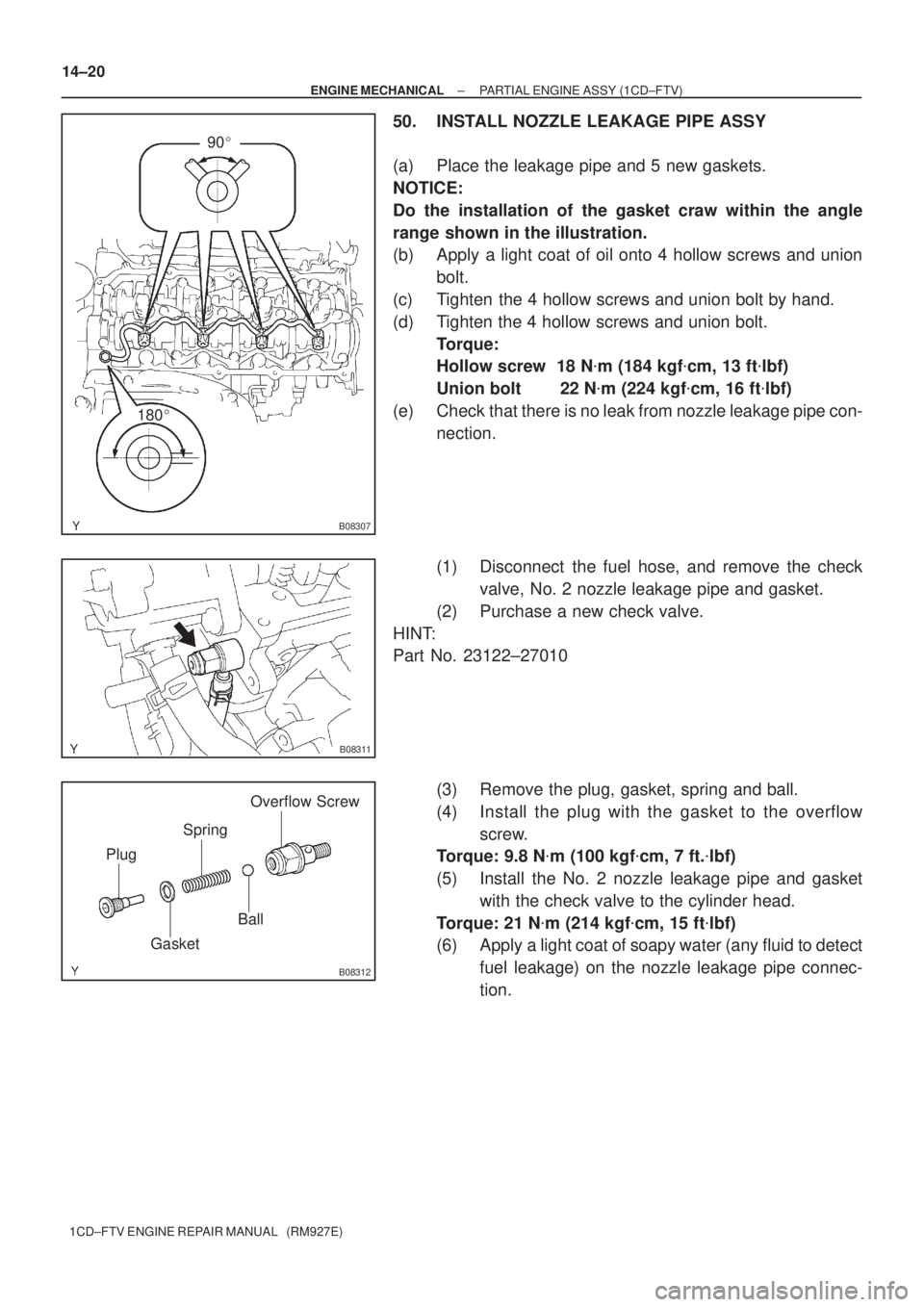
90
180
B08307
B08311
B08312
Plug
GasketOverflow Screw
Ball Spring 14±20
± ENGINE MECHANICALPARTIAL ENGINE ASSY (1CD±FTV)
1CD±FTV ENGINE REPAIR MANUAL (RM927E)
50. INSTALL NOZZLE LEAKAGE PIPE ASSY
(a) Place the leakage pipe and 5 new gaskets.
NOTICE:
Do the installation of the gasket craw within the angle
range shown in the illustration.
(b) Apply a light coat of oil onto 4 hollow screws and union
bolt.
(c) Tighten the 4 hollow screws and union bolt by hand.
(d) Tighten the 4 hollow screws and union bolt.
Torque:
Hollow screw 18 Nm (184 kgfcm, 13 ftlbf)
Union bolt 22 Nm (224 kgfcm, 16 ftlbf)
(e) Check that there is no leak from nozzle leakage pipe con-
nection.
(1) Disconnect the fuel hose, and remove the check
valve, No. 2 nozzle leakage pipe and gasket.
(2) Purchase a new check valve.
HINT:
Part No. 23122±27010
(3) Remove the plug, gasket, spring and ball.
(4) Install the plug with the gasket to the overflow
screw.
Torque: 9.8 Nm (100 kgfcm, 7 ft.lbf)
(5) Install the No. 2 nozzle leakage pipe and gasket
with the check valve to the cylinder head.
Torque: 21 Nm (214 kgfcm, 15 ftlbf)
(6) Apply a light coat of soapy water (any fluid to detect
fuel leakage) on the nozzle leakage pipe connec-
tion.
Page 81 of 136
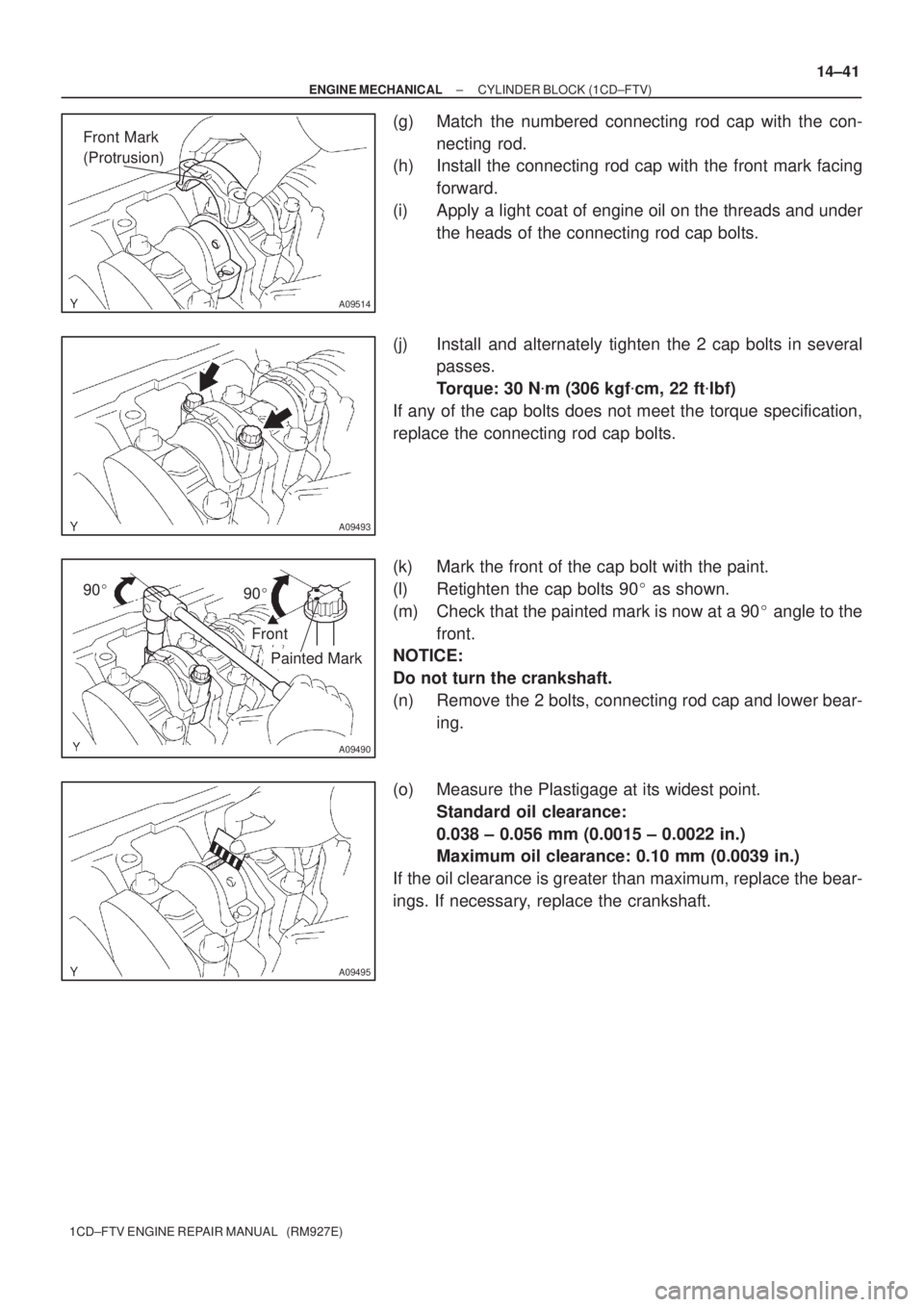
A09514
Front Mark
(Protrusion)
A09493
90
90
A09490
Front
Painted Mark
A09495
± ENGINE MECHANICALCYLINDER BLOCK (1CD±FTV)
14±41
1CD±FTV ENGINE REPAIR MANUAL (RM927E)
(g) Match the numbered connecting rod cap with the con-
necting rod.
(h) Install the connecting rod cap with the front mark facing
forward.
(i) Apply a light coat of engine oil on the threads and under
the heads of the connecting rod cap bolts.
(j) Install and alternately tighten the 2 cap bolts in several
passes.
Torque: 30 Nm (306 kgfcm, 22 ftlbf)
If any of the cap bolts does not meet the torque specification,
replace the connecting rod cap bolts.
(k) Mark the front of the cap bolt with the paint.
(l) Retighten the cap bolts 90 as shown.
(m) Check that the painted mark is now at a 90 angle to the
front.
NOTICE:
Do not turn the crankshaft.
(n) Remove the 2 bolts, connecting rod cap and lower bear-
ing.
(o) Measure the Plastigage at its widest point.
Standard oil clearance:
0.038 ± 0.056 mm (0.0015 ± 0.0022 in.)
Maximum oil clearance: 0.10 mm (0.0039 in.)
If the oil clearance is greater than maximum, replace the bear-
ings. If necessary, replace the crankshaft.
Page 97 of 136
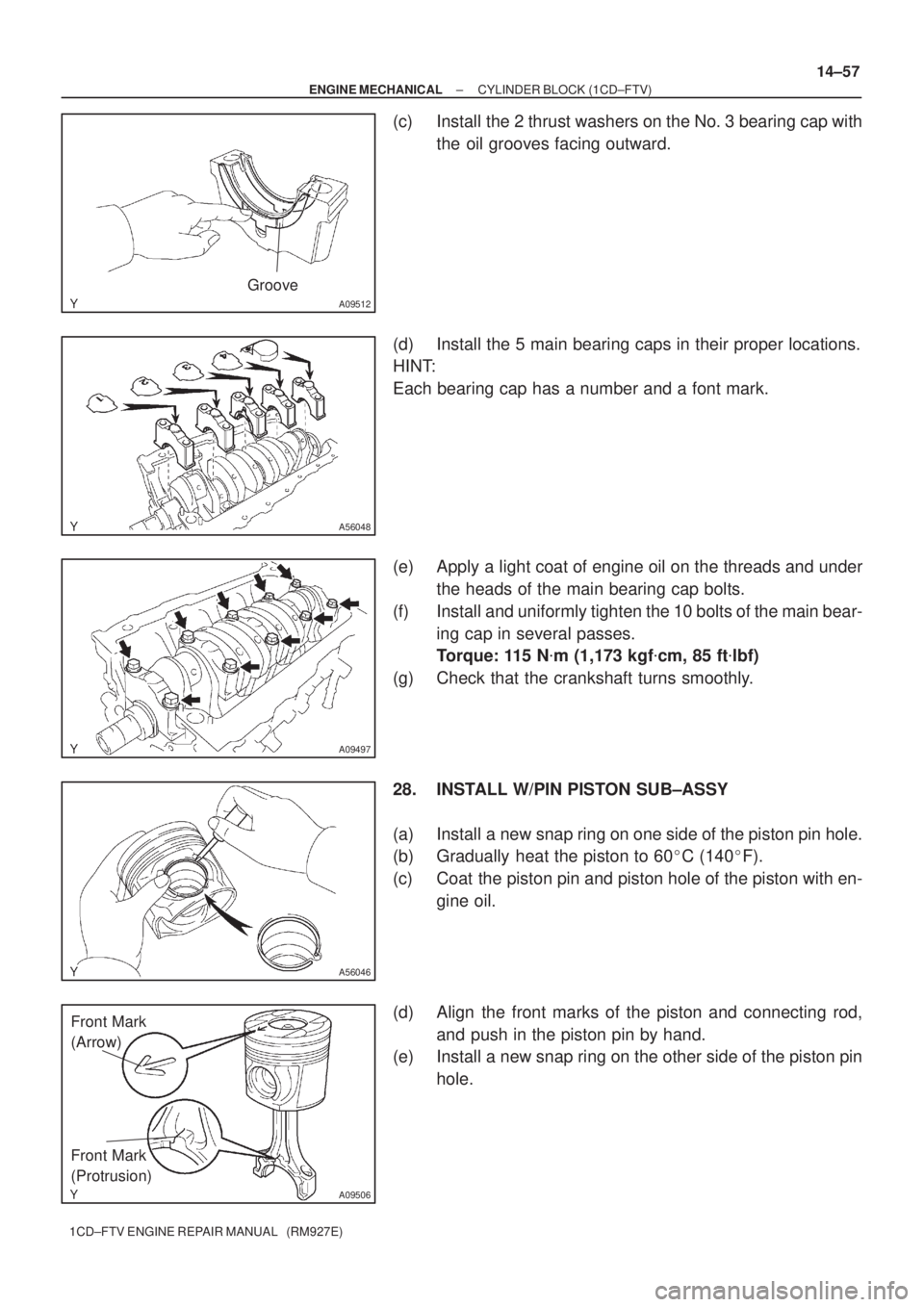
A09512
Groove
A56048
A09497
A56046
A09506
Front Mark
(Arrow)
Front Mark
(Protrusion)
± ENGINE MECHANICALCYLINDER BLOCK (1CD±FTV)
14±57
1CD±FTV ENGINE REPAIR MANUAL (RM927E)
(c) Install the 2 thrust washers on the No. 3 bearing cap with
the oil grooves facing outward.
(d) Install the 5 main bearing caps in their proper locations.
HINT:
Each bearing cap has a number and a font mark.
(e) Apply a light coat of engine oil on the threads and under
the heads of the main bearing cap bolts.
(f) Install and uniformly tighten the 10 bolts of the main bear-
ing cap in several passes.
Torque: 115 Nm (1,173 kgfcm, 85 ftlbf)
(g) Check that the crankshaft turns smoothly.
28. INSTALL W/PIN PISTON SUB±ASSY
(a) Install a new snap ring on one side of the piston pin hole.
(b) Gradually heat the piston to 60C (140F).
(c) Coat the piston pin and piston hole of the piston with en-
gine oil.
(d) Align the front marks of the piston and connecting rod,
and push in the piston pin by hand.
(e) Install a new snap ring on the other side of the piston pin
hole.
Page 99 of 136

A09511
Front Mark
(Arrow)
Front
Push
A09514
Front Mark
(Protrusion)
A09493
90
90
A09490
Painted Mark
Front
± ENGINE MECHANICALCYLINDER BLOCK (1CD±FTV)
14±59
1CD±FTV ENGINE REPAIR MANUAL (RM927E)
(c) Using a piston ring compressor, push the correctly num-
bered piston and connecting rod assemblies into each
cylinder with the front mark of the piston facing forward.
(d) Match the numbered connecting rod cap with the con-
necting rod.
(e) Install the connecting rod cap with the front mark facing
forward.
(f) Apply a light coat of engine oil on the threads and under
the heads of the connecting rod cap bolts.
(g) Install and alternately tighten the 2 cap bolts in several
passes.
Torque: 30 Nm (306 kgfcm, 22 ftlbf)
If any of the cap bolts does not meet the torque specification,
replace the connecting rod cap bolts.
(h) Mark the front of the cap bolt with the paint.
(i) Retighten the cap bolts 90 as shown.
(j) Check that the painted mark is now at a 90 angle to the
front.
(k) Check that the crankshaft turns smoothly.