Page 2780 of 4449
![INFINITI FX35 2004 Service Manual FRONT TIMING CHAIN CASE
EM-55
[VQ35DE]
C
D
E
F
G
H
I
J
K
L
MA
EM
Revision: 2004 November 2004 FX35/FX45
17. Obtain compression TDC of No. 1 cylinder as follows:
NOTE:
When timing chain is not removed/ INFINITI FX35 2004 Service Manual FRONT TIMING CHAIN CASE
EM-55
[VQ35DE]
C
D
E
F
G
H
I
J
K
L
MA
EM
Revision: 2004 November 2004 FX35/FX45
17. Obtain compression TDC of No. 1 cylinder as follows:
NOTE:
When timing chain is not removed/](/manual-img/42/57021/w960_57021-2779.png)
FRONT TIMING CHAIN CASE
EM-55
[VQ35DE]
C
D
E
F
G
H
I
J
K
L
MA
EM
Revision: 2004 November 2004 FX35/FX45
17. Obtain compression TDC of No. 1 cylinder as follows:
NOTE:
When timing chain is not removed/installed, this step is not required.
a. Rotate crankshaft pulley clockwise to align timing mark (grooved
line without color) with timing indicator.
b. Make sure intake and exhaust cam noses on No. 1 cylinder
(engine front side of right bank) are located as shown in the fig-
ure.
If not, turn crankshaft one revolution (360°) and align as
shown.
NOTE:
When only primary timing chain is removed, rocker cover
does not need to be removed. To confirm that No. 1 cylinder is
at its compression TDC, remove front timing chain case first.
Then check mating marks on camshaft sprockets. Refer to
EM-63, "
TIMING CHAIN" .
18. Remove crankshaft pulley with the following procedure:
a. Remove rear cover plate (2WD) or starter motor (AWD) and set
ring gear stopper (SST) as shown in the figure. Refer to SC-10,
"STARTING SYSTEM" .
b. Loosen crankshaft pulley bolt and locate bolt seating surface as
10 mm (0.39 in) from its original position.
CAUTION:
Do not remove crankshaft pulley bolt as it will be used as a
supporting point for suitable puller.
KBIA1717J
SEM418G
PBIC1098E
PBIC1103E
Page 2790 of 4449
TIMING CHAIN
EM-65
[VQ35DE]
C
D
E
F
G
H
I
J
K
L
MA
EM
Revision: 2004 November 2004 FX35/FX45
18. Remove collared O-ring from front timing chain case (left and
right side).
19. Remove right and left rocker covers. Refer to EM-51, "
ROCKER COVER" .
20. Obtain compression TDC of No. 1 cylinder as follows:
a. Rotate crankshaft pulley clockwise to align timing mark (grooved
line without color) with timing indicator.
b. Make sure intake and exhaust cam noses on No. 1 cylinder
(engine front side of right bank) are located as shown in the fig-
ure.
If not, turn crankshaft one revolution (360°) and align as
shown.
21. Remove crankshaft pulley with the following procedure:
a. Remove rear cover plate (2WD) or starter motor (AWD) and set
ring gear stopper (SST) as shown in the figure. Refer to SC-10,
"STARTING SYSTEM" .
PBIC2045E
KBIA1717J
SEM418G
PBIC1098E
Page 3590 of 4449
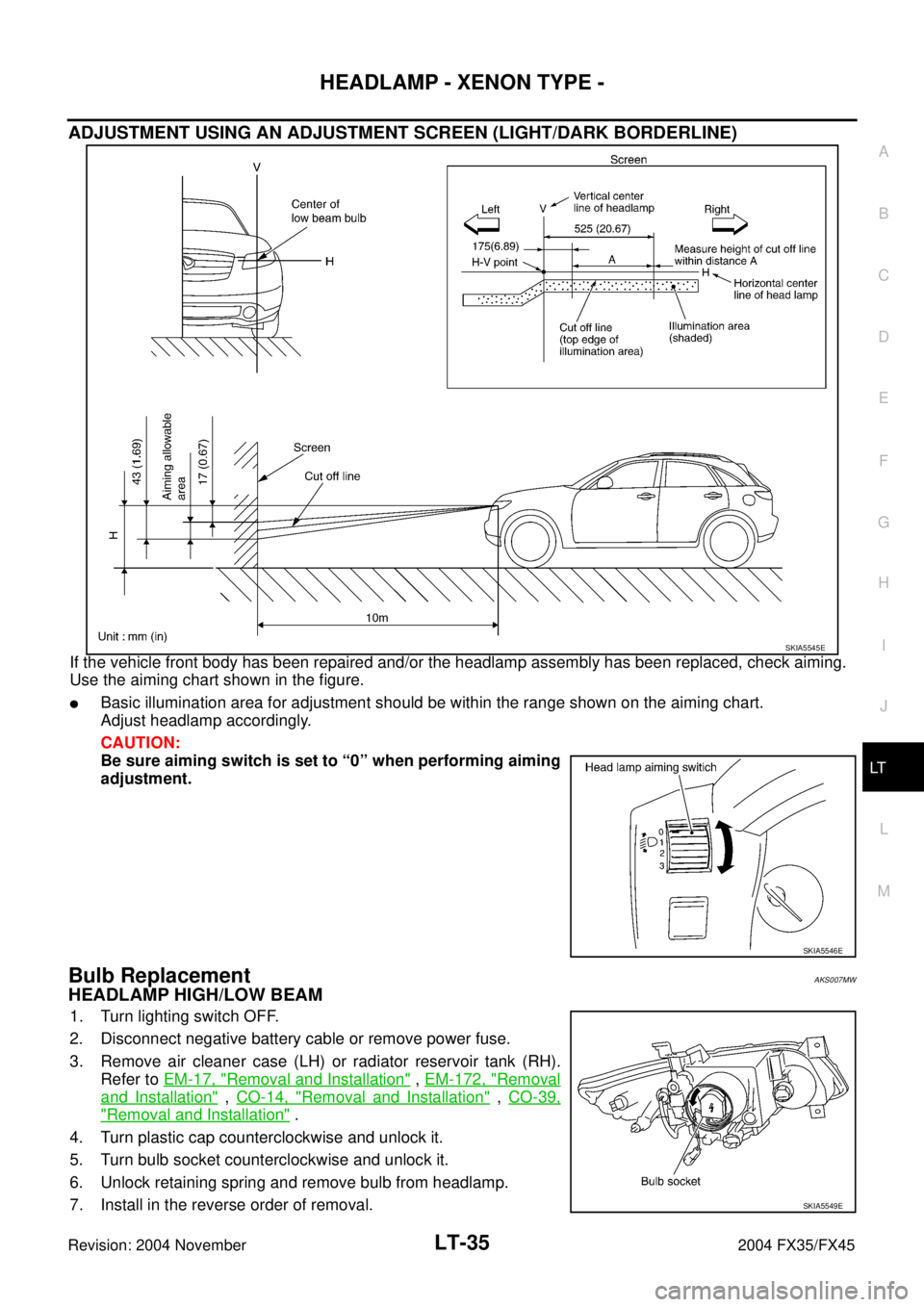
HEADLAMP - XENON TYPE -
LT-35
C
D
E
F
G
H
I
J
L
MA
B
LT
Revision: 2004 November 2004 FX35/FX45
ADJUSTMENT USING AN ADJUSTMENT SCREEN (LIGHT/DARK BORDERLINE)
If the vehicle front body has been repaired and/or the headlamp assembly has been replaced, check aiming.
Use the aiming chart shown in the figure.
Basic illumination area for adjustment should be within the range shown on the aiming chart.
Adjust headlamp accordingly.
CAUTION:
Be sure aiming switch is set to “0” when performing aiming
adjustment.
Bulb ReplacementAKS007MW
HEADLAMP HIGH/LOW BEAM
1. Turn lighting switch OFF.
2. Disconnect negative battery cable or remove power fuse.
3. Remove air cleaner case (LH) or radiator reservoir tank (RH).
Refer to EM-17, "
Removal and Installation" , EM-172, "Removal
and Installation" , CO-14, "Removal and Installation" , CO-39,
"Removal and Installation" .
4. Turn plastic cap counterclockwise and unlock it.
5. Turn bulb socket counterclockwise and unlock it.
6. Unlock retaining spring and remove bulb from headlamp.
7. Install in the reverse order of removal.
SKIA5545E
SKIA5546E
SKIA5549E
Page 3741 of 4449
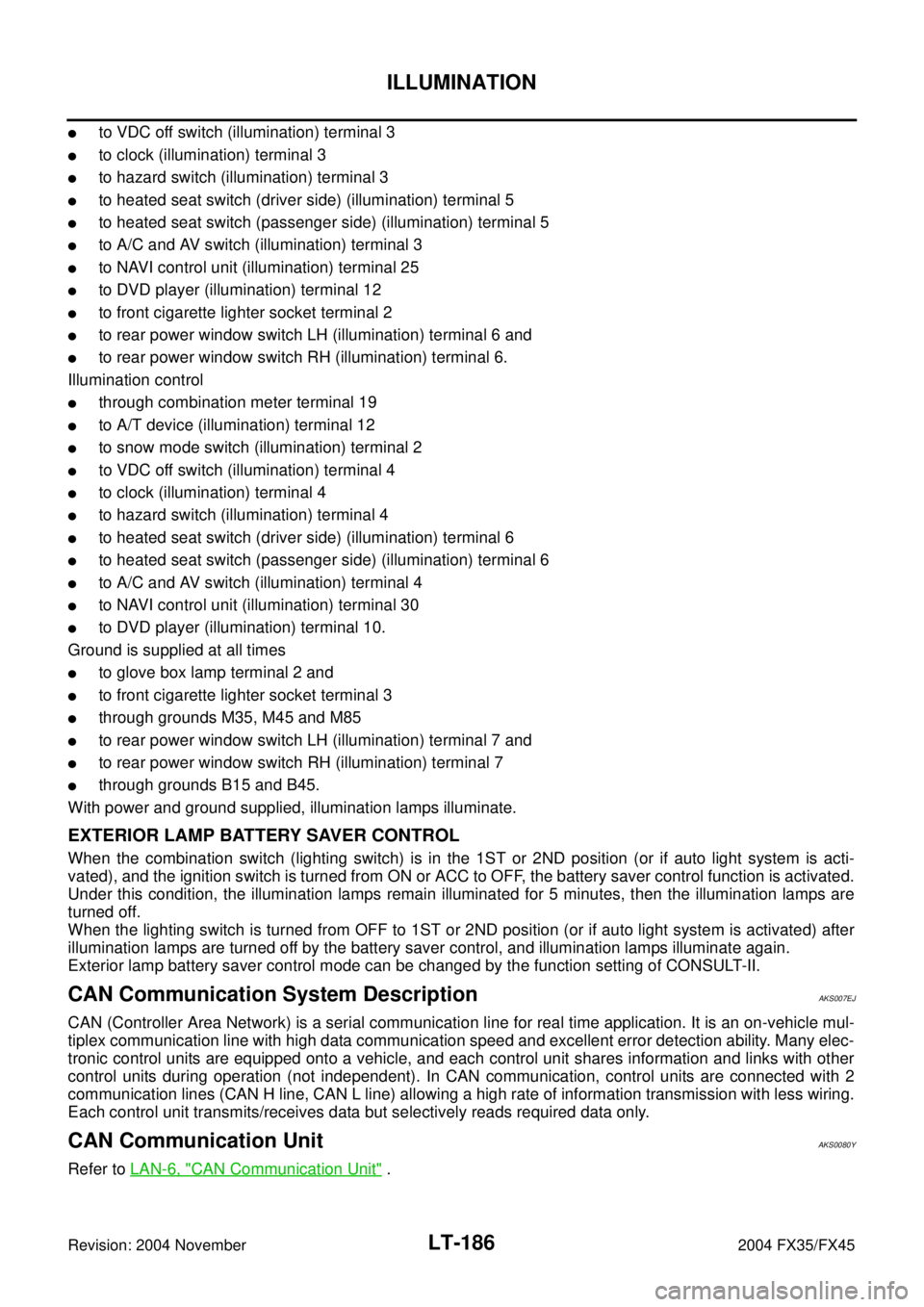
LT-186
ILLUMINATION
Revision: 2004 November 2004 FX35/FX45
to VDC off switch (illumination) terminal 3
to clock (illumination) terminal 3
to hazard switch (illumination) terminal 3
to heated seat switch (driver side) (illumination) terminal 5
to heated seat switch (passenger side) (illumination) terminal 5
to A/C and AV switch (illumination) terminal 3
to NAVI control unit (illumination) terminal 25
to DVD player (illumination) terminal 12
to front cigarette lighter socket terminal 2
to rear power window switch LH (illumination) terminal 6 and
to rear power window switch RH (illumination) terminal 6.
Illumination control
through combination meter terminal 19
to A/T device (illumination) terminal 12
to snow mode switch (illumination) terminal 2
to VDC off switch (illumination) terminal 4
to clock (illumination) terminal 4
to hazard switch (illumination) terminal 4
to heated seat switch (driver side) (illumination) terminal 6
to heated seat switch (passenger side) (illumination) terminal 6
to A/C and AV switch (illumination) terminal 4
to NAVI control unit (illumination) terminal 30
to DVD player (illumination) terminal 10.
Ground is supplied at all times
to glove box lamp terminal 2 and
to front cigarette lighter socket terminal 3
through grounds M35, M45 and M85
to rear power window switch LH (illumination) terminal 7 and
to rear power window switch RH (illumination) terminal 7
through grounds B15 and B45.
With power and ground supplied, illumination lamps illuminate.
EXTERIOR LAMP BATTERY SAVER CONTROL
When the combination switch (lighting switch) is in the 1ST or 2ND position (or if auto light system is acti-
vated), and the ignition switch is turned from ON or ACC to OFF, the battery saver control function is activated.
Under this condition, the illumination lamps remain illuminated for 5 minutes, then the illumination lamps are
turned off.
When the lighting switch is turned from OFF to 1ST or 2ND position (or if auto light system is activated) after
illumination lamps are turned off by the battery saver control, and illumination lamps illuminate again.
Exterior lamp battery saver control mode can be changed by the function setting of CONSULT-II.
CAN Communication System DescriptionAKS007EJ
CAN (Controller Area Network) is a serial communication line for real time application. It is an on-vehicle mul-
tiplex communication line with high data communication speed and excellent error detection ability. Many elec-
tronic control units are equipped onto a vehicle, and each control unit shares information and links with other
control units during operation (not independent). In CAN communication, control units are connected with 2
communication lines (CAN H line, CAN L line) allowing a high rate of information transmission with less wiring.
Each control unit transmits/receives data but selectively reads required data only.
CAN Communication UnitAKS0080Y
Refer to LAN-6, "CAN Communication Unit" .
Page 3961 of 4449
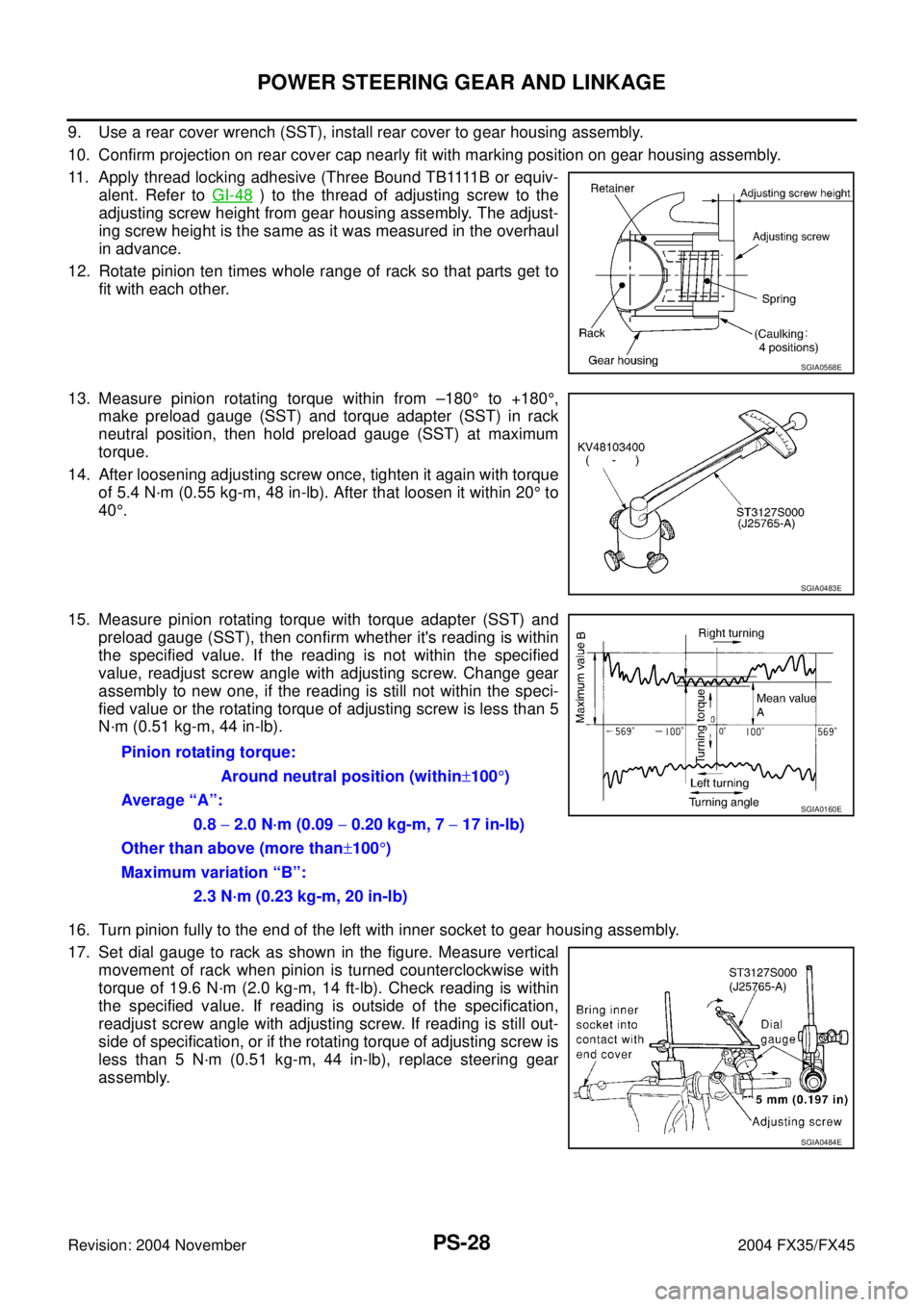
PS-28
POWER STEERING GEAR AND LINKAGE
Revision: 2004 November 2004 FX35/FX45
9. Use a rear cover wrench (SST), install rear cover to gear housing assembly.
10. Confirm projection on rear cover cap nearly fit with marking position on gear housing assembly.
11 . A p p l y t h r e a d l o c k i n g a d h e s i v e ( T h r e e B o u n d T B 1111 B o r e q u i v -
alent. Refer to GI-48
) to the thread of adjusting screw to the
adjusting screw height from gear housing assembly. The adjust-
ing screw height is the same as it was measured in the overhaul
in advance.
12. Rotate pinion ten times whole range of rack so that parts get to
fit with each other.
13. Measure pinion rotating torque within from –180° to +180°,
make preload gauge (SST) and torque adapter (SST) in rack
neutral position, then hold preload gauge (SST) at maximum
torque.
14. After loosening adjusting screw once, tighten it again with torque
of 5.4 N·m (0.55 kg-m, 48 in-lb). After that loosen it within 20° to
40°.
15. Measure pinion rotating torque with torque adapter (SST) and
preload gauge (SST), then confirm whether it's reading is within
the specified value. If the reading is not within the specified
value, readjust screw angle with adjusting screw. Change gear
assembly to new one, if the reading is still not within the speci-
fied value or the rotating torque of adjusting screw is less than 5
N·m (0.51 kg-m, 44 in-lb).
16. Turn pinion fully to the end of the left with inner socket to gear housing assembly.
17. Set dial gauge to rack as shown in the figure. Measure vertical
movement of rack when pinion is turned counterclockwise with
torque of 19.6 N·m (2.0 kg-m, 14 ft-lb). Check reading is within
the specified value. If reading is outside of the specification,
readjust screw angle with adjusting screw. If reading is still out-
side of specification, or if the rotating torque of adjusting screw is
less than 5 N·m (0.51 kg-m, 44 in-lb), replace steering gear
assembly.
SGIA0568E
SGIA0483E
Pinion rotating torque:
Around neutral position (within±100°)
Average “A”:
0.8 − 2.0 N·m (0.09 − 0.20 kg-m, 7 − 17 in-lb)
Other than above (more than±100°)
Maximum variation “B”:
2.3 N·m (0.23 kg-m, 20 in-lb)
SGIA0160E
SGIA0484E