Page 921 of 1574
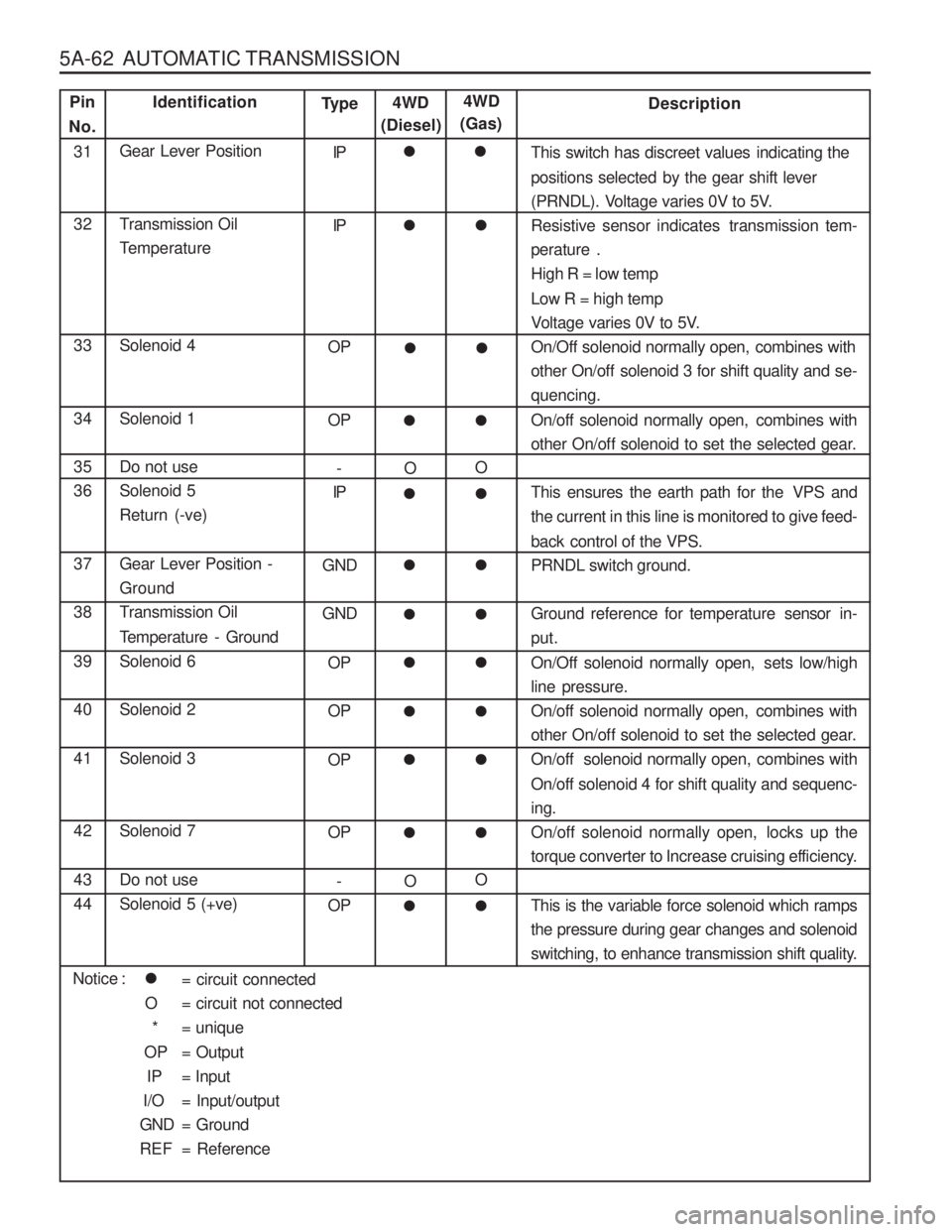
5A-62 AUTOMATIC TRANSMISSION
Identification
Gear Lever Position
Transmission Oil
Temperature Solenoid 4 Solenoid 1 Do not use Solenoid 5Return (-ve) Gear Lever Position - Ground
Transmission Oil
Temperature - Ground Solenoid 6 Solenoid 2 Solenoid 3 Solenoid 7 Do not use Solenoid 5 (+ve) Type
IP IP
OPOP -
IP
GND GND OPOP OP OP -
OP Description
This switch has discreet values indicating the
positions selected by the gear shift lever
(PRNDL). Voltage varies 0V to 5V.
Resistive sensor indicates transmission tem-perature .High R = low temp Low R = high temp
Voltage varies 0V to 5V.
On/Off solenoid normally open, combines with
other On/off solenoid 3 for shift quality and se-quencing.
On/off solenoid normally open, combines with
other On/off solenoid to set the selected gear.
This ensures the earth path for the VPS and
the current in this line is monitored to give feed-
back control of the VPS. PRNDL switch ground. Ground reference for temperature sensor in-
put.
On/Off solenoid normally open, sets low/high line pressure.
On/off solenoid normally open, combines with
other On/off solenoid to set the selected gear.
On/off solenoid normally open, combines with
On/off solenoid 4 for shift quality and sequenc- ing.
On/off solenoid normally open, locks up the
torque converter to Increase cruising efficiency. This is the variable force solenoid which ramps the pressure during gear changes and solenoid
switching, to enhance transmission shift quality.
4WD
(Diesel)
O O
4WD
(Gas)
O O
Pin
No. 31 32 33 34 35 36 37 38 39 40 41 42 43 44
= circuit connected
O = circuit not connected
* = unique
OP = Output
IP = Input
I/O = Input/output
GND = Ground
REF = Reference
Notice :
Page 939 of 1574
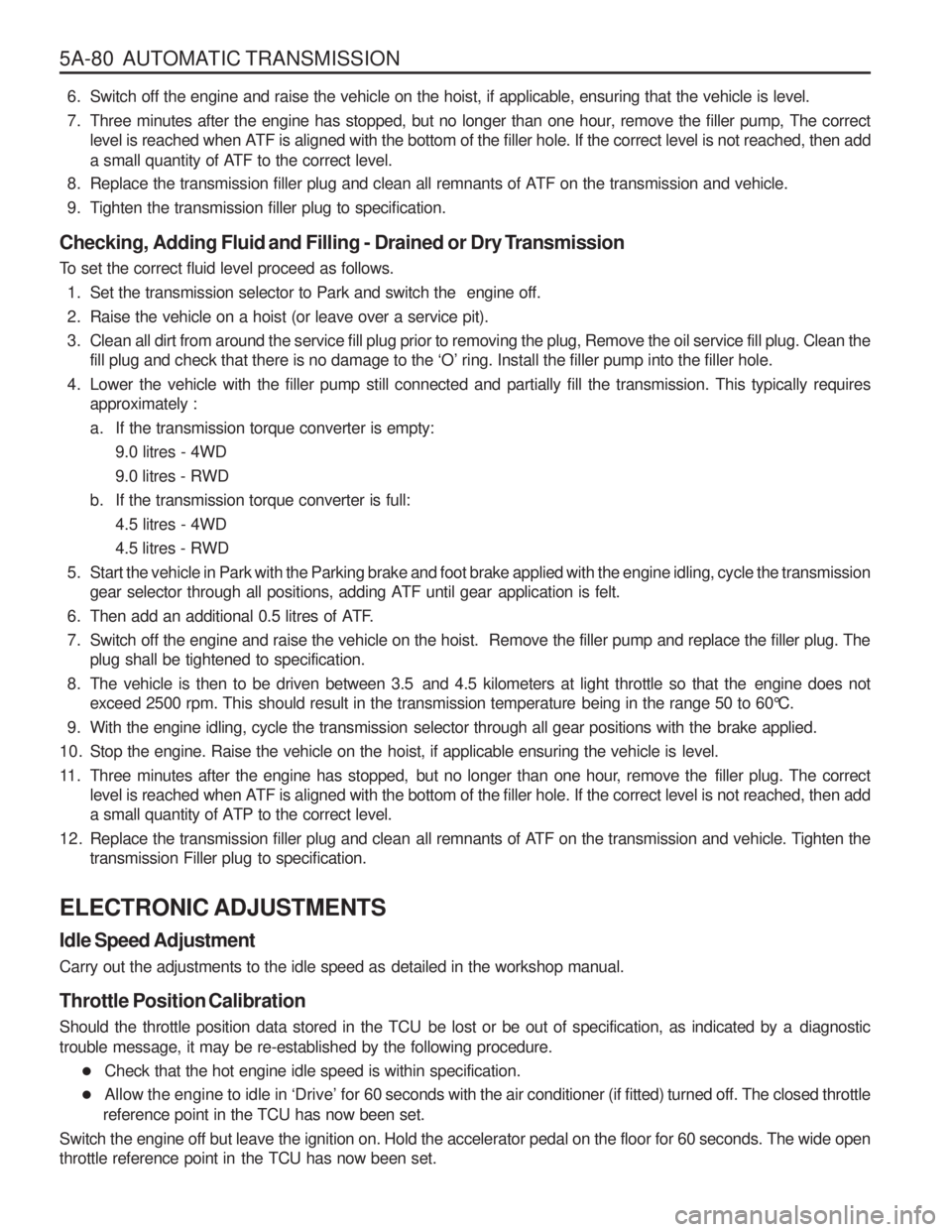
5A-80 AUTOMATIC TRANSMISSION6. Switch off the engine and raise the vehicle on the hoist, if applicable, ensuring that the vehicle is level.
7. Three minutes after the engine has stopped, but no longer than one hour, remove the filler pump, The correct level is reached when ATF is aligned with the bottom of the filler hole. If the correct level is not reached, then add
a small quantity of ATF to the correct level.
8. Replace the transmission filler plug and clean all remnants of ATF on the transmission and vehicle.
9. Tighten the transmission filler plug to specification.
Checking, Adding Fluid and Filling - Drained or Dry Transmission
To set the correct fluid level proceed as follows. 1. Set the transmission selector to Park and switch the engine off.
2. Raise the vehicle on a hoist (or leave over a service pit).
3. Clean all dirt from around the service fill plug prior to removing the plug, Remove the oil service fill plug. Clean the fill plug and check that there is no damage to the ‘O’ ring. Install the filler pump into the filler hole.
4. Lower the vehicle with the filler pump still connected and partially fill the transmission. This typically requires approximately :
a. If the transmission torque converter is empty:
9.0 litres - 4WD9.0 litres - RWD
b. If the transmission torque converter is full: 4.5 litres - 4WD4.5 litres - RWD
5. Start the vehicle in Park with the Parking brake and foot brake applied with the engine idling, cycle the transmission gear selector through all positions, adding ATF until gear application is felt.
6. Then add an additional 0.5 litres of ATF.
7. Switch off the engine and raise the vehicle on the hoist. Remove the filler pump and replace the filler plug. The plug shall be tightened to specification.
8. The vehicle is then to be driven between 3.5 and 4.5 kilometers at light throttle so that the engine does not exceed 2500 rpm. This should result in the transmission temperature being in the range 50 to 60 °C.
9. With the engine idling, cycle the transmission selector through all gear positions with the brake applied.
10. Stop the engine. Raise the vehicle on the hoist, if applicable ensuring the vehicle is level.
11. Three minutes after the engine has stopped, but no longer than one hour, remove the filler plug. The correct level is reached when ATF is aligned with the bottom of the filler hole. If the correct level is not reached, then add
a small quantity of ATP to the correct level.
12. Replace the transmission filler plug and clean all remnants of ATF on the transmission and vehicle. Tighten the transmission Filler plug to specification.
ELECTRONIC ADJUSTMENTS Idle Speed Adjustment
Carry out the adjustments to the idle speed as detailed in the workshop manual.
Throttle Position Calibration
Should the throttle position data stored in the TCU be lost or be out of specification, as indicated by a diagnostic
trouble message, it may be re-established by the following procedure. Check that the hot engine idle speed is within specification.
Allow the engine to idle in ‘Drive ’ for 60 seconds with the air conditioner (if fitted) turned off. The closed throttle
reference point in the TCU has now been set.
Switch the engine off but leave the ignition on. Hold the accelerator pedal on the floor for 60 seconds. The wide open
throttle reference point in the TCU has now been set.
Page 940 of 1574
AUTOMATIC TRANSMISSION 5A-81
Throttle Clearing
The leant throttle clearing routine uses the mode switch and gear lever. Carry out the following steps to complete the
automated throttle clearing procedure:
1. Switch ignition ‘ON ’ with handbrake applied and engine ‘OFF ’.
2. Select ‘M1 ’ and ‘WINTER ’ mode.
3. Move the T-bar to ‘M2 ’ and then select ‘NORMAL ’ or ‘POWER ’ mode.
4. Move the T-bar to ‘M3 ’ and then select ‘WINTER ’ mode.
Vehicle Coding
The vehicle coding is integrated as part of the diagnostic software. The coding applies to the following vehicle models: 1. 4WD Gasoline E32.
2. 4WD Gasoline 523
3. 4WD Gasoline 520.
4. 4WD Diesel D29NA.
5. 4WD Diesel D29LA.
6. 4WD Diesel D23LA.
7. RWD E20.
8. RWD E23.
Page 945 of 1574
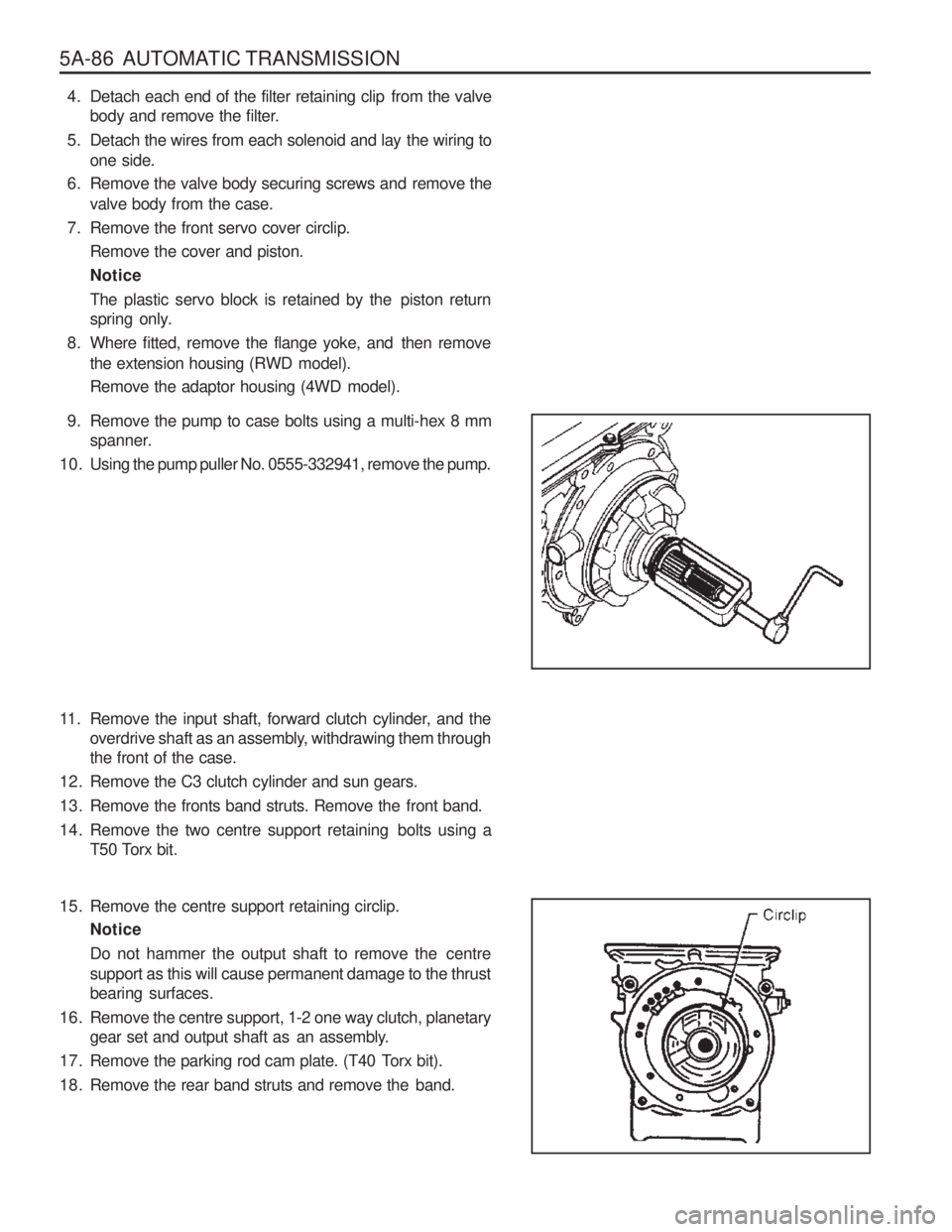
5A-86 AUTOMATIC TRANSMISSION
9. Remove the pump to case bolts using a multi-hex 8 mmspanner.
10. Using the pump puller No. 0555-332941, remove the pump.
11. Remove the input shaft, forward clutch cylinder, and the overdrive shaft as an assembly, withdrawing them through the front of the case.
12. Remove the C3 clutch cylinder and sun gears.
13. Remove the fronts band struts. Remove the front band.
14. Remove the two centre support retaining bolts using a T50 Torx bit.
15. Remove the centre support retaining circlip. Notice
Do not hammer the output shaft to remove the centre
support as this will cause permanent damage to the thrust bearing surfaces.
16. Remove the centre support, 1-2 one way clutch, planetary gear set and output shaft as an assembly.
17. Remove the parking rod cam plate. (T40 Torx bit).
18. Remove the rear band struts and remove the band. 4. Detach each end of the filter retaining clip from the valve
body and remove the filter.
5. Detach the wires from each solenoid and lay the wiring to one side.
6. Remove the valve body securing screws and remove the valve body from the case.
7. Remove the front servo cover circlip. Remove the cover and piston.Notice
The plastic servo block is retained by the piston return
spring only.
8. Where fitted, remove the flange yoke, and then remove the extension housing (RWD model).
Remove the adaptor housing (4WD model).
Page 946 of 1574
AUTOMATIC TRANSMISSION 5A-87
Transmission Case
To teardown the transmission case, proceed as follows:
1. Remove the pin from the cross shaft inhibitor switch side(4WD models) using tool No.0555-332942.
2. Remove the inhibitor switch from the case.
Remove the cross shaft seals with special tool No.0555- 331893.
3. Remove the circlip from the cross-shaft. Pull the shaft to release the drive pin from the selector quadrant.
4. Using tool No. 0555-331897, press the pin from the cross- shaft and withdraw the shaft from the case. Retrieve the spring and pin
5. Remove the manual valve lever and the park rod.
6. Remove the 10 pin plug from the wiring loom bracket adjacent to the inhibitor switch(RWD models),
7. Depress the tangs and withdraw the 10 pin connector from the case. Remove the loom assembly.
Page 955 of 1574
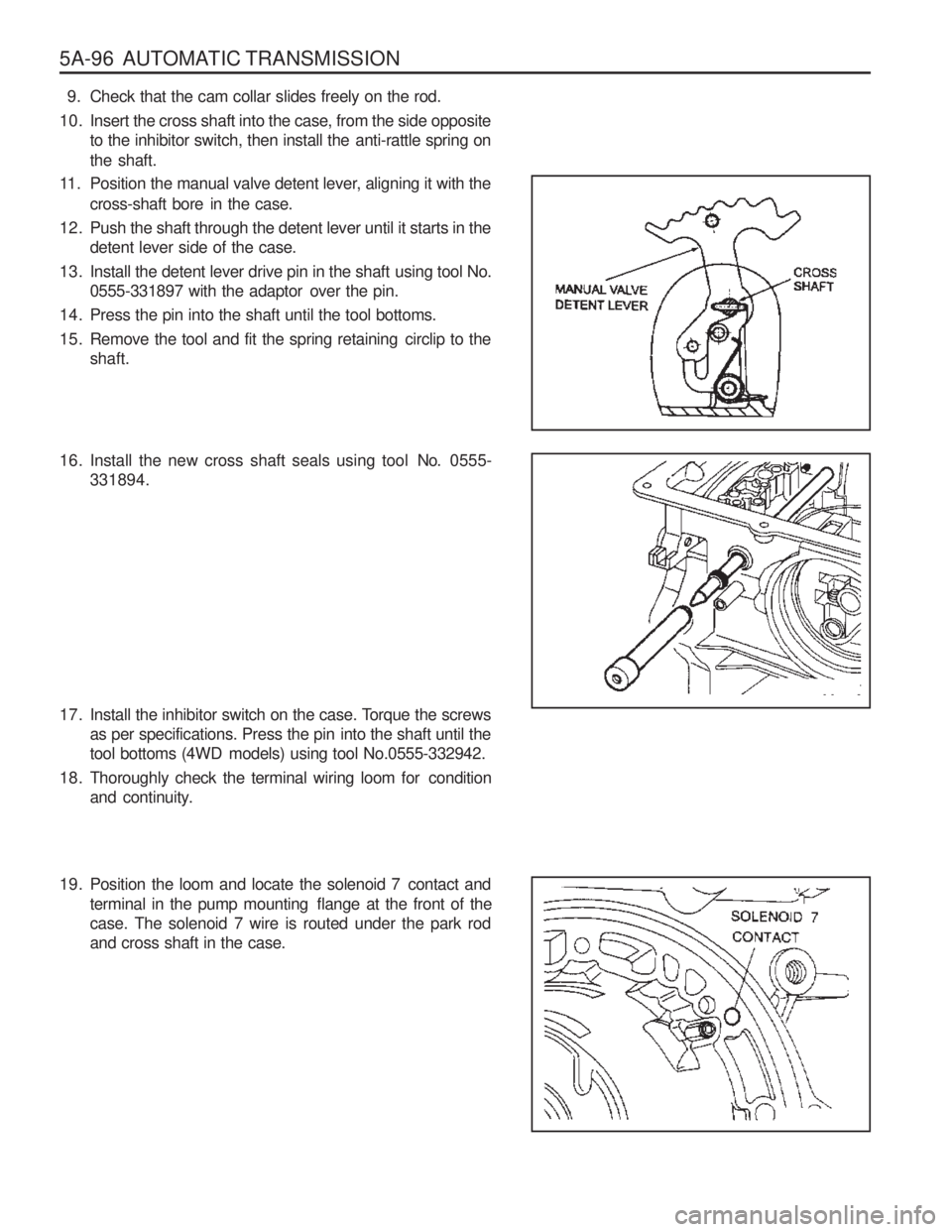
5A-96 AUTOMATIC TRANSMISSION9. Check that the cam collar slides freely on the rod.
10. Insert the cross shaft into the case, from the side opposite to the inhibitor switch, then install the anti-rattle spring on the shaft.
11. Position the manual valve detent lever, aligning it with the cross-shaft bore in the case.
12. Push the shaft through the detent lever until it starts in the detent lever side of the case.
13. Install the detent lever drive pin in the shaft using tool No. 0555-331897 with the adaptor over the pin.
14. Press the pin into the shaft until the tool bottoms.
15. Remove the tool and fit the spring retaining circlip to the shaft.
16. Install the new cross shaft seals using tool No. 0555-
331894.
17. Install the inhibitor switch on the case. Torque the screws as per specifications. Press the pin into the shaft until the
tool bottoms (4WD models) using tool No.0555-332942.
18. Thoroughly check the terminal wiring loom for condition and continuity.
19. Position the loom and locate the solenoid 7 contact andterminal in the pump mounting flange at the front of the case. The solenoid 7 wire is routed under the park rodand cross shaft in the case.
Page 956 of 1574
AUTOMATIC TRANSMISSION 5A-97
20. Install the ten pin connector in the case engaging the tangson the connector in the notches in case.
4WD MODELS ONLY
21. Route the portion of the wiring loom coming out of the case down between the inhibitor switch and the case.
Position the ten pin plug on the wiring loom bracket .
Page 960 of 1574
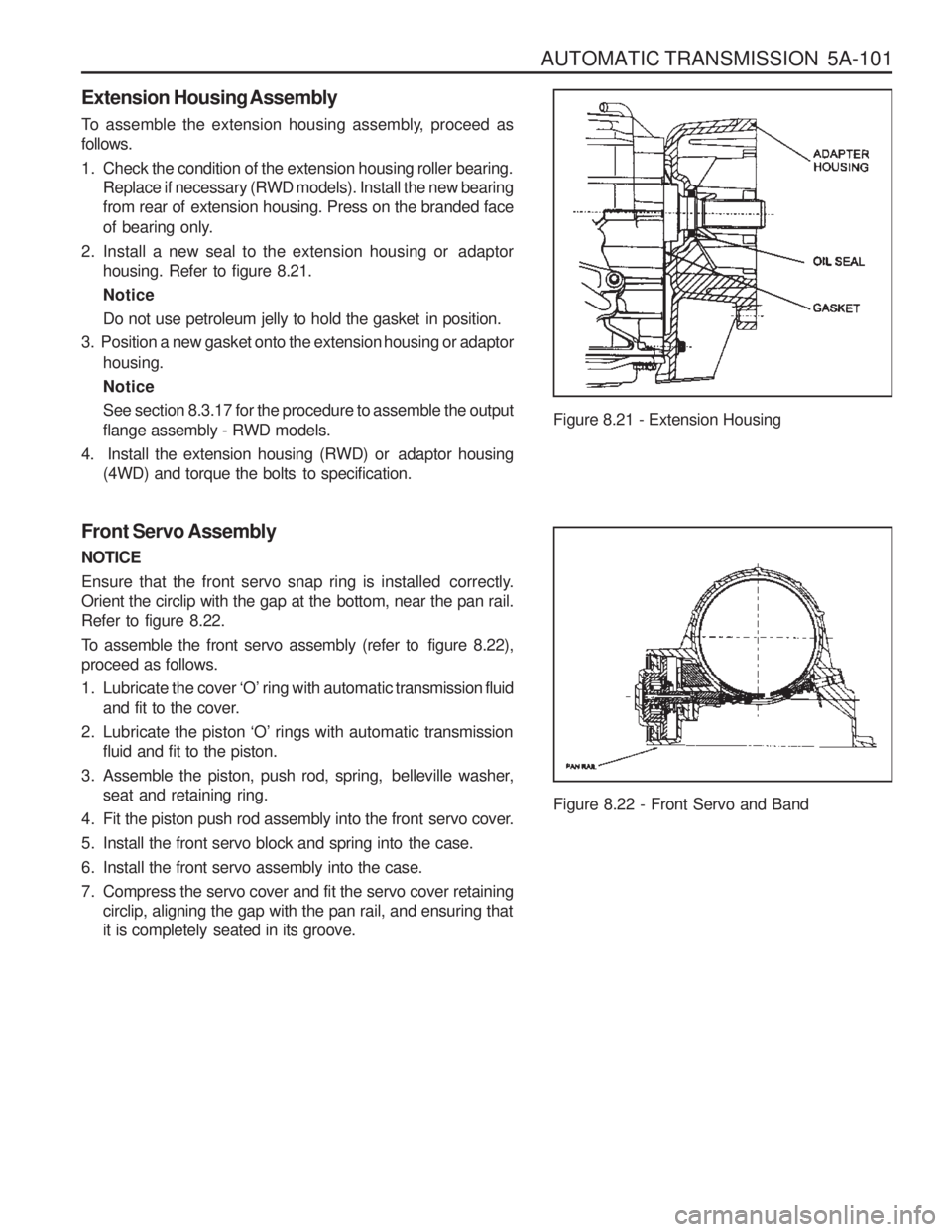
AUTOMATIC TRANSMISSION 5A-101
Extension Housing Assembly
To assemble the extension housing assembly, proceed as follows.
1. Check the condition of the extension housing roller bearing.Replace if necessary (RWD models). Install the new bearing
from rear of extension housing. Press on the branded face
of bearing only.
2. Install a new seal to the extension housing or adaptor housing. Refer to figure 8.21. Notice
Do not use petroleum jelly to hold the gasket in position.
3. Position a new gasket onto the extension housing or adaptor housing.Notice
See section 8.3.17 for the procedure to assemble the output
flange assembly - RWD models.
4. Install the extension housing (RWD) or adaptor housing (4WD) and torque the bolts to specification.
Front Servo Assembly NOTICE
Ensure that the front servo snap ring is installed correctly.
Orient the circlip with the gap at the bottom, near the pan rail.Refer to figure 8.22.
To assemble the front servo assembly (refer to figure 8.22), proceed as follows.
1. Lubricate the cover ‘O’ ring with automatic transmission fluid
and fit to the cover.
2. Lubricate the piston ‘O’ rings with automatic transmission
fluid and fit to the piston.
3. Assemble the piston, push rod, spring, belleville washer, seat and retaining ring.
4. Fit the piston push rod assembly into the front servo cover.
5. Install the front servo block and spring into the case.
6. Install the front servo assembly into the case.
7. Compress the servo cover and fit the servo cover retaining circlip, aligning the gap with the pan rail, and ensuring that
it is completely seated in its groove.
Figure 8.21 - Extension Housing
Figure 8.22 - Front Servo and Band