Page 930 of 1672
STEERING
REPAIRS 57-43
6.Disconnect 2 multiplugs from wiper switch
assembly.
7.Disconnect 2 multiplugs from light switch
assembly.
8.Loosen screw and remove switch assembly.
9.Disconnect ignition switch multiplug. 10.Disconnect multiplug from ignition switch
housing.
11.Release harness from column clip.
12.Remove 4 nuts securing steering column
assembly to fascia rail and remove steering
column assembly.
13.Remove rubber boot from steering column
assembly.
Page 931 of 1672
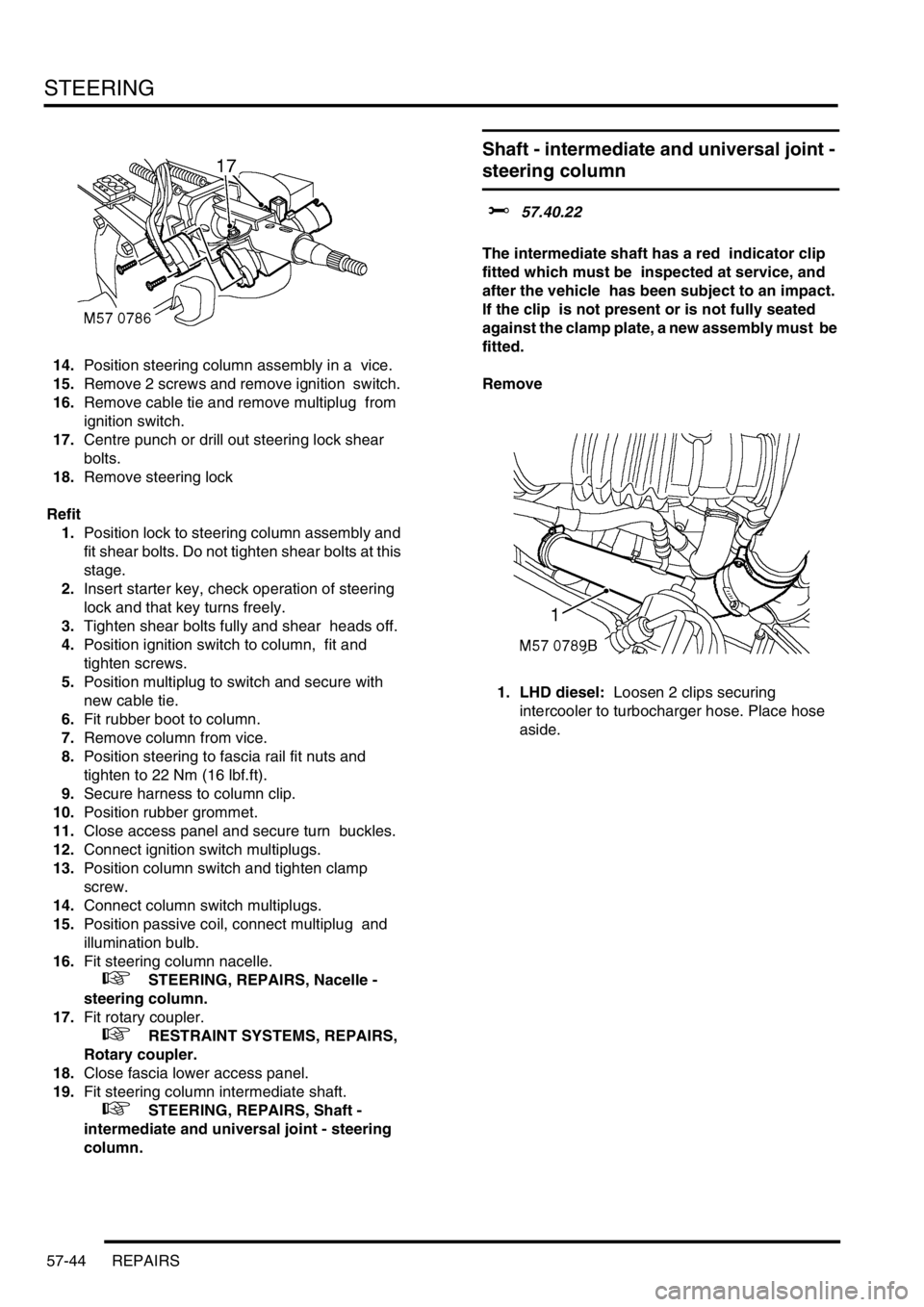
STEERING
57-44 REPAIRS
14.Position steering column assembly in a vice.
15.Remove 2 screws and remove ignition switch.
16.Remove cable tie and remove multiplug from
ignition switch.
17.Centre punch or drill out steering lock shear
bolts.
18.Remove steering lock
Refit
1.Position lock to steering column assembly and
fit shear bolts. Do not tighten shear bolts at this
stage.
2.Insert starter key, check operation of steering
lock and that key turns freely.
3.Tighten shear bolts fully and shear heads off.
4.Position ignition switch to column, fit and
tighten screws.
5.Position multiplug to switch and secure with
new cable tie.
6.Fit rubber boot to column.
7.Remove column from vice.
8.Position steering to fascia rail fit nuts and
tighten to 22 Nm (16 lbf.ft).
9.Secure harness to column clip.
10.Position rubber grommet.
11.Close access panel and secure turn buckles.
12.Connect ignition switch multiplugs.
13.Position column switch and tighten clamp
screw.
14.Connect column switch multiplugs.
15.Position passive coil, connect multiplug and
illumination bulb.
16.Fit steering column nacelle.
+ STEERING, REPAIRS, Nacelle -
steering column.
17.Fit rotary coupler.
+ RESTRAINT SYSTEMS, REPAIRS,
Rotary coupler.
18.Close fascia lower access panel.
19.Fit steering column intermediate shaft.
+ STEERING, REPAIRS, Shaft -
intermediate and universal joint - steering
column.
Shaft - intermediate and universal joint -
steering column
$% 57.40.22
The intermediate shaft has a red indicator clip
fitted which must be inspected at service, and
after the vehicle has been subject to an impact.
If the clip is not present or is not fully seated
against the clamp plate, a new assembly must be
fitted.
Remove
1. LHD diesel: Loosen 2 clips securing
intercooler to turbocharger hose. Place hose
aside.
Page 970 of 1672
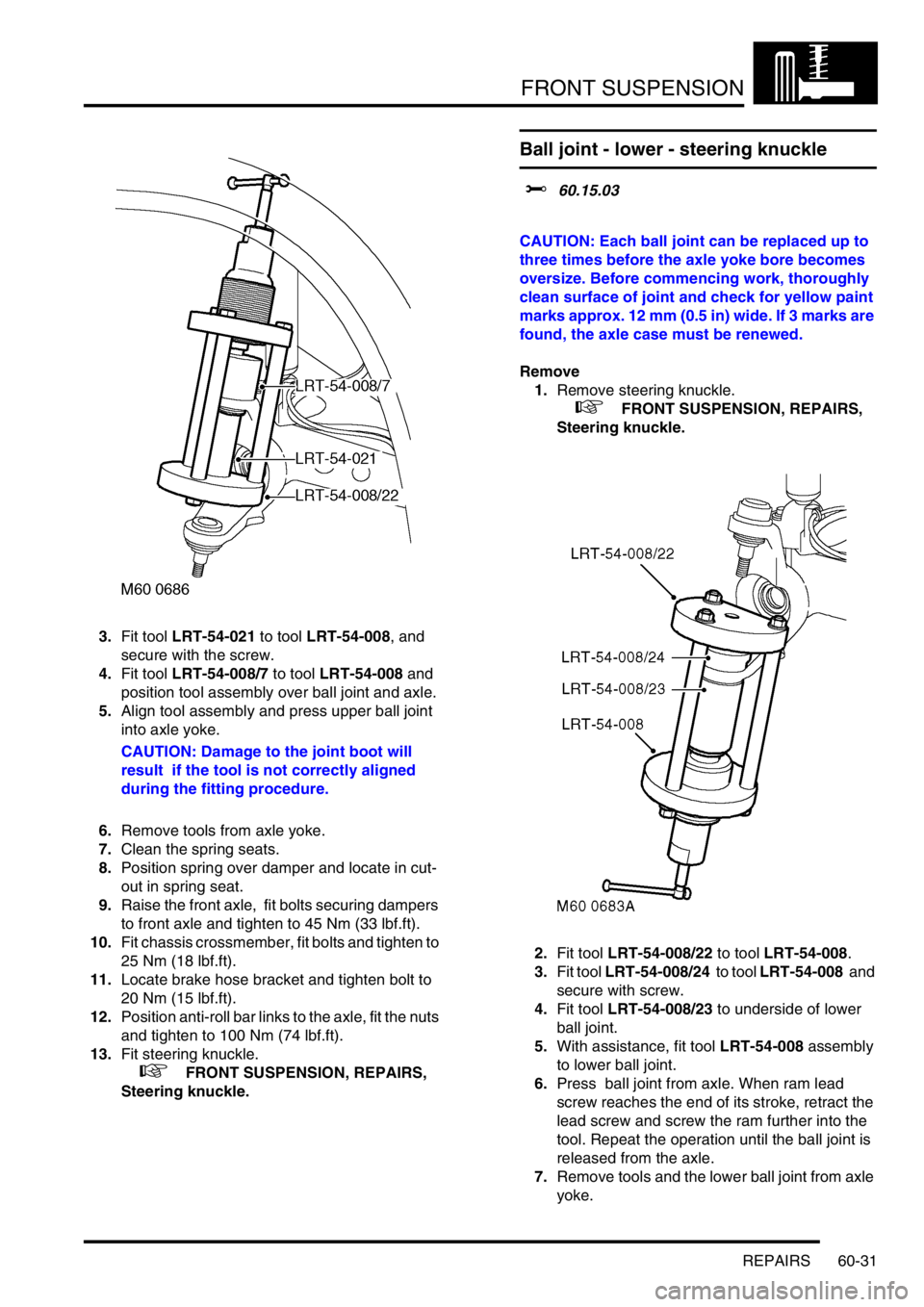
FRONT SUSPENSION
REPAIRS 60-31
3.Fit tool LRT-54-021 to tool LRT-54-008, and
secure with the screw.
4.Fit tool LRT-54-008/7 to tool LRT-54-008 and
position tool assembly over ball joint and axle.
5.Align tool assembly and press upper ball joint
into axle yoke.
CAUTION: Damage to the joint boot will
result if the tool is not correctly aligned
during the fitting procedure.
6.Remove tools from axle yoke.
7.Clean the spring seats.
8.Position spring over damper and locate in cut-
out in spring seat.
9.Raise the front axle, fit bolts securing dampers
to front axle and tighten to 45 Nm (33 lbf.ft).
10.Fit chassis crossmember, fit bolts and tighten to
25 Nm (18 lbf.ft).
11.Locate brake hose bracket and tighten bolt to
20 Nm (15 lbf.ft).
12.Position anti-roll bar links to the axle, fit the nuts
and tighten to 100 Nm (74 lbf.ft).
13.Fit steering knuckle.
+ FRONT SUSPENSION, REPAIRS,
Steering knuckle.
Ball joint - lower - steering knuckle
$% 60.15.03
CAUTION: Each ball joint can be replaced up to
three times before the axle yoke bore becomes
oversize. Before commencing work, thoroughly
clean surface of joint and check for yellow paint
marks approx. 12 mm (0.5 in) wide. If 3 marks are
found, the axle case must be renewed.
Remove
1.Remove steering knuckle.
+ FRONT SUSPENSION, REPAIRS,
Steering knuckle.
2.Fit tool LRT-54-008/22 to tool LRT-54-008.
3.Fit tool LRT-54-008/24 to tool LRT-54-008 and
secure with screw.
4.Fit tool LRT-54-008/23 to underside of lower
ball joint.
5.With assistance, fit tool LRT-54-008 assembly
to lower ball joint.
6.Press ball joint from axle. When ram lead
screw reaches the end of its stroke, retract the
lead screw and screw the ram further into the
tool. Repeat the operation until the ball joint is
released from the axle.
7.Remove tools and the lower ball joint from axle
yoke.
Page 971 of 1672
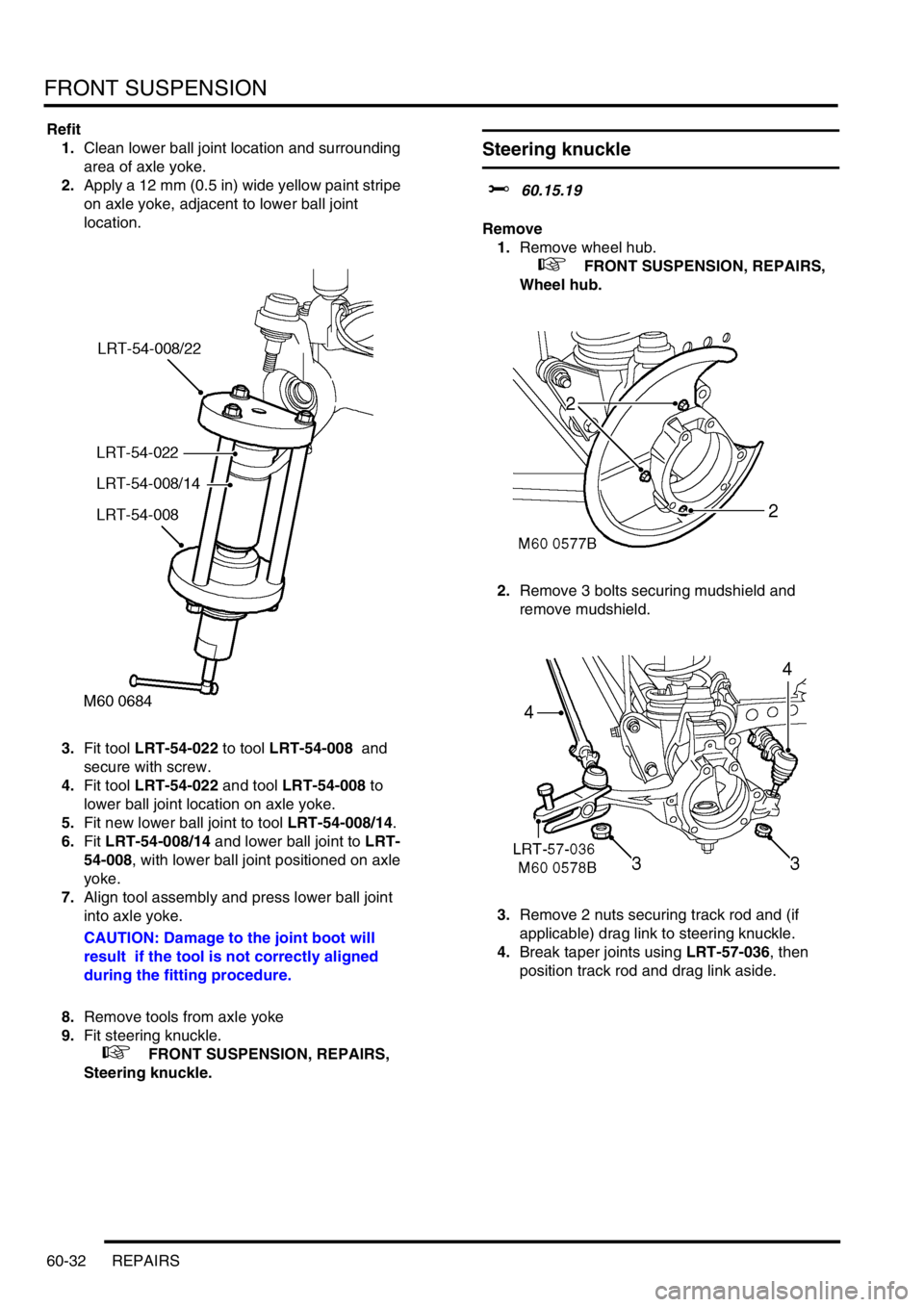
FRONT SUSPENSION
60-32 REPAIRS
Refit
1.Clean lower ball joint location and surrounding
area of axle yoke.
2.Apply a 12 mm (0.5 in) wide yellow paint stripe
on axle yoke, adjacent to lower ball joint
location.
3.Fit tool LRT-54-022 to tool LRT-54-008 and
secure with screw.
4.Fit tool LRT-54-022 and tool LRT-54-008 to
lower ball joint location on axle yoke.
5.Fit new lower ball joint to tool LRT-54-008/14.
6.Fit LRT-54-008/14 and lower ball joint to LRT-
54-008, with lower ball joint positioned on axle
yoke.
7.Align tool assembly and press lower ball joint
into axle yoke.
CAUTION: Damage to the joint boot will
result if the tool is not correctly aligned
during the fitting procedure.
8.Remove tools from axle yoke
9.Fit steering knuckle.
+ FRONT SUSPENSION, REPAIRS,
Steering knuckle.
Steering knuckle
$% 60.15.19
Remove
1.Remove wheel hub.
+ FRONT SUSPENSION, REPAIRS,
Wheel hub.
2.Remove 3 bolts securing mudshield and
remove mudshield.
3.Remove 2 nuts securing track rod and (if
applicable) drag link to steering knuckle.
4.Break taper joints using LRT-57-036, then
position track rod and drag link aside.
Page 1339 of 1672
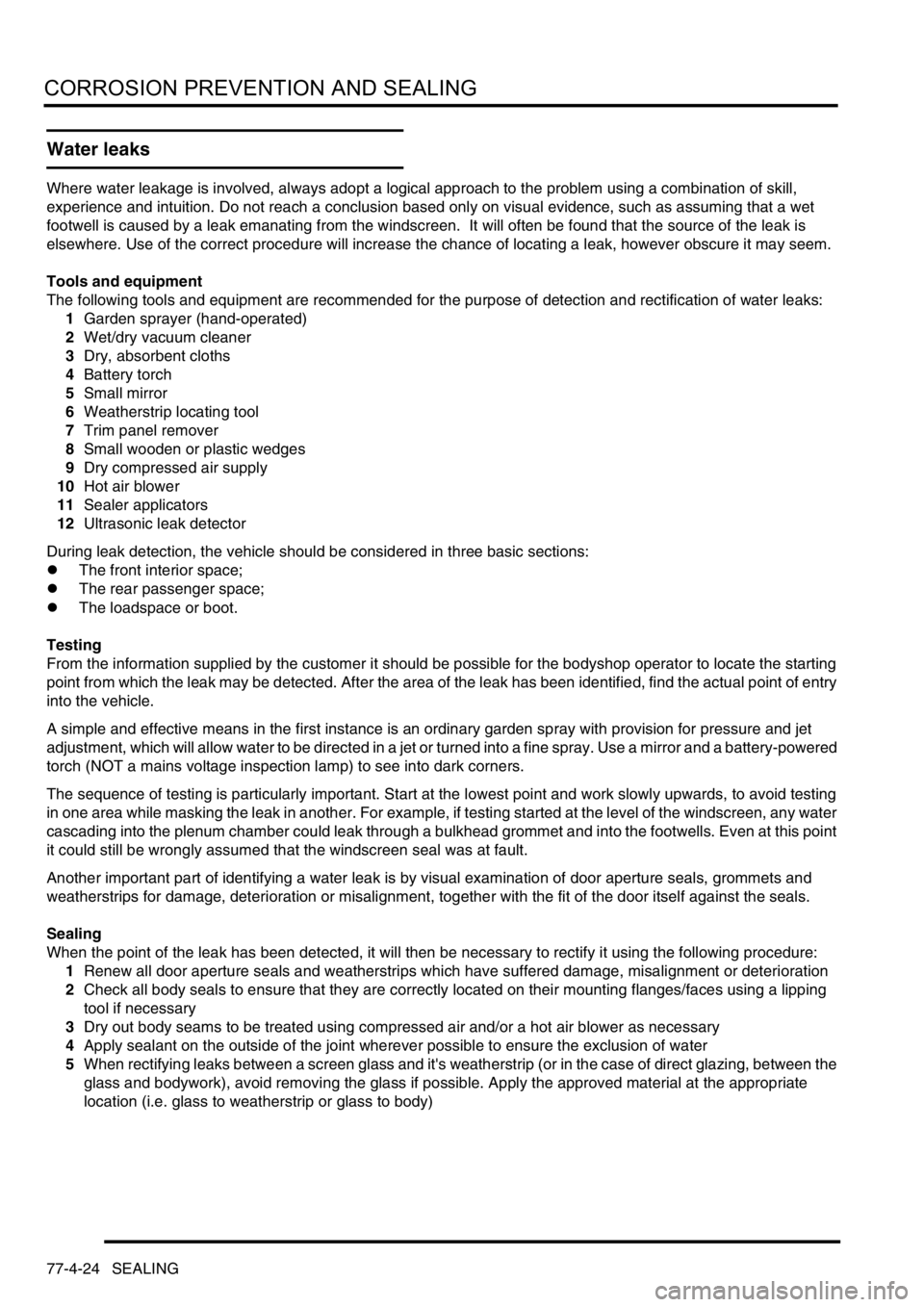
CORROSION PREVENTION AND SEALING
77-4-24 SEALING
Water leaks
Where water leakage is involved, always adopt a logical approach to the problem using a combination of skill,
experience and intuition. Do not reach a conclusion based only on visual evidence, such as assuming that a wet
footwell is caused by a leak emanating from the windscreen. It will often be found that the source of the leak is
elsewhere. Use of the correct procedure will increase the chance of locating a leak, however obscure it may seem.
Tools and equipment
The following tools and equipment are recommended for the purpose of detection and rectification of water leaks:
1Garden sprayer (hand-operated)
2Wet/dry vacuum cleaner
3Dry, absorbent cloths
4Battery torch
5Small mirror
6Weatherstrip locating tool
7Trim panel remover
8Small wooden or plastic wedges
9Dry compressed air supply
10Hot air blower
11Sealer applicators
12Ultrasonic leak detector
During leak detection, the vehicle should be considered in three basic sections:
lThe front interior space;
lThe rear passenger space;
lThe loadspace or boot.
Testing
From the information supplied by the customer it should be possible for the bodyshop operator to locate the starting
point from which the leak may be detected. After the area of the leak has been identified, find the actual point of entry
into the vehicle.
A simple and effective means in the first instance is an ordinary garden spray with provision for pressure and jet
adjustment, which will allow water to be directed in a jet or turned into a fine spray. Use a mirror and a battery-powered
torch (NOT a mains voltage inspection lamp) to see into dark corners.
The sequence of testing is particularly important. Start at the lowest point and work slowly upwards, to avoid testing
in one area while masking the leak in another. For example, if testing started at the level of the windscreen, any water
cascading into the plenum chamber could leak through a bulkhead grommet and into the footwells. Even at this point
it could still be wrongly assumed that the windscreen seal was at fault.
Another important part of identifying a water leak is by visual examination of door aperture seals, grommets and
weatherstrips for damage, deterioration or misalignment, together with the fit of the door itself against the seals.
Sealing
When the point of the leak has been detected, it will then be necessary to rectify it using the following procedure:
1Renew all door aperture seals and weatherstrips which have suffered damage, misalignment or deterioration
2Check all body seals to ensure that they are correctly located on their mounting flanges/faces using a lipping
tool if necessary
3Dry out body seams to be treated using compressed air and/or a hot air blower as necessary
4Apply sealant on the outside of the joint wherever possible to ensure the exclusion of water
5When rectifying leaks between a screen glass and it's weatherstrip (or in the case of direct glazing, between the
glass and bodywork), avoid removing the glass if possible. Apply the approved material at the appropriate
location (i.e. glass to weatherstrip or glass to body)