Page 331 of 2100
DIFFERENTIAL (FRONT) 4A1±18
16. Tighten the cap bolt to the specified torque.
Torque: 97 N´m (72 lb ft)
425RS036
Gear Tooth Contact Pattern Check and
Adjustment
1. Apply a thin coat of prussian blue or equivalent to
at least 7±8 ring gear teeth. Rotate the ring gear
and inspect the contact point of the impressions
and make the necessary adjustments as
described in the next page.
425RS038
Legend
(1) Heel
(2) Toe
(3) Concave Side(Coast)
(4) Convex Side(Drive)
425RS039
Page 362 of 2100
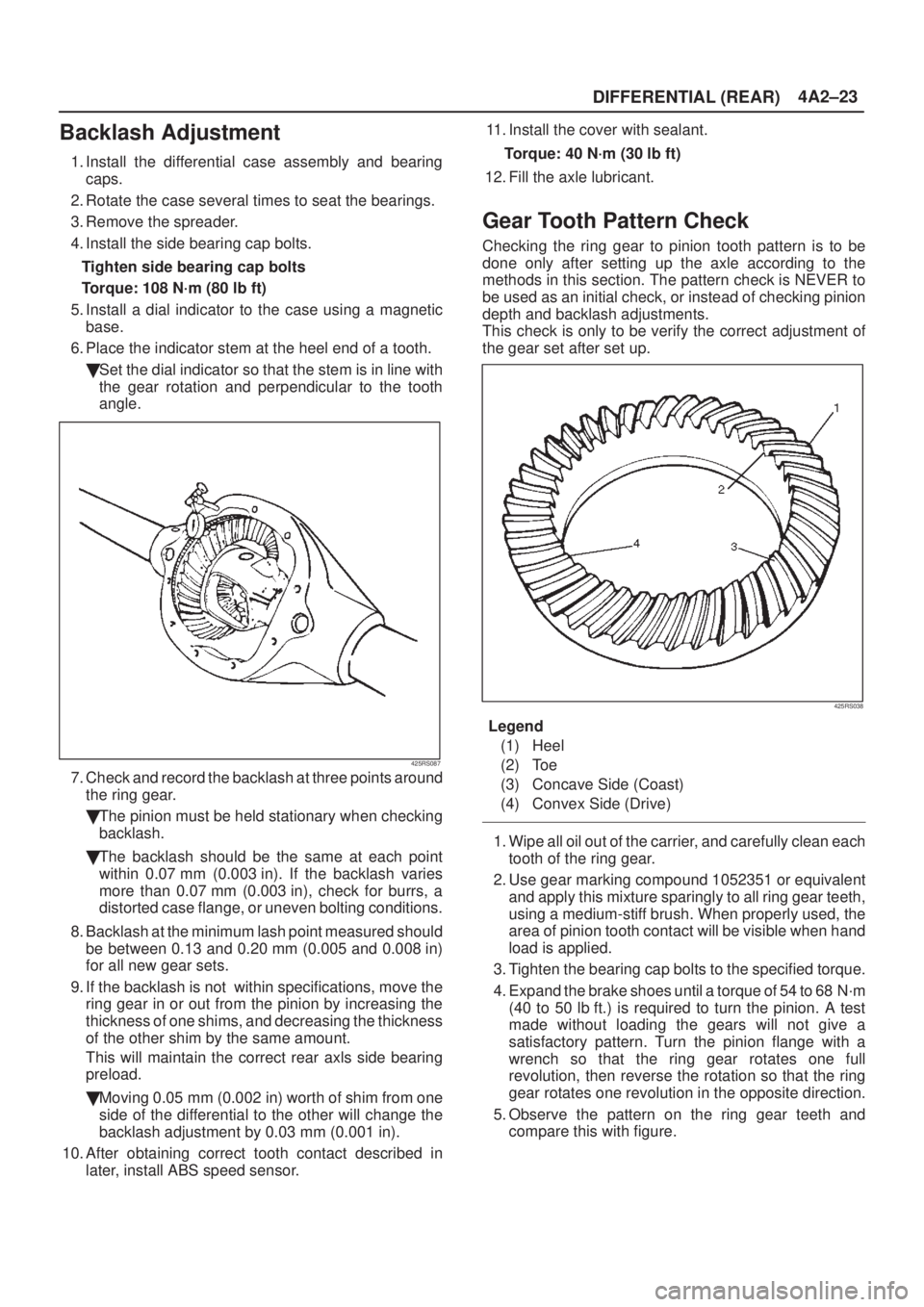
DIFFERENTIAL (REAR)4A2±23
Backlash Adjustment
1. Install the differential case assembly and bearing
caps.
2. Rotate the case several times to seat the bearings.
3. Remove the spreader.
4. Install the side bearing cap bolts.
Tighten side bearing cap bolts
Torque: 108 N´m (80 lb ft)
5. Install a dial indicator to the case using a magnetic
base.
6. Place the indicator stem at the heel end of a tooth.
Set the dial indicator so that the stem is in line with
the gear rotation and perpendicular to the tooth
angle.
425RS087
7. Check and record the backlash at three points around
the ring gear.
The pinion must be held stationary when checking
backlash.
The backlash should be the same at each point
within 0.07 mm (0.003 in). If the backlash varies
more than 0.07 mm (0.003 in), check for burrs, a
distorted case flange, or uneven bolting conditions.
8. Backlash at the minimum lash point measured should
be between 0.13 and 0.20 mm (0.005 and 0.008 in)
for all new gear sets.
9. If the backlash is not within specifications, move the
ring gear in or out from the pinion by increasing the
thickness of one shims, and decreasing the thickness
of the other shim by the same amount.
This will maintain the correct rear axls side bearing
preload.
Moving 0.05 mm (0.002 in) worth of shim from one
side of the differential to the other will change the
backlash adjustment by 0.03 mm (0.001 in).
10. After obtaining correct tooth contact described in
later, install ABS speed sensor.11. Install the cover with sealant.
Torque: 40 N´m (30 lb ft)
12. Fill the axle lubricant.
Gear Tooth Pattern Check
Checking the ring gear to pinion tooth pattern is to be
done only after setting up the axle according to the
methods in this section. The pattern check is NEVER to
be used as an initial check, or instead of checking pinion
depth and backlash adjustments.
This check is only to be verify the correct adjustment of
the gear set after set up.
425RS038
Legend
(1) Heel
(2) Toe
(3) Concave Side (Coast)
(4) Convex Side (Drive)
1. Wipe all oil out of the carrier, and carefully clean each
tooth of the ring gear.
2. Use gear marking compound 1052351 or equivalent
and apply this mixture sparingly to all ring gear teeth,
using a medium-stiff brush. When properly used, the
area of pinion tooth contact will be visible when hand
load is applied.
3. Tighten the bearing cap bolts to the specified torque.
4. Expand the brake shoes until a torque of 54 to 68 N´m
(40 to 50 lb ft.) is required to turn the pinion. A test
made without loading the gears will not give a
satisfactory pattern. Turn the pinion flange with a
wrench so that the ring gear rotates one full
revolution, then reverse the rotation so that the ring
gear rotates one revolution in the opposite direction.
5. Observe the pattern on the ring gear teeth and
compare this with figure.
Page 882 of 2100
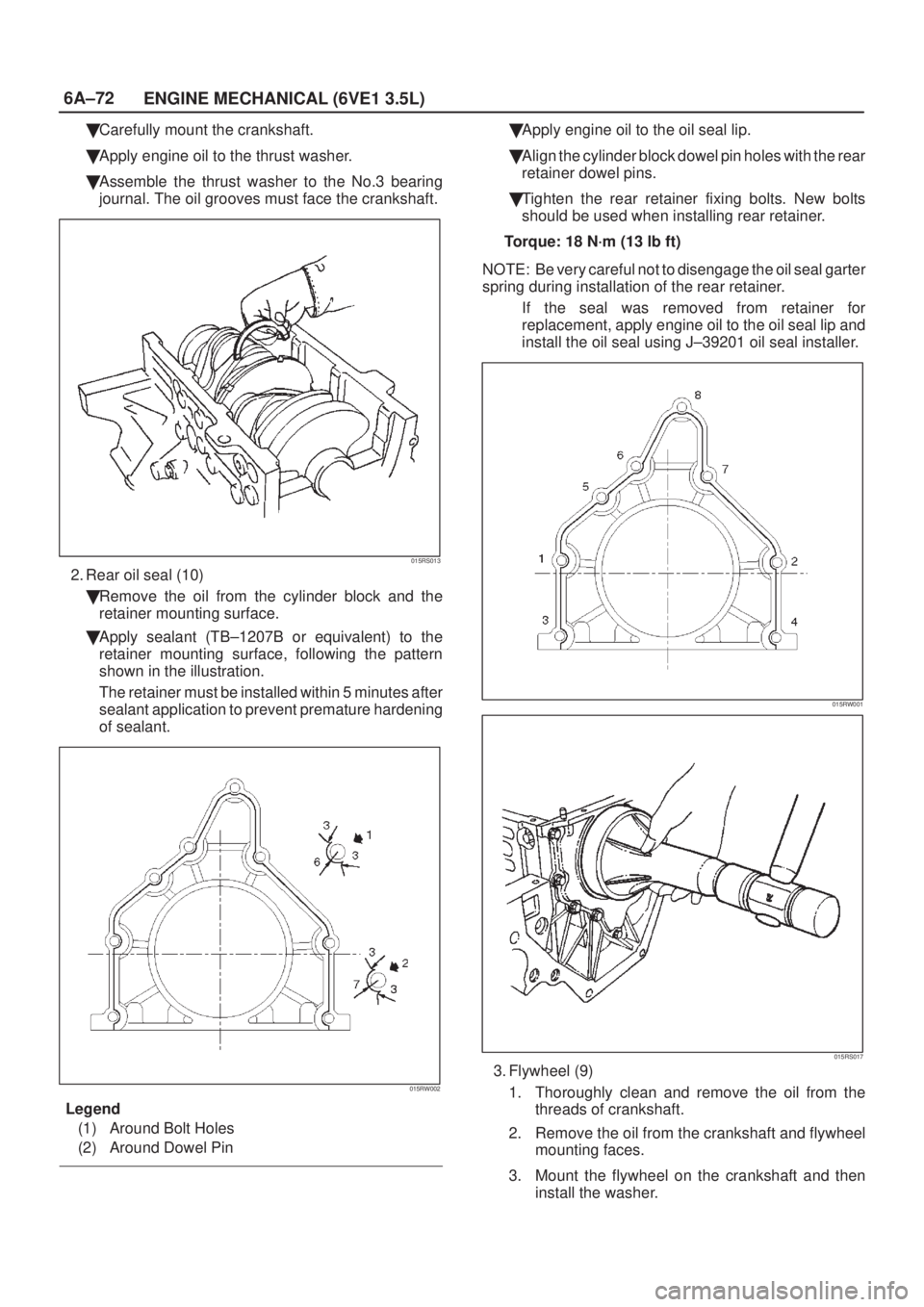
6A±72
ENGINE MECHANICAL (6VE1 3.5L)
Carefully mount the crankshaft.
Apply engine oil to the thrust washer.
Assemble the thrust washer to the No.3 bearing
journal. The oil grooves must face the crankshaft.
015RS013
2. Rear oil seal (10)
Remove the oil from the cylinder block and the
retainer mounting surface.
Apply sealant (TB±1207B or equivalent) to the
retainer mounting surface, following the pattern
shown in the illustration.
The retainer must be installed within 5 minutes after
sealant application to prevent premature hardening
of sealant.
015RW002
Legend
(1) Around Bolt Holes
(2) Around Dowel Pin
Apply engine oil to the oil seal lip.
Align the cylinder block dowel pin holes with the rear
retainer dowel pins.
Tighten the rear retainer fixing bolts. New bolts
should be used when installing rear retainer.
Torque: 18 N´m (13 lb ft)
NOTE: Be very careful not to disengage the oil seal garter
spring during installation of the rear retainer.
If the seal was removed from retainer for
replacement, apply engine oil to the oil seal lip and
install the oil seal using J±39201 oil seal installer.
015RW001
015RS017
3. Flywheel (9)
1. Thoroughly clean and remove the oil from the
threads of crankshaft.
2. Remove the oil from the crankshaft and flywheel
mounting faces.
3. Mount the flywheel on the crankshaft and then
install the washer.
Page 1652 of 2100
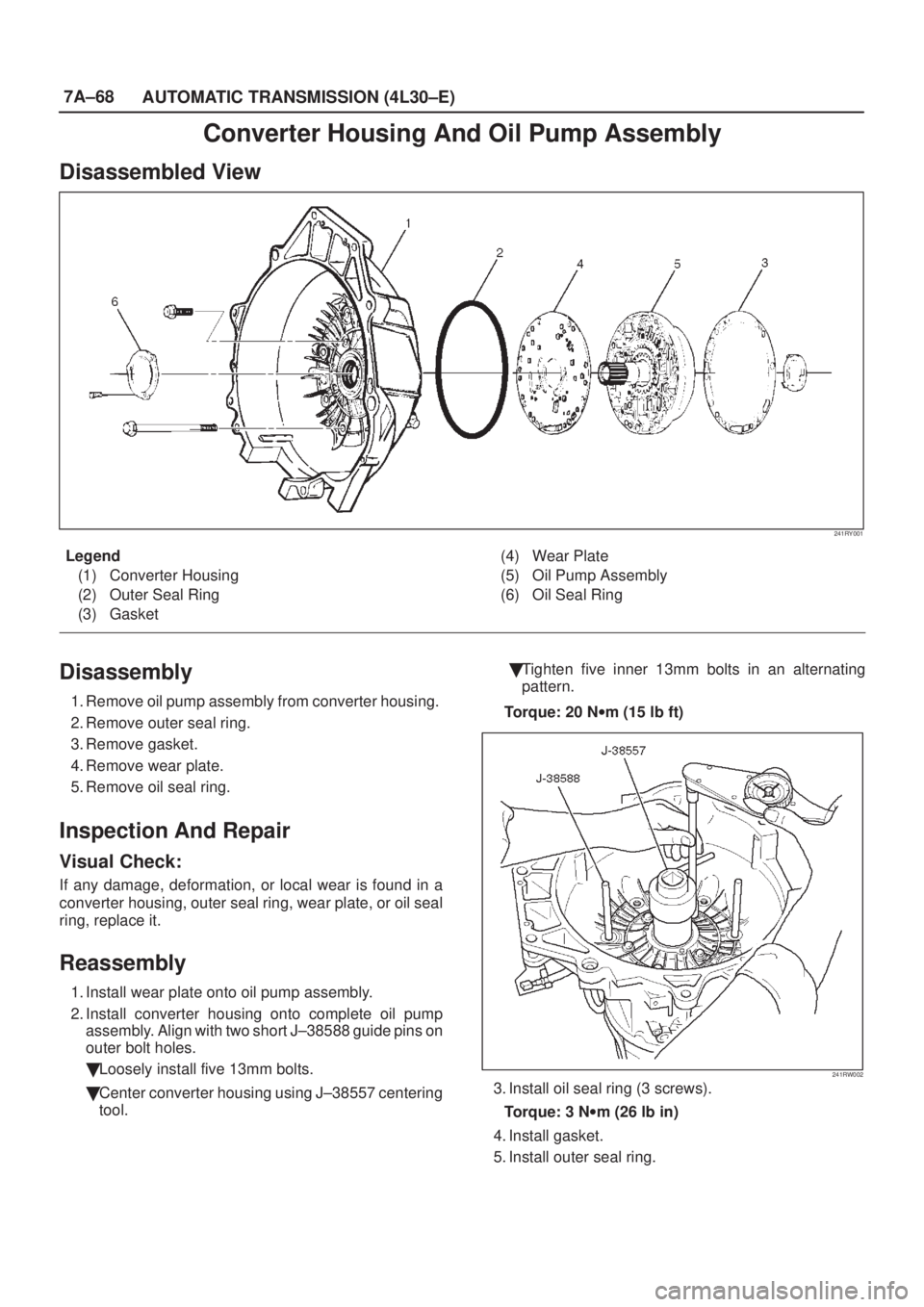
7A±68
AUTOMATIC TRANSMISSION (4L30±E)
Converter Housing And Oil Pump Assembly
Disassembled View
241RY001
Legend
(1) Converter Housing
(2) Outer Seal Ring
(3) Gasket(4) Wear Plate
(5) Oil Pump Assembly
(6) Oil Seal Ring
Disassembly
1. Remove oil pump assembly from converter housing.
2. Remove outer seal ring.
3. Remove gasket.
4. Remove wear plate.
5. Remove oil seal ring.
Inspection And Repair
Visual Check:
If any damage, deformation, or local wear is found in a
converter housing, outer seal ring, wear plate, or oil seal
ring, replace it.
Reassembly
1. Install wear plate onto oil pump assembly.
2. Install converter housing onto complete oil pump
assembly. Align with two short J±38588 guide pins on
outer bolt holes.
Loosely install five 13mm bolts.
Center converter housing using J±38557 centering
tool.Tighten five inner 13mm bolts in an alternating
pattern.
Torque: 20 Nwm (15 lb ft)
241RW002
3. Install oil seal ring (3 screws).
Torque: 3 Nwm (26 lb in)
4. Install gasket.
5. Install outer seal ring.