Page 1022 of 2395
Diagnostic ProcedureNBEC0712
1 RETIGHTEN GROUND SCREWS
1. Turn ignition switch ªOFFº.
2. Loosen and retighten engine ground screws.
SEF959Y
©GO TO 2.
2 CHECK INTAKE VALVE TIMING CONTROL POSITION SENSOR POWER SUPPLY CIRCUIT
1. Disconnect intake valve timing control position sensor harness connector.
SEF360Z
2. Turn ignition switch ªONº.
3. Check voltage between intake valve timing control position sensor harness connector terminal 3 and ground with CON-
SULT-II or tester.
SEF370X
4. Also check harness for short to ground and short to power.
OK or NG
OK©GO TO 4.
NG©GO TO 3.
GI
MA
EM
LC
FE
AT
TF
PD
AX
SU
BR
ST
RS
BT
HA
SC
EL
IDX
DTC P1140 (RIGHT, -B1), P1145 (LEFT, -B2) INTAKE VALVE TIMING CONTROL
POSITION SENSOR (CIRCUIT)
Diagnostic Procedure
EC-487
Page 1023 of 2395
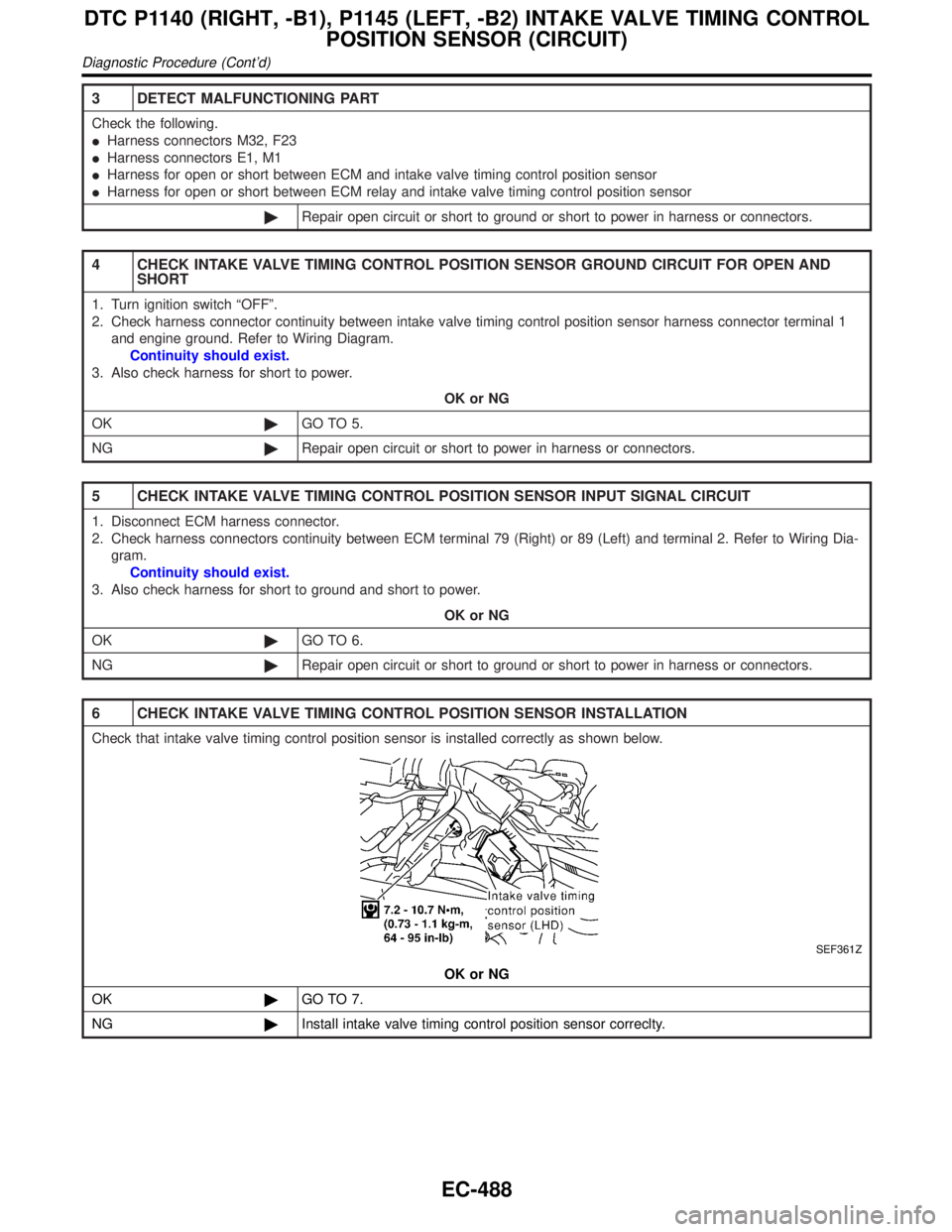
3 DETECT MALFUNCTIONING PART
Check the following.
IHarness connectors M32, F23
IHarness connectors E1, M1
IHarness for open or short between ECM and intake valve timing control position sensor
IHarness for open or short between ECM relay and intake valve timing control position sensor
©Repair open circuit or short to ground or short to power in harness or connectors.
4 CHECK INTAKE VALVE TIMING CONTROL POSITION SENSOR GROUND CIRCUIT FOR OPEN AND
SHORT
1. Turn ignition switch ªOFFº.
2. Check harness connector continuity between intake valve timing control position sensor harness connector terminal 1
and engine ground. Refer to Wiring Diagram.
Continuity should exist.
3. Also check harness for short to power.
OK or NG
OK©GO TO 5.
NG©Repair open circuit or short to power in harness or connectors.
5 CHECK INTAKE VALVE TIMING CONTROL POSITION SENSOR INPUT SIGNAL CIRCUIT
1. Disconnect ECM harness connector.
2. Check harness connectors continuity between ECM terminal 79 (Right) or 89 (Left) and terminal 2. Refer to Wiring Dia-
gram.
Continuity should exist.
3. Also check harness for short to ground and short to power.
OK or NG
OK©GO TO 6.
NG©Repair open circuit or short to ground or short to power in harness or connectors.
6 CHECK INTAKE VALVE TIMING CONTROL POSITION SENSOR INSTALLATION
Check that intake valve timing control position sensor is installed correctly as shown below.
SEF361Z
OK or NG
OK©GO TO 7.
NG©Install intake valve timing control position sensor correclty.
DTC P1140 (RIGHT, -B1), P1145 (LEFT, -B2) INTAKE VALVE TIMING CONTROL
POSITION SENSOR (CIRCUIT)
Diagnostic Procedure (Cont'd)
EC-488
Page 1024 of 2395
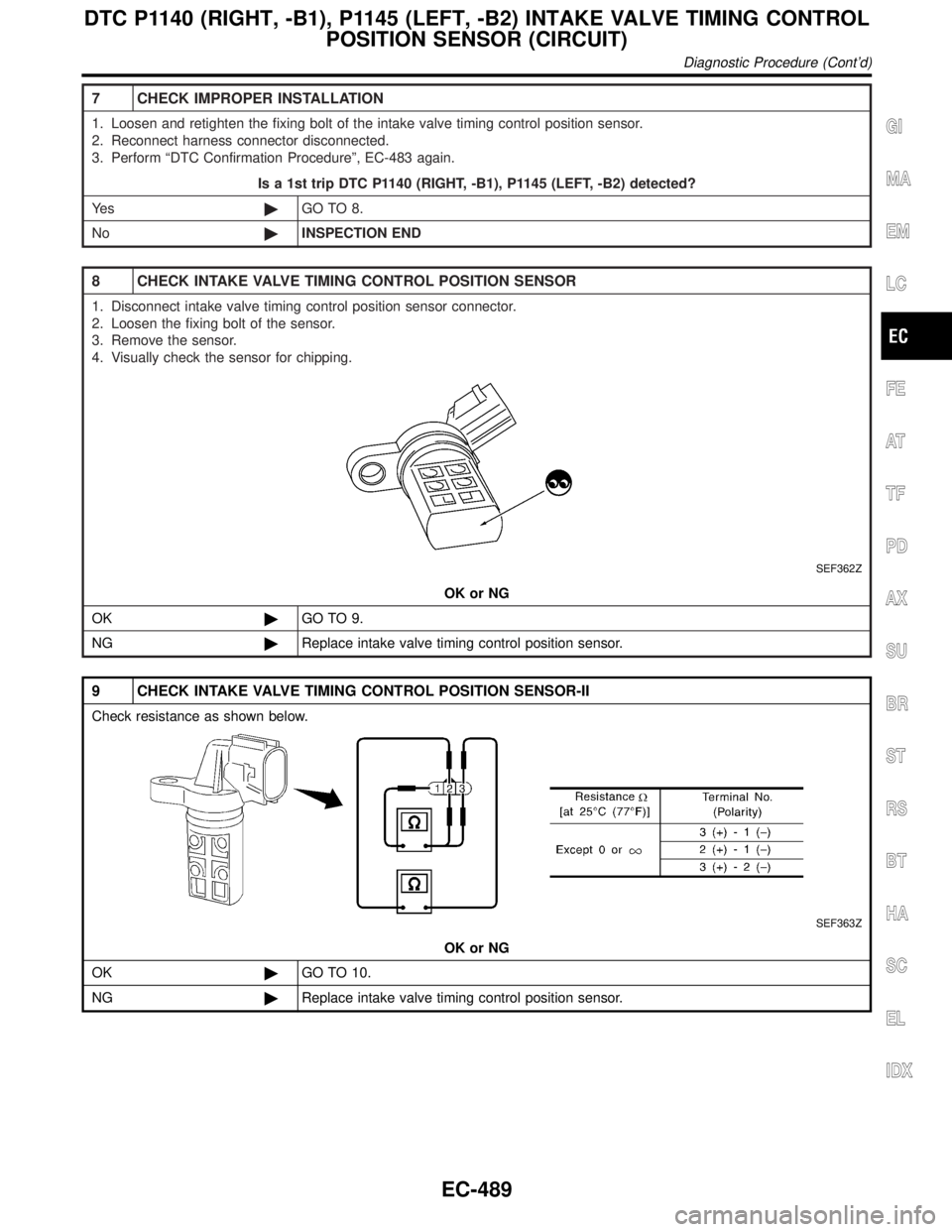
7 CHECK IMPROPER INSTALLATION
1. Loosen and retighten the fixing bolt of the intake valve timing control position sensor.
2. Reconnect harness connector disconnected.
3. Perform ªDTC Confirmation Procedureº, EC-483 again.
Is a 1st trip DTC P1140 (RIGHT, -B1), P1145 (LEFT, -B2) detected?
Ye s©GO TO 8.
No©INSPECTION END
8 CHECK INTAKE VALVE TIMING CONTROL POSITION SENSOR
1. Disconnect intake valve timing control position sensor connector.
2. Loosen the fixing bolt of the sensor.
3. Remove the sensor.
4. Visually check the sensor for chipping.
SEF362Z
OK or NG
OK©GO TO 9.
NG©Replace intake valve timing control position sensor.
9 CHECK INTAKE VALVE TIMING CONTROL POSITION SENSOR-II
Check resistance as shown below.
SEF363Z
OK or NG
OK©GO TO 10.
NG©Replace intake valve timing control position sensor.
GI
MA
EM
LC
FE
AT
TF
PD
AX
SU
BR
ST
RS
BT
HA
SC
EL
IDX
DTC P1140 (RIGHT, -B1), P1145 (LEFT, -B2) INTAKE VALVE TIMING CONTROL
POSITION SENSOR (CIRCUIT)
Diagnostic Procedure (Cont'd)
EC-489
Page 1025 of 2395
10 CHECK CAMSHAFT
Check accumulation of debris to the signal pick-up portion of the camshaft.
Refer to step 35 of ªTiming chain removalº, EM-23.
OK or NG
OK©GO TO 11.
NG©Remove debris and clean the signal pick-up cut out of camshaft.
11 CHECK INTERMITTENT INCIDENT
Refer to ªTROUBLE DIAGNOSIS FOR INTERMITTENT INCIDENTº, EC-140.
©INSPECTION END
DTC P1140 (RIGHT, -B1), P1145 (LEFT, -B2) INTAKE VALVE TIMING CONTROL
POSITION SENSOR (CIRCUIT)
Diagnostic Procedure (Cont'd)
EC-490
Page 1026 of 2395
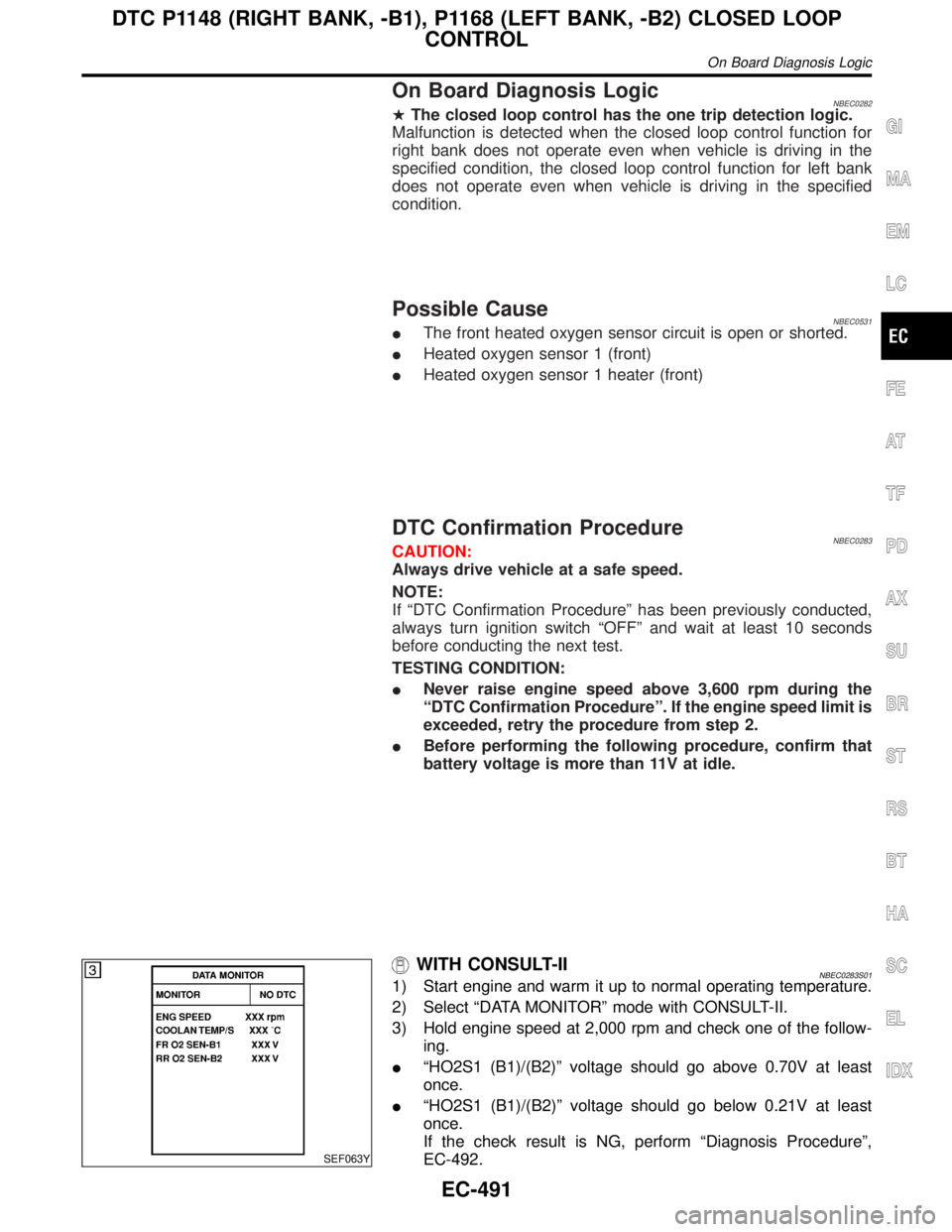
On Board Diagnosis LogicNBEC0282HThe closed loop control has the one trip detection logic.
Malfunction is detected when the closed loop control function for
right bank does not operate even when vehicle is driving in the
specified condition, the closed loop control function for left bank
does not operate even when vehicle is driving in the specified
condition.
Possible CauseNBEC0531IThe front heated oxygen sensor circuit is open or shorted.
IHeated oxygen sensor 1 (front)
IHeated oxygen sensor 1 heater (front)
DTC Confirmation ProcedureNBEC0283CAUTION:
Always drive vehicle at a safe speed.
NOTE:
If ªDTC Confirmation Procedureº has been previously conducted,
always turn ignition switch ªOFFº and wait at least 10 seconds
before conducting the next test.
TESTING CONDITION:
INever raise engine speed above 3,600 rpm during the
ªDTC Confirmation Procedureº. If the engine speed limit is
exceeded, retry the procedure from step 2.
IBefore performing the following procedure, confirm that
battery voltage is more than 11V at idle.
SEF063Y
WITH CONSULT-IINBEC0283S011) Start engine and warm it up to normal operating temperature.
2) Select ªDATA MONITORº mode with CONSULT-II.
3) Hold engine speed at 2,000 rpm and check one of the follow-
ing.
IªHO2S1 (B1)/(B2)º voltage should go above 0.70V at least
once.
IªHO2S1 (B1)/(B2)º voltage should go below 0.21V at least
once.
If the check result is NG, perform ªDiagnosis Procedureº,
EC-492.
GI
MA
EM
LC
FE
AT
TF
PD
AX
SU
BR
ST
RS
BT
HA
SC
EL
IDX
DTC P1148 (RIGHT BANK, -B1), P1168 (LEFT BANK, -B2) CLOSED LOOP
CONTROL
On Board Diagnosis Logic
EC-491
Page 1027 of 2395
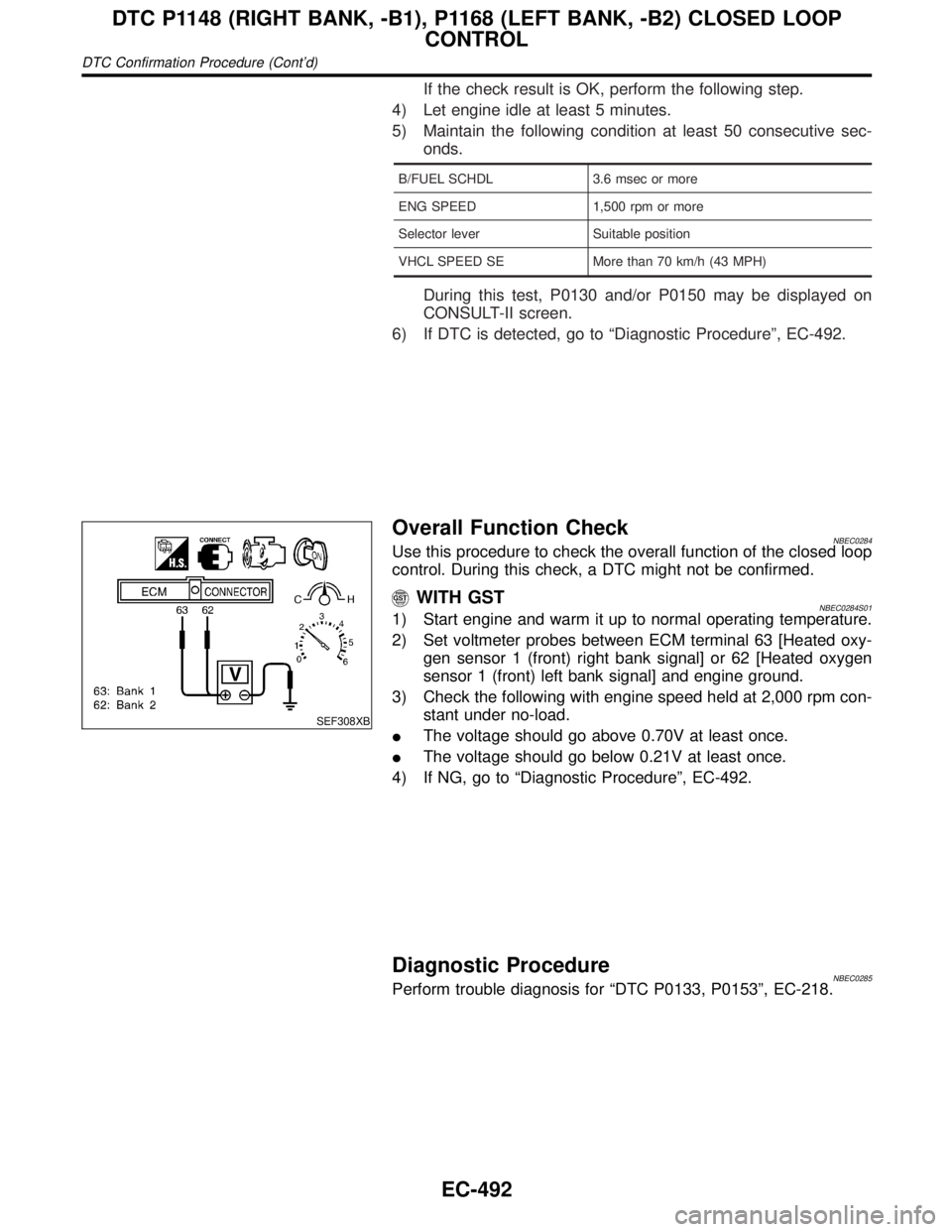
If the check result is OK, perform the following step.
4) Let engine idle at least 5 minutes.
5) Maintain the following condition at least 50 consecutive sec-
onds.
B/FUEL SCHDL 3.6 msec or more
ENG SPEED 1,500 rpm or more
Selector lever Suitable position
VHCL SPEED SE More than 70 km/h (43 MPH)
During this test, P0130 and/or P0150 may be displayed on
CONSULT-II screen.
6) If DTC is detected, go to ªDiagnostic Procedureº, EC-492.
SEF308XB
Overall Function CheckNBEC0284Use this procedure to check the overall function of the closed loop
control. During this check, a DTC might not be confirmed.
WITH GSTNBEC0284S011) Start engine and warm it up to normal operating temperature.
2) Set voltmeter probes between ECM terminal 63 [Heated oxy-
gen sensor 1 (front) right bank signal] or 62 [Heated oxygen
sensor 1 (front) left bank signal] and engine ground.
3) Check the following with engine speed held at 2,000 rpm con-
stant under no-load.
IThe voltage should go above 0.70V at least once.
IThe voltage should go below 0.21V at least once.
4) If NG, go to ªDiagnostic Procedureº, EC-492.
Diagnostic ProcedureNBEC0285Perform trouble diagnosis for ªDTC P0133, P0153º, EC-218.
DTC P1148 (RIGHT BANK, -B1), P1168 (LEFT BANK, -B2) CLOSED LOOP
CONTROL
DTC Confirmation Procedure (Cont'd)
EC-492
Page 1035 of 2395
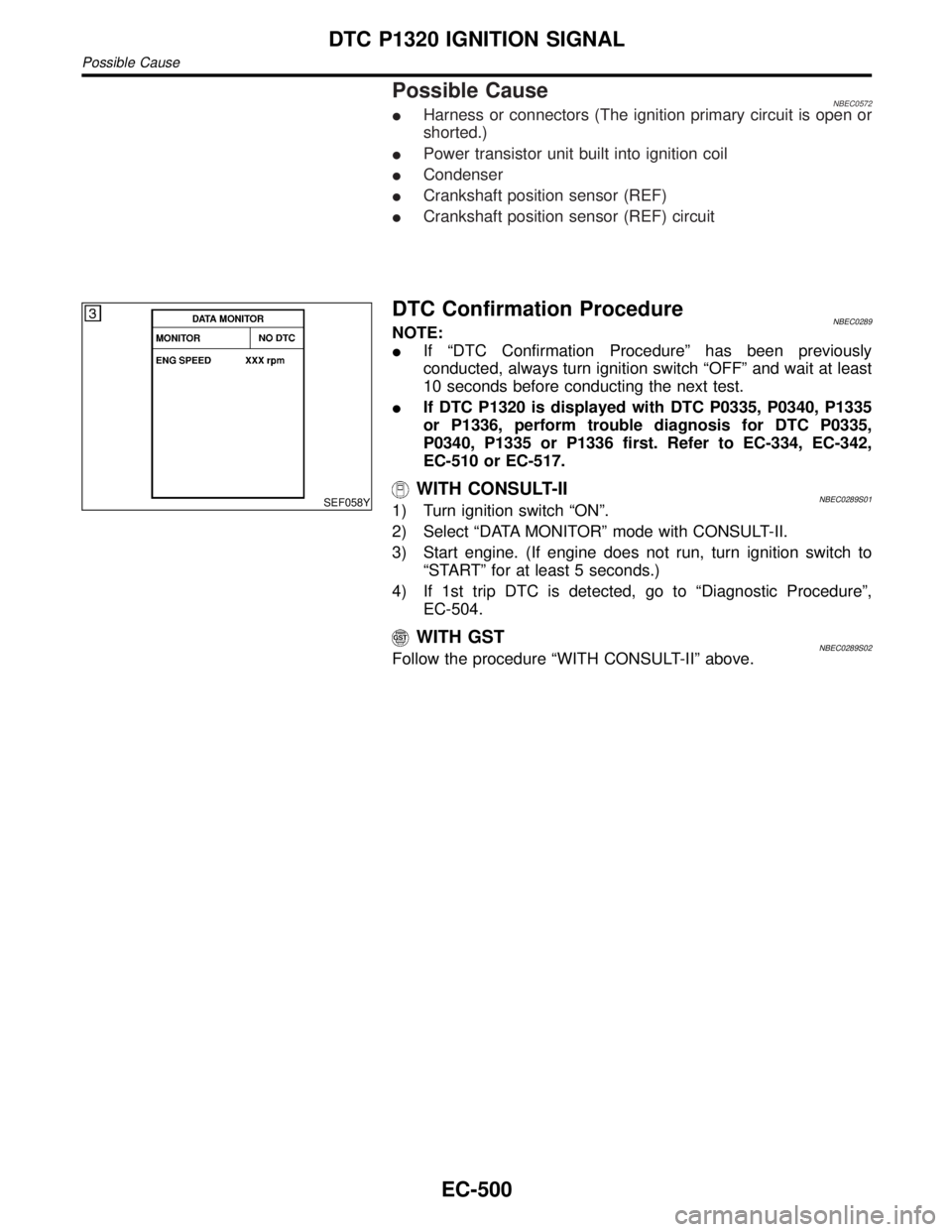
Possible CauseNBEC0572IHarness or connectors (The ignition primary circuit is open or
shorted.)
IPower transistor unit built into ignition coil
ICondenser
ICrankshaft position sensor (REF)
ICrankshaft position sensor (REF) circuit
SEF058Y
DTC Confirmation ProcedureNBEC0289NOTE:
IIf ªDTC Confirmation Procedureº has been previously
conducted, always turn ignition switch ªOFFº and wait at least
10 seconds before conducting the next test.
IIf DTC P1320 is displayed with DTC P0335, P0340, P1335
or P1336, perform trouble diagnosis for DTC P0335,
P0340, P1335 or P1336 first. Refer to EC-334, EC-342,
EC-510 or EC-517.
WITH CONSULT-IINBEC0289S011) Turn ignition switch ªONº.
2) Select ªDATA MONITORº mode with CONSULT-II.
3) Start engine. (If engine does not run, turn ignition switch to
ªSTARTº for at least 5 seconds.)
4) If 1st trip DTC is detected, go to ªDiagnostic Procedureº,
EC-504.
WITH GSTNBEC0289S02Follow the procedure ªWITH CONSULT-IIº above.
DTC P1320 IGNITION SIGNAL
Possible Cause
EC-500
Page 1045 of 2395
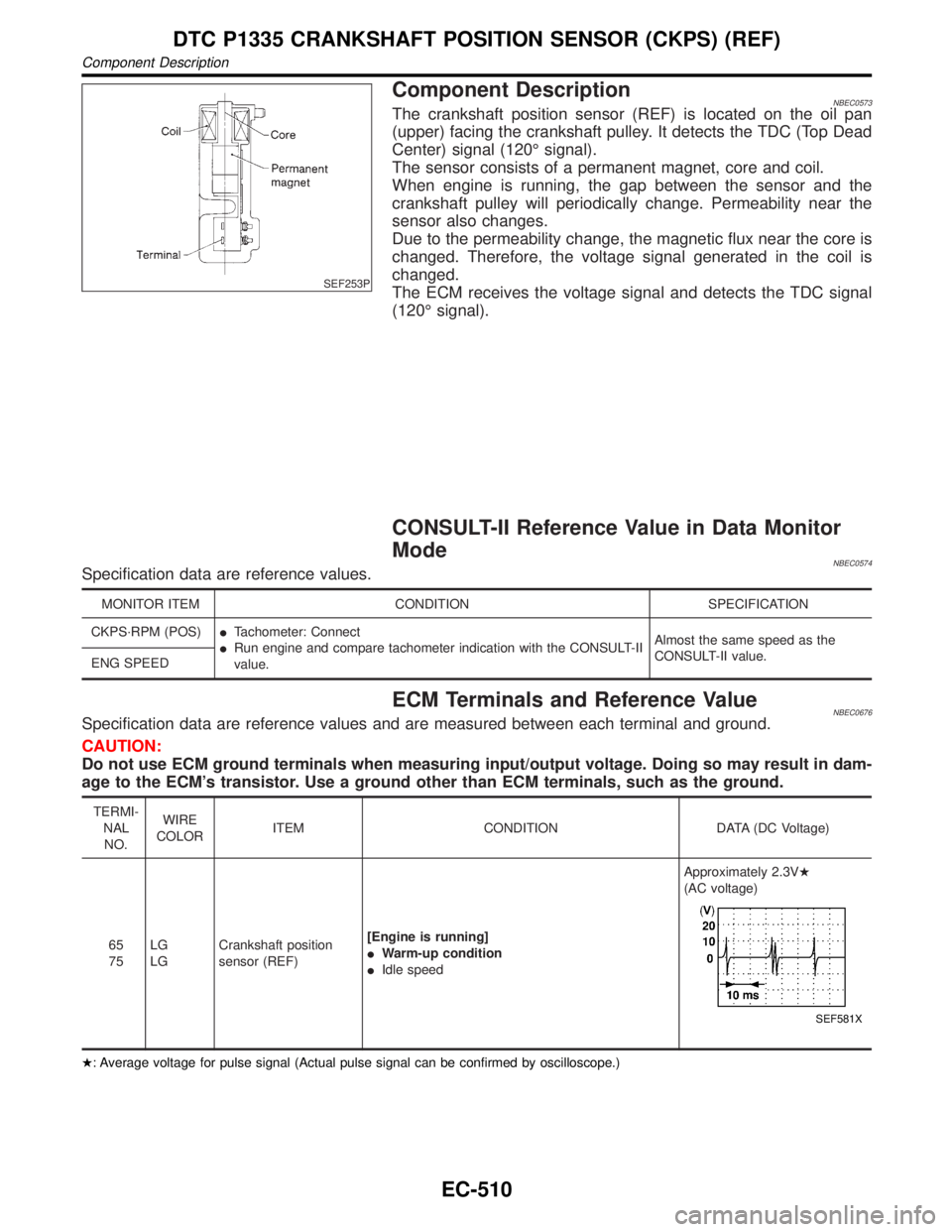
SEF253P
Component DescriptionNBEC0573The crankshaft position sensor (REF) is located on the oil pan
(upper) facing the crankshaft pulley. It detects the TDC (Top Dead
Center) signal (120É signal).
The sensor consists of a permanent magnet, core and coil.
When engine is running, the gap between the sensor and the
crankshaft pulley will periodically change. Permeability near the
sensor also changes.
Due to the permeability change, the magnetic flux near the core is
changed. Therefore, the voltage signal generated in the coil is
changed.
The ECM receives the voltage signal and detects the TDC signal
(120É signal).
CONSULT-II Reference Value in Data Monitor
Mode
NBEC0574Specification data are reference values.
MONITOR ITEM CONDITION SPECIFICATION
CKPS´RPM (POS)ITachometer: Connect
IRun engine and compare tachometer indication with the CONSULT-II
value.Almost the same speed as the
CONSULT-II value.
ENG SPEED
ECM Terminals and Reference ValueNBEC0676Specification data are reference values and are measured between each terminal and ground.
CAUTION:
Do not use ECM ground terminals when measuring input/output voltage. Doing so may result in dam-
age to the ECM's transistor. Use a ground other than ECM terminals, such as the ground.
TERMI-
NAL
NO.WIRE
COLORITEM CONDITION DATA (DC Voltage)
65
75LG
LGCrankshaft position
sensor (REF)[Engine is running]
IWarm-up condition
IIdle speedApproximately 2.3VH
(AC voltage)
SEF581X
H: Average voltage for pulse signal (Actual pulse signal can be confirmed by oscilloscope.)
DTC P1335 CRANKSHAFT POSITION SENSOR (CKPS) (REF)
Component Description
EC-510