Page 1054 of 2395
DTC Confirmation ProcedureNBEC0295NOTE:
If ªDTC Confirmation Procedureº has been previously conducted,
always turn ignition switch ªOFFº and wait at least 10 seconds
before conducting the next test.
TESTING CONDITION:
Before performing the following procedure, confirm that bat-
tery voltage is more than 10.5V.
SEF058Y
WITH CONSULT-IINBEC0295S011) Turn ignition switch ªONº and select ªDATA MONITORº mode
with CONSULT-II.
2) Start engine and run it for at least 70 seconds at idle speed.
3) If 1st trip DTC is detected, go to ªDiagnostic Procedureº,
EC-521.
WITH GSTNBEC0295S02Follow the procedure ªWITH CONSULT-IIº above.
GI
MA
EM
LC
FE
AT
TF
PD
AX
SU
BR
ST
RS
BT
HA
SC
EL
IDX
DTC P1336 CRANKSHAFT POSITION SENSOR (CKPS) (POS) (COG)
DTC Confirmation Procedure
EC-519
Page 1055 of 2395
Wiring DiagramNBEC0296
MEC959C
DTC P1336 CRANKSHAFT POSITION SENSOR (CKPS) (POS) (COG)
Wiring Diagram
EC-520
Page 1056 of 2395
Diagnostic ProcedureNBEC0297
1 RETIGHTEN GROUND SCERWS
1. Turn ignition switch ªOFFº.
2. Loosen and retighten engine ground screws.
SEF959Y
©GO TO 2.
2 CHECK CKPS (POS) POWER SUPPLY CIRCUIT
1. Disconnect harness connectors E132, E135.
SEF978Y
2. Check voltage between harness connector E135 terminal 6 and ground with CONSULT-II or tester.
SEF979Y
3. Also check harness for short to ground and short to power.
OK or NG
OK©GO TO 4.
NG©GO TO 3.
GI
MA
EM
LC
FE
AT
TF
PD
AX
SU
BR
ST
RS
BT
HA
SC
EL
IDX
DTC P1336 CRANKSHAFT POSITION SENSOR (CKPS) (POS) (COG)
Diagnostic Procedure
EC-521
Page 1057 of 2395
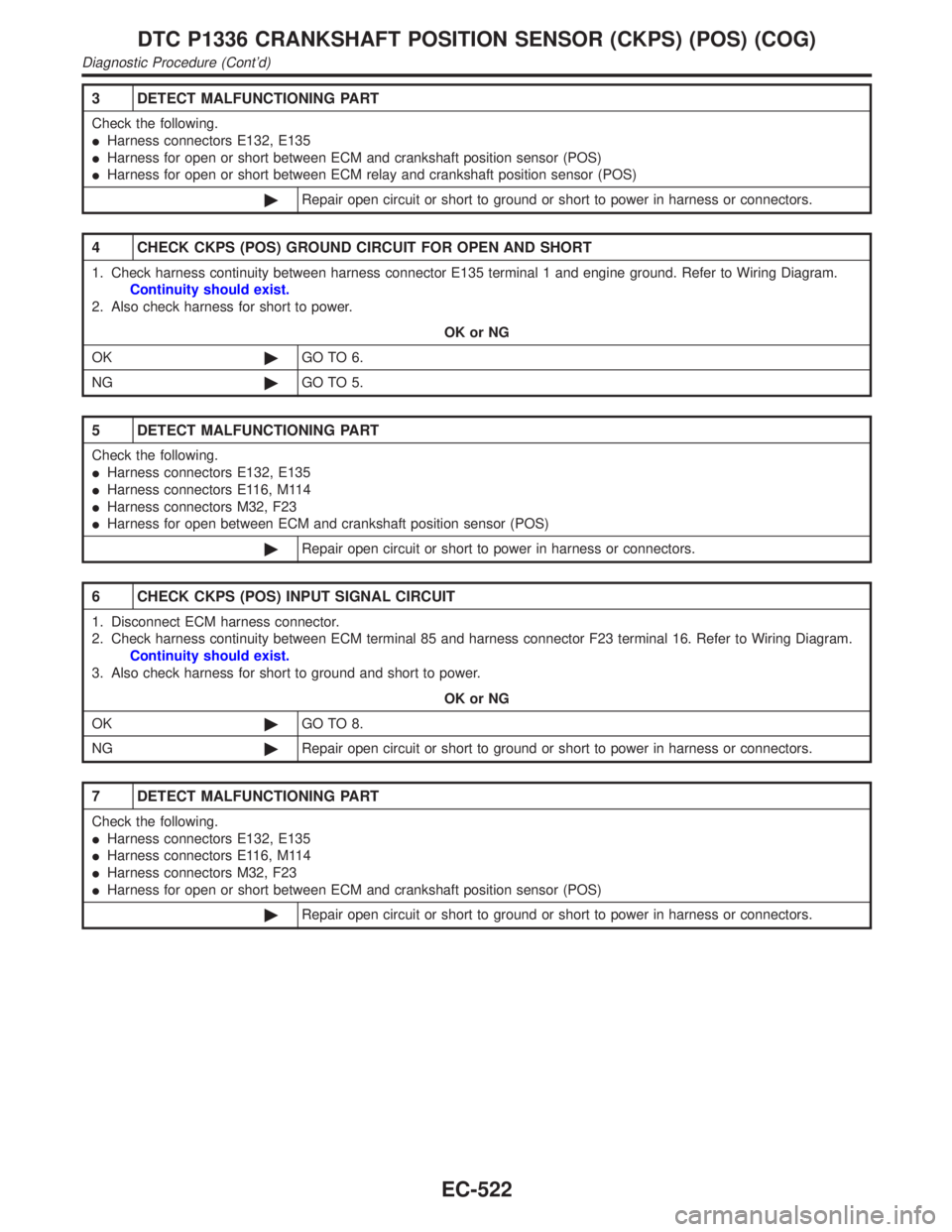
3 DETECT MALFUNCTIONING PART
Check the following.
IHarness connectors E132, E135
IHarness for open or short between ECM and crankshaft position sensor (POS)
IHarness for open or short between ECM relay and crankshaft position sensor (POS)
©Repair open circuit or short to ground or short to power in harness or connectors.
4 CHECK CKPS (POS) GROUND CIRCUIT FOR OPEN AND SHORT
1. Check harness continuity between harness connector E135 terminal 1 and engine ground. Refer to Wiring Diagram.
Continuity should exist.
2. Also check harness for short to power.
OK or NG
OK©GO TO 6.
NG©GO TO 5.
5 DETECT MALFUNCTIONING PART
Check the following.
IHarness connectors E132, E135
IHarness connectors E116, M114
IHarness connectors M32, F23
IHarness for open between ECM and crankshaft position sensor (POS)
©Repair open circuit or short to power in harness or connectors.
6 CHECK CKPS (POS) INPUT SIGNAL CIRCUIT
1. Disconnect ECM harness connector.
2. Check harness continuity between ECM terminal 85 and harness connector F23 terminal 16. Refer to Wiring Diagram.
Continuity should exist.
3. Also check harness for short to ground and short to power.
OK or NG
OK©GO TO 8.
NG©Repair open circuit or short to ground or short to power in harness or connectors.
7 DETECT MALFUNCTIONING PART
Check the following.
IHarness connectors E132, E135
IHarness connectors E116, M114
IHarness connectors M32, F23
IHarness for open or short between ECM and crankshaft position sensor (POS)
©Repair open circuit or short to ground or short to power in harness or connectors.
DTC P1336 CRANKSHAFT POSITION SENSOR (CKPS) (POS) (COG)
Diagnostic Procedure (Cont'd)
EC-522
Page 1058 of 2395
8 CHECK CKPS (POS) SUB-HARNESS CIRCUIT FOR OPEN AND SHORT
1. Disconnect CKPS (POS) harness connector.
SEF980Y
2. Check harness continuity between CKPS (POS) terminals and harness connector E132 terminals as follows.
MTBL0531
Continuity should exist.
3. Also check harness for short to ground and short to power.
OK or NG
OK©GO TO 9.
NG©Repair open circuit or short to ground or short to power in harness or connectors.
9 CHECK IMPROPER INSTALLATION
1. Loosen and retighten the fixing bolt of the crankshaft position sensor (POS).
2. Reconnect harness connectors disconnected.
3. Perform ªDTC Confirmation Procedureº, EC-519 again.
Is a 1st trip DTC P1336 detected?
Ye s©GO TO 10.
No©INSPECTION END
GI
MA
EM
LC
FE
AT
TF
PD
AX
SU
BR
ST
RS
BT
HA
SC
EL
IDX
DTC P1336 CRANKSHAFT POSITION SENSOR (CKPS) (POS) (COG)
Diagnostic Procedure (Cont'd)
EC-523
Page 1059 of 2395
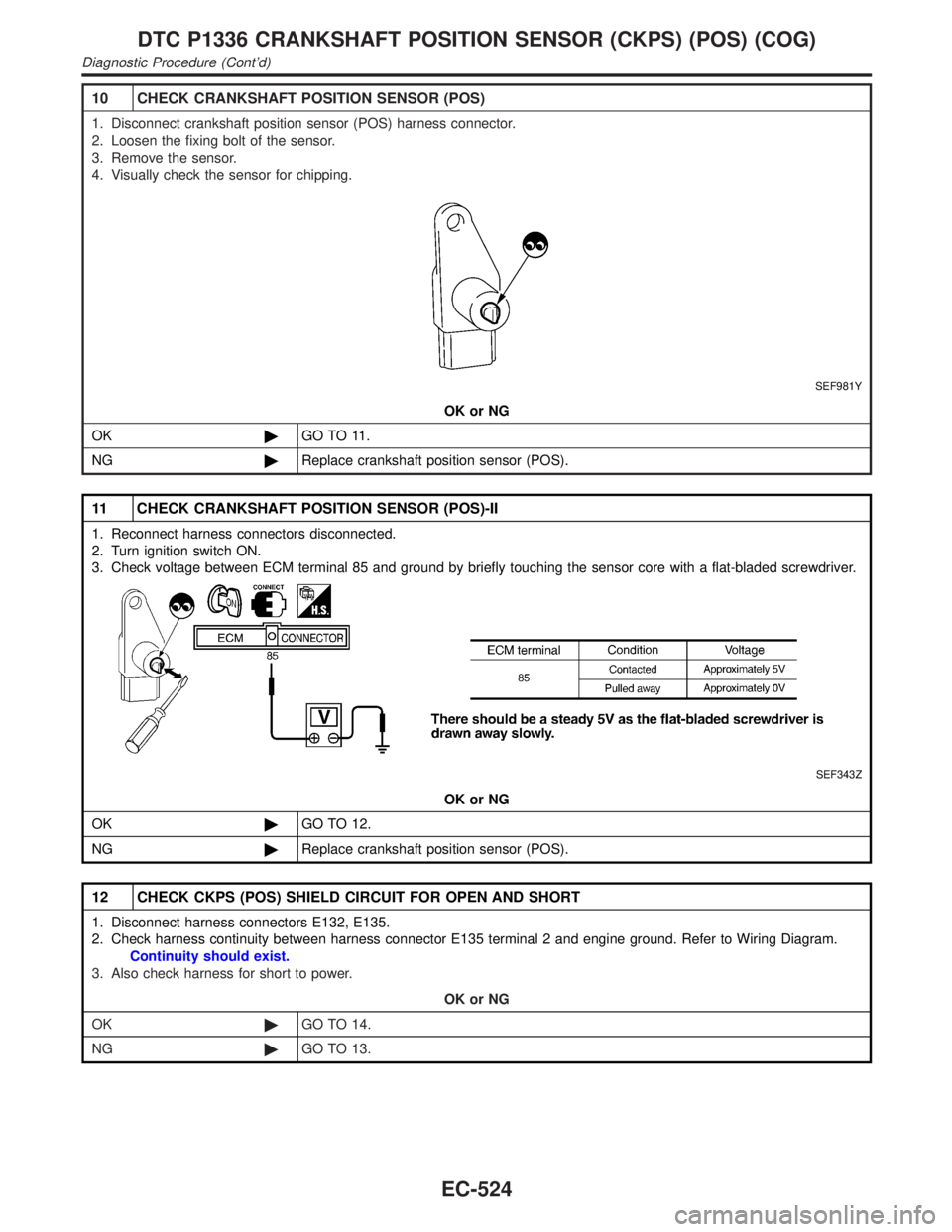
10 CHECK CRANKSHAFT POSITION SENSOR (POS)
1. Disconnect crankshaft position sensor (POS) harness connector.
2. Loosen the fixing bolt of the sensor.
3. Remove the sensor.
4. Visually check the sensor for chipping.
SEF981Y
OK or NG
OK©GO TO 11.
NG©Replace crankshaft position sensor (POS).
11 CHECK CRANKSHAFT POSITION SENSOR (POS)-II
1. Reconnect harness connectors disconnected.
2. Turn ignition switch ON.
3. Check voltage between ECM terminal 85 and ground by briefly touching the sensor core with a flat-bladed screwdriver.
SEF343Z
OK or NG
OK©GO TO 12.
NG©Replace crankshaft position sensor (POS).
12 CHECK CKPS (POS) SHIELD CIRCUIT FOR OPEN AND SHORT
1. Disconnect harness connectors E132, E135.
2. Check harness continuity between harness connector E135 terminal 2 and engine ground. Refer to Wiring Diagram.
Continuity should exist.
3. Also check harness for short to power.
OK or NG
OK©GO TO 14.
NG©GO TO 13.
DTC P1336 CRANKSHAFT POSITION SENSOR (CKPS) (POS) (COG)
Diagnostic Procedure (Cont'd)
EC-524
Page 1060 of 2395
13 DETECT MALFUNCTIONING PART
Check the following.
IHarness connectors E132, E135
IHarness connectors E116, M114
IHarness connectors M32, F23
IHarness for open between harness connector E135 and engine ground
©Repair open circuit or short to power in harness or connectors.
14 CHECK GEAR TOOTH
Visually check for chipping signal plate (flywheel or drive plate) gear tooth (cog).
OK or NG
OK©GO TO 15.
NG©Replace the signal plate (flywheel or drive plate).
15 CHECK INTERMITTENT INCIDENT
Refer to ªTROUBLE DIAGNOSIS FOR INTERMITTENT INCIDENTº, EC-140.
©INSPECTION END
GI
MA
EM
LC
FE
AT
TF
PD
AX
SU
BR
ST
RS
BT
HA
SC
EL
IDX
DTC P1336 CRANKSHAFT POSITION SENSOR (CKPS) (POS) (COG)
Diagnostic Procedure (Cont'd)
EC-525
Page 1062 of 2395
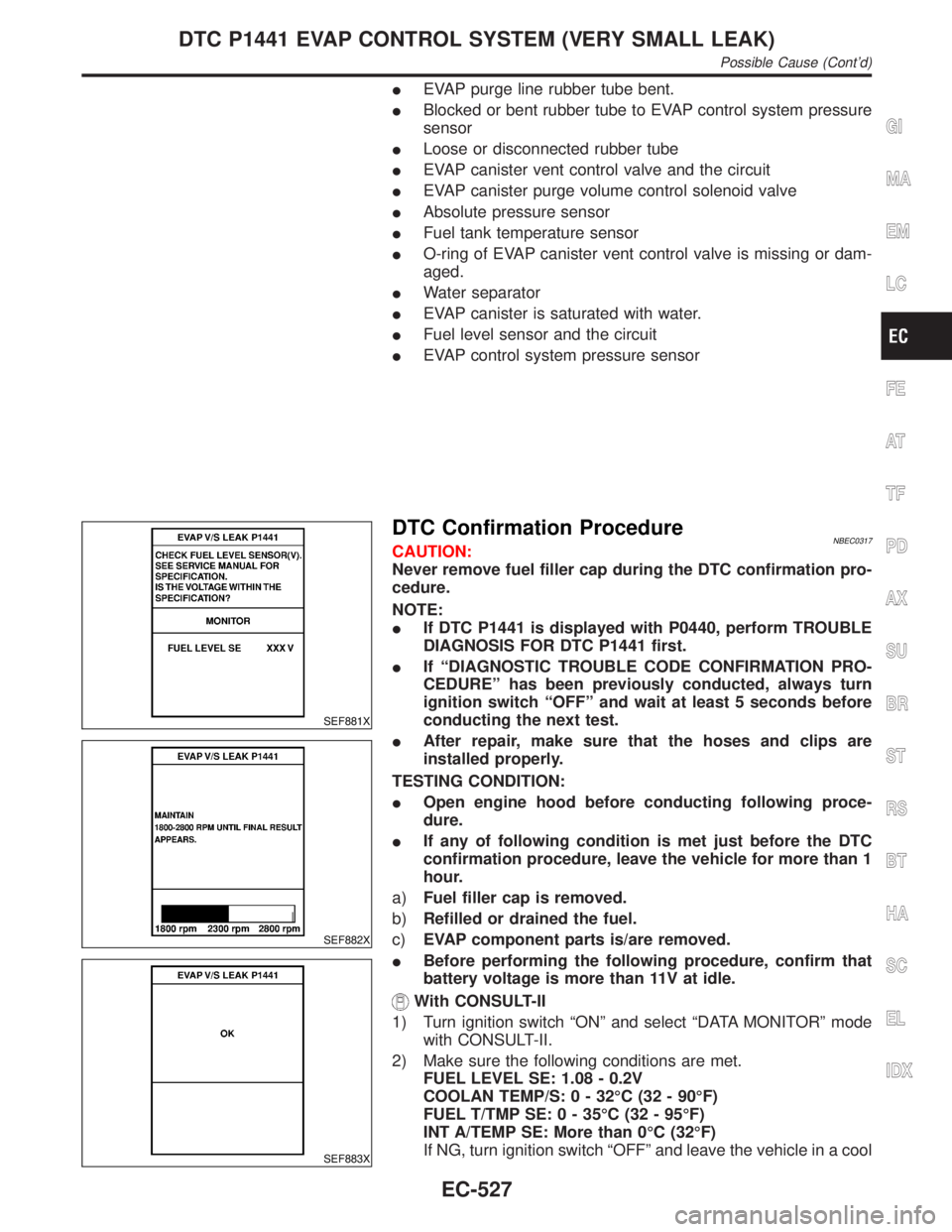
IEVAP purge line rubber tube bent.
IBlocked or bent rubber tube to EVAP control system pressure
sensor
ILoose or disconnected rubber tube
IEVAP canister vent control valve and the circuit
IEVAP canister purge volume control solenoid valve
IAbsolute pressure sensor
IFuel tank temperature sensor
IO-ring of EVAP canister vent control valve is missing or dam-
aged.
IWater separator
IEVAP canister is saturated with water.
IFuel level sensor and the circuit
IEVAP control system pressure sensor
SEF881X
SEF882X
SEF883X
DTC Confirmation ProcedureNBEC0317CAUTION:
Never remove fuel filler cap during the DTC confirmation pro-
cedure.
NOTE:
IIf DTC P1441 is displayed with P0440, perform TROUBLE
DIAGNOSIS FOR DTC P1441 first.
IIf ªDIAGNOSTIC TROUBLE CODE CONFIRMATION PRO-
CEDUREº has been previously conducted, always turn
ignition switch ªOFFº and wait at least 5 seconds before
conducting the next test.
IAfter repair, make sure that the hoses and clips are
installed properly.
TESTING CONDITION:
IOpen engine hood before conducting following proce-
dure.
IIf any of following condition is met just before the DTC
confirmation procedure, leave the vehicle for more than 1
hour.
a)Fuel filler cap is removed.
b)Refilled or drained the fuel.
c)EVAP component parts is/are removed.
IBefore performing the following procedure, confirm that
battery voltage is more than 11V at idle.
With CONSULT-II
1) Turn ignition switch ªONº and select ªDATA MONITORº mode
with CONSULT-II.
2) Make sure the following conditions are met.
FUEL LEVEL SE: 1.08 - 0.2V
COOLAN TEMP/S: 0 - 32ÉC (32 - 90ÉF)
FUEL T/TMP SE: 0 - 35ÉC (32 - 95ÉF)
INT A/TEMP SE: More than 0ÉC (32ÉF)
If NG, turn ignition switch ªOFFº and leave the vehicle in a cool
GI
MA
EM
LC
FE
AT
TF
PD
AX
SU
BR
ST
RS
BT
HA
SC
EL
IDX
DTC P1441 EVAP CONTROL SYSTEM (VERY SMALL LEAK)
Possible Cause (Cont'd)
EC-527