Page 22 of 447
7A-22 MANUAL TRANSMISSION
INPUT SHAFT ASSEMBLY
DISASSEMBLY
1) Remove input shaft right bearing (2) from input shaft (1) by
using bearing puller (3) and press.
2) Drive out 5th gear spacer (2), left bearing (3) and 4th gear
(4) all at once from input shaft (1) by using puller (5) and
press.
3) Take out 4th gear needle bearing and high speed synchro-
nizer ring.
4) Using circlip pliers, remove circlip (1).
5) Drive out high speed synchronizer sleeve & hub assembly
(2) together with 3rd gear (3) from input shaft (1) by using
puller (4) and press.
6) Take out 3rd gear needle bearing from shaft.
7) Disassemble synchronizer sleeve & hub assembly.
CAUTION:
To avoid gear tooth from being damaged, support it at flat
side of bearing puller.
CAUTION:
Make sure to use flat side of puller to avoid causing dam-
age to 3rd gear tooth.
Page 23 of 447
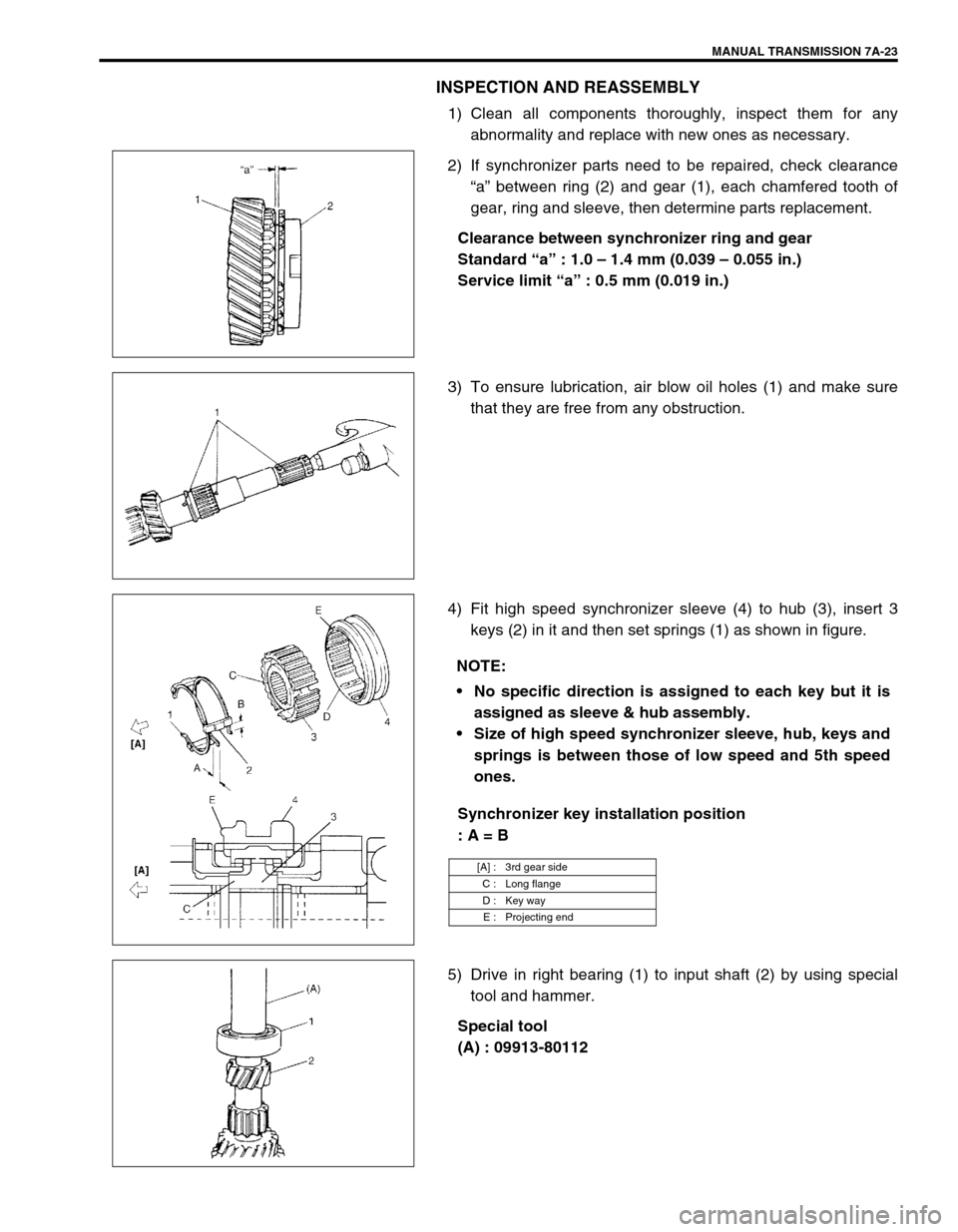
MANUAL TRANSMISSION 7A-23
INSPECTION AND REASSEMBLY
1) Clean all components thoroughly, inspect them for any
abnormality and replace with new ones as necessary.
2) If synchronizer parts need to be repaired, check clearance
“a” between ring (2) and gear (1), each chamfered tooth of
gear, ring and sleeve, then determine parts replacement.
Clearance between synchronizer ring and gear
Standard “a” : 1.0 – 1.4 mm (0.039 – 0.055 in.)
Service limit “a” : 0.5 mm (0.019 in.)
3) To ensure lubrication, air blow oil holes (1) and make sure
that they are free from any obstruction.
4) Fit high speed synchronizer sleeve (4) to hub (3), insert 3
keys (2) in it and then set springs (1) as shown in figure.
Synchronizer key installation position
: A = B
5) Drive in right bearing (1) to input shaft (2) by using special
tool and hammer.
Special tool
(A) : 09913-80112
NOTE:
No specific direction is assigned to each key but it is
assigned as sleeve & hub assembly.
Size of high speed synchronizer sleeve, hub, keys and
springs is between those of low speed and 5th speed
ones.
[A] : 3rd gear side
C : Long flange
D : Key way
E : Projecting end
Page 25 of 447
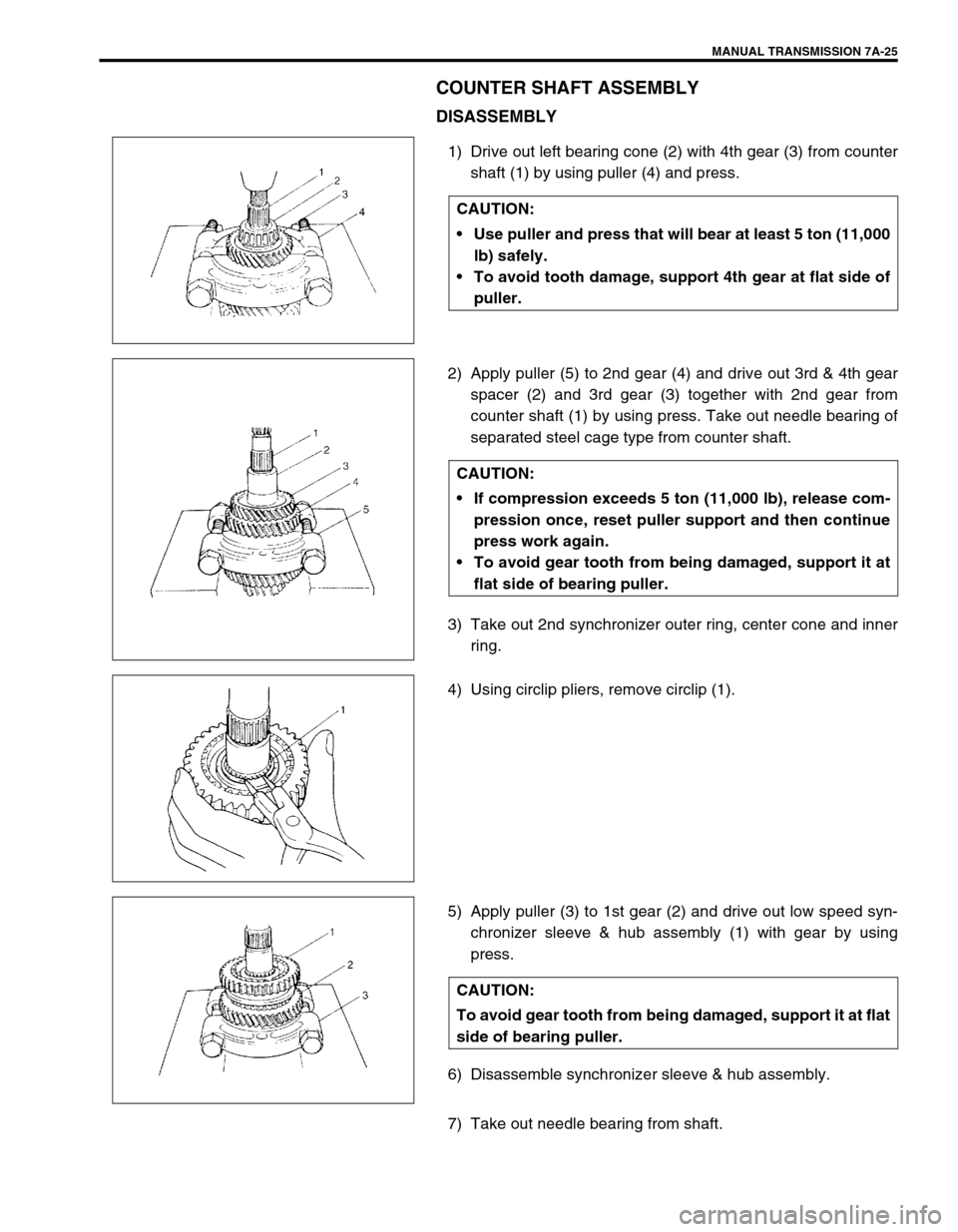
MANUAL TRANSMISSION 7A-25
COUNTER SHAFT ASSEMBLY
DISASSEMBLY
1) Drive out left bearing cone (2) with 4th gear (3) from counter
shaft (1) by using puller (4) and press.
2) Apply puller (5) to 2nd gear (4) and drive out 3rd & 4th gear
spacer (2) and 3rd gear (3) together with 2nd gear from
counter shaft (1) by using press. Take out needle bearing of
separated steel cage type from counter shaft.
3) Take out 2nd synchronizer outer ring, center cone and inner
ring.
4) Using circlip pliers, remove circlip (1).
5) Apply puller (3) to 1st gear (2) and drive out low speed syn-
chronizer sleeve & hub assembly (1) with gear by using
press.
6) Disassemble synchronizer sleeve & hub assembly.
7) Take out needle bearing from shaft.CAUTION:
Use puller and press that will bear at least 5 ton (11,000
lb) safely.
To avoid tooth damage, support 4th gear at flat side of
puller.
CAUTION:
If compression exceeds 5 ton (11,000 lb), release com-
pression once, reset puller support and then continue
press work again.
To avoid gear tooth from being damaged, support it at
flat side of bearing puller.
CAUTION:
To avoid gear tooth from being damaged, support it at flat
side of bearing puller.
Page 27 of 447
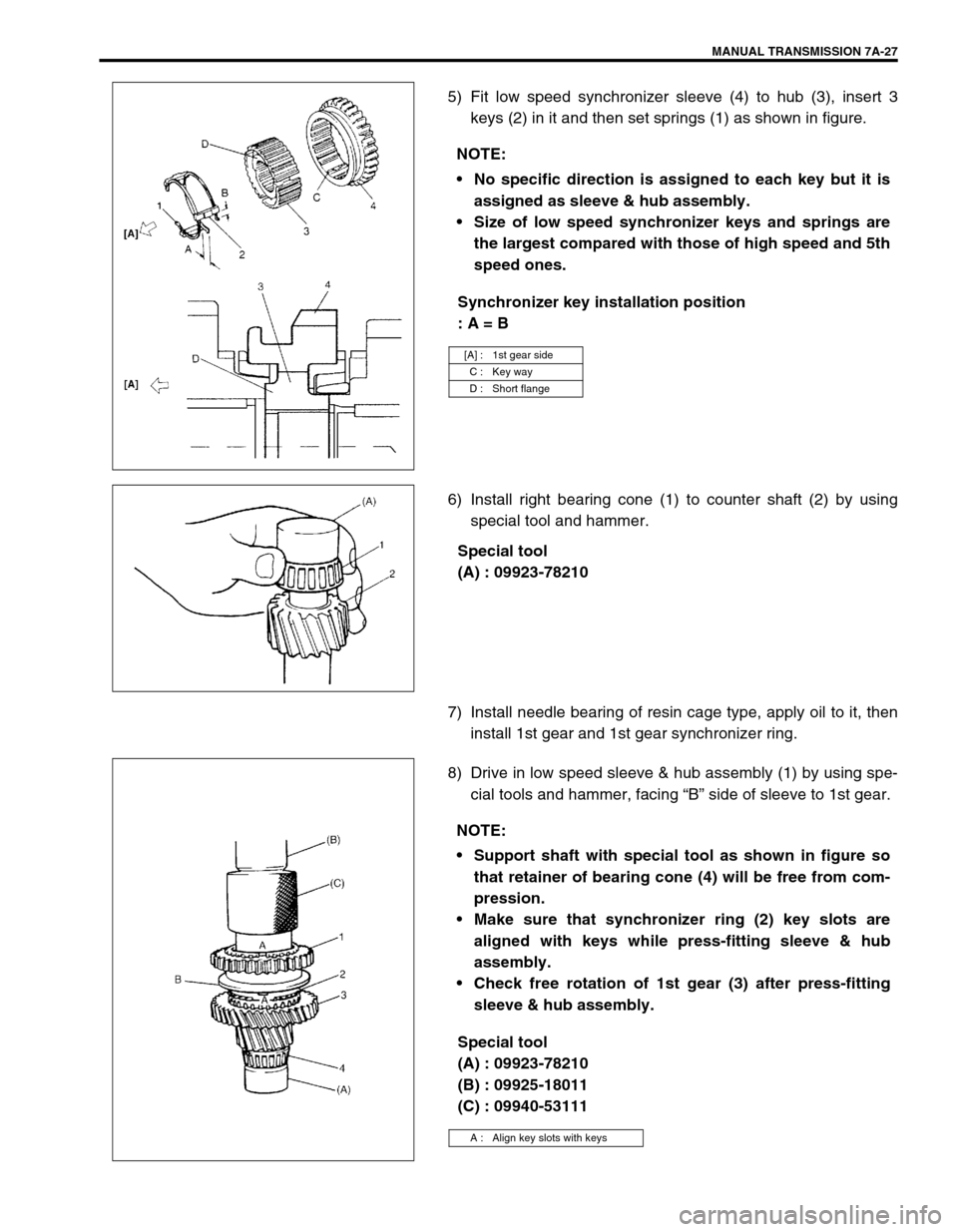
MANUAL TRANSMISSION 7A-27
5) Fit low speed synchronizer sleeve (4) to hub (3), insert 3
keys (2) in it and then set springs (1) as shown in figure.
Synchronizer key installation position
: A = B
6) Install right bearing cone (1) to counter shaft (2) by using
special tool and hammer.
Special tool
(A) : 09923-78210
7) Install needle bearing of resin cage type, apply oil to it, then
install 1st gear and 1st gear synchronizer ring.
8) Drive in low speed sleeve & hub assembly (1) by using spe-
cial tools and hammer, facing “B” side of sleeve to 1st gear.
Special tool
(A) : 09923-78210
(B) : 09925-18011
(C) : 09940-53111 NOTE:
No specific direction is assigned to each key but it is
assigned as sleeve & hub assembly.
Size of low speed synchronizer keys and springs are
the largest compared with those of high speed and 5th
speed ones.
[A] : 1st gear side
C : Key way
D : Short flange
NOTE:
Support shaft with special tool as shown in figure so
that retainer of bearing cone (4) will be free from com-
pression.
Make sure that synchronizer ring (2) key slots are
aligned with keys while press-fitting sleeve & hub
assembly.
Check free rotation of 1st gear (3) after press-fitting
sleeve & hub assembly.
A : Align key slots with keys
Page 28 of 447
7A-28 MANUAL TRANSMISSION
9) Install circlip (1) and confirm that circlip is installed in groove
securely.
Install needle bearing (2) of separated steel cage type, apply
oil to bearing.
With synchronizer outer ring (3), center cone (4) & inner ring
(5) put together and installed to 2nd gear (6) as shown in fig-
ure.
10) Press-fit 3rd gear (2) and spacer (1) by using special tools
and press.
Special tool
(A) : 09923-78210
(D) : 09913-80112
11) Press-fit 4th gear (2) by using the same procedure as the
above.
12) Install left bearing cone (1) by using special tools and ham-
mer.
Special tool
(A) : 09923-78210
(E) : 09925-98221
[A] : SECTION A - A
CAUTION:
Press-fit 3rd gear and spacer first, and then 4th gear later
separately so that counter shaft will not be compressed
excessively.
NOTE:
For protection of right bearing cone (3), always support
shaft with special tool as illustrated.
Page 29 of 447
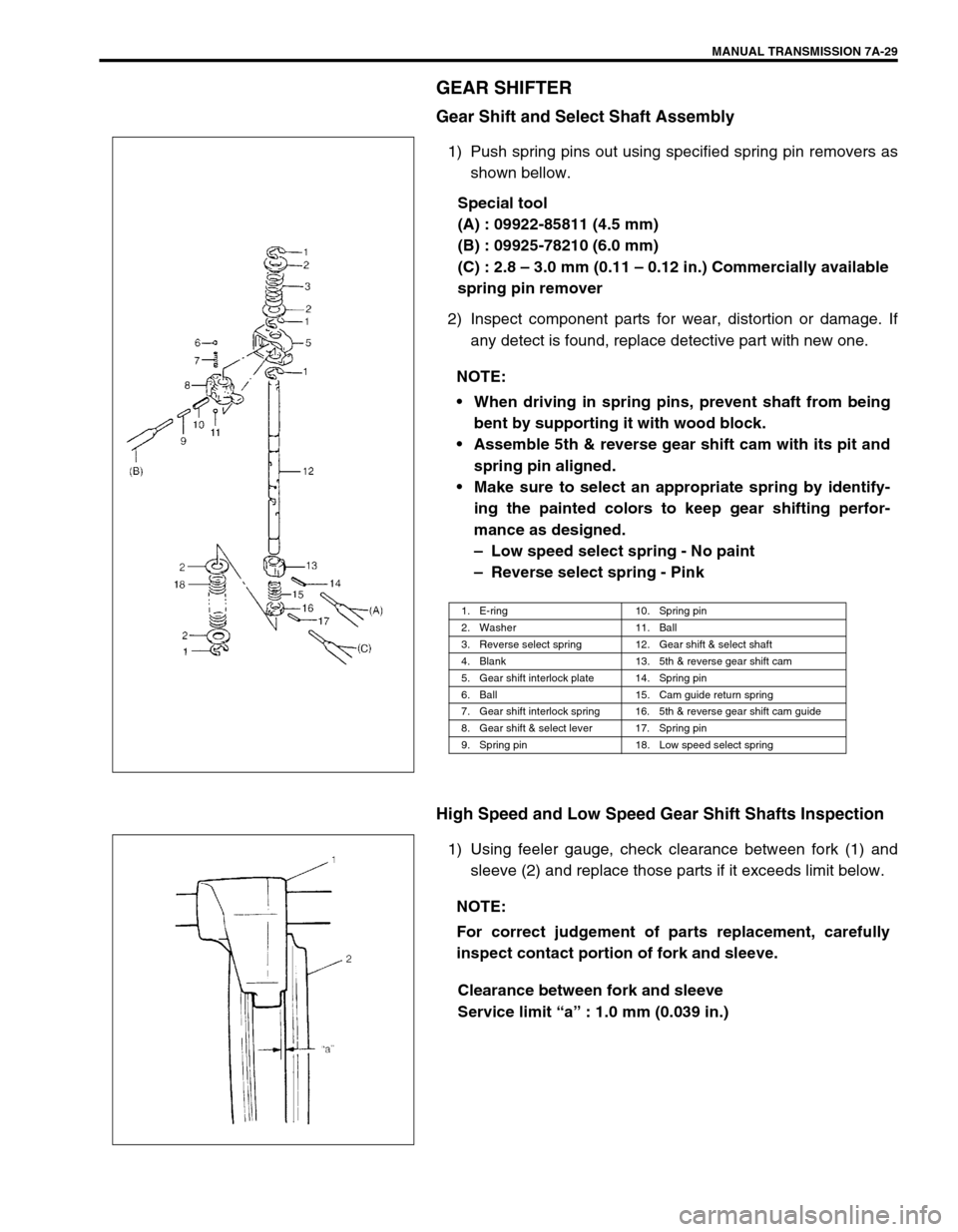
MANUAL TRANSMISSION 7A-29
GEAR SHIFTER
Gear Shift and Select Shaft Assembly
1) Push spring pins out using specified spring pin removers as
shown bellow.
Special tool
(A) : 09922-85811 (4.5 mm)
(B) : 09925-78210 (6.0 mm)
(C) : 2.8 – 3.0 mm (0.11 – 0.12 in.) Commercially available
spring pin remover
2) Inspect component parts for wear, distortion or damage. If
any detect is found, replace detective part with new one.
High Speed and Low Speed Gear Shift Shafts Inspection
1) Using feeler gauge, check clearance between fork (1) and
sleeve (2) and replace those parts if it exceeds limit below.
Clearance between fork and sleeve
Service limit “a” : 1.0 mm (0.039 in.) NOTE:
When driving in spring pins, prevent shaft from being
bent by supporting it with wood block.
Assemble 5th & reverse gear shift cam with its pit and
spring pin aligned.
Make sure to select an appropriate spring by identify-
ing the painted colors to keep gear shifting perfor-
mance as designed.
– Low speed select spring - No paint
– Reverse select spring - Pink
1. E-ring 10. Spring pin
2. Washer 11. Ball
3. Reverse select spring 12. Gear shift & select shaft
4. Blank 13. 5th & reverse gear shift cam
5. Gear shift interlock plate 14. Spring pin
6. Ball 15. Cam guide return spring
7. Gear shift interlock spring 16. 5th & reverse gear shift cam guide
8. Gear shift & select lever 17. Spring pin
9. Spring pin 18. Low speed select spring
NOTE:
For correct judgement of parts replacement, carefully
inspect contact portion of fork and sleeve.
Page 30 of 447
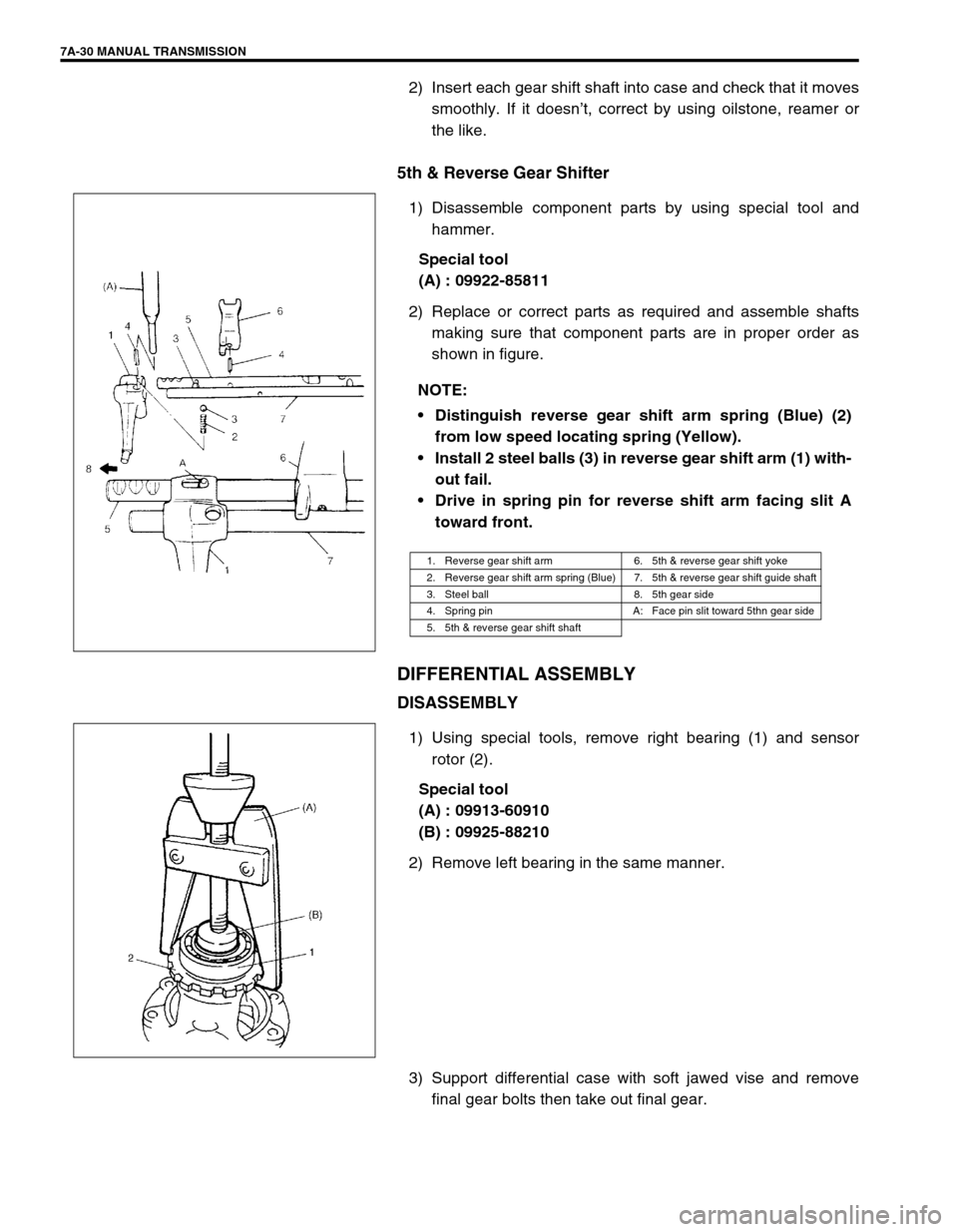
7A-30 MANUAL TRANSMISSION
2) Insert each gear shift shaft into case and check that it moves
smoothly. If it doesn’t, correct by using oilstone, reamer or
the like.
5th & Reverse Gear Shifter
1) Disassemble component parts by using special tool and
hammer.
Special tool
(A) : 09922-85811
2) Replace or correct parts as required and assemble shafts
making sure that component parts are in proper order as
shown in figure.
DIFFERENTIAL ASSEMBLY
DISASSEMBLY
1) Using special tools, remove right bearing (1) and sensor
rotor (2).
Special tool
(A) : 09913-60910
(B) : 09925-88210
2) Remove left bearing in the same manner.
3) Support differential case with soft jawed vise and remove
final gear bolts then take out final gear. NOTE:
Distinguish reverse gear shift arm spring (Blue) (2)
from low speed locating spring (Yellow).
Install 2 steel balls (3) in reverse gear shift arm (1) with-
out fail.
Drive in spring pin for reverse shift arm facing slit A
toward front.
1. Reverse gear shift arm 6. 5th & reverse gear shift yoke
2. Reverse gear shift arm spring (Blue) 7. 5th & reverse gear shift guide shaft
3. Steel ball 8. 5th gear side
4. Spring pin A: Face pin slit toward 5thn gear side
5. 5th & reverse gear shift shaft
Page 31 of 447
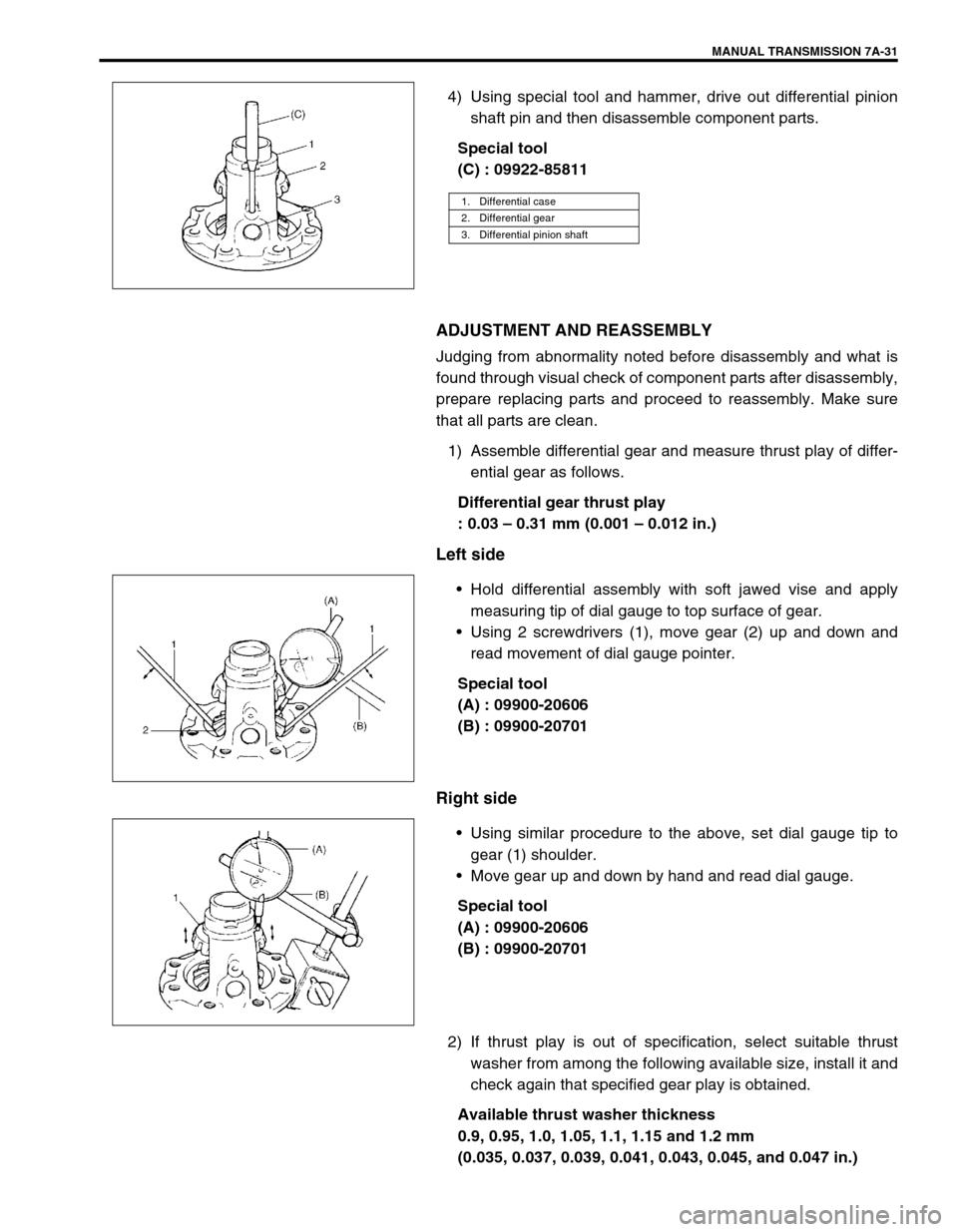
MANUAL TRANSMISSION 7A-31
4) Using special tool and hammer, drive out differential pinion
shaft pin and then disassemble component parts.
Special tool
(C) : 09922-85811
ADJUSTMENT AND REASSEMBLY
Judging from abnormality noted before disassembly and what is
found through visual check of component parts after disassembly,
prepare replacing parts and proceed to reassembly. Make sure
that all parts are clean.
1) Assemble differential gear and measure thrust play of differ-
ential gear as follows.
Differential gear thrust play
: 0.03 – 0.31 mm (0.001 – 0.012 in.)
Left side
Hold differential assembly with soft jawed vise and apply
measuring tip of dial gauge to top surface of gear.
Using 2 screwdrivers (1), move gear (2) up and down and
read movement of dial gauge pointer.
Special tool
(A) : 09900-20606
(B) : 09900-20701
Right side
Using similar procedure to the above, set dial gauge tip to
gear (1) shoulder.
Move gear up and down by hand and read dial gauge.
Special tool
(A) : 09900-20606
(B) : 09900-20701
2) If thrust play is out of specification, select suitable thrust
washer from among the following available size, install it and
check again that specified gear play is obtained.
Available thrust washer thickness
0.9, 0.95, 1.0, 1.05, 1.1, 1.15 and 1.2 mm
(0.035, 0.037, 0.039, 0.041, 0.043, 0.045, and 0.047 in.)
1. Differential case
2. Differential gear
3. Differential pinion shaft