Page 381 of 557
6B-4 ENGINE COOLING
COOLANT (WATER) TEMP. GAUGE
The coolant temp. gauge is included in engine coolant temp. (ECT)
sensor (1). This gauge activates a temp. meter in the instrument
cluster.
DIAGNOSIS
ConditionPossible CauseCorrection
Engine overheatsLoose or broken water pump belt
Not enough coolant
Faulty thermostat
Faulty water pump
Dirty or bent radiator fins
Coolant leakage on cooling system
Defective cooling fan motor
Plugged radiator
Faulty radiator cap
Maladjusted ignition timing
Dragging brakes
Slipping clutchAdjust or replace.
Check coolant level and add as
necessary.
Replace.
Replace.
Clean or remedy.
Repair.
Check and replace as
necessary.
Check and replace radiator as
necessary.
Replace.
Adjust.
Adjust brake.
Adjust or replace.
Page 384 of 557
1. Radiator hose
2. Clamp
ENGINE COOLING 6B-7
ON-VEHICLE SERVICE
WARNING:
Check to make sure that engine coolant temperature is
cold before removing any part of cooling system.
Also be sure to disconnect negative cord from battery ter-
minal before removing any part.
COOLING WATER PIPES OR HOSES
REMOVAL
1) Drain cooling system.
2) To remove these pipes or hoses, loosen screw on each pipe or
hose clip and pull hose end off.
INSTALLATION
Install removed parts in reverse order of removal procedure, noting
the following.
Tighten each clamp bolt securely.
Refill cooling system with proper coolant, referring to description
on COOLANT of MAINTENANCE.
THERMOSTAT
REMOVAL
1) Disconnect negative cable at battery.
2) Drain cooling system and tighten drain plug.
3) Disconnect thermostat cap (1) from thermostat case (2).
Page 385 of 557
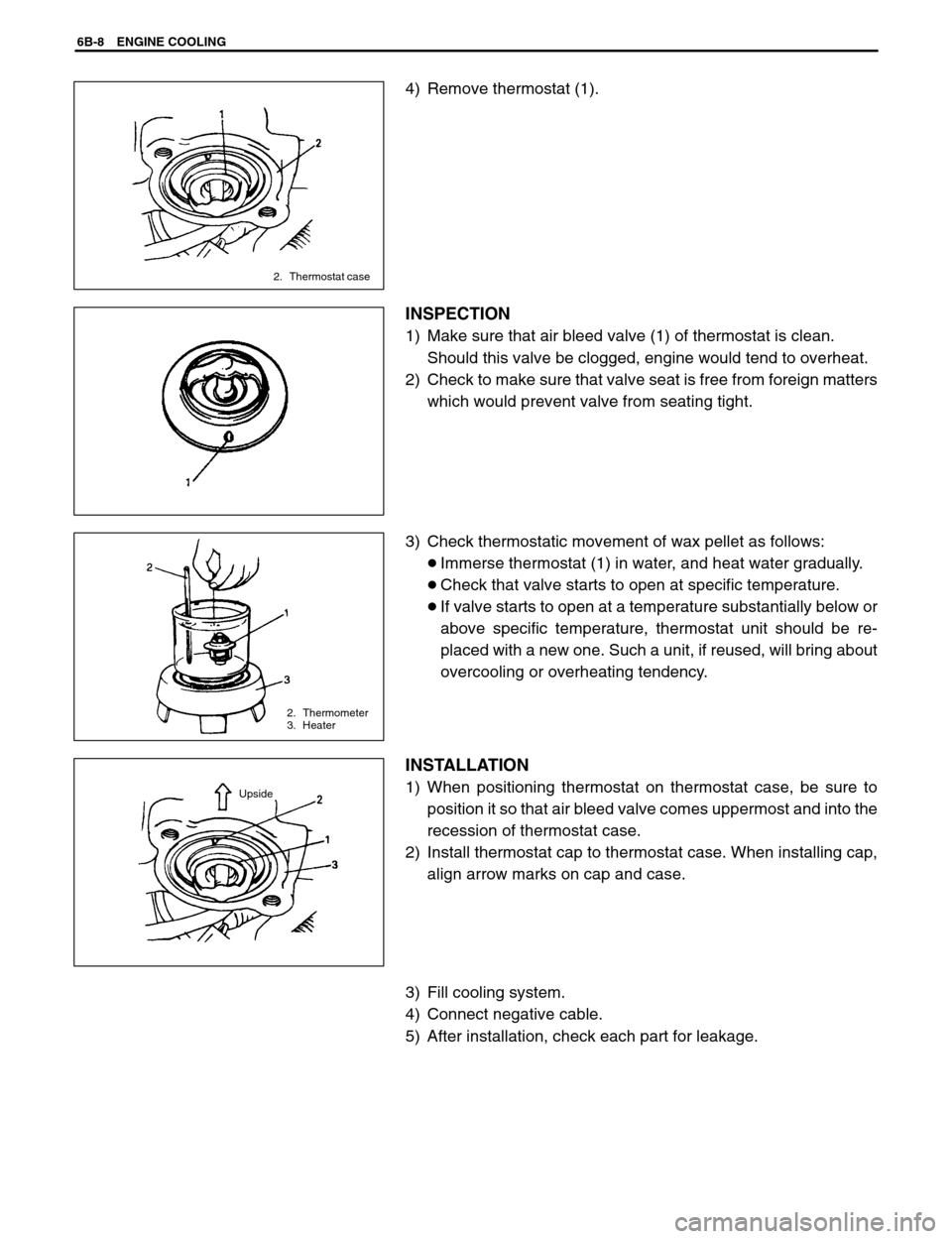
2. Thermostat case
2. Thermometer
3. Heater
Upside
6B-8 ENGINE COOLING
4) Remove thermostat (1).
INSPECTION
1) Make sure that air bleed valve (1) of thermostat is clean.
Should this valve be clogged, engine would tend to overheat.
2) Check to make sure that valve seat is free from foreign matters
which would prevent valve from seating tight.
3) Check thermostatic movement of wax pellet as follows:
Immerse thermostat (1) in water, and heat water gradually.
Check that valve starts to open at specific temperature.
If valve starts to open at a temperature substantially below or
above specific temperature, thermostat unit should be re-
placed with a new one. Such a unit, if reused, will bring about
overcooling or overheating tendency.
INSTALLATION
1) When positioning thermostat on thermostat case, be sure to
position it so that air bleed valve comes uppermost and into the
recession of thermostat case.
2) Install thermostat cap to thermostat case. When installing cap,
align arrow marks on cap and case.
3) Fill cooling system.
4) Connect negative cable.
5) After installation, check each part for leakage.
Page 386 of 557
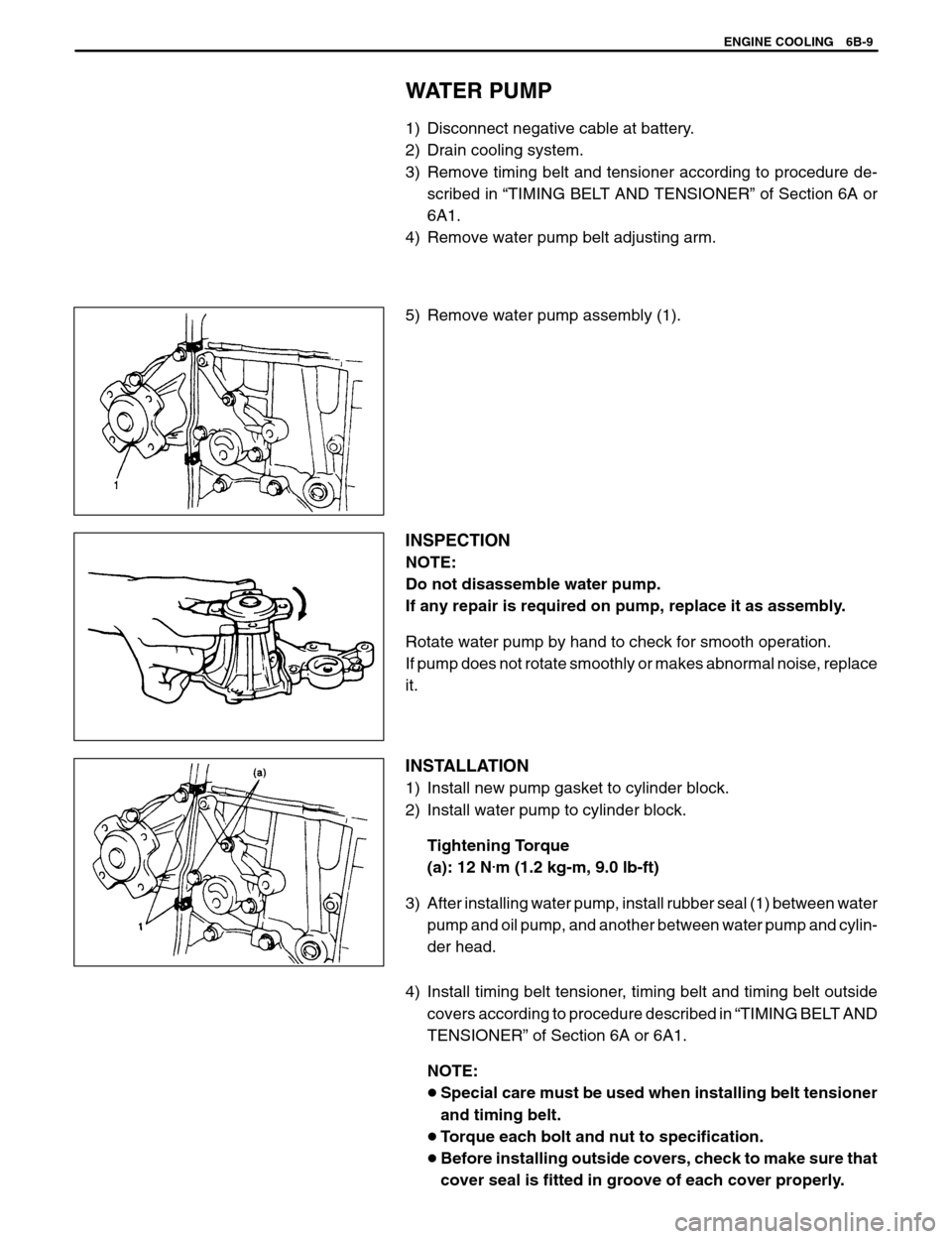
ENGINE COOLING 6B-9
WATER PUMP
1) Disconnect negative cable at battery.
2) Drain cooling system.
3) Remove timing belt and tensioner according to procedure de-
scribed in “TIMING BELT AND TENSIONER” of Section 6A or
6A1.
4) Remove water pump belt adjusting arm.
5) Remove water pump assembly (1).
INSPECTION
NOTE:
Do not disassemble water pump.
If any repair is required on pump, replace it as assembly.
Rotate water pump by hand to check for smooth operation.
If pump does not rotate smoothly or makes abnormal noise, replace
it.
INSTALLATION
1) Install new pump gasket to cylinder block.
2) Install water pump to cylinder block.
Tightening Torque
(a): 12 N
.m (1.2 kg-m, 9.0 lb-ft)
3) After installing water pump, install rubber seal (1) between water
pump and oil pump, and another between water pump and cylin-
der head.
4) Install timing belt tensioner, timing belt and timing belt outside
covers according to procedure described in “TIMING BELT AND
TENSIONER” of Section 6A or 6A1.
NOTE:
Special care must be used when installing belt tensioner
and timing belt.
Torque each bolt and nut to specification.
Before installing outside covers, check to make sure that
cover seal is fitted in groove of each cover properly.
Page 387 of 557
6B-10 ENGINE COOLING
5) Install crankshaft pulley, water pump pulley, and pump drive
belt referring to Section 6A or 6A1.
6) Adjust water pump belt tension.
7) Install fender apron extension on right side.
8) Install air cleaner assembly.
9) Connect negative cable at battery.
10) Fill cooling system.
11) After installation, check each part for leakage.
Page 389 of 557
1. Fuel tank
2. Fuel pump and level gauge
3. Fuel filler cap
4. 2-way check valve
5. Breather hose
6. Fuel feed line
7. Fuel return line
8. Fuel vapor line
9. Fuel cut valve
10. Fuel tank pad
11. Fuel tank fixer bolt
: Tightening Torque
6C-2 ENGINE FUEL
ON-VEHICLE SERVICE
FUEL LINES
INSPECTION
Visually inspect fuel lines for evidence of fuel leakage, hose crack
and deterioration, or damage.
Make sure all clamps are secure.
Replace parts as needed.
FUEL TANK
REMOVAL
1) Relieve fuel pressure in fuel feed line according to procedure de-
scribed in Section 6.
2) Disconnect negative cable at battery.
3) Remove rear seat cushion referring to Section 9.
4) Disconnect connectors (1) of fuel tank wire harness.
5) Hoist vehicle.
6) Disconnect fuel filler hose (3) from fuel tank and breather hose
(2) from filler neck (1).
Page 390 of 557
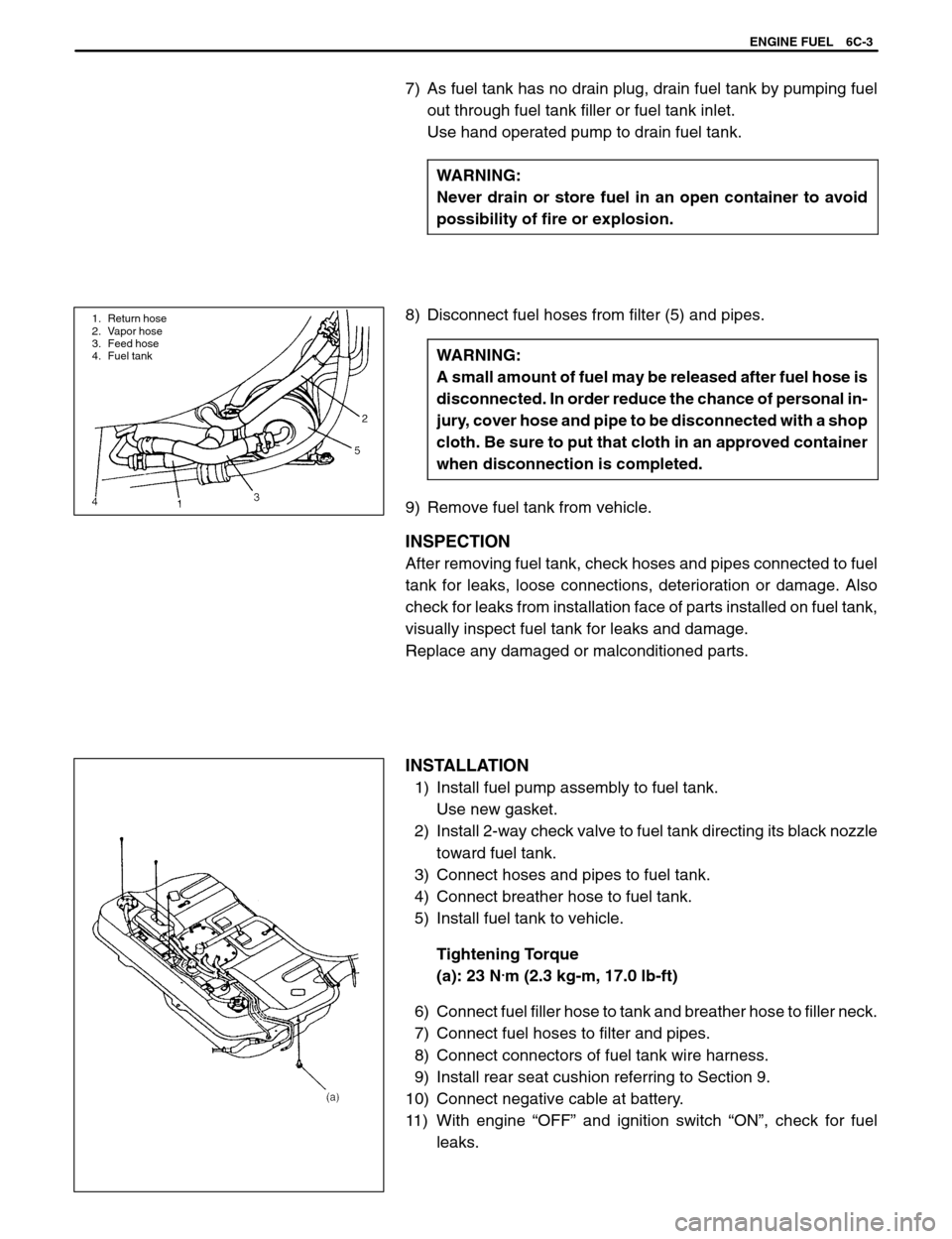
1. Return hose
2. Vapor hose
3. Feed hose
4. Fuel tank
ENGINE FUEL 6C-3
7) As fuel tank has no drain plug, drain fuel tank by pumping fuel
out through fuel tank filler or fuel tank inlet.
Use hand operated pump to drain fuel tank.
WARNING:
Never drain or store fuel in an open container to avoid
possibility of fire or explosion.
8) Disconnect fuel hoses from filter (5) and pipes.
WARNING:
A small amount of fuel may be released after fuel hose is
disconnected. In order reduce the chance of personal in-
jury, cover hose and pipe to be disconnected with a shop
cloth. Be sure to put that cloth in an approved container
when disconnection is completed.
9) Remove fuel tank from vehicle.
INSPECTION
After removing fuel tank, check hoses and pipes connected to fuel
tank for leaks, loose connections, deterioration or damage. Also
check for leaks from installation face of parts installed on fuel tank,
visually inspect fuel tank for leaks and damage.
Replace any damaged or malconditioned parts.
INSTALLATION
1) Install fuel pump assembly to fuel tank.
Use new gasket.
2) Install 2-way check valve to fuel tank directing its black nozzle
toward fuel tank.
3) Connect hoses and pipes to fuel tank.
4) Connect breather hose to fuel tank.
5) Install fuel tank to vehicle.
Tightening Torque
(a): 23 N
.m (2.3 kg-m, 17.0 lb-ft)
6) Connect fuel filler hose to tank and breather hose to filler neck.
7) Connect fuel hoses to filter and pipes.
8) Connect connectors of fuel tank wire harness.
9) Install rear seat cushion referring to Section 9.
10) Connect negative cable at battery.
11) With engine “OFF” and ignition switch “ON”, check for fuel
leaks.
Page 391 of 557
6C-4 ENGINE FUEL
FUEL PUMP ASSEMBLY
REMOVAL
1) Remove fuel tank (1) from vehicle referring to “FUEL TANK” in
this section.
2) Disconnect fuel feed hose (2), fuel return hose (3) and breather
hose (4) from fuel pump assembly (5).
3) Remove fuel pump assembly from fuel tank by removing
screws.
INSPECTION
Check fuel pump assembly for damage.
Check fuel suction filter (1) for evidence of dirt and contamination.
If present, replace or clean and check for presence of dirt in fuel
tank.
INSTALLATION
Reverse removal procedure for installation noting the followings.
Use new gasket.
Clamp hoses securely.