Page 325 of 557
6A1-30 ENGINE MECHANICAL (G13B, 1-CAM 16-VALVES ENGINE)
NOTE:
When installing oil seal (1), press-fit it till its end face is flush
with oil pump case (2) end face.
Check outer and inner rotors, rotor plate, and oil pump case for
excessive wear or damage.
MEASUREMENT
Radial clearance
Check radial clearance between outer rotor (1) and case, using
thickness gauge.
If clearance exceeds its limit, replace outer rotor or case.
Limit on radial clearance between outer rotor and case:
0.200 mm (0.079 in.)
Side clearance
Using straight edge and thickness gauge, measure side clear-
ance.
Limit on side clearance: 0.10 mm (0.0039 in.)
ASSEMBLY
1) Wash, clean and then dry all disassembled parts.
2) Apply thin coat of engine oil to inner (2) and outer rotors (1), oil
seal lip portion, and inside surfaces of oil pump case and plate.
3) Install outer and inner rotors to pump case.
Page 331 of 557

6A1-36 ENGINE MECHANICAL (G13B, 1-CAM 16-VALVES ENGINE)
Rocker Arm-to-Rocker Arm Shaft Clearance
Using a micrometer and a bore gauge, measure rocker shaft dia.
and rocker arm l.D.
Difference between two readings is arm-to-shaft clearance on
which a limit is specified.
If limit is exceeded, replace shaft or arm, or both.
Item
StandardLimit
Rocker arm l.D.15.996 – 16.014 mm
(0.629 – 0.630 in.)———
Rocker arm shaft dia.15.969 – 15.984 mm
(0.6287 – 0.6293 in.)———
Arm-to-shaft clearance0.012 – 0.045 mm
(0.0005 – 0.0018 in.)0.09 mm
(0.0035 in.)
Cam Wear
Using a micrometer, measured height of cam. If measured height
is below limit, replace camshaft.
Cam height
StandardLimit
Intake cam36.184 – 36.344 mm
(1.4246 – 1.4309 in.)36.084 mm
(1.4206 in.)
Exhaust cam35.900 – 36.060 mm
(1.4134 – 1.4197 in.)35.800 mm
(1.4094 in.)
Camshaft Runout
Hold camshaft between two “V” blocks, and measure runout by us-
ing a dial gauge.
If runout exceeds the limit, replace camshaft.
Runout limit: 0.10 mm (0.0039 in.)
Camshaft Journal Wear
Check camshaft journals and camshaft housings for pitting,
scratches, wear or damage.
If any malcondition is found, replace camshaft or cylinder head with
housing. Never replace cylinder head without replacing housing.
Page 332 of 557
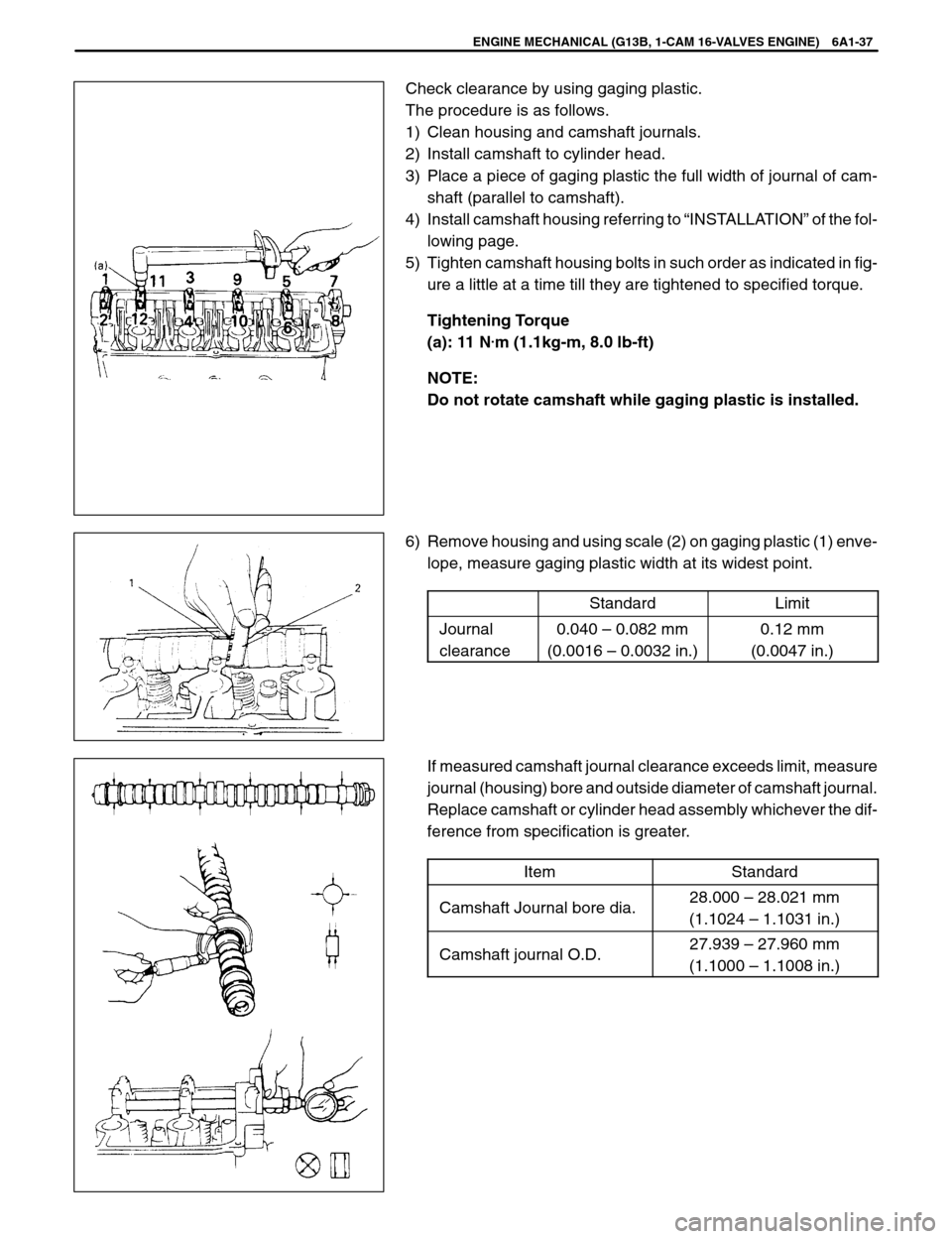
ENGINE MECHANICAL (G13B, 1-CAM 16-VALVES ENGINE) 6A1-37
Check clearance by using gaging plastic.
The procedure is as follows.
1) Clean housing and camshaft journals.
2) Install camshaft to cylinder head.
3) Place a piece of gaging plastic the full width of journal of cam-
shaft (parallel to camshaft).
4) Install camshaft housing referring to “INSTALLATION” of the fol-
lowing page.
5) Tighten camshaft housing bolts in such order as indicated in fig-
ure a little at a time till they are tightened to specified torque.
Tightening Torque
(a): 11 N
.m (1.1kg-m, 8.0 lb-ft)
NOTE:
Do not rotate camshaft while gaging plastic is installed.
6) Remove housing and using scale (2) on gaging plastic (1) enve-
lope, measure gaging plastic width at its widest point.
StandardLimit
Journal
clearance0.040 – 0.082 mm
(0.0016 – 0.0032 in.)0.12 mm
(0.0047 in.)
If measured camshaft journal clearance exceeds limit, measure
journal (housing) bore and outside diameter of camshaft journal.
Replace camshaft or cylinder head assembly whichever the dif-
ference from specification is greater.
Item
Standard
Camshaft Journal bore dia.28.000 – 28.021 mm
(1.1024 – 1.1031 in.)
Camshaft journal O.D.27.939 – 27.960 mm
(1.1000 – 1.1008 in.)
Page 335 of 557
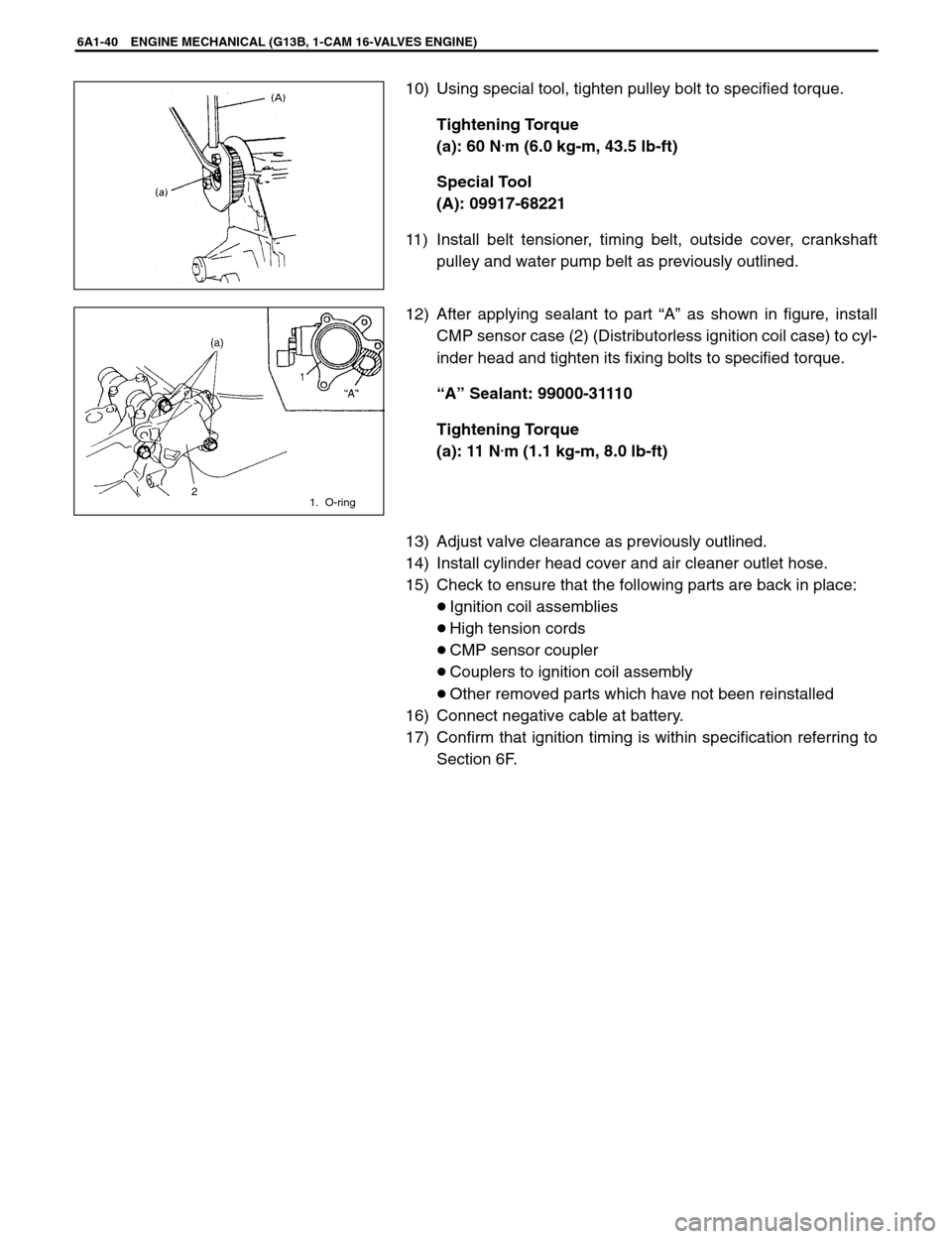
6A1-40 ENGINE MECHANICAL (G13B, 1-CAM 16-VALVES ENGINE)
1. O-ring2
10) Using special tool, tighten pulley bolt to specified torque.
Tightening Torque
(a): 60 N
.m (6.0 kg-m, 43.5 lb-ft)
Special Tool
(A): 09917-68221
11) Install belt tensioner, timing belt, outside cover, crankshaft
pulley and water pump belt as previously outlined.
12) After applying sealant to part “A” as shown in figure, install
CMP sensor case (2) (Distributorless ignition coil case) to cyl-
inder head and tighten its fixing bolts to specified torque.
“A” Sealant: 99000-31110
Tightening Torque
(a): 11 N
.m (1.1 kg-m, 8.0 lb-ft)
13) Adjust valve clearance as previously outlined.
14) Install cylinder head cover and air cleaner outlet hose.
15) Check to ensure that the following parts are back in place:
Ignition coil assemblies
High tension cords
CMP sensor coupler
Couplers to ignition coil assembly
Other removed parts which have not been reinstalled
16) Connect negative cable at battery.
17) Confirm that ignition timing is within specification referring to
Section 6F.
Page 340 of 557
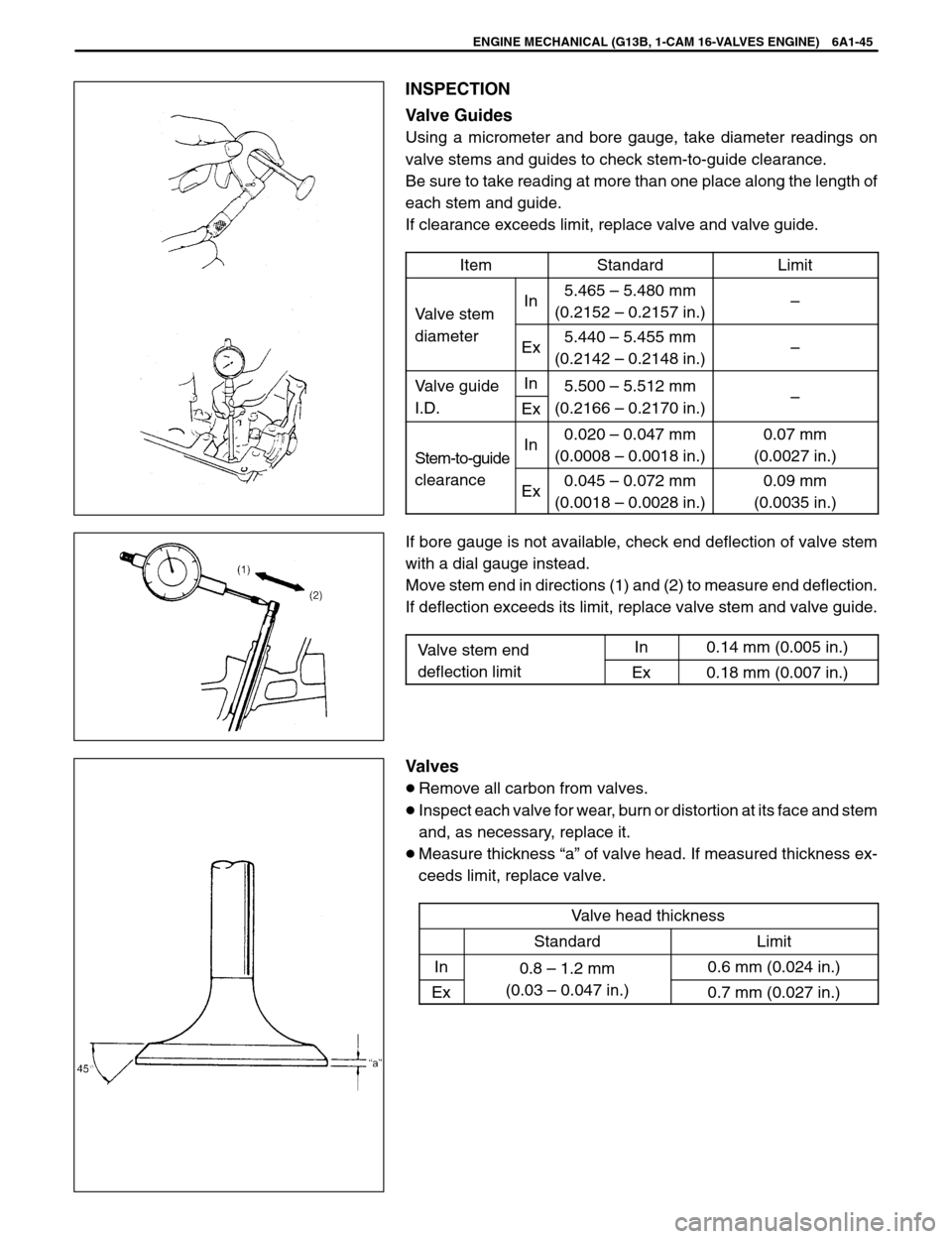
ENGINE MECHANICAL (G13B, 1-CAM 16-VALVES ENGINE) 6A1-45
INSPECTION
Valve Guides
Using a micrometer and bore gauge, take diameter readings on
valve stems and guides to check stem-to-guide clearance.
Be sure to take reading at more than one place along the length of
each stem and guide.
If clearance exceeds limit, replace valve and valve guide.
Item
StandardLimit
Valve stemIn5.465 – 5.480 mm
(0.2152 – 0.2157 in.)–
diameterEx5.440 – 5.455 mm
(0.2142 – 0.2148 in.)–
Valve guideIn5.500 – 5.512 mmg
I.D.Ex(0.2166 – 0.2170 in.)–
Stem-to-guideIn0.020 – 0.047 mm
(0.0008 – 0.0018 in.)0.07 mm
(0.0027 in.)
g
clearanceEx0.045 – 0.072 mm
(0.0018 – 0.0028 in.)0.09 mm
(0.0035 in.)
If bore gauge is not available, check end deflection of valve stem
with a dial gauge instead.
Move stem end in directions (1) and (2) to measure end deflection.
If deflection exceeds its limit, replace valve stem and valve guide.
Valve stem end
In0.14 mm (0.005 in.)
deflection limitEx0.18 mm (0.007 in.)
Valves
Remove all carbon from valves.
Inspect each valve for wear, burn or distortion at its face and stem
and, as necessary, replace it.
Measure thickness “a” of valve head. If measured thickness ex-
ceeds limit, replace valve.
Valve head thickness
StandardLimit
In0.8 – 1.2 mm0.6 mm (0.024 in.)
Ex(0.03 – 0.047 in.)0.7 mm (0.027 in.)
Page 344 of 557
ENGINE MECHANICAL (G13B, 1-CAM 16-VALVES ENGINE) 6A1-49
Valve Springs
Referring to data given below, check to be sure that each spring
is in sound condition, free of any evidence of breakage or weak-
ening. Remember, weakened valve springs can cause chatter,
not to mention possibility of reducing power output due to gas
leakage caused by decreased seating pressure.
Item
StandardLimit
Valve spring
free length36.83 mm
(1.4500 in.)35.67 mm
(1.4043 in.)
Valve spring
preload10.7 – 12.5 kg for
31.5 mm (23.6 –
27.5 lb / 1.24 in.)9.3 kg for 31.5 mm
(20.5 lb / 1.24 in.)
Spring squareness:
Use a square and surface plate to check each spring for square-
ness in terms of clearance between end of valve spring and
square. Valve springs found to exhibit a larger clearance than limit
given below must be replaced.
Valve spring squareness limit: 1.6 mm (0.063 in.)
Page 352 of 557
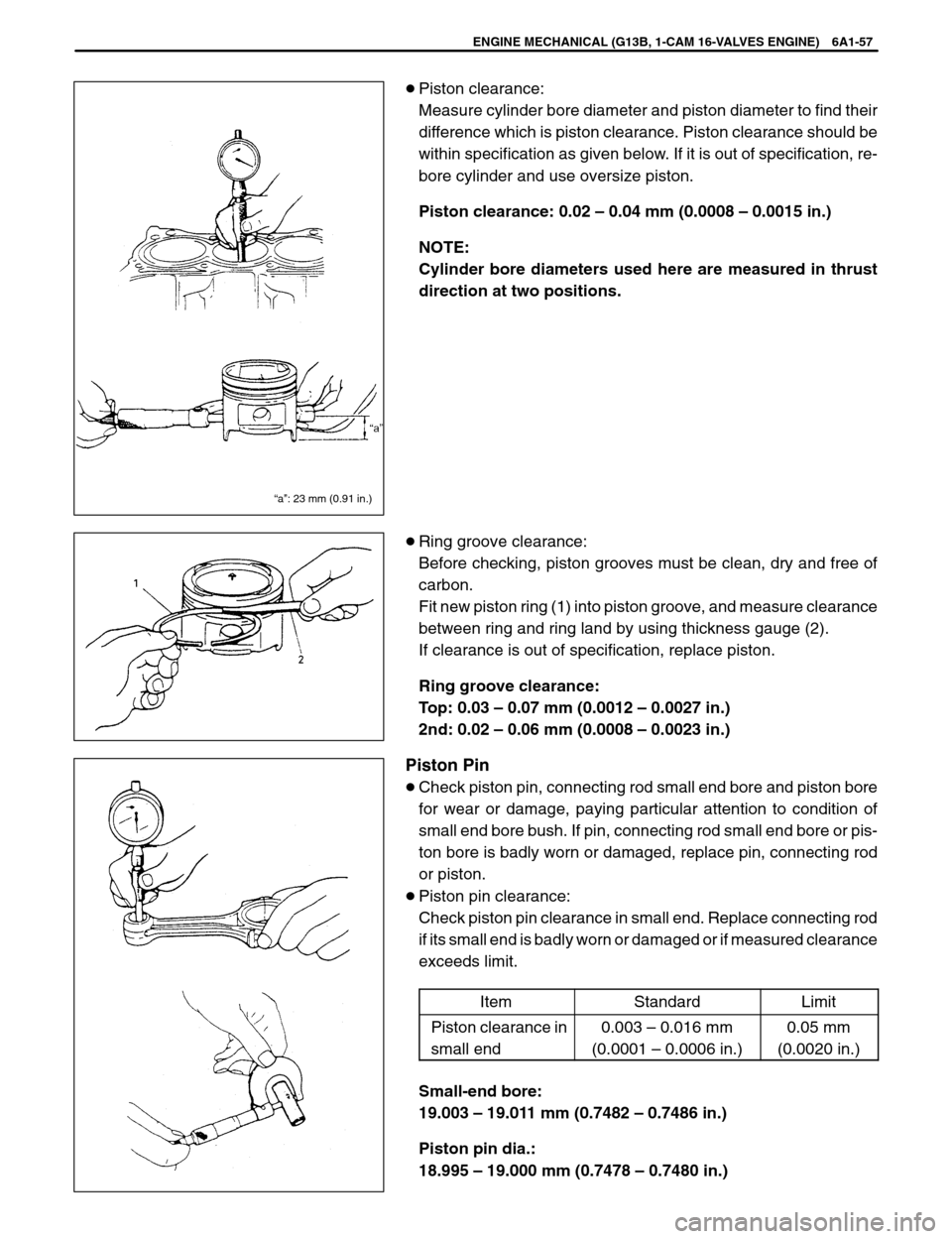
“a”: 23 mm (0.91 in.)
ENGINE MECHANICAL (G13B, 1-CAM 16-VALVES ENGINE) 6A1-57
Piston clearance:
Measure cylinder bore diameter and piston diameter to find their
difference which is piston clearance. Piston clearance should be
within specification as given below. If it is out of specification, re-
bore cylinder and use oversize piston.
Piston clearance: 0.02 – 0.04 mm (0.0008 – 0.0015 in.)
NOTE:
Cylinder bore diameters used here are measured in thrust
direction at two positions.
Ring groove clearance:
Before checking, piston grooves must be clean, dry and free of
carbon.
Fit new piston ring (1) into piston groove, and measure clearance
between ring and ring land by using thickness gauge (2).
If clearance is out of specification, replace piston.
Ring groove clearance:
Top: 0.03 – 0.07 mm (0.0012 – 0.0027 in.)
2nd: 0.02 – 0.06 mm (0.0008 – 0.0023 in.)
Piston Pin
Check piston pin, connecting rod small end bore and piston bore
for wear or damage, paying particular attention to condition of
small end bore bush. If pin, connecting rod small end bore or pis-
ton bore is badly worn or damaged, replace pin, connecting rod
or piston.
Piston pin clearance:
Check piston pin clearance in small end. Replace connecting rod
if its small end is badly worn or damaged or if measured clearance
exceeds limit.
Item
StandardLimit
Piston clearance in
small end0.003 – 0.016 mm
(0.0001 – 0.0006 in.)0.05 mm
(0.0020 in.)
Small-end bore:
19.003 – 19.011 mm (0.7482 – 0.7486 in.)
Piston pin dia.:
18.995 – 19.000 mm (0.7478 – 0.7480 in.)
Page 353 of 557
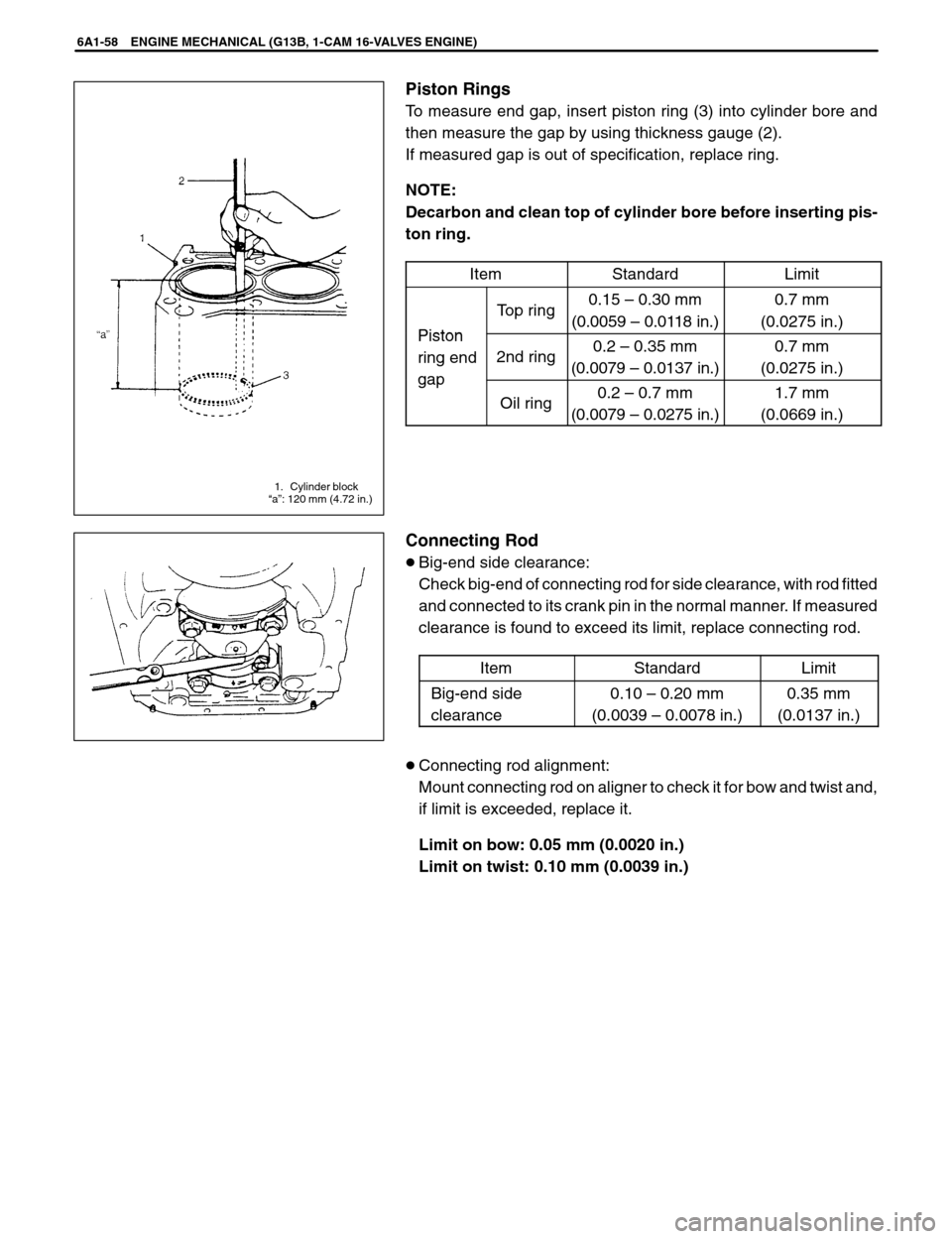
1. Cylinder block
“a”: 120 mm (4.72 in.)
6A1-58 ENGINE MECHANICAL (G13B, 1-CAM 16-VALVES ENGINE)
Piston Rings
To measure end gap, insert piston ring (3) into cylinder bore and
then measure the gap by using thickness gauge (2).
If measured gap is out of specification, replace ring.
NOTE:
Decarbon and clean top of cylinder bore before inserting pis-
ton ring.
Item
StandardLimit
Piston
Top ring0.15 – 0.30 mm
(0.0059 – 0.0118 in.)0.7 mm
(0.0275 in.)
Piston
ring end
gap
2nd ring0.2 – 0.35 mm
(0.0079 – 0.0137 in.)0.7 mm
(0.0275 in.)
ga
Oil ring0.2 – 0.7 mm
(0.0079 – 0.0275 in.)1.7 mm
(0.0669 in.)
Connecting Rod
Big-end side clearance:
Check big-end of connecting rod for side clearance, with rod fitted
and connected to its crank pin in the normal manner. If measured
clearance is found to exceed its limit, replace connecting rod.
Item
StandardLimit
Big-end side
clearance0.10 – 0.20 mm
(0.0039 – 0.0078 in.)0.35 mm
(0.0137 in.)
Connecting rod alignment:
Mount connecting rod on aligner to check it for bow and twist and,
if limit is exceeded, replace it.
Limit on bow: 0.05 mm (0.0020 in.)
Limit on twist: 0.10 mm (0.0039 in.)