Page 192 of 557
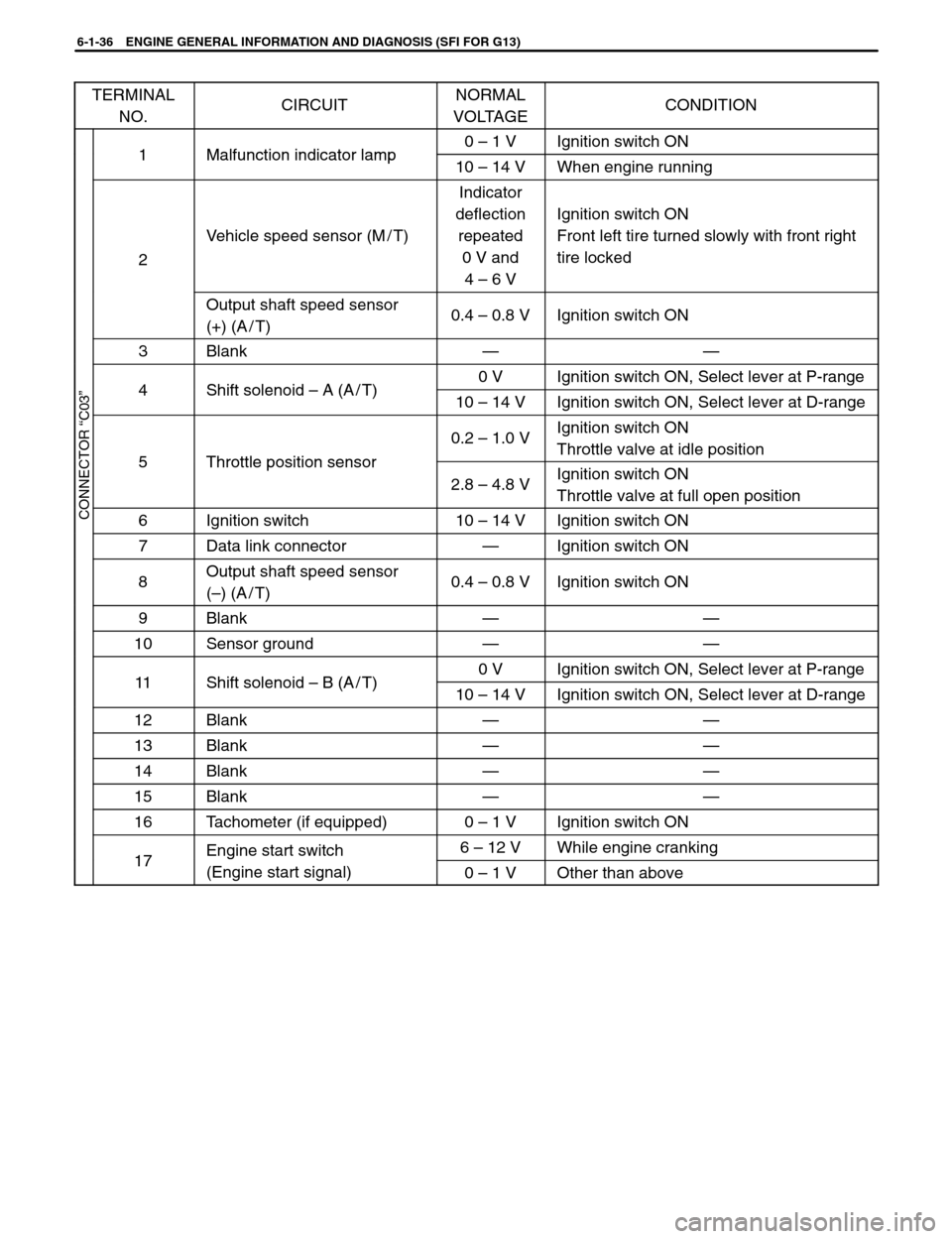
6-1-36 ENGINE GENERAL INFORMATION AND DIAGNOSIS (SFI FOR G13)
CONNECTOR “C03”
TERMINAL
NO.CIRCUITNORMAL
VOLTAGECONDITION
1Malfunction indicator lamp0 – 1 VIgnition switch ON1Malfunction indicator lamp10 – 14 VWhen engine running
2
Vehicle speed sensor (M / T)
Indicator
deflection
repeated
0 V and
4 – 6 V
Ignition switch ON
Front left tire turned slowly with front right
tire locked
Output shaft speed sensor
(+) (A / T)0.4 – 0.8 VIgnition switch ON
3Blank——
4Shift solenoidA(A / T)0 VIgnition switch ON, Select lever at P-range4Shift solenoid – A (A / T)10 – 14 VIgnition switch ON, Select lever at D-range
5Throttleposition sensor
0.2 – 1.0 VIgnition switch ON
Throttle valve at idle position
5Throttle position sensor
2.8 – 4.8 VIgnition switch ON
Throttle valve at full open position
6Ignition switch10 – 14 VIgnition switch ON
7Data link connector—Ignition switch ON
8Output shaft speed sensor
(–) (A / T)0.4 – 0.8 VIgnition switch ON
9Blank——
10Sensor ground——
11Shift solenoidB(A / T)0 VIgnition switch ON, Select lever at P-range11Shift solenoid – B (A / T)10 – 14 VIgnition switch ON, Select lever at D-range
12Blank——
13Blank——
14Blank——
15Blank——
16Tachometer (if equipped)0 – 1 VIgnition switch ON
17Engine start switch6 – 12 VWhile engine cranking17g
(Engine start signal)0 – 1 VOther than above
Page 225 of 557
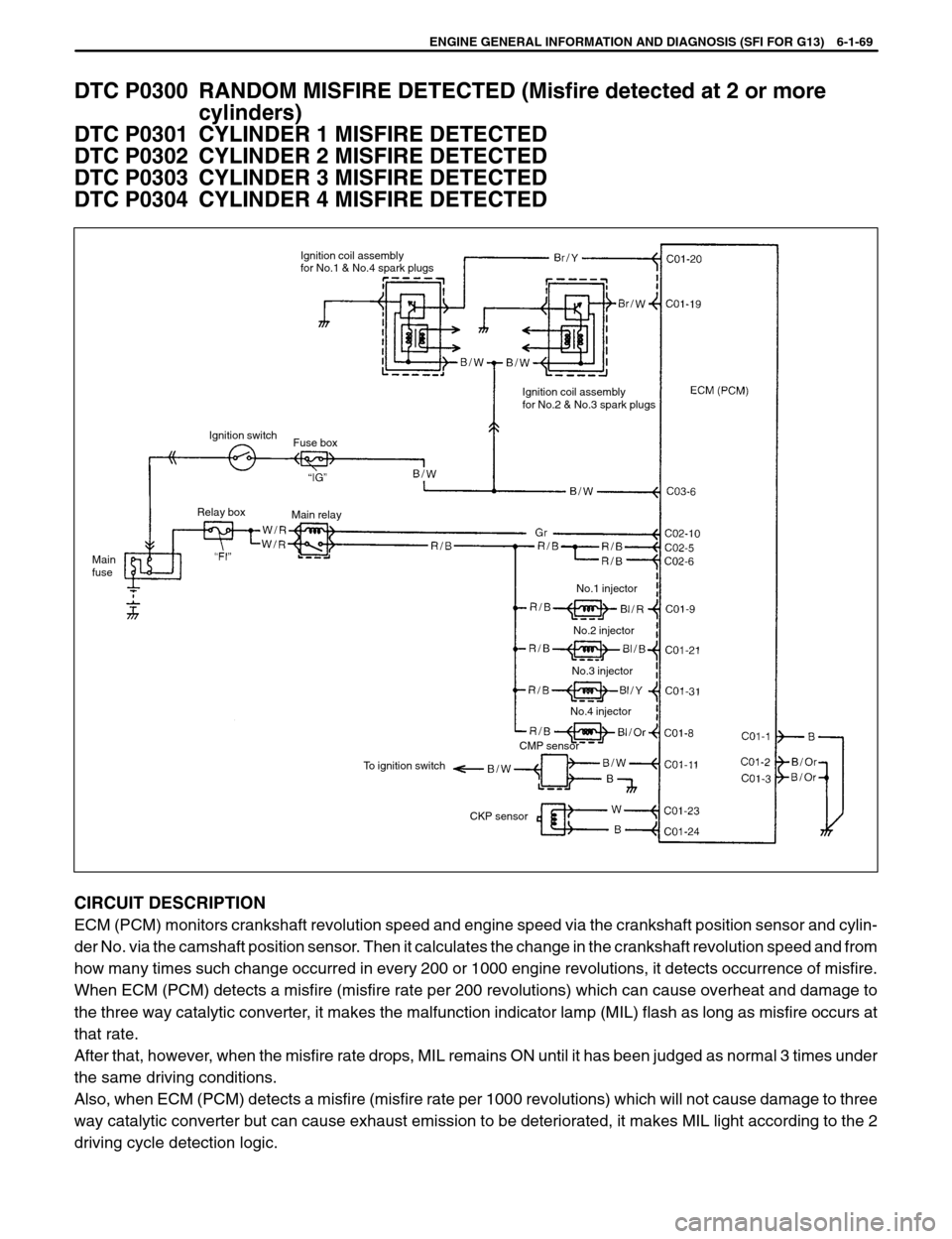
ENGINE GENERAL INFORMATION AND DIAGNOSIS (SFI FOR G13) 6-1-69
Ignition coil assembly
for No.1 & No.4 spark plugs
Ignition coil assembly
for No.2 & No.3 spark plugs
Ignition switch
Main relay
Main
fuseRelay box
To ignition switch
CKP sensorCMP sensorNo.1 injector
No.2 injector
No.3 injector
No.4 injector Fuse box
DTC P0300 RANDOM MISFIRE DETECTED (Misfire detected at 2 or more
cylinders)
DTC P0301 CYLINDER 1 MISFIRE DETECTED
DTC P0302 CYLINDER 2 MISFIRE DETECTED
DTC P0303 CYLINDER 3 MISFIRE DETECTED
DTC P0304 CYLINDER 4 MISFIRE DETECTED
CIRCUIT DESCRIPTION
ECM (PCM) monitors crankshaft revolution speed and engine speed via the crankshaft position sensor and cylin-
der No. via the camshaft position sensor. Then it calculates the change in the crankshaft revolution speed and from
how many times such change occurred in every 200 or 1000 engine revolutions, it detects occurrence of misfire.
When ECM (PCM) detects a misfire (misfire rate per 200 revolutions) which can cause overheat and damage to
the three way catalytic converter, it makes the malfunction indicator lamp (MIL) flash as long as misfire occurs at
that rate.
After that, however, when the misfire rate drops, MIL remains ON until it has been judged as normal 3 times under
the same driving conditions.
Also, when ECM (PCM) detects a misfire (misfire rate per 1000 revolutions) which will not cause damage to three
way catalytic converter but can cause exhaust emission to be deteriorated, it makes MIL light according to the 2
driving cycle detection logic.
Page 226 of 557
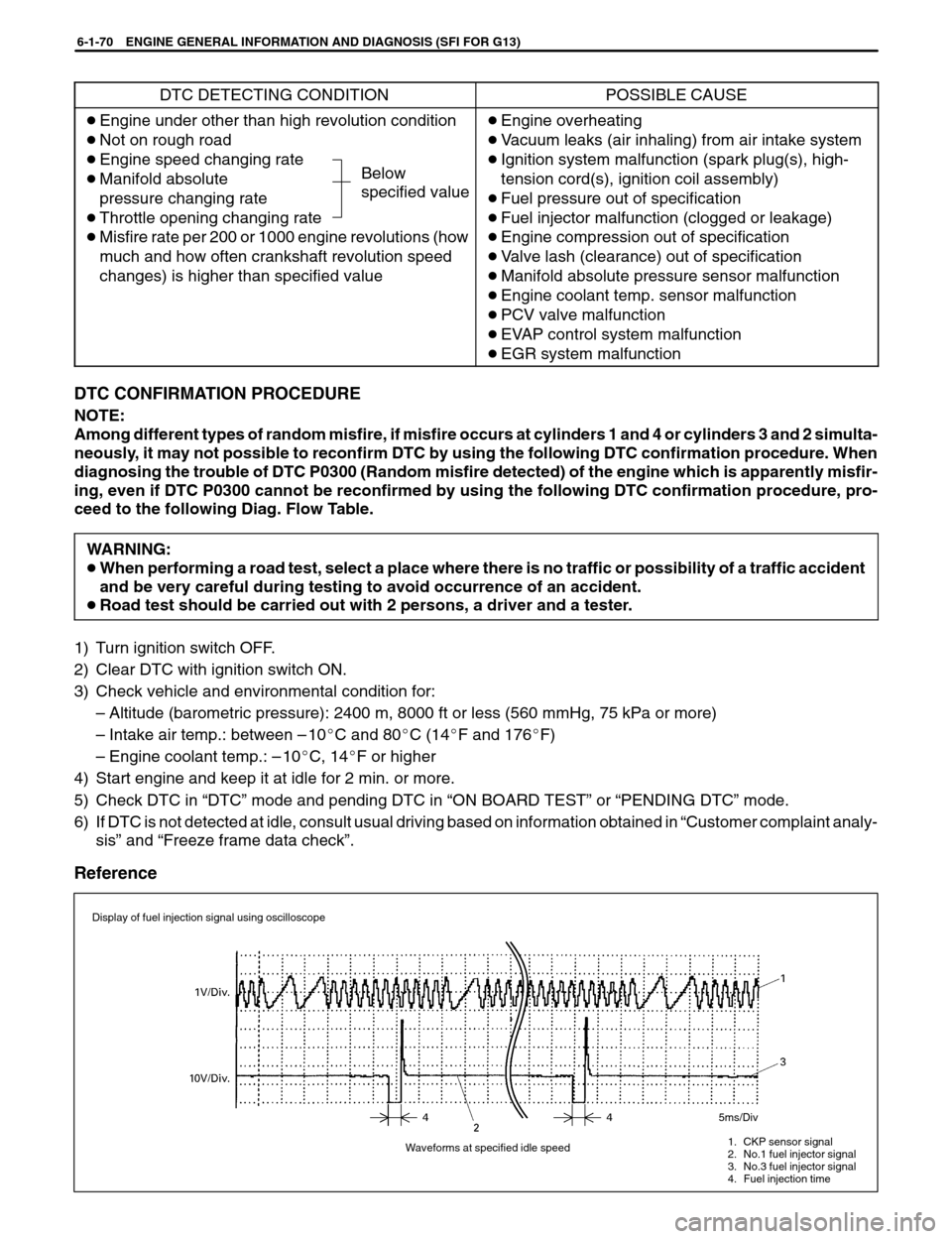
Below
specified value
6-1-70 ENGINE GENERAL INFORMATION AND DIAGNOSIS (SFI FOR G13)
1. CKP sensor signal
2. No.1 fuel injector signal
3. No.3 fuel injector signal
4. Fuel injection time
Display of fuel injection signal using oscilloscope
Waveforms at specified idle speed5ms/Div
DTC DETECTING CONDITIONPOSSIBLE CAUSE
Engine under other than high revolution condition
Not on rough road
Engine speed changing rate
Manifold absolute
pressure changing rate
Throttle opening changing rate
Misfire rate per 200 or 1000 engine revolutions (how
much and how often crankshaft revolution speed
changes) is higher than specified valueEngine overheating
Vacuum leaks (air inhaling) from air intake system
Ignition system malfunction (spark plug(s), high-
tension cord(s), ignition coil assembly)
Fuel pressure out of specification
Fuel injector malfunction (clogged or leakage)
Engine compression out of specification
Valve lash (clearance) out of specification
Manifold absolute pressure sensor malfunction
Engine coolant temp. sensor malfunction
PCV valve malfunction
EVAP control system malfunction
EGR system malfunction
DTC CONFIRMATION PROCEDURE
NOTE:
Among different types of random misfire, if misfire occurs at cylinders 1 and 4 or cylinders 3 and 2 simulta-
neously, it may not possible to reconfirm DTC by using the following DTC confirmation procedure. When
diagnosing the trouble of DTC P0300 (Random misfire detected) of the engine which is apparently misfir-
ing, even if DTC P0300 cannot be reconfirmed by using the following DTC confirmation procedure, pro-
ceed to the following Diag. Flow Table.
WARNING:
When performing a road test, select a place where there is no traffic or possibility of a traffic accident
and be very careful during testing to avoid occurrence of an accident.
Road test should be carried out with 2 persons, a driver and a tester.
1) Turn ignition switch OFF.
2) Clear DTC with ignition switch ON.
3) Check vehicle and environmental condition for:
–Altitude (barometric pressure): 2400 m, 8000 ft or less (560 mmHg, 75 kPa or more)
–Intake air temp.: between –10C and 80C (14F and 176F)
–Engine coolant temp.: –10C, 14F or higher
4) Start engine and keep it at idle for 2 min. or more.
5) Check DTC in “DTC” mode and pending DTC in “ON BOARD TEST” or “PENDING DTC” mode.
6) If DTC is not detected at idle, consult usual driving based on information obtained in “Customer complaint analy-
sis” and “Freeze frame data check”.
Reference
Page 229 of 557
ENGINE GENERAL INFORMATION AND DIAGNOSIS (SFI FOR G13) 6-1-73
Crankshaft
timing belt
pulleyCKP
sensor
Oscilloscope Waveforms
Waveforms at engine cranking (260 r/min) Waveforms at specified idle speed16 waives
for 10 signals13 waives for
10 signals
30 signal 30 signal 0.5 V / Div.
10 ms / Div.0.5 V / Div.
5 ms / Div.
DTC P0335 CRANKSHAFT POSITION (CKP) SENSOR CIRCUIT MALFUNCTION
CIRCUIT DESCRIPTION
DTC DETECTING CONDITIONPOSSIBLE CAUSE
NO CKP sensor signal for 2 seconds at engine
cranking.CKP sensor circuit open or short.
Crankshaft timing belt pulley teeth damaged.
CKP sensor malfunction, foreign material being
attached or improper installation.
ECM (PCM) malfunction.
Reference
Connect oscilloscope between terminals C01-23 (+) and C01-24 (–) of ECM (PCM) connector connected to ECM
(PCM) and check CKP sensor signal.
DTC CONFIRMATION PROCEDURE
1) Clear DTC and crank engine for 2 sec.
2) Select “DTC” mode on scan tool and check DTC.
Page 231 of 557
ENGINE GENERAL INFORMATION AND DIAGNOSIS (SFI FOR G13) 6-1-75
To ignition
switch
Signal rotor
on CamshaftCamshaft
position
sensor
Waveforms at specified idle speed
Oscilloscope Waveforms
2 V / Div.
Crank
angle20 ms / Div.
180
720
DTC P0340 CAMSHAFT POSITION (CMP) SENSOR CIRCUIT
MALFUNCTION
CIRCUIT DESCRIPTION
DTC DETECTING CONDITIONPOSSIBLE CAUSE
No CMP sensor signal during engine running
(CKP sensor signal is inputted).CMP sensor circuit open or short.
Signal rotor teeth damaged.
CMP sensor malfunction, foreign material being
attached or improper installation.
ECM (PCM) malfunction.
Reference
Connect oscilloscope between terminals C01-11 of ECM (PCM) connector connected to ECM (PCM) and body
ground and check CKP sensor signal.
DTC CONFIRMATION PROCEDURE
1) Clear DTC.
2) Start engine and keep it at idle for 1 min.
3) Select “DTC” mode on scan tool and check DTC.
Page 250 of 557
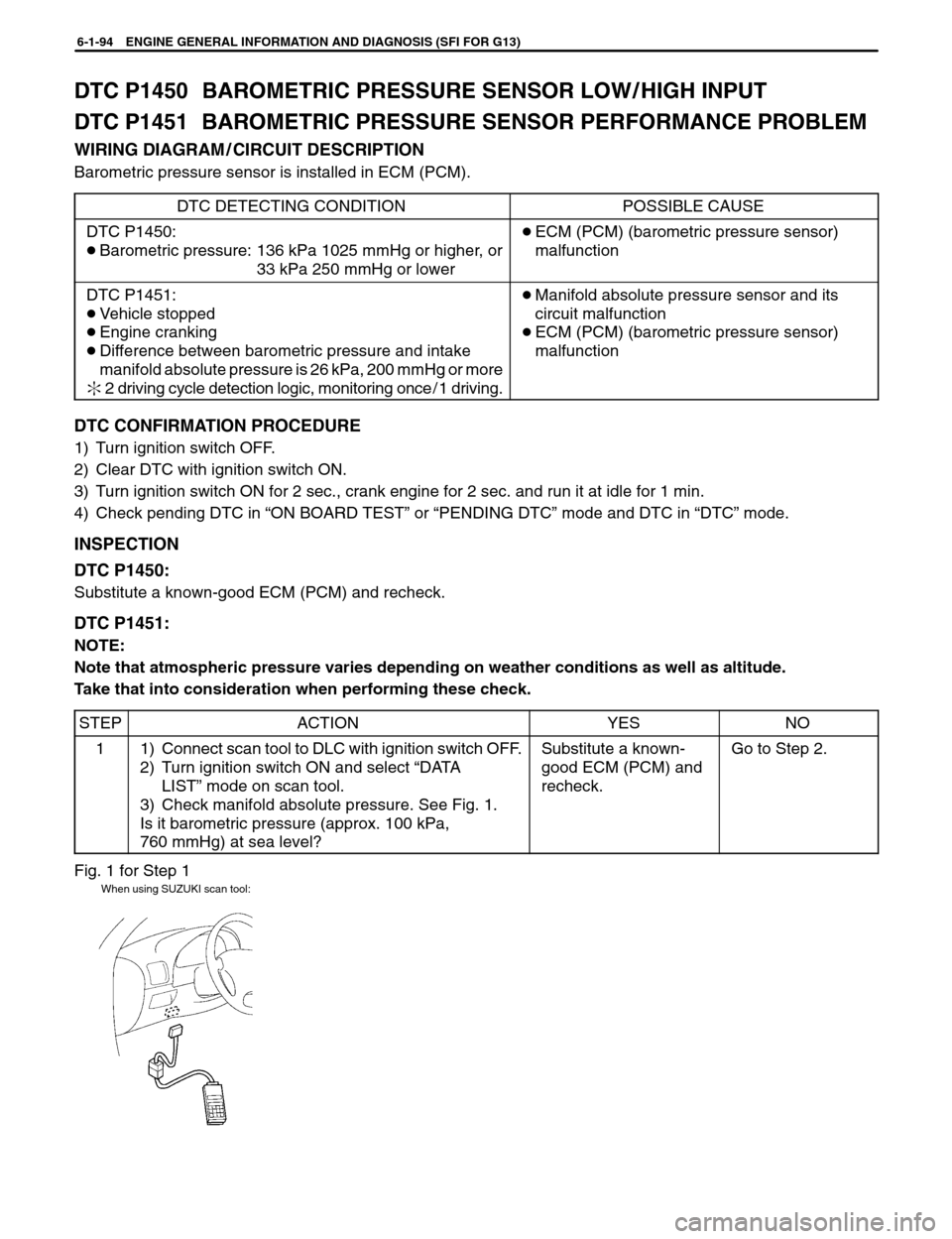
6-1-94 ENGINE GENERAL INFORMATION AND DIAGNOSIS (SFI FOR G13)
Fig. 1 for Step 1
When using SUZUKI scan tool:
DTC P1450 BAROMETRIC PRESSURE SENSOR LOW / HIGH INPUT
DTC P1451 BAROMETRIC PRESSURE SENSOR PERFORMANCE PROBLEM
WIRING DIAGRAM / CIRCUIT DESCRIPTION
Barometric pressure sensor is installed in ECM (PCM).
DTC DETECTING CONDITION
POSSIBLE CAUSE
DTC P1450:
Barometric pressure: 136 kPa 1025 mmHg or higher, or
33 kPa 250 mmHg or lowerECM (PCM) (barometric pressure sensor)
malfunction
DTC P1451:
Vehicle stopped
Engine cranking
Difference between barometric pressure and intake
manifold absolute pressure is 26 kPa, 200 mmHg or more
2 driving cycle detection logic, monitoring once / 1 driving.Manifold absolute pressure sensor and its
circuit malfunction
ECM (PCM) (barometric pressure sensor)
malfunction
DTC CONFIRMATION PROCEDURE
1) Turn ignition switch OFF.
2) Clear DTC with ignition switch ON.
3) Turn ignition switch ON for 2 sec., crank engine for 2 sec. and run it at idle for 1 min.
4) Check pending DTC in “ON BOARD TEST” or “PENDING DTC” mode and DTC in “DTC” mode.
INSPECTION
DTC P1450:
Substitute a known-good ECM (PCM) and recheck.
DTC P1451:
NOTE:
Note that atmospheric pressure varies depending on weather conditions as well as altitude.
Take that into consideration when performing these check.
STEP
ACTIONYESNO
11) Connect scan tool to DLC with ignition switch OFF.
2) Turn ignition switch ON and select “DATA
LIST” mode on scan tool.
3) Check manifold absolute pressure. See Fig. 1.
Is it barometric pressure (approx. 100 kPa,
760 mmHg) at sea level?Substitute a known-
good ECM (PCM) and
recheck.Go to Step 2.
Page 252 of 557
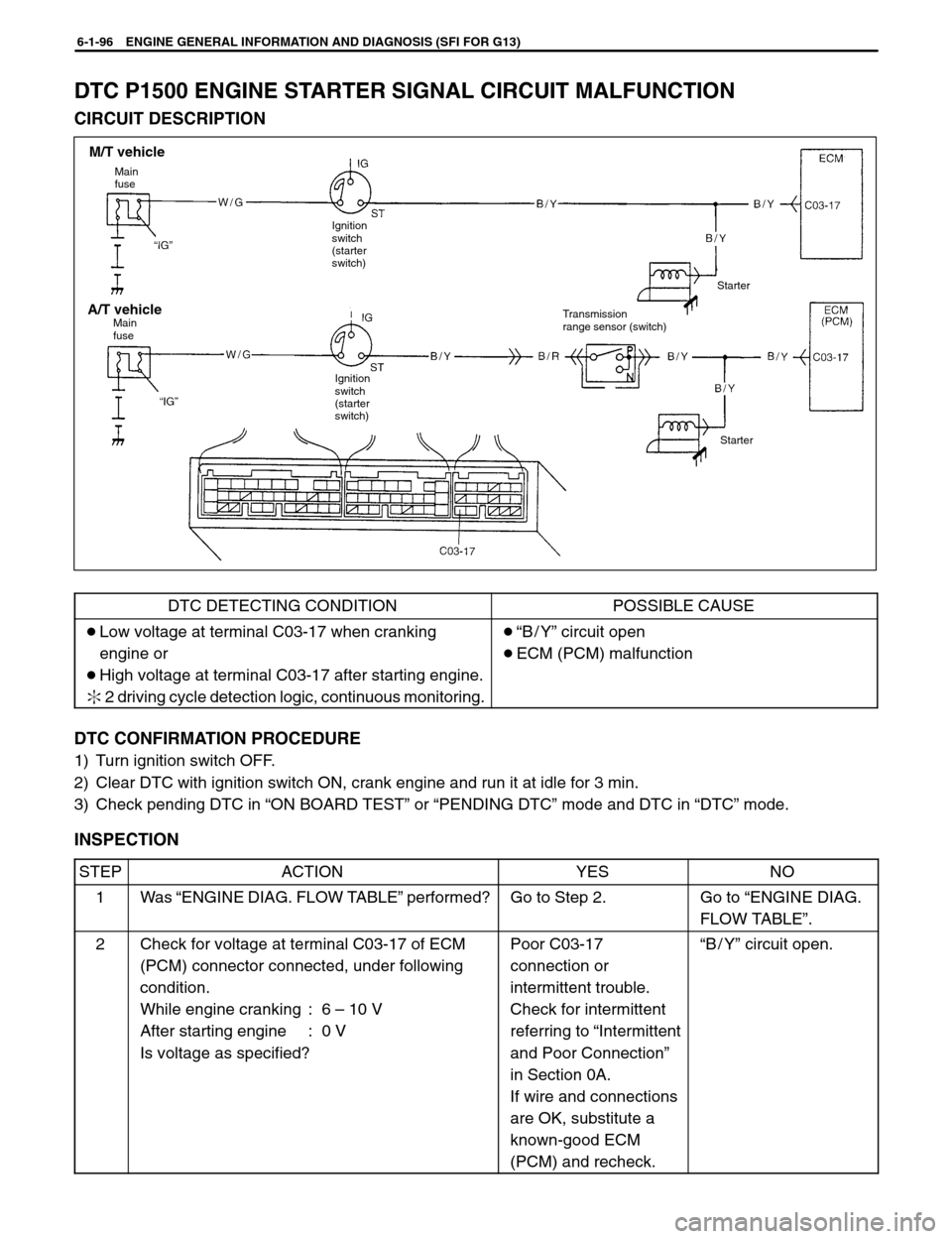
6-1-96 ENGINE GENERAL INFORMATION AND DIAGNOSIS (SFI FOR G13)
Main
fuse
M/T vehicle
A/T vehicle
Ignition
switch
(starter
switch)
Starter
Starter Transmission
range sensor (switch) Main
fuse
Ignition
switch
(starter
switch)
DTC P1500 ENGINE STARTER SIGNAL CIRCUIT MALFUNCTION
CIRCUIT DESCRIPTION
DTC DETECTING CONDITIONPOSSIBLE CAUSE
Low voltage at terminal C03-17 when cranking
engine or
High voltage at terminal C03-17 after starting engine.
2 driving cycle detection logic, continuous monitoring.“B/Y” circuit open
ECM (PCM) malfunction
DTC CONFIRMATION PROCEDURE
1) Turn ignition switch OFF.
2) Clear DTC with ignition switch ON, crank engine and run it at idle for 3 min.
3) Check pending DTC in “ON BOARD TEST” or “PENDING DTC” mode and DTC in “DTC” mode.
INSPECTION
STEPACTIONYESNO
1Was “ENGINE DIAG. FLOW TABLE” performed?Go to Step 2.Go to “ENGINE DIAG.
FLOW TABLE”.
2Check for voltage at terminal C03-17 of ECM
(PCM) connector connected, under following
condition.
While engine cranking : 6 – 10 V
After starting engine : 0 V
Is voltage as specified?Poor C03-17
connection or
intermittent trouble.
Check for intermittent
referring to “Intermittent
and Poor Connection”
in Section 0A.
If wire and connections
are OK, substitute a
known-good ECM
(PCM) and recheck.“B/Y” circuit open.
Page 335 of 557
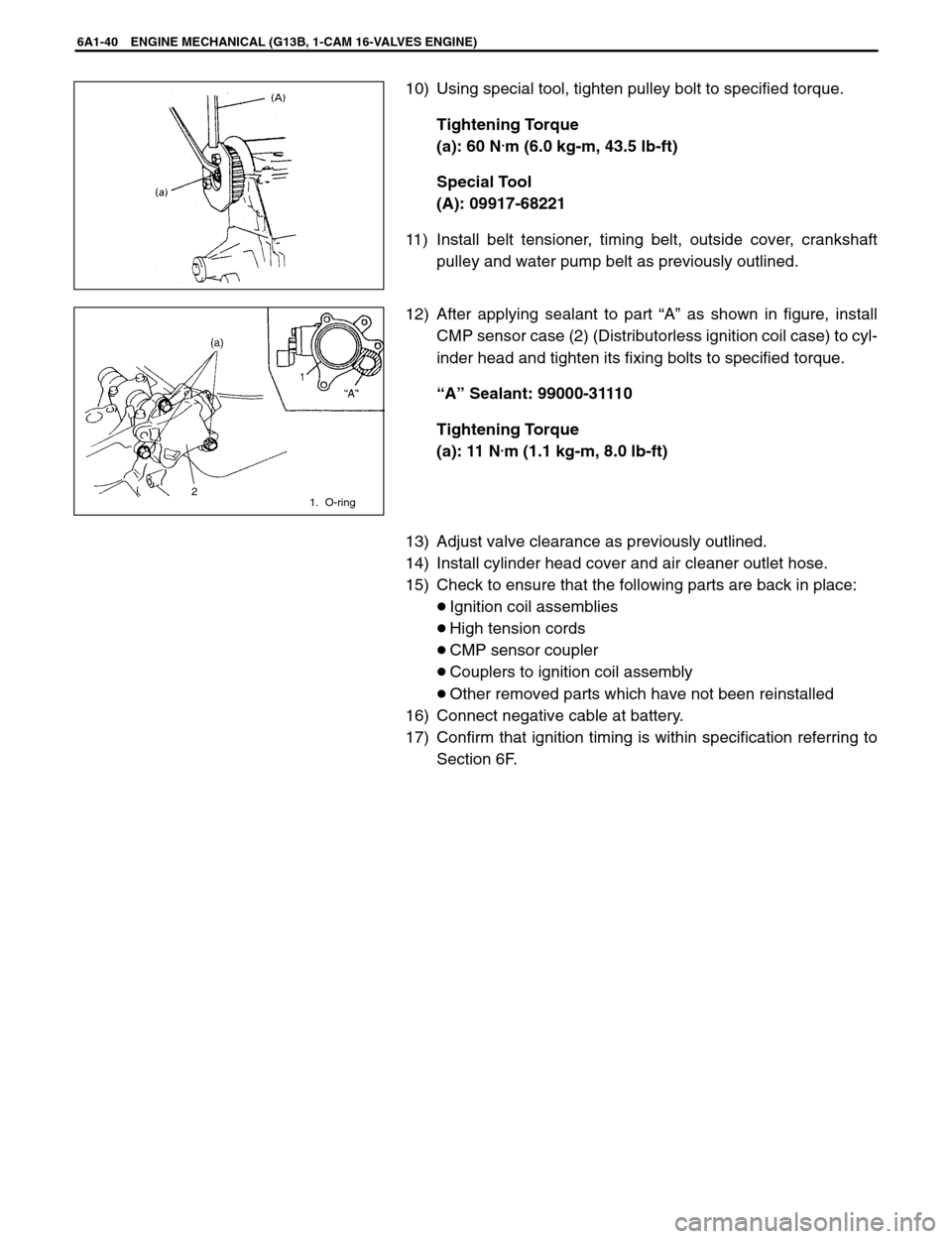
6A1-40 ENGINE MECHANICAL (G13B, 1-CAM 16-VALVES ENGINE)
1. O-ring2
10) Using special tool, tighten pulley bolt to specified torque.
Tightening Torque
(a): 60 N
.m (6.0 kg-m, 43.5 lb-ft)
Special Tool
(A): 09917-68221
11) Install belt tensioner, timing belt, outside cover, crankshaft
pulley and water pump belt as previously outlined.
12) After applying sealant to part “A” as shown in figure, install
CMP sensor case (2) (Distributorless ignition coil case) to cyl-
inder head and tighten its fixing bolts to specified torque.
“A” Sealant: 99000-31110
Tightening Torque
(a): 11 N
.m (1.1 kg-m, 8.0 lb-ft)
13) Adjust valve clearance as previously outlined.
14) Install cylinder head cover and air cleaner outlet hose.
15) Check to ensure that the following parts are back in place:
Ignition coil assemblies
High tension cords
CMP sensor coupler
Couplers to ignition coil assembly
Other removed parts which have not been reinstalled
16) Connect negative cable at battery.
17) Confirm that ignition timing is within specification referring to
Section 6F.