Page 440 of 557
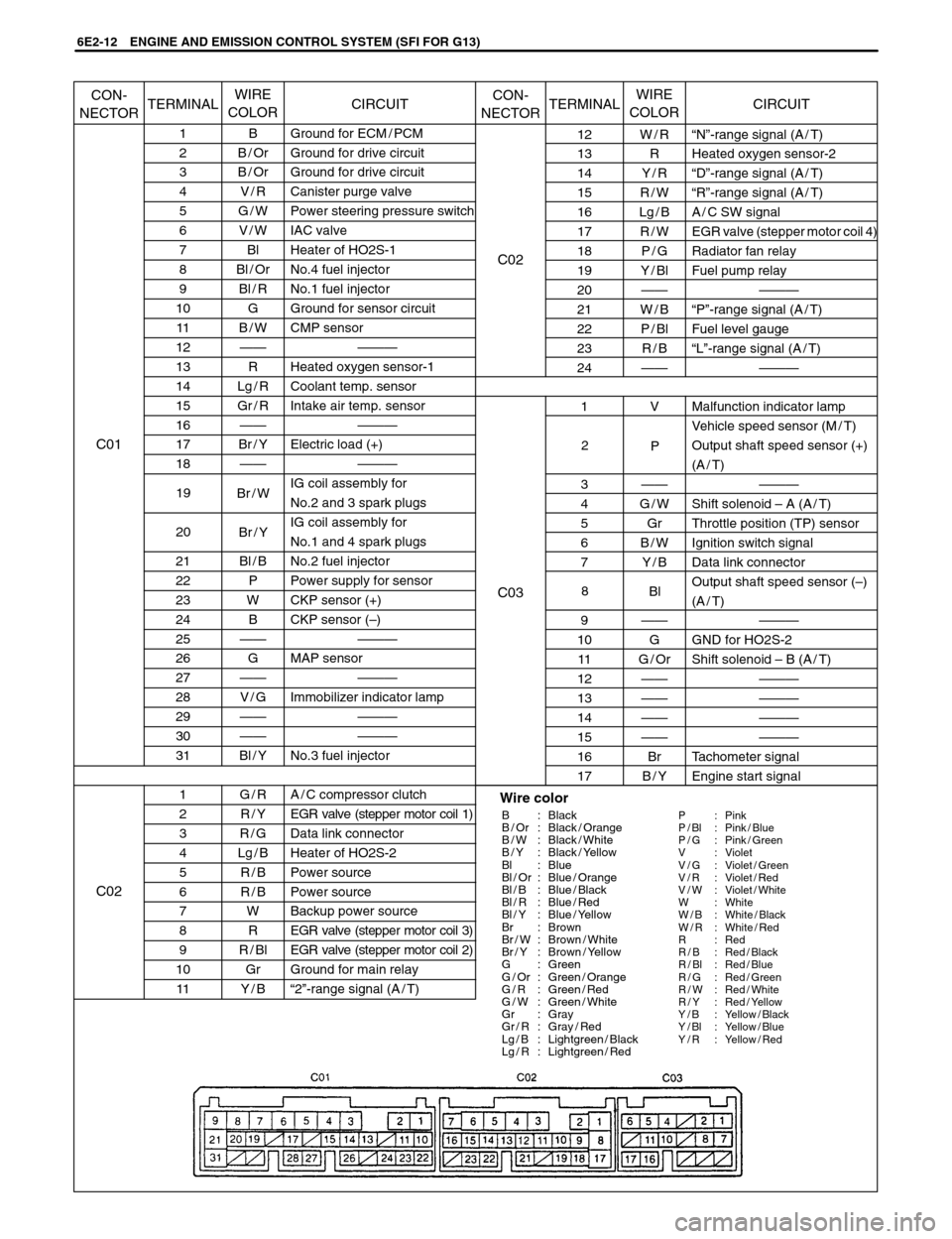
12 W / R “N”-range signal (A / T)
13 R Heated oxygen sensor-2
14 Y / R “D”-range signal (A / T)
15 R / W “R”-range signal (A / T)
16 Lg / B A / C SW signal
17 R / W EGR valve (stepper motor coil 4)
18 P / G Radiator fan relay
19 Y / Bl Fuel pump relay
20 —— ———
21 W / B “P”-range signal (A / T)
22 P / Bl Fuel level gauge
23 R / B “L”-range signal (A / T)
24 —— ———
1 V Malfunction indicator lamp
Vehicle speed sensor (M / T)
Output shaft speed sensor (+)
(A / T)
3 —— ———
4 G / W Shift solenoid – A (A / T)
5 Gr Throttle position (TP) sensor
6 B / W Ignition switch signal
7 Y / B Data link connector
Output shaft speed sensor (–)
(A / T)
9 —— ———
10 G GND for HO2S-2
11 G / Or Shift solenoid – B (A / T)
12 —— ———
13 —— ———
14 —— ———
15 —— ———
16 Br Tachometer signal
17 B / Y Engine start signal
CON-
NECTORTERMINALWIRE
COLORCIRCUITCON-
NECTORTERMINALWIRE
COLORCIRCUIT
20
Br / Y 19
Br / W
C02 C01C02
C03
Wire color
B : Black
B / Or : Black / Orange
B / W : Black / White
B / Y : Black / Yellow
Bl : Blue
Bl / Or : Blue / Orange
Bl / B : Blue / Black
Bl / R : Blue / Red
Bl / Y : Blue / Yellow
Br : Brown
Br / W : Brown / White
Br / Y : Brown / Yellow
G : Green
G / Or : Green / Orange
G / R : Green / Red
G / W : Green / White
Gr : Gray
Gr / R : Gray / Red
Lg / B : Lightgreen / Black
Lg / R : Lightgreen / RedP : Pink
P / Bl : Pink / Blue
P / G : Pink / Green
V : Violet
V / G : Violet / Green
V / R : Violet / Red
V / W : Violet / White
W : White
W / B : White / Black
W / R : White / Red
R : Red
R / B : Red / Black
R / Bl : Red / Blue
R / G : Red / Green
R / W : Red / White
R / Y : Red / Yellow
Y / B : Yellow / Black
Y / Bl : Yellow / Blue
Y / R : Yellow / Red
2
P
8
Bl
6E2-12 ENGINE AND EMISSION CONTROL SYSTEM (SFI FOR G13)
1 B Ground for ECM / PCM
2 B / Or Ground for drive circuit
3 B / Or Ground for drive circuit
4 V / R Canister purge valve
5 G / W Power steering pressure switch
6 V / W IAC valve
7 Bl Heater of HO2S-1
8 Bl / Or No.4 fuel injector
9 Bl / R No.1 fuel injector
10 G Ground for sensor circuit
11 B / W CMP sensor
12 —— ———
13 R Heated oxygen sensor-1
14 Lg / R Coolant temp. sensor
15 Gr / R Intake air temp. sensor
16 —— ———
17 Br / Y Electric load (+)
18 —— ———
IG coil assembly for
No.2 and 3 spark plugs
IG coil assembly for
No.1 and 4 spark plugs
21 Bl / B No.2 fuel injector
22 P Power supply for sensor
23 W CKP sensor (+)
24 B CKP sensor (–)
25 —— ———
26 G MAP sensor
27 —— ———
28 V / G Immobilizer indicator lamp
29 —— ———
30 —— ———
31 Bl / Y No.3 fuel injector
1 G / R A / C compressor clutch
2 R / Y EGR valve (stepper motor coil 1)
3 R / G Data link connector
4 Lg / B Heater of HO2S-2
5 R / B Power source
6 R / B Power source
7 W Backup power source
8 R EGR valve (stepper motor coil 3)
9 R / Bl EGR valve (stepper motor coil 2)
10 Gr Ground for main relay
11 Y / B “2”-range signal (A / T)
Page 441 of 557
1. Accelerator cable
3. Lock nut
ENGINE AND EMISSION CONTROL SYSTEM (SFI FOR G13) 6E2-13
ON-VEHICLE SERVICE
ACCELERATOR CABLE ADJUSTMENT
1) With throttle valve closed, check accelerator pedal play which
should be within following specification.
Pedal play “a”: 2 – 7 mm (0.08 – 0.27 in.)
If measured value is out of specification, adjust it to specification
with cable adjusting nut (2).
2) With accelerator pedal depressed fully (1), check clearance be-
tween throttle lever (2) and lever stopper (3) (throttle body)
which should be within following specification.
Clearance “b” : 0.5 – 2.0 mm (0.02 – 0.07 in.)
(With pedal
depressed fully)
If measured value is out of specification, adjust it to specification
with cable adjusting nut.
Page 442 of 557
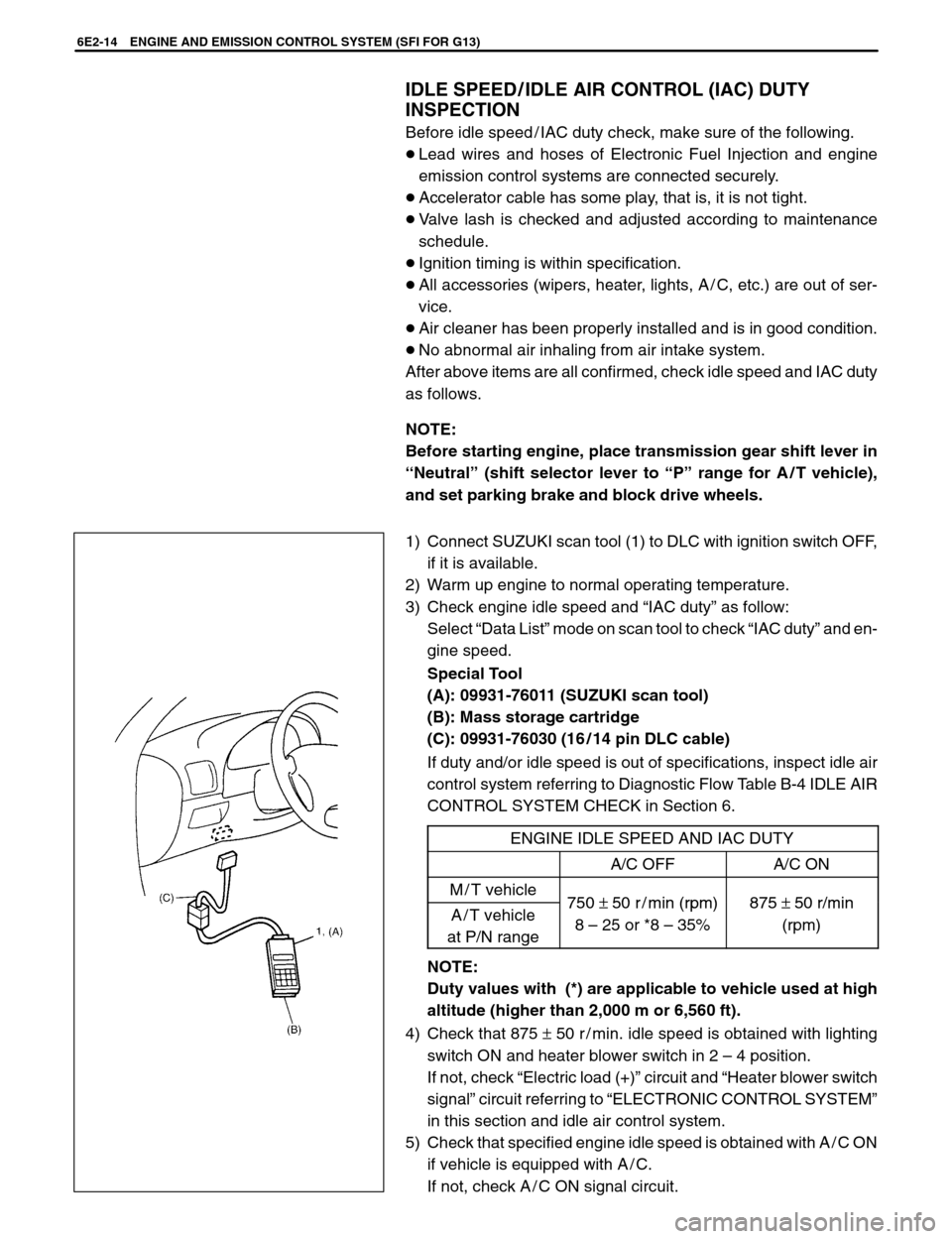
6E2-14 ENGINE AND EMISSION CONTROL SYSTEM (SFI FOR G13)
IDLE SPEED / IDLE AIR CONTROL (IAC) DUTY
INSPECTION
Before idle speed / IAC duty check, make sure of the following.
Lead wires and hoses of Electronic Fuel Injection and engine
emission control systems are connected securely.
Accelerator cable has some play, that is, it is not tight.
Valve lash is checked and adjusted according to maintenance
schedule.
Ignition timing is within specification.
All accessories (wipers, heater, lights, A / C, etc.) are out of ser-
vice.
Air cleaner has been properly installed and is in good condition.
No abnormal air inhaling from air intake system.
After above items are all confirmed, check idle speed and IAC duty
as follows.
NOTE:
Before starting engine, place transmission gear shift lever in
“Neutral” (shift selector lever to “P” range for A / T vehicle),
and set parking brake and block drive wheels.
1) Connect SUZUKI scan tool (1) to DLC with ignition switch OFF,
if it is available.
2) Warm up engine to normal operating temperature.
3) Check engine idle speed and “IAC duty” as follow:
Select “Data List” mode on scan tool to check “IAC duty” and en-
gine speed.
Special Tool
(A): 09931-76011 (SUZUKI scan tool)
(B): Mass storage cartridge
(C): 09931-76030 (16 / 14 pin DLC cable)
If duty and/or idle speed is out of specifications, inspect idle air
control system referring to Diagnostic Flow Table B-4 IDLE AIR
CONTROL SYSTEM CHECK in Section 6.
ENGINE IDLE SPEED AND IAC DUTY
A/C OFFA/C ON
M / T vehicle750±50 r / min (rpm)875±50 r/minA / T vehicle
at P/N range750 ±50 r/min (rpm)
8 – 25 or *8 – 35%
875 ±50 r/min
(rpm)
NOTE:
Duty values with (*) are applicable to vehicle used at high
altitude (higher than 2,000 m or 6,560 ft).
4) Check that 875 ± 50 r / min. idle speed is obtained with lighting
switch ON and heater blower switch in 2 – 4 position.
If not, check “Electric load (+)” circuit and “Heater blower switch
signal” circuit referring to “ELECTRONIC CONTROL SYSTEM”
in this section and idle air control system.
5) Check that specified engine idle speed is obtained with A / C ON
if vehicle is equipped with A / C.
If not, check A / C ON signal circuit.
Page 443 of 557
ENGINE AND EMISSION CONTROL SYSTEM (SFI FOR G13) 6E2-15
CAUTION:
Do not disassemble IAC
valve. Disassembly spoils
its original performanceCAUTION:
Do not remove or adjust
throttle stop screw as it is
factory adjusted precisely
1. Throttle body
2. Throttle stop screw
3. TP sensor
4. O-ring
5. Idle air control valve
6. IAC valve screws : Tightening torque
: Do not reuse
AIR INTAKE SYSTEM
THROTTLE BODY
On-Vehicle Inspection
Check that throttle valve lever (1) moves smoothly.
Removal
1) Disconnect negative cable at battery.
2) Drain cooling system.
3) Disconnect accelerator cable (1) from throttle body.
4) Disconnect air cleaner outlet hose (1) from throttle body.
Page 444 of 557
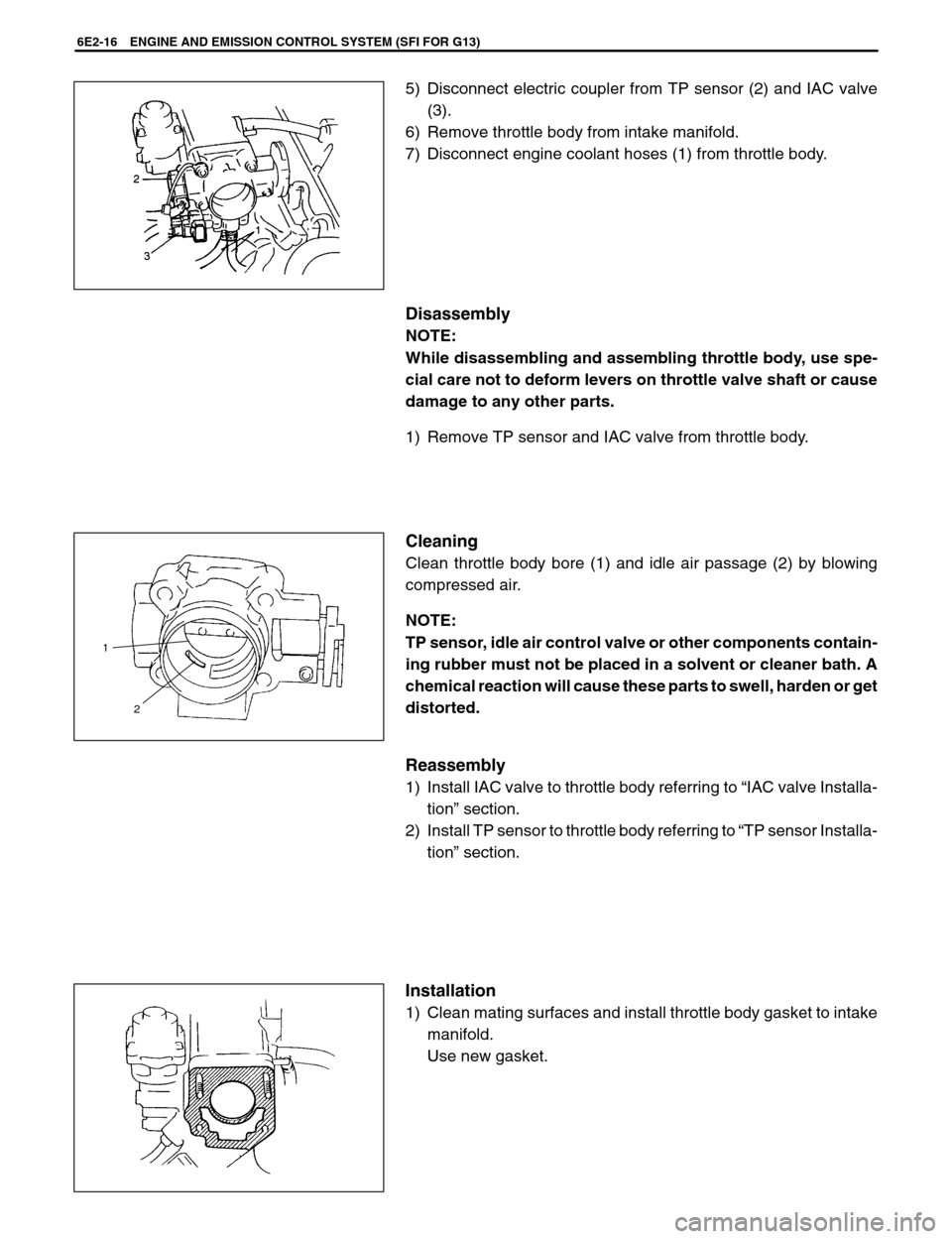
6E2-16 ENGINE AND EMISSION CONTROL SYSTEM (SFI FOR G13)
1
2
5) Disconnect electric coupler from TP sensor (2) and IAC valve
(3).
6) Remove throttle body from intake manifold.
7) Disconnect engine coolant hoses (1) from throttle body.
Disassembly
NOTE:
While disassembling and assembling throttle body, use spe-
cial care not to deform levers on throttle valve shaft or cause
damage to any other parts.
1) Remove TP sensor and IAC valve from throttle body.
Cleaning
Clean throttle body bore (1) and idle air passage (2) by blowing
compressed air.
NOTE:
TP sensor, idle air control valve or other components contain-
ing rubber must not be placed in a solvent or cleaner bath. A
chemical reaction will cause these parts to swell, harden or get
distorted.
Reassembly
1) Install IAC valve to throttle body referring to “IAC valve Installa-
tion” section.
2) Install TP sensor to throttle body referring to “TP sensor Installa-
tion” section.
Installation
1) Clean mating surfaces and install throttle body gasket to intake
manifold.
Use new gasket.
Page 445 of 557
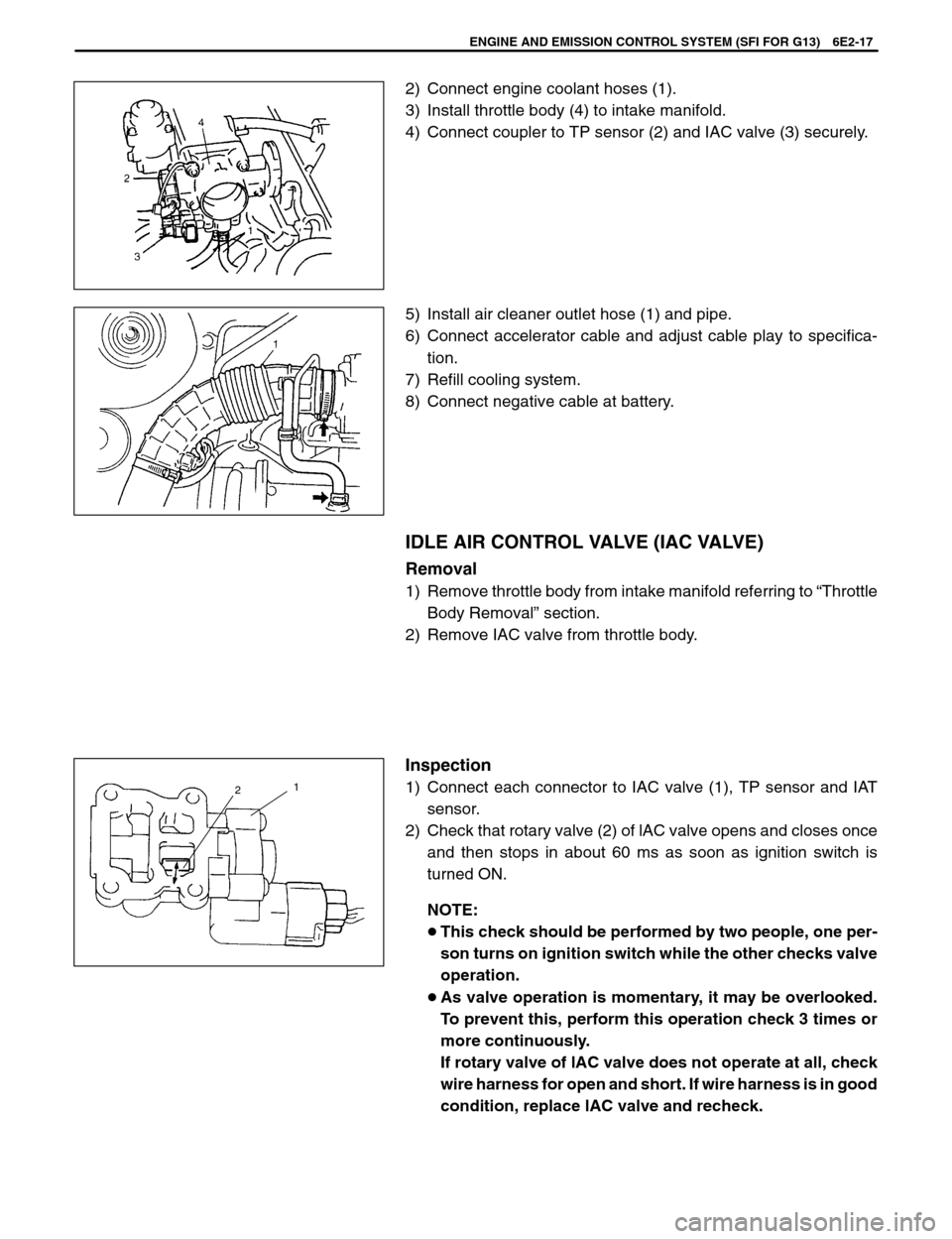
21
ENGINE AND EMISSION CONTROL SYSTEM (SFI FOR G13) 6E2-17
2) Connect engine coolant hoses (1).
3) Install throttle body (4) to intake manifold.
4) Connect coupler to TP sensor (2) and IAC valve (3) securely.
5) Install air cleaner outlet hose (1) and pipe.
6) Connect accelerator cable and adjust cable play to specifica-
tion.
7) Refill cooling system.
8) Connect negative cable at battery.
IDLE AIR CONTROL VALVE (IAC VALVE)
Removal
1) Remove throttle body from intake manifold referring to “Throttle
Body Removal” section.
2) Remove IAC valve from throttle body.
Inspection
1) Connect each connector to IAC valve (1), TP sensor and IAT
sensor.
2) Check that rotary valve (2) of lAC valve opens and closes once
and then stops in about 60 ms as soon as ignition switch is
turned ON.
NOTE:
This check should be performed by two people, one per-
son turns on ignition switch while the other checks valve
operation.
As valve operation is momentary, it may be overlooked.
To prevent this, perform this operation check 3 times or
more continuously.
If rotary valve of lAC valve does not operate at all, check
wire harness for open and short. If wire harness is in good
condition, replace lAC valve and recheck.
Page 446 of 557
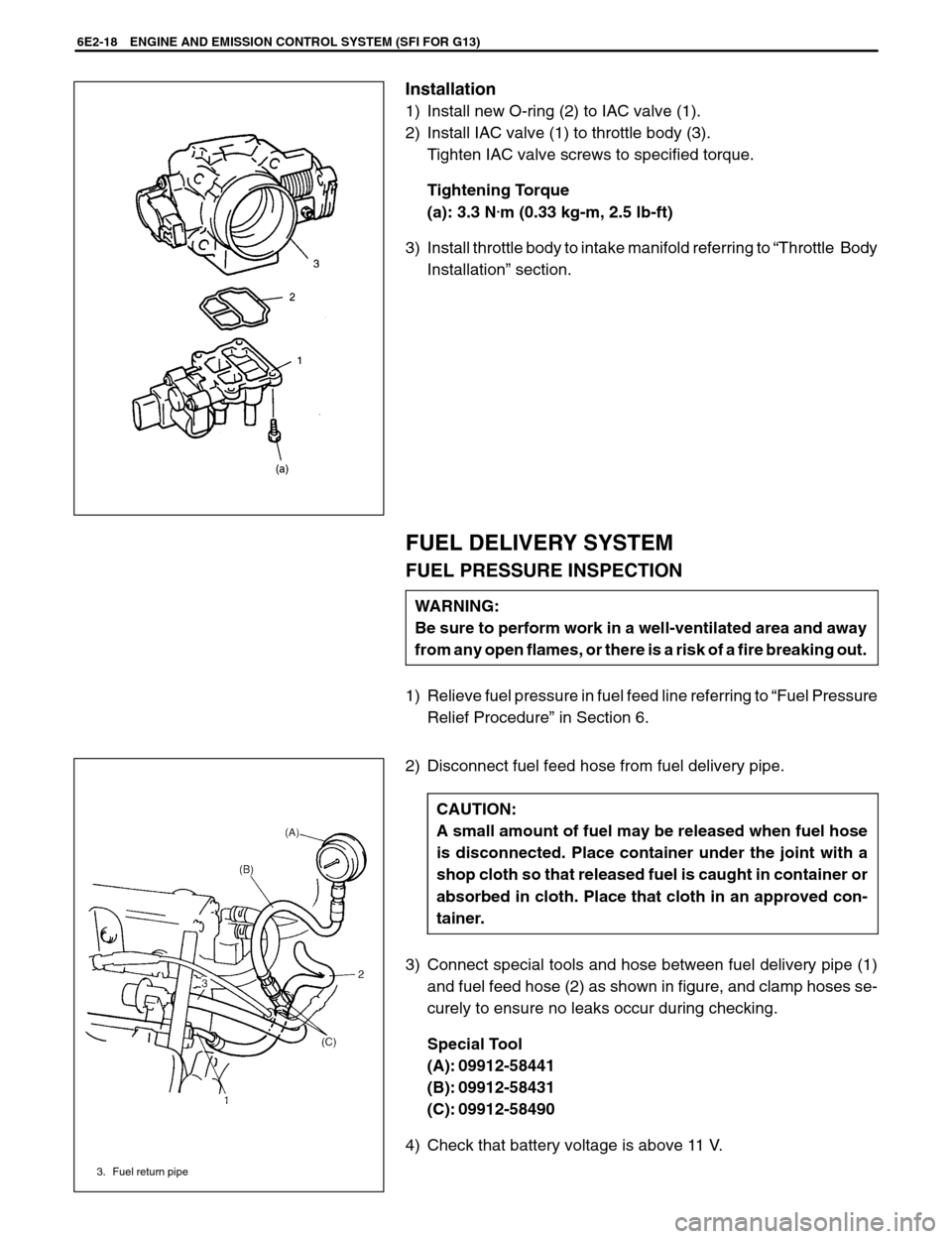
3. Fuel return pipe
6E2-18 ENGINE AND EMISSION CONTROL SYSTEM (SFI FOR G13)
Installation
1) Install new O-ring (2) to IAC valve (1).
2) Install IAC valve (1) to throttle body (3).
Tighten IAC valve screws to specified torque.
Tightening Torque
(a): 3.3 N
.m (0.33 kg-m, 2.5 lb-ft)
3) Install throttle body to intake manifold referring to “Throttle Body
Installation” section.
FUEL DELIVERY SYSTEM
FUEL PRESSURE INSPECTION
WARNING:
Be sure to perform work in a well-ventilated area and away
from any open flames, or there is a risk of a fire breaking out.
1) Relieve fuel pressure in fuel feed line referring to “Fuel Pressure
Relief Procedure” in Section 6.
2) Disconnect fuel feed hose from fuel delivery pipe.
CAUTION:
A small amount of fuel may be released when fuel hose
is disconnected. Place container under the joint with a
shop cloth so that released fuel is caught in container or
absorbed in cloth. Place that cloth in an approved con-
tainer.
3) Connect special tools and hose between fuel delivery pipe (1)
and fuel feed hose (2) as shown in figure, and clamp hoses se-
curely to ensure no leaks occur during checking.
Special Tool
(A): 09912-58441
(B): 09912-58431
(C): 09912-58490
4) Check that battery voltage is above 11 V.
Page 456 of 557
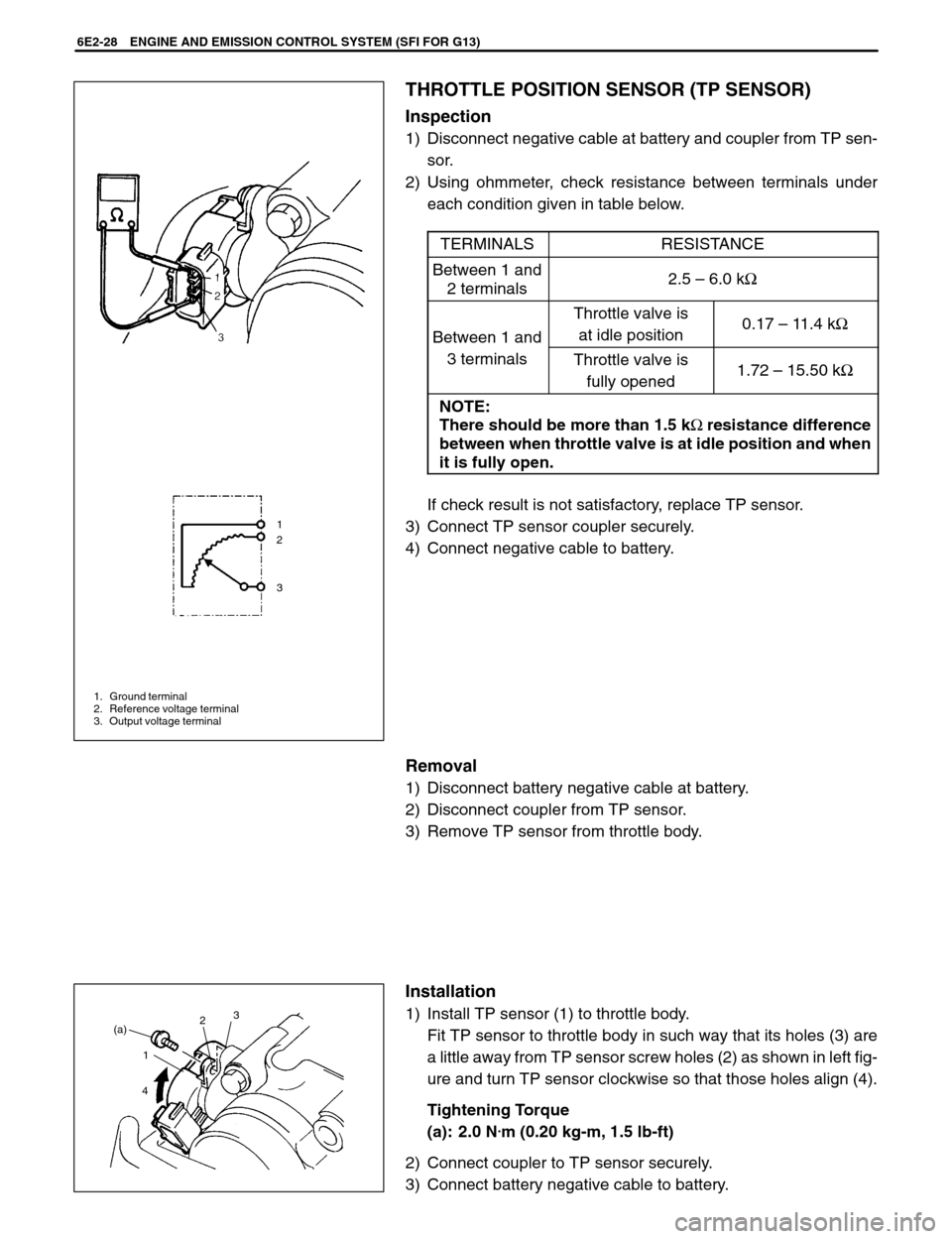
1
2
3
1. Ground terminal
2. Reference voltage terminal
3. Output voltage terminal
(a)
1
23
4
6E2-28 ENGINE AND EMISSION CONTROL SYSTEM (SFI FOR G13)
THROTTLE POSITION SENSOR (TP SENSOR)
Inspection
1) Disconnect negative cable at battery and coupler from TP sen-
sor.
2) Using ohmmeter, check resistance between terminals under
each condition given in table below.
TERMINALS
RESISTANCE
Between 1 and
2 terminals2.5 – 6.0 kΩ
Between 1 and
Throttle valve is
at idle position0.17 – 11.4 kΩ
3 terminalsThrottle valve is
fully opened1.72 – 15.50 kΩ
NOTE:
There should be more than 1.5 kΩ resistance difference
between when throttle valve is at idle position and when
it is fully open.
If check result is not satisfactory, replace TP sensor.
3) Connect TP sensor coupler securely.
4) Connect negative cable to battery.
Removal
1) Disconnect battery negative cable at battery.
2) Disconnect coupler from TP sensor.
3) Remove TP sensor from throttle body.
Installation
1) Install TP sensor (1) to throttle body.
Fit TP sensor to throttle body in such way that its holes (3) are
a little away from TP sensor screw holes (2) as shown in left fig-
ure and turn TP sensor clockwise so that those holes align (4).
Tightening Torque
(a): 2.0 N
.m (0.20 kg-m, 1.5 lb-ft)
2) Connect coupler to TP sensor securely.
3) Connect battery negative cable to battery.