Page 444 of 557
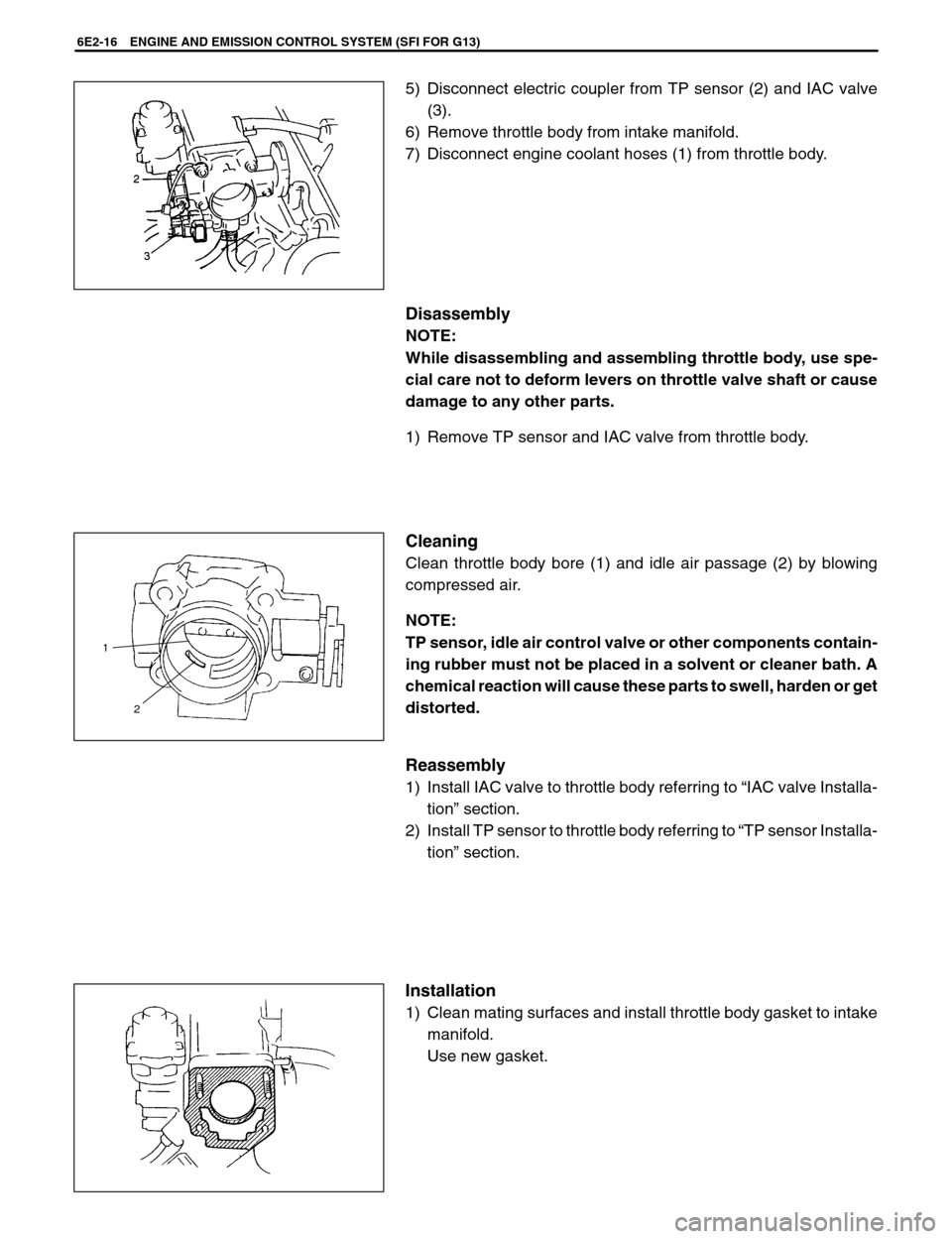
6E2-16 ENGINE AND EMISSION CONTROL SYSTEM (SFI FOR G13)
1
2
5) Disconnect electric coupler from TP sensor (2) and IAC valve
(3).
6) Remove throttle body from intake manifold.
7) Disconnect engine coolant hoses (1) from throttle body.
Disassembly
NOTE:
While disassembling and assembling throttle body, use spe-
cial care not to deform levers on throttle valve shaft or cause
damage to any other parts.
1) Remove TP sensor and IAC valve from throttle body.
Cleaning
Clean throttle body bore (1) and idle air passage (2) by blowing
compressed air.
NOTE:
TP sensor, idle air control valve or other components contain-
ing rubber must not be placed in a solvent or cleaner bath. A
chemical reaction will cause these parts to swell, harden or get
distorted.
Reassembly
1) Install IAC valve to throttle body referring to “IAC valve Installa-
tion” section.
2) Install TP sensor to throttle body referring to “TP sensor Installa-
tion” section.
Installation
1) Clean mating surfaces and install throttle body gasket to intake
manifold.
Use new gasket.
Page 445 of 557
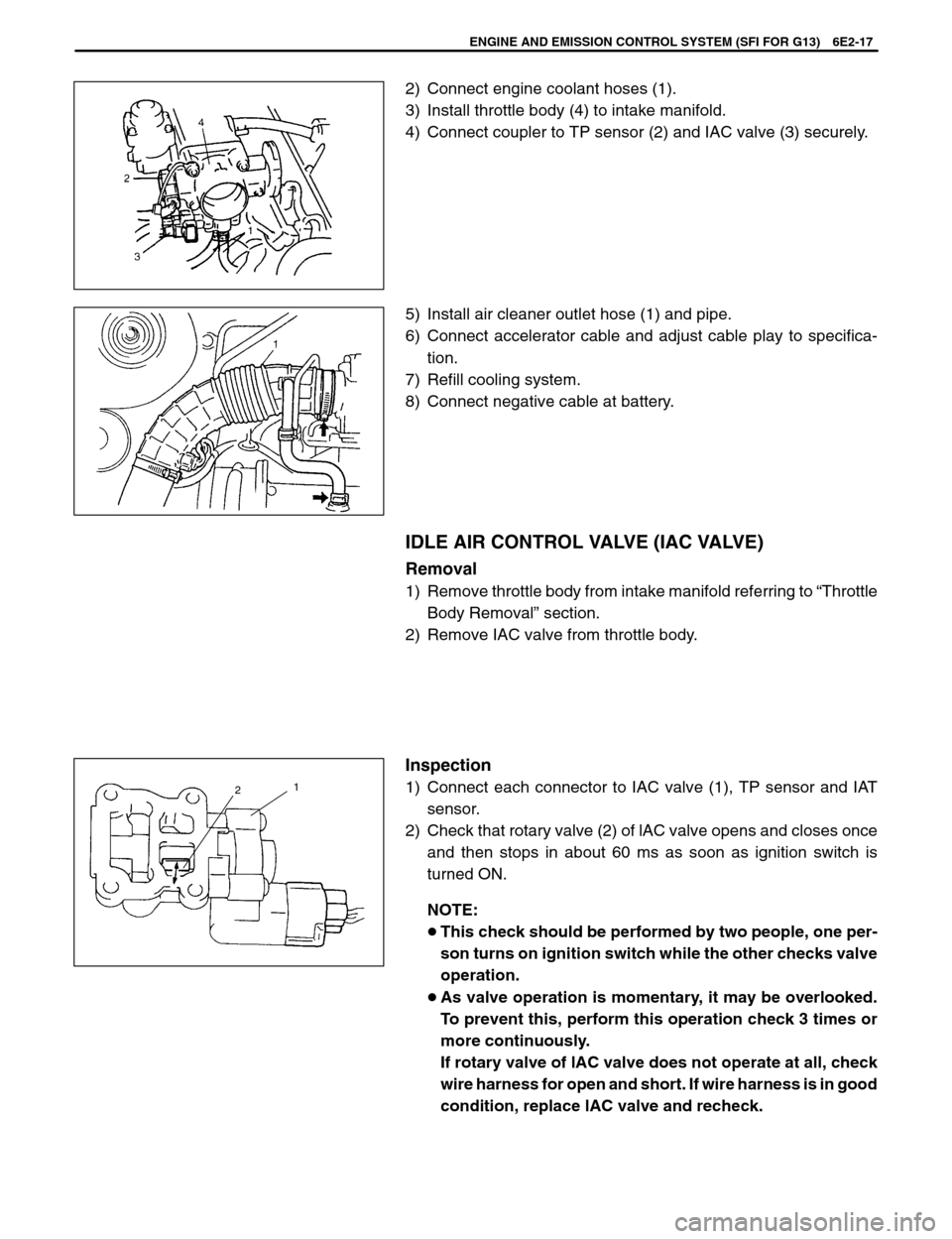
21
ENGINE AND EMISSION CONTROL SYSTEM (SFI FOR G13) 6E2-17
2) Connect engine coolant hoses (1).
3) Install throttle body (4) to intake manifold.
4) Connect coupler to TP sensor (2) and IAC valve (3) securely.
5) Install air cleaner outlet hose (1) and pipe.
6) Connect accelerator cable and adjust cable play to specifica-
tion.
7) Refill cooling system.
8) Connect negative cable at battery.
IDLE AIR CONTROL VALVE (IAC VALVE)
Removal
1) Remove throttle body from intake manifold referring to “Throttle
Body Removal” section.
2) Remove IAC valve from throttle body.
Inspection
1) Connect each connector to IAC valve (1), TP sensor and IAT
sensor.
2) Check that rotary valve (2) of lAC valve opens and closes once
and then stops in about 60 ms as soon as ignition switch is
turned ON.
NOTE:
This check should be performed by two people, one per-
son turns on ignition switch while the other checks valve
operation.
As valve operation is momentary, it may be overlooked.
To prevent this, perform this operation check 3 times or
more continuously.
If rotary valve of lAC valve does not operate at all, check
wire harness for open and short. If wire harness is in good
condition, replace lAC valve and recheck.
Page 455 of 557
ENGINE AND EMISSION CONTROL SYSTEM (SFI FOR G13) 6E2-27
ELECTRONIC CONTROL SYSTEM
ENGINE CONTROL MODULE (POWERTRAIN
CONTROL MODULE) [ECM (PCM)]
CAUTION:
As ECM (PCM) consists of precision parts, be careful not to
expose it to excessive shock.
Removal
1) Disconnect battery negative cable at battery.
2) Disable air bag system, refer to “DISABLING THE AIR BAG
SYSTEM” in Section 9J if equipped.
3) Lower fuse box after removing screws and remove fuse box
bracket.
4) Remove ECM (PCM) (1) from body.
5) Disconnect couplers from ECM (PCM).
Installation
Reverse removal procedure noting the following:
Connect couplers to ECM (PCM) securely.
MANIFOLD ABSOLUTE PRESSURE SENSOR (MAP
SENSOR)
Inspection
Check MAP sensor referring to “MAP Sensor Individual Check” in
DTC P0105 Flow Table. If malfunction is found, replace.
Page 456 of 557
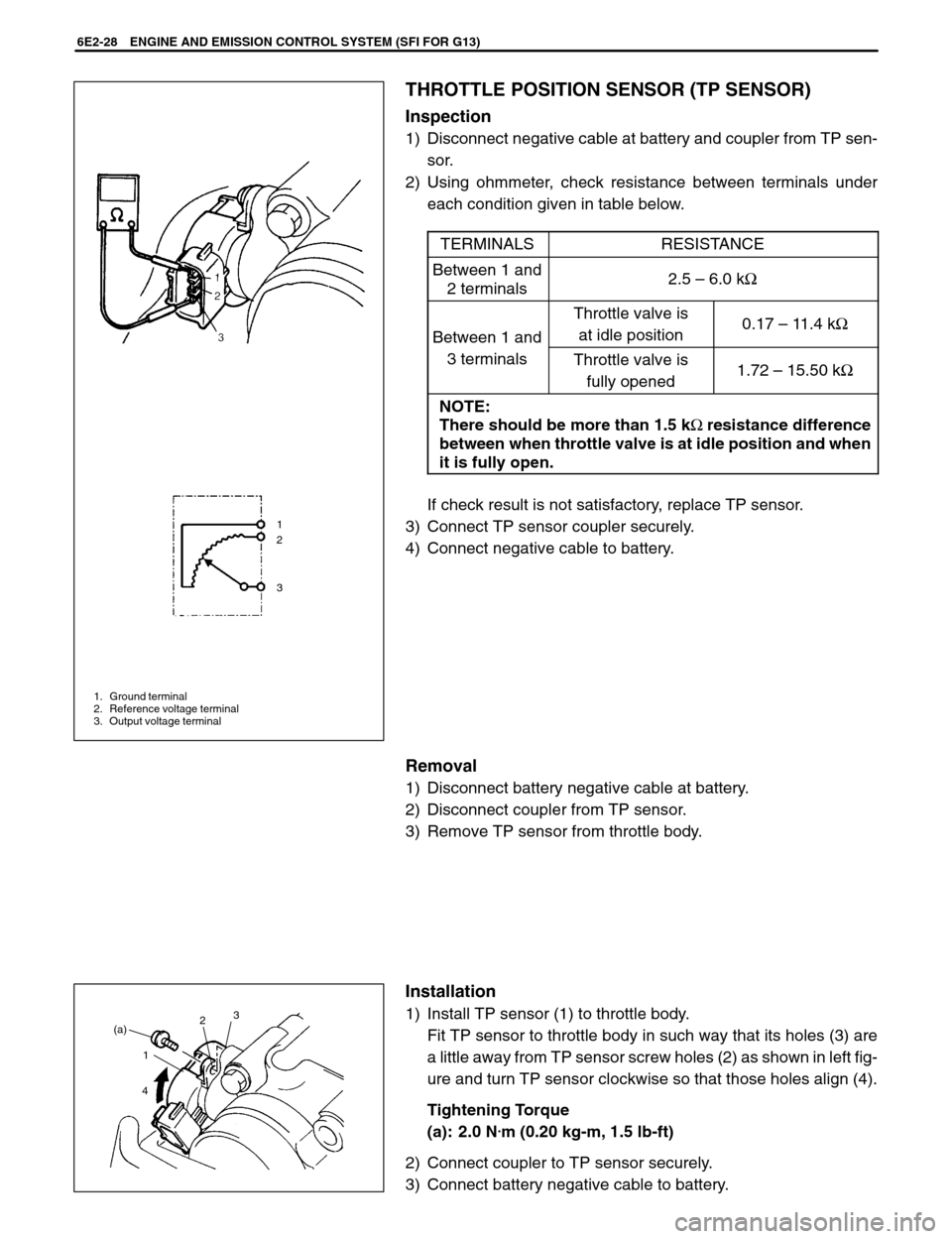
1
2
3
1. Ground terminal
2. Reference voltage terminal
3. Output voltage terminal
(a)
1
23
4
6E2-28 ENGINE AND EMISSION CONTROL SYSTEM (SFI FOR G13)
THROTTLE POSITION SENSOR (TP SENSOR)
Inspection
1) Disconnect negative cable at battery and coupler from TP sen-
sor.
2) Using ohmmeter, check resistance between terminals under
each condition given in table below.
TERMINALS
RESISTANCE
Between 1 and
2 terminals2.5 – 6.0 kΩ
Between 1 and
Throttle valve is
at idle position0.17 – 11.4 kΩ
3 terminalsThrottle valve is
fully opened1.72 – 15.50 kΩ
NOTE:
There should be more than 1.5 kΩ resistance difference
between when throttle valve is at idle position and when
it is fully open.
If check result is not satisfactory, replace TP sensor.
3) Connect TP sensor coupler securely.
4) Connect negative cable to battery.
Removal
1) Disconnect battery negative cable at battery.
2) Disconnect coupler from TP sensor.
3) Remove TP sensor from throttle body.
Installation
1) Install TP sensor (1) to throttle body.
Fit TP sensor to throttle body in such way that its holes (3) are
a little away from TP sensor screw holes (2) as shown in left fig-
ure and turn TP sensor clockwise so that those holes align (4).
Tightening Torque
(a): 2.0 N
.m (0.20 kg-m, 1.5 lb-ft)
2) Connect coupler to TP sensor securely.
3) Connect battery negative cable to battery.
Page 457 of 557
ENGINE AND EMISSION CONTROL SYSTEM (SFI FOR G13) 6E2-29
INTAKE AIR TEMPERATURE SENSOR (IAT SENSOR)
Removal
1) Disconnect battery negative cable at battery.
2) Disconnect coupler from IAT sensor (1).
3) Remove IAT sensor (1) from air cleaner outlet hose (2).
Inspection
Immerse temperature sensing part of IAT sensor in water (or ice)
and measure resistance between sensor terminals while heating
water gradually.
If measured resistance doesn’t show such characteristic as shown
in left figure, replace IAT sensor.
Installation
Reverse removal procedure noting the following.
Clean mating surfaces of IAT sensor and air cleaner outlet hose.
Connect IAT sensor coupler (1) securely.
Page 458 of 557
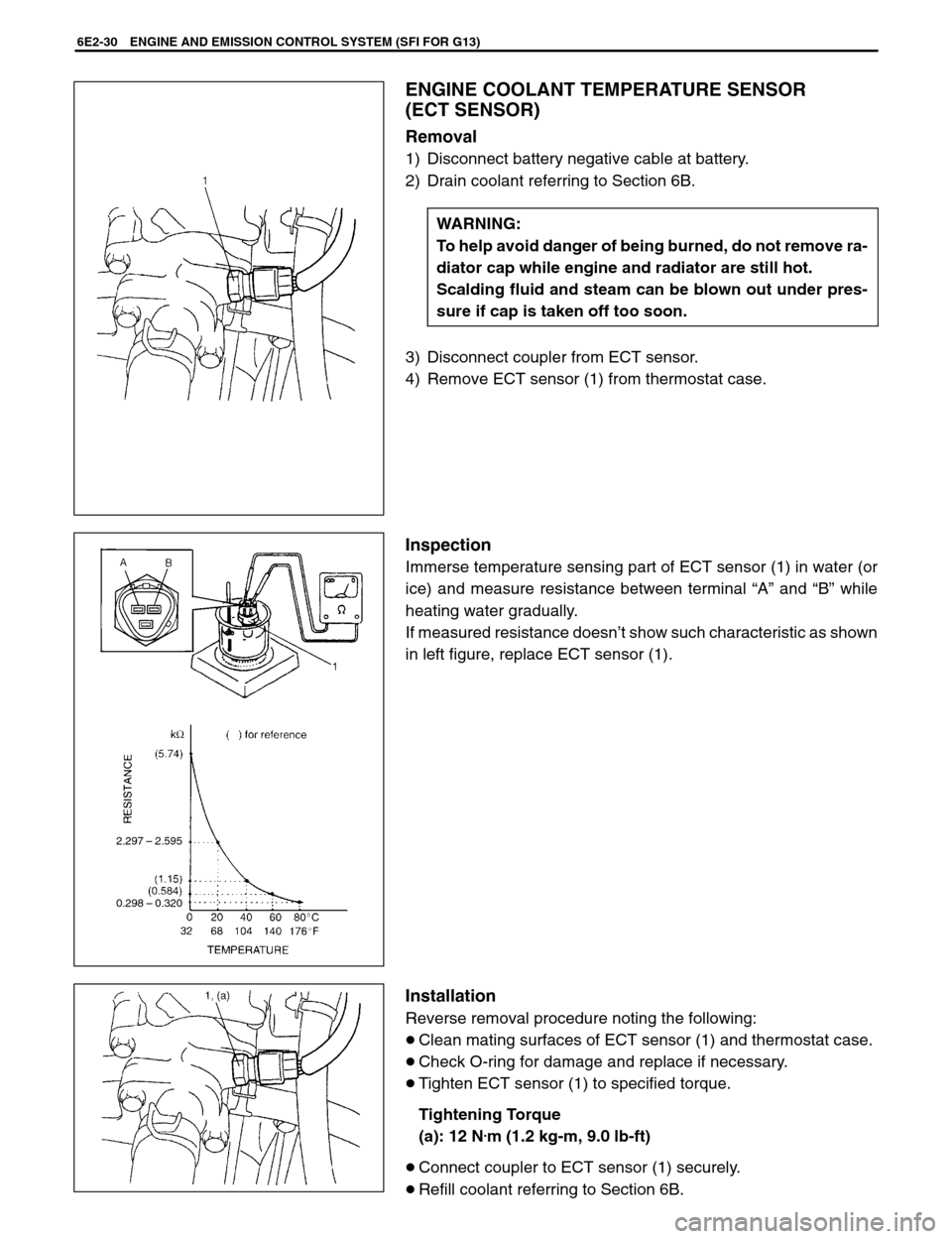
2.297 – 2.595
0.298 – 0.320
6E2-30 ENGINE AND EMISSION CONTROL SYSTEM (SFI FOR G13)
ENGINE COOLANT TEMPERATURE SENSOR
(ECT SENSOR)
Removal
1) Disconnect battery negative cable at battery.
2) Drain coolant referring to Section 6B.
WARNING:
To help avoid danger of being burned, do not remove ra-
diator cap while engine and radiator are still hot.
Scalding fluid and steam can be blown out under pres-
sure if cap is taken off too soon.
3) Disconnect coupler from ECT sensor.
4) Remove ECT sensor (1) from thermostat case.
Inspection
Immerse temperature sensing part of ECT sensor (1) in water (or
ice) and measure resistance between terminal “A” and “B” while
heating water gradually.
If measured resistance doesn’t show such characteristic as shown
in left figure, replace ECT sensor (1).
Installation
Reverse removal procedure noting the following:
Clean mating surfaces of ECT sensor (1) and thermostat case.
Check O-ring for damage and replace if necessary.
Tighten ECT sensor (1) to specified torque.
Tightening Torque
(a): 12 N
.m (1.2 kg-m, 9.0 lb-ft)
Connect coupler to ECT sensor (1) securely.
Refill coolant referring to Section 6B.
Page 459 of 557
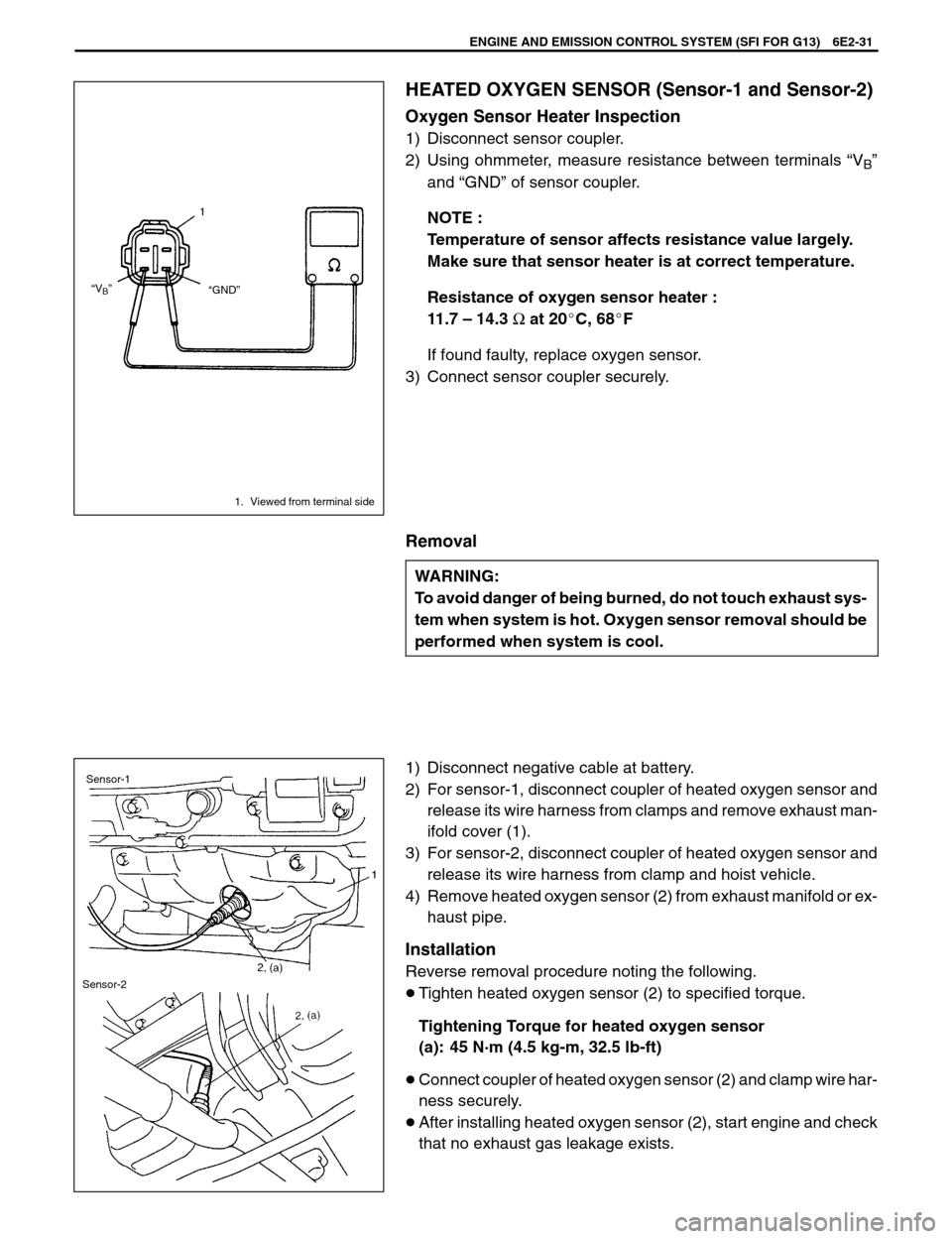
ENGINE AND EMISSION CONTROL SYSTEM (SFI FOR G13) 6E2-31
1. Viewed from terminal side
Sensor-1
Sensor-2
“VB”
“GND”
HEATED OXYGEN SENSOR (Sensor-1 and Sensor-2)
Oxygen Sensor Heater Inspection
1) Disconnect sensor coupler.
2) Using ohmmeter, measure resistance between terminals “V
B”
and “GND” of sensor coupler.
NOTE :
Temperature of sensor affects resistance value largely.
Make sure that sensor heater is at correct temperature.
Resistance of oxygen sensor heater :
11.7 – 14.3 Ω at 20C, 68F
If found faulty, replace oxygen sensor.
3) Connect sensor coupler securely.
Removal
WARNING:
To avoid danger of being burned, do not touch exhaust sys-
tem when system is hot. Oxygen sensor removal should be
performed when system is cool.
1) Disconnect negative cable at battery.
2) For sensor-1, disconnect coupler of heated oxygen sensor and
release its wire harness from clamps and remove exhaust man-
ifold cover (1).
3) For sensor-2, disconnect coupler of heated oxygen sensor and
release its wire harness from clamp and hoist vehicle.
4) Remove heated oxygen sensor (2) from exhaust manifold or ex-
haust pipe.
Installation
Reverse removal procedure noting the following.
Tighten heated oxygen sensor (2) to specified torque.
Tightening Torque for heated oxygen sensor
(a): 45 N·m (4.5 kg-m, 32.5 lb-ft)
Connect coupler of heated oxygen sensor (2) and clamp wire har-
ness securely.
After installing heated oxygen sensor (2), start engine and check
that no exhaust gas leakage exists.
Page 460 of 557
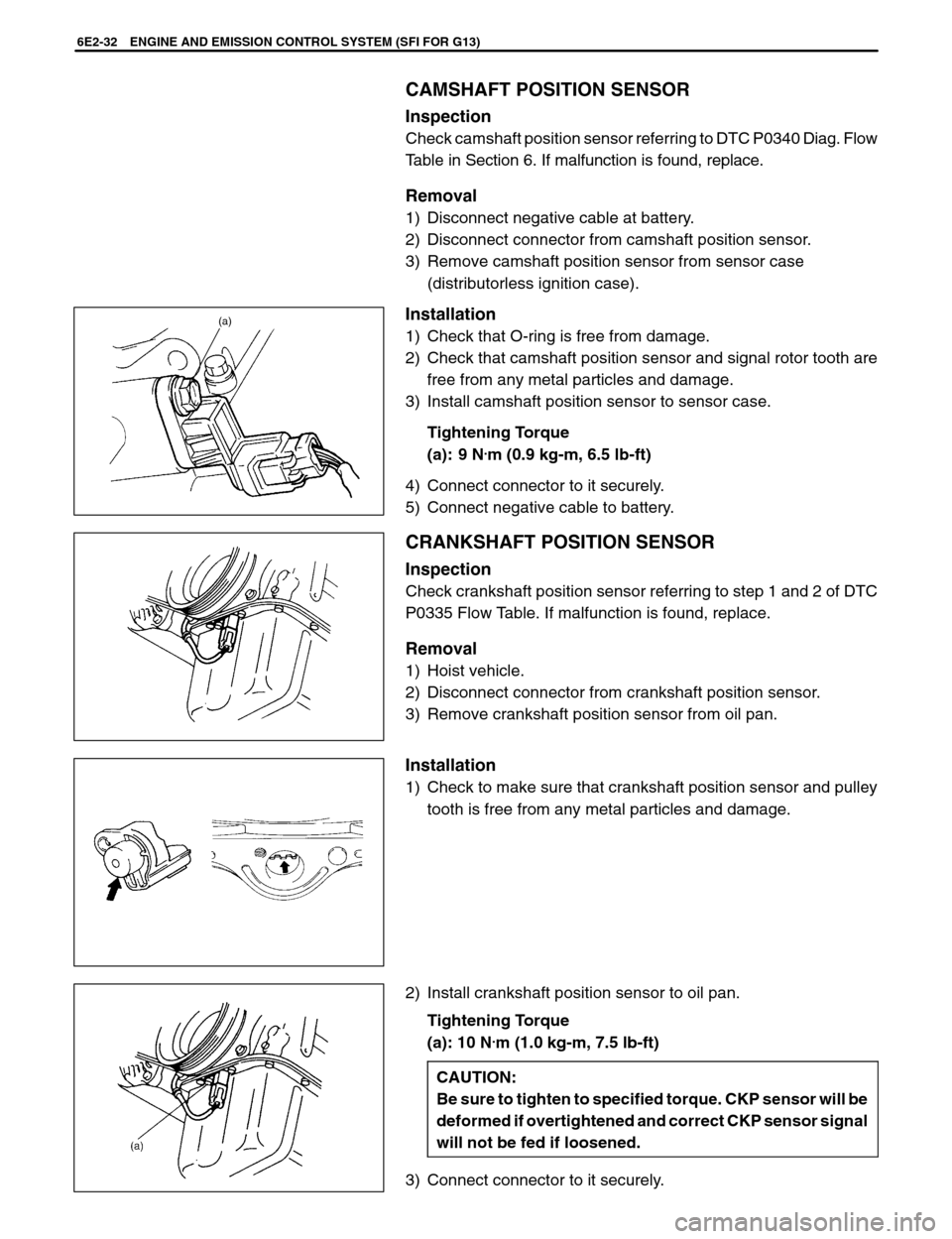
(a)
6E2-32 ENGINE AND EMISSION CONTROL SYSTEM (SFI FOR G13)
CAMSHAFT POSITION SENSOR
Inspection
Check camshaft position sensor referring to DTC P0340 Diag. Flow
Table in Section 6. If malfunction is found, replace.
Removal
1) Disconnect negative cable at battery.
2) Disconnect connector from camshaft position sensor.
3) Remove camshaft position sensor from sensor case
(distributorless ignition case).
Installation
1) Check that O-ring is free from damage.
2) Check that camshaft position sensor and signal rotor tooth are
free from any metal particles and damage.
3) Install camshaft position sensor to sensor case.
Tightening Torque
(a): 9 N
.m (0.9 kg-m, 6.5 lb-ft)
4) Connect connector to it securely.
5) Connect negative cable to battery.
CRANKSHAFT POSITION SENSOR
Inspection
Check crankshaft position sensor referring to step 1 and 2 of DTC
P0335 Flow Table. If malfunction is found, replace.
Removal
1) Hoist vehicle.
2) Disconnect connector from crankshaft position sensor.
3) Remove crankshaft position sensor from oil pan.
Installation
1) Check to make sure that crankshaft position sensor and pulley
tooth is free from any metal particles and damage.
2) Install crankshaft position sensor to oil pan.
Tightening Torque
(a): 10 N
.m (1.0 kg-m, 7.5 lb-ft)
CAUTION:
Be sure to tighten to specified torque. CKP sensor will be
deformed if overtightened and correct CKP sensor signal
will not be fed if loosened.
3) Connect connector to it securely.