Page 251 of 558
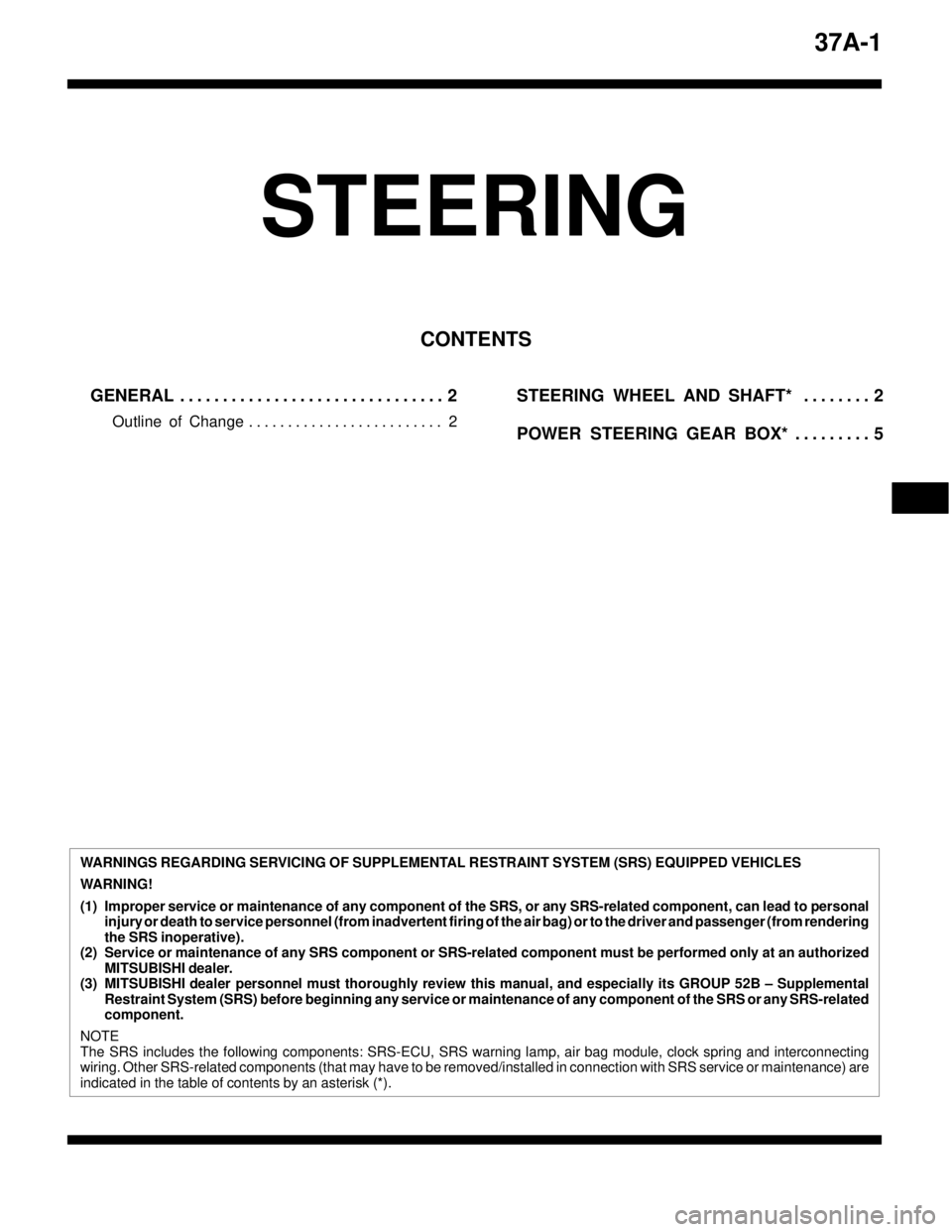
37A-1
STEERING
CONTENTS
GENERAL 2. . . . . . . . . . . . . . . . . . . . . . . . . . . . . . .
Outline of Change 2. . . . . . . . . . . . . . . . . . . . . . . . .
STEERING WHEEL AND SHAFT* 2. . . . . . . .
POWER STEERING GEAR BOX* 5. . . . . . . . .
WARNINGS REGARDING SERVICING OF SUPPLEMENTAL RESTRAINT SYSTEM (SRS) EQUIPPED VEHICLES
WARNING!
(1) Improper service or maintenance of any component of the SRS, or any SRS-related component, can lead to personal
injury or death to service personnel (from inadvertent firing of the air bag) or to the driver and passenger (from rendering
the SRS inoperative).
(2) Service or maintenance of any SRS component or SRS-related component must be performed only at an authorized
MITSUBISHI dealer.
(3) MITSUBISHI dealer personnel must thoroughly review this manual, and especially its GROUP 52B – Supplemental
Restraint System (SRS) before beginning any service or maintenance of any component of the SRS or any SRS-related
component.
NOTE
The SRS includes the following components: SRS-ECU, SRS warning lamp, air bag module, clock spring and interconnecting
wiring. Other SRS-related components (that may have to be removed/installed in connection with SRS service or maintenance) are
indicated in the table of contents by an asterisk (*).
Page 252 of 558
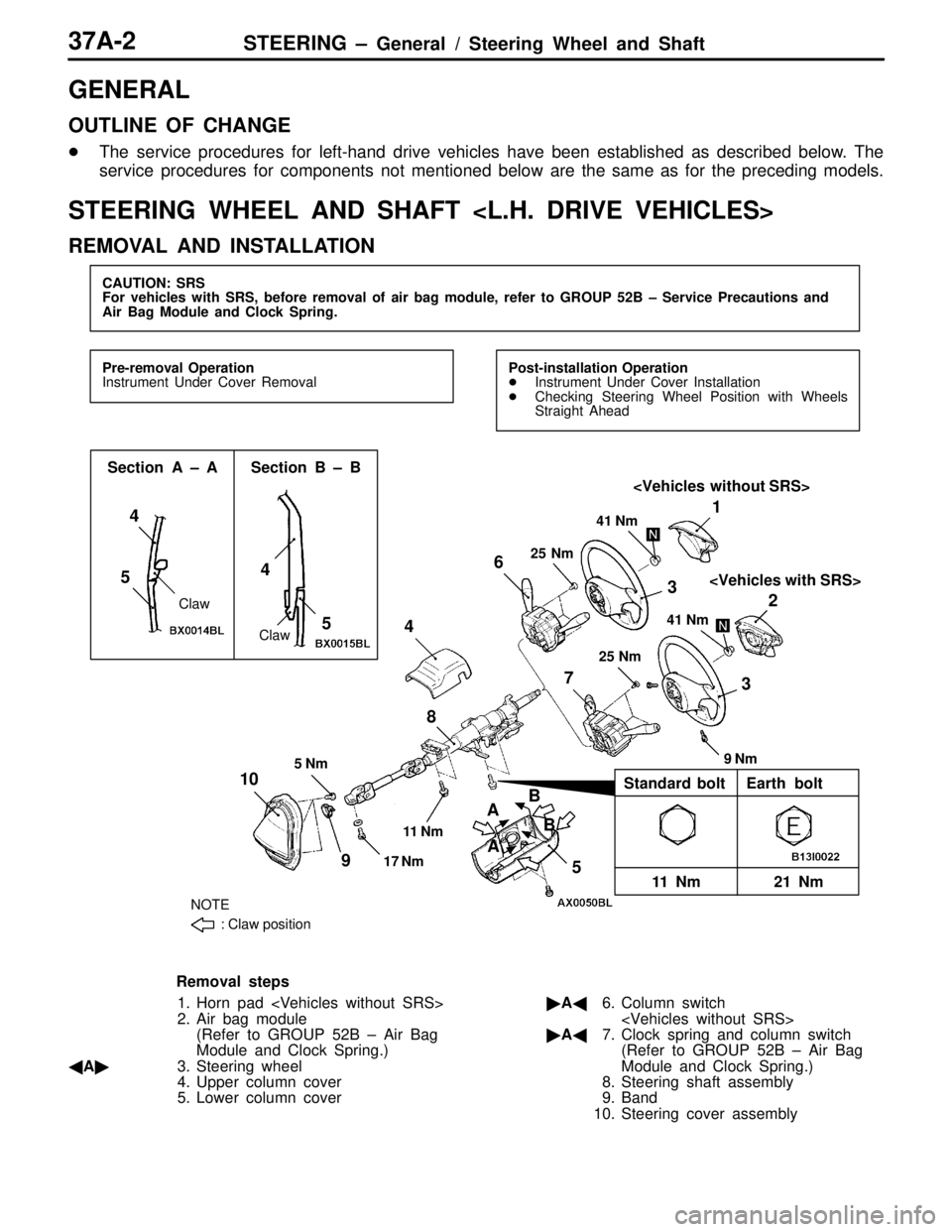
STEERING – General / Steering Wheel and Shaft37A-2
GENERAL
OUTLINE OF CHANGE
The service procedures for left-hand drive vehicles have been established as described below. The
service procedures for components not mentioned below are the same as for the preceding models.
STEERING WHEEL AND SHAFT
REMOVAL AND INSTALLATION
CAUTION: SRS
For vehicles with SRS, before removal of air bag module, refer to GROUP 52B – Service Precautions and
Air Bag Module and Clock Spring.
Pre-removal Operation
Instrument Under Cover RemovalPost-installation Operation
Instrument Under Cover Installation
Checking Steering Wheel Position with Wheels
Straight Ahead
5 Nm
17 Nm11 Nm
10
98 431
532
41 Nm
25 Nm
6
25 Nm41 Nm
7
9 Nm
Section A – A Section B – B
Claw
: Claw position
AB 4
5
AB
11 Nm 21 Nm Standard bolt Earth bolt
NOTE
4
5
Claw
Removal steps
1. Horn pad
2. Air bag module
(Refer to GROUP 52B – Air Bag
Module and Clock Spring.)
A3. Steering wheel
4. Upper column cover
5. Lower column coverA6. Column switch
A7. Clock spring and column switch
(Refer to GROUP 52B – Air Bag
Module and Clock Spring.)
8. Steering shaft assembly
9. Band
10. Steering cover assembly
Page 253 of 558
STEERING – Steering Wheel and Shaft37A-3
REMOVAL SERVICE POINT
ASTEERING WHEEL REMOVAL
INSTALLATION SERVICE POINT
ACLOCK SPRING AND COLUMN SWITCH / COLUMN
SWITCH INSTALLATION
Tighten the screws in an alphabetical order.
DISASSEMBLY AND REASSEMBLY
1
2
3 4
Disassembly steps
AA1. Special bolt
A2. Steering lock bracket
A3. Steering lock cylinder
4. Steering shaft
MB990803
A
BC
Page 254 of 558
STEERING – Steering Wheel and Shaft37A-4
DISASSEMBLY SERVICE POINT
ASTEERING LOCK BRACKET / STEERING LOCK
CYLINDER REMOVAL
If it is necessary to remove the steering lock cylinder, use
a hacksaw to cut the special bolts at the steering lock bracket
side.
REASSEMBLY SERVICE POINT
ASTEERING LOCK CYLINDER/STEERING LOCK
BRACKET / SPECIAL BOLT INSTALLATION
1. When installing the steering lock cylinder and steering
lock bracket to the column tube, temporarily install the
steering lock in alignment with the column boss.
2. After checking that the lock works properly, tighten the
special bolts until the head twists off.
Caution
The steering lock bracket and bolts must be replaced
with new ones when the steering lock is installed.
Steering lock bracket
Steering lock cylinder
Page 255 of 558
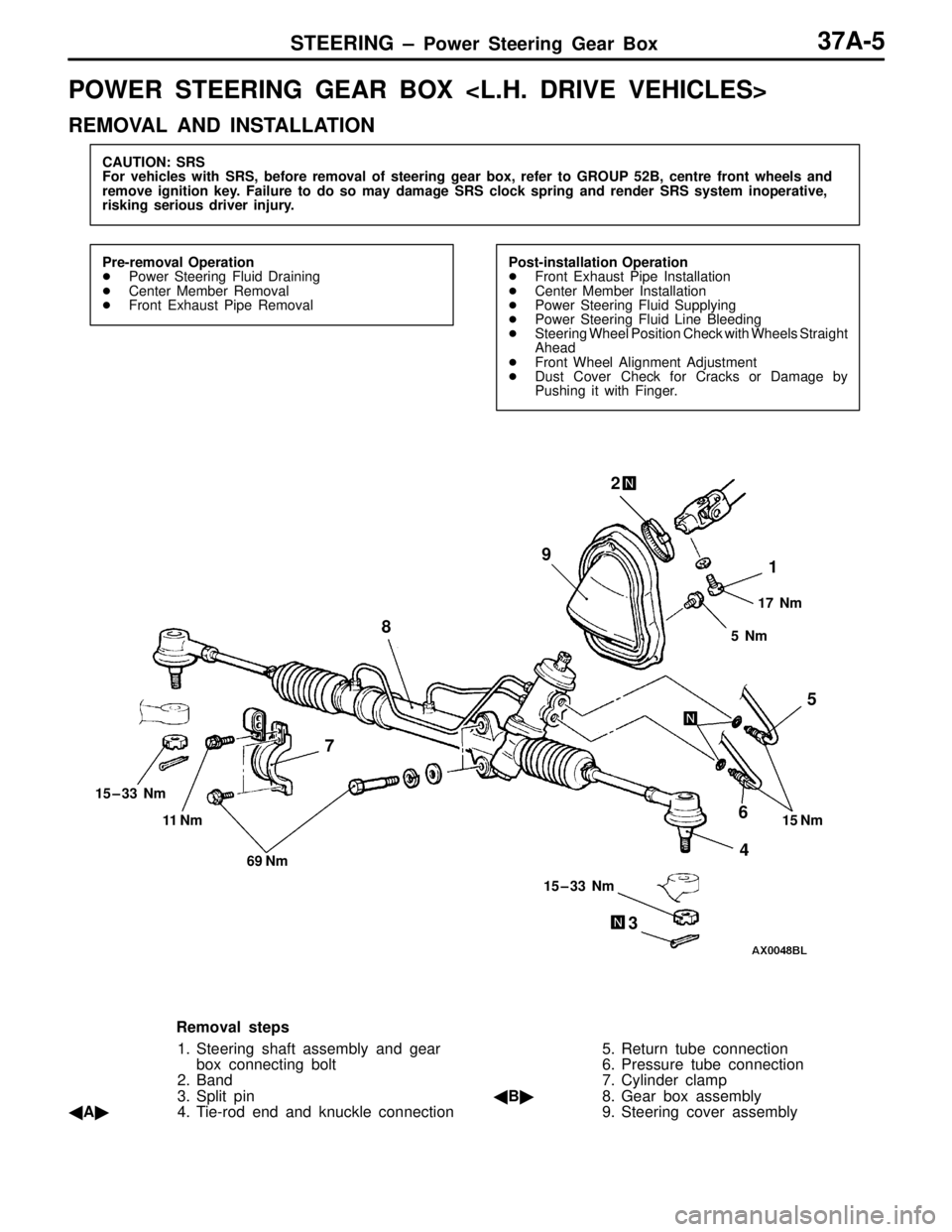
STEERING – Power Steering Gear Box37A-5
POWER STEERING GEAR BOX
REMOVAL AND INSTALLATION
CAUTION: SRS
For vehicles with SRS, before removal of steering gear box, refer to GROUP 52B, centre front wheels and
remove ignition key. Failure to do so may damage SRS clock spring and render SRS system inoperative,
risking serious driver injury.
Pre-removal Operation
Power Steering Fluid Draining
Center Member Removal
Front Exhaust Pipe RemovalPost-installation Operation
Front Exhaust Pipe Installation
Center Member Installation
Power Steering Fluid Supplying
Power Steering Fluid Line Bleeding
Steering Wheel Position Check with Wheels Straight
Ahead
Front Wheel Alignment Adjustment
Dust Cover Check for Cracks or Damage by
Pushing it with Finger.
15 Nm 15–33 Nm
69 Nm17 Nm
5 Nm
15–33 Nm
789
3
45 1 2
611 Nm
Removal steps
1. Steering shaft assembly and gear
box connecting bolt
2. Band
3. Split pin
A4. Tie-rod end and knuckle connection5. Return tube connection
6. Pressure tube connection
7. Cylinder clamp
B8. Gear box assembly
9. Steering cover assembly
Page 256 of 558
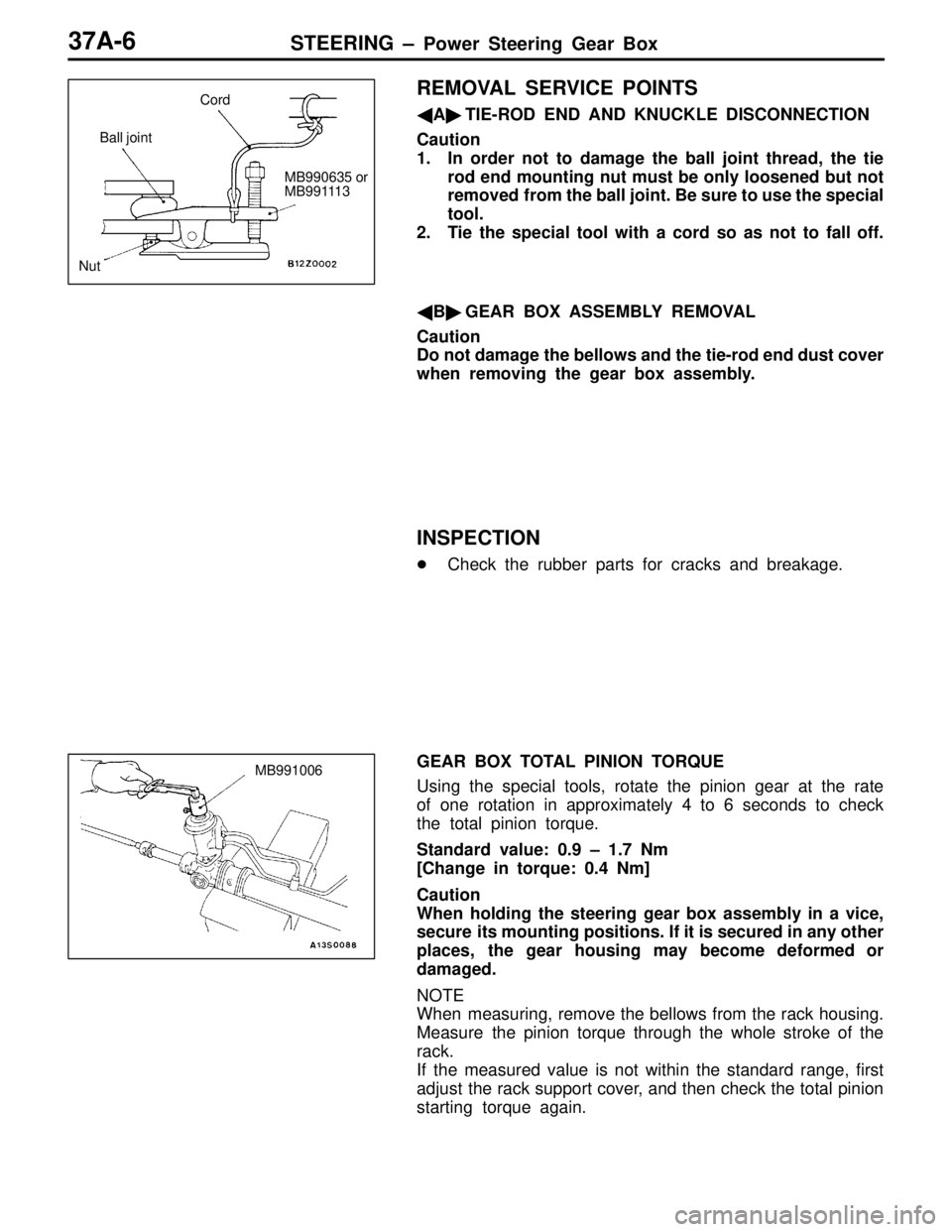
STEERING – Power Steering Gear Box37A-6
REMOVAL SERVICE POINTS
ATIE-ROD END AND KNUCKLE DISCONNECTION
Caution
1. In order not to damage the ball joint thread, the tie
rod end mounting nut must be only loosened but not
removed from the ball joint. Be sure to use the special
tool.
2. Tie the special tool with a cord so as not to fall off.
BGEAR BOX ASSEMBLY REMOVAL
Caution
Do not damage the bellows and the tie-rod end dust cover
when removing the gear box assembly.
INSPECTION
Check the rubber parts for cracks and breakage.
GEAR BOX TOTAL PINION TORQUE
Using the special tools, rotate the pinion gear at the rate
of one rotation in approximately 4 to 6 seconds to check
the total pinion torque.
Standard value: 0.9 – 1.7 Nm
[Change in torque: 0.4 Nm]
Caution
When holding the steering gear box assembly in a vice,
secure its mounting positions. If it is secured in any other
places, the gear housing may become deformed or
damaged.
NOTE
When measuring, remove the bellows from the rack housing.
Measure the pinion torque through the whole stroke of the
rack.
If the measured value is not within the standard range, first
adjust the rack support cover, and then check the total pinion
starting torque again.
Cord
Ball joint
NutMB990635 or
MB991113
MB991006
Page 257 of 558
STEERING – Power Steering Gear Box37A-7
If the total pinion starting torque cannot be adjusted to within
the standard range by adjusting the rack support cover, check
the rack support cover, rack support spring, rack support
and replace any parts if necessary.
CHECK THE TIE ROD FOR SWING RESISTANCE
1. Give 10 hard swings to the tie rod.
2. Measure the tie rod swing resistance with a spring balance.
Standard value: 5–18 N [1.5–4.9 Nm]
3. If the measured value exceeds the standard value, replace
tie rod.
4. Even if the measured value is below the standard value,
the tie rod which swings smoothly without excessive play
may be used.
Page 258 of 558
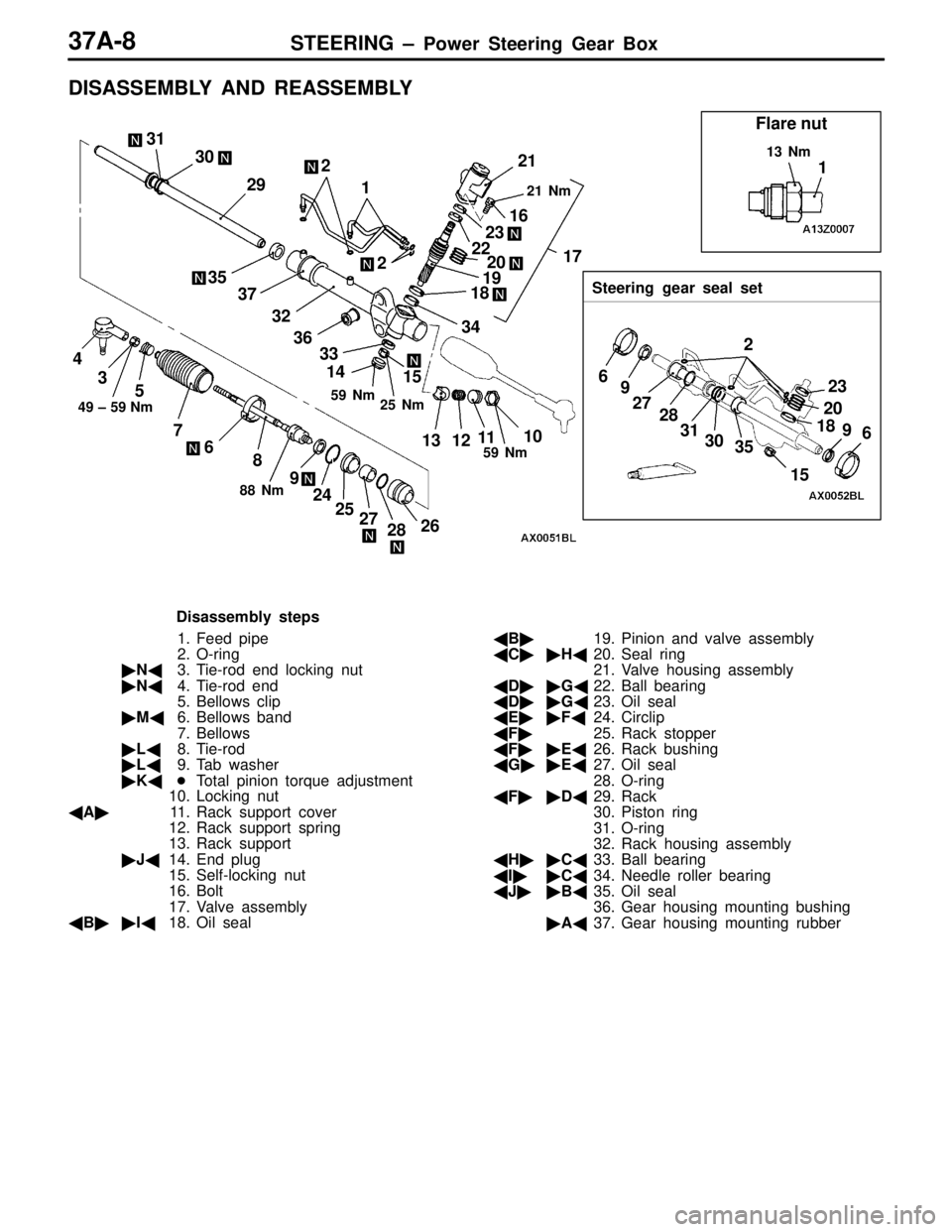
STEERING – Power Steering Gear Box37A-8
DISASSEMBLY AND REASSEMBLY
Steering gear seal set
Flare nut
1
3 4
5
6 7
8
910
11
12 13 14
15 17
1921
24
25
26 29
32
33
35
2
22
3416
27
28 31
3013 Nm
1
20
36 3718
25 Nm
49 – 59 Nm
88 Nm27
28
309 20
62
9 6 35
59 Nm
15
59 Nm
21 Nm
2
311823 23
Disassembly steps
1. Feed pipe
2. O-ring
N3. Tie-rod end locking nut
N4. Tie-rod end
5. Bellows clip
M6. Bellows band
7. Bellows
L8. Tie-rod
L9. Tab washer
KTotal pinion torque adjustment
10. Locking nut
A11. Rack support cover
12. Rack support spring
13. Rack support
J14. End plug
15. Self-locking nut
16. Bolt
17. Valve assembly
BI18. Oil sealB19. Pinion and valve assembly
CH20. Seal ring
21. Valve housing assembly
DG22. Ball bearing
DG23. Oil seal
EF24. Circlip
F25. Rack stopper
FE26. Rack bushing
GE27. Oil seal
28. O-ring
FD29. Rack
30. Piston ring
31. O-ring
32. Rack housing assembly
HC33. Ball bearing
IC34. Needle roller bearing
JB35. Oil seal
36. Gear housing mounting bushing
A37. Gear housing mounting rubber