Page 936 of 1463
POWER BOOSTER 4C-3
Removal & Installation Procedure
1. Remove the oil level sensor connector.
2. Remove the tube from the master cylinder.
Installation Notice
Notice
lBe careful not to drop the oil when removing the tube.
lIf the oil is dropped, promptly sweep up.
3. Remove the booster vacuum hose.
Notice
lConnect fully to the end of vacuum hose when installing.
4. Loosen the nut of master cylinder.
Installation Notice
5. Remove the clevis pin and disconnect the pedal and brake
booster push rod.
Notice
lInstall in the upper hole when PBR brake.
lConnect the snap pin in the hole of clevis pin fully.
lApply the grease around the hole of clevis pin.
Tightening Torque 14 - 22 Nm
Tightening Torque 15 - 19 Nm
Page 941 of 1463
FRONT DISC BRAKES 4D-3
Removal & Installation Procedure
1. MANDO Brake
Tightening Torque 25 - 35 Nm
2. PBR Brake
Remove the eye-hose bolt and disconnect the hose.
Installation Notice
Tightening Torque 15 - 18 Nm
3. Remove the wheel speed sensor (for ABS vehicies).
Installation Notice
Tightening Torque 6 - 8 Nm
4. Remove the mounting bolts and then caliper assembly.
Installation Notice
Tightening Torque 85 - 105 Nm
Remove the hose mounting nut and disconnect the hose.
Installation Notice
Page 948 of 1463
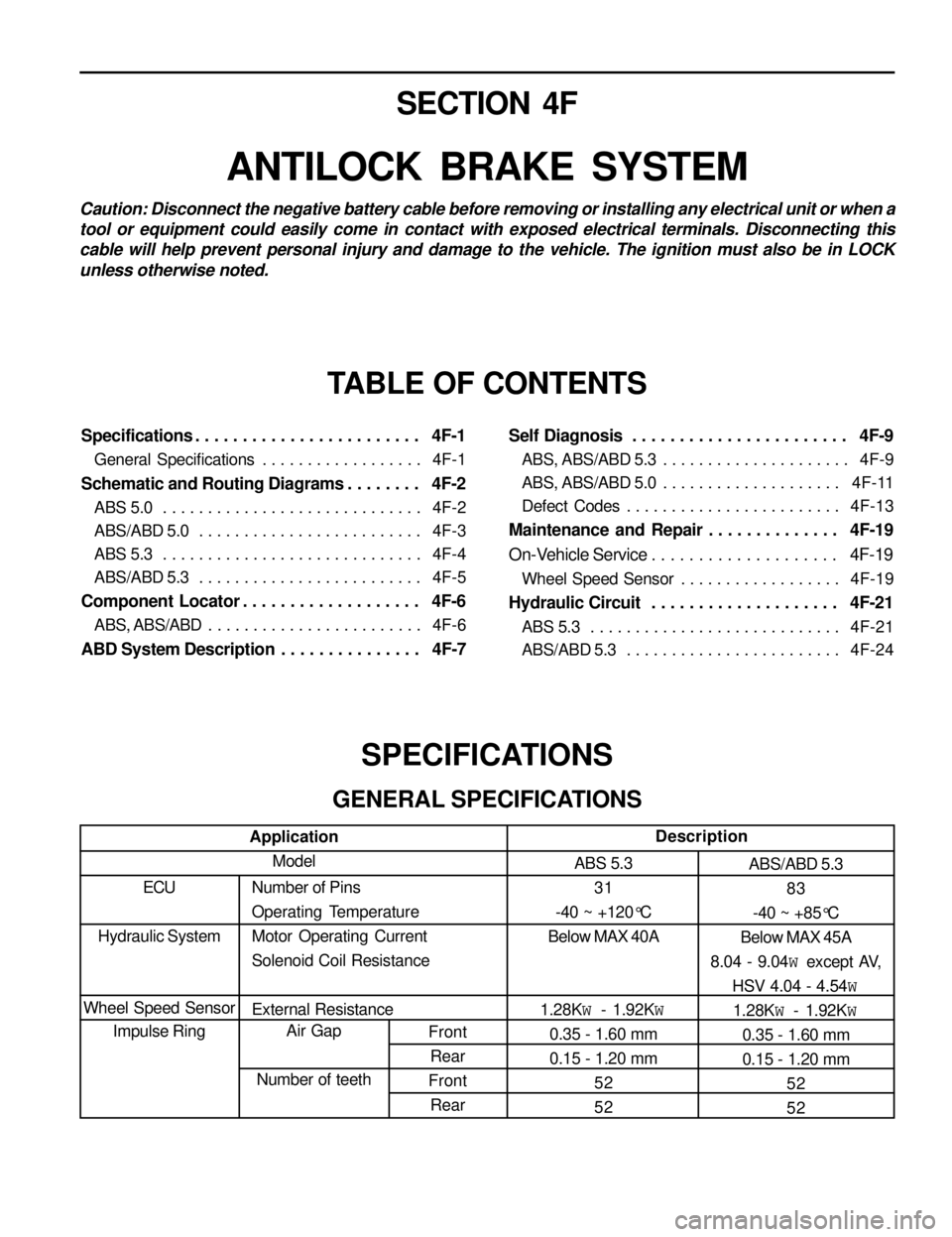
Front
Rear
Front
Rear
SECTION 4F
ANTILOCK BRAKE SYSTEM
TABLE OF CONTENTS
Caution: Disconnect the negative battery cable before removing or installing any electrical unit or when a
tool or equipment could easily come in contact with exposed electrical terminals. Disconnecting this
cable will help prevent personal injury and damage to the vehicle. The ignition must also be in LOCK
unless otherwise noted.
SPECIFICATIONS
GENERAL SPECIFICATIONS
Application
Model
ECUNumber of Pins
Operating Temperature
Motor Operating Current
Solenoid Coil Resistance
External Resistance
Air Gap
Number of teethDescription
ABS 5.3
31
-40 ~ +120°C
Below MAX 40A
1.28KW - 1.92KW
0.35 - 1.60 mm
0.15 - 1.20 mm
52
52ABS/ABD 5.3
83
-40 ~ +85°C
Below MAX 45A
8.04 - 9.04W except AV,
HSV 4.04 - 4.54W
1.28KW - 1.92KW
0.35 - 1.60 mm
0.15 - 1.20 mm
52
52 Hydraulic System
Wheel Speed Sensor
Impulse Ring
Specifications . . . . . . . . . . . . . . . . . . . . . . . . 4F-1
General Specifications . . . . . . . . . . . . . . . . . . 4F-1
Schematic and Routing Diagrams . . . . . . . . 4F-2
ABS 5.0 . . . . . . . . . . . . . . . . . . . . . . . . . . . . . 4F-2
ABS/ABD 5.0 . . . . . . . . . . . . . . . . . . . . . . . . . 4F-3
ABS 5.3 . . . . . . . . . . . . . . . . . . . . . . . . . . . . . 4F-4
ABS/ABD 5.3 . . . . . . . . . . . . . . . . . . . . . . . . . 4F-5
Component Locator . . . . . . . . . . . . . . . . . . . 4F-6
ABS, ABS/ABD . . . . . . . . . . . . . . . . . . . . . . . . 4F-6
ABD System Description . . . . . . . . . . . . . . . 4F-7Self Diagnosis . . . . . . . . . . . . . . . . . . . . . . . 4F-9
ABS, ABS/ABD 5.3 . . . . . . . . . . . . . . . . . . . . . 4F-9
ABS, ABS/ABD 5.0 . . . . . . . . . . . . . . . . . . . . 4F-11
Defect Codes . . . . . . . . . . . . . . . . . . . . . . . . 4F-13
Maintenance and Repair . . . . . . . . . . . . . . 4F-19
On-Vehicle Service . . . . . . . . . . . . . . . . . . . . 4F-19
Wheel Speed Sensor . . . . . . . . . . . . . . . . . . 4F-19
Hydraulic Circuit . . . . . . . . . . . . . . . . . . . . 4F-21
ABS 5.3 . . . . . . . . . . . . . . . . . . . . . . . . . . . . 4F-21
ABS/ABD 5.3 . . . . . . . . . . . . . . . . . . . . . . . . 4F-24
Page 953 of 1463
4F-6 ANTILOCK BRAKE SYSTEM
ABS,ABS/ABD
COMPONENT LOCATOR
1 ABS Hydraulic Unit
2 ABS/ABD Hydraulic Unit
3 Diagnosis Socket
4 Front Wheel Speed Sensor
5 Front Impulse Ring6 Rear Wheel Speed Sensor
7 Rear Impulse Ring
8 ABS Warning Indicator Light
9 TCS Indicator Light
1 0 ABS/ABD ECU
Page 960 of 1463
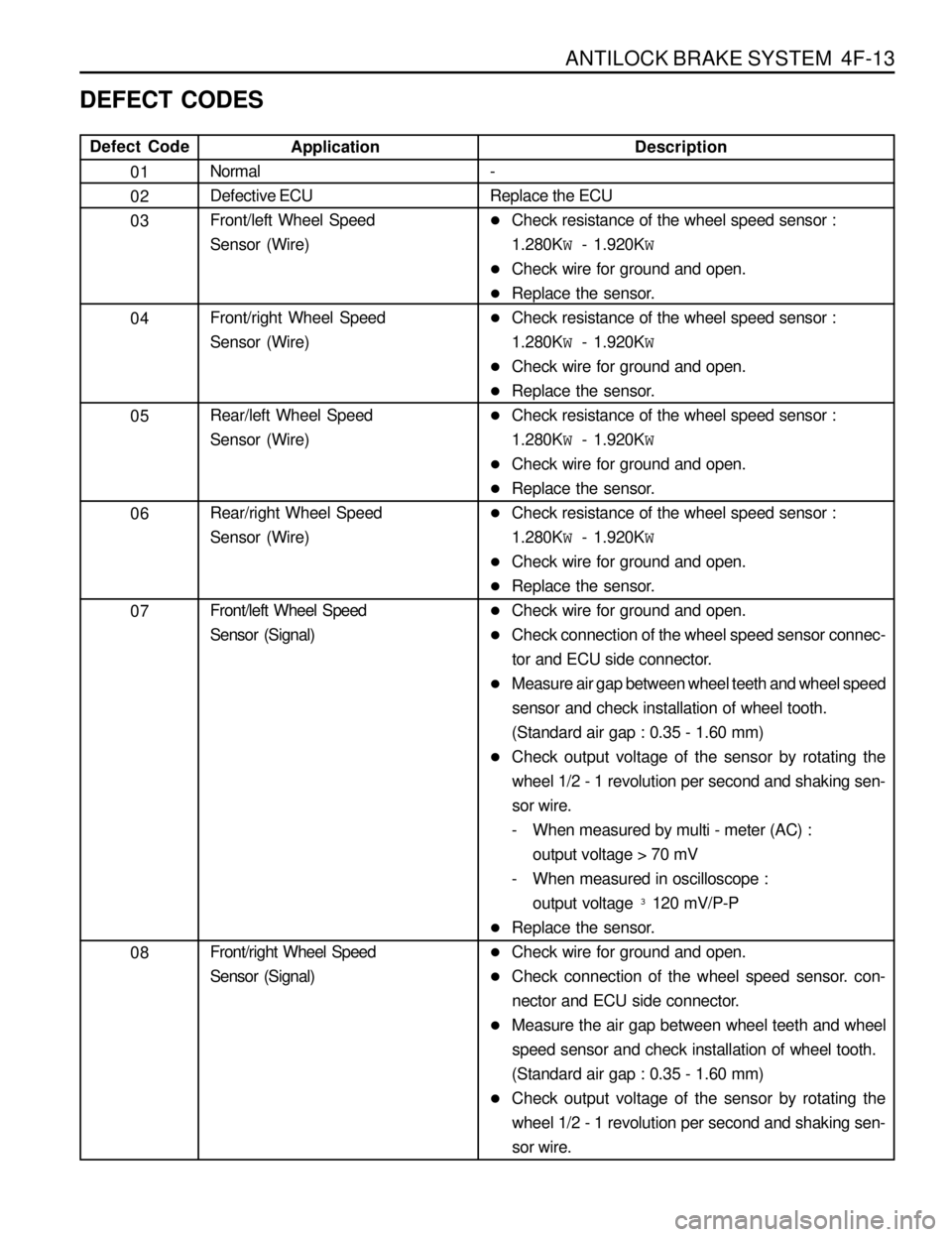
ANTILOCK BRAKE SYSTEM 4F-13
DEFECT CODES
Description
-
Replace the ECU
lCheck resistance of the wheel speed sensor :
1.280KW - 1.920KW
lCheck wire for ground and open.
lReplace the sensor.
lCheck resistance of the wheel speed sensor :
1.280KW - 1.920KW
lCheck wire for ground and open.
lReplace the sensor.
lCheck resistance of the wheel speed sensor :
1.280KW - 1.920KW
lCheck wire for ground and open.
lReplace the sensor.
lCheck resistance of the wheel speed sensor :
1.280KW - 1.920KW
lCheck wire for ground and open.
lReplace the sensor.
lCheck wire for ground and open.
lCheck connection of the wheel speed sensor connec-
tor and ECU side connector.
lMeasure air gap between wheel teeth and wheel speed
sensor and check installation of wheel tooth.
(Standard air gap : 0.35 - 1.60 mm)
lCheck output voltage of the sensor by rotating the
wheel 1/2 - 1 revolution per second and shaking sen-
sor wire.
- When measured by multi - meter (AC) :
output voltage > 70 mV
- When measured in oscilloscope :
output voltage ³ 120 mV/P-P
lReplace the sensor.
lCheck wire for ground and open.
lCheck connection of the wheel speed sensor. con-
nector and ECU side connector.
lMeasure the air gap between wheel teeth and wheel
speed sensor and check installation of wheel tooth.
(Standard air gap : 0.35 - 1.60 mm)
lCheck output voltage of the sensor by rotating the
wheel 1/2 - 1 revolution per second and shaking sen-
sor wire. Defect Code
01
02
03
04
05
06
07
08Application
Normal
Defective ECU
Front/left Wheel Speed
Sensor (Wire)
Front/right Wheel Speed
Sensor (Wire)
Rear/left Wheel Speed
Sensor (Wire)
Rear/right Wheel Speed
Sensor (Wire)
Front/left Wheel Speed
Sensor (Signal)
Front/right Wheel Speed
Sensor (Signal)
Page 961 of 1463
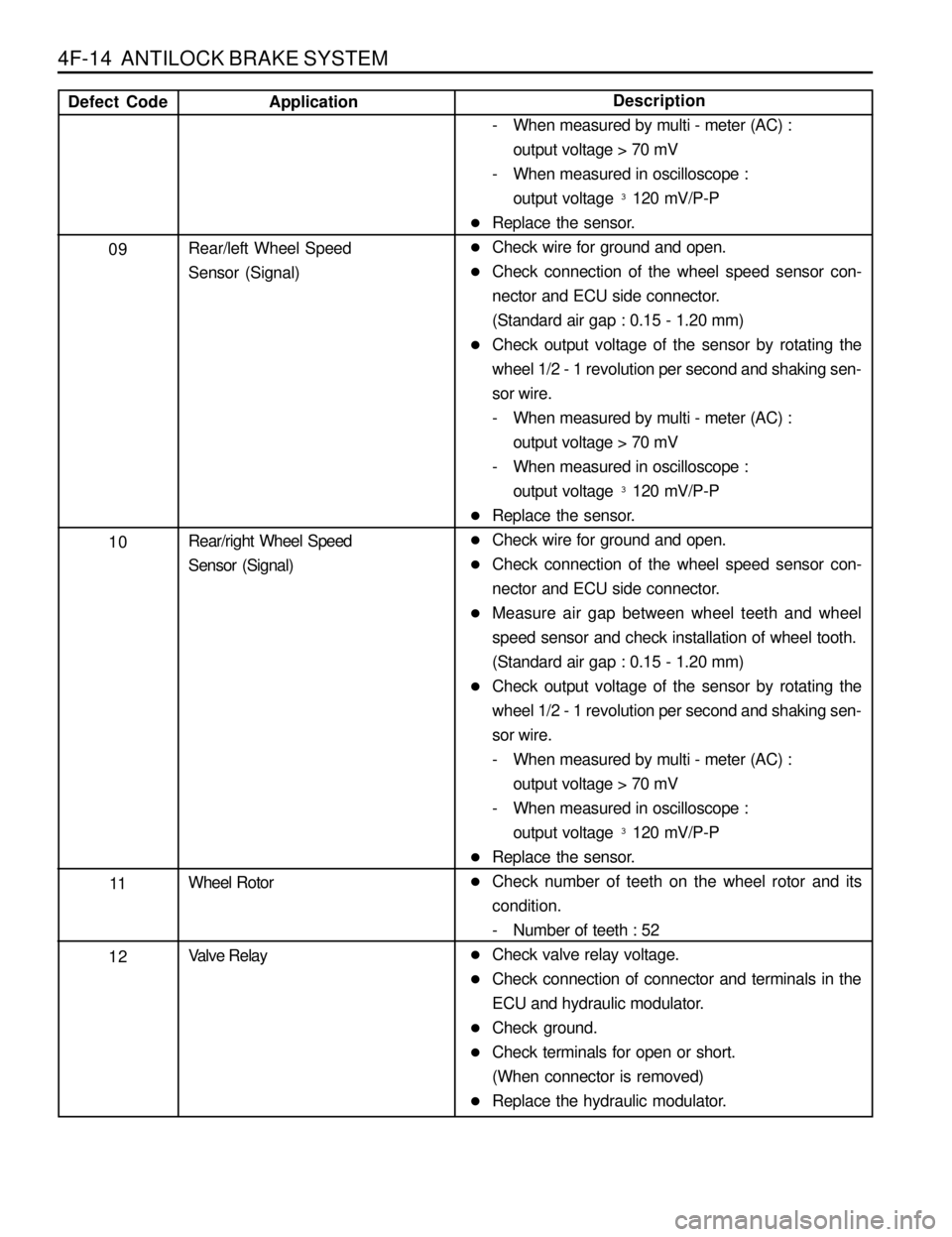
4F-14 ANTILOCK BRAKE SYSTEM
Description
- When measured by multi - meter (AC) :
output voltage > 70 mV
- When measured in oscilloscope :
output voltage ³ 120 mV/P-P
lReplace the sensor.
lCheck wire for ground and open.
lCheck connection of the wheel speed sensor con-
nector and ECU side connector.
(Standard air gap : 0.15 - 1.20 mm)
lCheck output voltage of the sensor by rotating the
wheel 1/2 - 1 revolution per second and shaking sen-
sor wire.
- When measured by multi - meter (AC) :
output voltage > 70 mV
- When measured in oscilloscope :
output voltage ³ 120 mV/P-P
lReplace the sensor.
lCheck wire for ground and open.
lCheck connection of the wheel speed sensor con-
nector and ECU side connector.
lMeasure air gap between wheel teeth and wheel
speed sensor and check installation of wheel tooth.
(Standard air gap : 0.15 - 1.20 mm)
lCheck output voltage of the sensor by rotating the
wheel 1/2 - 1 revolution per second and shaking sen-
sor wire.
- When measured by multi - meter (AC) :
output voltage > 70 mV
- When measured in oscilloscope :
output voltage ³ 120 mV/P-P
lReplace the sensor.
lCheck number of teeth on the wheel rotor and its
condition.
- Number of teeth : 52
lCheck valve relay voltage.
lCheck connection of connector and terminals in the
ECU and hydraulic modulator.
lCheck ground.
lCheck terminals for open or short.
(When connector is removed)
lReplace the hydraulic modulator. Defect Code
09
10
11
12Application
Rear/left Wheel Speed
Sensor (Signal)
Rear/right Wheel Speed
Sensor (Signal)
Wheel Rotor
Valve Relay
Page 963 of 1463
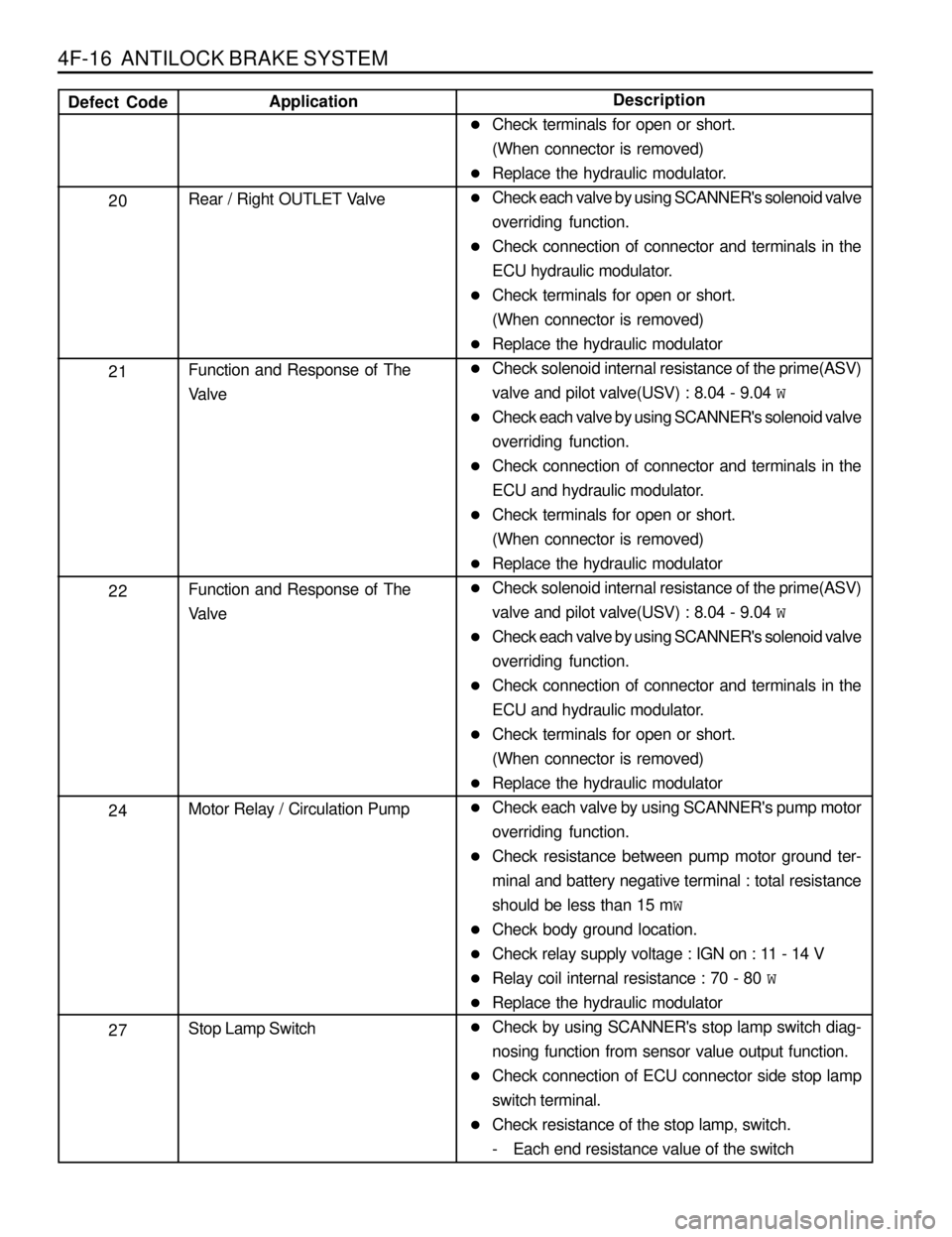
4F-16 ANTILOCK BRAKE SYSTEM
Description
lCheck terminals for open or short.
(When connector is removed)
lReplace the hydraulic modulator.
lCheck each valve by using SCANNER's solenoid valve
overriding function.
lCheck connection of connector and terminals in the
ECU hydraulic modulator.
lCheck terminals for open or short.
(When connector is removed)
lReplace the hydraulic modulator
lCheck solenoid internal resistance of the prime(ASV)
valve and pilot valve(USV) : 8.04 - 9.04 W
lCheck each valve by using SCANNER's solenoid valve
overriding function.
lCheck connection of connector and terminals in the
ECU and hydraulic modulator.
lCheck terminals for open or short.
(When connector is removed)
lReplace the hydraulic modulator
lCheck solenoid internal resistance of the prime(ASV)
valve and pilot valve(USV) : 8.04 - 9.04 W
lCheck each valve by using SCANNER's solenoid valve
overriding function.
lCheck connection of connector and terminals in the
ECU and hydraulic modulator.
lCheck terminals for open or short.
(When connector is removed)
lReplace the hydraulic modulator
lCheck each valve by using SCANNER's pump motor
overriding function.
lCheck resistance between pump motor ground ter-
minal and battery negative terminal : total resistance
should be less than 15 mW
lCheck body ground location.
lCheck relay supply voltage : IGN on : 11 - 14 V
lRelay coil internal resistance : 70 - 80 W
lReplace the hydraulic modulator
lCheck by using SCANNER's stop lamp switch diag-
nosing function from sensor value output function.
lCheck connection of ECU connector side stop lamp
switch terminal.
lCheck resistance of the stop lamp, switch.
- Each end resistance value of the switch Application
Rear / Right OUTLET Valve
Function and Response of The
Valve
Function and Response of The
Valve
Motor Relay / Circulation Pump
Stop Lamp Switch
Defect Code
20
21
22
24
27
Page 964 of 1463
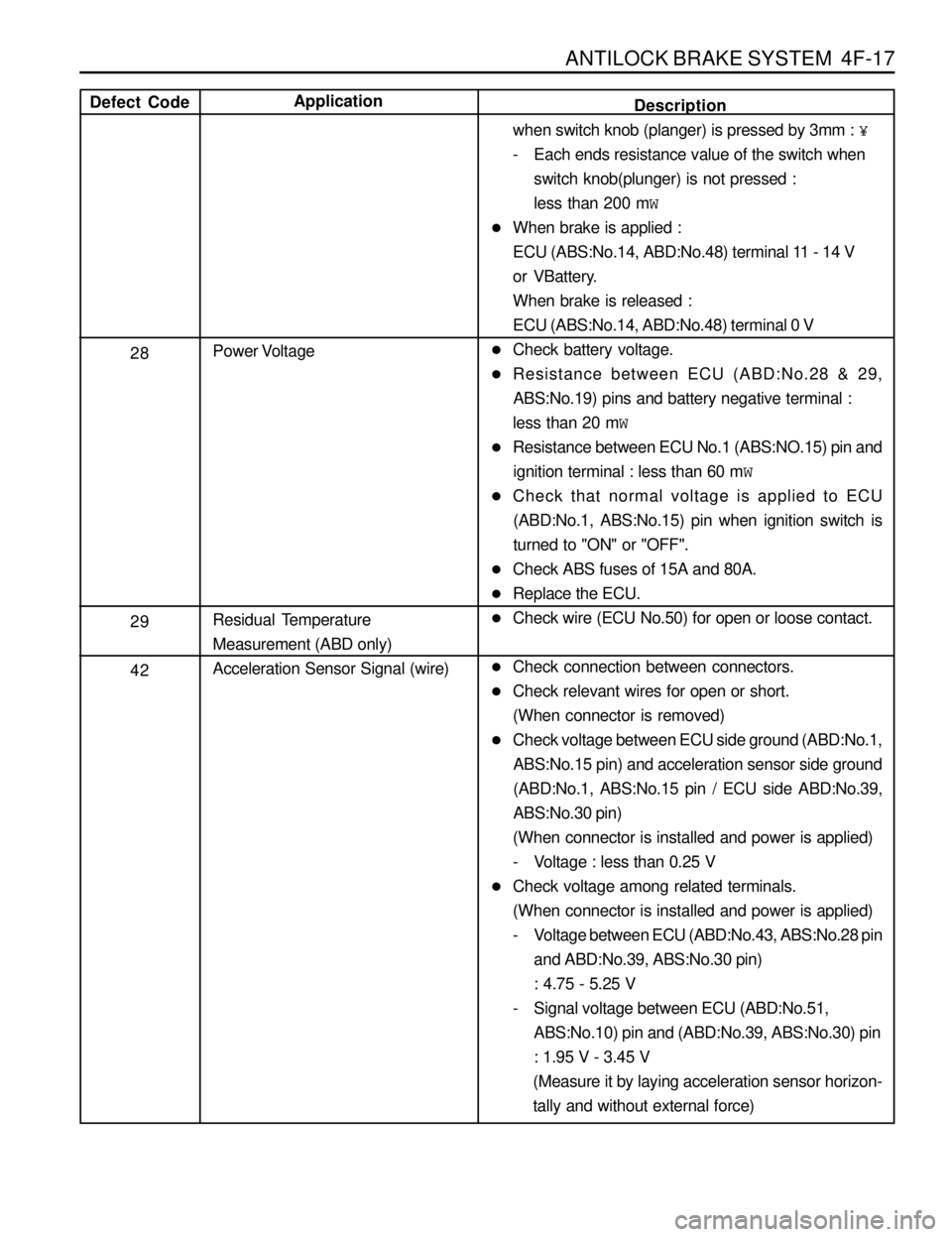
ANTILOCK BRAKE SYSTEM 4F-17
Application
Power Voltage
Residual Temperature
Measurement (ABD only)
Acceleration Sensor Signal (wire)Defect Code
28
29
42Description
when switch knob (planger) is pressed by 3mm : ¥
- Each ends resistance value of the switch when
switch knob(plunger) is not pressed :
less than 200 mW
lWhen brake is applied :
ECU (ABS:No.14, ABD:No.48) terminal 11 - 14 V
or VBattery.
When brake is released :
ECU (ABS:No.14, ABD:No.48) terminal 0 V
lCheck battery voltage.
lResistance between ECU (ABD:No.28 & 29,
ABS:No.19) pins and battery negative terminal :
less than 20 mW
lResistance between ECU No.1 (ABS:NO.15) pin and
ignition terminal : less than 60 mW
lCheck that normal voltage is applied to ECU
(ABD:No.1, ABS:No.15) pin when ignition switch is
turned to "ON" or "OFF".
lCheck ABS fuses of 15A and 80A.
lReplace the ECU.
lCheck wire (ECU No.50) for open or loose contact.
lCheck connection between connectors.
lCheck relevant wires for open or short.
(When connector is removed)
lCheck voltage between ECU side ground (ABD:No.1,
ABS:No.15 pin) and acceleration sensor side ground
(ABD:No.1, ABS:No.15 pin / ECU side ABD:No.39,
ABS:No.30 pin)
(When connector is installed and power is applied)
- Voltage : less than 0.25 V
lCheck voltage among related terminals.
(When connector is installed and power is applied)
- Voltage between ECU (ABD:No.43, ABS:No.28 pin
and ABD:No.39, ABS:No.30 pin)
: 4.75 - 5.25 V
- Signal voltage between ECU (ABD:No.51,
ABS:No.10) pin and (ABD:No.39, ABS:No.30) pin
: 1.95 V - 3.45 V
(Measure it by laying acceleration sensor horizon-
tally and without external force)